
8 minute read
Energy effi ciency: Grenzebach/CNUD Waste recovery system improves effi ciency
A waste heat recovery system (WHR) from Grenzebach* and CNUD EFCO** can help companies fight climate change, improve energy efficiency during production, reduce the use of resources while also improving the CO2 emission balance, and cutting costs.
Glass production has always required a lot of energy. The main cause for that is the relatively inefficient glass melting process with a rather low energy efficiency.
A large part of the lost energy is in the exhaust gas from the glass melting tanks. This is where typical WHR plants come in: they use this waste heat to generate electricity, as well as heating and cooling energy for process and air-conditioning purposes.
“Our patented waste heat recovery concept stands out from other technologies especially thanks to its improved efficiency without neglecting the plant reliability of a float glass or container glass line”, says Dennis Schattauer, Managing Director of CNUD EFCO.
The advanced waste heat recovery solution from Grenzebach and CNUD EFCO makes a real contribution to achieving climate targets, conserving resources and improving cost efficiency – three of the fundamental challenges in the glass industry.
The use of a WHR system increases the energy efficiency in the production and reduces the carbon footprint. Costs are significantly cut by avoiding CO2 emissions and purchasing less electricity and fossil fuels.
“Against the backdrop of the European Green Deal in particular, companies should act now to sustainably reduce their carbon footprint”, Mr Schattauer emphasises.
The aim of the European Green Deal is to make all 27 member states climate-
� The WHR system from Grenzebach and CNUD EFCO is manufactured to operate at the highest level of efficiency.
neutral by 2050. Numerous measures are taken to achieve this aim.
The CO2 prices will increase noticeably as will the number of specifications for the energy efficiency of production sites.
As an interim target, member states commit themselves to cutting more than 40 percent of their CO2 emissions by 2030.
Requests to raise this target even up to 55 percent have already been submitted. The glass industry has to increase their efforts significantly beyond this selfcommitment to reach the aspired aim of being climate-neutral by 2050.
The path to a climate-neutral glass industry
A climate-neutral glass industry? Ambitious, yet feasible. To reach this aim, existing technologies have to be retrofitted sustainably, or even rethought.
It is still a long path to electric melting furnaces or hydrogen-powered furnaces, which aim on producing glass climateneutrally. Some open questions need to be answered first: � Which economic and ecological advantages and disadvantages arise from these new technologies? � When will a sufficient quantity of green energy and green synthetic fuels be available? � When will new technologies, like electric furnaces or hydrogen-powered furnaces, be ready for the market?
The development and testing of such technologies will also still take time, too much time.
To be able to reach the aspired goals of cutting CO2, sustainable decisions in the
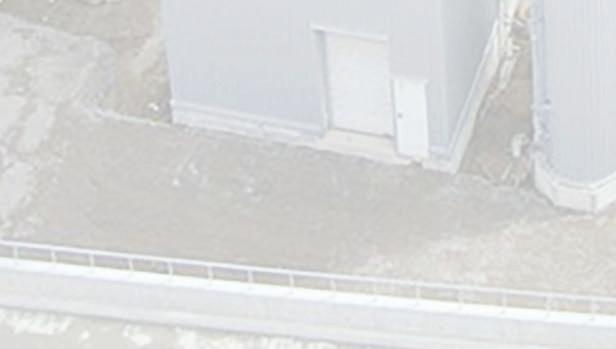
� The two companies join their expertise together to develop improved waste heat recovery systems for fl oat glass plants.
