
16 minute read
TECNOLOGIA IR E UV
• Riscaldo di materiali compositi preimpregnati
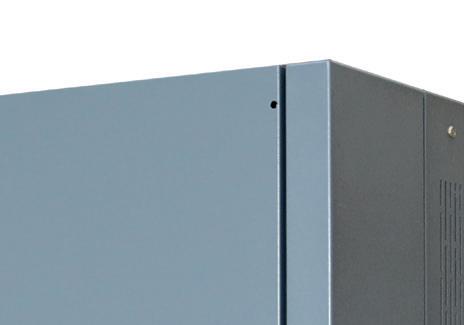
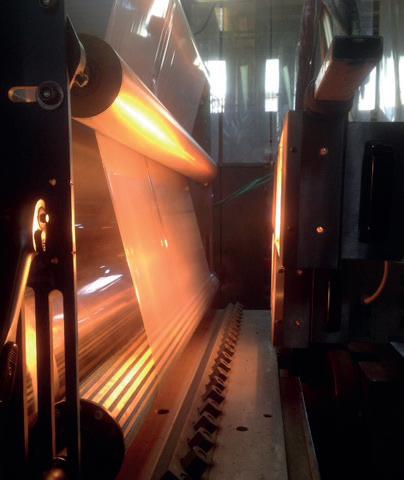
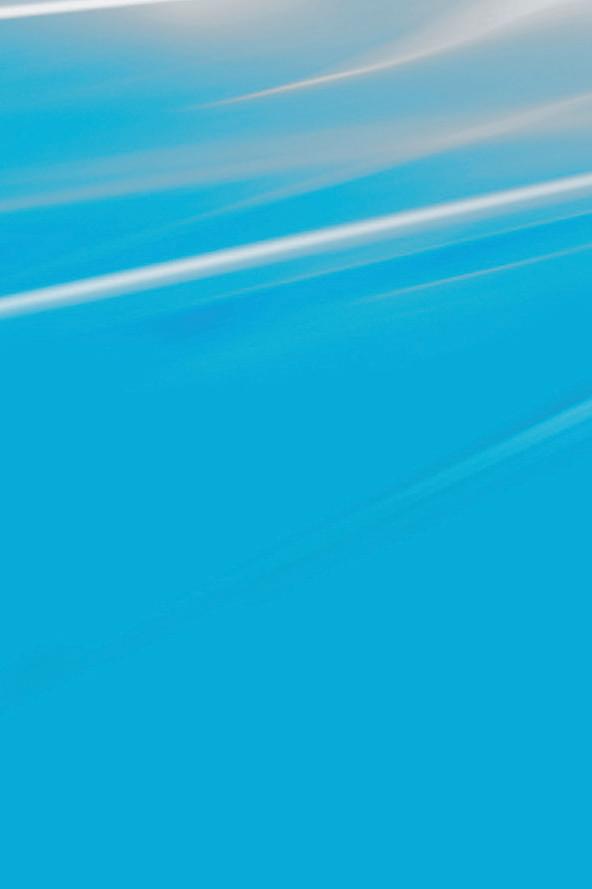
• Riscaldamento IR per preforme PET (Macchine Soffiatrici)
• Termoformatura di componenti plastici
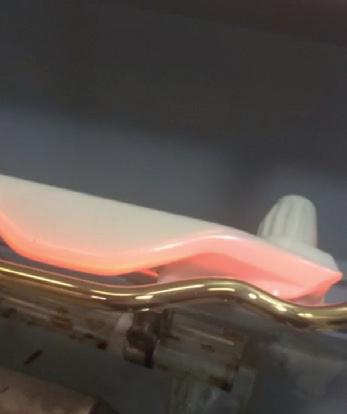
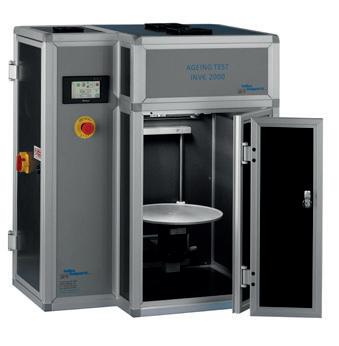
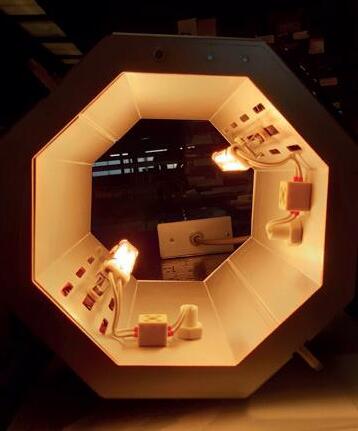
• Sbavatura parti stampate
• Processi di goffratura
• Essiccazione di granuli plastici

• Cristallizzazione e essiccazione di PET, PPS, PLA
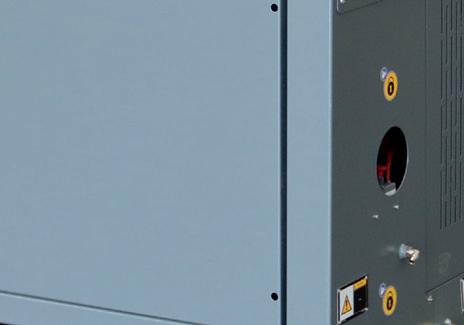
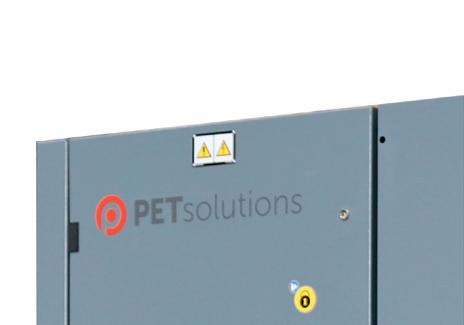
• Serigrafia di vernici su plastica www.heliosquartz.com
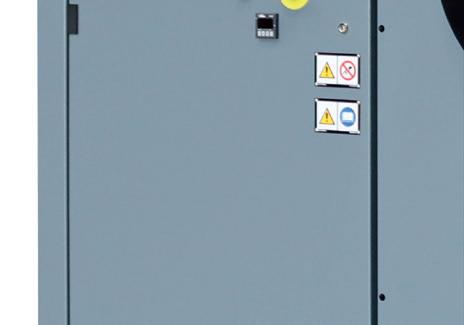
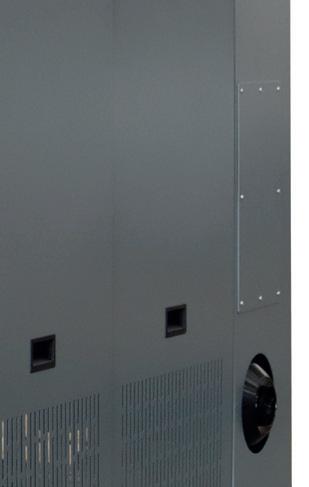



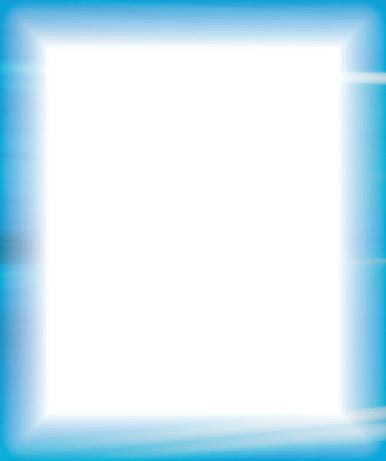
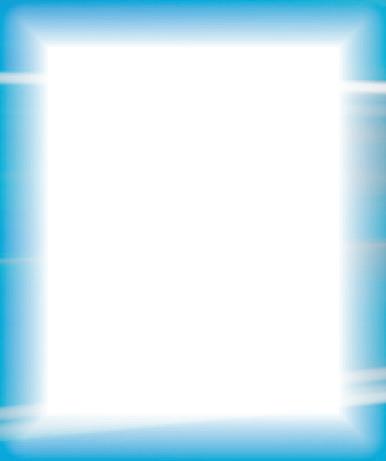

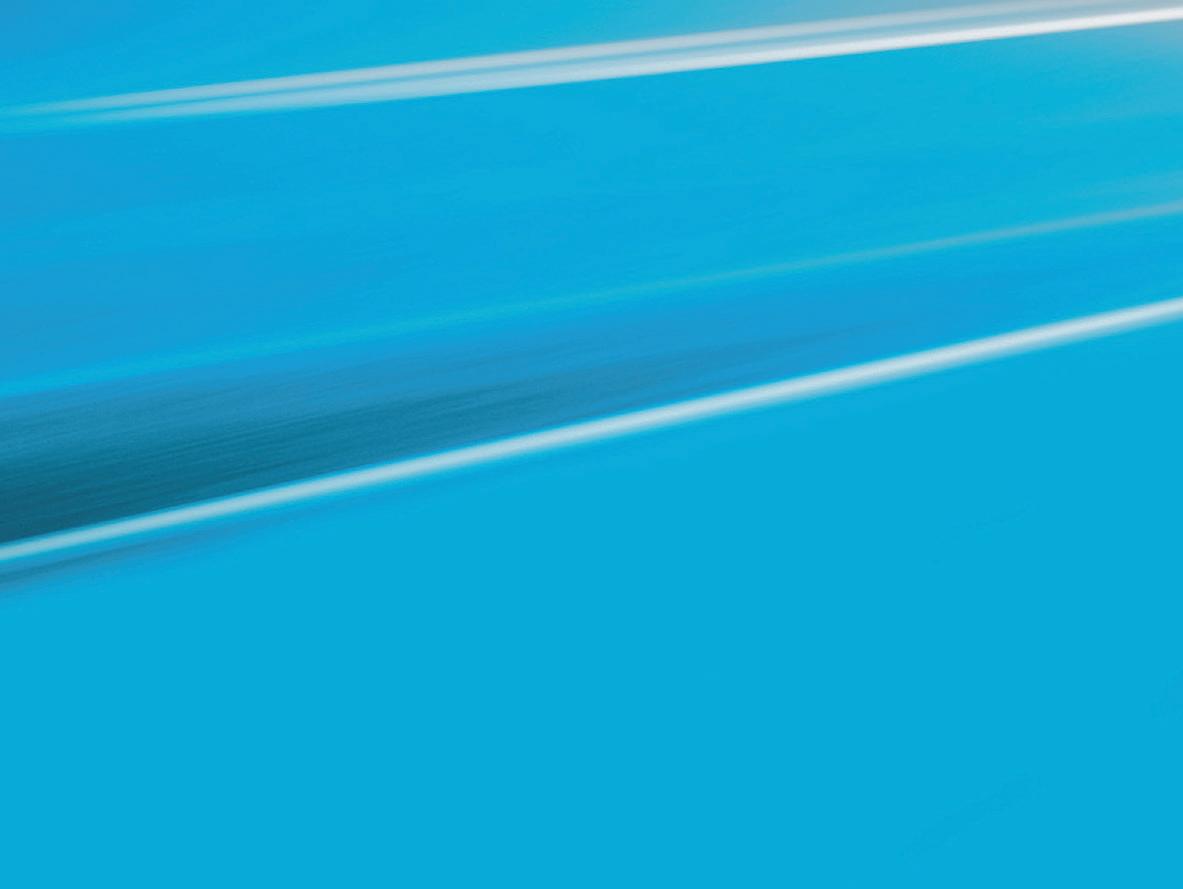
• Processi di ammorbidimento
• Processi di formatura
• Processi di curvatura
• Processi di vulcanizzazione nell’industria della gomma
• Trafila di tubi plastici
• Processi di sigillatura
• Processi di incollaggio
• Test invecchiamento dei materiali
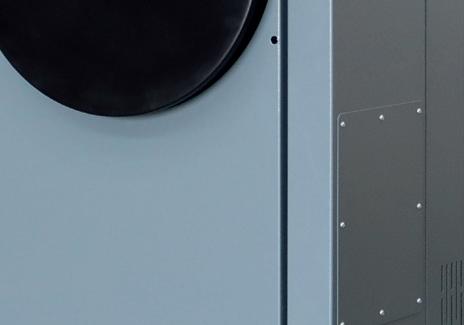
Helios Quartz Group SA
Via Roncaglia 20
6883 Novazzano - Switzerland
Tel. +41 (0) 919233555/6 Fax +41 (0) 919233557 swiss@heliosquartz.com
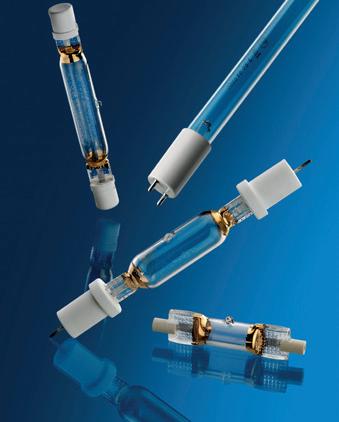
Helios Italquartz S.r.l.

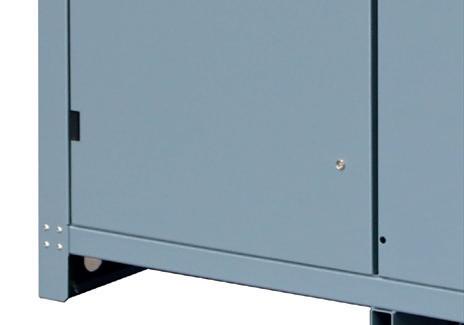
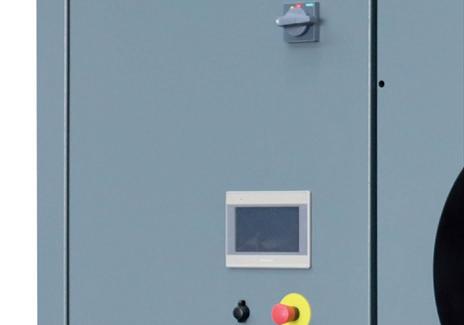
Via delle Industrie 103/A 20040 Cambiago - Milano - Italy
Tel. +39 02 95 34 93 18 Fax +39 02 95 34 50 85 italy@heliosquartz.com
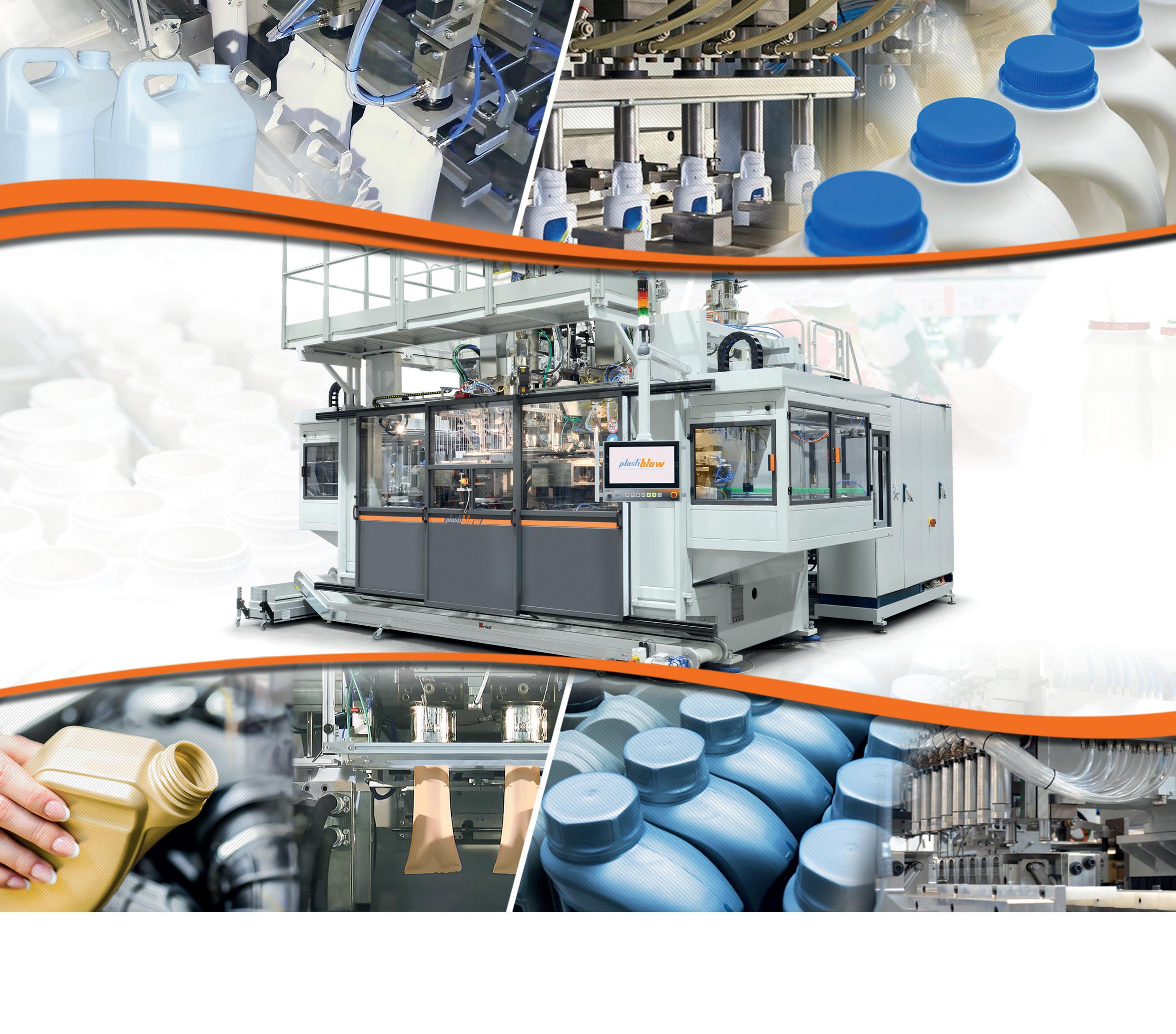
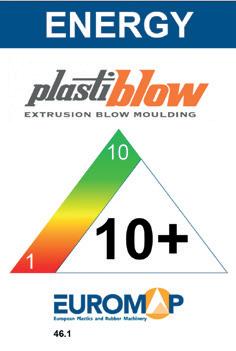
L’azienda padovana si presenta a Plast 2023 con alle spalle una storia di oltre quarant’anni che consente di offrire un insieme di attrezzature ausiliarie per ogni fase del processo di trasformazione delle materie plastiche, in particolare per la deumidificazione. Prodotti che si collocano tra i più avanzati al mondo nei rispettivi ambiti di applicazione.
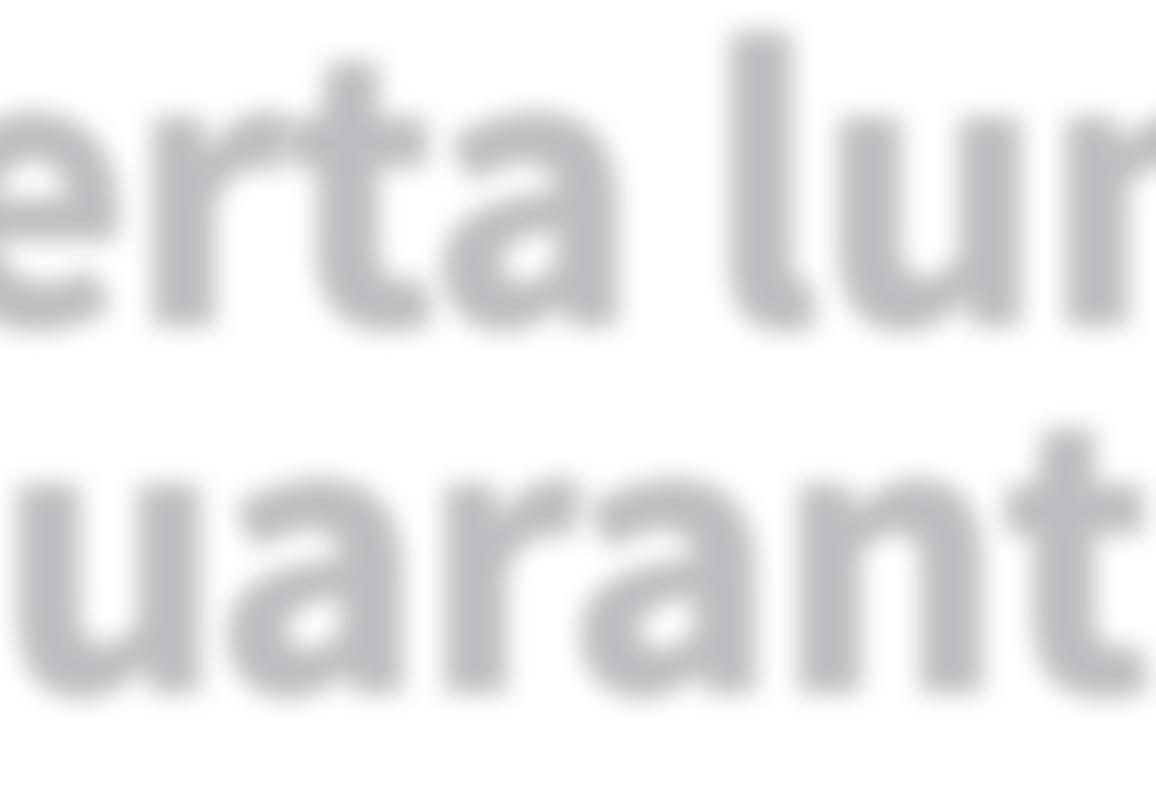
Oltre quarant’anni di attività aziendale e di sviluppo tecnologico fanno da sfondo alla partecipazione di Moretto a Plast 2023. L’azienda attiva nella costruzione di attrezzature ausiliarie per la trasformazione delle materie plastiche, e, in particolare, per la deumidificazione, infatti, propone tutte le soluzioni che non solo compongono la propria offerta attuale, ma che ne ricostruiscono la storia. A cominciare da X Dryer, flessibile sistema di deumidificazione presentato per la prima volta a Plast 2006 e disponibile in nove grandezze, che si contraddistingue per alcune caratteristiche distintive: ONE Power, unica fonte energetica, movimento elettrico delle valvole scambiatrici, display da 7 pollici nella serie attuale, raffreddamento aria-aria e consumi energetici circa del 45% più bassi rispetto alle soluzioni presenti sul mercato. Al 2008 risale invece il dryer XD serie 800 che porta con sé il bagaglio costruttivo e tecnologico della serie 20.
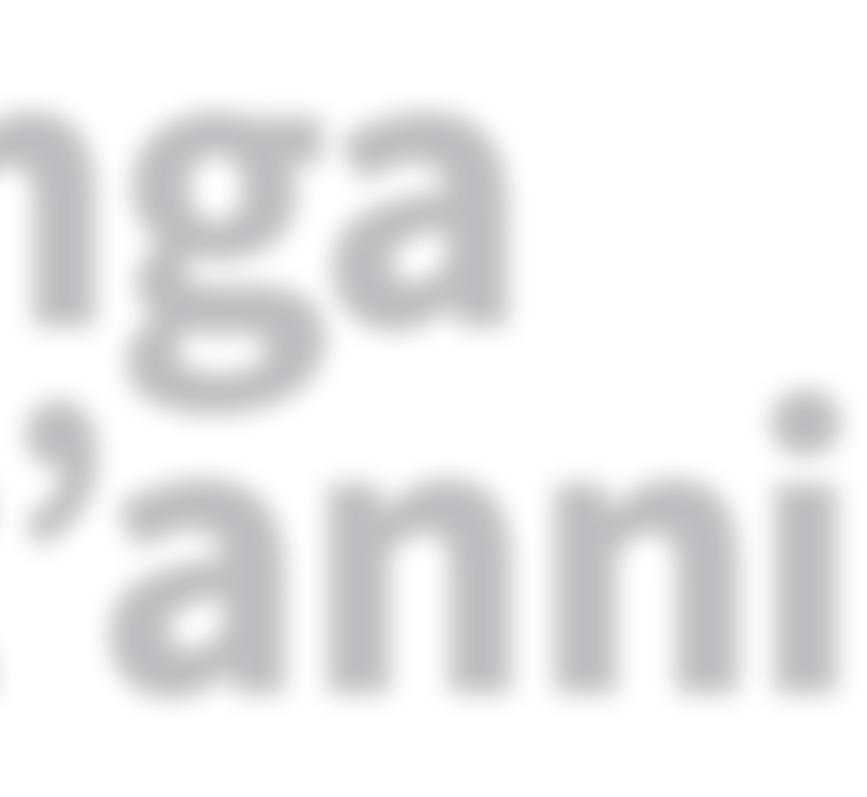
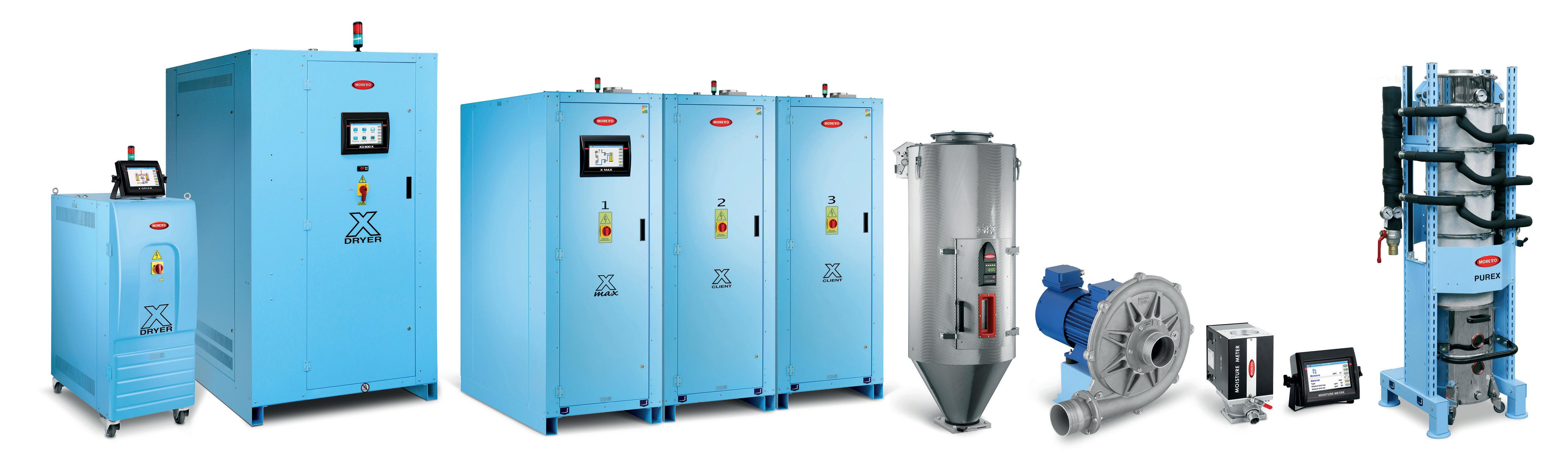

