
16 minute read
Il tuo partner per la produzione del futuro
IL COLAB SCHUNK DA OGGI ANCHE IN ITALIA
L’11 LUGLIO È STATO INAUGURATO IL COLAB, UN CENTRO APPLICATIVO PER COBOT E SISTEMI DI PRESA A SERIVIZIO DEI CLIENTI
di Eleonora Segafredo
Il CoLab è un concept originale e innovativo, lanciato a fine 2020 dalla casa madre Schunk in Germania ed esportato successivamente negli Stati Uniti, in Cina e in Messico. Il CoLab inaugurato a luglio in Italia è il secondo in Europa, a conferma del ruolo strategico che il nostro Paese rappresenta per l’azienda.
Grazie al nuovo centro applicativo i clienti italiani potranno usufruire di un servizio nuovo, unico e innovativo. Nella sede di Lurate Caccivio nei pressi di Como, sarà possibile testare la fattibilità delle applicazioni in un ambiente realistico. Grazie alla preziosa collaborazione di ABB, Fanuc, Omron e Universal Robots, i tecnici avranno la possibilità di accompagnare il cliente nella realizzazione completa del processo, dal componente di presa all’applicazione reale. d’idea di espandere il numero di CoLab è venuta dopo il successo del primo centro applicativo in Germania. Infatti i processi automatizzati, la robotica industriale e collaborativa rendono la produzione più efficiente ed ottimizzata. Tuttavia, iniziare con l’automazione non è sempre facile: è necessario considerare diverse variabili, e solo l’esperienza insegna. SCHUNK ha quindi pensato di supportare i suoi clienti mettendo a disposizione di un team di tecnici interni un laboratorio attrezzato con cobot per analizzare, testare e convalidare le richieste di applicazione dei clienti con lo scopo di minimizzare il rischio dell’investimento e offrendo un supporto concreto per l’avvio di un processo automatizzato. Con questo approccio pratico, SCHUNK offre la possibilità di automatizzare senza rischi, verificando i sistemi di presa e gli accessori robot più idonei al pezzo da manipolare fornito, effettuando report, analisi di processo, studi di fattibilità e video dimostrativi, anche per nuove tecnologie. “In questo spazio i nostri clienti avranno la possibilità di testare le applicazioni con i nostri sistemi di presa prima di acquistarli. Un’idea originale che ci distingue dalla concorrenza e che ci offre svariate possibilità. Il nostro CoLab sarà uno spazio multifunzionale anche per corsi formativi, eventi online e in presenza, attività marketing e comunicazione insieme ai nostri provider tecnologici.” spiega Andrea Lolli, Sales Manager Sistemi di Presa, che ha condotto la realizzazione del progetto nella filiale italiana.
Un know-how completo per ogni esigenza applicativa
Grazie al contributo appunto di ABB, Fanuc, Omron e Universal Robots e altri player del settore che offrono soluzioni per i processi di automazione, SCHUNK Intec Italia è in grado ora di fornire un know-how completo a 360° e per ogni diversa esigenza applicativa. Per l’inaugurazione dell’11 luglio, sono state preparate e mostrate alla stampa, quattro diverse demo per illustrare al meglio le potenzialità del CoLab a clienti finali, system integrator e alla stampa specializzata, intervenuta all’evento. Ogni applicazione mette in rilievo le caratteristiche uniche e innovative di
ogni sistema di presa applicato a ciascun cobot. Il linguaggio di programmazione semplice del nuovo GoFa™ di ABB è stato abbinato al modulo bionico e sostenibile ADHESO nella manipolazione di lenti o componenti elettronici; l’accuratezza e la precisione del cobot FANUC CRX si sono rivelate perfette per un’applicazione di sbavatura con i nuovi tool R-EMENDO per la finitura superficiale. La videocamera integrata sul polso dell’OMRON TM ci ha permesso di realizzare un’applicazione con FlexiBowl® di Ars Automation, l’innovativo alimentatore di pezzi, in questo caso ferromagnetici, da manipolare con i nuovi moduli elettro-permanenti EMH. Infine, la cella di carico integrata nel cobot UR10 di Universal Robots è risultata particolarmente funzionale per un’applicazione di machine tending, in cui con i nuovi Kit MTB - Machine Tending Bundle, composti da un doppio modulo di presa e una da morsa pneumatica controllabile direttamente dal controllore del robot, hanno simulato un carico e scarico macchina utensile efficiente ed ottimizzato.