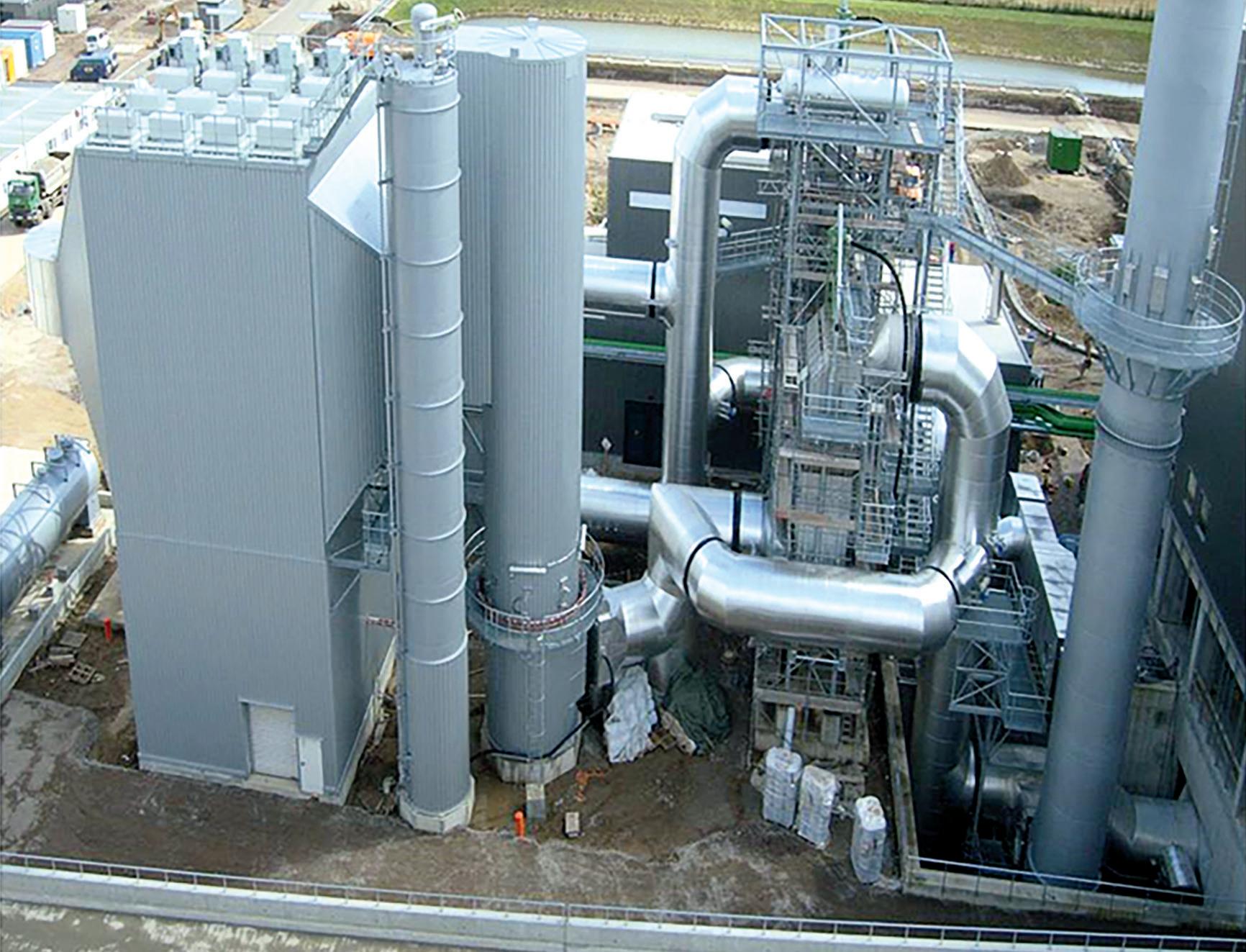
glass industry have to be made now.
Therefore, it has to be considered, among other things, which of the already available climate-friendly technologies are suited best to achieve the interim targets, as it could still take years until electric melting furnaces and hydrogenpowered furnaces are available.
Today’s approaches have to reduce emissions, increase the energy effi ciency, and have an optimal cost-benefi t ratio. All of these aspects are combined in the advanced waste heat recovery system.
Advanced WHR system – Significantly higher energy effi ciency and energy production values
On the basis of mastered and tested technologies, waste heat recovery plants increase the energy effi ciency and reduce the used resources at the same time.
Compared to other systems on the market, the advanced waste heat recovery system solution from Grenzebach and CNUD EFCO excels itself through its extraordinarily high effi ciency in generating energy, which can amount to up to 35 percent or more.