Innovazioni senza soluzione di continuità
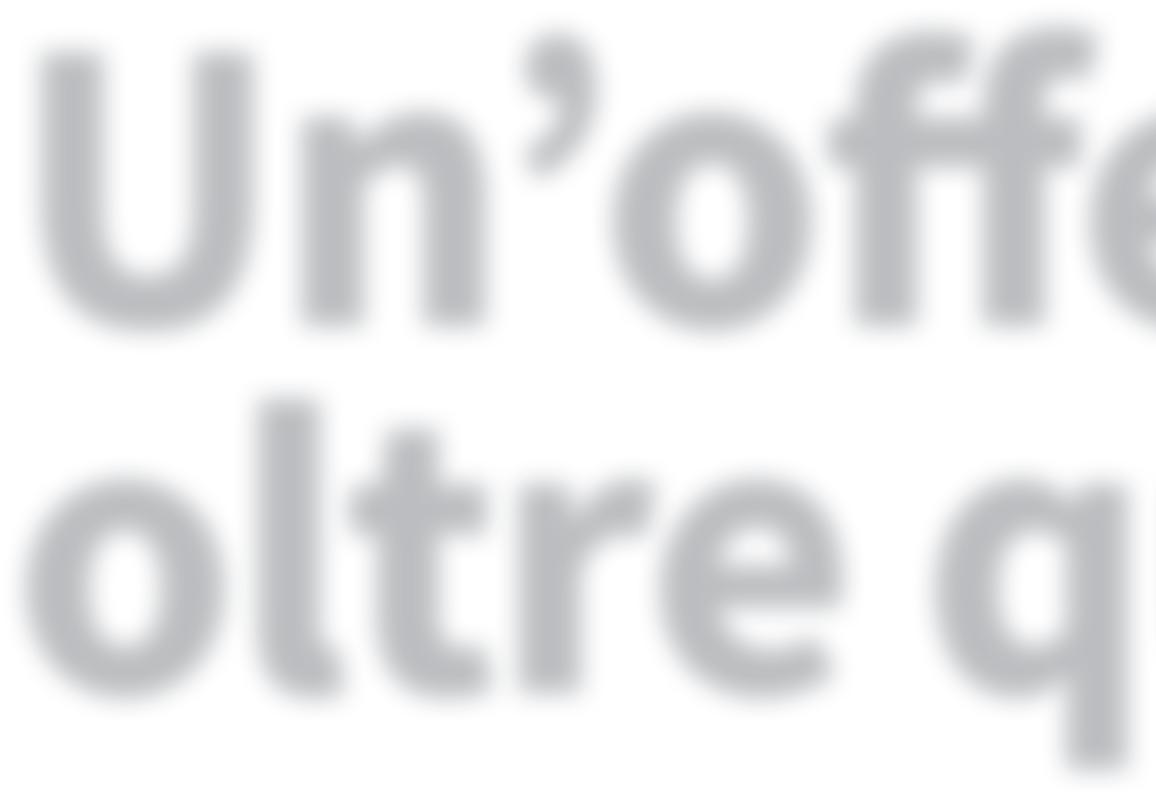
Il 2010 è l’anno di OTX, tramoggia ad alta efficienza basata sul super calcolatore Leonardo, capace di 22.000 miliardi di operazioni al secondo, e su una nuova geometria che assicura un flusso regolare del materiale, garantendo la corretta essiccazione di ogni singolo granulo trattato. L’ottimizzazione dei parametri di processo ha permesso, a parità di produzione oraria, di ridurre del 40% le dimensioni della tramoggia, il flusso di aria tecnologica e il tempo di trattamento. La riduzione delle dimensioni della tramoggia, migliorata del 66% a parità di capacità produttiva e possibile grazie all’efficienza energetica di OTX, si traduce in un dryer più piccolo, combinazione che permette di ottenere un risparmio energetico reale del 41,2%. Nel 2012 viene messo a punto un sistema modulare per la condensazione di vapori nel circuito di essiccazione che migliora il processo aumentando l’efficienza degli es- siccatori e l’autonomia del dryer. Il 2014 vede invece il completamento del progetto turbocompressore Hyper Flow e il lancio della prima macchina capace di generare 1.800 mc/h di aria tecnologica. Una soluzione nata con l’obiettivo di realizzare una soluzione in grado di garantire flusso d’aria utilizzando la minor quantità di energia possibile. Ciò che contraddistingue il turbocompressore di Moretto è la velocità della girante, che va da 6.000 a 20.000 giri al minuto in funzione del modello. Il motore ad alta velocità è applicato direttamente sulla girante, evitando la trasmissione per mezzo di cinghie soggette a usura. Il turbocompressore Hyper Flow è disponibili in 10 taglie: da 15, 30, 90, 150, 240, 400, 800, 1200, 1800 e 2400 mc/h. Nel 2016 i turbocompressori Hyper Flow vengono applicati sulla serie X MAX e sui dryer XD 800 e presto applicati all’intera gamma di dryer della serie XD20. La prima applicazione di questo turbocompressore avviene presso un importante trasformatore americano, che aveva commissionato un sistema per l’essiccazione di PET per una produzione oraria di 8.800 kg. Il progetto ha visto la realizzazione di un dryer con sette unità capace di generare 12.600 mc/h di aria tecnologica. L’impianto oggi ha un consumo energetico di 60,2 watt per kg e raggiunge una umidità finale di 25 ppm grazie a: tecnologia X Dryer; valvola di scambio ad azionamento elettrico; raffreddamento aria-aria; recupero energetico totale; tramoggia OTX (Original Thermal eXchanger); turbocompressore
La tramoggia OTX assicura alta efficienza grazie al super calcolatore Leonardo, capace di 22.000 miliardi di operazioni al secondo.

Hyper Flow; dryer X MAX. Un insieme di soluzioni che si è tradotto in un risparmio energetico del 41,2% e nel ritorno dell’investimento in 21,2 mesi.
Misura dell’umidità in linea senza tarature
A completamento di questo percorso di sviluppo tecnologico, nel 2016 nasce Moisture Meter, dispositivo per la misura dell’umidità in linea che non necessita di tarature. Collegato al dryer, il dispositivo gestisce il processo modulando automaticamente l’essiccatore in funzione del contenuto di umidità del granulo. La versione Manager comprende uno strumento che rileva il contenuto di umidità del granulo vergine in entrata nella tramoggia e trasmette il dato al dryer, che si setta sul livello di prestazione adatto a ottenere il valore di umidità finale all’interno del valore di stampabilità, e un secondo strumento che rileva il valore finale allo scarico della tramoggia immediatamente prima della trasformazione. In questo modo viene impiegata la quantità di energia strettamente necessaria a ottenere una produzione di qualità con il minimo costo energetico. Moisture Meter Manager sorveglia e gestisce il processo di essiccazione controllando il risultato in termini di umidità finale, partendo dal rilevamento iniziale che indica al dryer quale sia il livello di prestazione neces- sario, anticipando e aggiustando minuto per minuto il processo.
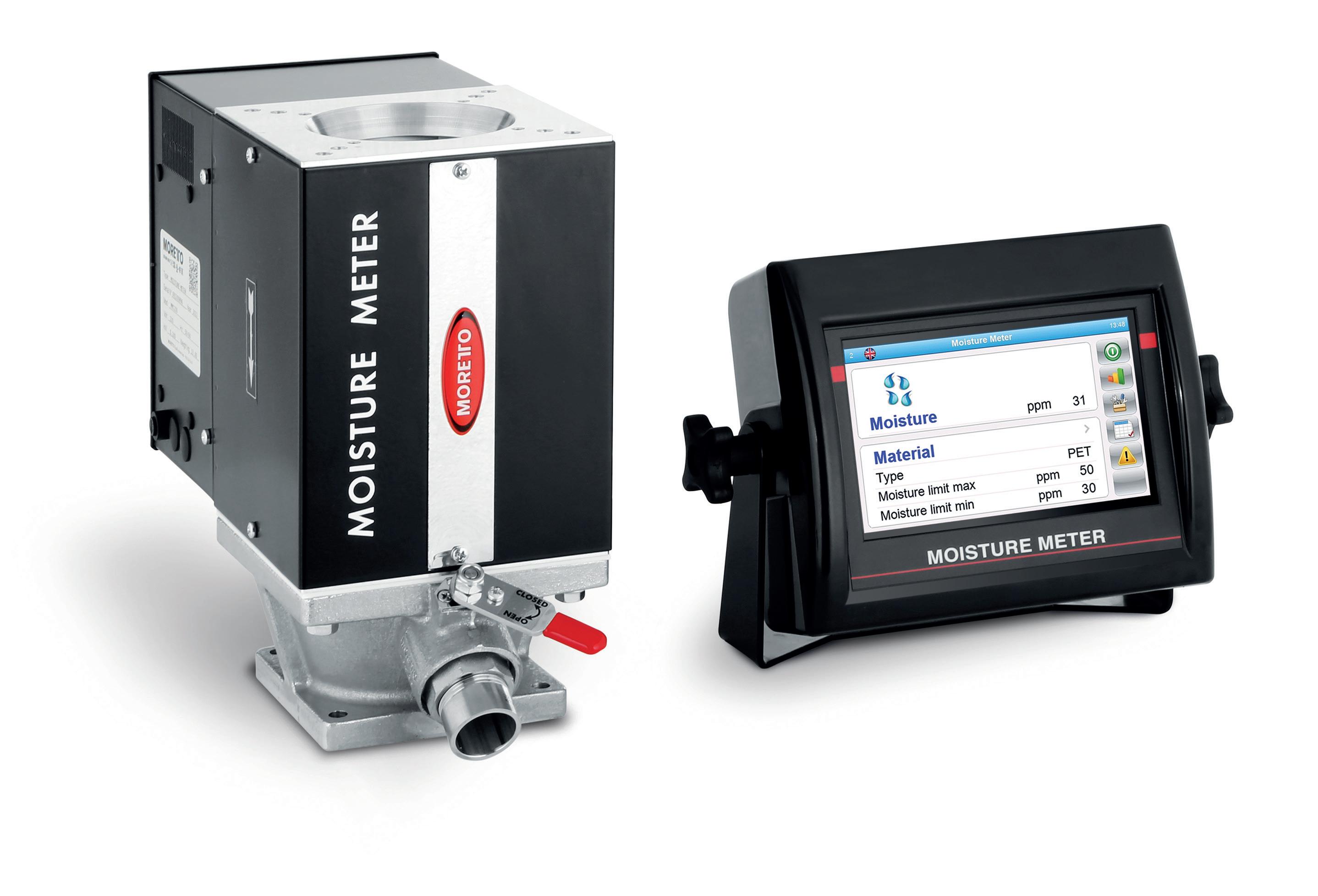
Il separatore di condensati si basa su un progetto modulare e consente appunto la condensazione di vapori nel circuito di essiccazione.
Un trattamento monitorabile anche da remoto attraverso Mowis, la piattaforma software sviluppata da Moretto per gestire tutto il processo produttivo nell’impianto di trasformazione. Modulare e auto-configurabile, utilizzabile sul posto o da remoto, tramite protocollo OPC UA connette macchine, processi, reparti e impianti secondo il concetto di fabbrica intelligente 4.0.
In definitiva, tecnologia X Dryer, tramoggia OTX, turbocompressore Hyper Flow, dispositivo Moisture Meter Manager e supervisore Mowis rappresentano una cinquina esclusiva di attrezzature ausiliarie per la trasformazione delle materie plastiche.

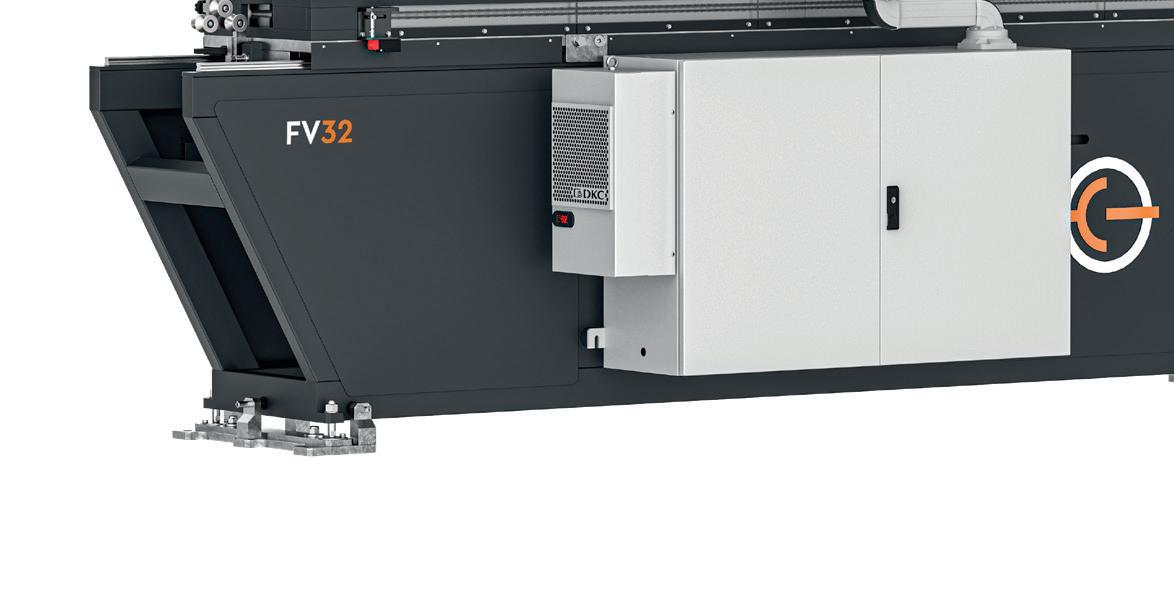
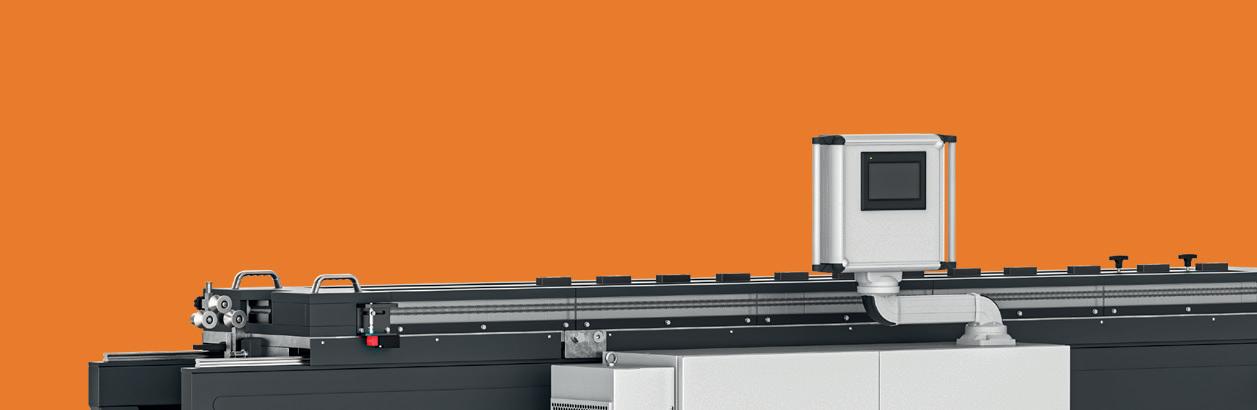
Nei processi industriali refrigerazione e termoregolazione meritano oggi un adeguato approfondimento, soprattutto da parte di chi intende mettere mano con urgenza alle rese energetiche dei propri impianti. Di seguito le recenti soluzioni sviluppate da Frigosystem a tale scopo.
Dopo aver riprogettato le proprie serie due volte negli ultimi sei anni, alla ricerca di sempre più elevati livelli di efficienza energetica (che vanno ben oltre i minimi requisiti imposti oggi dalle normative internazionali), Frigosystem si presenta a Plast 2023 con tecnologie innovative per ridurre drasticamente bollette e costi di produzione. Il raffreddamento e la termoregolazione dei fluidi sono determinanti in molte applicazioni, dove influiscono in maniera significativa su qualità dei prodotti finiti e produttività delle linee, ma le apparecchiature dedicate a tali funzionalità sono particolarmente energivore. È importante, quindi, affidarsi a chi, come l’azienda di Caronno Pertusella (Varese), ricerca e sviluppa continuativamente soluzioni mirate al processo diverse da quelle tradizionali applicate al settore del condizionamento.
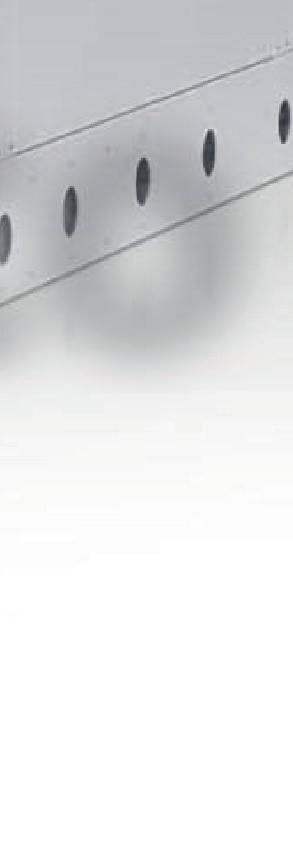

