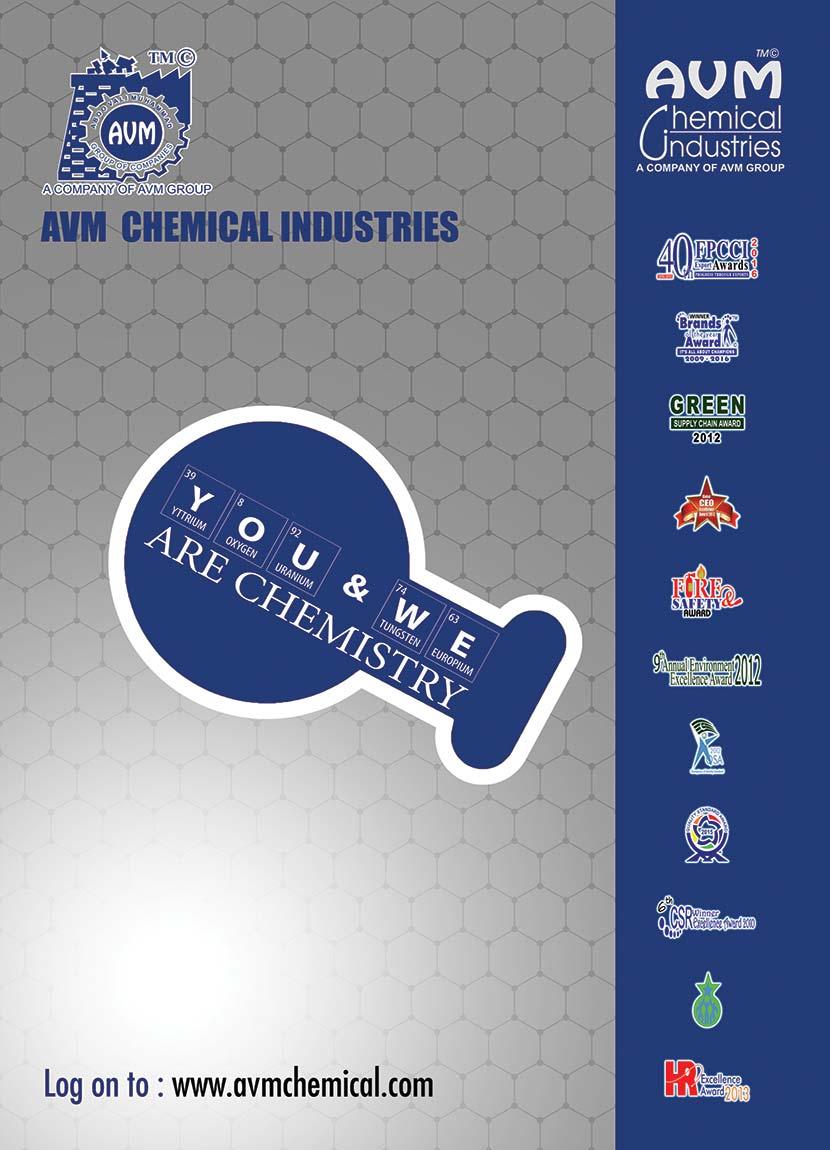
44 minute read
We are hopeful and reasonably confident that textile business will flourish with the present boom.” . . . . . . . . . . . . . . . . . . . . . . . . . . . . . . . . . . . . . . .3
EDITOR’S PAGE
Value added textile exports must retain the growth momentum
Advertisement
The value-added exports of knitwear and bedwear fell 13% and 1.2% year-on-year, respectively. The downtrend was mainly due to the downbeat value-added sector that is a key to drive exports growth. In February, basic textiles exports – cotton yarn, cotton cloth, noncotton yarn, and raw cotton increased 13% month-on-month. However, the value-added sector and other textiles witnessed a decline of 11% and 10%, respectively.
The exports declined 6.7% in dollar terms and 7.3% in rupees term while cotton yarn increased 40% month-on-month to $120 million. This increase in raw material exports is indicative of the post covid recovery of competing economies. The value-added sector is demanding a moratorium on yarn exports as without an abundant supply of local raw material, enhanced export targets cannot be met. Within the value-added segment, knitwear, bedwear, towel and ready-made declined 10%, 7%, 11% and 15% respectively in February 2021 as compared with January 2021. The value-added sector for the first eight months of 2020-2021 witnessed an increase of 12% to $6.9 billion.
While there is a decline in exports of value-added textiles, a major part of exports remain in this higher quality and better-priced segment led by the knitwear sector and followed by readymade garments bedwear and towels.
The momentum gained by the textile exporters in making inroads in established and new markets must continue. The current issue as in the past is devoted to Switzerland. The highlight of the issue is a special report on Archroma Pakistan, the global chemical leader from Switzerland that continues making waves through innovative developments such as Aniline free denim that are contributing significantly to the global sustainability initiative. Mr Mujtaba Rahim, the Managing Director and CEO of Archroma Pakistan shares his views on how Pakistan can help retain the edge in value-added textiles achieved through hard work and perseverance.
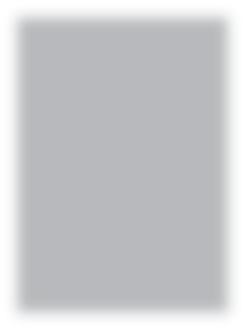
Knitwear
Readymade Garments
Bedwear
Cotton Cloth
Cotton Cloth Towels
Made-up articles Other Textile Materials
Synthetic Textiles Tents Canvas & Tarpaulin Yarn other than Cotton Textile Exports February 2021 (000 US$)
0 50000 100000 150000 200000 250000 300000
Established 1951
March 2021 Swiss Review
March 2021
1The cotton production in Pakistan has plunged 34% to 5.57 million bales (of 155 kg per bale) in the current fiscal year 202021 compared to the same period of last year. This output was in line with the full-year production estimated at a four-decade low in the ongoing year.
2The Chinese Ambassador to Pakistan Nong Rong has said that the startling success of Challenge Textile Factory with the Chinese investment of $60 million has paved the way for numerous investments under CPEC.
3Pakistan Readymade Garments Manufacturers & Exporters Association (PRGMEA) has called for the final approval of the new textile policy 2020-25 by the Economic Coordination Committee (ECC) of the Cabinet as it is vital for new investment and marketing plan in this major export-oriented sector.
4The July-February figures showed that growth in textile and clothing exports came from the value-added sector. The value of exports reached US$ 9.99 billion in the July-Feb period this year as against US$ 9.37 billion over the corresponding months of last year, showing a growth of 6.69%.
5Exporters are demanding that the textile industry should be provided electricity at 7.5 cents per unit for five years and the subsidy issue should be resolved between the Power Division, Petroleum Division and Finance Division but not through additional DLTL on gas and electricity.
6The Khyber Pakhtunkhwa Textile Mills Association (KPTMA) has rejected the decision of the federal cabinet committee on energy (CCoE) to place a moratorium on the supply of gas to textile units for selfgeneration of electricity.
7The government has withdrawn a 5% regulatory duty (RD) on the import of cotton yarn. The Federation of Pakistan Chambers of Commerce and Industry (FPCCI) said the move would greatly support the textile sector and contribute to economic stability.
8German Consul General Holger Ziegeler has advised Pakistan to pivot from traditional exports and promote high valueaddition by utilising human capital and developing industries.
9Sapphire Textile Mills and Britain-based Carrington Textiles have formed a joint venture in Pakistan – Carrington Textiles International, with new textile dyeing and finishing operations in Lahore that would provide up to 20 million meters a year of dyed and grey fabric.
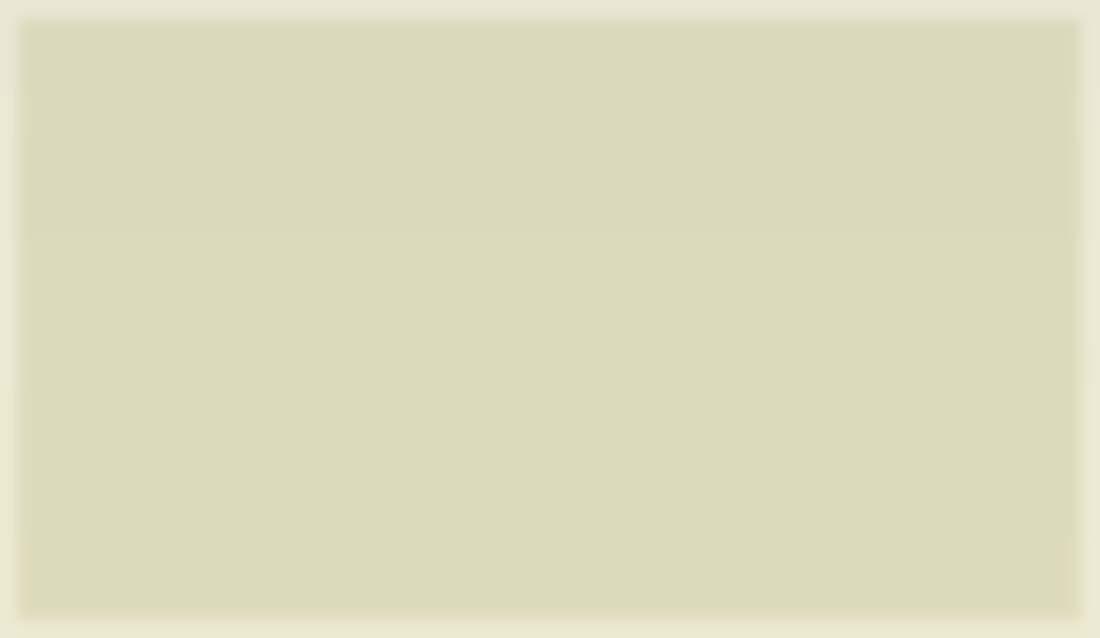
Textile Briefs International

1The Australian cotton industry is seeking to substitute in South East Asia its 611 million Australian dollars cotton trade to China. Australia’s cotton industry is entirely dependent on exports and China is one of the country’s main markets. The cotton industry is one of Australia’s most important contributors to the agricultural sector, with yearly exports worth around US$ 2 billion.
2One of the leading apparel manufacturers in Bangladesh, Maksons Group is going to set up three industrial units at the Bangabandhu Sheikh Mujib Shilpa Nagar (BSMSN) in Mirsarai at a combined investment of US$ 111 million. 3The US companies are ready to offer expertise and systems, including those to reduce congestion and boost efficiency, to improve the infrastructure at the Chittagong Port, according to the US Embassy in Dhaka JoAnne Wagner.
