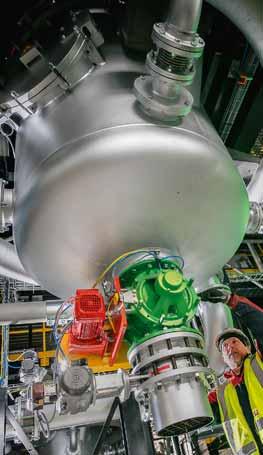
25 minute read
Kort nieuws
SUBSIDIE TECHNISCHE OPLEIDERS
NL Leert Door stelt € 4 miljoen subsidie beschikbaar voor technische opleiders die vermeld staan op TechniekOpleiding.nl. De site vermeldt een lijst met gratis te volgen technische opleidingen. De subsidieregeling is een initiatief van de overheid voor deelnemers die een band met de Nederlandse arbeidsmarkt hebben. Iedereen die zich wil scholen, kan zich nu inschrijven voor diverse trainingen. Volgens John Huizing, directeur bij TechniekOpleiding.nl, kunnen er met deze subsidie in de eerste helft van 2021 al 4.000 technici worden opgeleid. Dit kan de tekorten aan functioneel inzetbaar personeel oplossen, een probleem waar de technische branche al jaren mee kampt. Het kan bijvoorbeeld gaan om het opleiden van mensen die zonder werk zitten door de coronacrisis of het faciliteren van een carrièreswitch naar de techniek.
Advertisement
€ 7 miljoen aan operationele kosten te besparen. Het effect daarvan moet in 2023 volledig zichtbaar worden. In 2025 wil het bedrijf de kosten zelfs met ten minste € 10 miljoen hebben teruggebracht. (Bron: Beurs Damrak)
MINDER PRODUCTIE FORFARMERS
De beursgenoteerde voederproducent ForFarmers zag zijn omzet in 2020 met 4,5 % dalen naar € 2,35 miljard. De nettowinst daalde van € 17,7 miljoen naar € 14,2 miljoen, een afname met bijna 20%. ForFarmers is van plan om in 2021 en 2022
RISICO’S CHROOM-6 GRAFISCH IN BEELD NIEUWE FABRIEK BLACK BEAR CARBON
Installatie voor het terugwinnen van koolstof uit bandengranulaat bij Black Bear Carbon. (Foto: Black Bear Carbon) Op het Chemelot Industrial Park gaat Black Bear Carbon, gespecialiseerd in het terugwinnen van koolstof uit bandengranulaat, een nieuwe fabriek realiseren. Die moet best-in-class worden qua procestechnologie, veiligheid en betrouwbaarheid. De fabriek past in de ambitie van de regio Limburg om uit te groeien tot circulaire hub en in 2050 volledig klimaatneutraal te zijn. De plannen van Black Bear Carbon vallen volledig binnen de huidige koepelvergunning van Chemelot. Het bedrijf gaat zich daar richten op het terugwinnen van de hoogwaardige grondstoffen uit het (nagenoeg) staal- en textielvrij, verkleind rubbergranulaat van auto- en vrachtwagenbanden. Op het industriepark van Chemelot gaat dat proces volledig circulair worden.
<FP2102-05 2 VOMI_Chroom-6_2> ZO GROOT PLAATSEN DAT HIJ LEESBAAR ISN Met de Chroom-6 infographic geeft VOMI het startsein voor een campagne om bewustwording rondom het veilig werken met Chroom-6-houdende materialen te bevorderen. (Tekening: VOMI)
VOMI, de branchevereniging van dienstverleners in de procesindustrie, heeft een infographic laten maken die bedrijven bewuster moet maken van de noodzaak veilig te werken met Chroom-6-houdende materialen. Belanghebbenden kunnen de grafische tekening ook gebruiken om beleid met andere belanghebbenden af te stemmen. Blootstelling aan Chroom-6 kan ernstige gevolgen hebben voor de gezondheid. Bij onderhoudswerkzaamheden kunnen medewerkers van VOMI-leden te maken krijgen met Chroom-6. Daarom moeten bij het werken aan installatieonderdelen waar deze giftige stof in zit, de nodige voorzorgsmaatregelen genomen worden door zowel VOMI-leden als eigenaren van de installaties. Exemplaren van de infographic Chroom-6 zijn te downloaden van de VOMI-website: http://bit.ly/VOMI-Cr-6
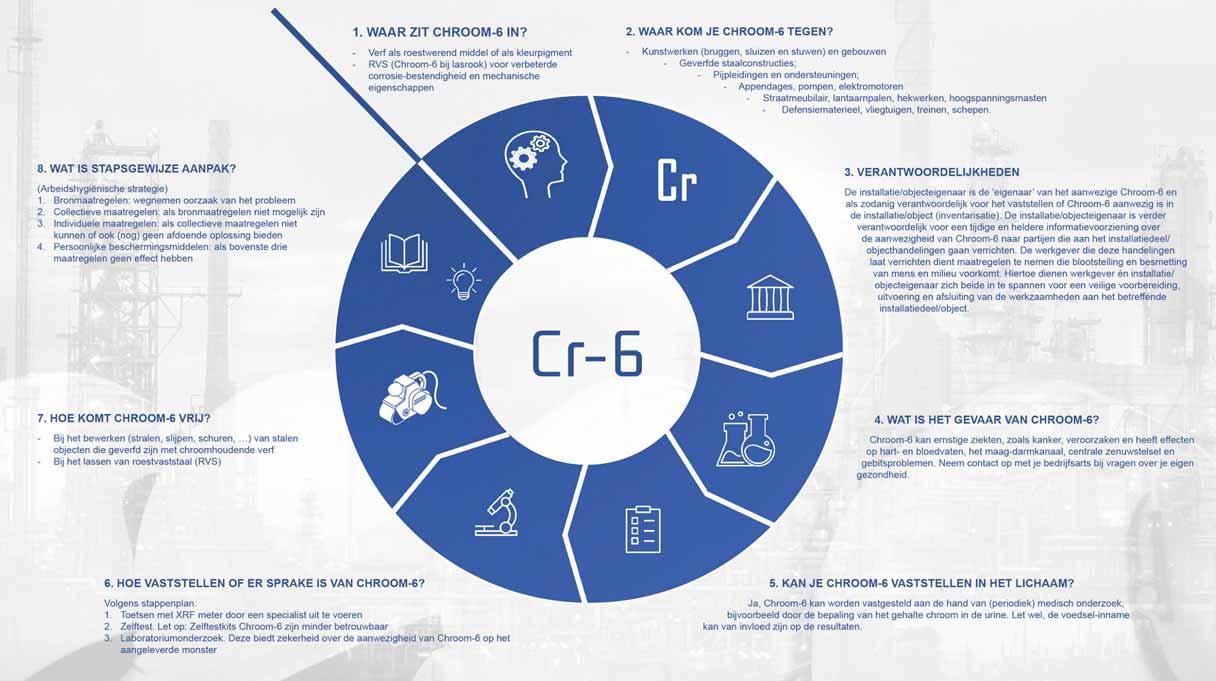
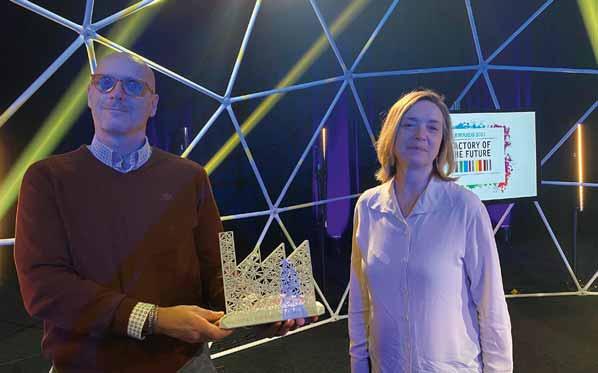
De Factory of the Future-bokaal in handen van Marco Moes (Cargill), uitgereikt door Nadia Lapage van Fevia Vlaanderen. (Foto: Agoria)
NIEUWE FABRIEKEN VAN DE TOEKOMST