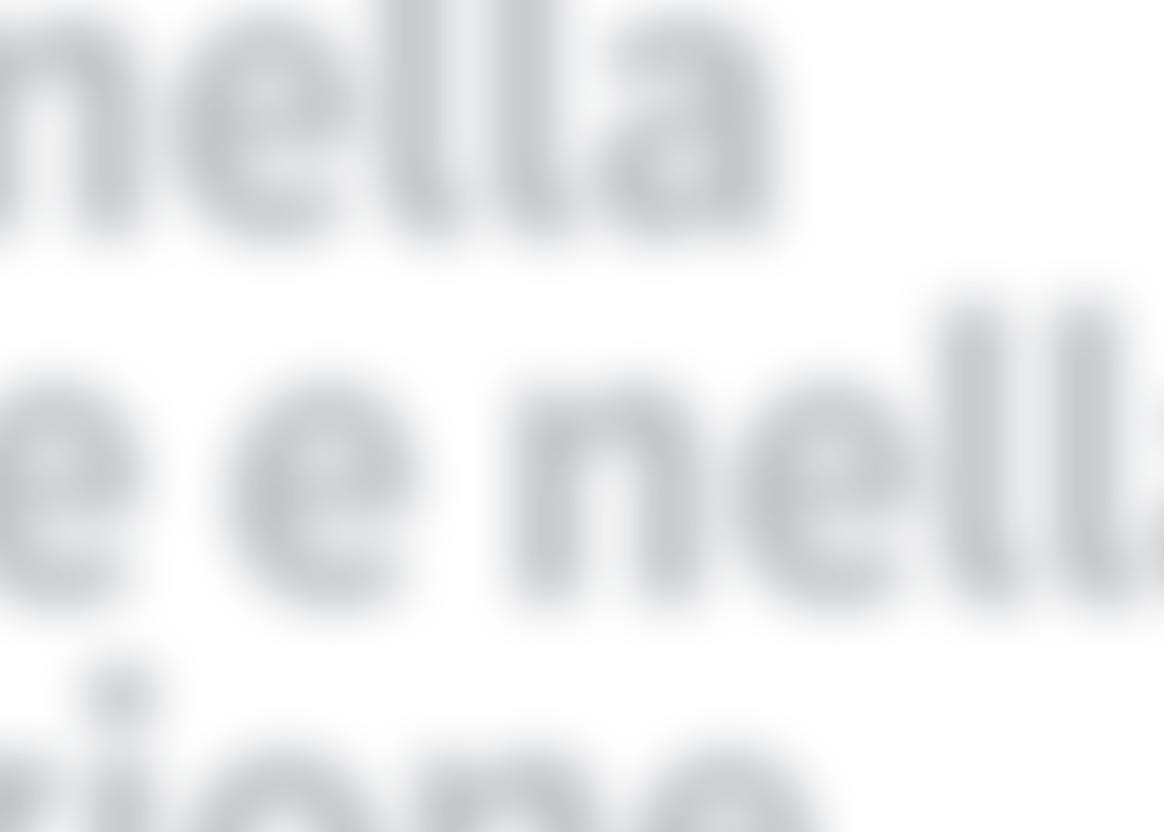

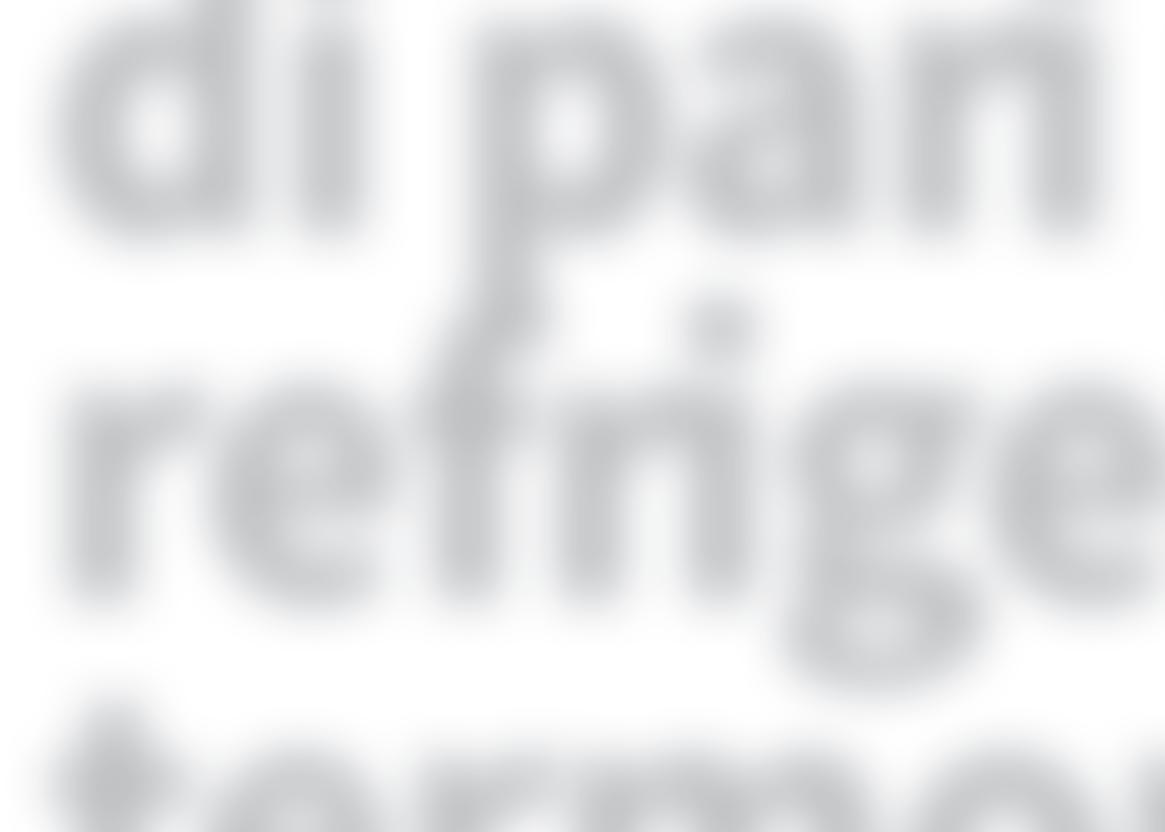
Soluzioni per la refrigerazione
In fiera Frigosystem presenta alcune delle sue più recenti tecnologie, a cominciare dalla gamma di refrigeratori I-RES con compressori a levitazione magnetica e potenze di raffreddamento fino a 4.700 kW. L’unità esposta a Plast 2023, con condensatore ad acqua, risulta essere uno dei modelli più efficienti nel mercato. Il suo SEPR (Seasonal Efficiency Performance Ratio) è 12.04, più del doppio rispetto ai chiller tradizionali.
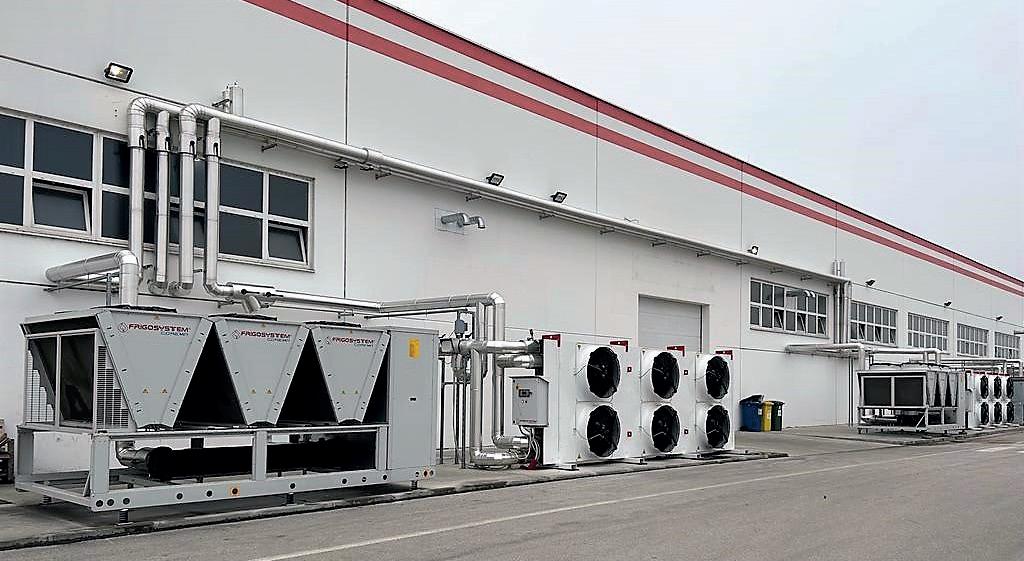
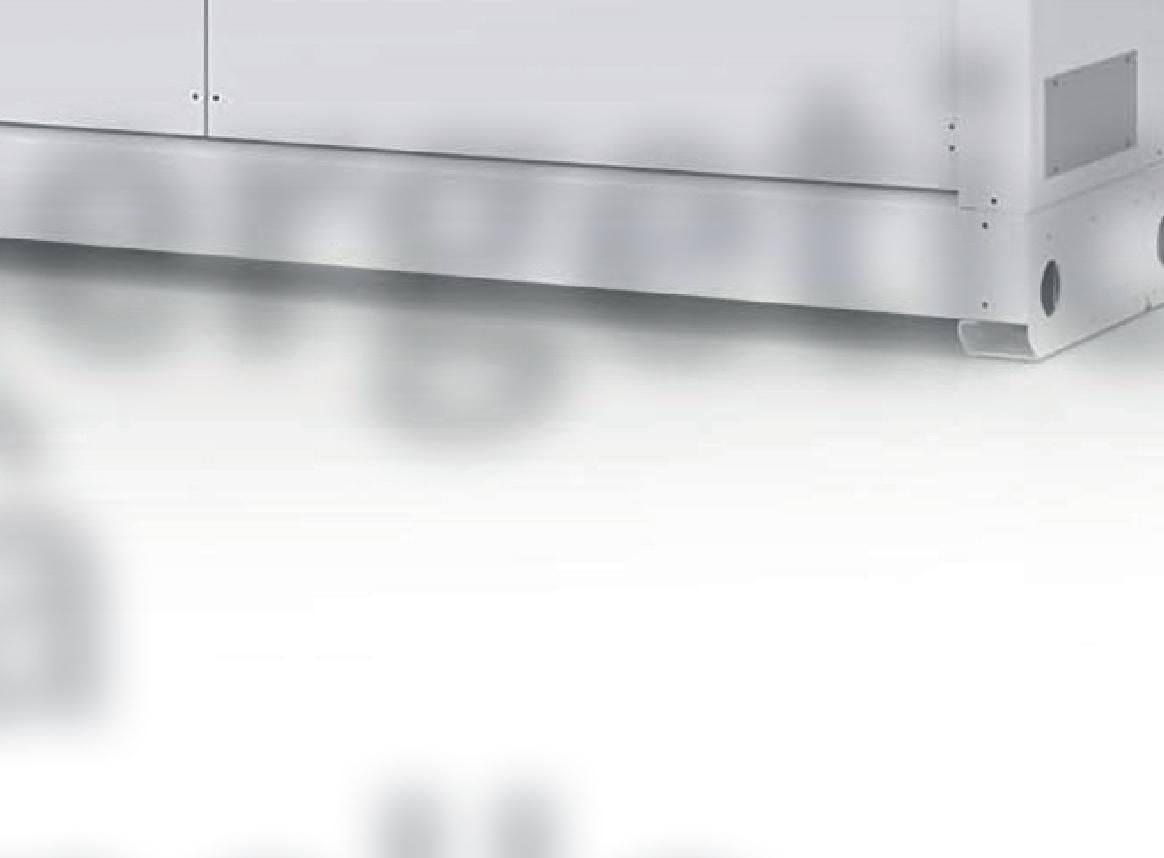
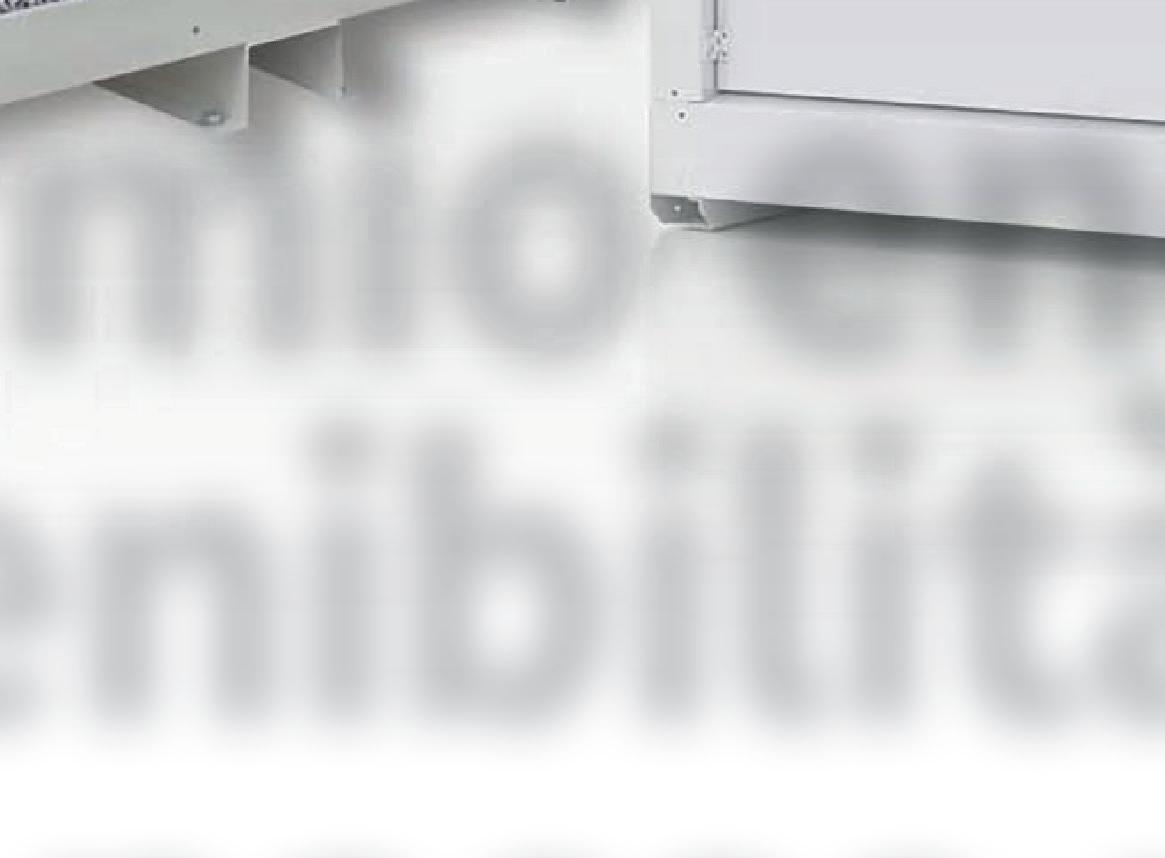
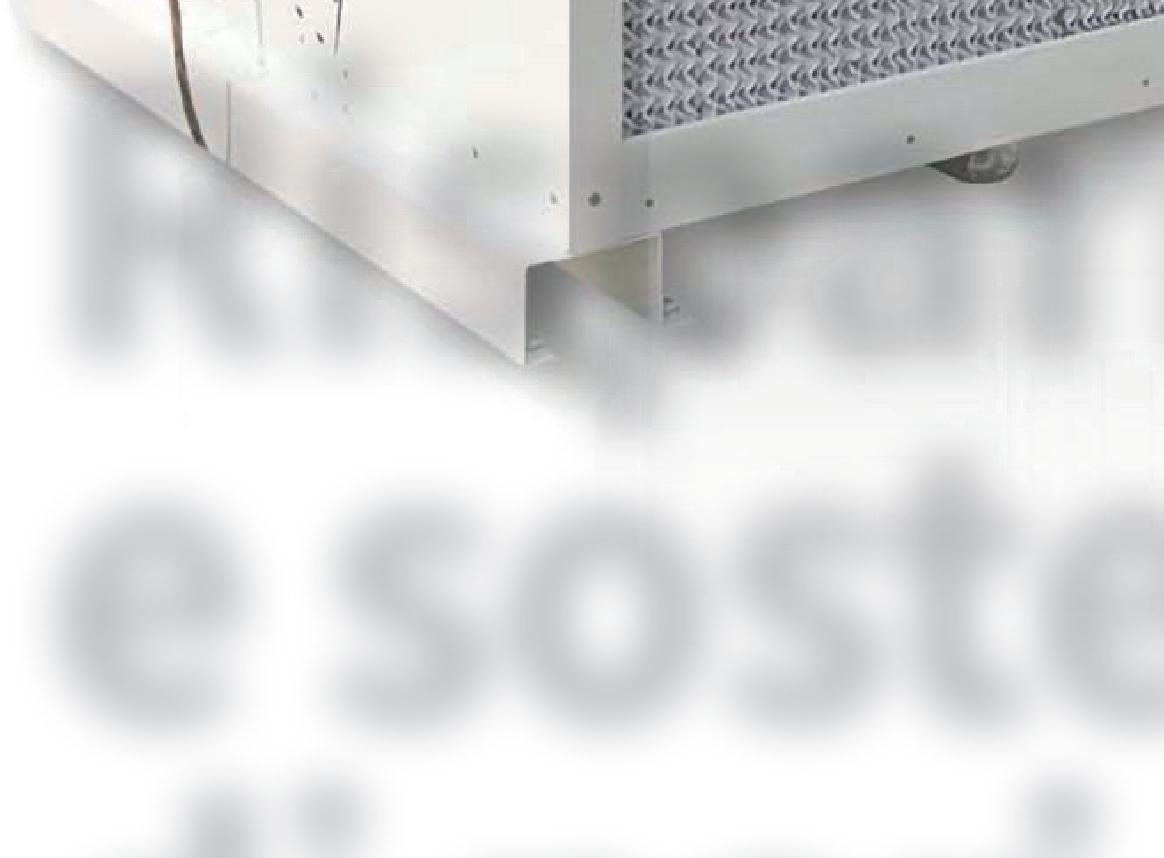
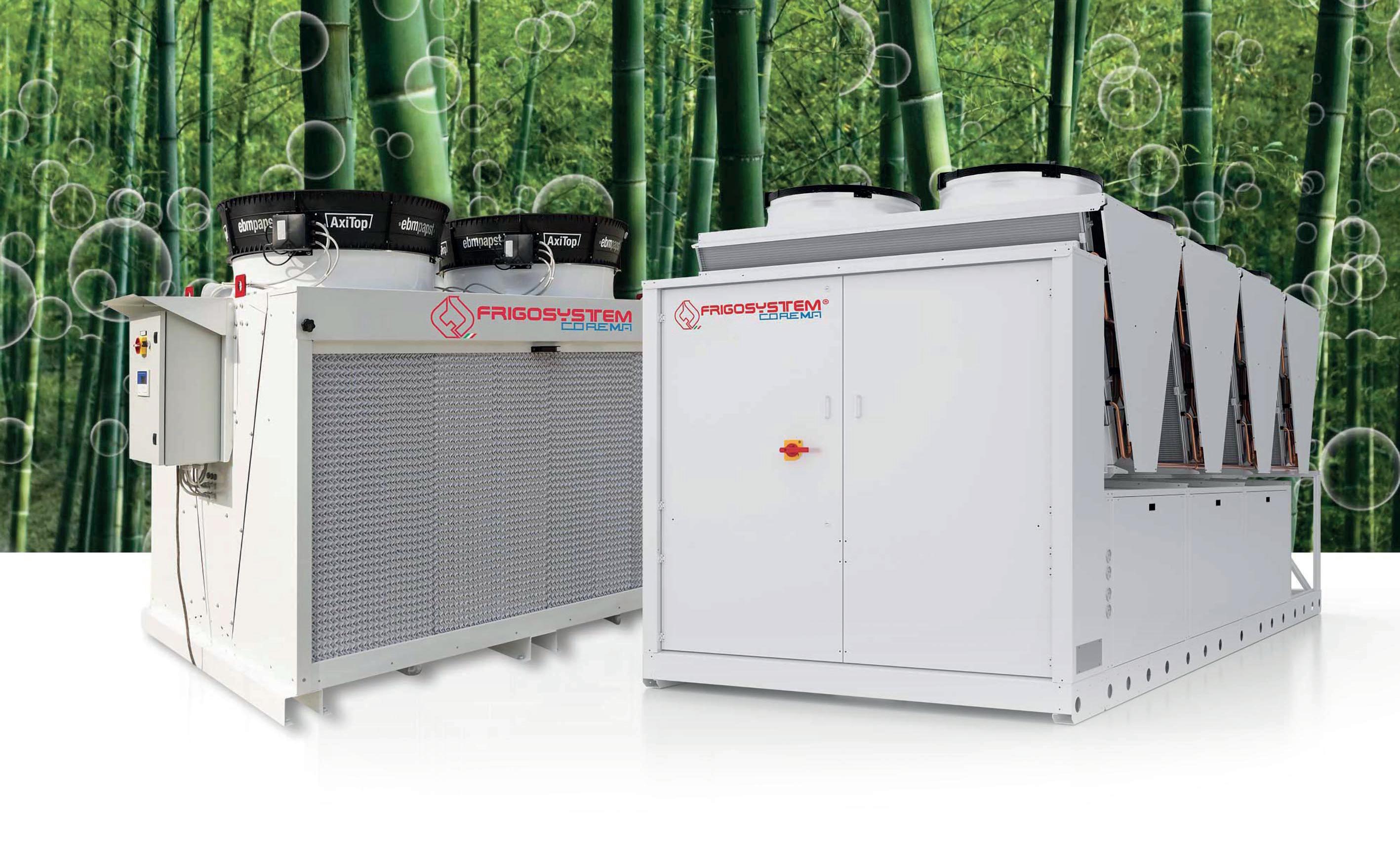
La gamma Raca Plus Energy rimane la serie più versatile, in termini sia di applicazioni che di condizioni climatiche di installazione. A oggi, ogni modello può essere dotato di recupero di calore totale o parziale. Ogni circuito frigorifero in funzione, infatti, risulta essere una fonte gratuita di calore che spesso viene dissipato: oggi con Frigosystem è possibile recuperarlo. L’applicazione di un sistema di recupero di calore permette di ottenere: acqua calda fino a un massimo di 80 °C di temperatura (utilizzabile per impianti sanitari o anche per processi); potenza di riscaldamento gratuita fino al 50% della potenza frigorifera impegnata; risparmio di un metro cubo di gas metano per ogni 8 kW di potenza termica recuperata. Anche l’opzione di free-cooling, disponibile su tutti i chiller per acqua, è stata ulteriormente efficientata per estendere i tempi di funzionamento nel corso dell’anno, ovvero quelli in cui il sistema va in appoggio ai compressori parzializzandoli o spegnendoli totalmente in base alle temperature rilevate, sia nell’ambiente che nel processo. Il free-cooling, infatti, sfrutta le condizioni climatiche agevoli che si verificano, per esempio, durante l’inverno, le mezze stagioni o semplicemente di notte nel sito dell’installazione. Con i recenti, maggio- rati costi dell’energia elettrica, alcune realizzazioni nell’area di Milano hanno evidenziato un ritorno dell’investimento addizionale per l’opzione di free-cooling abbinato a chiller per acqua, di meno di un anno. Un tempo rapidissimo se si pensa che il beneficio energetico dei periodi successivi al primo anno diventa un risparmio economico puro.

Per Frigosystem, il free-cooling non è legato solo ai chiller per acqua. A Plast 2023, viene proposta la linea Kite-Kite Dex in una veste fantasiosa e attrattiva. Questa linea di refrigeratori per aria, tipicamente installati su linee per estrusione di film in bolla per il raffrescamento di anello e IBC, è la sola presente nel mercato a poter contare su un sistema di free-cooling progettato ad hoc. Anche in questo caso, l’impianto confronta automaticamente e in autonomia, le temperature richieste al processo e quelle in arrivo dalla fonte di condensazione esterna in circuito chiuso, andando a sgravare o spegnere i compressori. Non solo elettricità ma anche acqua. Sono queste le risorse il cui consumo viene ulteriormente ottimizzato nella nuova serie di raffreddatori adiabatici ACE, concepiti per i massimi rendimenti anche nei climi più gravosi. L’ampiezza delle batterie di scambio, l’efficientamento del- la distribuzione dell’acqua, i ventilatori brushless a velocità variabile sono tra le principali novità nel contenimento del “caro bollette”. Per gli utilizzatori più esigenti nell’ambito della greenology, Frigosystem ha replicato le proprie gamme, offrendo gas refrigeranti alternativi con basso o bassissimo GWP (Global Warming Potential). L’utilizzatore può quindi scegliere il gas più confacente in termini di reperibilità, costi e normative nel Paese dell’installazione, oltre che in considerazione della futura manutenzione. La manutenzione rimane un aspetto fondamentale nella preservazione del livello di efficienza delle unità.
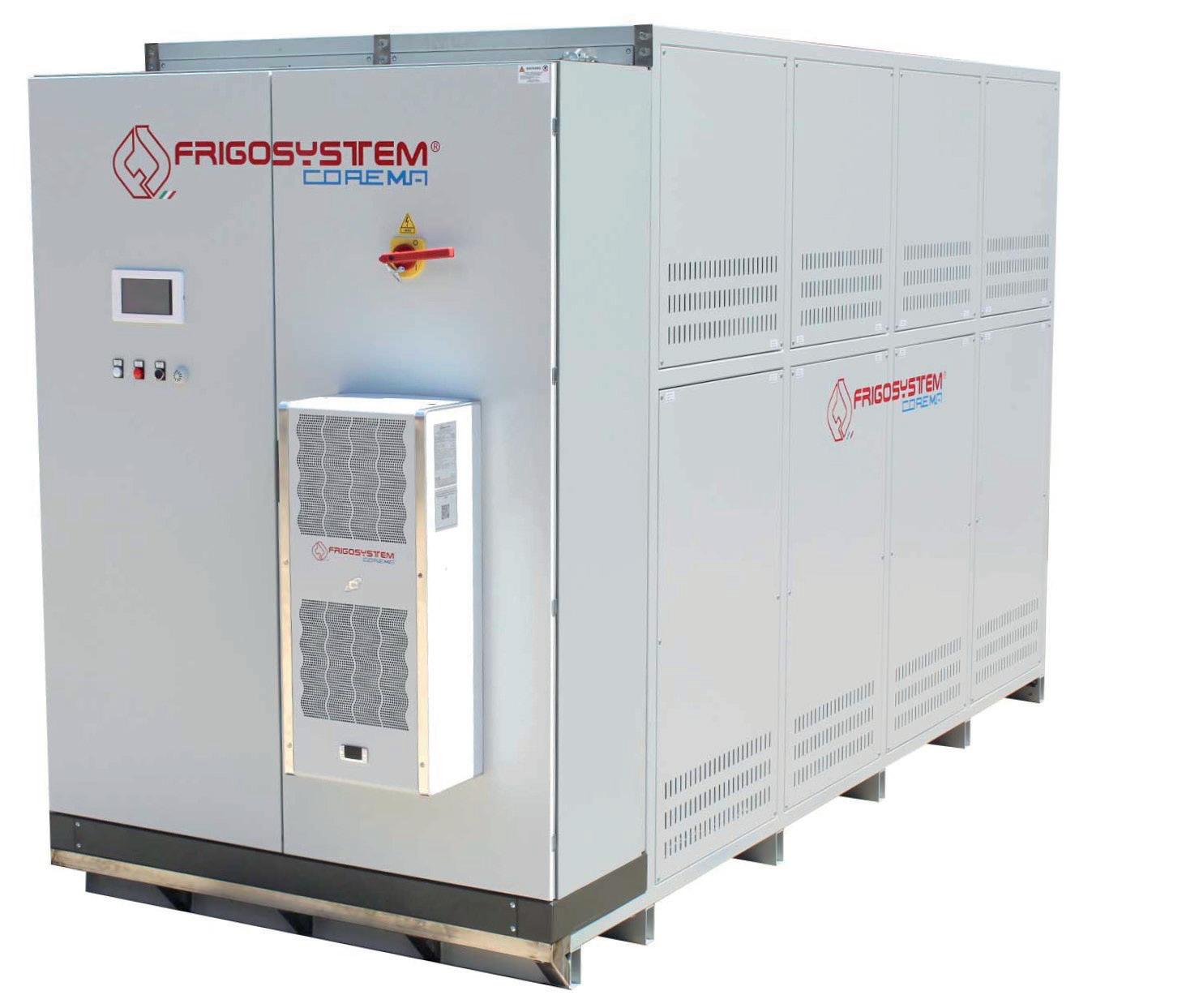
Tre configurazioni per la termoregolazione
A Plast 2023 non mancano tre delle innumerevoli configurazioni che Frigosystem progetta nella termoregolazione, con acqua fino a 180 °C e olio diatermico fino a 350 °C. Negli ultimi anni, l’esigenza di aumentare la produttività delle linee, per esempio, di film plastico, con impianti di riscaldamento, ricottura e raffreddamento dei materiali più tecnici e più costosi, ha portato allo sviluppo di impianti multi-zona dedicati alle linee MDO, dove la precisione di temperatura unita agli assorbimenti, sono argomenti di rilievo sia per gli utilizzatori finali che per i costruttori delle linee. A fianco a questi ultimi, Frigosystem ha ottimizzato i sistemi di scambio termico, l’accuratezza nella gestione delle temperature e il controllo delle portate agli impianti, ottenendo risultati ragguardevoli anche in questa nicchia.
Odour optimised, energy efficient, recyclable. And for specific applications: super clean and food contact compliant. Recycled pellets of the future can do more. Get more out of your post consumer material flow with innovative EREMA technologies featuring digital assistance systems. More quality, more productivity. For a better end product. Take the new energy saving dual filtration solution INTAREMA® TVEplus® DuaFil® Compact, for example, as well as proven ReFresher anti odour technology and the smart predictive maintenance tool Predict:On. Enter this future right now with EREMA. Enter the new era of recycling.
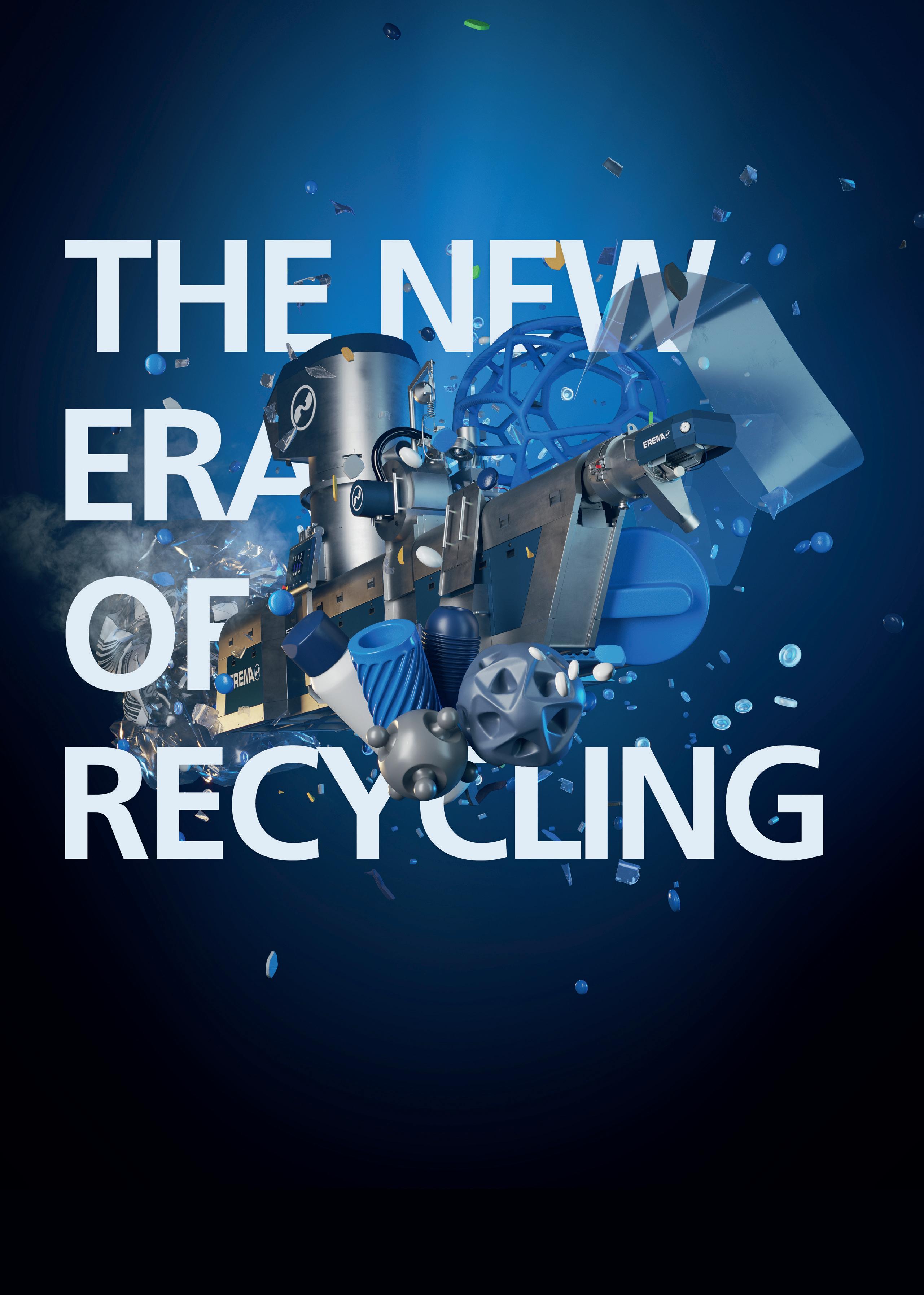
YOUR LOCAL EREMA CONTACT PROCHEMA S.R.L. Monza / Italy info@prochema.it www.prochema.it
Una collaborazione che dura da più di due decenni vede protagonisti il trasformatore GelliPlast e il costruttore Frigel. Che recentemente hanno rinsaldato il rapporto di fiducia con una commessa basata sulla tecnologia di termoregolazione Syncro. Con reciproca soddisfazione.
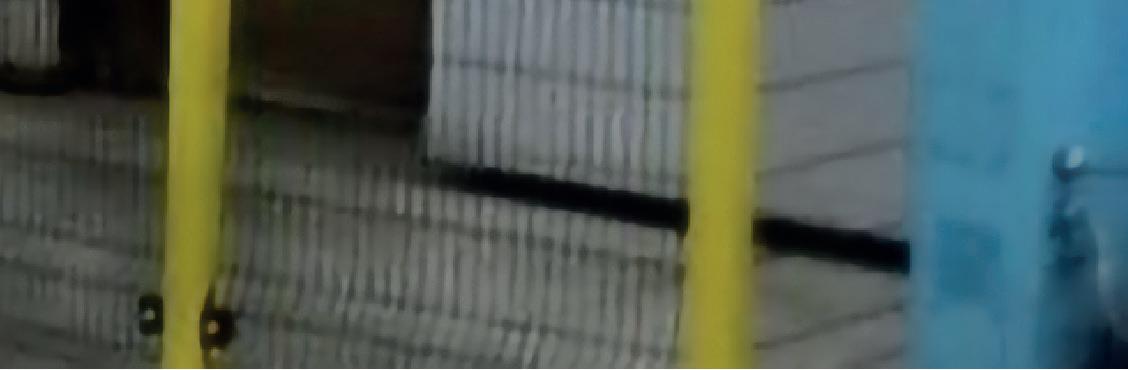

