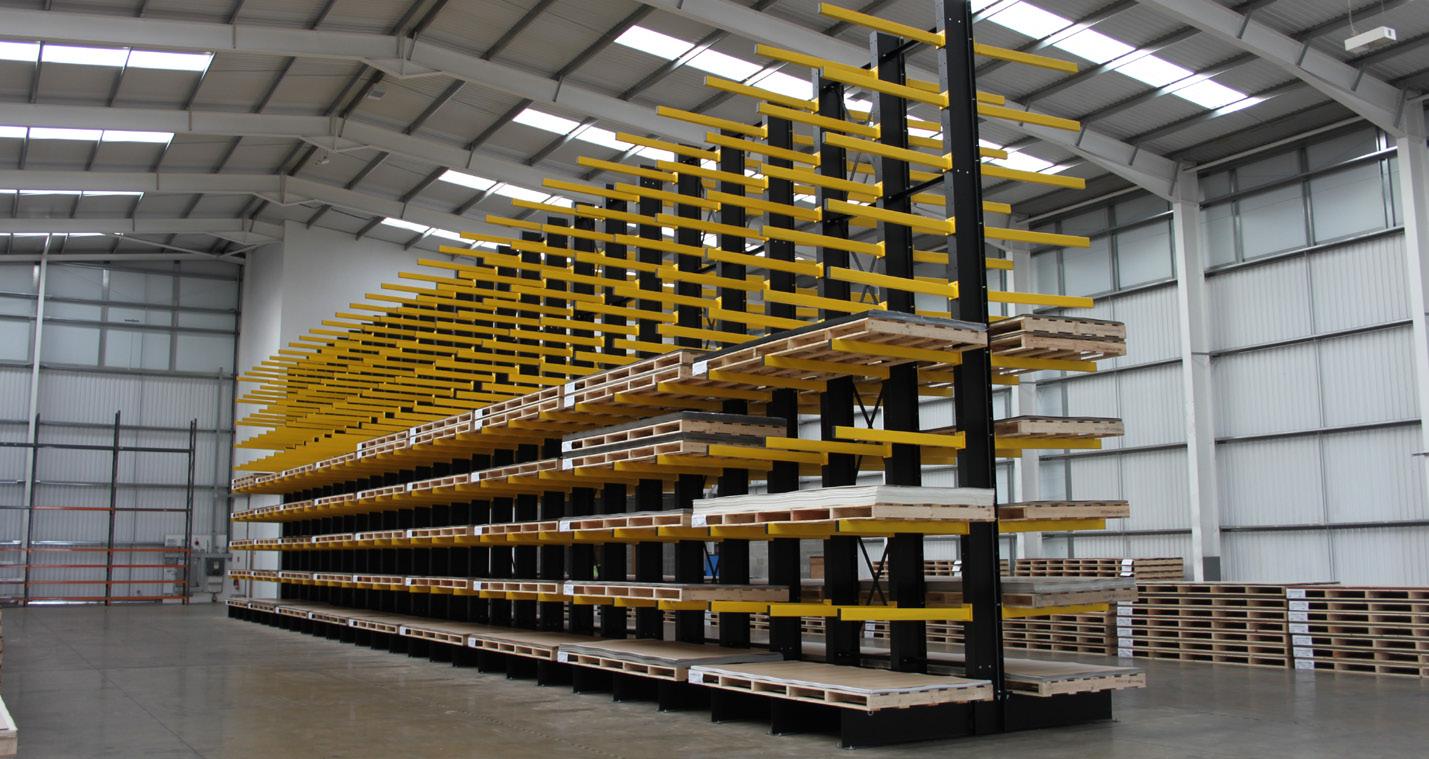
6 minute read
Organising Storage and Improving Operations
Wickens Engineering, a leading UK racking manufacturer shares some thoughts on what to consider when reorganising storage and what to look for when purchasing racking systems
Capital investment questions related to building layouts, site organisation, storage systems and lifting plant are often raised when relocating or opening a new site. However, a decision to reorganise the existing storage facilities is also quite common. It is generally based on a few reasons: the ratio of footfall versus the volume of storable items in combination with inability to extend the storage space whether it is a building or a yard; lack of organisation delaying smooth running of day-to-day operations; damage caused to items from storing them on the floor. On some occasions, the above scenarios can also result in some basic health and safety breaches and accidents.