4China´s export growth spiked to the highest of 60.6% in over two decades on-year in the January-February period, well above analysts´ expectations, while imports rose 22.2%.
5Being Europe’s largest producer of cotton with more than 45,000 registered cotton farmers Greece is going to promote more sustainable Greek cotton cultivation. Which makes them able to sell their cotton as Better Cotton from the 202021 cotton season. 6Being Europe’s largest producer of cotton with more than 45,000 registered cotton farmers Greece is going to promote more sustainable Greek cotton as “Better Cotton” from the 2020-21 cotton season.
7The Southern India Mills’ Association (SIMA) has appealed to the Prime Minister for withdrawal of the 10% import duty on raw cotton that was previously allowed to be imported duty free.
8The Clothing Manufacturers Association of India (CMAI), the apex association of the apparel industry of the country has hailed the announcement on setting up of seven mega textile parks in the Union Budget. 9More efforts have been made in South Africa to localise the production of personal protective equipment (PPE) to boost the retail, clothing, textile, footwear and leather (RCTFL) sectors in light of the devastating effects of the COVID-19. 10Vietnam textilegarment exports set to fall 15% to US$ 34 billion Exports to the US and European markets will continue to face difficulties due to a shortage of orders, according to Vietnam’s Ministry of industry and trade, which recently said in a report that the 15% decrease in exports is, however, still lower than the 20%-25% plunge in global demand this year.
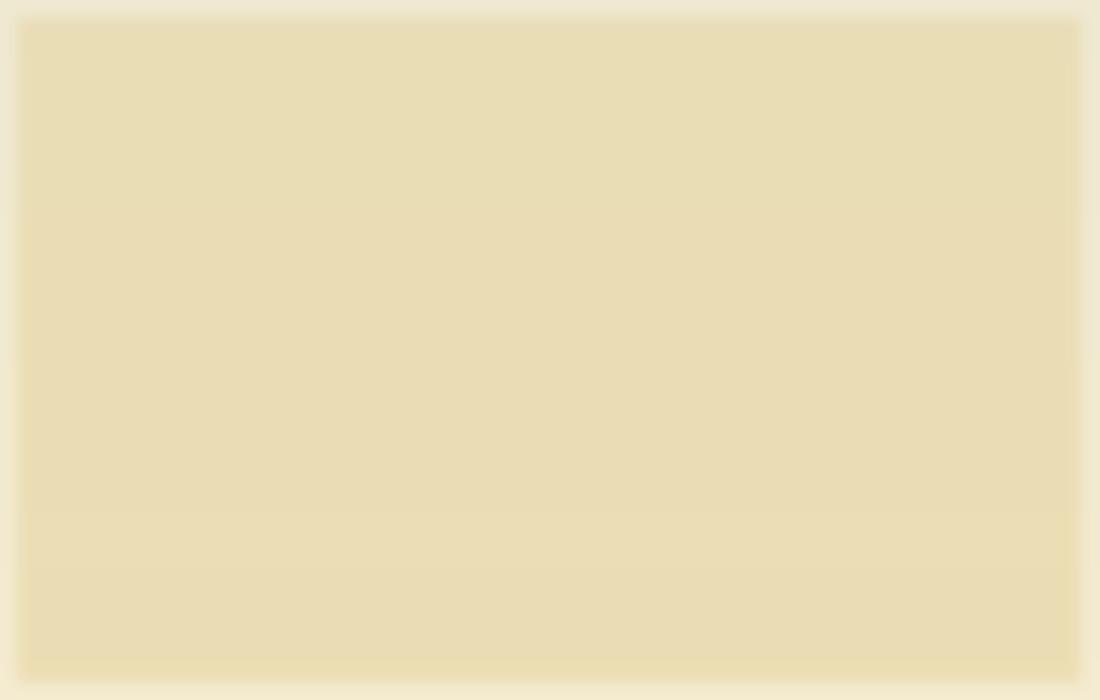

Industry decries the absence of policy to boost cotton output
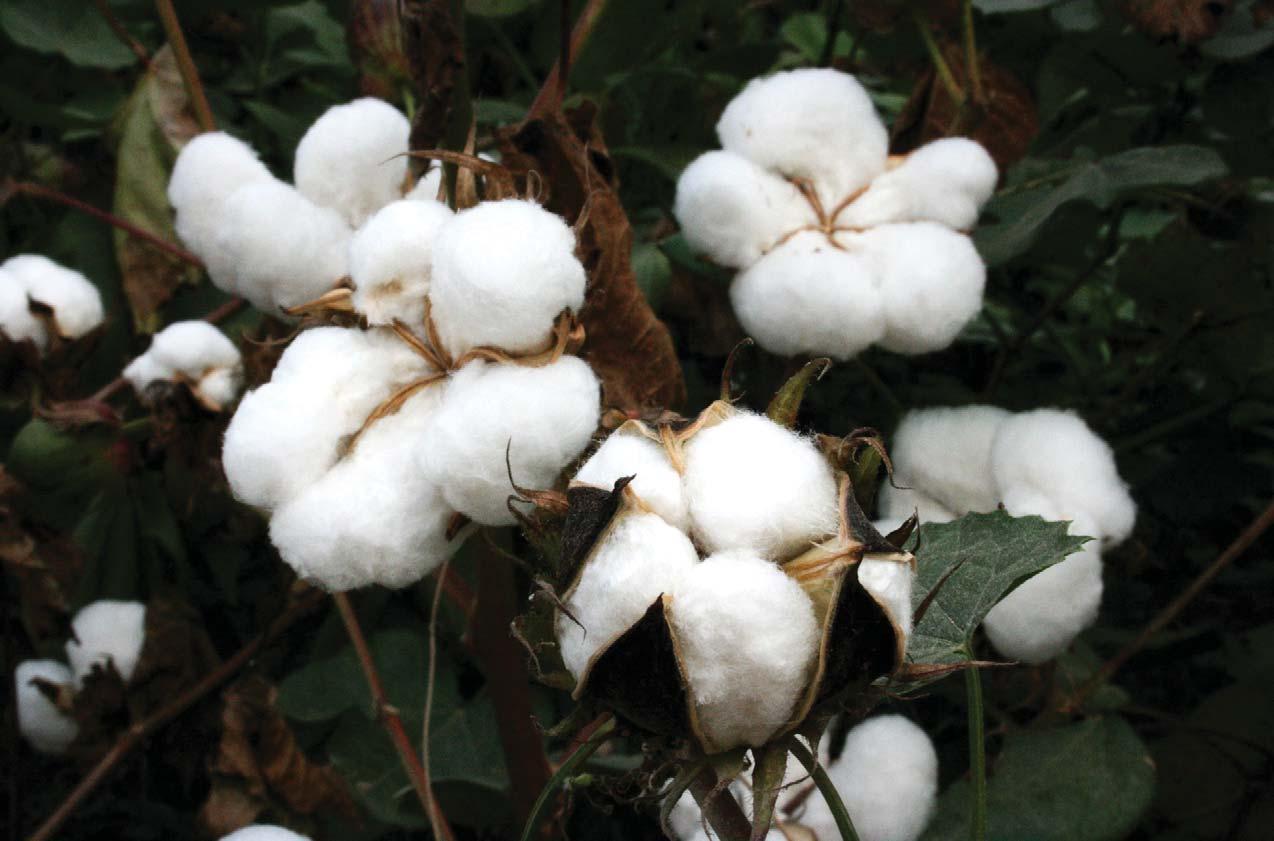
The textile industry has termed it unfortunate that no concrete policy to enhance cotton production has been announced by the government while the price of cotton has soared to an 11-year high of Rs12,000 per maund.
Pakistan Hosiery Manufacturers and Exporters Association (PHMA) Zonal Chairman Faisal Mehboob Sheikh and Chief Coordinator Adil Butt noted that Pakistan was expected to produce 5.6 million bales of cotton in the current season, which would be the lowest in the last 30 years.
On the other hand, demand from the textile industry stood at 18 million bales, hence, over 8 million bales worth $4 billion had to be imported, they pointed out. According to Sheikh, the reason behind the unprecedented increase in cotton prices was the steep decline in its production and bullish trend in the international market.
He appealed to Prime Minister Imran Khan to immediately formulate a strategy to overcome the cotton yarn crisis so that thousands of workers could continue to work in the largest export-oriented industry of Pakistan.
Exporters, spinners spar over yarn imports from India
While the value-added sector terms the situation as a crisis, spinners insist a false picture is being presented. “As per Customs data, yarn is already being imported from 59 countries,” Chairman of the All Pakistan Textile Mills Association (Aptma) Sindh-Balochistan Asif Inam said. “India’s hostile attitude towards Pakistani products is worrying,” the Aptma representative said.
“The data is strangely fabricated to portray a doom and gloom scenario. There was a slight decline in exports when comparing exports of 28 days of Feb 2021 with 29 days in the same month last year (2020 was a leap year),” he added.
The seven-month data (7MFY21) shows that Pakistan has already imported cotton worth $1.336 billion. The massive imports highlight the cotton shortage in the country, with production at its record lowest level. Mr. Inam said the government should not allow imports of cotton yarn or cotton from India until the “country goes for trade normalization with Pakistan”.
“The value-added garment and home-textile industries are facing jeopardy in the wake of unavailability of cotton yarn and abrupt decrease in the value of rupee against the dollar,” said Pakistan Apparel Forum Chairman Jawed Bilwani. “During the past three months, cotton yarn 30/1 prices have been increased by 15pc while it is not available in the market,” he said.
In the last six months, the dollar has also depreciated against the Pak rupee by 5.58pc — down from Rs166.5 to Rs157.2. Exporters previously had negotiated and finalized their export orders at a dollar rate of Rs166.5, Mr. Bilwani said. The fortnightly report of the Pakistan Cotton Ginners Association shows that 72,000 bales of cotton were sold to exporters.
“Cotton prices are high in the market while arrival for this year is almost over. There is a need to import more cotton but more important there is a need for a policy to improve cotton growth with high-quality seeds and increased cultivation area,” said Karachi Cotton Brokers Forum Chairman Nasim Usman.
Chinese envoy visits Challenge textile factory
Chinese Ambassador to Pakistan Nong Rong has said that the startling success of Challenge Textile Factory with the Chinese investment of $60 million has paved the way for numerous investments under CPEC.