Attiva nello stampaggio di materie plastiche nel settore calzaturiero, GelliPlast oggi, grazie alla costante crescita, si propone come una delle principali realtà nello stampaggio di componentistica per vari settori, quali ferroviario, alimentare e illuminotecnica. La sua area produttiva (nella foto di apertura, uno scorcio) si avvale di 25 presse a iniezione da 80 a 1.500 tonnellate e una linea di taglio laser. In totale vengono impiegati 559 stampi attivi e 369 diverse tipologie di materie prime, per la realizzazione di 2.147 prodotti finiti.
Gli investimenti degli ultimi anni hanno permesso a GelliPlast di dedicarsi anche alla progettazione e alla realizzazione di prodotti a proprio marchio. Tra gli ultimi nati Flexy Dream, un supporto modulare da applicare alle doghe del letto che è già stato brevettato a livello internazionale. Flexy Dream è un prodotto su cui il trasformatore sta puntando fortemente e per il quale ha realizzato un piano di lancio dedicato, che consenta una distribuzione commerciale del prodotto su larga scala.
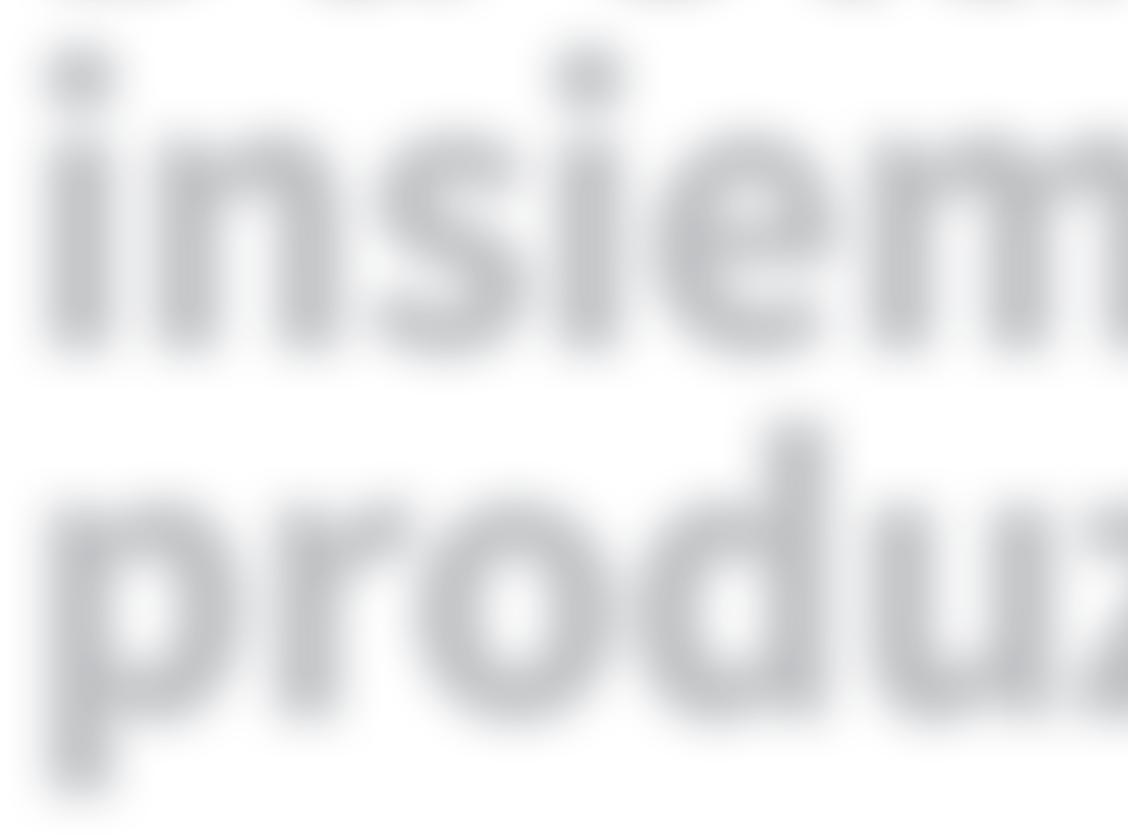
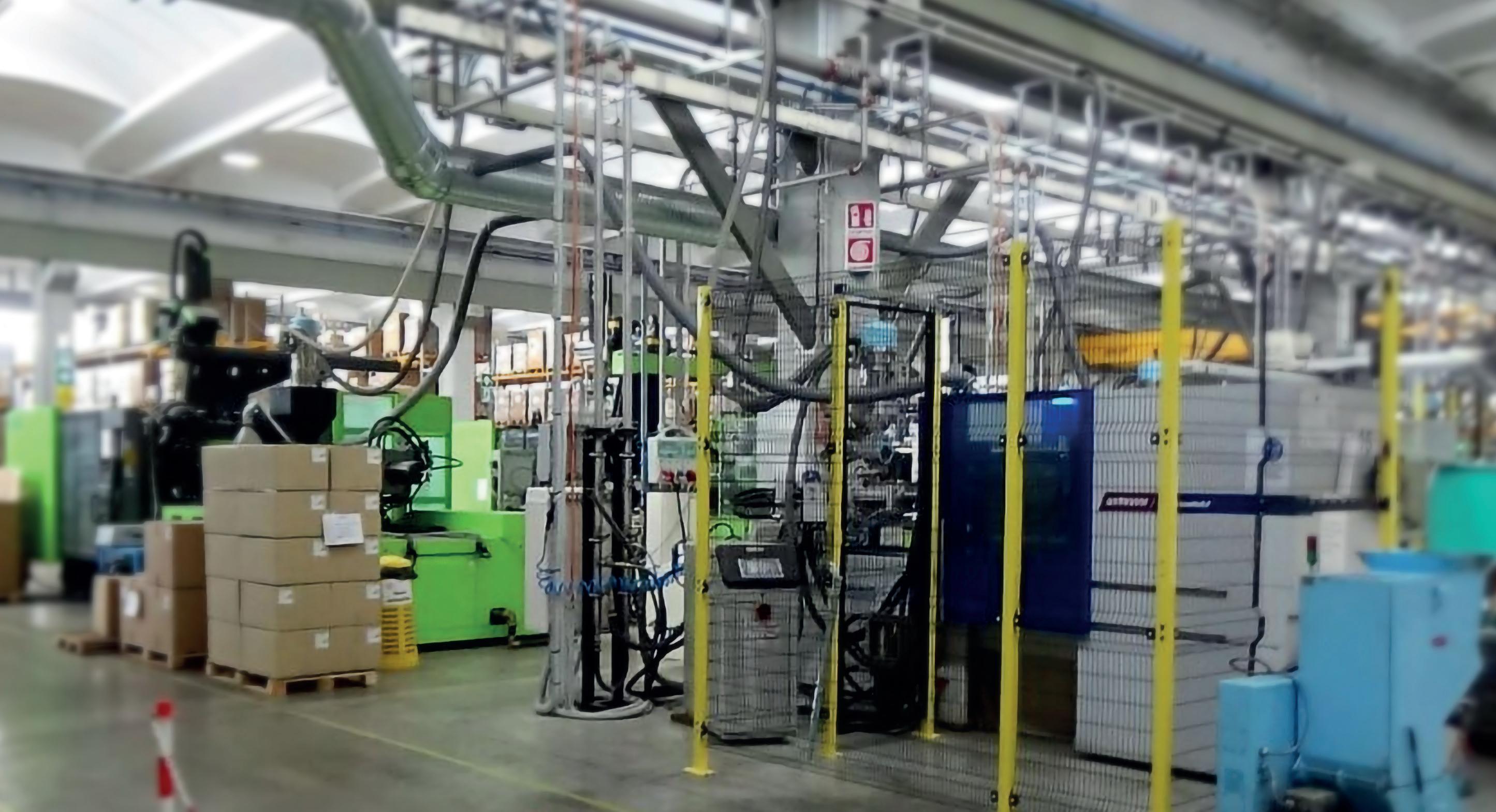
La collaborazione con Frigel
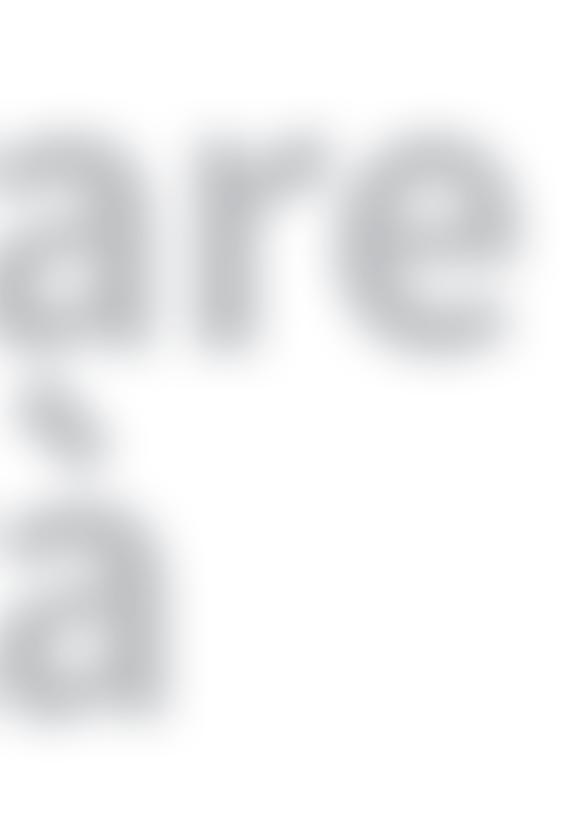
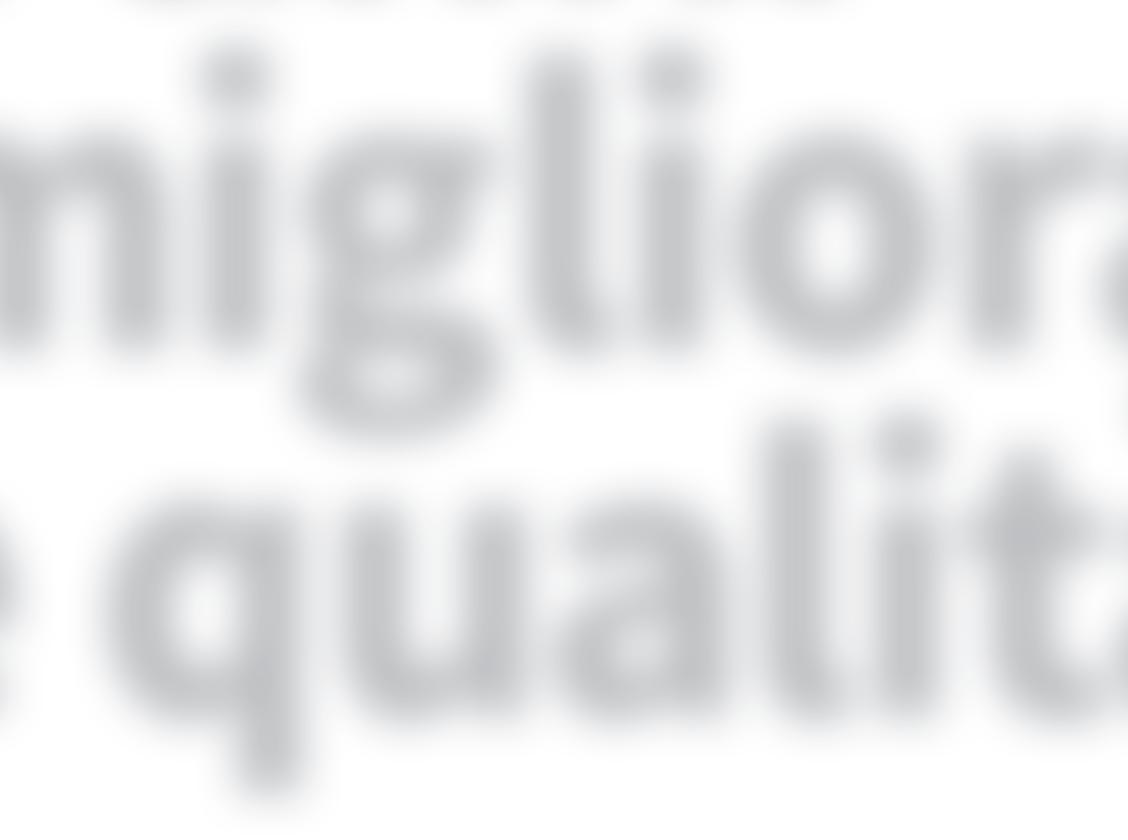
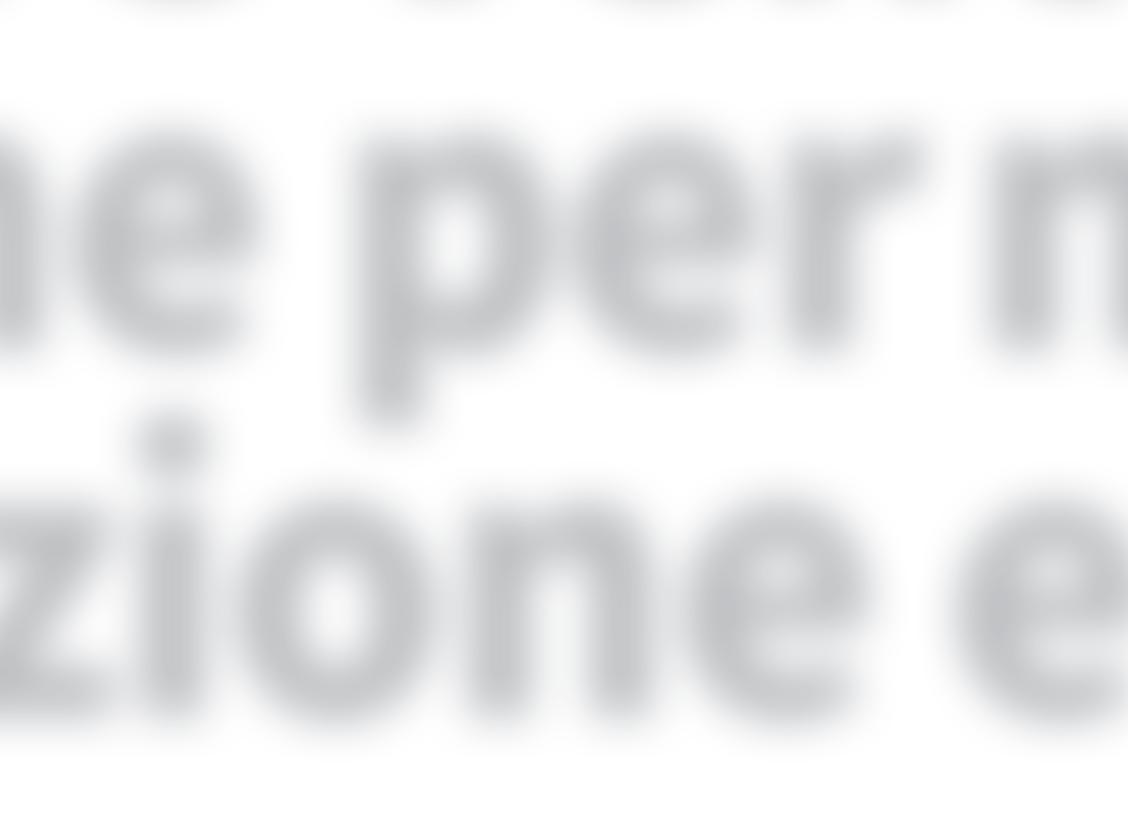
Sono oltre vent’anni anni che GelliPlast si affida a Frigel per soluzioni progettate su misura per il raffreddamento dei processi di stampaggio a iniezione. “Possiamo affermare che siamo cresciuti insieme, l’uno ha visto crescere l’altro e viceversa. Frigel ci ha sempre offerto livelli di qualità, prodotto e assistenza impareggiabili”, ha dichiarato Filippo Gelli, production manager dell’azienda.
Su ognuna delle 25 presse è presente almeno un’unità Frigel, cui GelliPlast continua a dare fiducia. Le unità di termoregolazione Microgel (tra quelle che il costruttore proporrà a Plast 2023) gestiscono in modo intelligente centinaia di stampi diversi che si intervallano settimana dopo settimana. “Ogni pressa ha le sue ricette impostate direttamente sul Microgel, ricette che possono essere riutilizzate nel tempo, ciò rende tutto più semplice e ben pianificato. Il responsabile di linea tiene sotto controllo la produzione e ha la possibilità di agire direttamente sui parametri di termoregolazione per ottimizzare la qualità del pezzo e ridurre gli scarti”, ha proseguito il production manager.
In particolare, i risultati ottenuti dal nuovo modello Microgel Syncro, che inizialmente Frigel aveva proposto in prova, sono stati sorprendenti. Viste le prestazioni ottenute, GelliPlast ha scelto la nuova tecnologia Syncro come standard per tutte le nuove installazioni.
Il supporto modulare Flexy Dream da applicare alle doghe del letto, stampato da GelliPlast anche grazie all’ausilio delle unità di termoregolazione di Frigel.
In primo piano una unità fornita a GelliPlast installata per la termoregolazione dello stampaggio a iniezione di componenti tecnici.
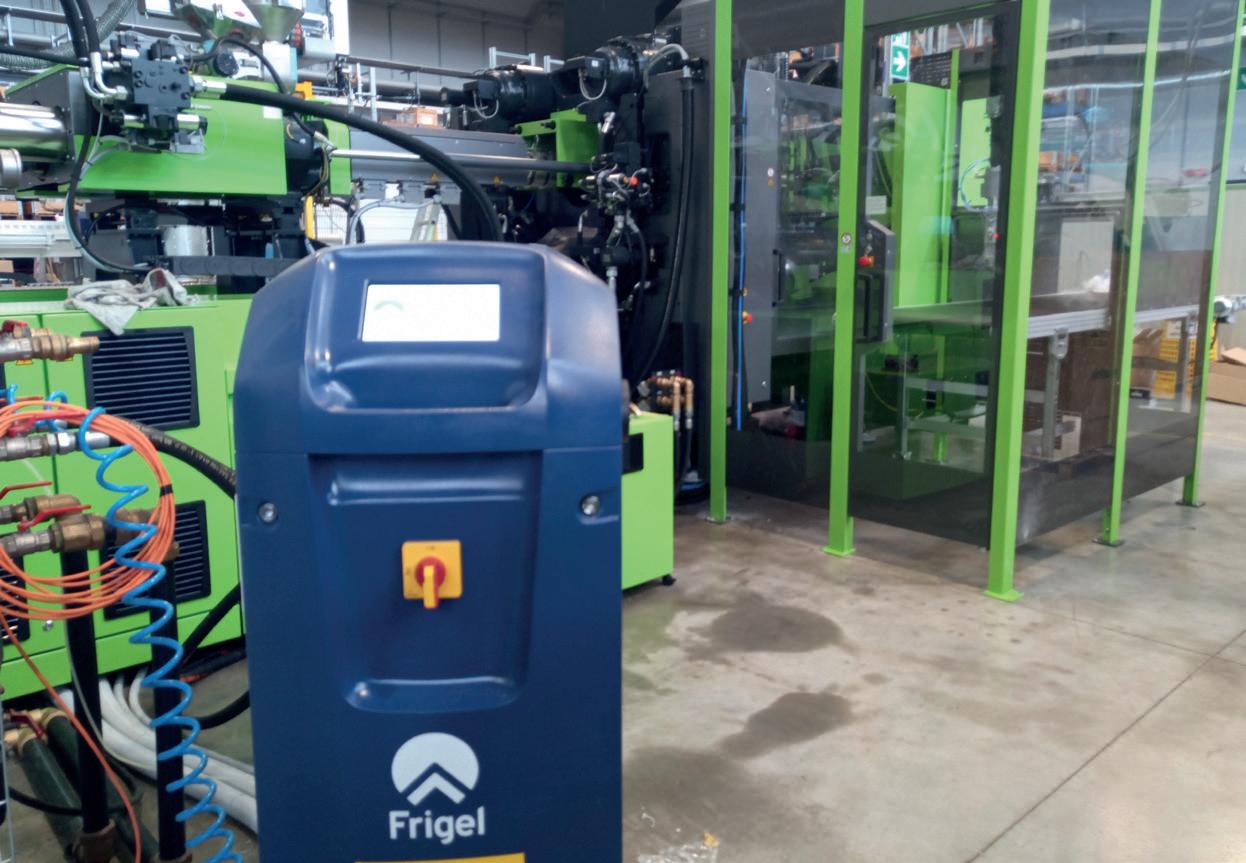
La tecnologia Syncro
Il Microgel RSY Syncro sta introducendo un nuovo approccio nella termoregolazione dello stampaggio a iniezione di pezzi tecnici, che si basa alla completa integrazione tra il sistema di controllo della temperatura dello stampo e il processo di iniezione e stampaggio. Consente una significativa riduzione del tempo ciclo, fino al 40%, garantendo un’altissima qualità del prodotto finito.
Sincronizzato digitalmente con lo stampo, Microgel Syncro eroga acqua fredda solo durante la fase di raffreddamento, riducendo drasticamente il tempo di raffreddamento e mantenendo calde le cavità dello stampo durante la fase di iniezione. Grazie alla forte riduzione del tempo di raffreddamento incrementa la produttività fino al 60%; in termini di tolleranze dimensionali, caratteristiche strutturali e finitura estetica grazie a un migliore riempimento dello stampo, migliora la qualità del prodotto; grazie alla riduzione della pressione di iniezione, al minor consumo di canali caldi e alla minore forza di chiusura, utilizza in modo intelligente il consumo di energia.
I risultati ottenuti
Tramite un tool online GelliPlast ha effettuato, con il supporto di Frigel, il fine tuning della macchina, trovando la migliore ricetta per l’applicazione Flexy Dream. “Il tempo ciclo da 62 secondi è passato a 50 secondi, con un decremento di circa il 20%, a fronte di un conseguente aumento della produttività”, ha aggiunto Filippo Gelli.
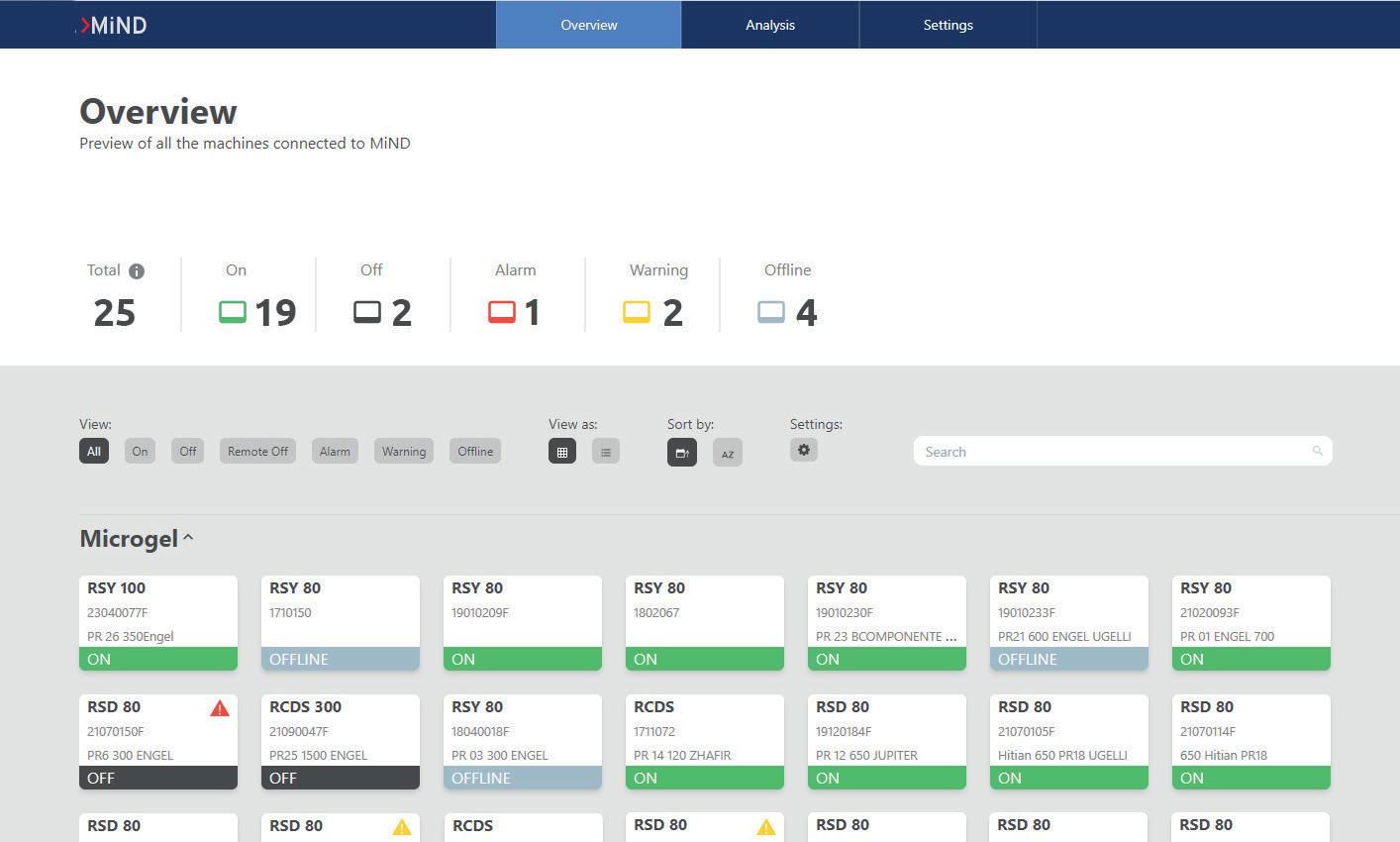
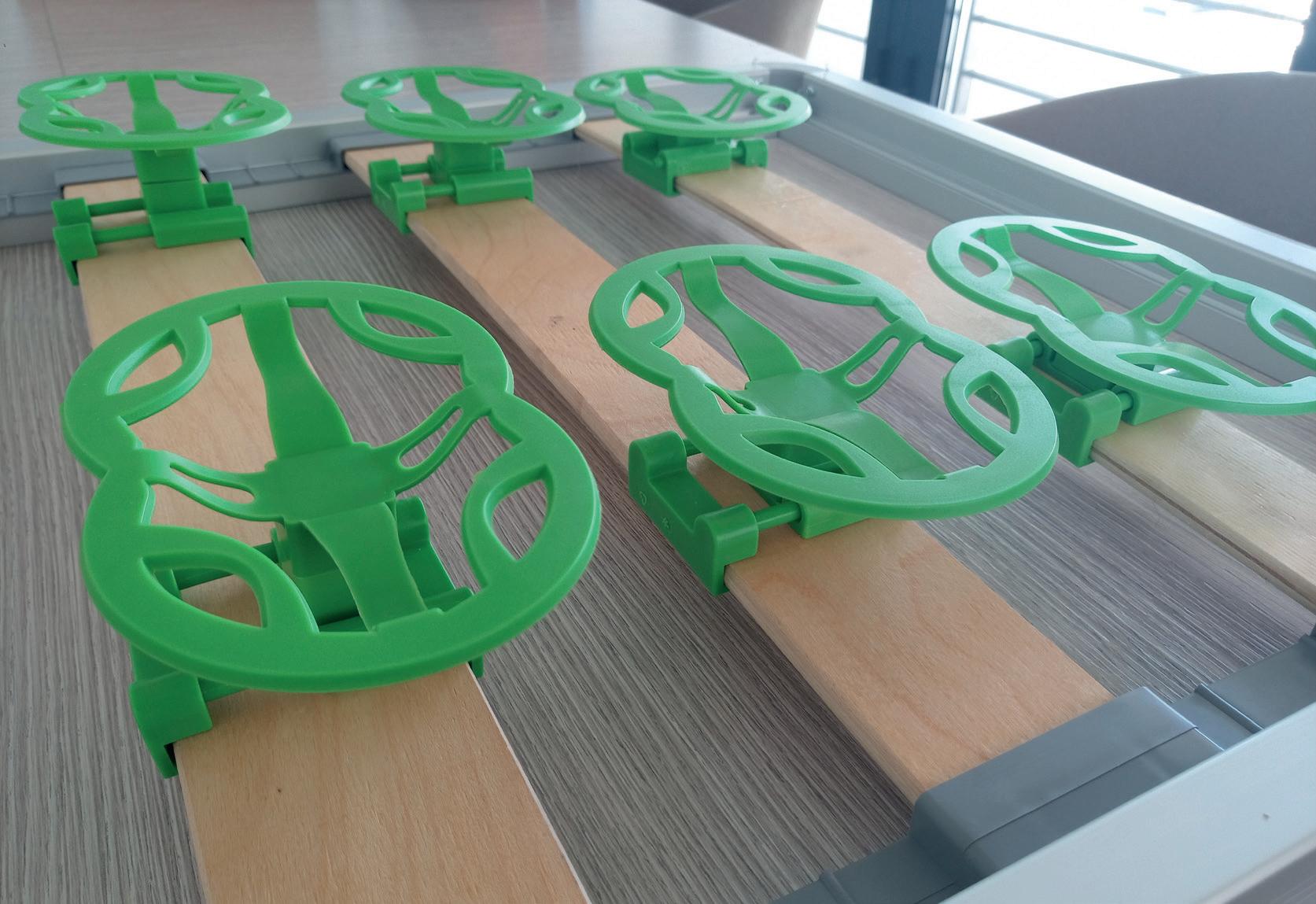
Un report di prestazioni dell’unità viene inviato settimanalmente con i dettagli relativi alla produzione e al funzionamento della macchina. L’adozione del Microgel RSY Syncro ha permesso a GelliPlast di raggiungere risultati sorprendenti, aumentando la propria competitività sul mercato nel proporre il nuovo prodotto Flexy Dream. “L’adozione del Microgel Syncro ci ha offerto la possibilità di aggiudicarci una commessa che altrimenti avremmo perso. La riduzione del tempo ciclo, degli scarti e dei tempi morti ci ha consenti-to di abbassare sensibilmente i costi di produzione”, ha spiegato ancora il production manager.
La supervisione da remoto
Il progetto ha previsto anche l’installazione del Netgel MiND, un sistema di supervisione che monitora in tempo reale ogni singolo macchinario Frigel presente sull’impianto. MiND è la soluzione ideale di diagnostica che può facilitare il processo di trasformazione aziendale verso l’Industria 4.0. Rende immediata la lettura e l’analisi dei dati in qualsiasi momento, su qualsiasi dispositio. “MiND ci consente di tenere sotto controllo la produzione in qualsiasi momento della giornata, anche quando siamo via per lavoro o in vacanza. Se l’impianto di nuova generazione non fosse monitorato dal MiND non ci sentiremmo così tranquilli come siamo adesso”, ha commentato Gelli.
MiND si è rivelato molto utile per GelliPlast, consentendo di risolvere con celerità delle problematiche che in altri casi avrebbero bloccato la produzione per molto tempo. “Da fuori ufficio riesco a ricevere gli alert di blocco macchina/impianto sul mio smartphone. Posso contattare immediatamente il responsabile di turno per verificare gli impianti. In poche decine di minuti, analizzando la tipologia e la localizzazione dell’errore è possibile individuare il problema con sufficiente facilità, per esempio il filtro dell’acqua ostruito. Grazie a MiND e alla reattività del service Frigel una piccola complicanza viene risolta velocemente. Anni fa episodi simili avrebbero fermato la produzione per ore”, ha concluso Filippo Gelli.
MiND, nella foto una schermata, è il sistema di supervisione che monitora in tempo reale ogni singolo macchinario di Frigel presente nel reparto di produzione.
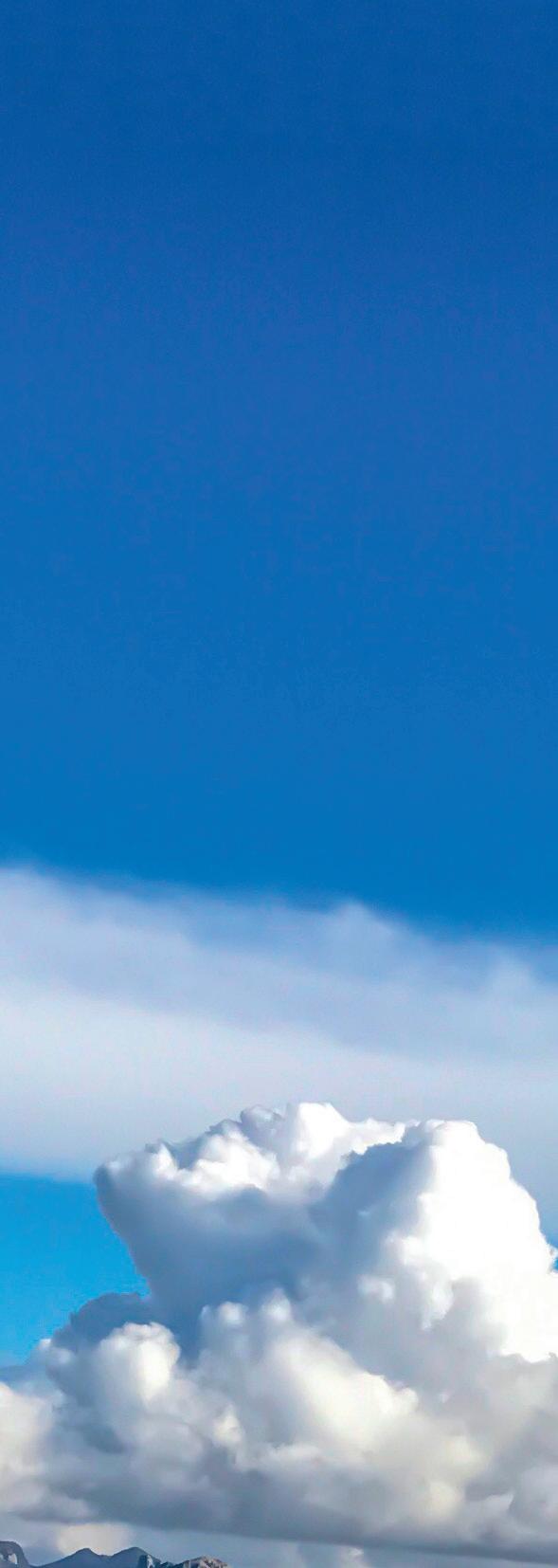

