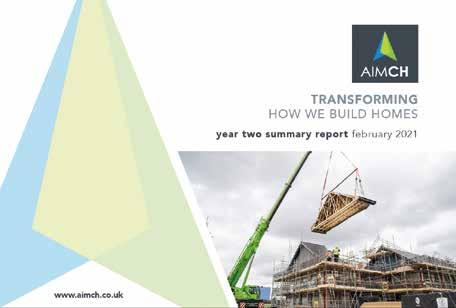
11 minute read
Constant Evolution
Advanced Industrialised Methods for the Construction of Homes (AIMCH), the innovation consortium set up to transform the housebuilding sector, has published its second-year progress report and highlights some fundamental learning points.
AIMCH is a three-year research and development project aiming to help tackle the UK housing crisis by building new homes faster, to higher quality and more cost effectively than masonry methods using panelised offsite systems. The latest report highlights several key learnings for the industry across several important and innovative areas. One of the highlights being able to achieve a weathertight, insulated and secure superstructure in just one day. All advanced panelised offsite systems and lean construction solutions trialled so far have been successful and early analysis is recognising the benefits of these systems with the hard data to back it up. Other important outputs of the project in the last year include the completion of several studies and the publication of guides for industry including:
• Design standardisation and the development of product families • Guide to creating a BIM housing manual • Design for Manufacturing and
Assembly (DfMA) • Designing a future factory.
1
“Despite the challenges of COVID-19 the project team has worked hard to build momentum,” says Stewart Dalgarno, AIMCH Project Director and Stewart Milne Group Director of Product Development. “It has delivered some important outputs which confirm panelised MMC as a very real and viable alternative to masonry, over the final year, we hope to take this to a new level.”
Monitoring has taken place on 42 plots (23 Barratt and 19 L&Q), with over 100,000 operative observations recorded and 500,000 pieces of data collected and used to evaluate masonry, timber frame and advanced closed panel MMC methods.
A collaboration between Stewart Milne Group, Barratt Developments, L&Q, Forster Group, the Manufacturing Technology Centre (MTC) and Construction Scotland Innovation Centre (CSIC), the project compares conventional and panelised MMC construction methods on actual building sites, and the impact scaling up panelised MMC will have on the housebuilding industry. The threeyear project, which has been live since early 2019, has been trialling new digital design tools, manufacturing advancements, and improved near-tomarket offsite panelised systems, using lean site processes on live housing projects over the past two years.
Standardisation of subassemblies and the creation of product families, within housing design, as a mainstream industrialised process, is a significant shift for the AIMCH developers and wider industry.
Mark Farmer, the Government’s MMC Champion for Housebuilding and new AIMCH Chair, said: “Mainstreaming all categories of MMC is more important than ever. In a post-COVID world the sector needs to transform productivity, improve quality as well as improving the welfare of its workforce. We also need to find more sustainable ways of building in order to achieve a net zerocarbon built environment.
“The AIMCH project has already made great progress across a number of fronts which will better enable greater MMC adoption across all parts of industry including SME’s. The work done on design standardisation, panelised and sub-assembly system applications, productivity and carbon measurement and manufacturing
process optimisation are all rich sources of knowledge for others to learn from and use.”
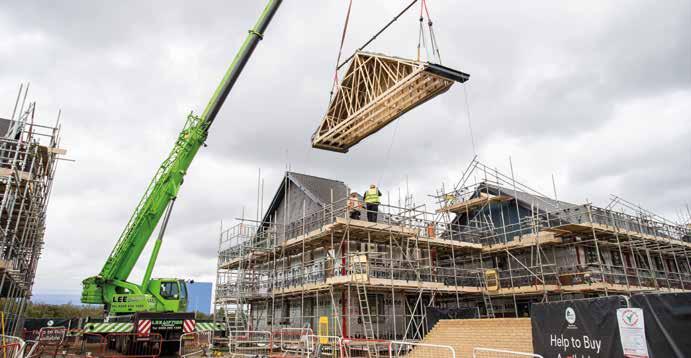
The completion of Future Factory Simulation has paved the way for Offsite Manufacturing (OSM) companies to make more agile decisions about increasing capacity to the market by using modelling and simulation tools to support and control digital factory planning activities.

The project recognises the challenges of MMC manufacturing and through engagement with MTC, lead manufacturing partner, has conducted advanced manufacturing and digital business systems studies. These include down selection process for an integrated ERP system for MMC manufacturing and installation, along with detailed proof of concept studies into specific manufacturing areas, where using robotics and advanced automation can improve MMC manufacturing output, productivity, quality and lower costs, including the design of future factories using mathematical models, dynamic simulation and 3D technology to improve investment decisions.