He expressed these views during his visit to $60 million Challenge Textile Factory on Lahore-Multan Road where he was briefed by Karen Chen, managing director of the company. The ambassador said Pakistan and China are not only neighbours but also brothers and after CPEC, Pakistan has gained historical significance, as China now see many investment opportunities that will create thousands of jobs in Pakistan.
More Chinese companies are ready to invest billions of dollars in various sectors in Pakistan, which will see an improvement in Pakistan’s economy. Rong said with the resumption of export of textile products from the factory, Pakistan’s foreign exchange reserves will also increase.
Later, the ambassador visited various sectors of the textile factory and appreciated the arrangements made.
Chen briefed him on the investment in the textile sector. Employees have been provided with good pay, as well as transport, food and accommodation, he said, adding that after the $60 million Chinese investment, the group will now invest another $150 million in textiles.
In Phase one in only eight months, they have been able to establish a 370,000 square feet stitching facility that houses 4000 employees. Through this new facility, their exports are already going up to $70 million from $45 million last year, and are estimated to go up to $100 million next year if work continues at this rate.
The group deals mostly in outdoor and sports apparel, and has been in the technical circular knit business for two decades, starting out in 2001. In China, they have been declared one of top three most innovative companies in the textile industry because of their creative product lines. China’s ministry of industry and information technology has also declared them one of the four most sustainable companies in the textile industry.

Duty-free yarn imports demanded to save textile exports
Value-added textile exporters have urged the government to allow duty-free import of cotton yarn to reverse downtrend in exports.
Addressing a news conference, representatives of Council of All Pakistan Textile Association and Pakistan Apparel Forum said they have been drawing the attention of the government, through appeals and press statements, towards unavailability and shortage of cotton yarn – which is the basic raw material – for the last five months.
If cotton yarn’s duty-free import is not allowed, exporters will go for countrywide protests, they said without elaborating whether or not protest implies shutdown of factories.
Value-added textile contributes to around 62 percent in total exports, provides 42 percent urban employment particularly to female workforce, earns highest foreign exchange and supports approximately 40 allied industries.
Zubair Motiwala and Jawed Bilwani said 4.5 percent decrease in exports endorses the viewpoint of exporters that unavailability of cotton yarn would hurt the export orders, which will further be diverted to other competing countries if the cotton yarn is not made available in the required quantity.
Exports fell 4.5 percent year-on-year to $2 billion in February after maintaining the growth pace for five months.
They cautioned the government about the dire consequences of not allowing duty-free import of cotton yarn and not banning export of cotton yarn to save the exports, industries and employment.

Mohammad Zubair Motiwala
Sapphire Textile Mills and Britainbased Carrington Textiles have formed a joint venture in Pakistan – Carrington Textiles International, with new textile dyeing and finishing operations in Lahore that would provide up to 20 million meters a year of dyed and white fabric.
“Sapphire Textile Mills has agreed to form a Joint Venture (JV) with Carrington Textiles, a British company. Both the companies will combine their strength in manufacturing, marketing and research and development to bring value to the customers. The JV will be formed in United Kingdom,” a bourse filing said.
Carrington Textiles noted in a statement that a new production facility, now in operation, had some of the most modern European dyeing and finishing plant and machinery, which would further enhance the capabilities of the JV.
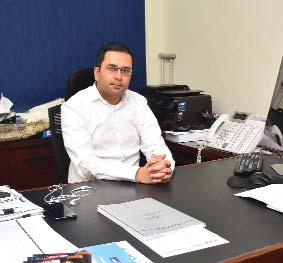
“With the closeness to Sapphire’s existing spinning and weaving operations, as well as to other existing local suppliers, this adds to the ability of Carrington Textiles International to provide a vertically integrated manufacturing solution, reducing lead times and further enhancing service to customers. Finished stock will be warehoused in Lahore, Asia and the South African port of Durban, ensuring the best possible service to all major markets.”
This new venture with Sapphire Textile Mills would increase Carrington’s capacity to 130 million square meters a year. It is the start of a series of investments that Carrington Textiles’ parent company, the RTS Group, is implementing across the rest of its production facilities.
Nabeel Abdullah, Sapphire’s COO says, “Carrington Textiles International is an excellent project we are excited to be part of, and we are pleased our longstanding relationship with
Carrington Textiles has developed into this joint venture.” Carrington Textiles’ CEO John
Vareldzis said, “Following years of working closely with Sapphire as one of our strategic loomstate suppliers, we have made the next logical step together and invested in a new state of the art dyeing and finishing factory in Lahore.”
He said this not only gave Carrington its own European engineered manufacturing plant in Asia, but also would provide access to a vertical operation, from spinning through to weaving, dyeing and finishing.
“All of the dyeing and finishing machinery has been specified by our technical experts to meet the exacting standards of the work-wear market and we are confident this integration of our supply chains will help to give our customers the best chance to succeed in a challenging and exciting market,” he added.
Carrington is the largest producer of work-wear fabrics in the UK, exporting to more than 80 countries worldwide. Carrington produces over 55 million meters of fabric annually.

Decision to suspend gas supply to textile mills rejected
The Khyber Pakhtunkhwa Textile Mills Association (KPTMA) has rejected the decision of the federal cabinet committee on energy (CCoE) to place moratorium on the supply of gas to textile units for self-generation of electricity.
The decision was made at a meeting recently with Salim Saifullah Khan in the chair. The meeting rejected the CCoE decision to curtail the supply of gas to the export-oriented textile industry and divert the gas supply to the IPPs for power generation.
The KPTMA urged Chief Minister Mahmood Khan, the federal energy minister, the PM’s special assistant, the chief minister’s adviser on energy & power and the provincial chief secretary to intervene to resolve the issue.
The association also stressed the need for taking up the issue with the Council of Common Interest.
Briefing media persons after the meeting, Salim Saifullah showed his serious concerns over the adverse effects of the decision on textile industry, and asked government to review it. He urged the Khyber Pakhtunkhwa government to intervene in the matter, otherwise the mills would close down their operations, and large scale workers would lose jobs.
He warned the government that such unsolicited decision would result in high cost of production, unemployment, loss of investment and decline in export of textile products.
He further said it would also be a challenge for the government to provide uninterrupted electricity to the industry as available grid stations were already overloaded.
Mr Saifullah said shifting of manufacturing units to Wapda electricity was also not possible on such short notice. He suggested the government in consultation with stakeholders devise some workable plan if implementation of the decision was necessary.
Salim Saifullah.
Germany advises Pakistan to learn from neighbours for exports
German Consul General Holger Ziegeler has advised Pakistan to pivot from traditional exports and promote high value-addition by utilising human capital and developing industries.
In a recent meeting he said Pakistan has been sending mostly textile, leather and some other products to Germany. It must make good use of human capital, develop industries and produce highvalue products for more exports to Germany and other countries, he said.
“You must look at the region and see how your competitors like Bangladesh and others have improved their exports to Germany and other countries,” Ziegeler said during a meeting with the officials of the Karachi Chamber of Commerce and Industry (KCCI).
“Pakistani exporters should not confine to producing raw material or semi-finished goods for exports but they must also be able to produce all classes of the entire value-chain of not just textile sector but other sectors as well,” he said.
“We are also suffering right now from the absence of trade fairs and limited possibilities of travelling.
“Joint ventures between the business communities of Germany and Pakistan are possible as soon as we start visiting again. We have to deal with the first step which is the fear of entering into Pakistan due to security concerns. I will try my best to bring German businessmen and once they are here, it’s your game to make them partners.”
Prior to assuming charge as Consul General in Karachi, he served as Consul General in Jeddah for four years and before that he was head of Export Promotion at the ministry of foreign affairs in Berlin and then preferred to get posted in Karachi because of the economic importance of the port city and because of the potential this city has for development of bilateral trade with Germany.
KCCI President Shariq Vohra stressed the need for joint ventures in agricultural and automotive sectors. Most of the agricultural products being harvested in Germany are also farmed in Pakistan. German business community must come forward, improve ties and explore investment opportunities in Pakistan.
“Unfortunately, we have not been able to take advantage of what is being offered which is something that needs special attention,” Vohra said.
He also appreciated Germany’s constant support to Pakistan in the form of aids and grants for various socioeconomic development projects and also the vocational training initiatives which helped a lot in further improving the skills of Pakistani workforce and proved favorable for the economy.
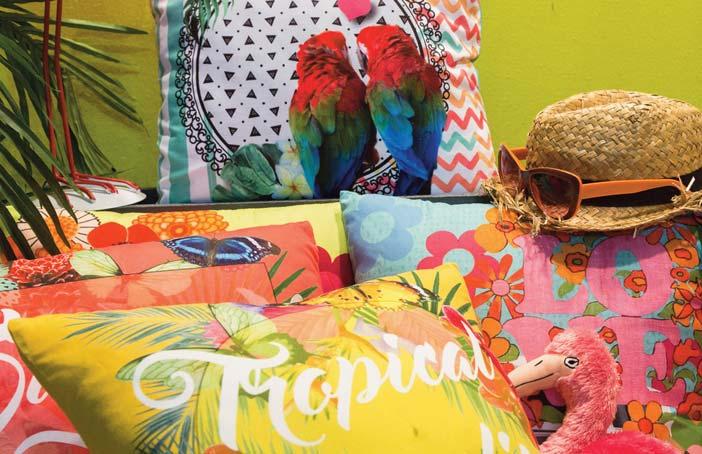
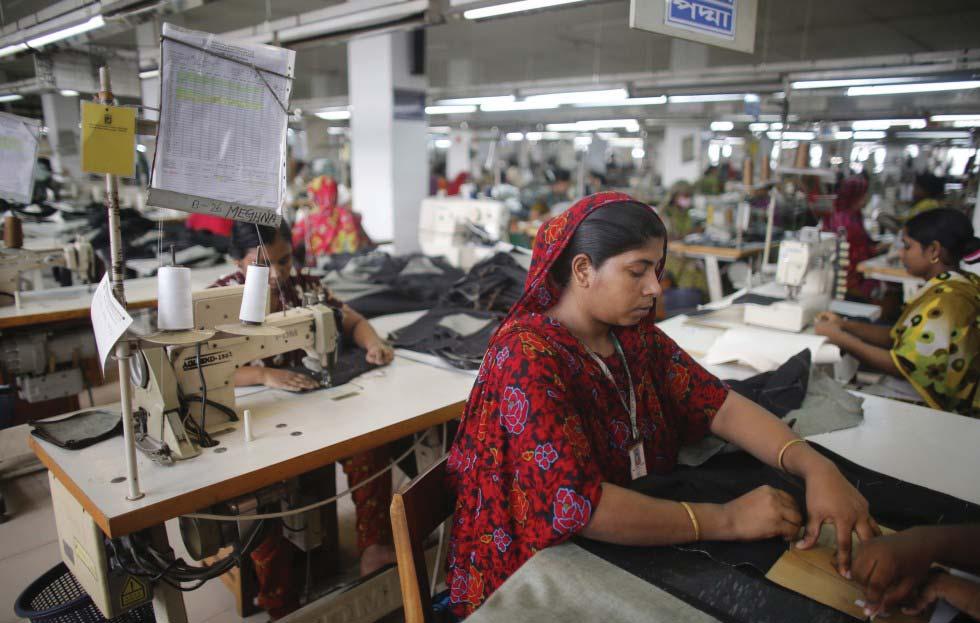
AUSTRALIA
Australia seeks alternative market for its cotton in South East Asia
The China and Australia relationship continues to worsen, after year-long rhetoric of indirect allegations, declining common trust and repressed trade agreements. The Australian cotton industry is seeking to substitute in South East Asia its 611 million Australian dollars cotton trade to China.