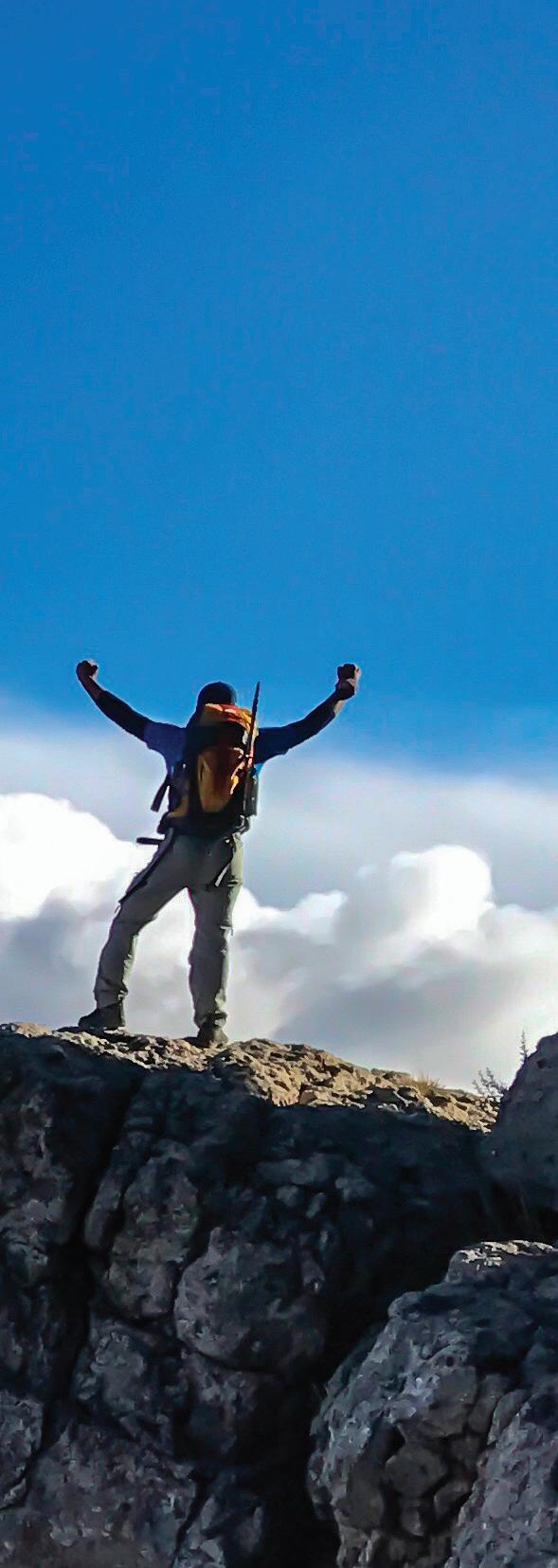
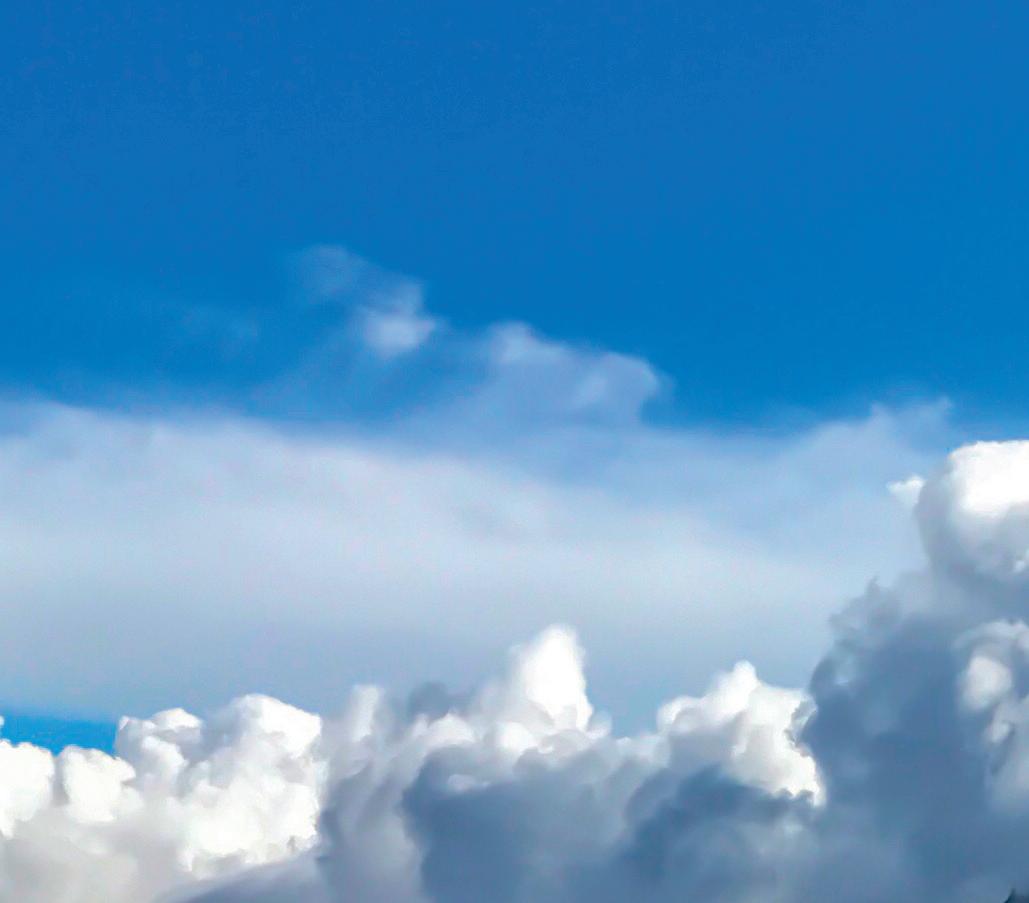

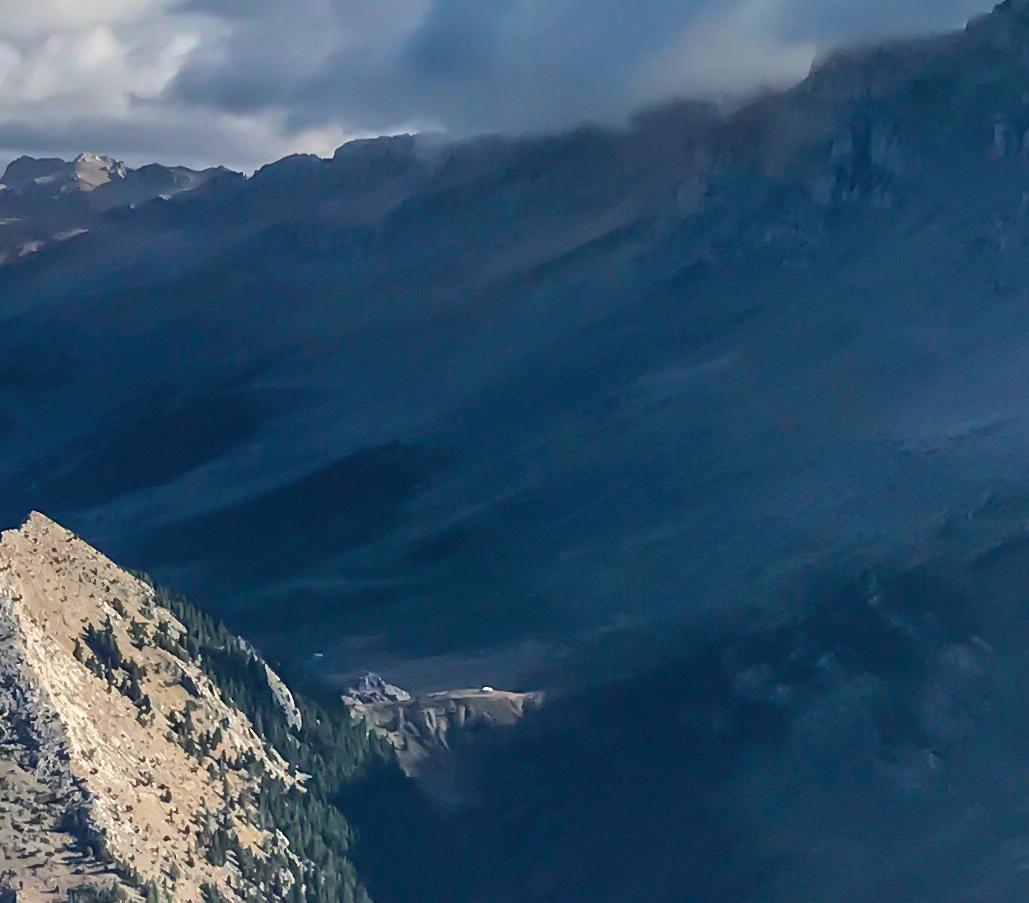
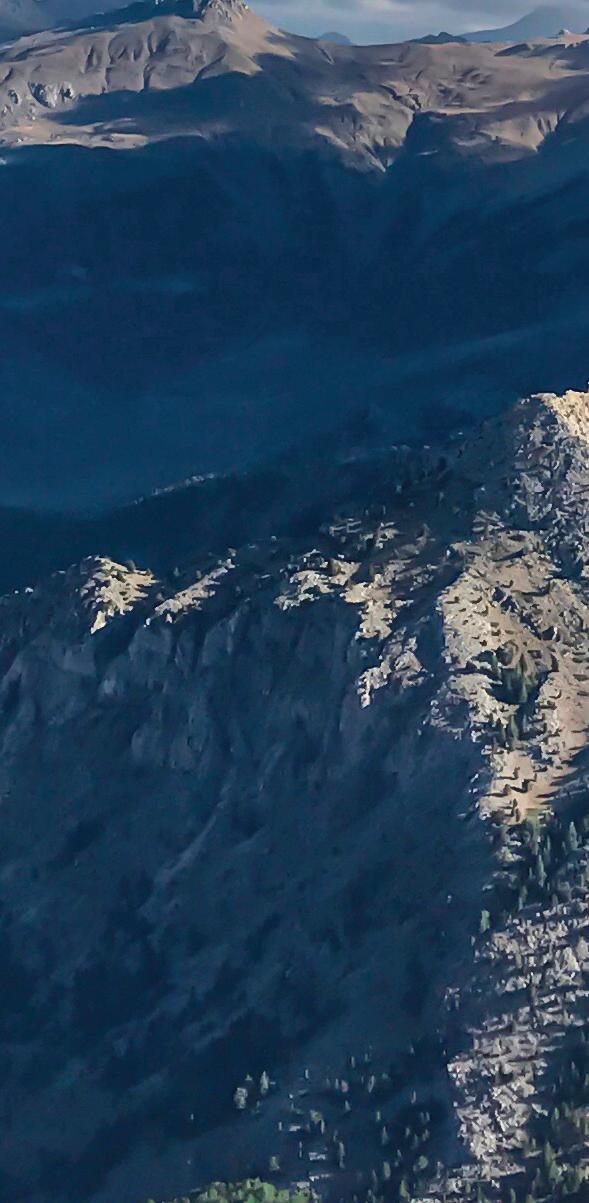



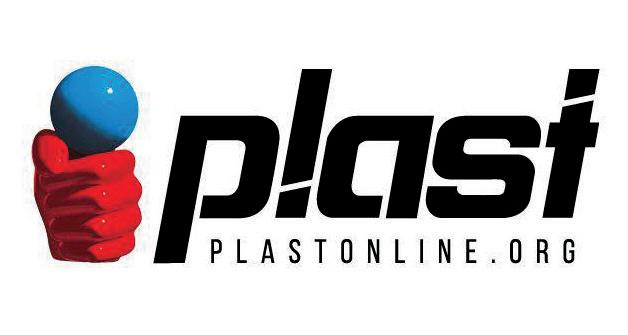
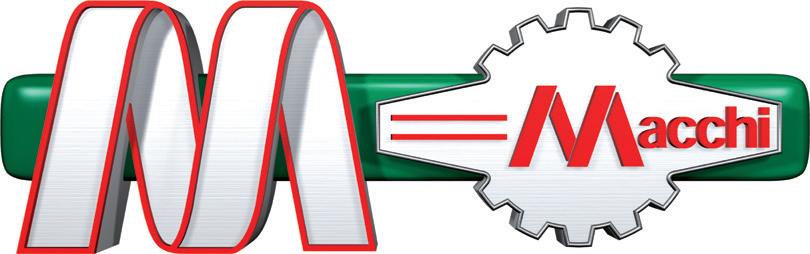
Ampia e variegata la gamma di soluzioni con cui CMG si presenta a Plast 2023 per il comparto del riciclo. Tutte caratterizzate da tratti innovativi in grado di renderle efficienti e flessibili per adattarsi ai diversi processi di trasformazione.
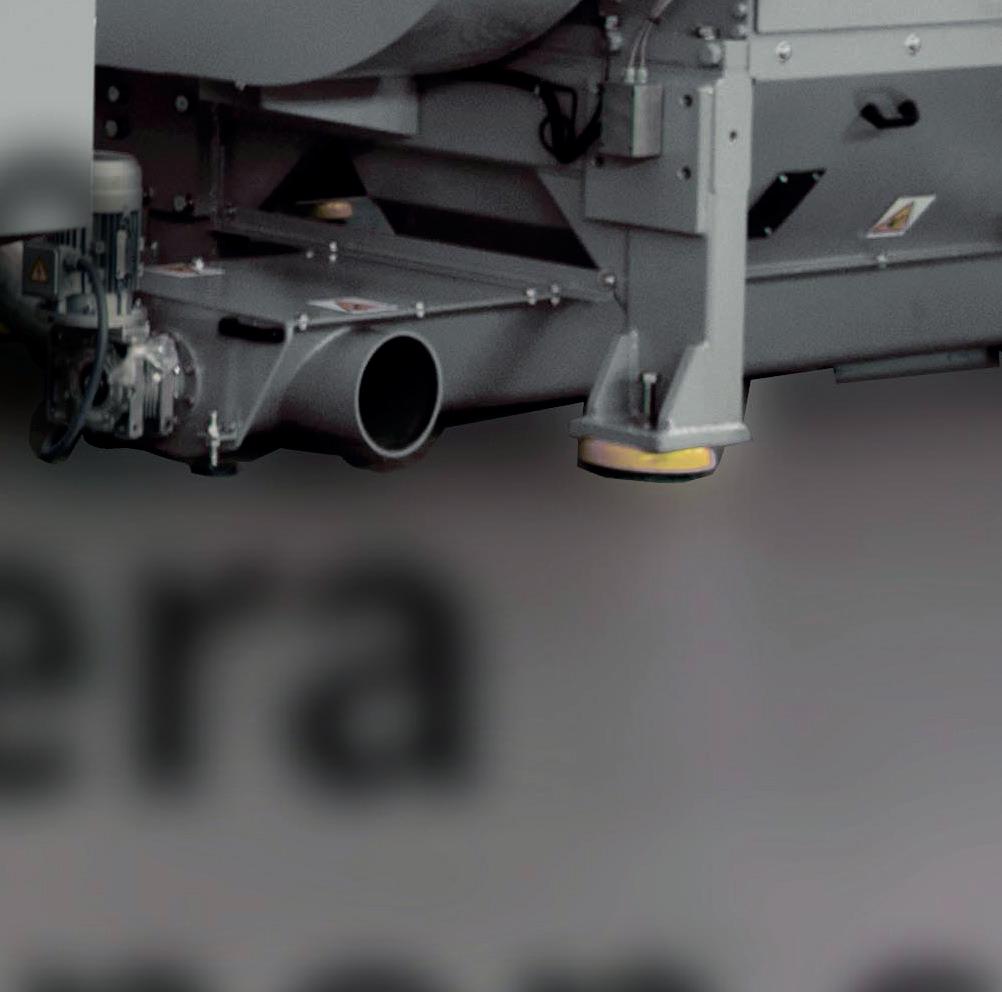
Soluzioni innovative per il riciclo ad alta efficienza energetica e sostenibili compongono la proposta espositiva di CMG Granulators a Plast 2023, i cui riflettori sono puntati anzitutto sulla nuova camera di taglio per la serie di granulatori Evoluzione, la cui caratteristica di spicco è rappresentata dalla configurazione del rotore, che permette alle lame rotanti di tagliare il materiale plastico perpendicolarmente contro le lame fisse, ottenendo così una elevata precisione di taglio. Le lame sono montate direttamente sull’estremità della staffa di supporto e non su un blocco lama, così che l’elevata inclinazione delle lame si traduca non solo in un processo efficiente, ma anche in interventi di manutenzione e sostituzione facili e veloci, cui contribuisce l’accessibilità frontale alla camera di tagli stessa.
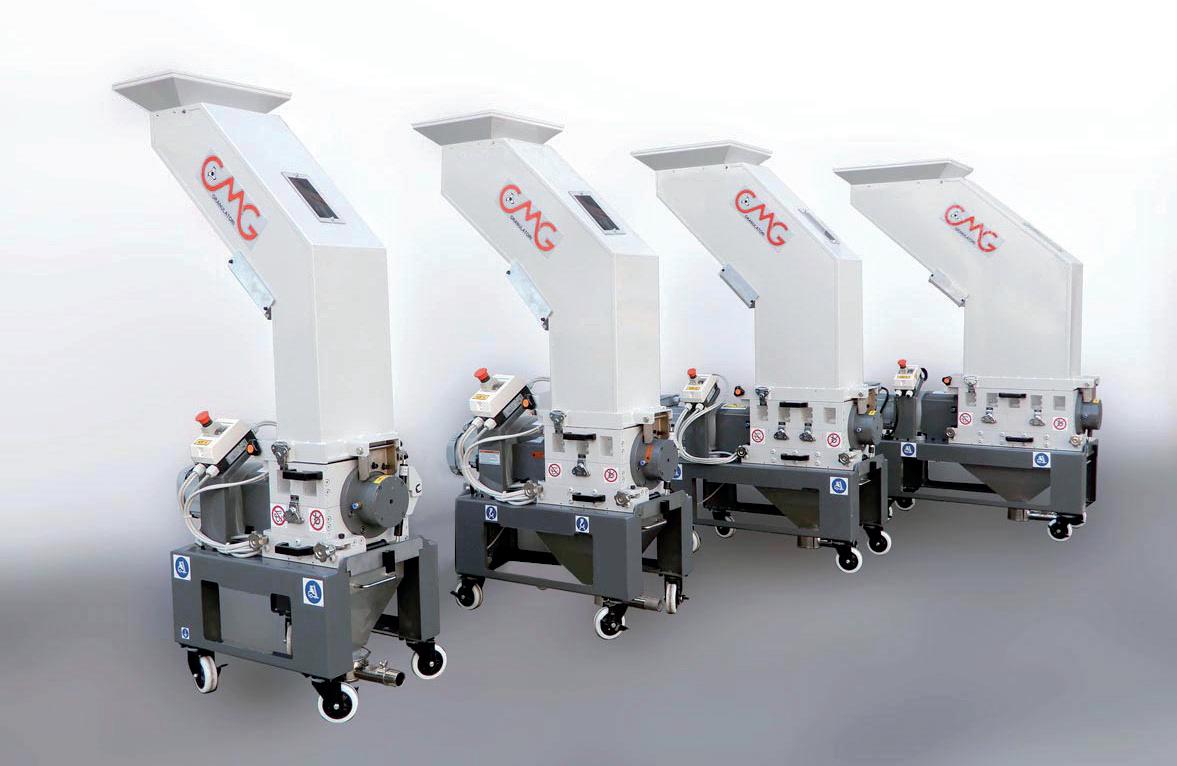
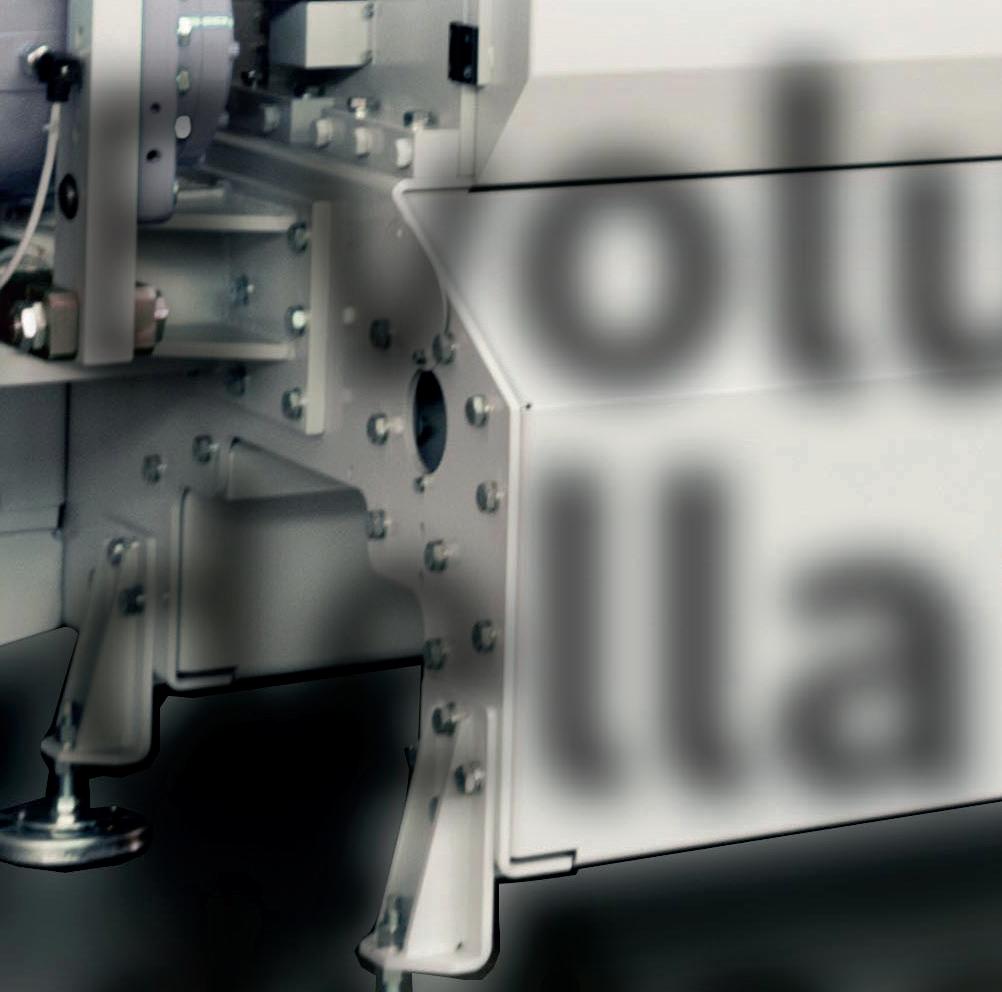
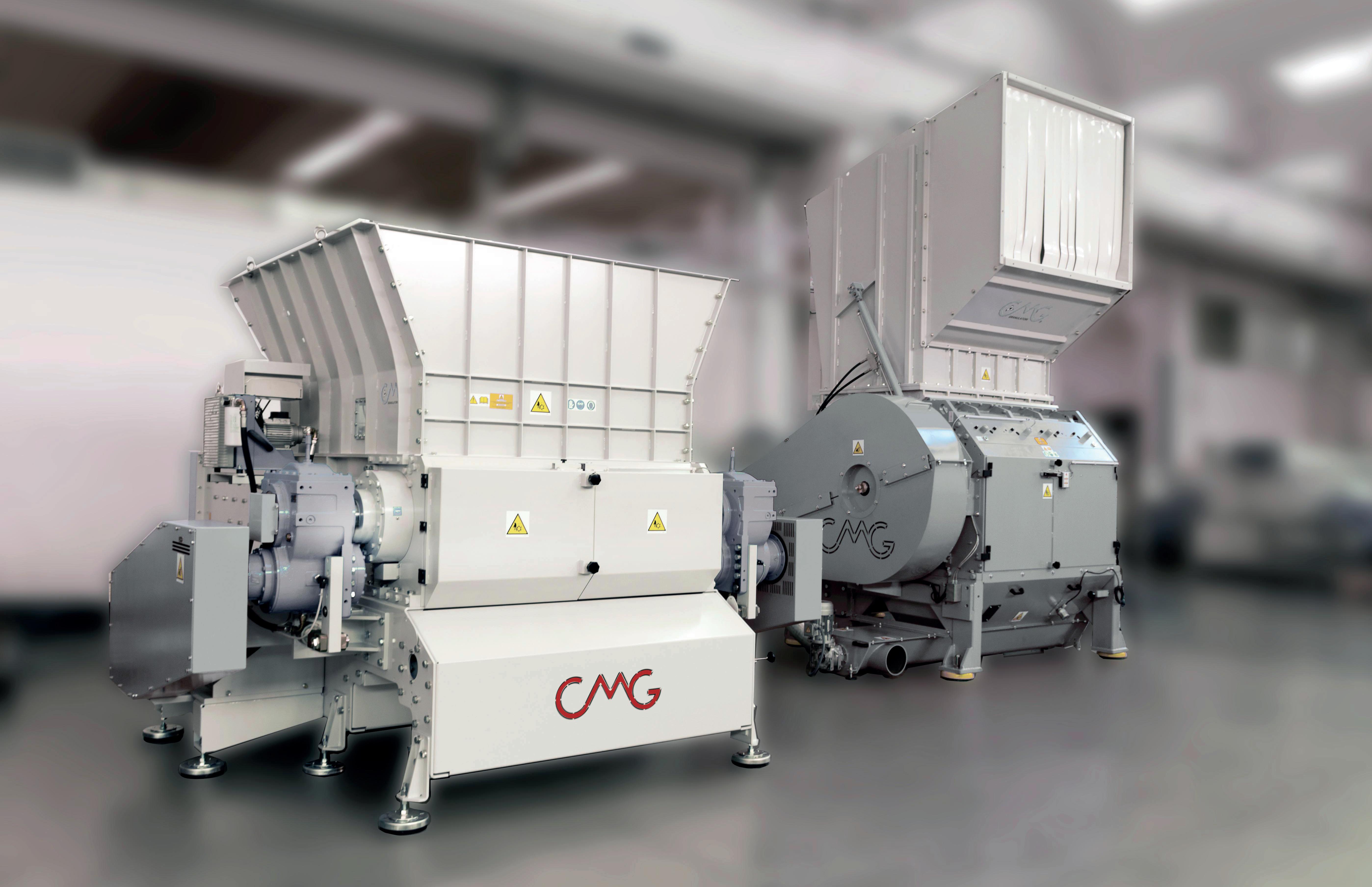
La rotazione del rotore non dà luogo all’effetto “trascinamento”, che si verifica quando la massa di materiale da macinare non ruota con il rotore, evitando così la generazione di polvere e piccole particelle, che diventano materiale di scarto nella fase di lavaggio. La produzione di microparticelle è ridotta a pochi punti percentuali, contro il 15% o più di un granulatore convenzionale.
Il design a rotore aperto permette di occupare solo il 30% dello spazio all’interno della camera di taglio, mentre il rapporto tra volume del rotore e della camera di taglio è di 30/70 rispetto a quello di 70/30 dei granulatori convenzionali. Questa caratteristica consente di introdurre più del doppio di materiale nella camera di taglio, aumentandone la capacità di granulazione. La camera di taglio presenta uno “sviluppo tangenziale”, che conferisce voracità e garanzia di ingestione del materiale da macinare, senza la necessità di ricorrere e sistemi di alimentazione forzata.

