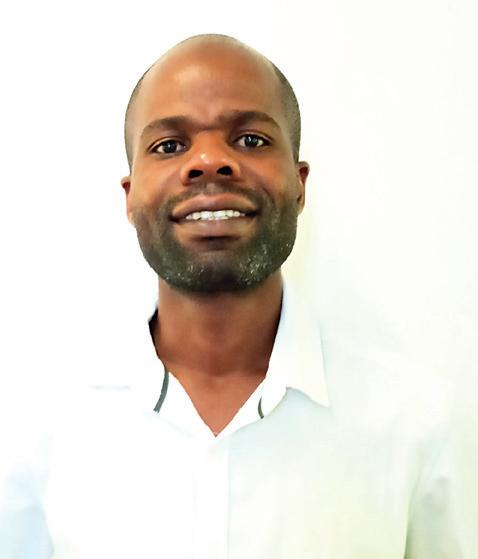
3 minute read
On the Move
Walter Mxabangu Ntuli
Walter Mxabangu Ntuli has been appointed Aquamarine Water Solution’s Sales Engineer: Public Sector
Advertisement
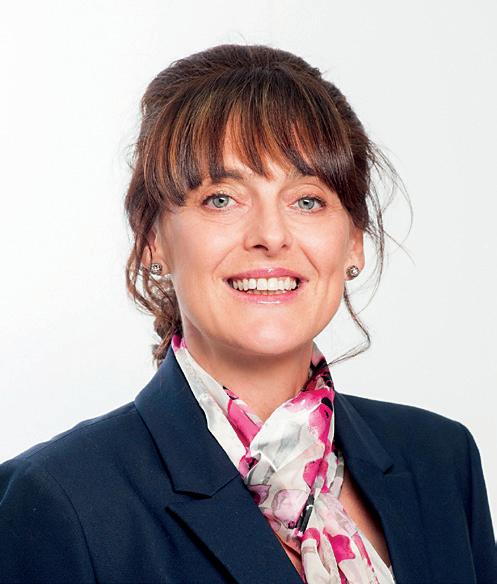
Atlas Copco has appointed Wendy Buffa-Pace as managing director to the board of directors Wendy Buffa-Pace
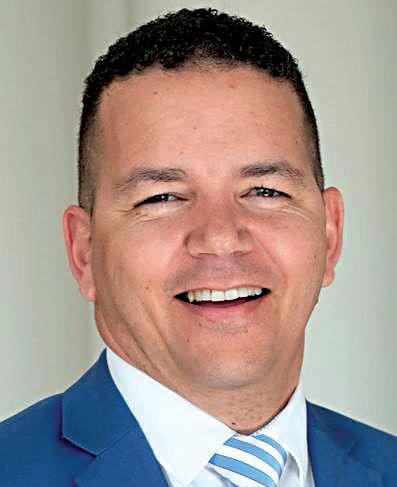
Xylem South Africa has appointed Jehiel E Lawrence as its new Sales Director for Southern Africa Jehiel E Lawrence
Aimed at OEMs looking to add mobility to their autonomous or collaborative robots, NSK has developed an innovative direct-drive wheel unit specifically designed for use in quiet environments, such as hospitals, hotels, offices and libraries. Robots fitted with the new wheel unit can efficiently carry and move loads up to 100kg without disturbing people. With digital trends such as AI (artificial intelligence) and ML (machine learnNow a Reality
ing) beginning to show genuine promise in real world applications, efforts are ramping up to develop mobile robots and humanoid robot hardware that can perform useful tasks in close proximity to people. The major obstacle with systems like conventional AGVs (autonomous guided vehicles) used in factories and warehouses, is the noise they make. In contrast, the NSK direct-drive wheel unit is much quieter, facilitating use in public spaces and non-manufacturing environments. Settings such as service sector businesses and public facilities require robots that operate quietly to avoid impeding conversations and disturbing people from their tasks. The quiet nature of NSK´s wheel unit can be attributed to its gearless structure (direct-drive motor), which leverages the technology behind the company´s Megatorque Motor to eliminate the operating noise generated by typical gearboxes. Geraldene Govender, (011) 458-3600 Email: nsk-sa@nsk.com
Dependable Infrastructure
“BMG specialists play an important role in upgrading ageing water and wastewater facilities and designing new drive systems, to ensure a dependable infrastructure,” explains Kelly Mac Iver, Gears Business Unit Manager, BMG ElectroMechanical Division. “The selection of robust equipment, which can endure continuous operation under severe conditions is critical. Every drive package selected must match the application perfectly, to ensure energy-efficiency, low running costs, minimum downtime and extended service life of the system. “Care for the environment is also a priority and for this reason, we select environmentally-friendly drive solutions that help minimise emissions. “It is also important to prevent unnecessary breakdowns, which is why reliability is our main focus when designing the drive systems for new and upgraded facilities. All BMG components are precisely matched to each other and to application requirements, to ensure high productivity, smooth operation and long service-life. “Apart from the supply of new drive systems, the company’s broad branch network offers original spares and advanced workshop resources that ensure all repairs to drive components meet pristine OEM standards,” Kelly concludes.
