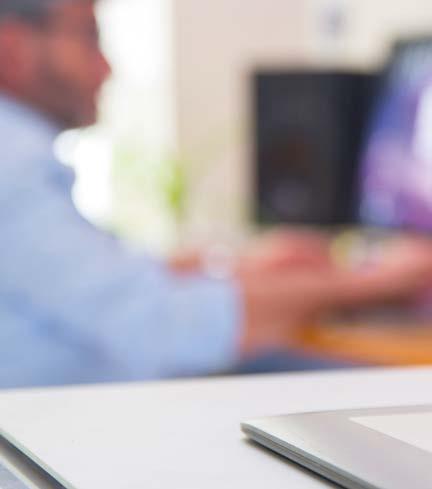
6 minute read
G processing
PER L’OTTIMIZZAZIONE DELLA QUALITÀ DELLE SUPERFICI PER LA STAMPA 3D
I MATERIALI PIÙ INNOVATIVI PER PROGETTARE PEZZI 3D PIÙ RESISTENTI, LEGGERI, FLESSIBILI O DUREVOLI E I TRATTAMENTI E LE FINITURE PER SODDISFARE I VINCOLI E I REQUISITI DI SETTORI PARTICOLARMENTE ESIGENTI di Patrizia Ricci
Grazie alla stampa 3D è possibile realizzare prototipi e produrre parti per un’ampia gamma di applicazioni in modo rapido ed economico. Tuttavia, per ottenere parti che abbiano l’aspetto desiderato o proprietà meccaniche, chimiche e caratteristiche funzionali specifiche, non basta scegliere il giusto processo di stampa 3D perché il risultato finale dipenderà in gran parte anche dai materiali scelti.
I recenti progressi tecnologici ottenuti per i materiali e i processi produttivi hanno permesso all’industria della produzione additiva una continua crescita, sotto ogni punto di vista. Attualmente, la stampa 3D sta riscuotendo un successo sempre maggiore, venendo incorporata e consolidata da diversi settori applicativi. Infatti, anche se il mercato della produzione additiva è stato indebolito dalla crisi sanitaria, è riuscito a resistere, dimostrando i suoi punti di forza e rivelandosi in crescita nell’anno appena concluso con buone prospettive per il 2023. Come già anticipato, i materiali, insieme ai trattamenti e alle finiture, sono una componente chiave del mercato della stampa 3D. Sulla base dell’andamento del 2022, per il nuovo anno si prospettano importanti novità per ognuna delle quattro famiglie di materiali - polimeri, metalli, ceramiche e compositi – destinati alla produzione additiva che contribuiranno alla crescita del settore dell’AM. Nel caso dei polimeri, ad esempio, la sostenibilità e reperibilità stanno diventando sempre più importanti e i produttori spingono sempre di più verso filamenti, resine o polveri provenienti da risorse naturali e rinnovabili. D’altra parte, anche gli utenti sono indirizzati verso la produzione di parti riciclabili o almeno riutilizzabili, con un impatto sempre minore sull’ambiente.
Infatti sia nel mercato dei filamenti, sempre più spesso realizzati a partire da risorse naturali, materiali riciclati o scarti di produzione tecnica delle aziende, che nel segmento delle polveri, i cui produttori cercano di migliorarne continuamento il tasso di riutilizzo e di sviluppare plastiche che possano essere riciclate, la sostenibilità sta assumendo un ruolo centrale.
Parlando di filamenti e quindi di processi di stampa a estrusione, viene spontaneo pensare alla tecnologia FDM. La FDM, o modellazione a deposizione fusa, è spesso considerata la tecnologia di stampa 3D più semplice in quanto consta essenzialmente di tre elementi fondamentali: un piatto di stampa sul quale viene stampato il pezzo; una bobina di filamento che funge da materiale di stampa e una testina di estrusione, anche chiamata estrusore. Il processo consiste nella fusione del filamento dall’estrusore della stampante, che deposita il materiale strato per strato sul piatto.
In questa tecnologia, tuttavia, i filamenti non sono l’unico materiale utilizzabile. Sono sempre più presenti sul mercato stampanti 3D alimentate con pellet. I pellet sono dei granuli utilizzati per lo stampaggio a iniezione che stanno diventando sempre più popolari nella stampa 3D perché consentono un risparmio sui costi e offrono anche una gamma più ampia di materiali rispetto ai filamenti.