Super granulatori e trituratori ad alta efficienza
Con la nuova serie Evoluzione, CMG presenta i modelli EV916 ed EV616, soluzioni adatte alle condizioni operative più critiche, per la granulazione con acqua o a secco che richiedano elevate prestazioni, capacità di granulazione da 2.000 a oltre 5.000 kg all’ora, versatilità, efficienza e sostenibilità. La serie Evoluzione garantisce costanza operativa e resistenza all’usura elevate gra- zie alle soluzioni costruttive quali l’utilizzo di acciaio armonico e strutture modulari assemblate.
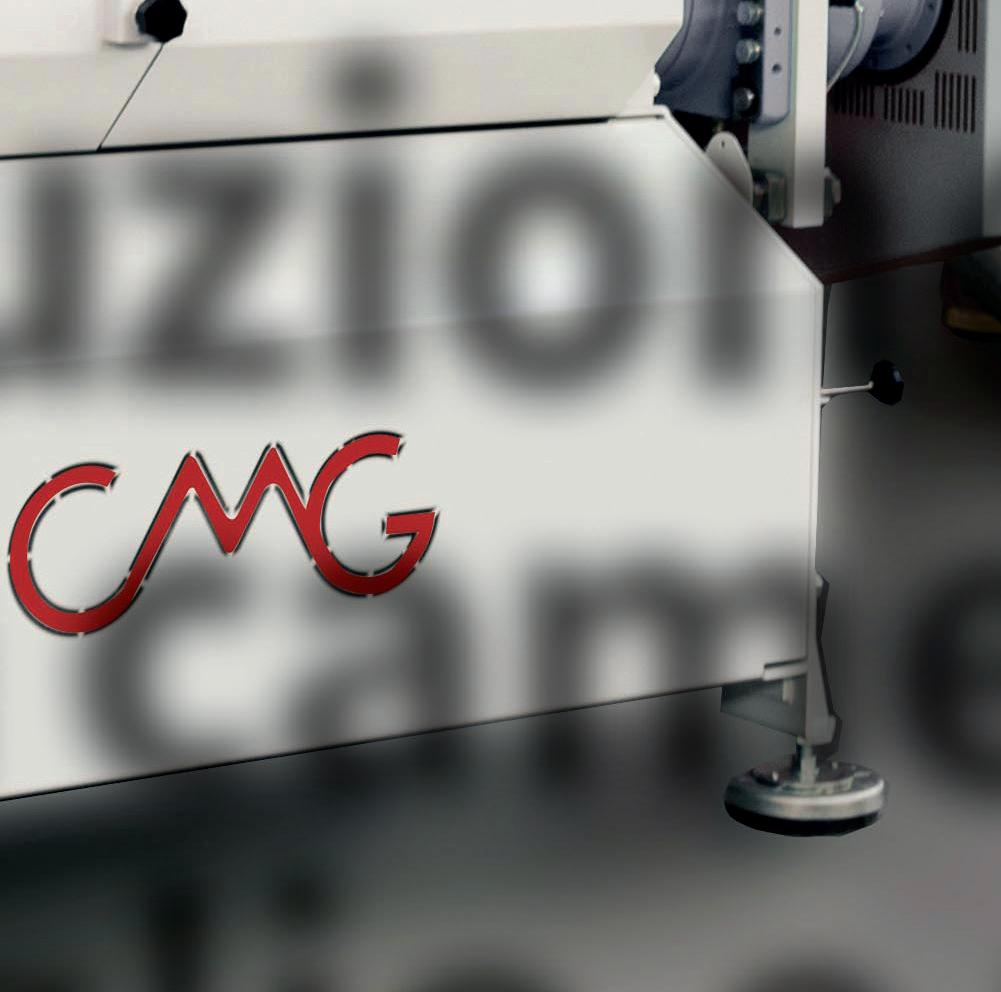
Rendering della nuova camera di taglio della serie Evoluzione.
Oltre alla precisione costruttiva al centesimo di millimetro, che consente una prolungata durata delle lame, tutti i modelli della serie sono dotati di controlli avanzati, in chiave Industria 4.0, per rendere l’operatività della macchina monitorabile e gestibile al 100%. Inoltre, parametri funzionali quali temperatura di esercizio, usura lame, produttività, efficienza operativa, utilizzo dell’energia sono tutti gestibili a bordo macchina o da remoto con connettività basata sul protocollo OPC-UA.
L’elevata precisione di taglio dei trituratori di CMG, derivante da un design brevettato dove la lama è inserita in un’apertura a V sul rotore, garantisce resistenza allo stress meccanico e prestazioni e fornisce omogeneità dimensionale e assenza di particelle di piccole dimensioni. Ogni trituratore è equipaggiato con comandi avanzati per regolare autonomamente la potenza del motore e gli RPM del rotore, ottenendo plastica macinata di qualità utilizzando la minore quantità di energia elettrica.
La gamma di trituratori TRM copre applicazioni da 200 a 1.500 kg all’ora ed è composta da quattro modelli, TRM600, TRM900, TRM1200 e TRM1500, tutti equipaggiati con il design brevettato delle lame e con comandi PLC intelligenti.
Granulatori per termoformatura, stampaggio, soffiaggio ed estrusione
CMG introduce i nuovi granulatori GT per il riciclo in linea degli scarti di produzione, in particolare lastre, scheletri e pezzi di scarto da termoformatura. La serie comprende quattro modelli adatti a coprire capacità da 200 a 1.000 kg all’ora. Anche in questi granulatori spicca il design delle lame del rotore, posizionate con un’inclinazione di 50° rispetto alla lama fissa, garantendo precisione di taglio, omogeneità dimensionale del rimacinato, ridotte sonore e assenza di polvere. La camera di taglio è assemblata a “spine e bulloni”, non utilizza componenti fusi o saldati e tutte le parti sono lavorate a CNC per ottenere una precisione di assemblaggio al centesimo di millimetro. Questi granulatori hanno un fabbisogno energetico di 20 Wh/kg, rispetto agli oltre 40 Wh/kg richiesta dalle unità convenzionali. Tutti i modelli GT sono ribassati e insonorizzati, in modo da poter essere posizionati sotto il nastro trasportatore delle macchine di trasformazione.

La gamma di granulatori G26 è invece stata sviluppata per l’impiego nei processi di stampaggio a iniezione, soffiaggio ed estrusione, le cui caratteristiche innovative sono finalizzate a ottenere produttività, qualità del rimacinato (omogeneità dimensionale delle particelle di rimacinato e assenza di polvere), efficienza di funzionamento, assenza di polvere e ridotto TCO. La gamma copre produzioni da 50 a 300 kg/ora e comprende i modelli G26-30, G26-45 e G26-60, le cui caratteristiche di punto sono rappresentate da insonorizzazione integrale e tramoggia di alimentazione progettata per accogliere la più ampia varietà di forme e dimensioni delle parti da macinare. Tutti i modelli funzionano in condizioni di alta efficienza, montano motori EISA “premium-efficiency”, possono essere dotati della funzione AMP (Adaptive Motor Power) e hanno un fabbisogno energetico che si attesta anche in questo caso a 20 Wh/kg.

Anche i granulatori N55-90 e G35-60 esposti in fiera fanno parte di una gamma di 11 modelli sviluppati per la macinazione di contenitori soffiati e di articoli ingombranti con capacità da 20 a 1.500 kg all’ora.
La nuova serie di granulatori SL a bassa velocità e senza griglia proposta per il settore dello stampaggio tecnico comprende quattro modelli con capacità da 5 a 30 kg all’ora, progettati per ottenere rimacinato con forma e dimensioni estremamente omogenee e completamente privo di polvere, grazie a lame rotanti che, anziché fratturare o rompere i componenti da macinare, eseguono un taglio fine e preciso. Gli elementi di macinazione sono disponibili di tre diverse dimensioni, per ottenere granuli di dimensioni paragonabili a quelle dei granuli vergini e idonee al processo di iniezione, soprattutto su presse di ridotto tonnellaggio. Una piastra magnetica posizionata in corrispondenza dell’alimentazione del granulatore cattura i contaminanti metallici, evitando che danneggino il granulatore o la pressa a iniezione.
Un’ampia gamma di granulatori di CMG è disponibile nella configurazione ET2 per riciclare alla fonte i rifili da estrusione, la cui precisione di assemblaggio della camera di taglio permette la granulazione anche dei rifili più sottili.
Ultimi ma non ultimi, i granulatori G17 consentono di ottenere un rimacinato di dimensioni molto ridotte, oltre che di forma omogenea e completamente privo di polvere, che può essere aggiunto in percentuali più alte al materiale vergine senza influenzare la qualità del prodotto finito. I sistemi per piccoli lotti produttivi sono dotati di viti di plastificazione di piccolo diametro in grado di processare granuli con dimensioni maggiori a quelle del granulo vergine.
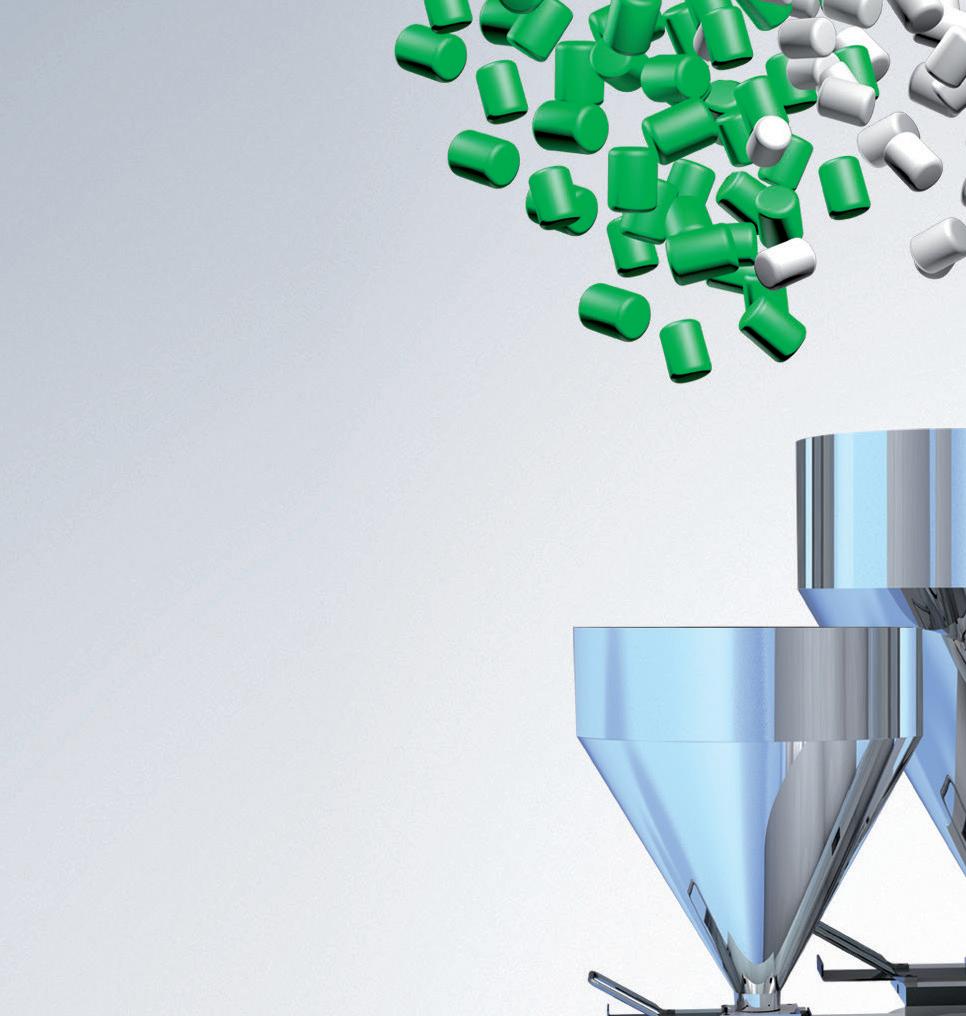

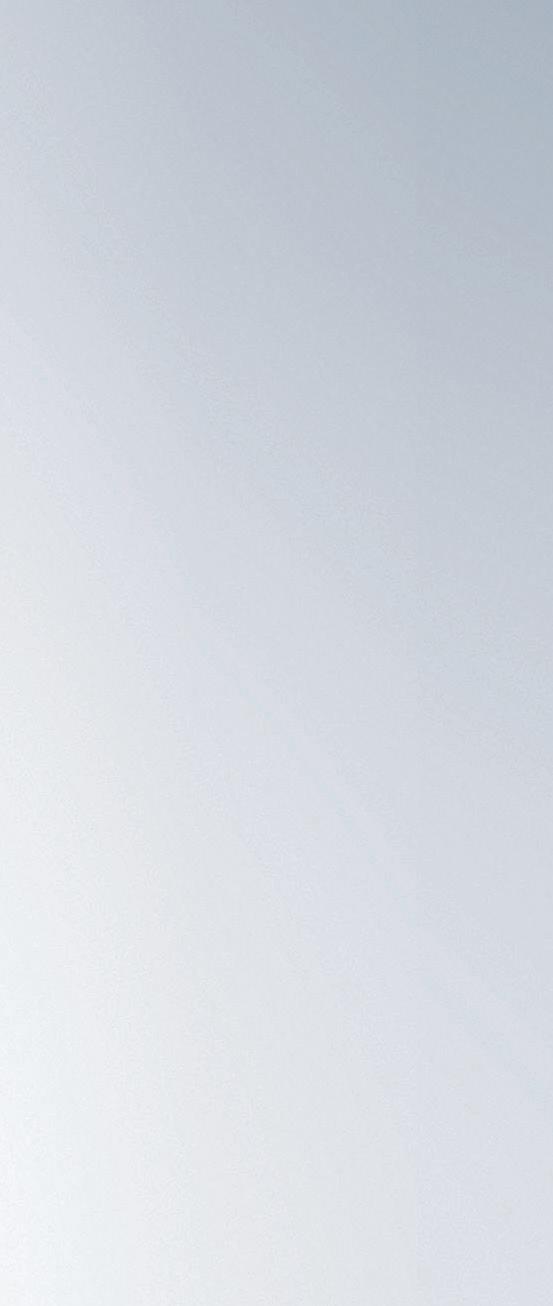

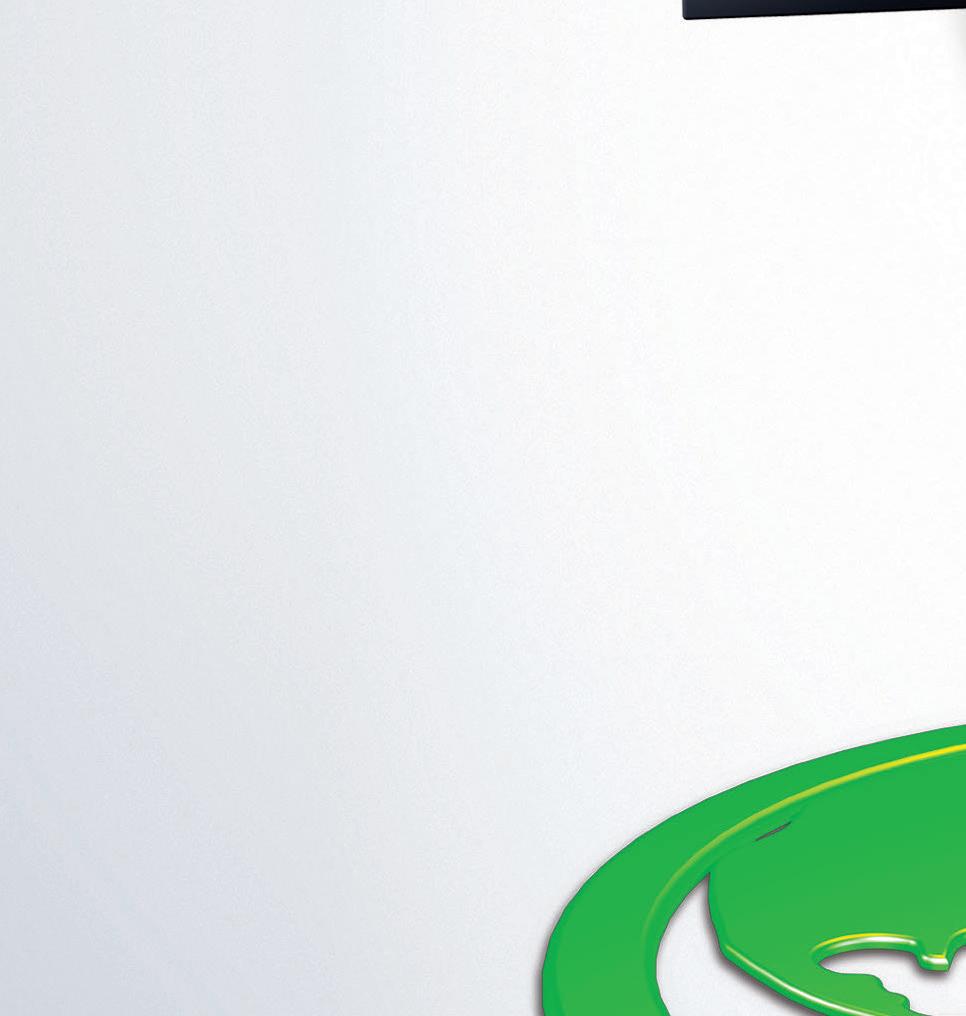
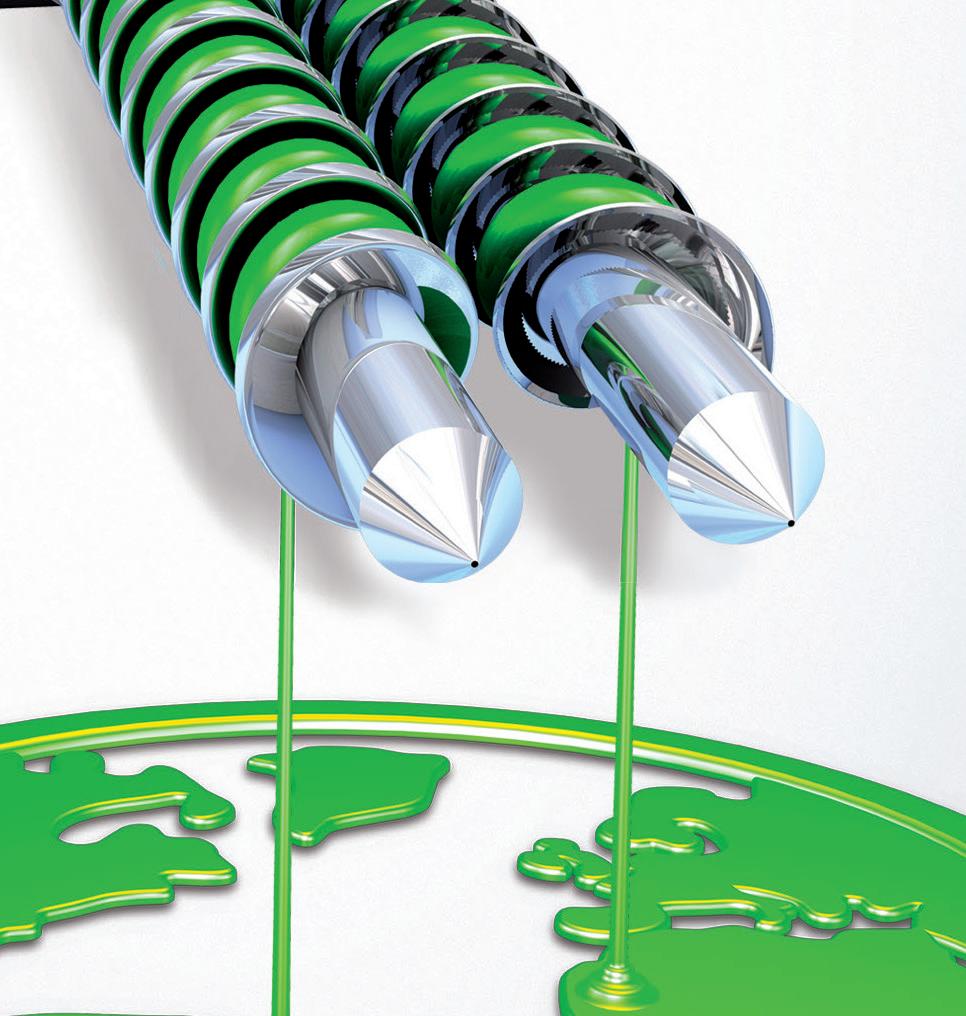
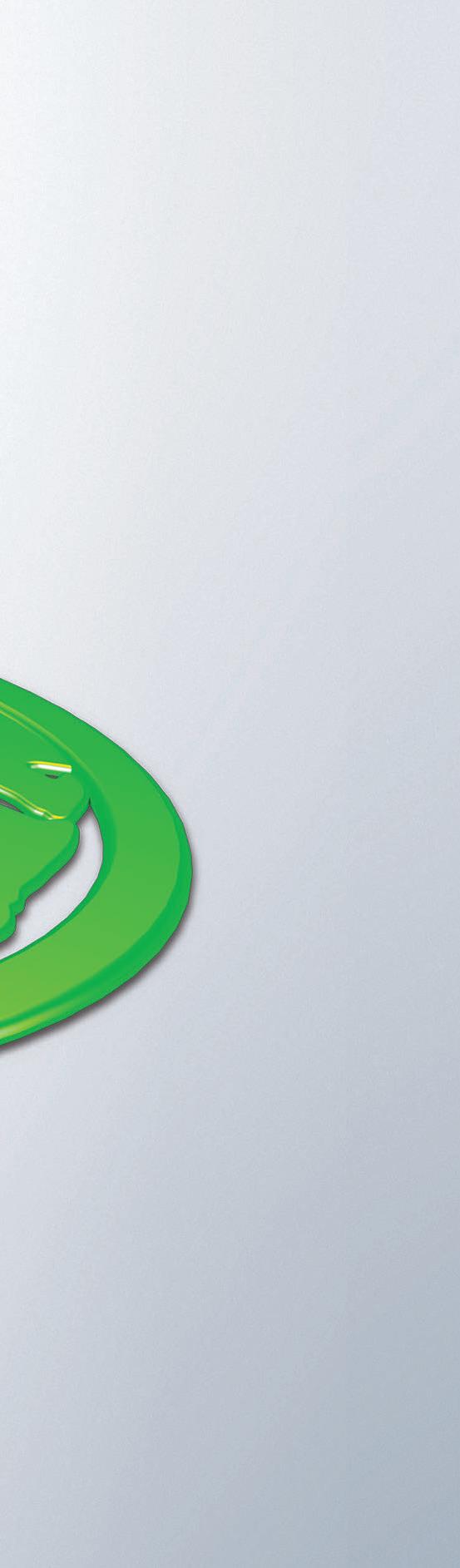
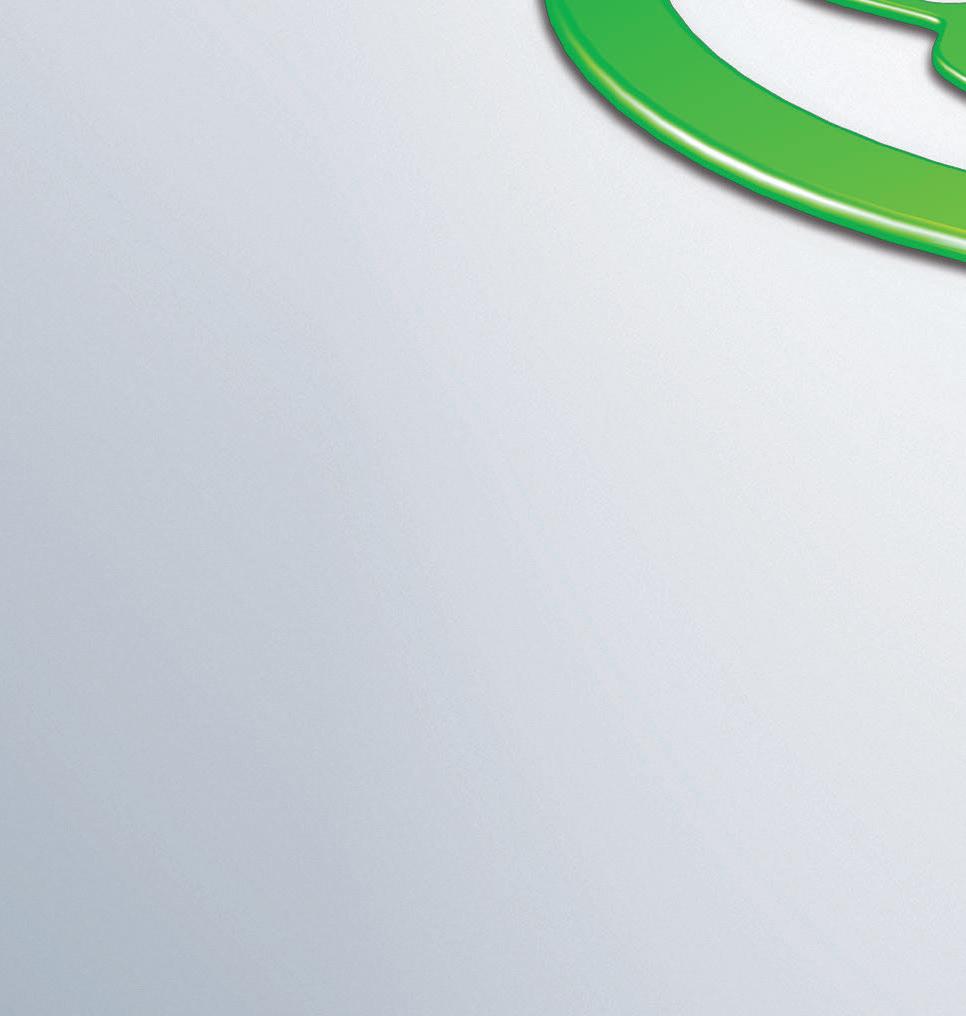