Gears Business Unit Manager BMG ElectroMechanical Division Kelly Mac Iver Mobile: 082-453-7347 Tel: (011) 620-1615 Email: KellyM@bmgworld.net
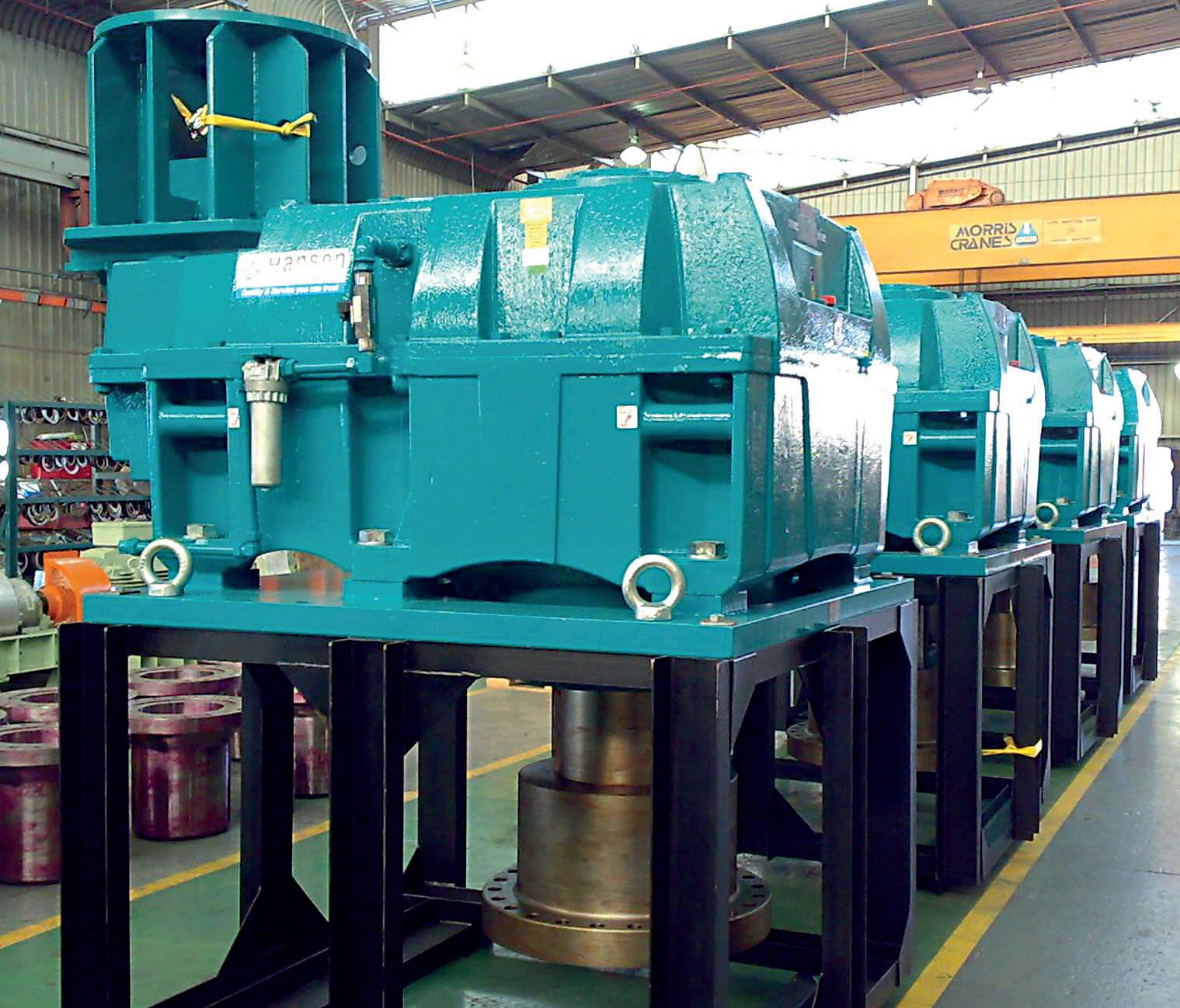
What is High Security Weld Mesh HIGH Security Weld Mesh is wire fused and welded at a Horizontal distance of 76.2mm and a vertical distance of 12.7mm also known as 35B/3510 where 3 denotes 3”(distance between vertical wires), 5 denotes 0.5” (distance between horizontal wires), and B or 10 denotes gauge of wire High security welded mesh Pallisade Gates Gate Automation Razor wire and more ....