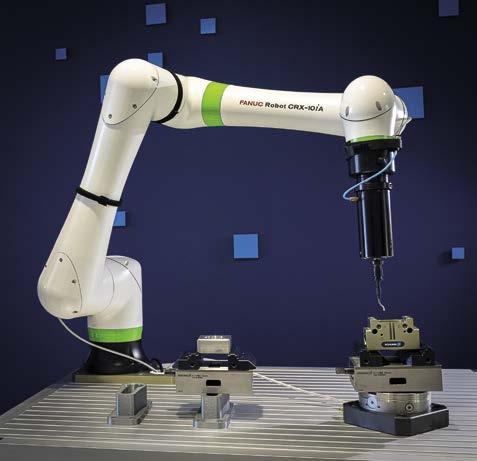
L’accuratezza e la precisione del cobot FANUC CRX si sono rivelate perfette per un’applicazione di sbavatura con i nuovi tool R-EMENDO per la finitura superficiale. Foto: SCHUNK
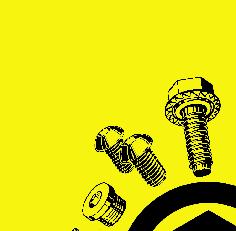
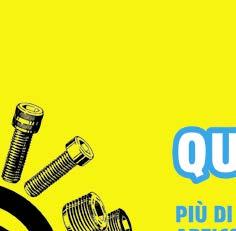
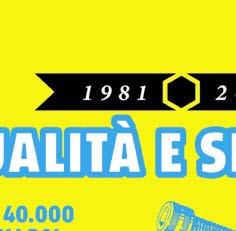
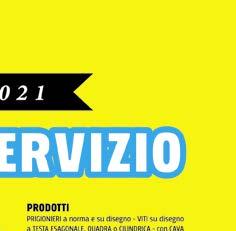
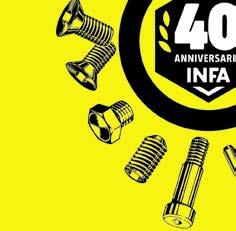
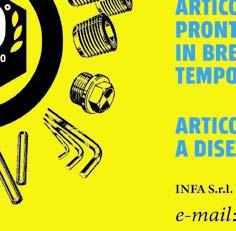
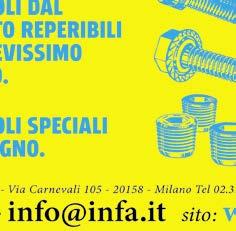
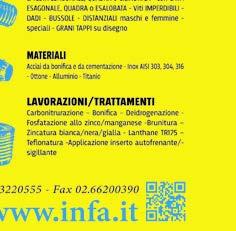
IL TUO PARTNER PER LA PRODUZIONE DEL FUTURO

UNO STAND RICCO QUELLO CHE RENISHAW PRESENTERÀ ALLA PROSSIMA EDIZIONE DI BIMU MILANO.OLTRE ALLE ULTIME SOLUZIONI DI SMART FACTORY E INDUSTRIA 4.0, CI SARANNO TUTTE LE NOVITÀ REALIZZATE NELLA RACCOLTA E GESTIONE DEI DATI DI DISPOSITIVI, PROCESSI E COMPONENTI
di Cristina Gualdoni
Renishaw, azienda specializzata in metrologia industriale, additive manufacturing e controllo di processo, parteciperà come di consueto a BIMU 2022. Proprio in occasione dell’evento l’azienda ha presentato in anteprima alla stampa le ultime novità del settore e i trend manifatturieri futuri. Un dato sicuramente importante, a dimostrazione dell’importanza che Renishaw dà alle innovazioni tecnologiche è quello della spesa in R&S. “Nel 2021 l’azienda ha investito il 13% di fatturato in R&S – come ha sottolineato Roberto Rivetti, A.D. di Renishaw spa, alla presentazione. – L’investimento in R&S diventa sempre più fondamentale viste le sfide e le esigenze produttive che siamo chiamati ad affrontare: le aziende cercano maggiore efficienza, sostenibilità e semplicità. Sono questi i fili conduttori del futuro. Un aspetto fondamentale emerso dal momento specifico che stiamo vivendo è non sprecare tempo, risorse e materie: la sostenibilità