Whatever the reason for the site improvements, there are numerous considerations to take into account and various storage system options to choose from.
Which type of storage system?
The first question that should always be asked is what is being stored? The most efficient storage systems are normally tailored to product, its type, dimensions, weight and quantities. Every type of item, whether bar, tube and lengths of metal, coils, flats, heavy machinery components, tools or any other, might require a specialised storage approach.
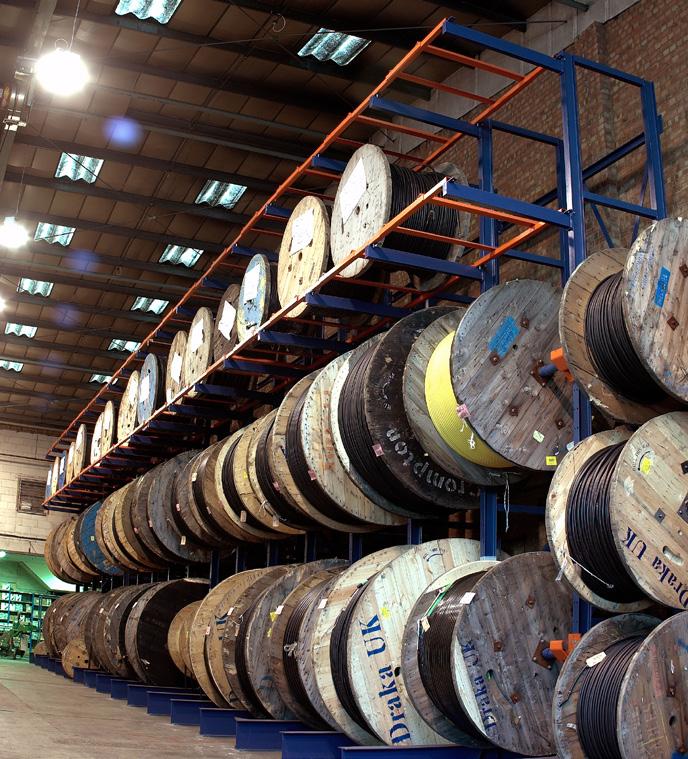
A coil racking system allows unwinding cable whilst coils are in situ on racking
The way of storing these items is also important for determining racking type and specification, which could differ for items stored on pallets, bundles, in cradles or loose. Based on the product type, there are multiple racking system types available ranging from some of the most popular options like cantilever racking, an openfront system that is suitable for extra-long, bulky stock to heavy duty racks, capable of withstanding up to 20-tonne loads per location.
Then there are more niche products, like coil racks, a system allowing storage of multiple cable coils in the height of the rack and with ability to unwind them whilst they are in situ. Whilst there are some racking systems with a standard specification on the market, Wickens takes a different approach and tailors it’s racking systems to maximise their effectiveness. ‘Our first task is to understand what the customer needs’ says Dave Wheatley, Sales Director at Wickens. ‘We then work on developing a bespoke solution that suits those requirements in the most cost-efficient way yet offers a structurally sound, fit-for-purpose system.’
What else to consider?
Whilst understanding the product specification is important, there are other elements to consider, in particular the site itself and potential space limitations. This could include height restrictions dictated by both ceiling beam locations and lifting plant limitations. The type of the forklift used can also affect the specification of the racking and the overall layout of the storage area due to factors such as bedspace height and the required turning area.
In some instances, where space is limited, a guide rail system may be a good solution for ensuring that the forklift is guided down narrower aisles. One of the popular Wickens products is Rack Clad buildings – a fully enclosed storage system that utilises racking as the structural framework of the building and is designed with all the storage and space considerations in mind. The benefit of such a structure is its semi-temporary nature, meaning it can be erected in as little as ten weeks and extended or relocated at a later date.