Technologiefederatie Agoria en Sirris, het collectief centrum van de Belgische technologische industrie, hebben bekend gemaakt dat de in België gevestigde fabrieken van Cargill (Izegem), Danone (Rotselaar), Delhez Tôlerie (Thimister-Clermont) en L’Oréal (Libramont) zijn uitgeroepen tot de nieuwe Factories of the Future. De winnaars ontvingen hun onderscheiding digitaal uit handen van Jan Jambon en Willy Borsus, Vlaamse minister-president en Waals viceminister-president. Agoria definieert Factories of the Future als ‘bedrijven die investeren in digitalisering, in hun personeel, in slimme processen en producten en in een productie van wereldniveau. Ze gaan doordacht om met energie en materialen en stimuleren de betrokkenheid, creativiteit en autonomie van medewerkers.’ Dat er heel wat komt kijken om deze prijs in de wacht te slepen blijkt uit de prestaties bij Danone en Cargill, waarbij de geleverde inspanningen tot 10 jaar terug in de beoordeling zijn meegenomen. Zuivelbedrijf Danone, vestiging Rotselaar, werd onderscheiden vanwege zijn voortrekkersrol op het vlak van innovatie. Samen met de verpakkingsleverancier lukte het om het aandeel plastic in de Actimel-fles in een paar jaar met 50% te verminderen. Wapenfeiten uit de jaren ervoor zijn op de site van Agoria terug te lezen. De Cargill-vestiging te Izegem raffineert oliën en vetten voor de voedingsindustrie en sprong er positief uit vanwege de hoge technische standaard van de productiefaciliteiten. Een focus op automatisering heeft het mogelijk gemaakt om flexibeler te werken. Ook werd er 2020 een nieuwe warmtekrachtkoppeling in gebruik genomen. Dit innovatietraject is niet los te zien van alle vernieuwingen die al sinds 2009 zijn doorgevoerd, waarover meer op de Agoria-site (http://bit.ly/FotF2021).
KAMPIOEN MATRASSENRECYCLING
Nederland blijkt wereldwijd koploper in het recyclen van matrassen. Van de ongeveer 1,6 tot 1,8 miljoen matrassen die er jaarlijks in Nederland worden weggegooid, belandden er in 2019 nog 67% in de verbrandingsovens, met alle CO2-uitstoot van dien. Slechts 33% werd gerecycled tot bijvoorbeeld judomatten, isolatiemateriaal en ondertapijt. Door uitbreiding van de verwerkingscapaciteit lukt het Retourmatras en Matras Recycling Europe (MRE), de twee matrasrecyclingbedrijven in Nederland, om respectievelijk 900.000 en 500.000 matrassen per jaar te recyclen. Dat betekent dat nu ongeveer 75% van alle afgedankte matrassen gerecycled wordt. Daarmee is de doelstelling van de sector om per 2028
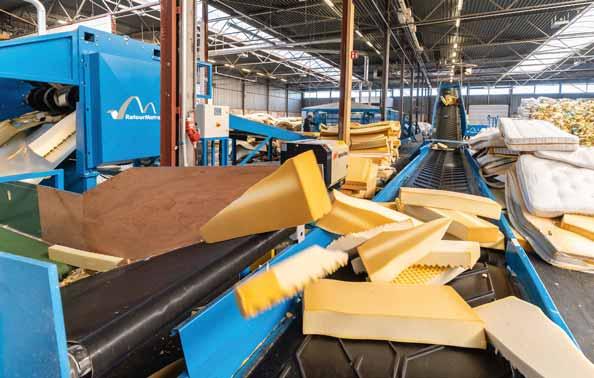
COLUMN ‘ONDERHOUDSPLAN? BRENG HET ONDER BIJ DE MAKER ZELF!’
En dan ligt plots de hele productielijn stil. Downtime. Geen opbrengst, enkel kosten. Als bedrijf krab je jezelf dan even goed achter de oren, als blijkt dat je deze calamiteit met zoiets simpels als een onderhoudsplan had kunnen voorkomen. Gelukkig is het nooit te laat om een onderhoudsplan voor productiemachines op te stellen en voorgoed af te rekenen met onnodige, terugkerende calamiteiten én kosten.
Nu kun je als bedrijf besluiten om zelf zo’n plan op te stellen. Vervolgens maak je een afspraak met een extern servicebedrijf en dat staat een paar keer per jaar stipt op de stoep. Prima! Zolang de orders maar van de productieband rollen, toch?
Maar laten we even inzoomen op de bulkwagenvullers en schroeftransporteurs van Van Beek. Dat zijn stuk voor stuk kwalitatief hoogstaande maatwerkoplossingen. Speciaal ontwikkeld voor onze klanten en voorzien van innovatieve, technische snufjes. Dus waarom zou je zo’n onderhoudsplan dan niet onderbrengen bij de maker zelf? Onze engineers hebben de machine bedacht, ontwikkeld en geproduceerd. Profiteer daar dan ook van!
Onderhoudsplannen gaan verder dan alleen het inplannen van afspraken, het aflopen van traditionele servicebeurten en het schrijven van een bezoekverslag. Onze servicemedewerkers zijn onze ogen en oren. Ze voorzien een onderhoudsplan van belangrijke informatie, waardoor onze engineers pro-actief met klanten kunnen meedenken om calamiteiten voor te zijn.
Nu weten we veel bij Van Beek, maar ook wij worden nog weleens verrast door het effect dat sommige producten op onze machines hebben. Zo kunnen er gasdampen vrijkomen, die letterlijk het staal van de schroef aanvreten. Dat gaat dus verder dan slijtage door corrosie of erosie. Het controleren van de bladdikte, bladhoogte en zelfs de wanddikte van een behuizing zijn ook onderdeel van het onderhoudsplan.