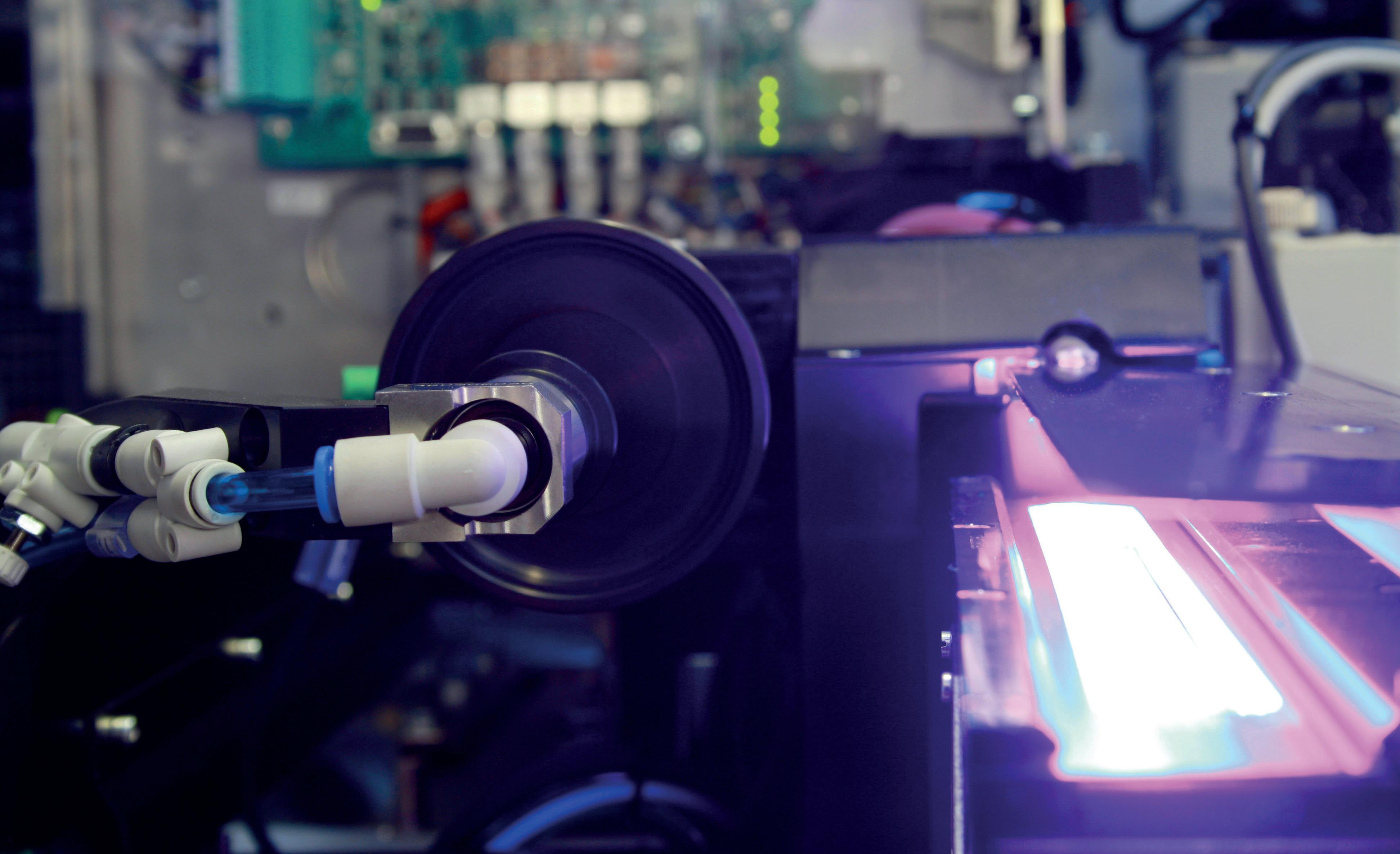
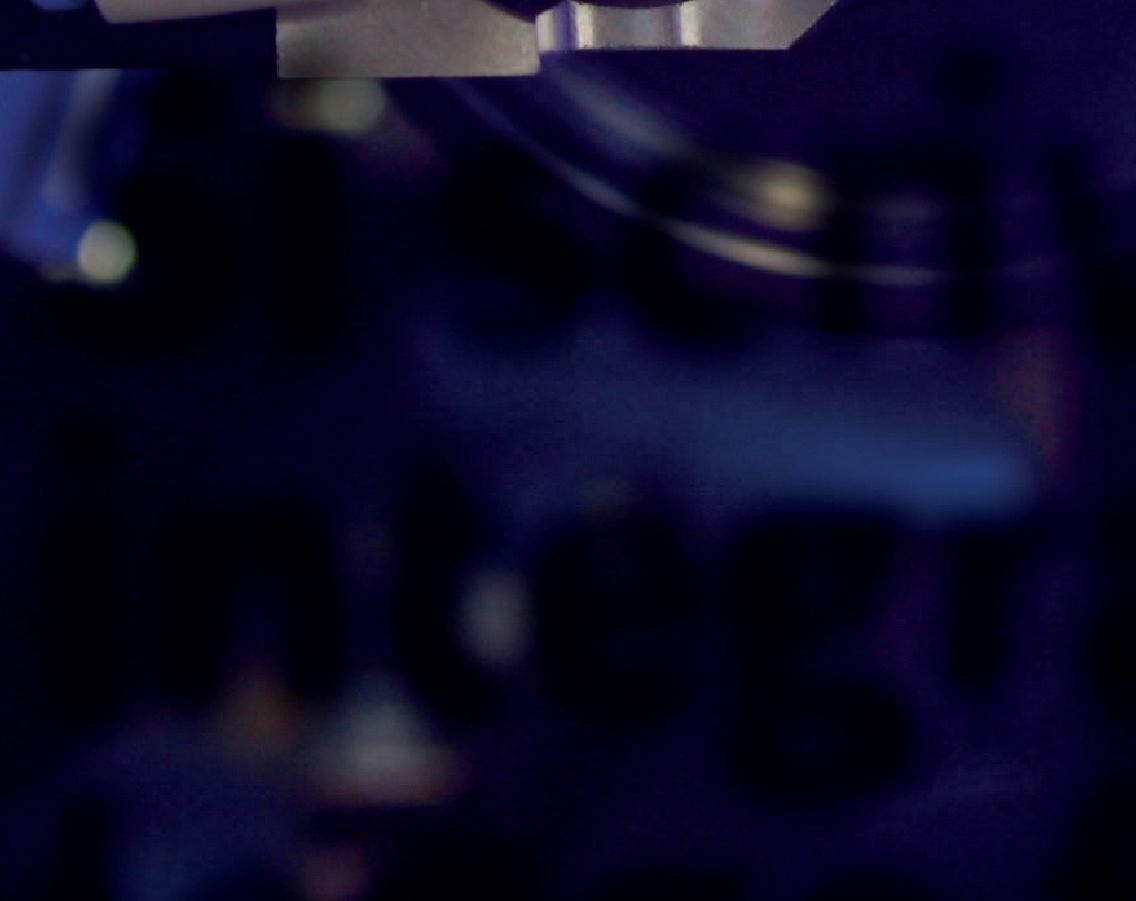
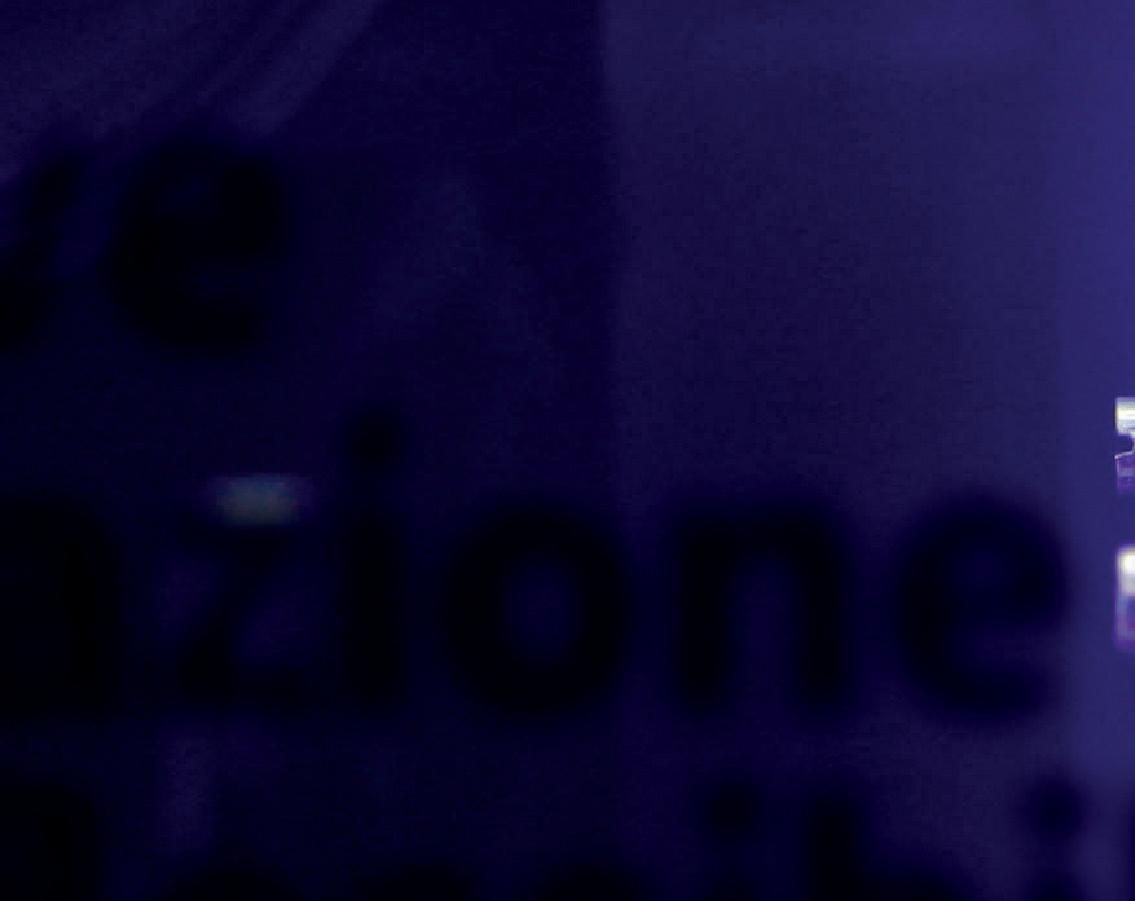
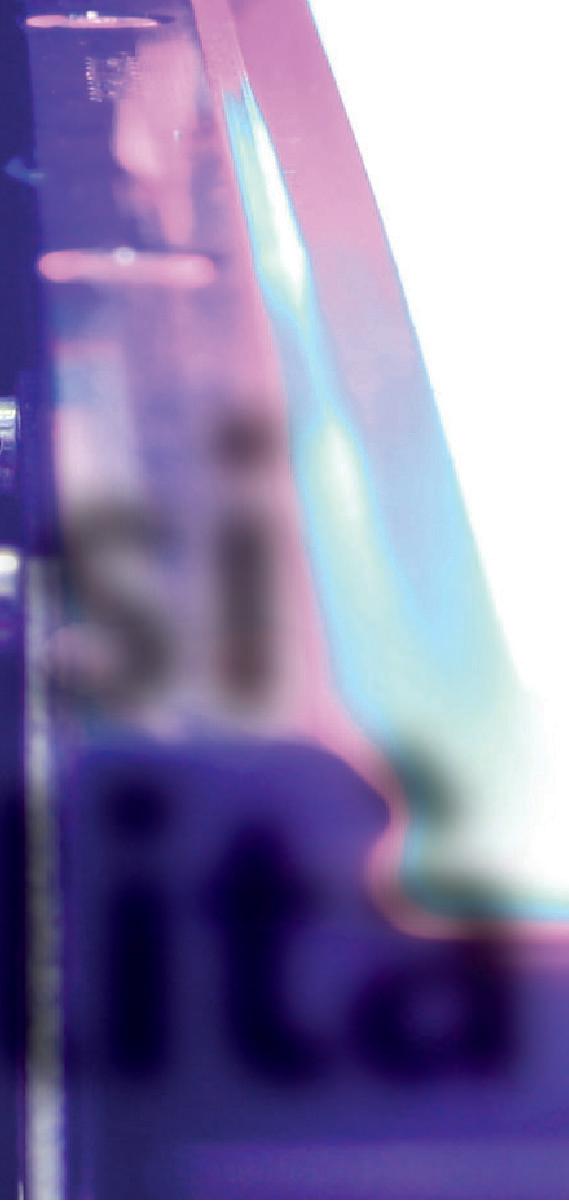

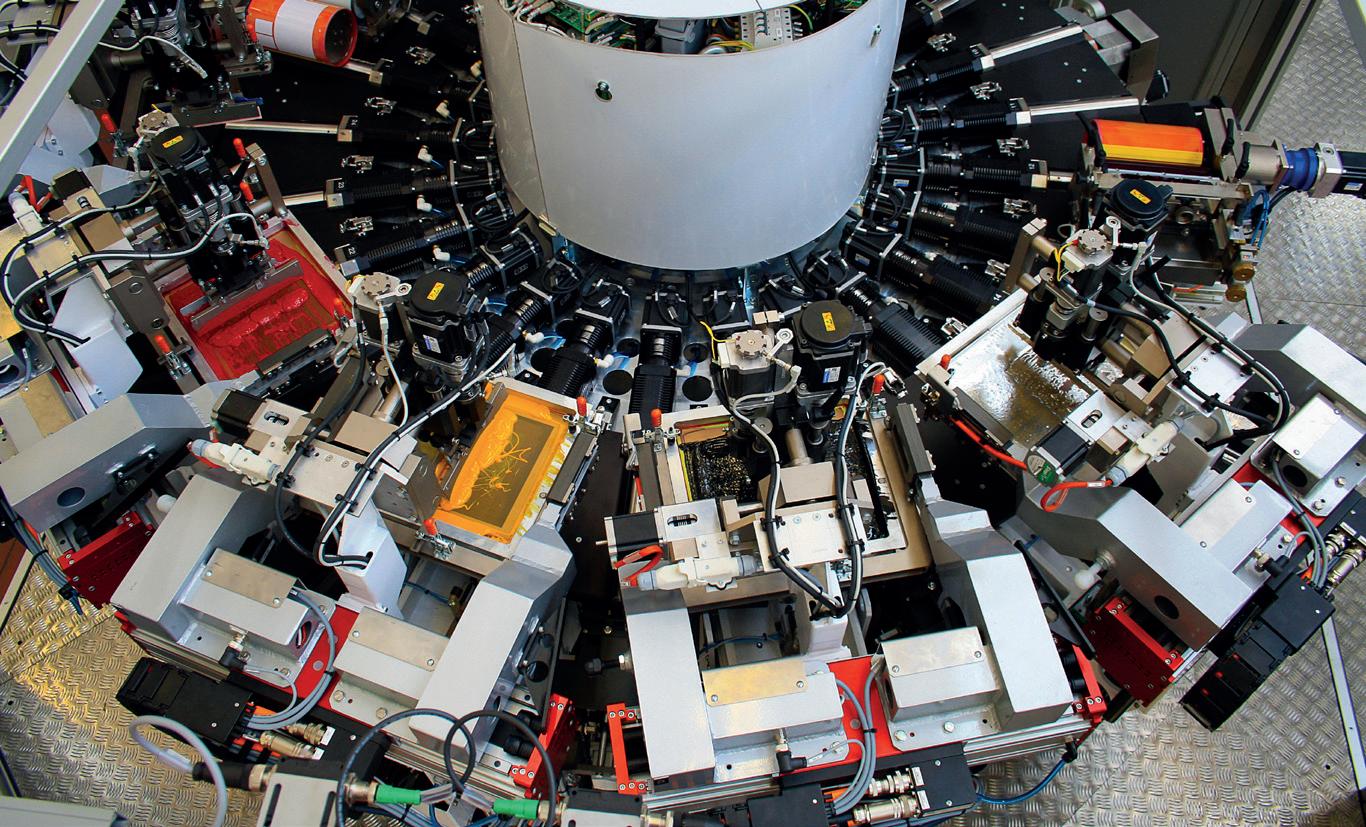
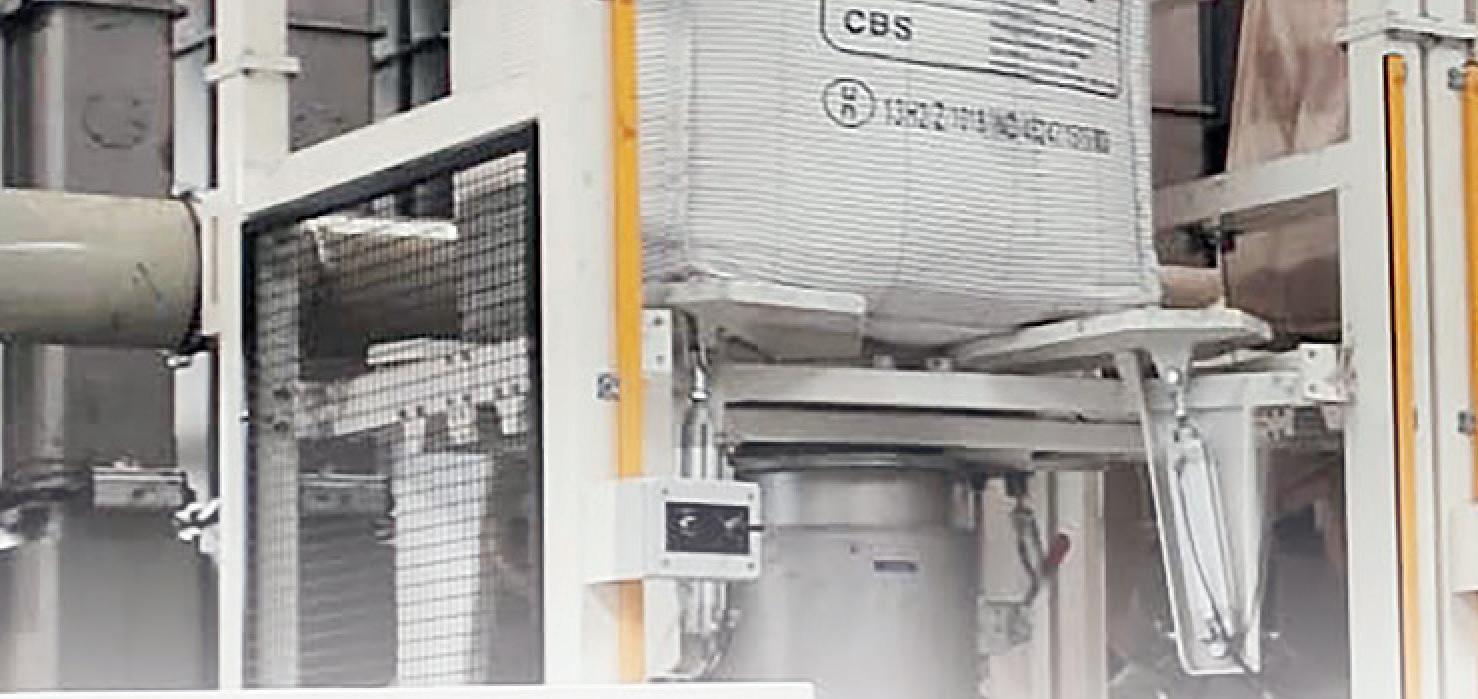
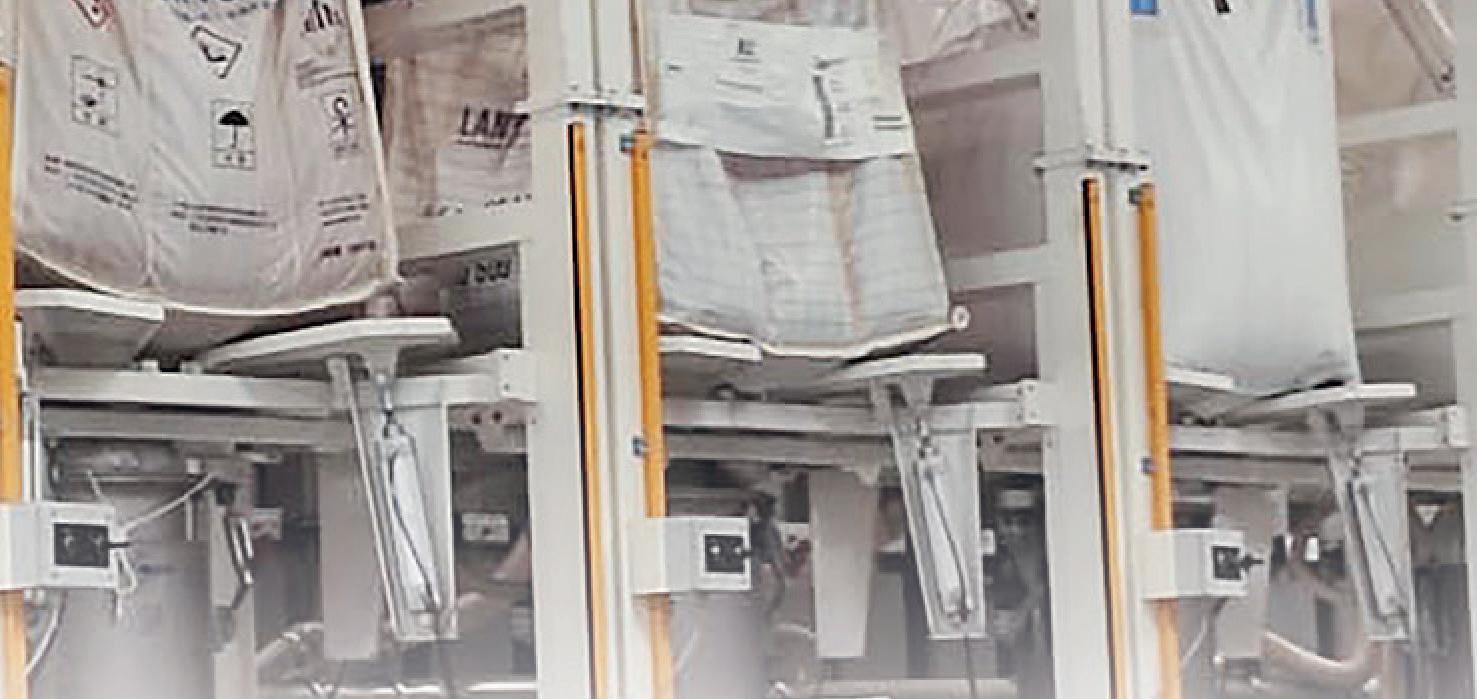