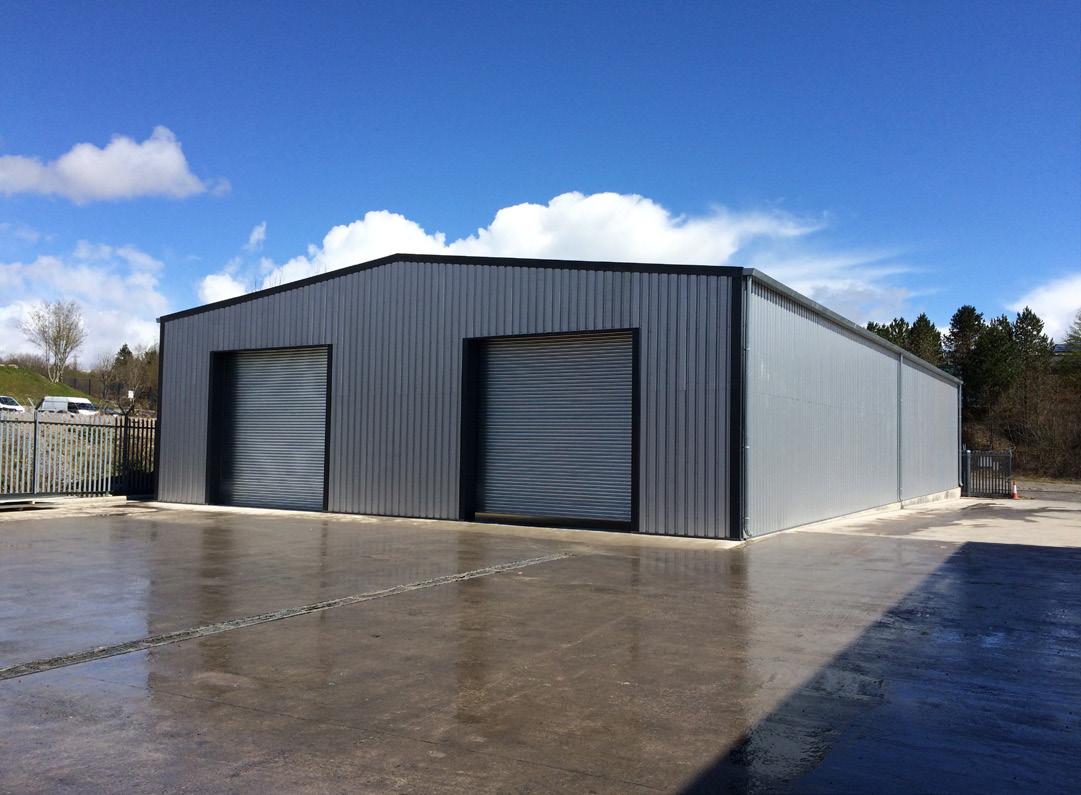
Rack Clad Building – storage racking forms the structural framework of the building, complete with roof, cladding and doors.
What about safety?
Any racking system is a structural feature, which has its capabilities and limitations. Therefore, it needs to be suitable for the application and meet quality standards.