Nu hoor ik je denken, wanddikte? Daar kan toch niks mee gebeuren? Niets is minder waar. Een verticale schroef moet drie keer zo hard draaien om hetzelfde rendement te behalen als een horizontale schroef. Het te transporteren product stuwt zich een weg naar boven en kan letterlijk gaten slaan in een steeds dunner wordende behuizingswand. Dat is specialistische insiderkennis waar externe servicemonteurs nu eenmaal niet over beschikken. Lijkt mij een ‘onderhoudend’ belletje naar Van Beek meer dan waard, toch?
Téan van Horssen, teamleider service Van Beek
driekwart van alle afgedankte matrassen te recyclen dus nu al behaald. Momenteel is er vooral sprake van ‘laagwaardige’ recycling in de vorm van onder meer isolatiemateriaal. De sector wil matrassen anders gaan ontwerpen om het ontleden en recyclen te vereenvoudigen. Als onderdelen niet meer verlijmd worden en er een ander soort schuim in zit, kan er straks ook hoogwaardig gerecycled worden, zoals het produceren van nieuwe matrassen uit afgedankte exemplaren.

Elke stenengrijper bestaat uit 36 luchtbalgsystemen (6 rijen met elk 6 grijpers en luchtbalgen).
REVISIE STENENGRIJPER BESPAART DUIZENDEN EURO’S
De stenengrijpers bij steenfabriek Wienerberger gebruikten (te) veel energie, onder andere door persluchtlekkages. Het bedrijf kon kiezen: een derde compressor bijplaatsen of de lekkages aanpakken. De keus viel op het laatste. Dankzij de lekdetectiespecialist die werd ingehuurd bespaart de fabriek nu jaarlijks duizenden euro’s.
‘Dit leverde direct een meetbare besparing op van 14 kW per uur ofwel € 3.400 op jaarbasis’ Wienerberger
De Winterswijkse productielocatie van Wienerberger is onderdeel van de Oostenrijkse onderneming Wienerberger AG, fabrikant van bouw- en bestratingsmaterialen. In Nederland werken zo’n 1.000 medewerkers verspreid over 19 productielocaties met elk zijn eigen specialiteit. Winterswijk is gespecialiseerd in het produceren van handvorm gevelstenen. Dit zijn machinaal vervaardigde keramische gevelstenen, die lijken op ouderwetse handgevormde gevelstenen. Winterswijk produceert dunne Waalformaat gevelstenen en dikke, Engels formaat stenen. Beide formaten zijn in tientallen varianten leverbaar, met verschillende kleurschakeringen, uitstraling en/of samenstelling. Elke variant heeft dus een eigen recept, met steeds wisselende leem- en zandverhoudingen en additieven zoals mangaan, zout, mineralen en kalk. Vermeldenswaardig is dat de leem uit een eigen kleigroeve komt in de Achterhoek. Die kleigroeve stamt nog uit het tertiare tijdperk. Alleen al in Winterswijk rollen jaarlijks 26 miljoen bakstenen (gemeten in Waal-formaat) van de band, omgerekend komt dit neer op zo’n half miljoen bakstenen per week.

Elk type baksteen heeft een eigen recept, met eigen leem- en zandverhoudingen en additieven zoals mangaan, zout, mineralen en kalk.
De steenfabriek in Winterswijk verbruikte al jaren extreem veel perslucht. De grootste energieverslinders waren de vijf, 30 jaar oude stenengrijpers die de ovenwagens volcontinu beladen en ontladen. Elke stenengrijper bestaat uit 36 luchtbalgsystemen (6 rijen met elk 6 grijpers en luchtbalgen). Elke grijper met luchtbalg wordt aangedreven door een pneumatische compactcilinder met een diameter van 80 mm en een slaglengte van 50 mm. Om steeds 36 stenen (een laag) per keer te kunnen oppakken worden de 36 grijpers met behulp van een gelijkloopsysteem elektrisch aangestuurd. Elke stenengrijper verwerkt 100.000 stenen per dag, een half miljoen stenen per week. SLIJTAGE Het is een relatief eenvoudig, maar zeer gevoelig systeem. Het oppakken van de stenen en het in- en uitsturen van de pneumatische cilinders kost veel energie en door het vele openen en sluiten slijten de luchtbalgen relatief snel, waardoor veel perslucht weglekt. Van de drie compressoren die Wienerberger had staan, moesten er twee continu op volle capaciteit draaien om het systeem draaiende te houden, terwijl de derde – verouderde – compressor als backup diende. Om de bedrijfscontinuïteit te garanderen moest ofwel de verouderde compressor vervangen worden, ofwel iets gedaan worden aan de persluchtlekkages. Op advies van de compressorfabrikant koos de steenfabrikant voor dat laatste en klopte aan bij lekdetectiespecialist Airsave.
EERSTE GRIJPER Pim Duterloo, directeur van Airsave, vertelt hoe zijn bedrijf dit project aangepakt heeft. “We gingen van start met één stenengrijper. Daarbij voerden we een complete lekdetectie uit en repareerden de lekkages. Bij veel van de cilinders, luchtbalgen en andere pneumatische componenten constateerden we forse verliezen. Na de inventarisatie hebben we de nodige nieuwe componenten besteld. Tijdens een stopdag zijn we begonnen
met de ombouw. Dit leverde direct een meetbare besparing van 14 kW per uur op ofwel een besparing op jaarbasis van € 3.400. Zo maakten we inzichtelijk wat de te realiseren besparingen konden zijn.”