Australia’s cotton industry is entirely dependent on exports and China is one of the country’s main markets. The cotton industry is one of Australia’s most important contributors to the agricultural sector, with yearly exports worth around US$ 2 billion. Australia is one of the world’s top four cotton exporters, competing in a deeply subsidized international market.
In a recent opinion piece for ‘Queensland Country Life’, Michael O'Reilly, chairman, Chairman, Australian Cotton Shippers Association, says that the industry needs to move on, which “means reviving established markets and growing markets where consumption of Australian cotton is smaller.”
Australian cotton earned its reputation as a reliable supplier of highquality fibre in the tradition markets such as South Korea, Japan, Indonesia and Vietnam. Unlike China, India, or Pakistan, these traditional markets for Australian cotton do not have any source of local production, making them completely dependent on imported cotton.
Japan and South Korea remain significant purchasers of Australian cotton, according to O’Reilley, even if they have seen their respective spinning companies relocated to other more competitive markets including Indonesia, China and Vietnam.
Though the number of spinning companies in Indonesia and Thailand demanding Australian cotton has declined since the late 1990s, these markets still recognize and appreciate Australian cotton’s quality.
Australian cotton must compete with Brazil and US cotton not only in Indonesia but also in Vietnam, another potential expansion market.
BANGLADESH
Maksons invests US$ 111 million in Bangabandhu economic zone
One of the leading apparel manufacturers in Bangladesh, Maksons Group is going to set up three industrial units at the Bangabandhu Sheikh Mujib Shilpa Nagar (BSMSN) in Mirsarai at a combined investment of US$ 111 million.
Mohammad Ali Khokon, Managing Director of Maksons Group and three other concerns under the group, signed a land-lease agreement with the Bangladesh Economic Zones Authority (Beza) in Dhaka to establish the units on 30 acres of land by 2022.
Metro Spinning Ltd will invest US$ 40 million and create jobs for 1,200 people. Maksons Spinning Mills Ltd. will invest US$ 30 million to create 800 jobs. Also, another unit of the Group will invest US$ 41 million.
Maksons Group will produce fabric and export-oriented apparel items at the proposed industrial units. The group has a target to start production by 2022.
US ready to help improve Chittagong Port infrastructure
The US companies are ready to offer expertise and systems, including those to reduce congestion and boost efficiency, to improve the infrastructure at the Chittagong Port, according to the US Embassy in Dhaka JoAnne Wagner.
Wagner said the US Trade and Development Agency is eager to support infrastructure projects in high-growth emerging markets such as Bangladesh with feasibility studies, technical assistance and pilot projects.
Wagner visited Chittagong recently to support the robust economic partnership between Bangladesh and the United States. She discussed expansion plans for the Chittagong Port, including opportunities for participation by US companies; engaged with female entrepreneurs pursuing successful businesses and overcoming gender discrimination; and explored further opportunities with the operators of Pahartali Textile and Hosiery Mills for using US-grown cotton.
CHINA
China exports rise to highest in two decades after coronavirus hit
With imports sharply bouncing back from the coronavirus outbreak, China´s export growth spiked to the highest in over two decades.
Exports spiked 60.6% on-year in the JanuaryFebruary period, well above analysts´ expectations, while imports rose 22.2%. The latest figures stand in stark contrast to last year´s fall of around 17% in exports and 4% drop in imports. The country struggled to contain the spread of Covid-19 early on, with consumers staying home and businesses seeing a slow return to operations.
Electronics and textile exports such as masks contributed to the spike in outbound shipments, as demand for work-from-home supplies and protective gear against the virus outbreak soared during the pandemic.
EGYPT
Absence of indicative price affects cotton sowing in Egypt
The Egyptian government has been announcing an indicative price for buying cotton before the planting season commenced every year in the past. However, for the first time, the government had not announced indicative prices in the current year. This has affected cotton cultivation in 2020-21, which is expected to decline 35% to 65,000 hectares.

The indicative price was a subtle attempt by the Egyptian government to urge the textile industry to buy cotton from farmers at the indicative price, However, it was not priced support or commitment from the government to buy the crop.In MY 2020-21, the total cotton area harvested in Egypt is expected to decrease by approximately 35% to 65,000 hectares (ha), from 100,000 ha in MY 2019-20.
The low cotton prices were another reason for farmers sowing less cotton. In MY 2019-10, price averages were US$ 133 per 50 kg of lint cotton to US$ 146 per 50 kg of lint cotton for extra-long varieties and US$ 120 per 50 kg of lint cotton to US$ 133 per 50 kg of lint cotton for long-medium staple cotton.
In MY 2020-21, cotton consumption of Egypt is expected to plunge by 5,000 bales to 6,25,000 bales, a drop of 1% over last year attributed to lower domestic demand due to a decrease in demand from public spinners.
GREECE
Greece has entered into ‘The Better Cotton’ era
The Better Cotton Standard System has decided that the Greek AGRO-2 Integrated Management Standards will equally run with the Better Cotton Initiative (BCI)’s Better Cotton Standard System (BCSS).
Being Europe’s largest producer of cotton with more than 45,000 registered cotton farmers Greece is going to promote more sustainable Greek cotton cultivation allowing them to sell their cotton as Better Cotton from the 202021 cotton season.
By the end of 2022, it is estimated that 5,000 farmers will grow AGRO-2 licensed cotton (equivalent to Better Cotton), on 270,000 hectares, producing around 185,000 bales covering 10% of the total agricultural land.
The Greek cotton producer complies for several years with high environmental and social ISCC (International Sustainability & Carbon Certification) to achieve a reduction in water and pesticide use while increasing yields and profits. Because thirteen of the world’s biggest clothing and textile companies signed a pledge to source 100% sustainable cotton by 2025 in a deal brokered by the UK’s Prince of Wales.
INDIA
SIMA appeals for withdrawal of import duty on cotton
Stating that the imposition of 10% import duty on cotton is a severe blow for the cotton textile value chain, the Southern India Mills’ Association (SIMA) has appealed to the Prime Minister for withdrawal of the duty. However, it has hailed the announcement of MITRA scheme aiming at developing seven mega textile parks with plug and play facility.
India has been globally competitive only in the cotton textile manufacturing, thereby accounting for 80% of its total exports. As per Union Budget 2021-22, cotton and cotton waste which is currently under nil rate of import duty is being subjected to 10% import duty through the budgetary announcement comprising of 5% Basic Customs Duty and another 5% Agriculture Infrastructure and Development Cess (AIDC) on cotton and 10% BCD on cotton waste. The new import duty comes into effect from February 2, 2021. This has come as a severe blow for the ailing cotton textiles and apparel industry, said SIMA chairman Ashwin Chandran.
He appealed to the Prime Minister to immediately withdraw the levy of 10% import duty on cotton and cotton waste to sustain the global competitiveness of Indian textiles and apparel industry and prevent job losses for several lakhs of people, prevent fall in the exports and also curb cheaper imports of value-added products from the SAFTA countries like Bangladesh, Sri Lanka, etc.
Seven mega textiles parks highlight of Budget
The announcement on setting up of seven mega textiles parks is the highlight of the Union Budget 2021-22, directly impacting the textile industry according to The Clothing Manufacturers Association of India (CMAI), the apex association of the apparel industry of the country. Several announcements impacting consumer spending will also help the apparel sector.
The increase of import duty on cotton and cotton fibre may not impact the industry too adversely, since the current imports are at a miniscule level. However, this does come at a time when the industry is reeling from an unprecedented increase of raw material prices, especially yarn, and could send a wrong signal.
In an indirect manner though, the Budget has made several announcements which will have a positive impact on consumer spending such as increases in infrastructure and overall government expenditure – and this will help the industry, especially the apparel sector.
The textile industry welcomed the Union Budget presented by Finance Minister Nirmala Seetharaman, particularly the announcement on textile and apparel parks. In a statement, the Indian Texpreneurs Federation (ITF) appreciated the thrust given to the textile
sector by proposing the seven mega integrated textile region and apparel parks (MITRA).
With the concept of the parks with a plug-and-play model, the textile and apparel sector, particularly the SMEs (small and medium enterprises), can build competitiveness in manufacturing, ITF convenor Prabhu Dhamodharan said in the statement. Further, the parks can be aligned with environmental, social and governance goals to attract international buyers as well as investors, he said.
Welcoming the budget, president of Tirupur Exporters Association Raja M Shanmugham termed it as a pragmatic one presented to address all issues in the sectors. While appreciating the parks scheme, he said as expected, this would create global champions in exports and was hopeful that Tirupur exporters would opt to set up the units in the parks. He thanked the government for allotting Rs 700 crore for the Amended Technology Upgradation Scheme (ATUFs) against Rs 545 crore in the last budget which, he said, would help clear the pending capital subsidy.
SOUTH AFRICA
SA minimising COVID-19 impact on textile-apparel
More efforts have been made to localise production of personal protective equipment (PPE) to boost the retail, clothing, textile, footwear and leather (RCTFL) sectors in light of the devastating effects of the COVID-19. South African Deputy Minister of Trade, Industry and Competition Fikile Majola informed about these efforts to parliament’s select committee on trade and industry, economic development, small business development, tourism, employment and labour.
He said government is committed to reviving the sector as it focuses on rebuilding manufacturing and to enable it to expand its capacity. He mentioned that the government is working towards significantly reducing illegal imports to eliminate unfair competition against local retailers and manufacturers.