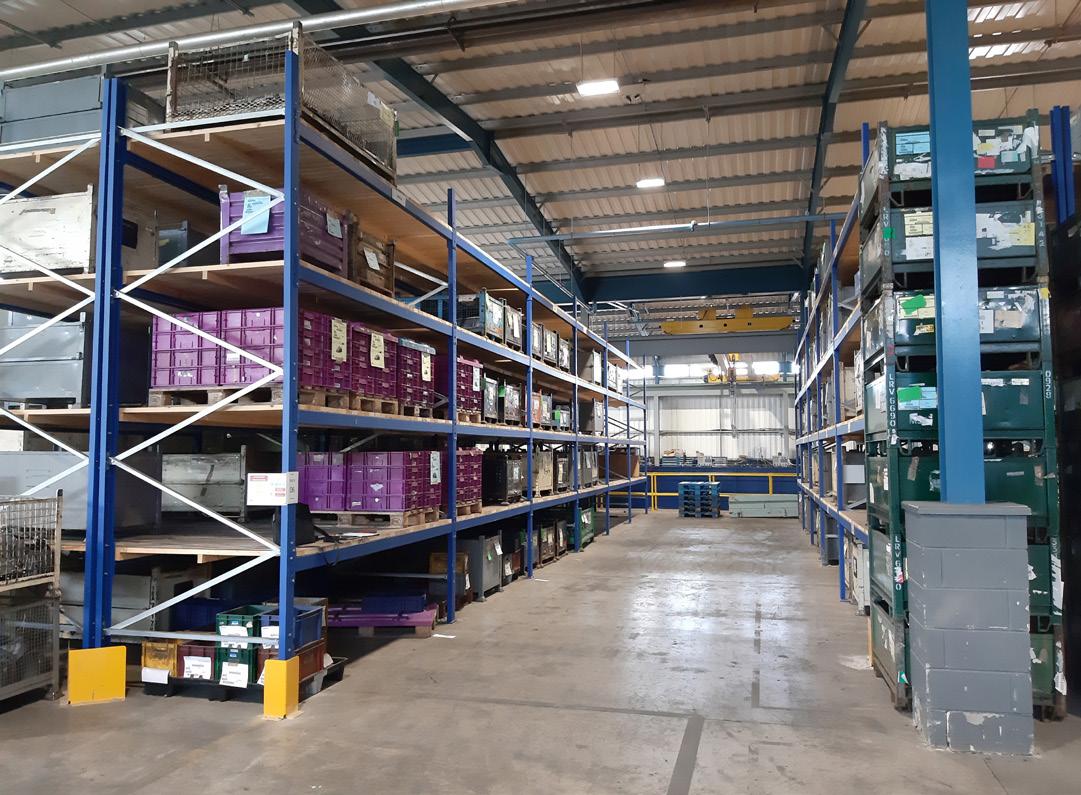
Wickens Structural Pallet Racking is made from hot-rolled structural steel sections, making it more resistant to forklift damage than conventional pallet racking.
Both design and manufacture of racking must comply with legal requirements such as CE marking. In addition, Wickens is ISO 9001:2015 accredited, demonstrating quality management systems in place throughout the business from initial enquiry processing to manufacturing and despatch. ‘Quality is key to our business and products, so we ensure that our systems are robust and reliable, that the standards are met throughout manufacturing processes and control systems, and that high quality structural steel is used for every rack system and the finish used is aesthetically pleasing’ comments Dave.
Racks should be installed by qualified teams, who follow strict method statements and installation instructions. Failure to install components correctly can have dangerous consequences to the integrity of the heavy load bearing structure.
Once in place, all racking systems must have load labels with weight capacities clearly visible to operators, who should be trained to operate lifting plant and be aware of loading restrictions.
Needless to say, racking systems also require regular maintenance like annual racking safety inspections and replacement of damaged components.
How can Wickens help?
Wickens has an extensive distributor network operating in the Rail Industry, so depending on site location, overall requirements and other determining factors, racking systems could be supplied either directly or through a distributor. Either way, the aim is to provide the best service with a full project management option for larger and more complex projects.
Normally, this includes a number of steps in the process: the initial visit or a discussion when the overall requirements are understood and the specification drafted; a site survey to ensure that the floor is level and suitable for the rack as well as to spot any hazards and limitations which could have an effect on the functionality of the storage system. It is then followed by the design and manufacture of the racking at purpose-built factory premises in Worcester. Once delivered, it will then be installed by a team of professional racking installers, who aim to complete the project on time and with minimum disruption on site. Whichever racking option is chosen, all of the important elements of the project should always be based on outstanding product quality, complimented by excellent customer service, and that is what Wickens believes to be the core of its business for every storage system project.
Tel: 01905 456780
Email: sales@wickens.co.uk Visit www.wickens.co.uk
Address: Wickens Engineering Ltd
1 Shire Business Park, Wainwright Road, Worcester, WR4 9FA