a 360 gradi. Le rilavorazioni hanno costi troppo elevati per poterseli permettere”. Renishaw è un’azienda che si vanta di essere particolarmente attenta a questo tema da sempre. Nel Novembre 2021 infatti si è impegnata a raggiungere l’obiettivo ‟Net Zero” entro e non oltre il 2050. Di cosa si tratta? Net Zero è l’obiettivo, portato avanti dalle aziende europee, di azzerare le emissioni di carbonio entro il 2050, in modo tale da poter contribuire a frenare l’aumento delle temperature globali. Già adesso l’80% del fabbisogno totale di elettricità di Renishaw arriva da fonti rinnovabili ed è in continuo aumento. Nell’anno finanziario 2021, meno del 10% di tutti i rifiuti è andato in discarica. I progettisti Renishaw lavoreranno per quantificare e ridurre l’impronta di carbonio dei nuovi prodotti e per creare soluzioni ‟circolari”. Inoltre tutti gli obiettivi saranno monitorati e convalidati dall’organismo internazionale Science Based Target (SBTi) a dimostrazione dell’impegno concreto dell’azienda. La pandemia da Covid-19 ha messo in luce alcune difficoltà soprattutto nell’ambito della supply chain.
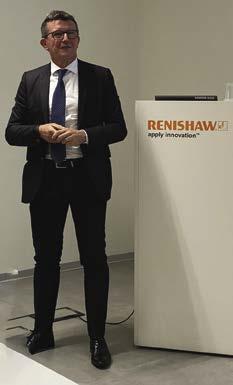

Roberto Rivetti, Amministratore Delegato di Renishaw spa
L’importanza di avere una produzione flessibile che si possa adattare alle variabili legate alle catene di approvvigionamento globali e alle fluttuazioni del mercato è diventata fondamentale per le aziende. Ed è per questo che Renishaw allo stand C13 Pad 9 a BIMU presenterà ai visitatori le proprie soluzioni volte ad una maggiore automazione dei processi, eliminazione dei gap di competenze, una Produzione sostenibile ed una maggiore flessibilità. I visitatori, inoltre, oltre ad ammirare le soluzioni per migliorare produttività e sostenibilità, potranno assistere a dimostrazioni dal vivo.