This leads to notably higher energy effi ciency and energy production values in comparison to relatively low investment costs. The advanced WHR system uses the available thermal energy in the melting tank exhaust gas to produce steam at pressures up to 90 bar by integrating heat ex-changer boiler systems into the exhaust gas fl ow.
This steam is then fed into the highly effi cient turbine/generator unit to generate electrical power.
Due to its effi ciency, advanced waste heat recovery plants are suited specifi cally for the use in big glass melting plants, such as fl oat glass melting tanks or container glass plants with several glass melting tanks at one site.
The transition to climate-neutral technologies will take the longest time in the fl oat glass industry due to the long service lives of melting tanks, which can last be-tween 15 and 20 years.
This is where the advantages of the advanced WHR system become clear. A clever solution on the path to climateneutrality: � Signifi cant increase of energy effi ciency � Notable reduction of used resources � Sustainable reduction of the carbon footprint � Signifi cant reduction of costs
The advanced WHR plants are integrated “smartly” into the existing production process so that the glass production process remains almost unaffected.
This advantage, together with the already mentioned economic and ecological bene-fi ts, leads to a high return on investment.
The capital payback period of this WHR solution is considerably reduced thanks to investment subsidies granted in many countries.
An advanced waste heat recovery plant from Grenzebach and CNUD EFCO is therefore a profi table investment in the future, with signifi cantly higher energy effi ciency and energy production values in comparison to relatively low investment costs.
Climate-friendly advantages even after 2050
Even after achieving the aim of being climate-neutral by the year 2050, waste heat recovery plants will still be of major importance in the glass industry.
New technologies will continue to have to deal with the questions of sensible use of resources and optimal energy effi ciency.
WHR plants will thus continue to make an important contribution to the effi cient and climate-friendly use of resources when utilising synthetic fuels, such as hydrogen.