REDESIGN “Omdat de eerste resultaten verbluffend waren, kregen we direct opdracht om ook een tweede stenengrijper te reviseren in een nieuw project”, zegt Duterloo. Met een team van zes personen werden in vier werkdagen alle pneumatische componenten van de stenengrijpers vervangen: van 5/2-ventielen, pneumatische cilinders, luchtbalgen, slangen, koppelingen en de vingers van de grijpers tot bouten, moeren, fitwerk en slijtagepunten in de draaiende delen. Uit het oogpunt van duurzaamheid en veiligheid werd bij sommige van de componenten, zoals bij de slangen, gekozen voor een iets duurdere versie. Richard Thuis, productieleider bij Wienerberger, legt uit waarom: “Als ergens slangbreuk optreedt in de fabriek, moet een van onze operators zich in de machine
Productieproces
Op de productielijn in Winterswijk wordt batchgewijs gewerkt. Na het mengen van de verschillende ingrediënten voor een bepaalde batch, gaat de massa door twee walsen die 3 mm ten opzichte van elkaar staan afgesteld. Van hieruit gaat de massa door naar de pers waar hij nogmaals wordt gemengd, ditmaal op de juiste plasticiteit, zodat vervolgens op de vormband vormelingen kunnen worden vervaardigd. Een batch vormelingen verblijft gemiddeld zo’n drie dagen in een van de 19 droogkamers, die op temperatuur worden gebracht met de restwarmte van de tunneloven. De temperatuur wordt bij de droogovens in stappen opgebouwd van 20°C tot 60°C. Na het drogen gaan de bakstenen naar de zetmachine. Deze legt de bakstenen in een van te voren geprogrammeerd zetpatroon op de ovenwagens. Bij dit zetpatroon is rekening gehouden met een bepaalde tussenruimte, zodat de onder- en boventemperatuur van de stenen in de tunneloven gelijk is. Vervolgens wordt elke ovenwagen beladen met 11 lagen steen. Daarna worden de ovenwagens achter elkaar de 65 meter lange tunneloven in gereden. De temperatuur loopt in deze tunneloven geleidelijk op van 300° C aan het begin, tot circa 1100° C in het midden van de oven. Aan het einde van de tunneloven worden de stenen met behulp van een snelkoeler in ongeveer een uur weer teruggekoeld naar circa 300° C. In totaal kunnen 32 ovenwagens tegelijk in de tunneloven, die zeer langzaam van het begin van de oven naar het einde schuiven. Dit hele proces duurt per ovenwagen 5 dagen. Zodra de ovenwagens uit de oven komen, worden ze ontladen en dan worden de stenen uit de verschillende batches door elkaar gemengd, zodat de batches een natuurlijkere uitstraling hebben. Vervolgens worden de stenen verpakt in hoezen en op pallets gezet, klaar voor transport.

manoeuvreren, met alle risico’s van dien. Zo’n potentieel gevaarlijke situatie moet zoveel mogelijk vermeden worden. Airsave adviseerde daarom een duurdere oplossing, die meer bedrijfszekerheid biedt, namelijk slangen met een conische sluiting die werken op basis van lagedruk hydrauliek.” Duterloo beaamt: “De stenengrijper is dus deels gereviseerd volgens de oorspronkelijke specificaties en deels geredesigned, zodat hij weer voldoet aan de laatste stand der techniek en weer tientallen jaren mee kan.”
WIN-WIN Nu de eerste twee stenengrijpers onderhanden zijn genomen, is de compressorcapaciteit van de tweede compressor weer grotendeels beschikbaar als backup. “En dit is nog maar het topje van de ijsberg”, zegt Duterloo trots. “Dit jaar staan verdere vervolgacties op de agenda op het gebied van preventief onderhoud en lekkagedetectie. Op basis van de resultaten van de eerste twee stenengrijpers is de verwachting dat de tweede compressor na het volgende project niet meer hoeft mee te draaien. Zo wordt niet alleen fors bespaard op compressorcapaciteit, maar ook op onderhoudskosten. Een win-win situatie dus voor zowel Wienerberger als het milieu.” ●
Met de opkomst van smart industry en het Industrial Internet of Things neemt de zorg over de veiligheid van digitale systemen in de industrie toe. Wat moeten bedrijven doen om de digitale veiligheid te waarborgen?