With decarbonisation of the built environment a priority, the project embarked on a study to measure and profile Embodied Carbon and Whole Life Costing in the use of MMC systems across four housing types to current and near zero carbon standards. A strategy for a proof of concept, near zero carbon home trial was also developed with Barratt Developments.
The project also recognises the importance of SMEs and through Forster Group, roofing specialist, has helped accelerate their roofing technology, through collaborative learning and proof of concept trials with MTC and the AIMCH developers. Dissemination is important and provided by CSIC including presenting at several key industry events, a dedicated industry stakeholder group, project website and social media.
2
The housing industry is well suited to BIM adoption, where the benefits of a standardised designs, collaborative procurement and repeatable processes are inherently built into the housebuilding delivery process.
The goal of the project is to support the sector by delivering 120,000 homes for the same or less cost than traditional methods and built 30% quicker. The project has potential to impact on 35,000 homes being delivered by AIMCH partners across the UK each year. In the project’s final year, a number of outputs and learnings for the sector will be completed and shared on the AIMCH website as well as at industry events, with final findings published in March 2022.
3
As traditional resources of labour and materials become more expensive and limited and with the journey towards greater energy efficiency and carbon neutrality, it is now more important than ever to achieve cost certainty, better quality, speedier build and reduction in carbon footprint.
For more information and to download the year 2 progress report visit: www.aimch.co.uk
Images:
01. Transforming How We Build Homes:
Year 2 summary report 02. Housebuilding is at the centre of creating a sustainable future for the UK 03. New AIMCH Chair, Mark Farmer
CASE STUDY GEOMETRY LESSONS FOR IBSTOCK
2
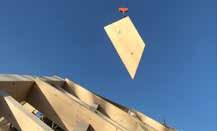
Maccreanor Lavington recently completed a refectory at Ibstock Place School, an independent, co-educational day-school for over 1,200 four- to 18-year-old pupils in south-west London.
The building replaces its conservatorystyle, acoustically flawed predecessor at the heart of the landscaped school campus. An intricate timber roof structure conveys intimacy and grandeur to the interiors, where natural light and orchard views bestow a calm and contemplative quality upon the warm, convivial space. Rising to three glazed lanterns, the roof supports a simple natural ventilation strategy and defines the uses below.
As the largest element the building, the roof’s geometry and construction were a focus for aesthetics and performance in which the use of timber became instrumental: working with structural consultants engineersHRW, Maccreanor Lavington developed a structure that provides a clear order and scale to the building’s volumes. The refectory’s ceilings are defined by a striking spruce glulam lattice structure, with oak panelling insets incorporating acoustic absorption. The glulam elements are constructed on a diamond grid, although, structurally, they owe much to a traditional cut timber roof.
“There is a hierarchy of elements with the primary rafters spanning between a steel ring-beam at the eaves and a timber ring-beam at the lantern or the corner rafters,” says Greg Nordberg from engineersHRW. “The primary rafters support secondary and tertiary elements that form the rest of the lattice. The secondary elements are sized to match the primaries, providing the desired pattern within the space. Using the rafters as a two-way spanning diagrid was also considered in detail. This format reduced the stresses on the individual members however the more onerous connections meant equivalent sized sections would be required. The stiffness of the roof geometry and the truss action of the roof were considered with separate models to provide an envelope of forces for element design and examine alternative load paths for disproportionate collapse.”
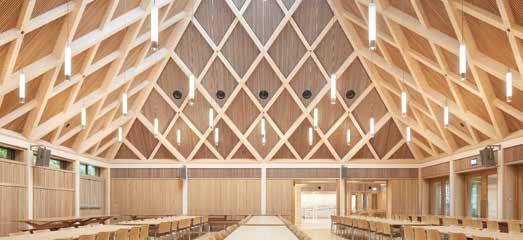
Between the deep rafters sits a subsidiary grid of smaller glulam sections. The striking graphic arrangement of the rafters into this ‘tartan’ provides a rational and attractive framework for oak batten infill panels with acoustic backing, which were prefabricated and fully finished offsite. The geometry was developed to limit the panels to just four different shapes across the building and make them a manageable size for manual handling.
The millimetre precision of the glulam allowed for the development and construction of complex connections, enabling the assembly of roof pitches set to different angles. These connections formed the interface between the timber roof and the steel structure that supports them. The galvanised plate connections were developed by engineersHRW and specialist contractors Constructional Timber considering both the structural requirements and the ability for the large timber elements to be installed.
“With the restricted site access all deliveries were arranged using rigid vehicles only, which was challenging when the hip-beams were nearly 11m long and weighing 1.2 tonnes,” says Andrew King, Director, Constructional Timber. “For the installation sequence it was key to fix the level of the lantern beams off the temporary loadbearing scaffold supplied by the main contractor. The lantern beams were levelled to the correct height before the twin hip-beams were craned into position. The members were all supplied fully protected and with their fire treatment applied so to reduce site time and potential for damage.”