I metalli sono tra i materiai più utilizzati nella stampa 3D industriale, soprattutto nei settori aeronautico, automobilistico e bio-medico. Le tecnologie additive a metallo più importanti sono sicuramente la Laser Powder Bed Fusion (LPBF) e l’Electron Beam Melting (EBM, fusione a fascio di elettroni) o Directed Energy Deposition (DED).
Tuttavia, anche per quanto riguarda i metalli, occorre sottolineare la crescita della tecnologia FDM nota anche come fabbricazione a fusione di filamento (FFF), ispirata allo stampaggio a iniezione dei metalli (MIM). Il vantaggio principale di questo processo, che permette di fabbricare una parte metallica con le sole tre fasi di stampa, sformatura e sinterizzazione, è il suo basso costo rispetto alle soluzioni di fusione laser a letto di polvere dotate di uno o più laser, o anche di un fascio di elettroni. Per questo motivo i suoi produttori sono in continuo aumento sul mercato.
Il mercato offre anche composti di rame, caratterizzati dalla presenza di particelle fini e medie che offrono un’elevata conducibilità termica ed elettrica, consentendo un migliore trasferimento di calore e una migliore corrispondenza del coefficiente di espansione termica; polveri di origine biologica e neutrali dal punto di vista climatico o a basso contenuto di carbonio; filamenti che offrono una diversa permittività elettrica e che sono caratterizzati da basse perdite dielettriche con i quali progettare forme più complesse e variare la permittività del pezzo; polveri di titanio a basso contenuto di ossigeno che consentono agli utenti di progettare parti di migliore qualità e durata, poiché è necessario meno ossigeno per produrre la polvere.
Le innovazioni sui materiali per la stampa 3D non si limitano ai polimeri e ai metalli, ma riguardano anche soluzioni più rare come il silicone o la ceramica. Grazie a queste novità, gli utenti della manifattura additiva sono in grado di progettare pezzi più resistenti, più leggeri, talvolta flessibili o addirittura più durevoli. Il silicone, ad esempio, è un materiale sempre più popolare nel mercato della produzione additiva, con proprietà interessanti per molti settori. Sul mercato sono presenti siliconi per i processi basati sul Liquid Deposition Modeling (LDM) e nuovi materiali di supporto idrosolubile che consentiranno agli utenti di immaginare geometrie ancora più complesse, così come stampanti 3D con le quali stampare pezzi con diversi siliconi contemporaneamente.
Perché migliorare la qualità delle superfici delle parti stampate in 3D
Il mondo della stampa 3D è in continua evoluzione, nonostante la sua “giovane” età, anche a seguito delle necessità che con il progredire delle tecniche si delineano tra gli utilizzatori di questa tecnologia, ossia ingegneri, produttori e industrie, ognuno dei quali si trova ad affrontare difficoltà più o meno specifiche in relazione al proprio ambito di attività.
I manufatti ottenibili mediante tecnologie additive hanno raggiunto ormai una qualità molto elevata, basti pensare a quella del- le microfusioni ottenute mediante fusione a letti di polvere; anche i polimeri lavorabili presentano caratteristiche sempre più elevate, come la resistenza al calore e alle sollecitazioni meccaniche e chimiche. Tuttavia una delle caratteristiche dei processi additivi, in particolare con tecnologie LPBF (Laser Powder Bed Fusion), è proprio la non ottimale qualità superficiale dei componenti dopo la fase di stampa. Questo è dovuto all’utilizzo di polveri come materia prima, alla realizzazione del componente strato su strato (staircase effect) e alla presenza di supporti necessari alla produzione del componente stesso. Anche se la risoluzione ottenibile ha raggiunto livelli molto alti, si va dai decimi di millimetro della tecnologia FFF ai centesimi della stereolitografia ai micron della fusione a letti di polvere dettata delle dimensioni del granello di polvere metallica, tali tecnologie additive non presentano ancora la possibilità di produrre particolari estetici senza alcun trattamento successivo e quindi non si può prescindere dal ricorso a trattamenti estetici e funzionali. A seconda delle specifiche esigenze di ogni singolo componente vengono applicate tecnologie e soluzioni differenti.