Vincent Wagenaar, general manager van industriële automatiseerder HMS Networks Benelux, noemt de digitalisering van de industrie een positieve ontwikkeling, “zolang digitalisering en digitale veiligheid maar hand in hand gaan.” De vraag is of dat voldoende gebeurt. Nederland zit in de kopgroep wat betreft industriële automatisering en digitale infrastructuur, maar scoort tamelijk laag op cyberveiligheid. Dat concludeerde accountants- en advieskantoor PwC in februari 2021. Even googelen levert artikelen op over recente hacks bij tapijtfabrikant Desso, bandenfabriek Apollo Vredestein, farmaceut MSD, Pilz automatisering en Machinefabriek Almi. De gevolgen van die hacks lopen uiteen van kortstondige downtime en systeemfalen tot virussen en malware die diep in het systeem doordringen. Dit kan diefstal van informatie, onvoorspelbaar gedrag, kwaliteitsproblemen en zeer hoge kosten tot gevolg hebben.
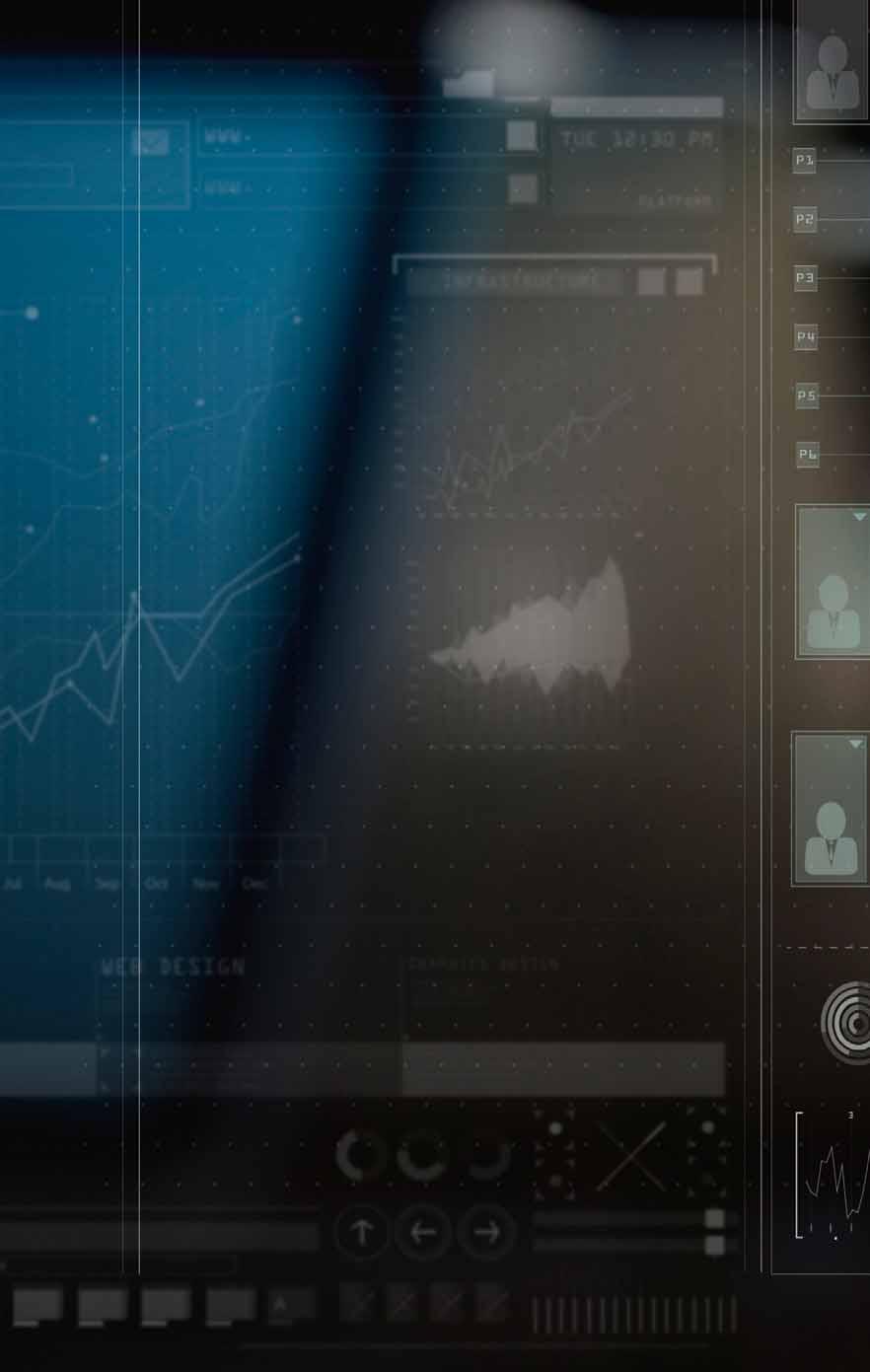
TIJDELIJK “Nieuws over dat soort incidenten verhoogt het veiligheidsbesef tijdelijk”, zegt Wagenaar, “maar de aandacht ebt even snel weer weg. In Nederland voelen we ons over het algemeen veilig, security is niet van nature ons eerste aandachtspunt. Gebruikers hebben vooral interesse in bepaalde aspecten van digitalisering, zoals predictive maintenance, en wat dat oplevert. Maar één ding is zeker: als je gehackt wordt, levert dat heel weinig op. Veiligheid is een randvoorwaarde voor mogelijk voordeel. Toch is cyberveiligheid niet systematisch geïntegreerd in het denken en handelen hier.” Zo’n gebrek aan veiligheidsbesef uit zich bijvoorbeeld in de aanschaf van ‘slimme’ schakelaars en thermostaten,
SMART INDUSTRY EN IIOT KUNNEN 100% VEILIG
Tips
• Maak cybersecurity standaard onderdeel van elk ontwerp • Check certificering leveranciers • Check certificering van toeleveranciers Let ook op: • transparantie over veiligheidsmaatregelen • dubbele authenticatie • meerstaps-verdediging tegen aanvallen • penetratietesten • audit trail • closed source software • beveiliging van de hardware die gebruikt worden in de gebouwautomatisering. Wagenaar: “Sommige van die apparaten zijn makkelijk binnen te komen. Dat klinkt onschuldig. Maar bedenk eens wat er gebeurt als een hacker van schakelaar via router en laptop uiteindelijk de fabriek binnenkomt. Een systeem is zo sterk als de zwakste schakel.” DOORVRAGEN Iedereen die bezig is met smart industry moet digitale veiligheid dus serieus nemen. “Bedrijven kunnen niet alles zelf weten, maar ze zouden security wel op kunnen nemen als standaard onderdeel van het ontwerp”, zegt Wagenaar. “Een tweede tip is dat bedrijven in het offertetrajcet goed naar de
Cyberveiligheid moet systematisch geïntegreerd worden in het denken en handelen in de Nederlandse industrie. (Foto: Adobe Stock)

certificering van de leveranciers vragen, en naar de beveiliging van hard- en software. Rond ISO27001 zit bijvoorbeeld een addertje onder het gras. Die standaard bestaat uit heel veel verschillende onderdelen waarvan een bedrijf zelf de scope kan bepalen. Zo’n bedrijf hoeft dus niet alles wat binnen ISO27001 benoemd wordt, toe te passen om zichzelf toch ‘ISO27001-gecertificeerd’ te mogen noemen. Het gaat er dus om, dat leveranciers kunnen aantonen, dat ze aan alle cybersecuritygerelateerde onderdelen van die standaard voldoen.” Klanten moeten dus vragen – en doorvragen, vindt Wagenaar. “Werken de leveranciers zelf ook met toeleveranciers die alleen best practices toepassen? Hoe transparant is de leverancier in zijn security aanpak? Hanteren ze een verdediging in meerdere stappen tegen aanvallen?”
BEWUST Wagenaar wil managers in de industrie niet bang maken, maar wel bewust van digitale veiligheid.
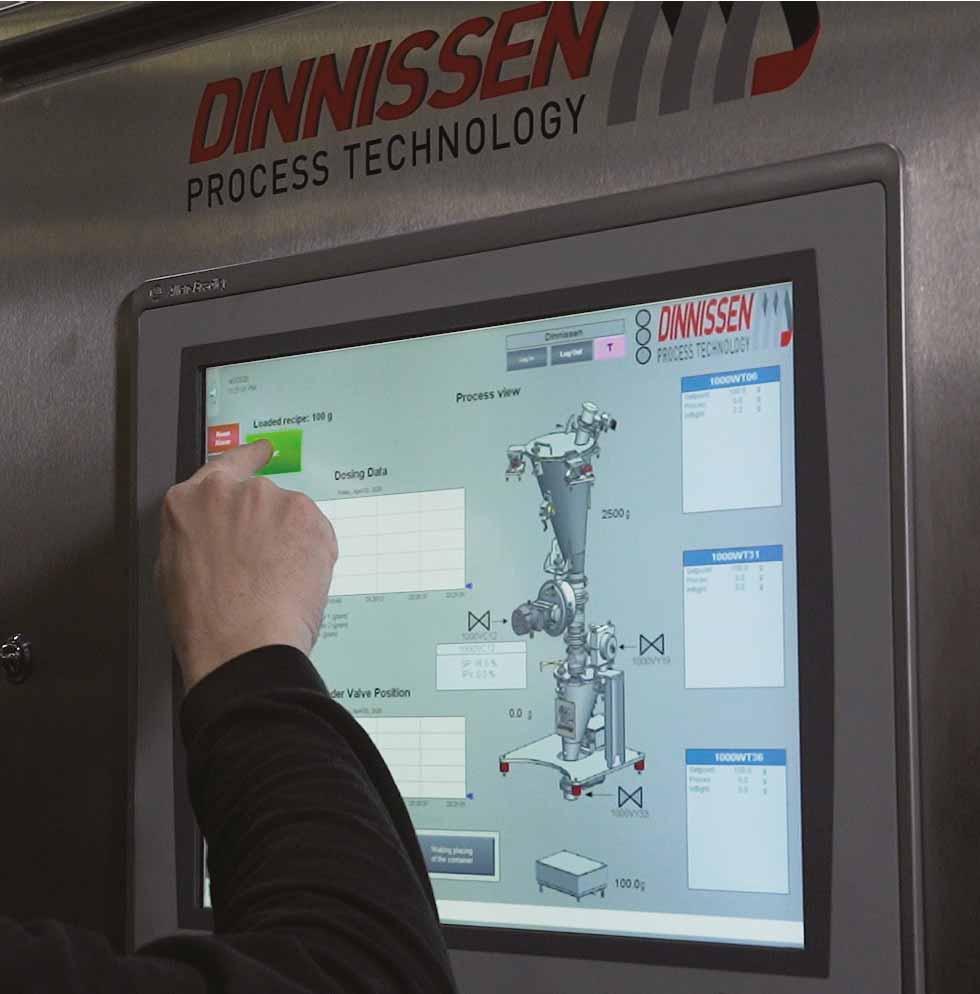

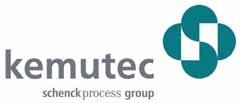




Een fabriek koppelen met internet, bijvoorbeeld via IIOT, klinkt kwetsbaar, maar hoeft dat niet te zijn, verzekert hij. “Een firewall alleen is niet voldoende. Maar als je veiligheid serieus neemt, kan het honderd procent veilig. Als specialist in industriële automatisering steken wij voor onze producten de hand in het vuur.”