1
Ensuring long-lasting harmony in the different timber finishes – spruce glulam structure, oak timber linings and joinery and oak engineered wood floors – was important. We were keen to control the aesthetic over time and were mindful that the softwood glulam would redden from sunlight exposure. We wanted to avoid the space adopting an orangey ‘sauna’ look and a strident contrast with the more muted hue of the aged oak finishes. For this, we worked closely with timber coatings’ company Renner to do accelerated ageing of the different glulam finishes in a lab, developing a white tinted fire-proofing finish that would remain UV-stable.
For more information visit: www.maccreanorlavington.com
Images:
01-02. The striking graphic arrangement of the rafters provides a rational and attractive framework for oak batten infill panels with acoustic backing and were prefabricated and fully finished offsite
HYBRID WALL PANELS: A NEW APPROACH
Metsä Wood and its partners have designed a landmark hybrid sandwich wall panel that combines concrete with Kerto® LVL (laminated veneer lumber) to bring sustainable and efficient construction to the offsite arena.
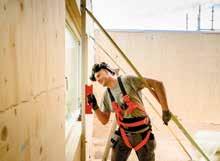
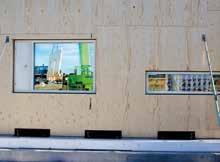
1
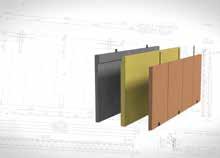
The need for more sustainable solutions is acute with construction causing 30% of all carbon emissions. Combining concrete and Kerto® LVL, the hybrid sandwich wall panel offers an easy way to replace typical concrete sandwich elements, and can be used in residential, office or industrial multistorey buildings.
Metsä Wood partnered with Finnish construction and structural design companies to design the hybrid sandwich wall panel. Precast element manufacturer Lipa-Betoni saw the potential of the hybrid approach. “The hybrid sandwich wall element is a great opportunity. We look for a new market with a product, which can be used in the same way as concrete sandwich elements,” says Satu Lipsanen, CEO of Lipa-Betoni.
The starting point for the new element design, was a common residential seven-storey building with a concrete structure, including hollow-core slabs and party walls made from concrete. In the hybrid sandwich wall panel, the load-bearing internal panel is replaced with a Kerto® LVL Q-panel. Otherwise, the structure of the element remains the same – the façade is made from concrete and the element has an insulation layer.
“As a material, Kerto® LVL is very comparable with concrete,” says
2
Ari Mättö, Structural Designer of JM-Rakenne Oy. “The compressive strength of the Kerto® LVL panel is as high as that of C25 concrete, 26 MPa. Also, the tensile strength of the panel is at the same level, whereas in concrete it is 10% of the compressive strength without steel reinforcement. In a hybrid sandwich element, the reinforcement is needed only in the façade.”
During construction, the loads are transferred from the external wall to the concrete structure to stiffen the building. The new element also provides effective insulation. By building a hybrid element from timber and concrete, the U-value can be 20% better. “The hybrid sandwich wall element helps to increase the share of wood to build more sustainable buildings efficiently,” says Jussi Björman, Director, Business Construction at Metsä Wood. “This joint development is our effort to support the construction industry. Around one million square metres of concrete wall elements are produced annually in Finland. Their load-bearing core creates 45,000 tons of carbon emissions. If all concrete walls were replaced with hybrid sandwich wall elements, carbon emissions would decrease by 30,000 tons a year and 95,000 tons of carbon would be stored.” The first hybrid sandwich wall panels will be produced at Lipa-Betoni's factory in Pieksämäki, Finland, for Metsä Fibre's Rauma sawmill construction project. Metsä Fibre’s new Rauma pine sawmill is the largest sawmill investment ever in Finland costing EUR 200million. The sawmill will produce around 750,000 cubic metres of pine sawn timber annually, with production set to begin during the third quarter of 2022.
On a global scale, the potential is huge. “Metsä Wood currently works with European and Australian companies to produce similar ideas that fit the local way of construction,” adds Björman. “Half a dozen designs are being prepared for publication this year. As Kerto® LVL is a light material, the hybrid sandwich wall elements will be faster to produce at the factory and transport to site, and even the transport emissions will decrease due to the light load. The light elements are also faster to lift.” The hybrid sandwich wall element designs are already available at the Open Source Wood platform, which aims at facilitating knowledge sharing, co-creation and growth in modular timber construction.
3
For more information visit:
www.metsawood.com
Images:
01-03. The hybrid sandwich wall panel combines concrete with Kerto® LVL (laminated veneer lumber) to deliver project cost and carbon savings