The R-CTFL value chain’s total gross domestic product contribution is R74 billion, while its employment contribution is more than 210 000. The R-CTFL Master Plan was signed in 2019 with seven commitments. These include growing the domestic market, driving domestic sourcing, ending illegal imports and value chain transformation.
During this period of the pandemic specific focus has been placed on intensifying support for products such as surgical and consumer masks, respirators, medical textiles, leather and footwear products, gloves and body bags, according to a press release from the department of trade, industry and competition (DTIC).
VIETNAM
Vietnam textile-garment exports set to fall 15% to US$ 34 billion
Exports to the US and European markets will continue to face difficulties due to a shortage of orders, according to Vietnam’s ministry of industry and trade, which recently said in a report that the 15% decrease in exports is, however, still lower than the 20%-25% plunge in global demand this year. Many companies expect new trade pacts will help boost exports.
Domestic companies have been making efforts to pump up revenue by producing low-value products to ensure cash flow, according to Vietnamese media reports.
HCMC-based Dony Garment is focusing on small orders, including those of masks, whose price is 5%-10% of other products made before the pandemic. The company’s revenues in the first 11 months actually surged 2.7 times year-on-year because of masks.
Vietnam Textile and Apparel Association (VITAS) chairman Vu Duc Giang said the recently-signed Regional Comprehensive Economic Partnership (RCEP) is likely to boost China’s demand for garments made in Vietnam.

Seamless chic swimsuit demonstrates the performance of the new RASCHELTRONIC®
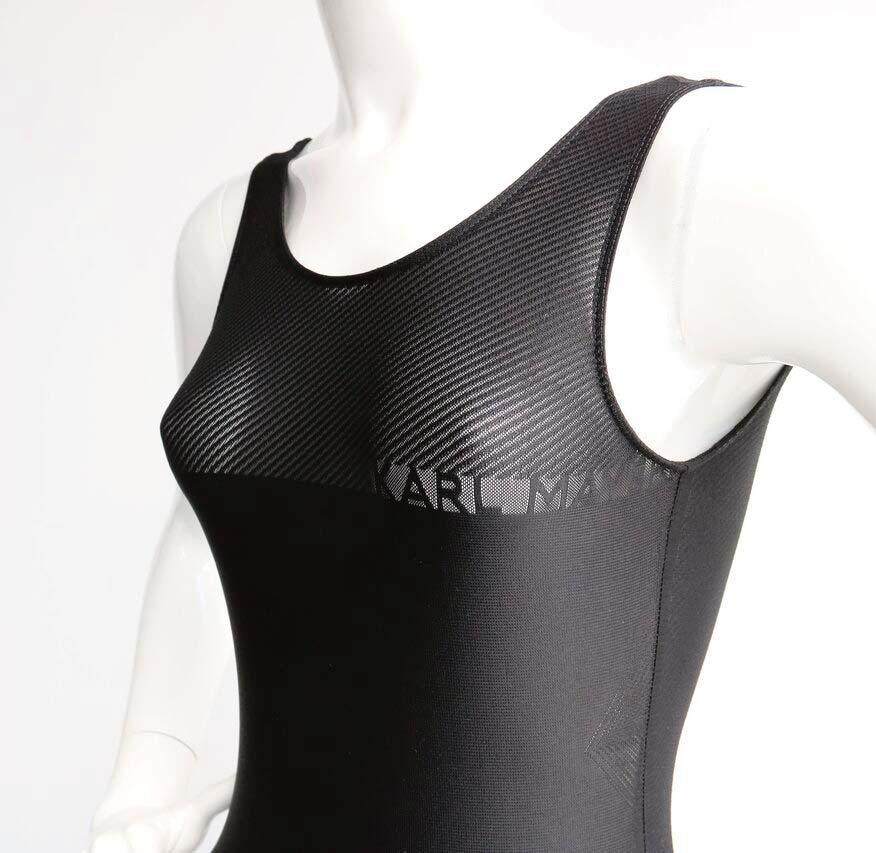
Sunny prospects with the RJ 5/1 N.
Now stylish swimwear from KARL MAYER’s Textile Product Development department shows the potential of this five-bar newcomer.
KARL MAYER is continually adapting its RASCHELTRONIC® range to the needs of the market. With adjusted performance profiles, the efficient raschel machines are intended to give customers
the edge in their usually dynamic business
It was only at the end of last year that the manufacturer launched a highly productive model, the RJ 5/1 N, which sets trends in the production of chic lingerie articles and inelastic, lacelike fabrics. Now stylish swimwear from KARL MAYER’s Textile Product Development department shows the potential of this five-bar newcomer. The RJ 5/1 N can be used to produce typical RSJ articles, such as locknit produced with three guide bars, SpotNet qualities and elastic or rigid Powernet qualities, and to create effective seamless constructions. Front and back parts are produced directly on the machine, into which opaque areas and open pattern parts are alternately incorporated as required, and even lettering is seamlessly incorporated. Appropriately designed leg, neck and back cut-outs can also be integrated and do not require seams thanks to the free-cut design. Only the side seams need to be closed as part of the confectioning process.
However, it is not only the making up that is efficient, but also the textile production itself. The RJ 5/1 N reaches a maximum speed of 1,100 rpm and is therefore just as fast as the previous five-bar RASCHELTRONIC®, the RSJ 5/1. The finished fabric for the swimsuit developed by KARL MAYER was produced at a speed of 12.8 m/h. Like the RSJ 5/1, the new raschel machine also works with four ground bars and one split jacquard bar. The patterning is done by a standard N gear. It is also offered in gauges E 28 and E 32. However, the RJ 5/1 N, which is produced at KARL MAYER (CHINA), is superior to the established model in terms of its price performance ratio. “The RJ 5/1 N is up to 60% better than the RSJ 5/1 in terms of investment per production. We expect that it will become established with customers in the five-bar RASCHELTRONIC® sector,” says Sascha Müller, Product Owner Local Lace & Raschel at KARL MAYER.
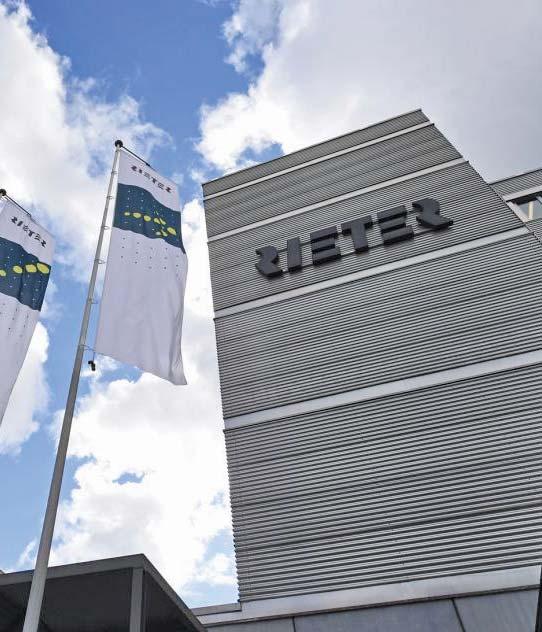
Picanol Group has acquired a minority stake in Rieter Holding AG (SWX: RIEN), amounting to a total of 467,236 shares for a price of 45.4 million EUR (or a price per share of 107.5 CHF).
Rieter is the world’s leading supplier of systems for short-staple fiber spinning. The company develops and manufactures machinery, systems and components used to convert natural and man-made fibers into yarns.
As a result of the transaction, Picanol Group is now holding 10% of the share capital of Rieter Holding AG. With the financial participation in Rieter Holding AG, Picanol Group wants to further diversify its activities in the textile industry and secure a stable shareholding for Rieter Holding AG in the long term.
Financial Calendar: Picanol Group will announce its financial results for 2020 on March 25, 2021 (before opening of the stock exchange).
Michael Pieper, a member of the Board of Directors of Rieter Holding AG since 2009, has informed Rieter that Artemis Beteiligungen I AG has sold its 11.5% block of shares to the Picanol Group (Picanol NV), Belgium, and that he thus will not stand for re-election at the Annual General Meeting on April 15, 2021.
Michael Pieper has supported and helped to significantly shape the development of Rieter for more than ten years. He joined Rieter as a major shareholder in 2008, and since then has been strongly involved in the strategic realignment of the group.
“On behalf of the Rieter Group, I extend our sincere gratitude to Michael Pieper for his extremely successful and valuable work on the Board of Directors and, above all, for his commitment as a long-term major shareholder,” said Bernhard Jucker, Chairman of the Board of Directors of Rieter Holding AG.
The Board of Directors of Rieter Holding AG today announced its intention to propose Stefaan Haspeslagh for election to the Board of Directors at the Annual General Meeting on April 15, 2021.
Stefaan Haspeslagh (born 1958) holds a Master’s degree in Applied Economics from the University of Antwerp, Belgium. He has been Chairman of the Board of Directors and Chief Financial Officer of the Picanol Group (Picanol NV), Belgium, since 2010. In addition, Stefaan Haspeslagh has also been Chairman of the Board of Directors, Chief Operating Officer and Chief Financial Officer of the Tessenderlo Group NV, Belgium, since 2014. As a director of Cellpack NV, Belgium, he has been in office since 2001.
“Rieter welcomes the new major shareholder, Picanol NV. Luc Tack, majority shareholder and CEO of Picanol, has been a member of the Board of Directors of Rieter for four years. Stefaan Haspeslagh is characterized by broad, international management experience in the textile sector and is very well connected in the industry”, stated Bernhard Jucker, Chairman of the Board of Directors.
All other current members of the Board of Directors will stand for reelection at the Annual General Meeting.
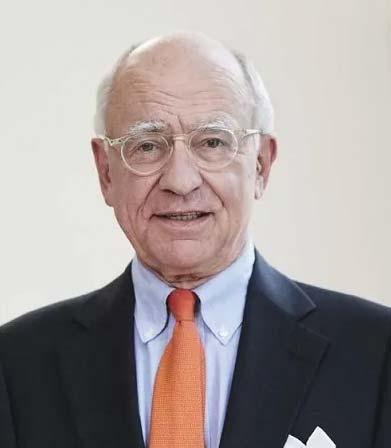
Michael Pieper, a member of the Board of Directors of Rieter Holding AG
Christian Straubhaar – New Head of Sales at Rieter Machines & Systems
Christian Straubhaar took on the position of Senior Vice President Sales at Rieter Machines & Systems in Winterthur on January 1, 2021. Straubhaar succeeded Reto Thom who retires this year.