BESCHIKBAARHEID Ook belangrijk is dat veiligheid niet ten koste gaat van de productiviteit. “Cybersecurity staat bij HMS Networks centraal, maar wel altijd in combinatie met gebruiksgemak en optimale beschikbaarheid van de systemen”, zegt Wagenaar. “Traditioneel is beschikbaarheid een van de belangrijkste drivers in de operationele technologie, terwijl dat in de informatietechnologie minder prioriteit heeft. Maar waar IT ingezet wordt voor operationele technologie, is beschikbaarheid leidend.” Om ervoor te zorgen dat veiligheid en beschikbaarheid in balans zijn, ontwikkelen HMS Networks en collegabedrijven hun producten conform de industriestandaarden ISO27001 en IEC62443-4-1 voor ‘connected devices’. Bedrijven die deze standaarden volgen, hebben cybersecurity volledig geïntegreerd.
TESTEN “Bovendien onderwerpen wij onze producten aan penetratietesten door een cybersecuritybedrijf als NVISO”, legt Wagenaar uit. “We zorgen voor een ‘audit trail’ die alle events logt, zodat je zo nodig kunt reconstrueren wat er is gebeurd en daar maatregelen op kunt nemen. Helaas gaan lang niet alle bedrijven in onze branche zo te werk – en
Vincent Wagenaar, general manager van industriële a utomatiseerder HMS Networks Benelux: “Als je veiligheid serieus neemt, kan het honderd procent veilig.” (Foto: HMS)
HMS Networks
De naam van het Zweedse HMS Networks staat voor ‘Hardware Meets Software’, het snijvlak van operationele technologie (OT) en informatietechnologie (IT). Het bedrijf maakt producten voor de communicatie in machines, tussen machines en van machines naar managementsystemen. In de industriële automatisering van onder andere Siemens, Rockwell en Atlas Copco zitten hard/softwaremodules van HMS Networks. Als gevolg van die activiteiten runt HMS Networks de grootste machine-IIoT cloud ter wereld (https://www.ewon.biz/products/Talk2M). HMS Networks heeft recent als eerste een industriële 5G router op de markt gebracht.
niet al hun klanten weten dat. Kwetsbaarheden ontstaan door oplossingen die niet voldoen aan de actuele veiligheidseisen. Daarom vermijden wij ook open source software-onderdelen, omdat een gepubliceerde kwetsbaarheid razendsnel door hackers kan worden benut, terwijl een oplossing tijd kost.”
MENSELIJKE FOUT Uiteindelijk zijn het vaak menselijke fouten, bijvoorbeeld slordig omgaan met inloggegevens, waardoor het in de praktijk fout gaat. “Technologieproducten kunnen menselijke fouten niet voorkomen”, zegt Wagenaar, “maar wel verminderen. Het is daarom bijvoorbeeld belangrijk dat leveranciers altijd met dubbele authenticatie werken; niet één wachtwoord, maar twee wachtwoorden op twee verschillende apparaten die moeten samenkomen om een systeem te kunnen binnenkomen.”
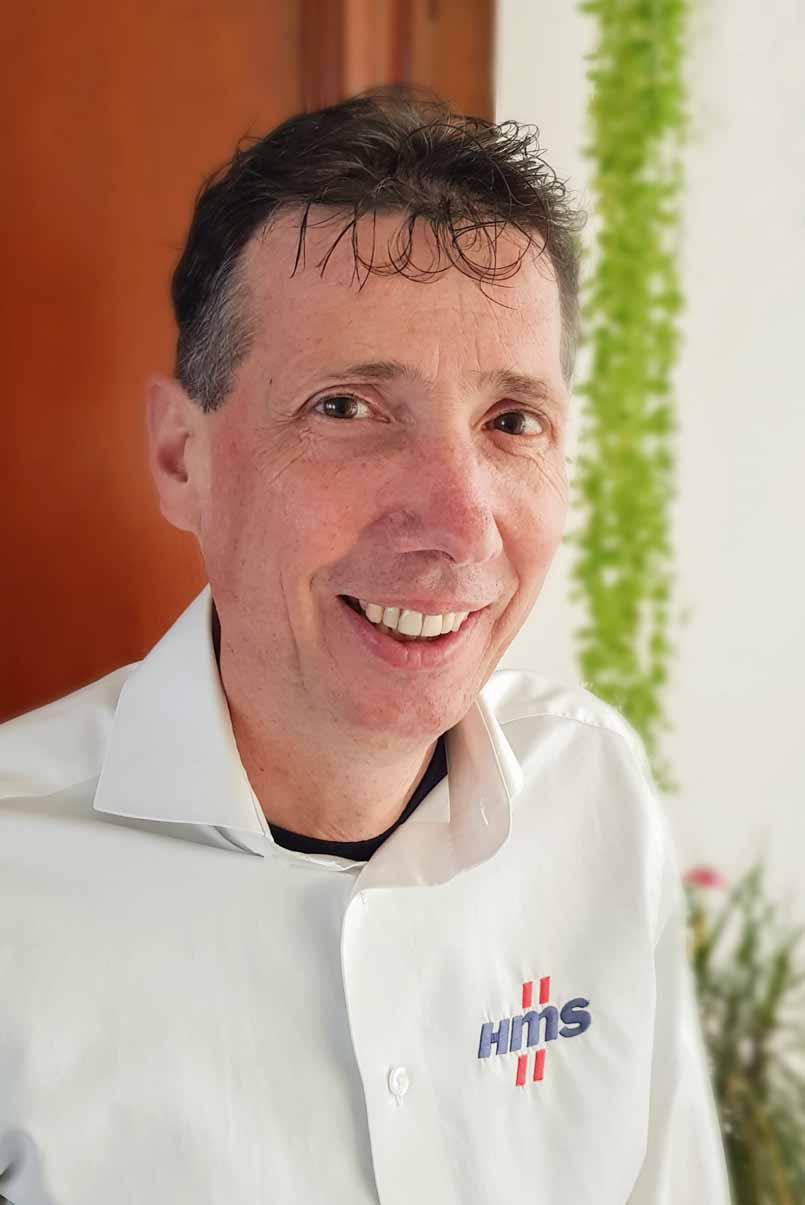
SECURITY ON CHIP Goede hardware maakt hacken moeilijker, ook als mensen fouten maken. “Onze nieuwste producten hebben ‘security on chip’”, geeft Wagenaar als voorbeeld. “Daarbij zit de embedded software in de hardware vergrendeld. Veiligheid is als het ware ingebakken. Door de veiligheid nog een niveau dieper in te bouwen, wordt het moeilijker om toegang tot wachtwoorden en veiligheidscertificaten te krijgen. Zo neemt de kwetsbaarheid voor menselijke fouten af.” ●
KRATTENSTAPELAAR DOET HET ZWARE WERK
Bij peenteler In ’t Zandt worden dagelijks 12-15 ton wortels in kratten gestapeld. Tot voor kort ging dat met spierkracht. Nu nemen een robot-krattenstapelaar en een transportsysteem het zwaarste werk over.