La nuova generazione di sonde di presetting utensili senza contatto NC4+ Blue
Partendo dalla base dell’ultimo sistema di presetting utensili senza contatto NC4+ Blue, presentato a EMO Hannover 2019, questa nuova versione riprende molte delle eccellenti caratteristiche dell’originale, ma ha un design ultracompatto ed è disponibile in quattro formati diversi, con spazi operativi che vanno da 55 a 240 mm. Anche la ripetibilità delle misure è stata migliorata in tutta la gamma, arrivando ad appena +/- 0,5 micron nelle taglie più piccole. Grazie all’innovativa tecnologia con laser blu e alle nuove ottiche, i sistemi NC4+ Blue di Renishaw migliorano significativamente l’accuratezza delle misure e consentono di lavorare i componenti con maggiore precisione ed efficienza. Inoltre i sistemi NC4+ Blue sfruttano il pacchetto software Renishaw per il presetting utensili senza contatto, il quale viene costantemente aggiornato per assicurare misure sempre più rapide e affidabili anche in condizioni ostili come in elevata presenza di refrigerante. Il software adotta una tecnologia con ottimizzazione automatica che controlla gli spostamenti dell’utensile in ingresso e in uscita dal fascio, riducendo al minimo i movimenti inutili e abbreviando il tempo ciclo. Il pacchetto include una serie di funzionalità molto utili, come ad esempio la modalità di misura doppia, che permette di misurare l’utensile in uscita dal fascio o come l’opzione di pulizia avanzata che mantiene l’utensile libero da impurità e refrigerante durante la misura. Anche i cicli per misurare il profilo e l’eccentricità dell’utensile sono stati migliorati al fine di accrescere l’affidabilità e fornire nuove funzionalità agli utenti più esperti. Per proteggere le ottiche, NC4+ Blue utilizza le tecnologie MicroHole™ e PassiveSeal™ che permettono di misurare gli utensili in modo rapido e affidabile anche in presenza di refrigerante. Il supporto per NC4+ Blue è ora integrato in tutte le interfacce utente di Renishaw, incluse le app per CN e smartphone, come Set and Inspect e GoProbe. Queste piattaforme di programmazione, intuitive e molto potenti, sono lo strumento ideale per gli operatori con scarse conoscenze di programmazione, ma risultano estremamente utili anche per gli utenti esperti.
Il nuovo Sistema di trasmissione radio RMI-QE
L’interfaccia RMI-QE presenta un protocollo di comunicazione aggiornato, che la rende robusta, compatta e affidabile anche in ambienti saturi di frequenze radio. Grazie a una versione aggiornata del consolidato sistema a spettro diffuso con salto di frequenza (FHSS - frequency hopping spread spectrum) da 2.4 GHz, il sistema risulta conforme alle normative radio internazionali e funziona in modo affidabile anche in ambienti con un gran numero di segnali radio. L’interfaccia è ideale per applicazioni in cui non è possibile garantire una linea visiva fra la sonda e il ricevitore, come ad esempio nei centri di lavoro 5 assi e macchine multi-tasking di tornitura/ fresatura. È inoltre adatto all’installazione su centri di lavoro con tavole rotanti o con cambio pallet, perché consente di gestire fino a quattro diverse sonde di presetting utensili
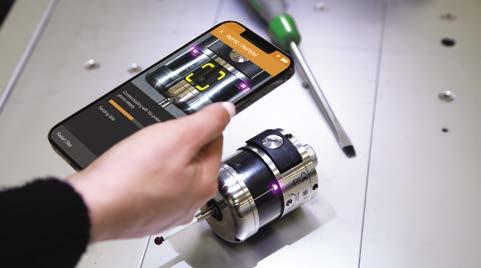
Configurazione di una sonda con l’app Probe Setup
o ispezione pezzo sulla stessa macchina CNC. Grazie al suo design ultracompatto, assicura un’eccellente flessibilità di montaggio e garantisce piena compatibilità con le versioni precedenti. La configurazione è estremamente facile e intuitava. Infatti con la rivoluzionaria tecnologia Opti-Logic™, accessibile tramite la nuova app Probe Setup, è possibile configurare le impostazioni della sonda direttamente dallo smartphone. Inoltre grazie alle innovazione all’elettronica, la durata delle batterie è aumentata del 400% con un’ulteriore attenzione all’ambiente.