Christian Straubhaar holds an Engineering Master’s Degree in Industrial Management from the Swiss Federal Institute of Technology in Zurich (ETH) and is a sales executive with 20 years of extensive experience in the textile industry.
Recently, Straubhaar was responsible as Group Sales & Marketing Director at Itema for the world-wide sales of machines and spare parts. Prior, he held various positions in Operations and as Business Unit Head in Itema and other global textile companies.
His professional career shows a solid track record in identifying new market potentials and growing the business for the company. Straubhaar has longstanding experience in selling to both large and small customers and developing key accounts within our industry.
Reto Thom has very successfully led the Sales department at Rieter Machines & Systems for many years and made an enormous contribution to the success of the company.
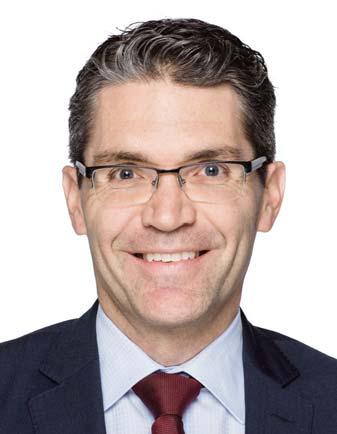
Gerald Vogt as new CEO of the Stäubli Group
Stäubli is one of the leaders in industrial and mechatronic solutions, is starting the new year with a new Chief Executive Officer. Gerald Vogt, previously responsible for the global business of the Robotics Division. He took charge as CEO from Rolf Strebel on January 1, 2021.
With Gerald Vogt, an experienced manager from within the company's own ranks will take over the management of the diversified and growing family-owned company.
The 50-year-old FrancoGerman engineer and business economist has been responsible for the global Robotics business as Group Division Manager since mid2016 and is already a member of the Group Management.
When he joined Stäubli almost 20 years ago, Gerald Vogt initially moved from the development and production site in Faverges, France, to the US for several years.
As Division Manager he significantly expanded business for Stäubli Robotics North America. Afterwards he returned to Faverges as Head of Development before taking over responsibility for the German business as Head of Stäubli Robotics in Bayreuth.
To ensure a smooth transition and prepare for his future tasks as CEO, the Stäubli Board of Directors nominated Gerald Vogt as the designated successor to Rolf Strebel at the beginning of 2020. Since then, Gerald Vogt has accompanied the current CEO and is responsible for the introduction and implementation of the new business strategy for Stäubli until 2030. "We are delighted to have found in Gerald Vogt a forward-looking manager with an extensive international experience and a clear entrepreneurial spirit who is already very well connected within the Group. He has our full confidence to further advance the business of the entire Stäubli Group worldwide," said Yves Serra, Chairman of the Board of Directors. "On behalf of the entire Board of Directors and the Stäubli family, I would like to take this opportunity to thank Rolf Strebel for more than 40 years of dedication to Stäubli and his outstanding work as CEO of the Stäubli Group over the past 14 years. We wish him all the best for the time ahead," added Serra.
Christophe Coulongeat will assume the global responsibility for the Robotics Division on January 1, 2021. The French manager has been Deputy Division Manager since 2018 and previously gathered extensive experience in the packaging and automation industry in France, Austria, the United Arab Emirates and Switzerland.
With this succession in management, Stäubli is setting the course to consistently pursue its growth and further expand its market position worldwide, especially in North America and Asia.
Gerald Vogt becomes new CEO of Stäubli Group.
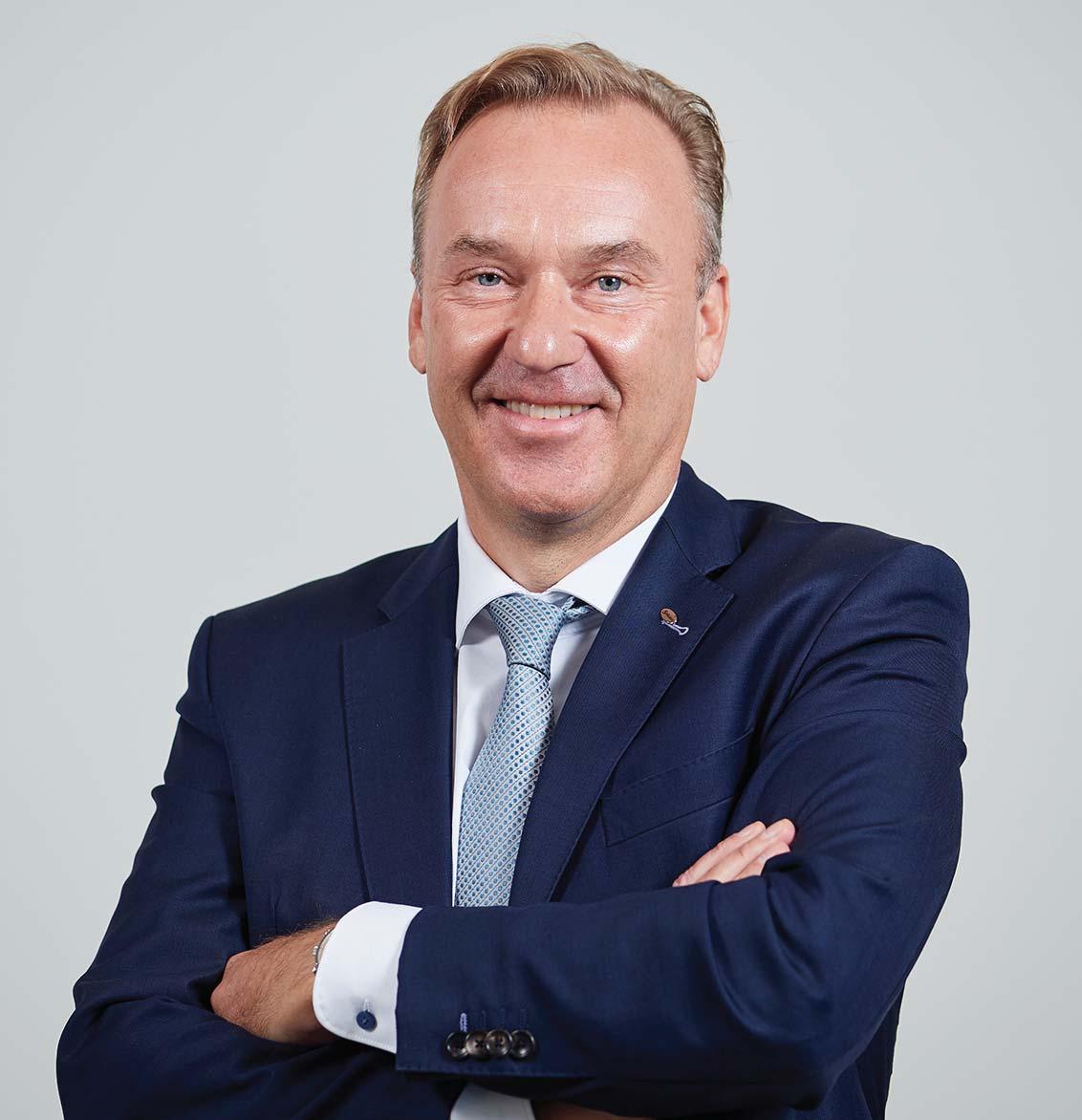
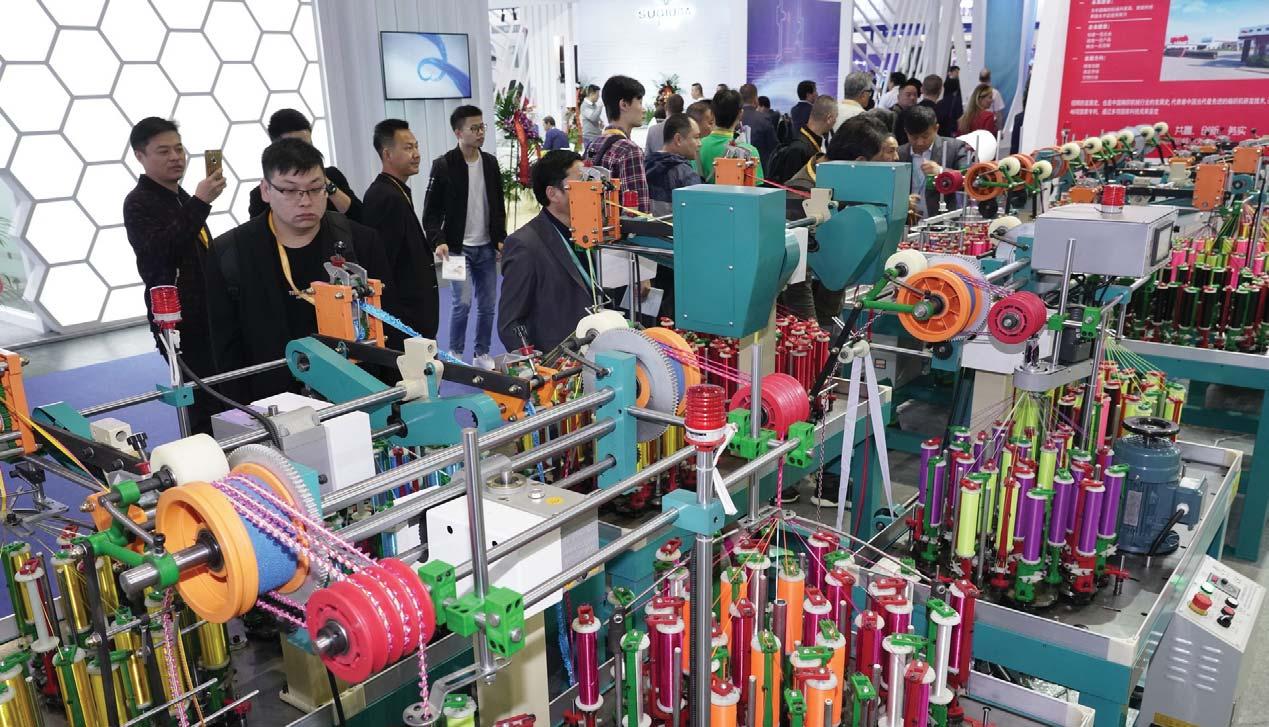
Online visitor registration for ITMA Asia + CITME 2020 which will be held during 12 to 16 June 2021 at the National Exhibition and Convention Centre (NECC) in Shanghai is now open.