An additional asset of the advanced waste heat recovery system is that further ecological and economic potential can be tapped into through the “intelligent” system integration of the advanced WHR plant into the glass melting process.
Upon customer request, additional possibilities of saving energy, such as generating heating or cooling energy, can be included into the WHR concept at any time.
“The WHR technology is a very concrete offer we can make the glass industry thanks to the combined competencies of Grenzebach and CNUD EFCO.
“Our customers benefi t from the fact that we now work with the integrated knowhow from the hot and cold end of fl oat glass lines. And a particular focus is on energy effi ciency”, says Egbert Wenninger, Chief Commercial Offi cer and member of the Grenzebach Management Team.
Proven technology from power plant construction
The WHR systems from Grenzebach and CNUD EFCO are exclusively equipped with proven technology from power plant construction.
The design is based on many years of experience and proven computer-aided simulation pro-grams.
The WHR solutions demonstrate a
Continued>>
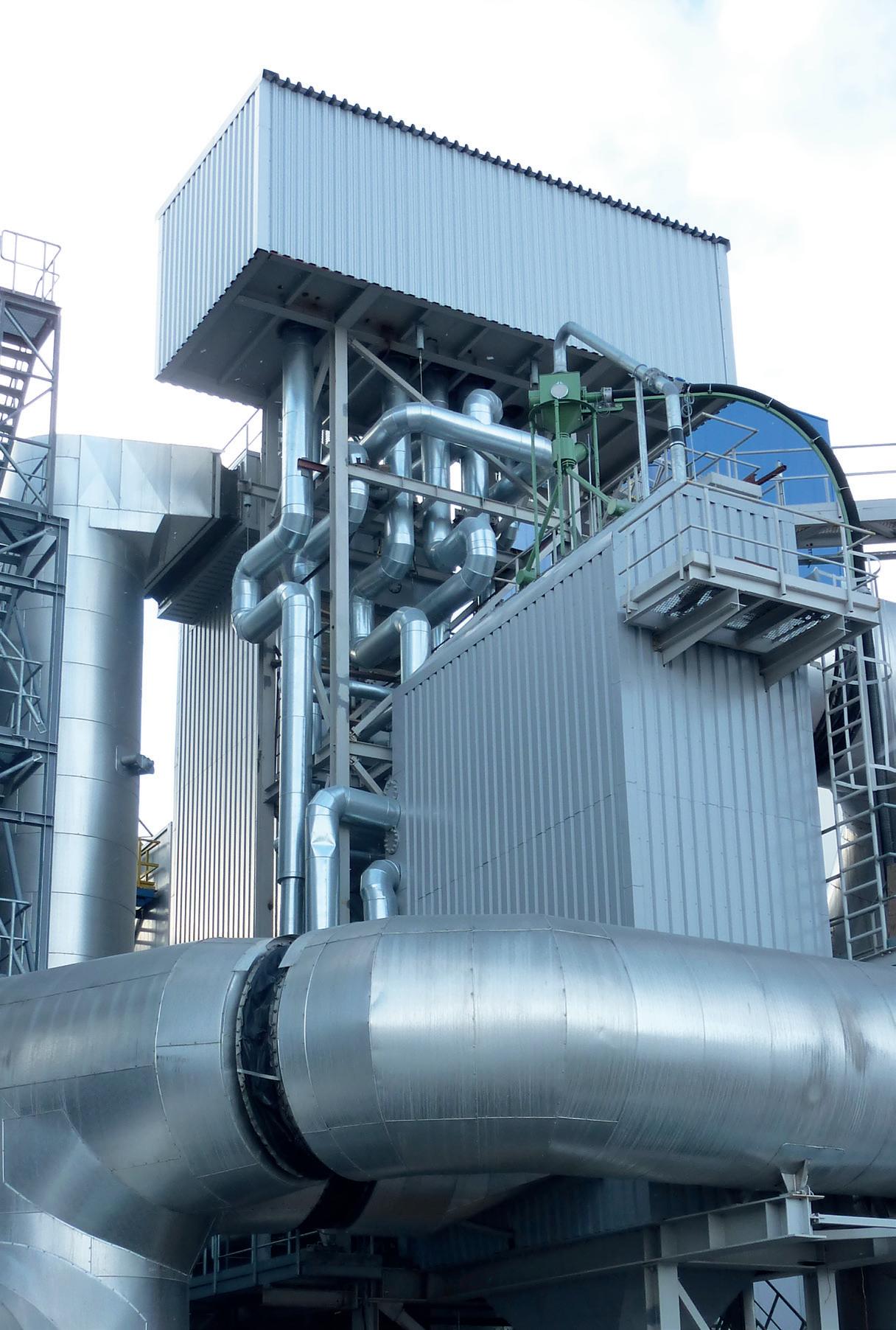
�The advanced WHR system is said to yield much higher energy effi ciency and energy production values.
unique performance with guaranteed effi ciency, net energy generation and plant availability.
Years of comprehensive knowledge from the construction and operation of glass production plants are part of many detailed solutions for the optimal integration of the WHR plants.
This smart integration of the WHR plants allows an additional reduction of operating and investment costs for peripheral plants.
State-subsidised in many countries
When considering the return on investment (ROI), it has to be taken into account that the installation of WHR systems is subsidised by the state with 25 percent and more in many countries.
In the long term, higher electricity and gas prices are to be expected, as well as a stronger use of CO2 certifi cates.
“Already today, a plant like this will pay for itself within three to four years in a favourable environment,” Mr Schattauer explains.
The benefi ts of the advanced WHR systems will also remain completely unchanged when natural gas is replaced by hydrogen as the primary energy source.