AxiSet™ Check-Up la nuova soluzione per la verifica di allineamenti e posizionamenti degli assi rotativi
AxiSet™ Check-Up fornisce un metodo di prova accurato e ripetibile usando routine di tastatura automatiche su un pezzo di riferimento e include una analisi semplice ma completa. Tutte le prove utilizzano tastatori a contatto Renishaw collocati nel mandrino, vale a dire una attrezzatura standard su molte macchine multiasse, in combinazione con routine di tastatura generate usando macro software specifiche per il modello di macchina e fornite con AxiSet™ Check-Up. Il piazzamento è rapido e semplice. Per eseguire la prova l’utilizzatore, utilizzando una base magnetica, colloca all’interno dell’area di lavoro della macchina una sfera calibrata. Con le macro del software personalizzato la sonda è portata a misurare
Ballbar QC20
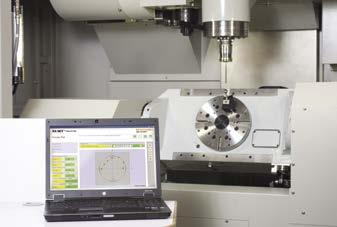
Axiset check-up con sonda Renishaw RMP600
diversi punti sulla sfera. L’utilizzatore ha sempre il pieno controllo del processo e può definire specifici angoli di prova per assicurarsi di provare la macchina nelle orientazioni critiche. Per ottenere la massima accuratezza si consiglia l’utilizzo di tastatori Renishaw con sistema estensimetrico Rengage™. I risultati delle prove eseguite con AxiSet™ Check-Up sono inviati a un PC su cui un foglio elettronico di Microsoft® Excel presenta un analisi di semplice comprensione e confronta le prestazioni della macchina con tolleranze definite. Se necessario l’utilizzatore della macchina può comunicare con il costruttore per effettuare ulteriori prove ed, eventualmente, correggere gli errori. Per assicurare l’ottimizzazione dell’analisi degli assi rotanti utilizzando AxiSet™ Check-Up, è importante che i tre assi lineari
si muovano in maniera corretta. Questo requisito dovrebbe essere verificato e ottenuto con correzioni, se necessarie, provenienti da un sistema di calibrazione laser XL-80, e verificato regolarmente con il nuovo sistema ballbar QC20-W. L’uso combinato di questi strumenti assicura che i pezzi della più alta qualità possano essere prodotti in maniera affidabile e riproducibile su centri di lavoro a cinque assi e macchine di tornitura-fresatura. Ballbar QC20 rappresenta il metodo più rapido, semplice ed efficace per monitorare le prestazioni delle macchine utensili. Il nuovo sistema è perfettamente compatibile con i programmi e i processi sviluppati per QC20-W e permette agli utenti di ottimizzare le misure ballbar, continuando a sfruttare gli investimenti fatti in precedenza. Il ballbar QC20 utilizza la nuovissima tecnologia BLE (Bluetooth Low Energy) la quale garantisce connessioni tramite PC molto più stabili, ottimizzando l’efficienza energetica e prolungando significativamente la durata della batteria. I test ballbar rappresentano una comoda soluzione per eseguire controlli rapidi sulla macchina CNC, per valutarne le prestazioni di posizionamento sulla base di standard riconosciuti a livello internazionale. In questo modo, gli utenti possono definire standard prestazionali, tenere traccia del rendimento delle macchine e
Foto 5 Test ballbar QC20 su tornio
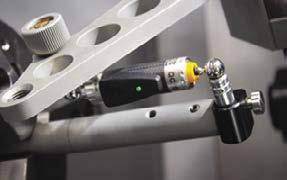
risolvere rapidamente eventuali problemi individuandone le relative cause. Ballbar QC20 va a sostituire il vecchio modello QC20-W.