Visitors who purchase their badge at www.itmaasia.com and www.citme.com.cn will enjoy special online rates. Early-bird rates available till 6 June are RMB 60 for a five-day badge and RMB 30 for a one-day badge. Standard onsite rates cost RMB 100 for a five-day badge and RMB 50 for a oneday badge. Visitors who register online will be also given access to the exhibition e-catalogue.
The show owners and organisers are committed to working closely with the authorities, such as the Joint Prevention and Control Mechanism of the State Council and the Shanghai Convention and Exhibition Industries Association (SCEIA), to implement preventive and social distancing measures to enable the combined exhibition to be held safely.
“We would like to assure that the safety of our participants, partners and staff during the exhibition is of utmost importance to us. Strict safety measures will be implemented onsite. Visitors should purchase their badge online to avoid onsite queues and allow better and smooth entry process,” urged Mr Ernesto Maurer, President of CEMATEX.
“Taking into consideration the needs of the industry, we have decided to continue with the staging of the combined exhibition. Since the certificate of admission and stand details were issued last December, many exhibitors have responded positively to the news that the combined exhibition will be staged as planned,” said Mr Wang Shutian, Honorary President of China Textile Machinery Association (CTMA).
He added, “The pandemic has created pent-up demand for quality machinery for sectors such as nonwovens and technical textiles as there was a lack of sales and marketing opportunities last year. Therefore, our machinery manufacturers are eager to reconnect with the market.”
Despite the ongoing Covid-19 challenge, the seventh edition of the combined exhibition is expected to feature a gross exhibition space of 170,000 square metres. To-date, it has attracted the participation of 1,500 exhibitors, including many established machinery manufacturers from 24 countries.
ITMA ASIA + CITME is owned by CEMATEX and Chinese partners - the Sub-Council of Textile Industry, CCPIT (CCPIT-Tex), China Textile Machinery Association (CTMA) and China Exhibition Centre Group Corporation (CIEC), and organised by Beijing Textile Machinery International Exhibition Co Ltd and co-organised by ITMA Services. Japan Textile Machinery Association is a special partner of the combined show.
The last combined show in 2018 attracted 1,733 exhibitors from 28 economies and registered a visitorship of over 100,000 from 116 countries and
regions.
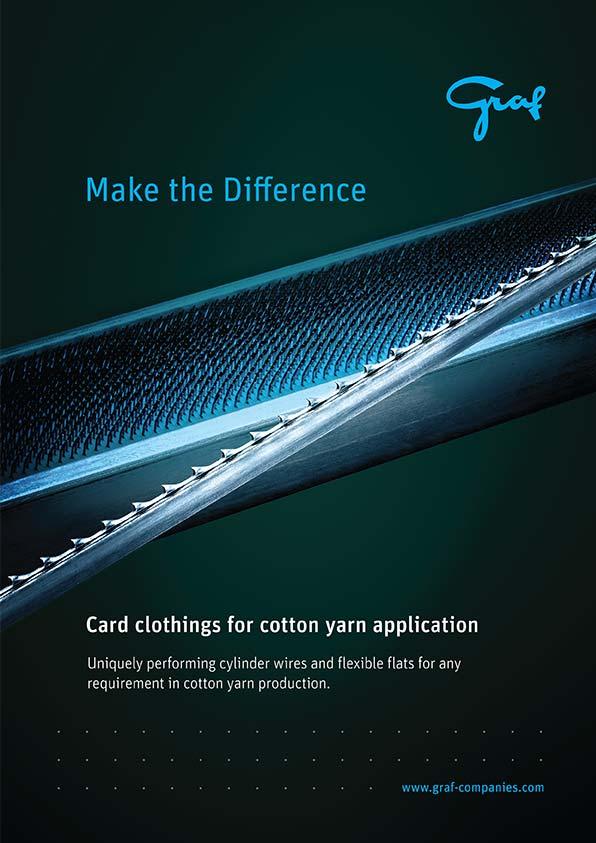
Imtiaz Rastgar.
CECA conducted skill training under UniversityIndustry Linkage Program
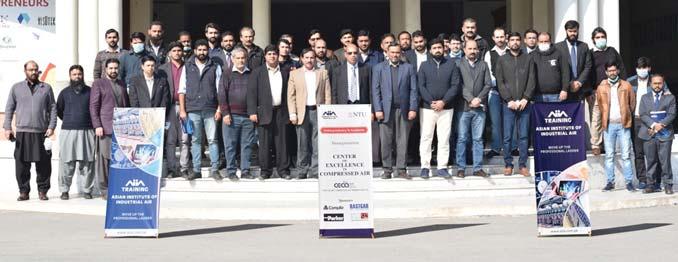
National Textile University Faisalabad established (CECA) Center of Excellence in Compressed Air for capacity building of Industry professionals as well as university faculty and students on Industrial Air Engineering and relevant topics in collaboration with the Asian Institute of Industrial Air. Participants from 19 different public and private sector organizations participated in one Day Professional Training Course on “Understanding of Compressed Air Systems” held on January 27, 2021.
CECA, Centre of Excellence in Compressed Air training facility was inaugurated on 16th October 2020.
Compressed Air is the most important but least understood utility in the textile sector. Realizing the needs of this important knowledge, CECA organized a oneday Professional Certificate course on “Understanding of Compressed Air Systems”. Industry Expert trainers having a strong practical background in maintenance management of Industrial compressors provided an in-depth understanding of compressors and compressed air-related issues faced by the technical managers.
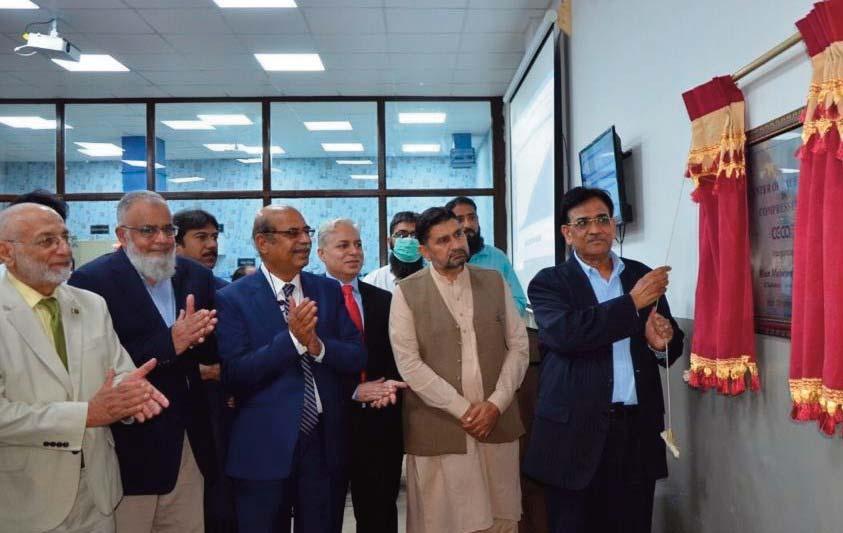
CECA has published an annual training calendar for a series of the training program which will cover the complete domain of compressors and compressed air systems.
The training calendar also includes the training programs related to manufacturing processes and other technologies.The next two days Professional Certificate training program scheduled in February will cover the topic of “Compressor Maintenance.”
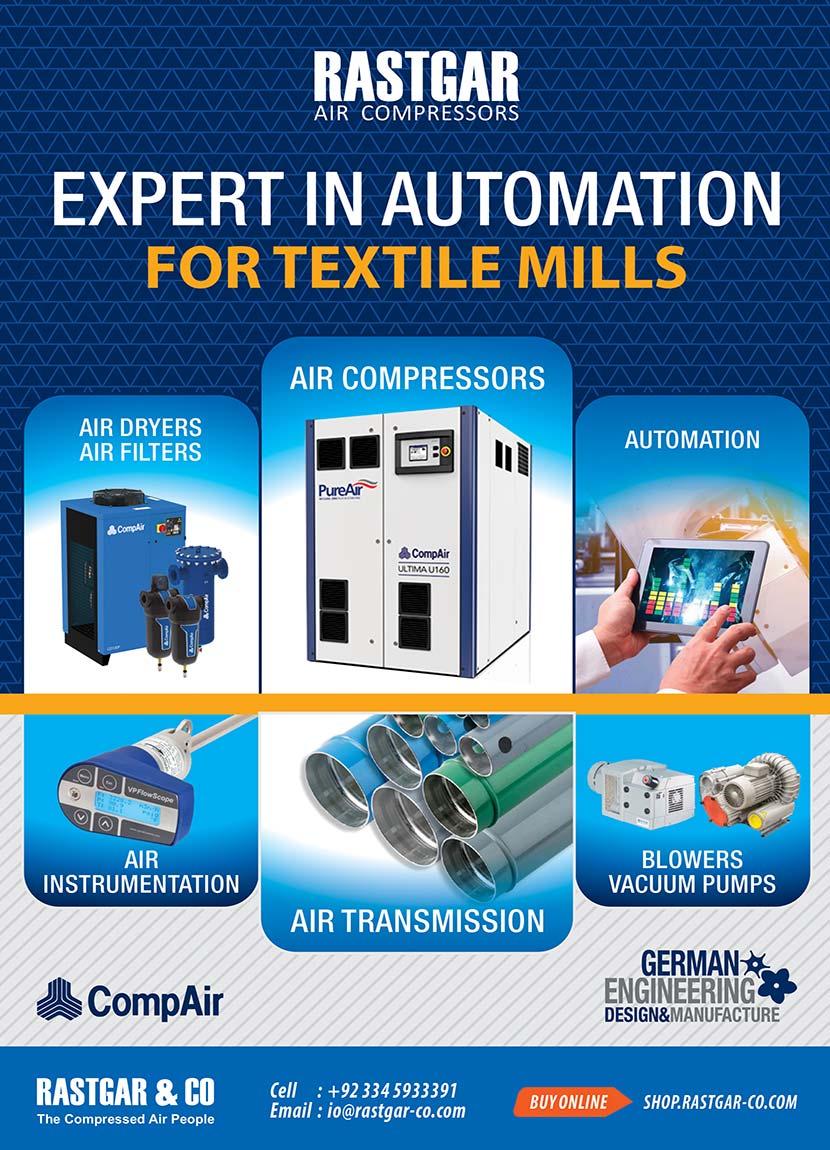
Asia Pacific Rayon to ramp up viscose fibre production to meet market demand

Asia Pacific Rayon (APR) plans to increase its production capacity to 600,000 tonnes to meet the strong growth potential of viscose staple fiber (VSF) and strengthen its market position in Indonesia and export markets across the region. The additional capacity will be achieved through improved optimisation and efficiencies, and by adding 300,000-tonne viscose production facility in Pangkalan Kerinci - Riau, Indonesia where APR is colocated with sister company and fiber supplier APRIL Group.