Peenteler In ’t Zandt wast en sorteert 60 tot 75 ton wortelen per week. De wortels worden opgeslagen in kratten, die gevuld zo’n 10 tot 20 kilo per stuk wegen. Die werden altijd door mensen op pallets getild, 12 lagen hoog, tot een hoogte van 2.60 meter. Loodzwaar werk dat uit ergonomisch oogpunt beter kon. De oplossing lag in een gerobotiseerde krattenstapelaar.
EISENPAKKET De keuze viel op een Eterpol robot-krattenstapelaar, in combinatie met een 30 meter lang elektromechanisch transportsysteem. Dirk Wiermans, technisch manager bij Elsto Services, dat het systeem ontwierp en leverde, legt uit aan welke eisen de stapelaar moest voldoen. “De robot moest twee verschillende soorten kratten, namelijk klapkratten en vaste kratten met elk hun eigen afmetingen, kunnen hanteren. Bovendien moest hij ook twee verschillende typen pallets – europallets met een afmeting van 1.20 meter bij 80 centimeter en blokpallets van 1.20 meter bij 1 meter – kunnen beladen met 8 tot 14 lagen kratten. Per uur moesten 550 kratten worden gehandeld. Op hoeveel pallets dat uitkomt, hangt af van het type pallet. Op een blokpallet passen 70 kratjes en op een europallet 40.” EXTRA UITDAGING “Een extra uitdaging was de beperkte opstellingsruimte van 75 vierkante meter”, zegt Wiermans. “Dat was een harde eis om te zorgen dat de medewerkers aan de sorteerder ongehinderd hun werk konden blijven doen. Verder moest er ook een 30 meter lang transportsysteem op maat worden gemaakt. En de bovenste laag kratten op de pallet moest steeds worden afgedekt met een plastic vel om de wortels niet uit te laten drogen.”
ROBOTKOP OP MAAT Met dit eisenpakket in de hand ging Elsto Services aan de slag met het ontwerpen van een robotkop op maat voor een ‘refurbished’ standaard robot van ABB. Vanaf het begin was duidelijk dat de nieuwe kop moest bestaan uit vier grippers, namelijk voor het hanteren van de twee verschillende

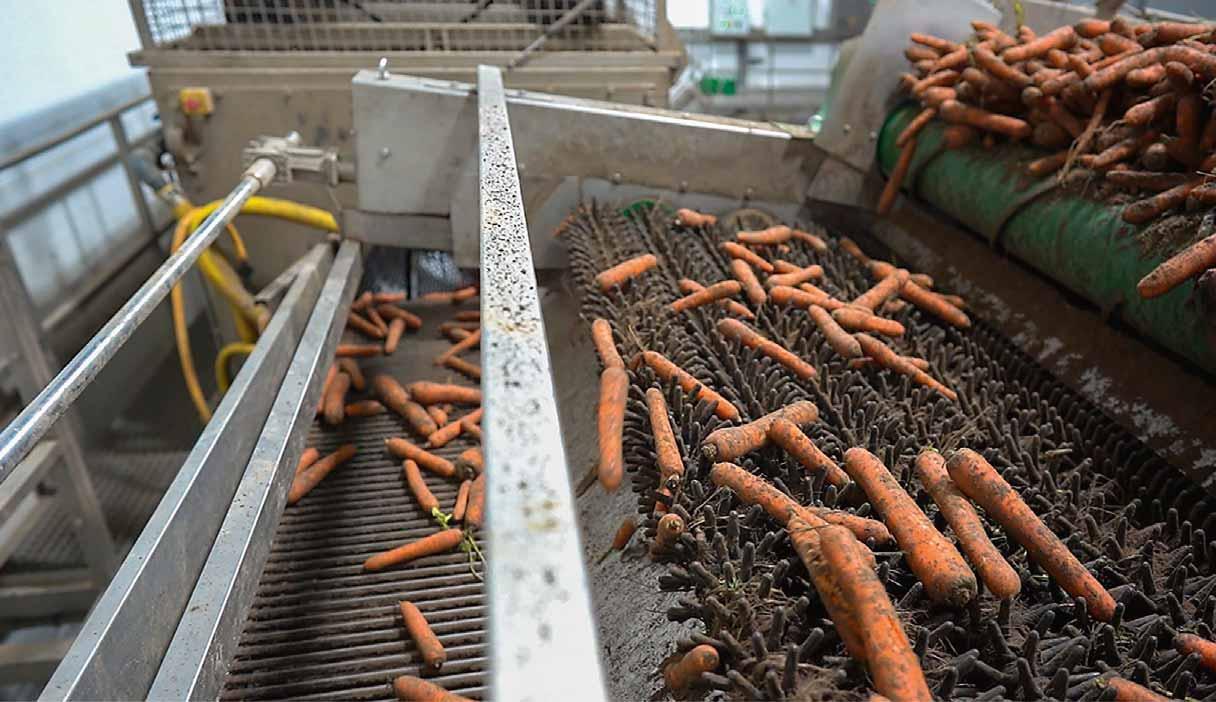
Vuile peen wordt ontdaan van aanhangende grond bij peenteler In ’t Zandt.
maten kratten en voor de twee palletvarianten. De pneumatisch aangedreven grippers worden volledig bestuurd vanuit een PLC, die is ondergebracht in een besturingskast die elders staat opgesteld. Voor elke functionaliteit is een eigen type gripper toegepast. Moeilijkheid hierbij was dat het ‘pakken’ van de kratten van binnenuit niet mogelijk was vanwege de vershoudfolie die over de bovenste laag kratten wordt gespannen op het afweegpunt aan de sorteerder. Een geïntegreerde teller geeft de operator aan het sorteerstation een seintje als de laatste kratten voor één pallet worden gevuld. Die voorziet de kratten dan van een afdekfolie. De robot pakt de kratten steeds per twee op. Om dit te kunnen realiseren worden de kratten altijd volgens een bepaald patroon zonder tussenruimte geplaatst. Zo worden de pallets dus niet alleen
In ‘t Zandt
In ’t Zandt maakt samen met nog een tweede bedrijf deel uit van het samenwerkingsverband VersePeen in Noord-Limburg en is als zodanig aangesloten bij telersvereniging Fossa Eugenia. De afzet van de peen gaat via Fossa Eugenia. In ’t Zandt teelt peen op circa 35 hectare en levert aan distributiecentra voor onder andere supermarkten, groothandelaren en de verwerkende industrie. strakker, maar ook steviger gestapeld. Bij het oppakken van de kratten van de buitenkant is het van belang dat die, ondanks de snelheid waarmee gestapeld wordt, niet in elkaar worden gedrukt.