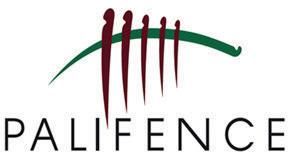
Salient Features
• Difficult to Climb: The spaces between the Horizontal wires are too narrow for fingers to have grip • Impregnable: Extremely difficult to cut with a hand cutter as the beak of a wire cutter will not be able to penetrate the horizontal wires
• Excellent Replacement option to Solid Wall as:
1. More economical than a solid wall 2. Faster to install than a solid wall 3. CCTV Camera has a clear view
• Further upgrade possible with electric security system • Anti-corrosive & low maintenance
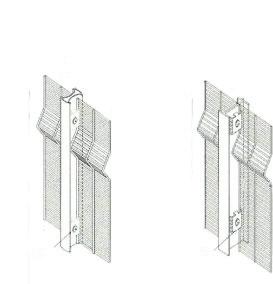
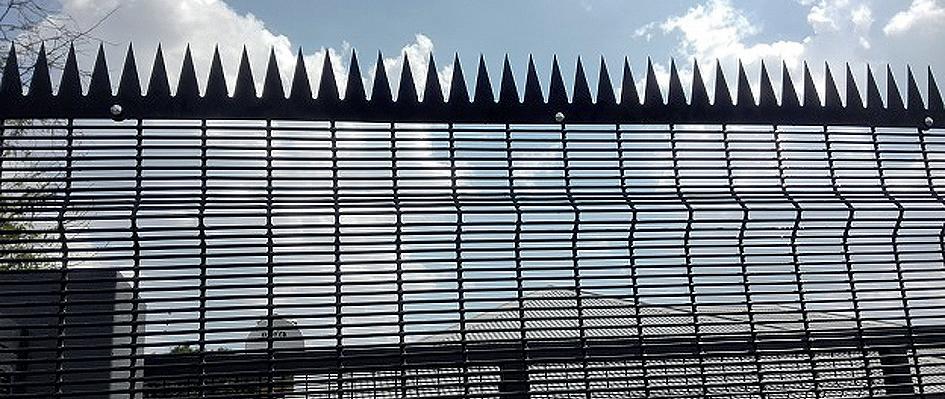
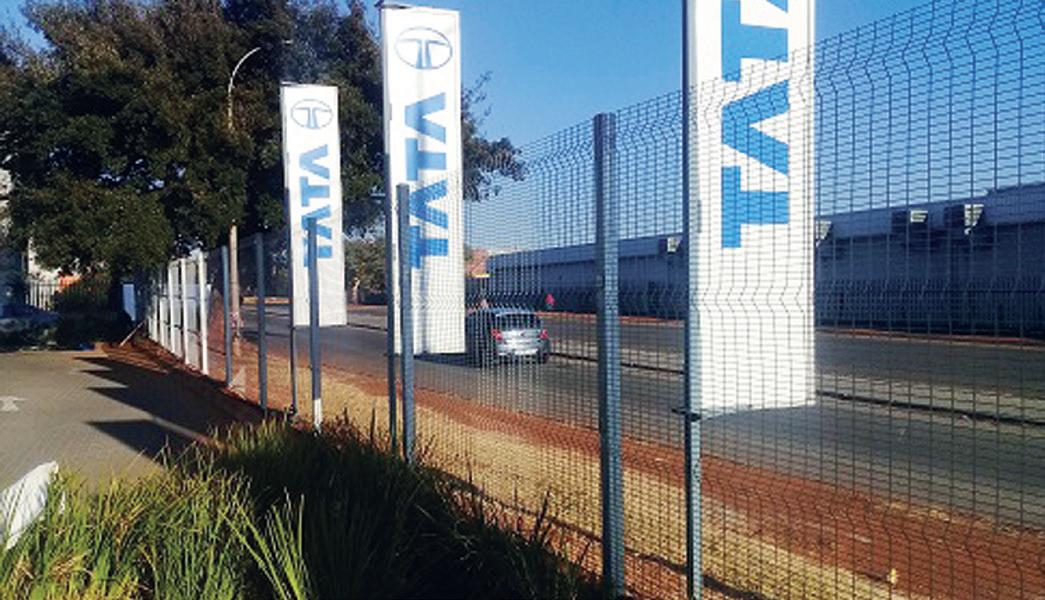
Standards
• Manufactured according to BS EN 10016-2 • Wire Sizes in accordance with BS EN 10218-2 • Tolerance on Mesh Size in accordance wiht EN 10223-7 • Tolerance on Panel Size in accordance with EN 10223-4 • Welding Strength in accordance with BS EN 1461 • Zinc Coating in accordance with EN 10245-1 • Anti Corrosion in accordance with BS En 3900 E4/F4
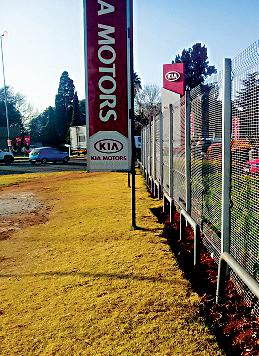
Tensile Strength
• Wire has a tensile strenght of min 550 MPA