Uno dei temi più attuali , quindi, riguarda la continua ricerca della finitura perfetta. Anche perché molto spesso determinate industrie o settori industriali hanno una serie di standard obbligatori da soddisfare per garantire il corretto funzionamento di determinate parti, sistemi o servizi. Il che costringe, nel caso di pezzi o parti prodotti con stampa 3D, al controllo delle proprietà delle parti stampate in 3D, sia in termini di prestazioni che di biocompatibilità, per il soddisfacimento di questi requisiti. In tal senso, è fondamentale la post-produzione delle parti grezze realizzate con produzione additiva. Si tratta di passaggi successivi alla fase di produzione in cui vengono eliminate le imperfezioni inevitabilmente presenti sul pezzo stampato mediante i quali gli utenti riescono a conseguire la finitura desiderata o richiesta dagli standard. Accade spesso, infatti, soprattutto quando si utilizza la tecnologia di stampa FFF, che l’oggetto che esce dalla stampante 3D necessiti di ulteriori trattamenti superficiali.
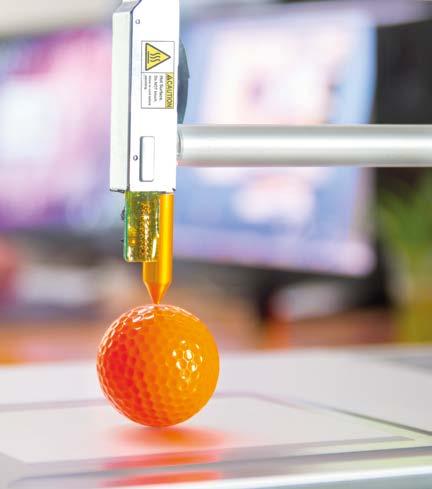
Per questo motivo sono nate diverse soluzioni di postproduzione per le parti stampate in 3D atte al conseguimento delle certificazioni necessarie per le diverse applicazioni, che consentono di competere direttamente con i processi tradizionali, come lo stampaggio a iniezione. Come naturale conseguenza, i principali attori dell’Additive Manufacturing stanno mostrando un crescente interesse per il post-processing grazie al quale ottenere l’alta qualità delle superfici finali, le ottime performance e una buona estetica.
Le più attuali tecniche di post- processing della stampa 3D
Le soluzioni di post-lavorazione disponibili sul mercato vanno dalla pulizia del pezzo, intesa sia in termini di rimozione del materiale in eccesso e/o dei supporti, alla finitura superficiale, e infine alla colorazione. Per quanto riguarda la pulizia della parte, occorre precisare che una volta stampato il componente, raramente è utilizzabile così com’è. Il più delle volte, è necessario un passaggio per rimuovere il materiale in eccesso. Nel caso delle tecnologie a letto di polvere – metallo o plastica – il processo viene chiamato de-powdering, mentre nel caso delle tecnologie a resina, pulizia. Qualora sia necessario rimuovere anche i supporti di stampa, in alcuni casi si interviene a mano, in altri, come nel caso dei processi metallici, occorre una macchina specifica in quanto i metodi di rifinitura a mano sono costosi, irregolari e non riescono a stare al passo di una produzione di massa.
Una delle sfide più attuali della post-elaborazione è la riduzione del tempo necessario per completarla, che mediamente richiede tra l’11-25% del tempo totale di produzione. Indipendentemente dal processo utilizzato, infatti, la richiesta dei produttori è quella di ottenere soluzioni più rapide, accessibili e automatizzate. Per questo motivo, oggi, l’evoluzione della tecnologia e in particolare delle tecniche di post-processing sta portando sempre di più all’utilizzo di metodi automatizzati per la finitura dei componenti. Il processo di rifinitura delle superfici per la produzione additiva può essere automatizzato, ad esempio, con soluzioni tecnologiche, in alcuni casi ancora in fase di brevetto, che integrano hardware e software proprietari con la chimica, garantendo che ogni componente stampato abbia la Ruvidezza Media (Ra) e la consistenza dimensionale desiderata, e conservi intatta la rifinitura dei dettagli delle stampe in 3D. Queste tecnologie innovative, che assicurano la rimozione coerente e totale dei supporti da ogni componente senza rotture e garantiscono la sicurezza che ogni componente