The expansion will utilise APRIL’s current rayon grade AE pulp capacity from existing pulp production lines, with fiber supply sourced from APRIL’s existing responsibly managed renewable fiber plantations in compliance with internationally recognised forest certification standards and its sustainability policy and in keeping with the recently announced APRIL2030 commitments and targets.
Construction of the additional APR production lines is scheduled to commence in the second half of 2021 and will include features such as a chemical recovery process upgrade, slush-pulp processing installation and other investments aimed at reducing APR’s energy use and environmental footprint. Upon the additional lines’ completion in 2023, APR will be the world’s largest single-site integrated viscose manufacturing facility, seamlessly integrating dissolving wood pulp from APRIL’s renewable fiber plantations.
“As a relatively new entrant in the VSF market, APR has established a strong market presence within two years with a growing network of customers in Bangladesh, India, Pakistan and Turkey. Our VSF business will continue to expand into the international markets by partnering with others in the textile value chain. With the advantage of economies of scale, we are committed to responding to customer demand for sustainable viscose with quality, differentiated product offerings, and competitive pricing,” said Sachin Malik, APR Sales Head.
Formally inaugurated by Indonesia President Joko Widodo in February 2020, APR is a vertically integrated operation from renewable fiber plantations to highvalue textile development, located in Riau, Sumatra. In the same year, Asia Pacific Yarn (APY) and Jakarta Fashion Hub (JFH) were established to respectively support yarn research and development, and promote fashion design talent and collaboration.
APR ensures that dissolving wood pulp sources come from internationally recognised, credible forest certification systems such as PEFC™ which guarantee the wood fibre to be from sustainably managed forests and controlled sources. APR will continue to maintain 100% PEFC™ Chain of Custody certification for our viscose.
APR’s products carry the labels MADE in GREEN by OEKO-TEX®, USDA Biobased, Seedling, OK biodegradable, and Medically Tested-Tested for Toxins by FKT. The company obtained ISO 9001 quality management and 14001 environmental management systems, and 45001 for occupational health and safety management systems.
For further information: nauman_ilyas@asiafibre.com.
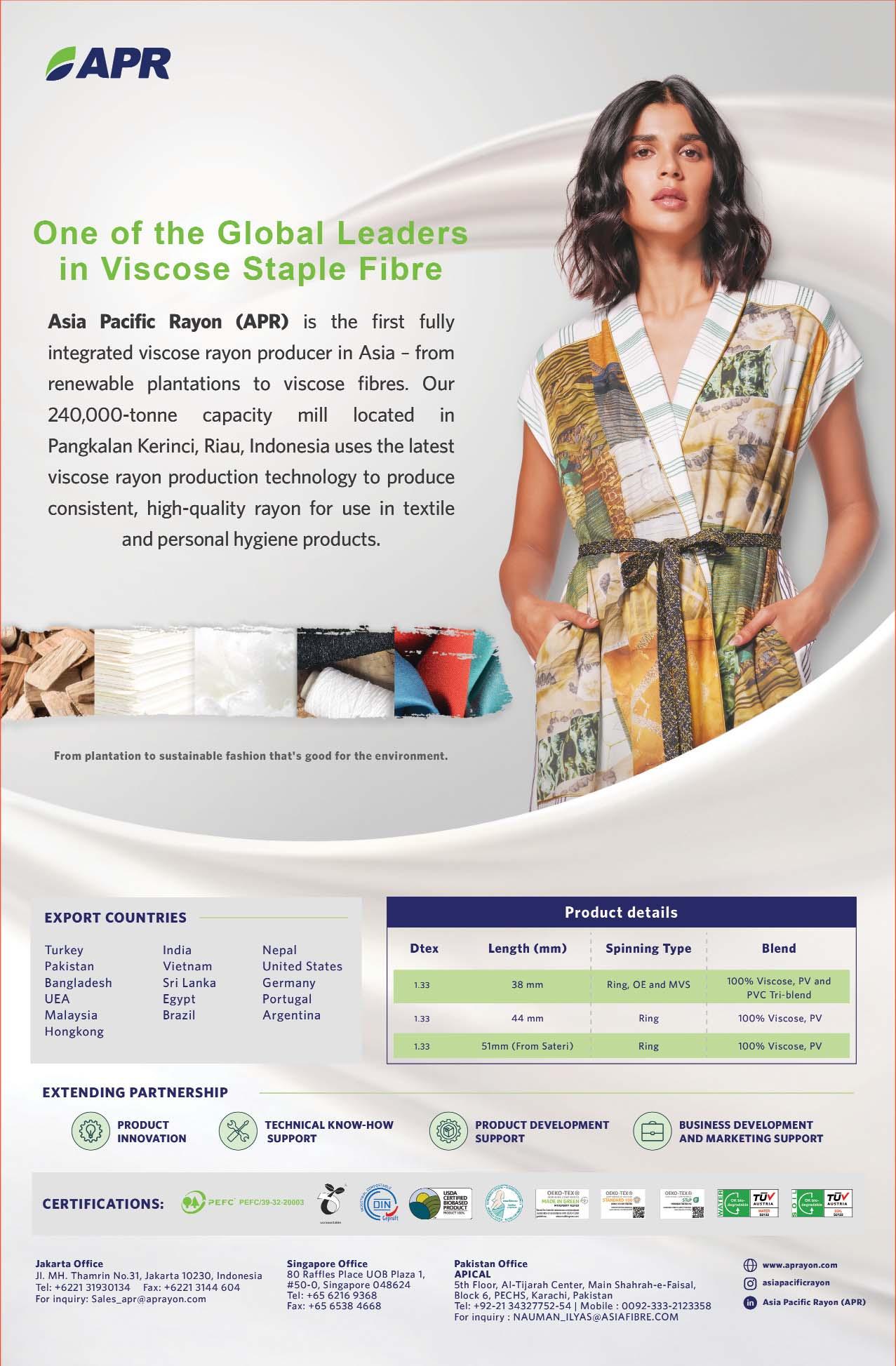
A recent Montex®Coat installation at a European mill.

The Montex®Coat ticks all the right boxes for coating success in 2021
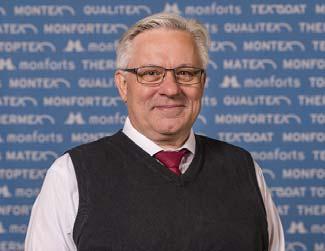
Monforts Head of Technical Textiles Jürgen Hanel.
Flexibility, product uniformity and automation are the keys to success for coating businesses in today’s rapidly-changing technical textiles industry, explained Jürgen Hanel, Monforts Head of Technical Textiles, at the recent 1st World Congress on Textile Coating.
Introducing the latest Montex®Coat magnetic roller coating option to virtual delegates from around the world at the conference organised by International Newsletters, Hanel explained why this technology makes perfect sense now
“The magnetic roller system allows a wide range of coatings and finishes to be carried out, while being easy to handle for operators and much easier to clean at the end of the process.”
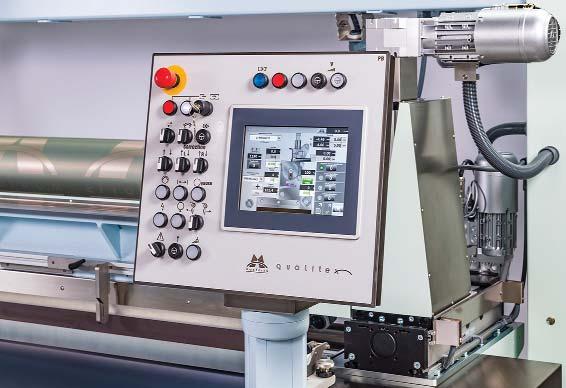
The touchscreen control of the Montex®Coat allows simple and easy adjustment of previously complicated settings.
He said. “It provides textile finishers with an expanded range of options due to the fully-adjustable positioning of the magnet within the roller and with four different magnet positions possible, can be set to operate both as a direct coating system and as an indirect coater.”
With traditional dip coating systems, he added, as well as with many standard knife coating technologies, there is always a difference in the tension between the centre and the edges of the wide width fabrics being treated – and hence the amount of pressure with which the coating is applied. With the use of a magnetic roller, equal pressure is applied across the full width of the fabric, with consistent results even at wide widths of over 2.4 metres. In addition, adjusting the roller surface, rather than changing the coating formulation to match the required add-on and viscosity for each coating effect required, leads to much higher output from the line.
Cleaner and less wasteful
The contribution of such flexible and resource-saving new technologies to a cleaner and less wasteful textile industry was a key theme at the congress – held virtually across the four afternoons of February 11th, 12th, 18th and 19th – as was digitalization and the many advantages it is providing.
“A typical integrated Monforts coating line is automated from the inlet feed to the winder,” Hanel told delegates. “Adjustments can also be made simply and easily from the touchscreen and with the new hand-held remote controller which has recently been introduced for the Montex®Coat unit.”
Manual adjustment, he added, is time consuming and needs the attention of an experienced operator or the reproducibility will not be accurate between coating operations. The adjustment by motors allows each coating to be stored and downloaded again for 100% reproducibility.
The motors can be fully controlled from the touchscreen and all necessary adjustments carried out remotely, making switching from one process to another extremely quick and easy.
The accuracy that is now being demanded by today’s most exacting customers is met with an optional carbon fibre roller – especially in dealing with the winding tension required in the processing of materials such as prepregs for composites and other heavyweight fabrics. Typical applications for the Montex®Coat include the finishing of tents and awnings, black-out roller blinds and sail cloth, automotive interior fabrics and medical disposables. Full PVC coatings, pigment dyeing or minimal application surface and low penetration treatments can all be accommodated.
“The World Congress on Textile Coating was characterised by some very stimulating presentations and forums between the speakers and a global audience of textile specialists,” Jürgen Hanel concluded. “It truly reflected the high level of positive changes now taking place in not just textile coating, but the entire textile industry. I look forward to the next edition, which hopefully will be a face-to-face event for even deeper level discussions and debate.”
Stimulating forums between textile specialists took place at the 1st World Congress on Textile Coating.