Mr Schattauer concludes: “You will keep the yield of a WHR plant, even if you decide to run your production line with hydrogen in the future.” �

Boom, Belgium http://www.grenzebach.com/en/ http://www.cnudefco.com
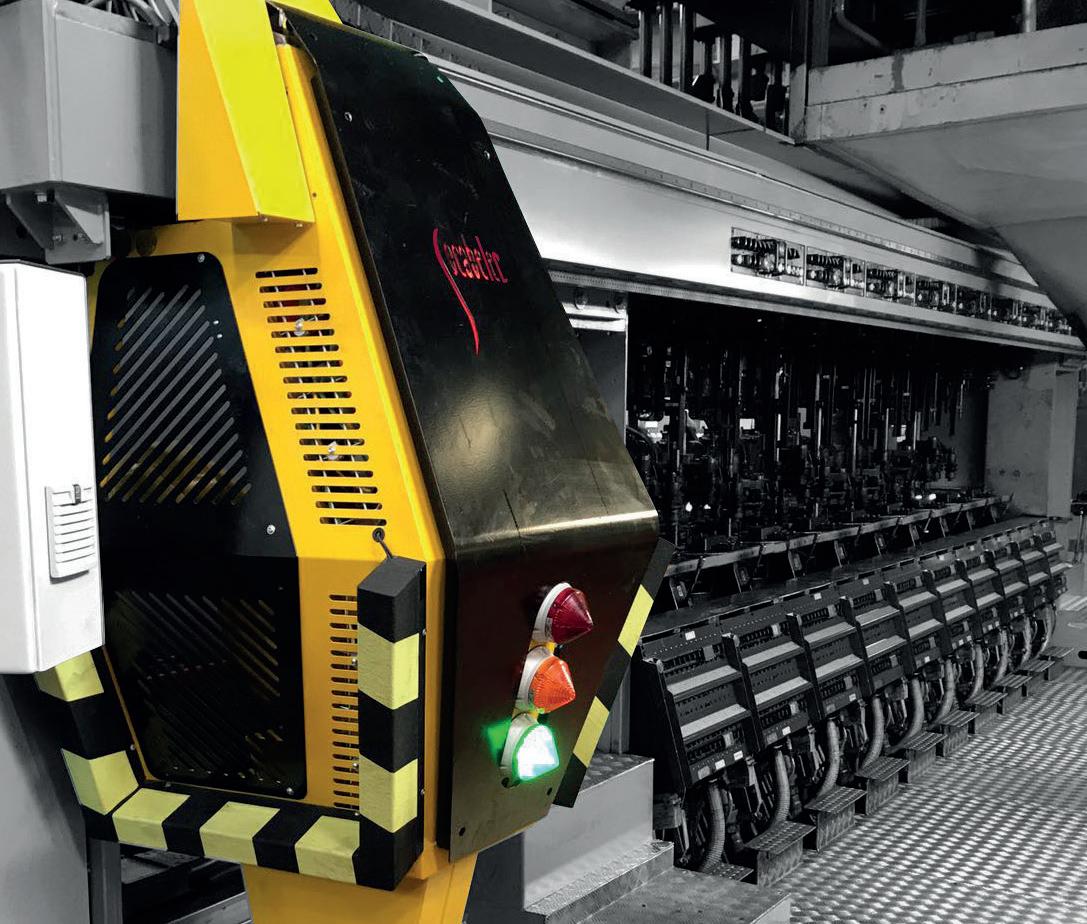


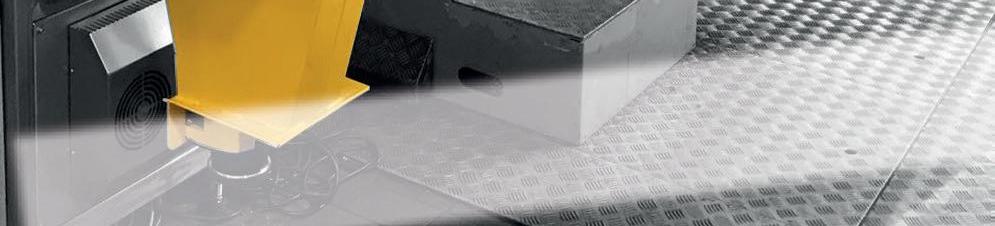


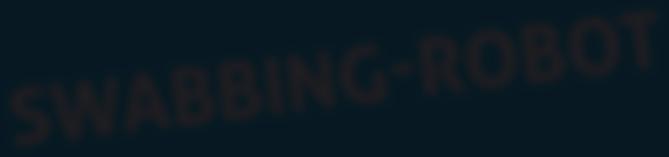