La nuova sonda RUP per sistemi di misura a 5 assi
La nuova sonda RUP arricchisce la gamma dei sensori della testa REVO, con l’aggiunta delle ispezioni a ultrasuoni per misurare lo spessore dei particolari. A differenza di molti altri sistemi a ultrasuoni, RUP assicura una buona trasmissione del segnale anche senza vasche d’acqua o gel di accoppiamento. Utilizza invece un’innovativa punta a sfera con elastomeri che garantisce un accoppiamento eccellente fra la sonda e il materiale da misurare. Di conseguenza, la sonda RUP non richiede la presenza di operatori specializzati capaci di interpretare le informazioni visualizzate sull’oscilloscopio e permette anche di liberare spazio in officina perché non sono più necessarie né vasche di immersione né CMM dedicate. La possibilità di installare altri sensori nella stessa CMM, contribuisce a incrementare la produttività in modo significativo. Tutte le sonde del sistema REVO sono intercambiabili automaticamente e offrono una grande varietà di funzioni: scansioni e ispezioni a contatto, finitura delle superfici, ultrasuoni, ispezioni senza contatto, a visione e a luce strutturata. Tutte le sonde vengono posizionate su una struttura di riferimento comune, assicurata al piano della CMM, che consente di scegliere il dispositivo più indicato alla misura di particolari anche molto diversi tra loro Le tecnologie multisensore di Renishaw vengono inoltre utilizzate per aiutare le aziende del settore automotive a rinnovare le loro metodologie produttive in preparazione di un futuro più elettrico e sostenibile.
Le tecnologie RENGAGE™ e SupaTouch per ispezioni su macchine utensili
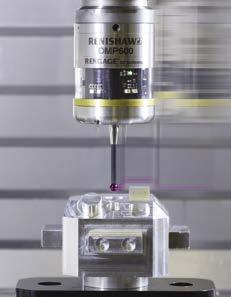
Sonda OMP600 con SupaTouch
A BIMU Renishaw offrirà una serie di dimostrazioni del funzionamento della propria sonda RMP400 per macchine utensili, in combinazione con la tecnologia SupaTouch. RMP400 va ad affiancare RMP600, OMP400, OMP600 e MP250, arricchendo ulteriormente l’offerta Renishaw nel campo delle sonde per macchine utensili con tecnologia RENGAGE™. Questi prodotti uniscono una tecnologia estensimetrica dalla comprovata affidabilità ed elettroniche ultracompatte per assicurare prestazioni 3D straordinarie e ripetibilità inferiori al micron. Ideali per la misura di forme complesse,
le sonde RENGAGE sono perfette per applicazioni nel campo degli stampi e nel settore aerospaziale in cui si utilizzano frequentemente macchine a 5 assi. Grazie alla loro bassissima forza di attivazione, le sonde non causano danni a forme e superfici dei componenti e risultano particolarmente adatte all’ispezione di pezzi delicati. SupaTouch è in grado di determinare in modo intelligente la velocità massima che una macchina utensile può raggiungere senza compromettere la ripetibilità delle misure. Grazie alla sua tecnologia può prendere decisioni intelligenti durante il ciclo di lavorazione e implementare per ciascuna misura la strategia di ispezione più rapida ed efficiente scegliendo tra contatto singolo o doppio. Questa tecnologia elimina gli interventi di configurazione manuale necessari per definire le strategie di ispezione e le velocità di posizionamento e di avanzamento. Rispetto ai cicli software tradizionali, assicura una riduzione del tempo ciclo fino al 60% nelle macchine CNC. SupaTouch permette di sfruttare al meglio le eccellenti funzionalità del rinomato software Inspection Plus di Renishaw.
Equator™, il calibro flessibile programmabile
i calibri da officina Equator offrono tutta la flessibilità di cui le aziende hanno bisogno per affrontare un mercato in costante evoluzione. Le ispezioni attraverso Equator consentono di svolgere semplici procedure di controllo qualità direttamente in produzione. I sistemi di ispezione fissa di tipo tradizionale vengono costruiti per uno specifico
Equator in cella d’automazione ad alta produttività
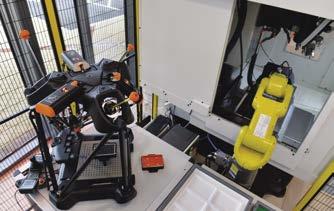
componente. Questo significa che quando un progetto cambia, la sostituzione del calibro può risultare lunga e dispendiosa. Equator di Renishaw è diverso. Il sistema misura gli elementi con una serie di rapide ispezioni a contatto e scansioni ad alta velocità. Assicura un’ottima ripetibilità, non risente delle variazioni termiche, è versatile e, soprattutto, riprogrammabile. Se il design di un prodotto cambia oppure se si deve verificare un progetto completamente nuovo, è possibile riprogrammare Equator e iniziare rapidamente a ispezionare i nuovi componenti. Il calibro Equator usato con il software IPC (Intelligent Process Control) di Renishaw, integra una soluzione per il controllo in officina dei processi di lavorazione a macchina utensile. Il software IPC utilizza i risultati dell’ispezione per aggiornare i correttori utensile e comunicarli al controllo della macchina. In questo modo, si possono identificare automaticamente le cause della deriva del processo, come l’usura dell’utensile, e adattare la lavorazione di conseguenza. Integrato in una cella automatizzata oppure usato in officina come stazione di misura flessibile, Equator può portare a un miglioramento significativo della capacità produttiva.