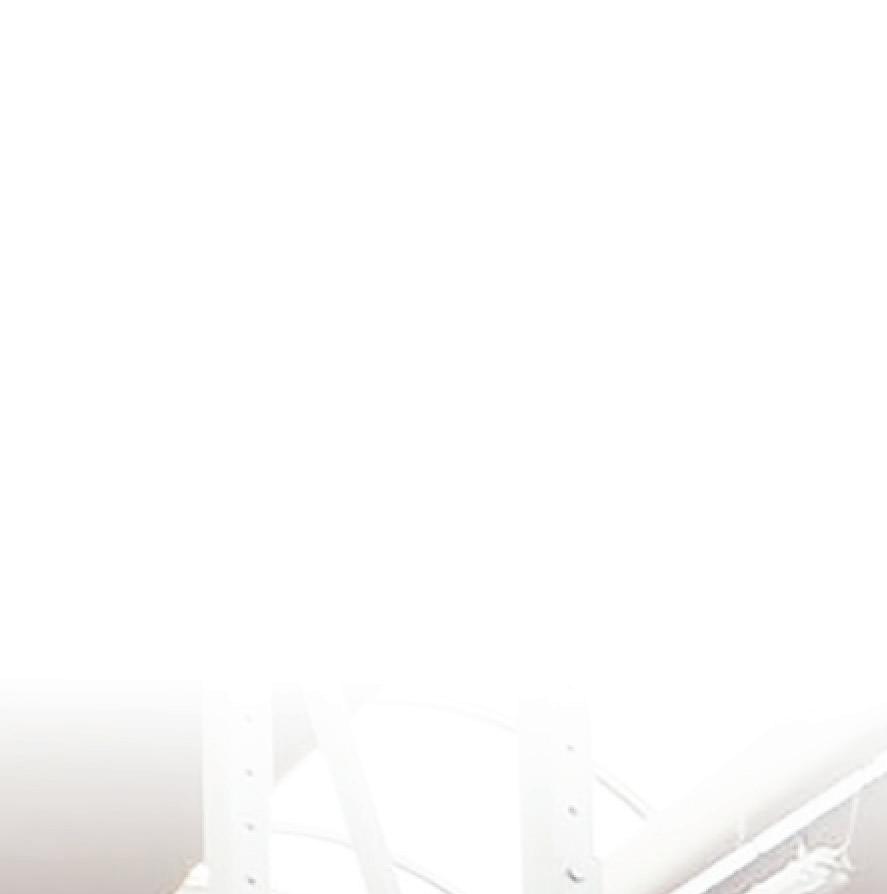


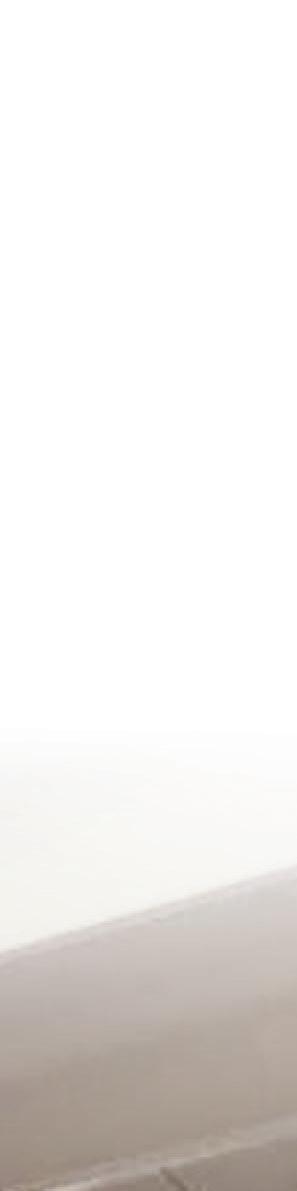
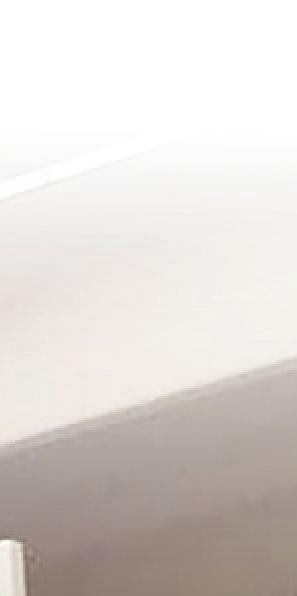
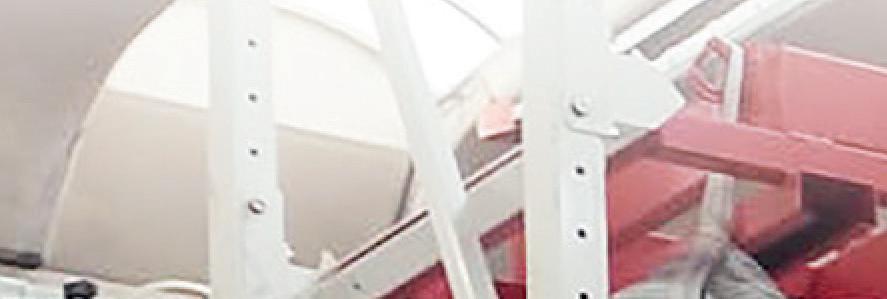
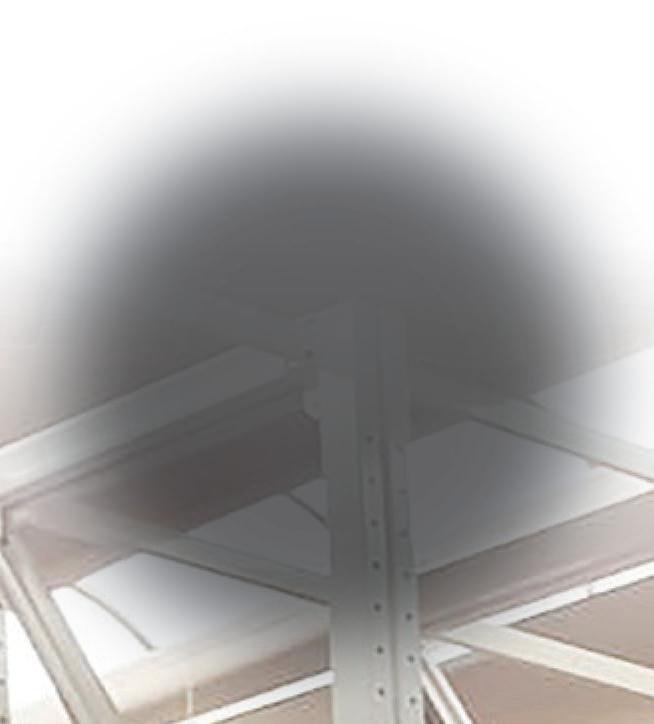
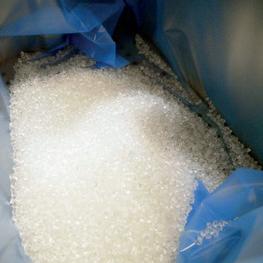
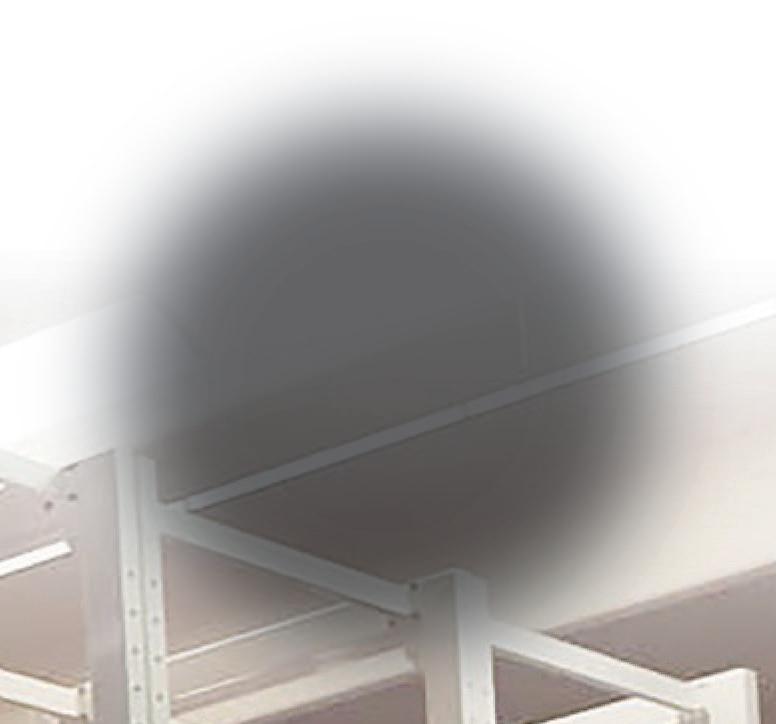
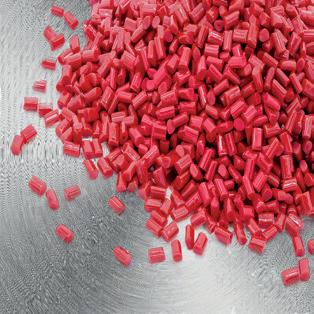
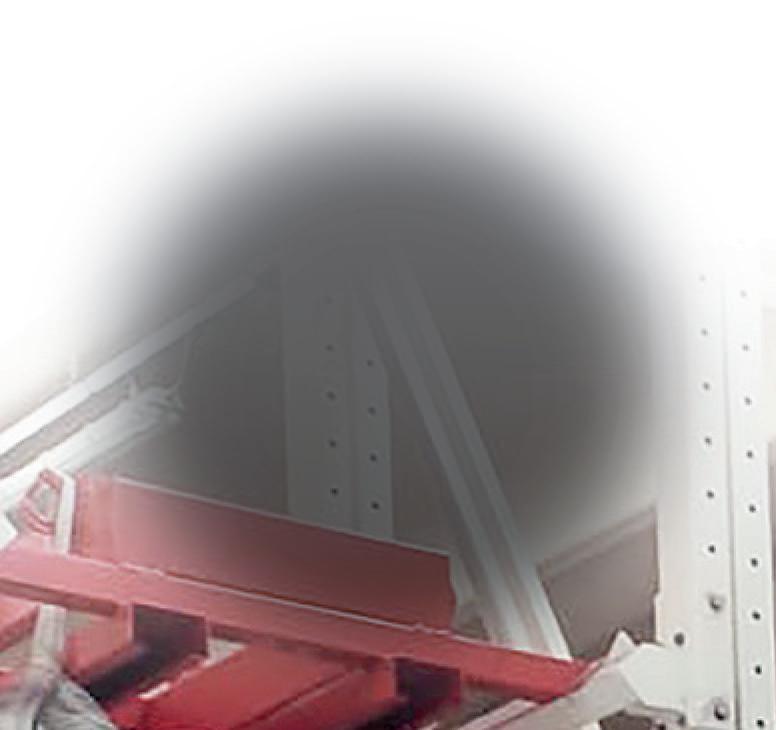
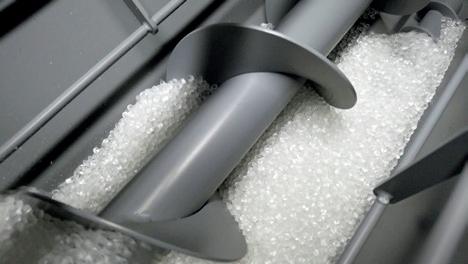
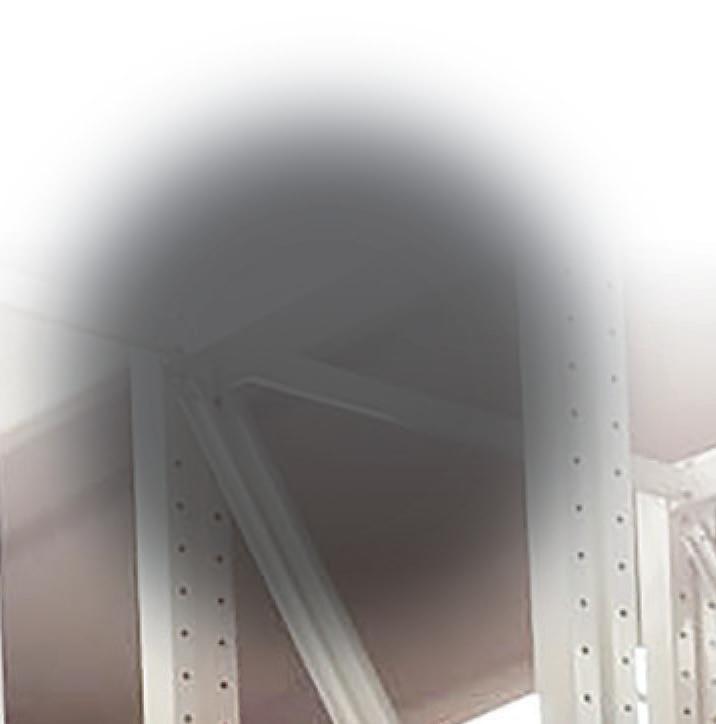
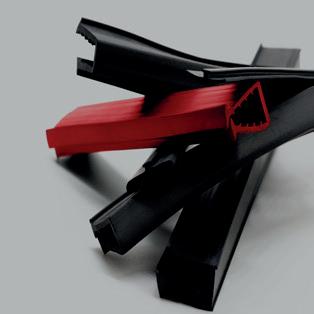
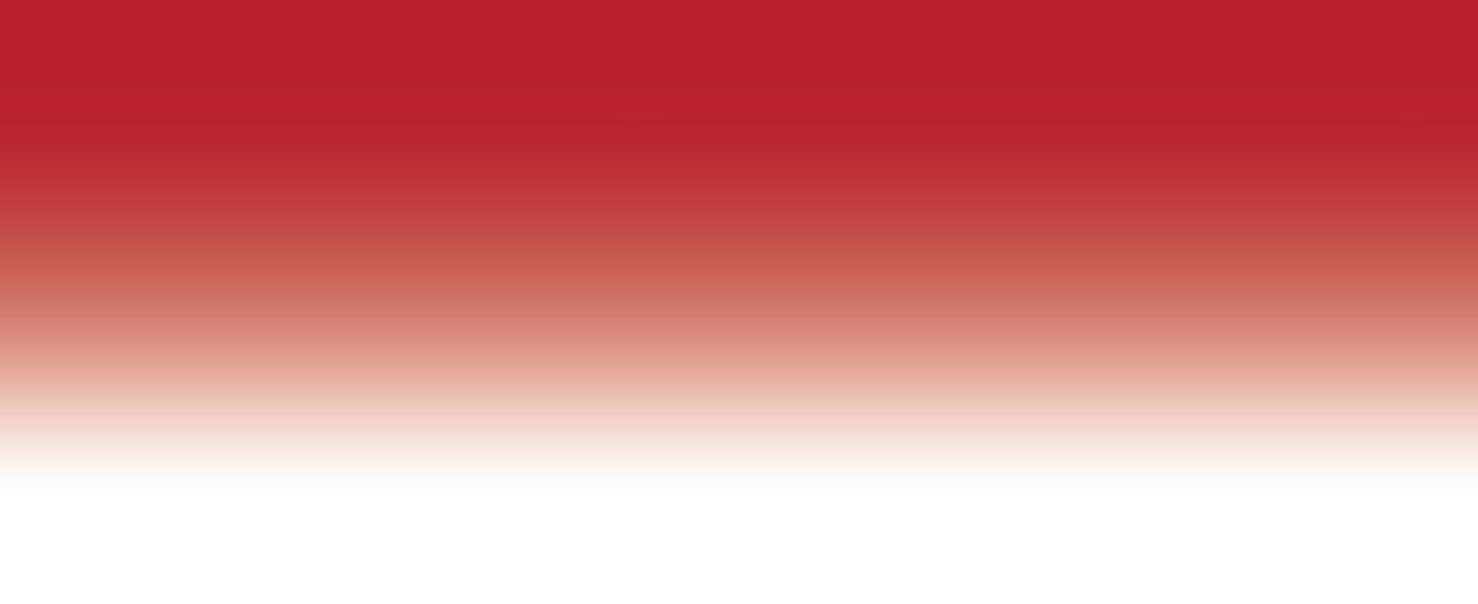
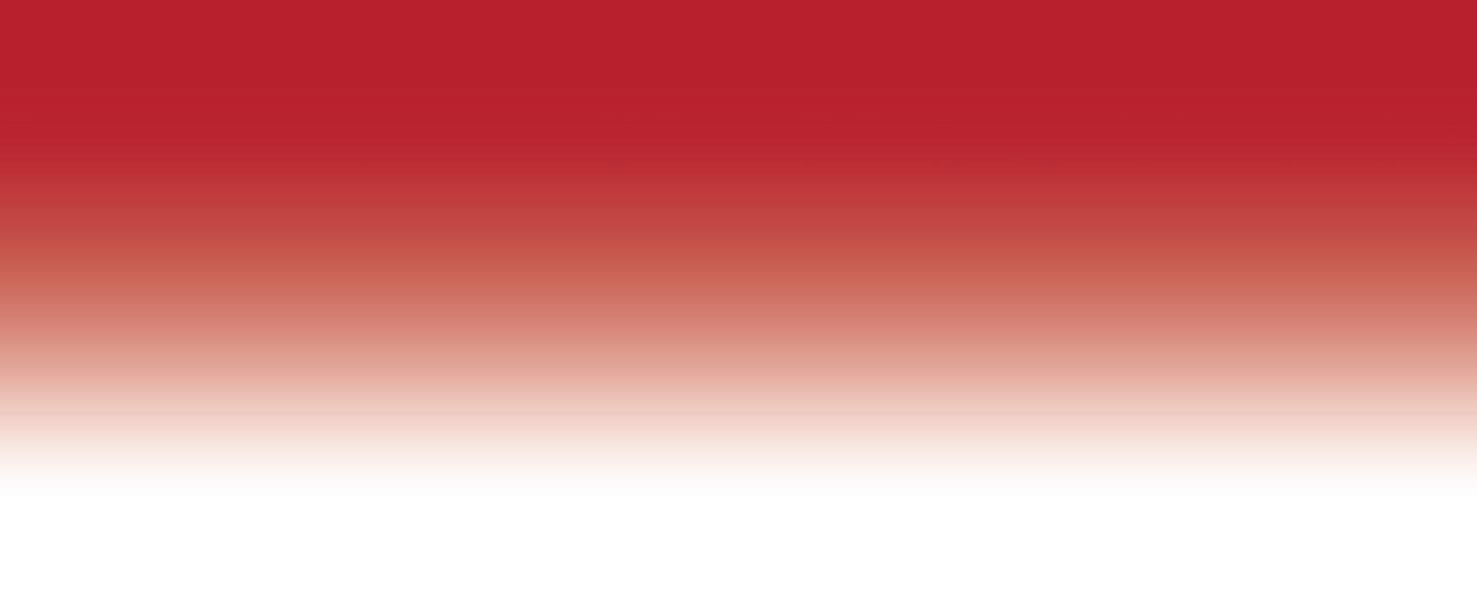
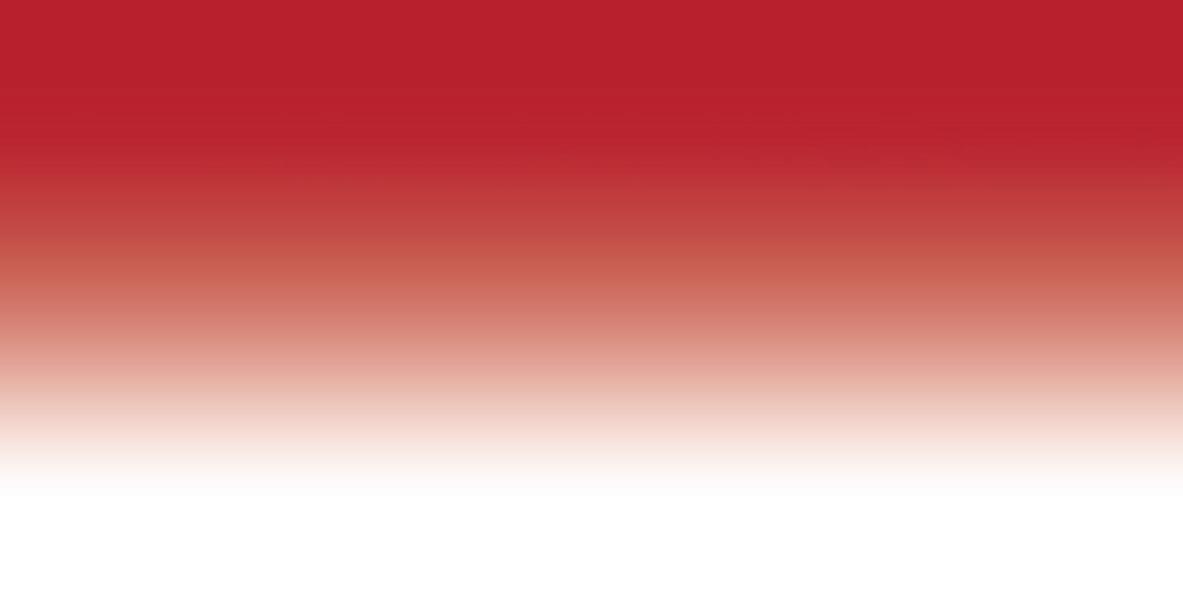

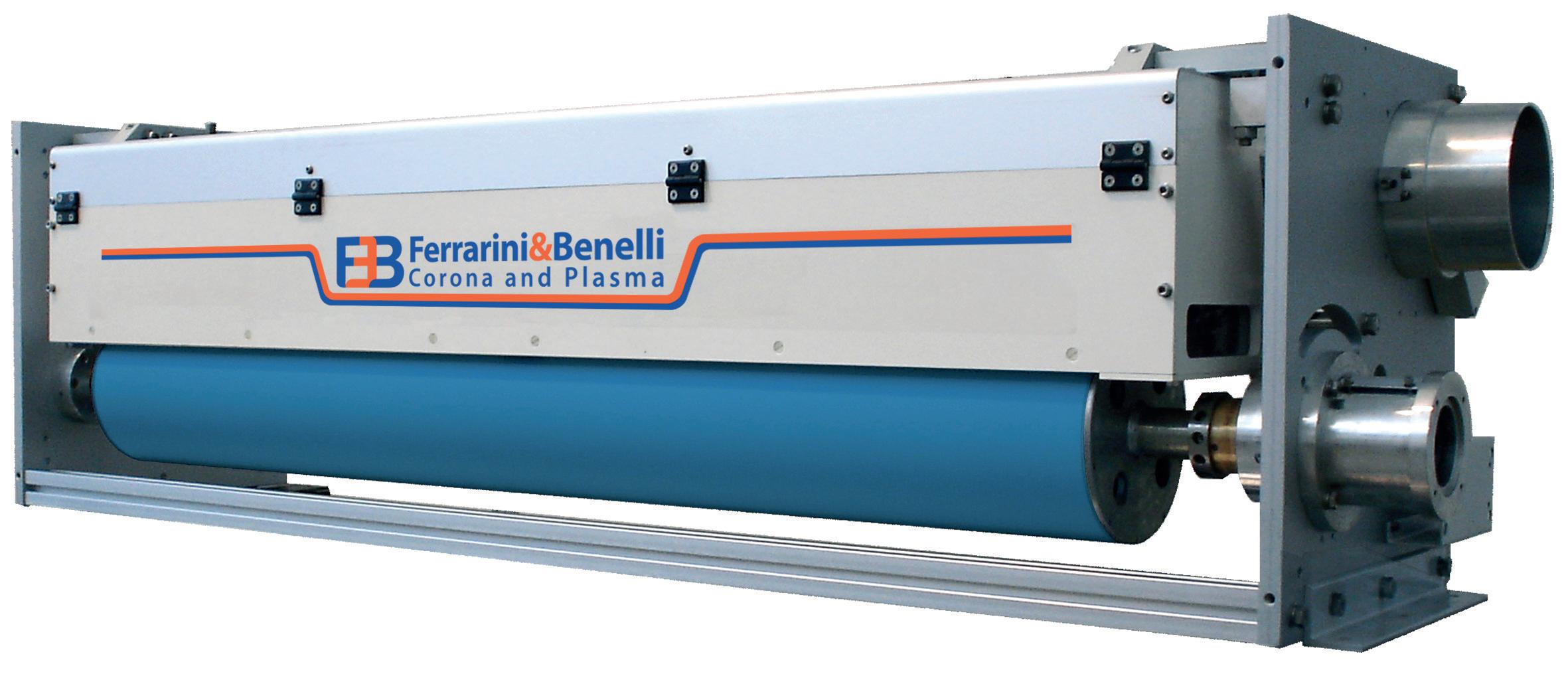
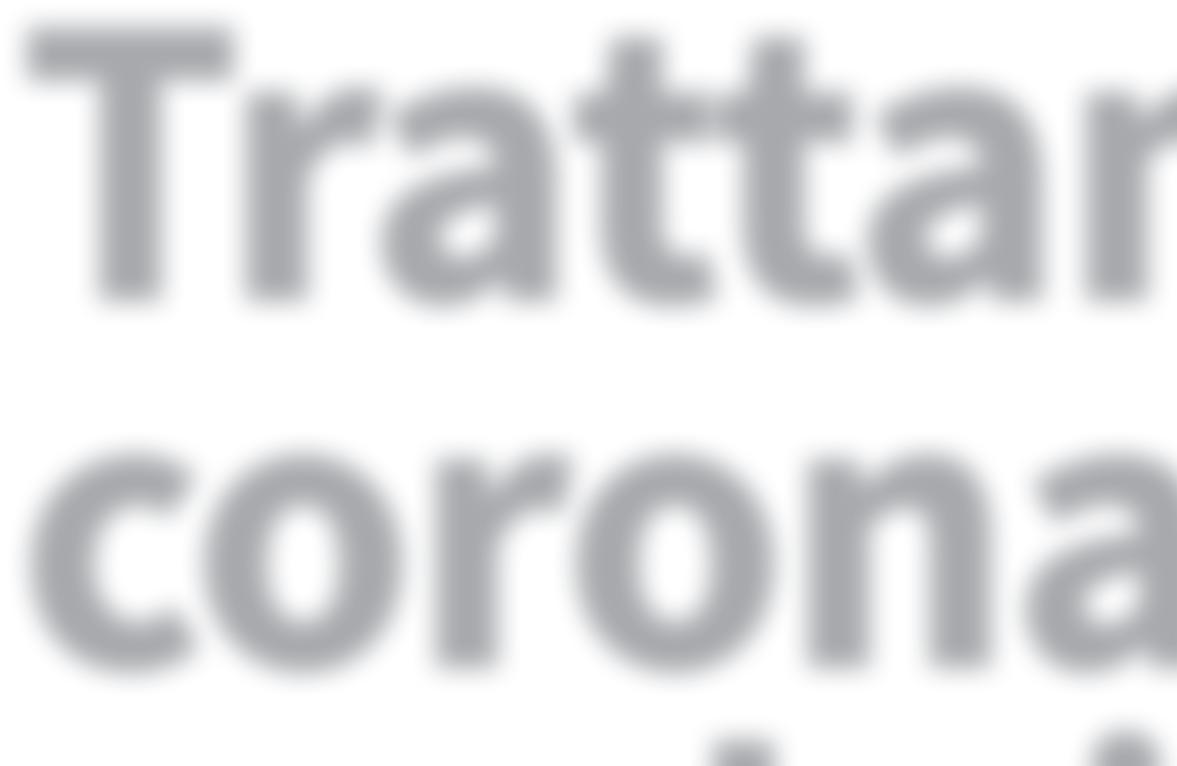

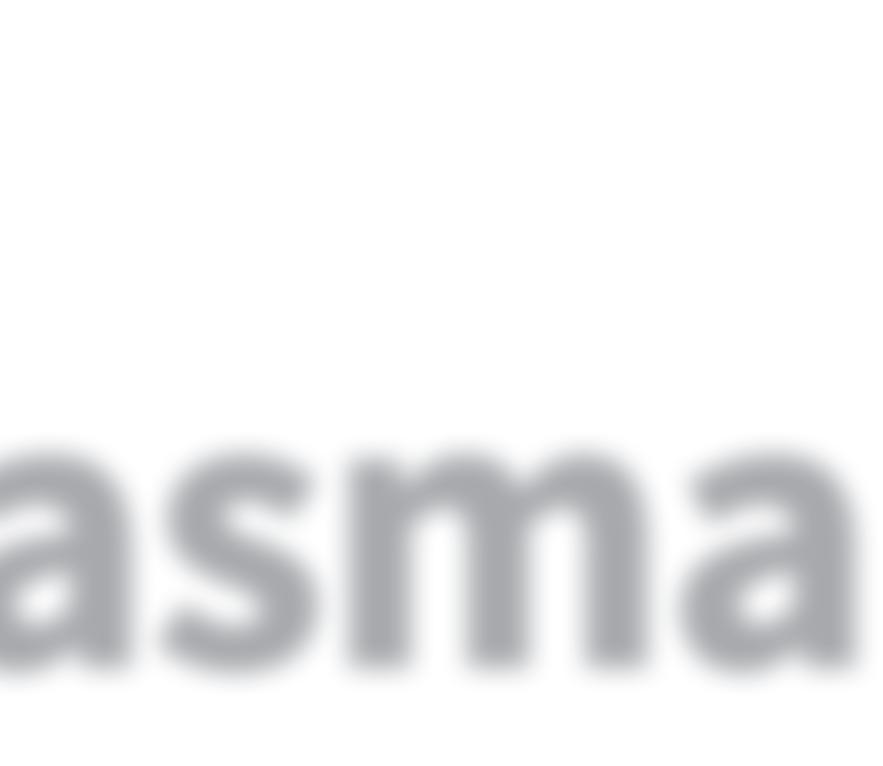

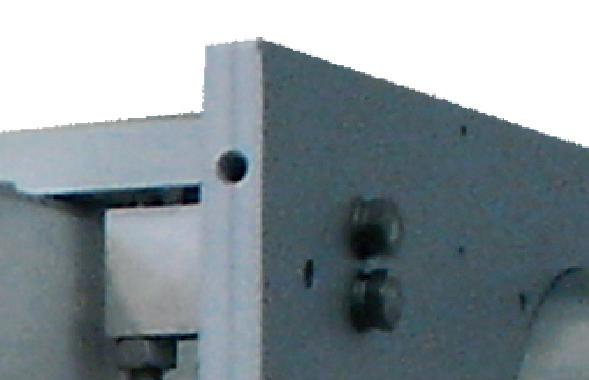
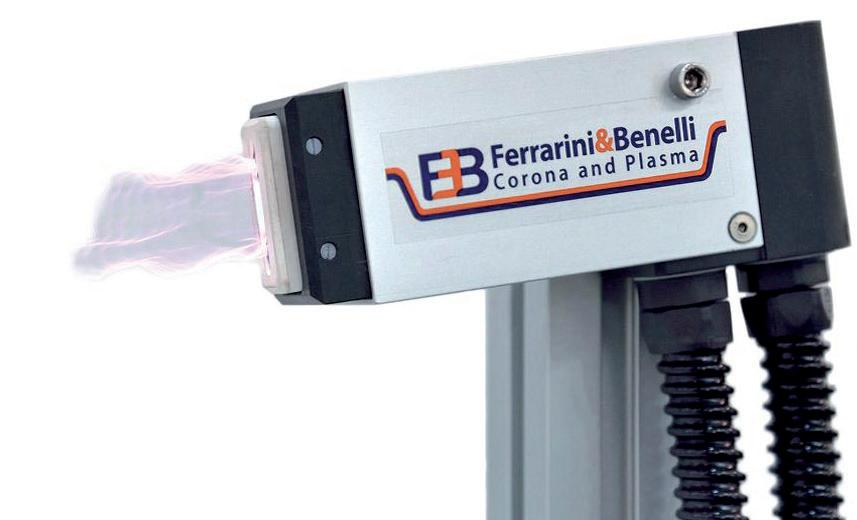