La nuova sfera di calibrazione ACS-1
La sfera di calibrazione avanzata ACS-1 elimina tutti i passaggi manuali, per massimizzare l’accuratezza delle misure svolte sulle macchine utensili. Il meccanismo serraggio di ACS-1 elimina la necessità di ricorrere a blocchetti calibrati e di riscontro e garantisce la massima ripetibilità e affidabilità. La calibrazione diventa un’operazione molto rapida, in pochi minuti ACS-1 misura con accuratezza la lunghezza della sonda e il diametro della sfera e, grazie alla sua base magnetica, il sistema può essere facilmente installato sul mandrino o sul piano della macchina sia in posizione orizzontale che verticale per adattarsi a tutti i tipi di macchine utensili. Il suo design estremamente robusto e completamente meccanico non richiede batterie e permette al sistema di durare a lungo e di eliminare l’errore umano dai processi di calibrazione delle sonde.
Il nuovo software per il laser di allineamento XK10
Il sistema di allineamento laser XK10 è uno strumento rapido, preciso ed efficiente, che permette di misurare la rettilineità, l’ortogonalità, il parallelismo di rotazione, il parallelismo delle guide, la planarità e l’orizzontalità. Inoltre, consente di determinare la direzione del mandrino e la coassialità delle macchine rotanti. È anche uno strumento efficace per effettuare diagnosi e individuare l’origine degli errori a seguito di una ricostruzione, oppure all’interno di una normale routine di manutenzione. Infatti la nuova tecnologia XK10 utilizza misure laser per acquisire due punti su ciascuna guida, determinare l’angolo fra le due guide e registrarlo in modo digitale. Il sistema XK10 include una dotazione di fissaggi che aiutano a ridurre i tempi di impostazione e può essere utilizzato con l’ottica di parallelismo (opzionale) studiata in modo specifico per questo tipo di applicazione. Con il nuovo sistema, diventa anche più semplice effettuare misure in assenza di guide, perché si possono usare supporti magnetici che permettono al rilevatore di scorrere lungo il bordo del pezzo.
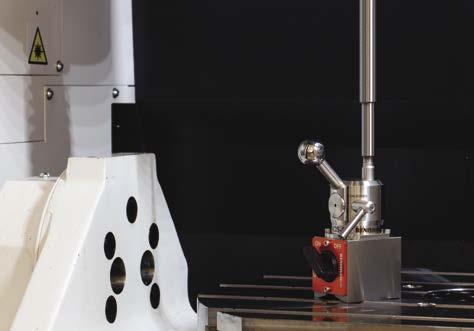
La sfera di calibrazione ACS-1
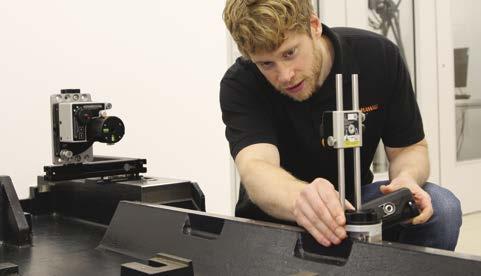