PALLETBELADING Gemiddeld wordt gedurende een dag ongeveer vier uur gesorteerd op de lijn. Bij aanvang geeft de operator de gewenste recepturen in op het touchscreen van de PLC. Per recept is beschreven welk type pallet er moet worden beladen met welke kratten en welke sortering er gemaakt dient te worden. Wiermans: “Voor de kratten en de pallets hebben we een elektromechanisch aangedreven transportsysteem geëngineerd en op maat gemaakt. Voor de kratten werken we met transportbanden en voor de pallets mets een kettingtransporteur. Beide systemen worden aangestuurd met Elsto Drives & Controls componenten. Zodra de kratten op het einde van de transportbanden komen, detecteren ingebouwde sensoren of het juiste type krat voorbij komt. De sensoren sturen signalen naar de PLC en vervolgens instrueert de lijnbesturing de robot waar de krat moet worden geplaatst. De stroomopname van de geautomatiseerde krattenstapelaar komt omgerekend neer op circa 15-20 Ampère. Rekening houdend met beperkte opstellingsruimte zijn we er toch in geslaagd om aan bijna alle eisen te voldoen. En er waren nogal wat variatiemogelijkheden, zoals de diverse laaghoogtes (van 8 tot 14 lagen), vier verschillende sorteringen, vaste kratten en klapkratten, hoge en lage kratten, alsmede euro- en blokpallets. Bij slechts één stapelpositie van al deze variaties was het niet mogelijk om de 14 lagen te halen, omdat de reikwijdte van de robot niet groot genoeg was. Maar we zijn achter de schermen hard aan het denken over een oplossing om ook dit te ondervangen.”
HELE AGRISECTOR Volgens Wiermans kan de gerobotiseerde Eterpol krattenstapelaar van Elsto Services een wereld van verschil gaan maken op het gebied van ergonomie in de agrisector. Voorheen werd namelijk uitsluitend gewerkt met pick and place-spots, waarbij altijd dezelfde weg moest worden afgelegd. De Eterpol heeft niet alleen een groter bereik, maar kan ook meer werk verrichten in aanzienlijk minder tijd. In het kader van procesoptimalisatie is de robotoplossing met elektromechanisch transportsysteem echt een uitkomst voor de mensen die nu het zware werk doen in de agrisector. ●
CONTINU WEGENDE MENGER MENGT CONTINU WEGENDE MENGER MENGT

Bij grote volumes is nauwkeurig mengen niet eenvoudig. Met de mengstraat van EMT kunnen volumes van 20 tot 200 ton per uur exact gemengd én gecoat worden.
Hogesnelheids-machine (80 ton per uur) voor het afvullen van bigbags of zakken van 500-1.500 kg..
De weegbunkers zijn open aan de bovenkant en kunnen geladen worden met een loader met schepbak.
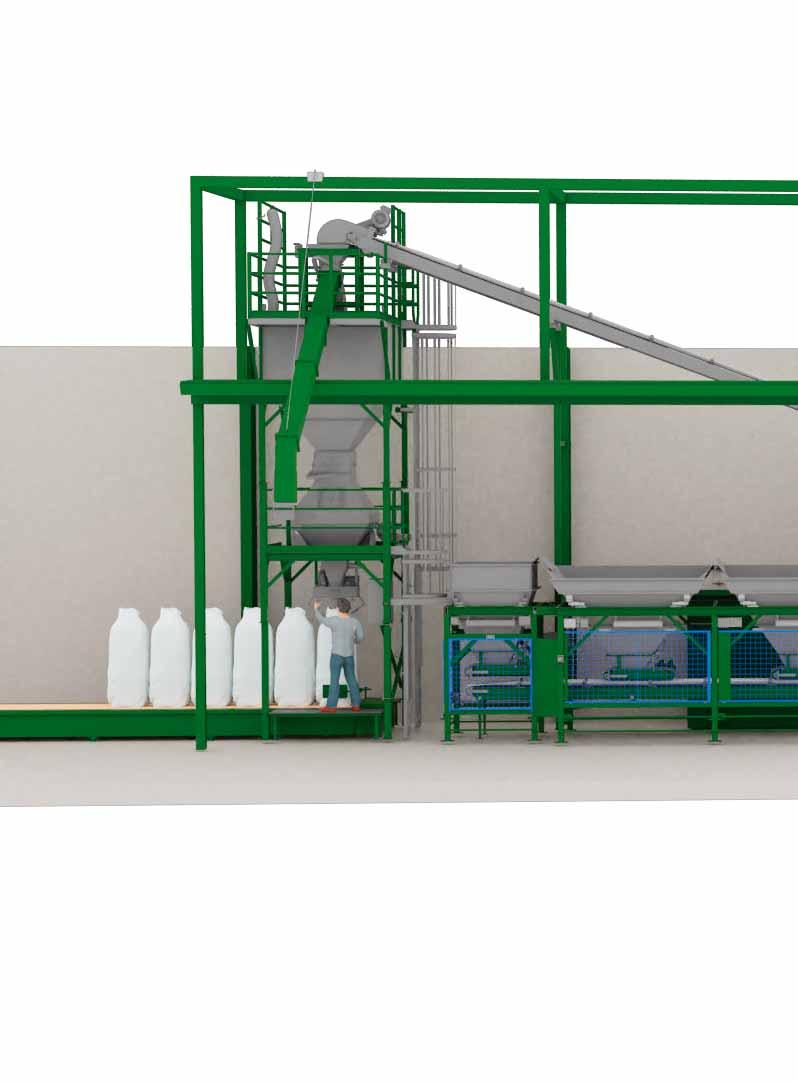

Weegbunker op loadcells


Loss in weight systeem De snelheid van de band en de hoogte van de schuif worden automatisch geregeld.
Digitaal weegsysteem regelt de dosering. De grondstoffen worden in lagen op de afvoerband gelegd. In de mengvijzel worden ze uiteindelijk gemengd.
EN COAT EXACT EN COAT EXACT

Weighcontcontinu wegende menger
De hele machine wordt bestuurd vanuit een pc en kan aan een netwerk aangesloten worden. Daardoor is er complete controle over de kwaliteit van het mengsel. Elke weegbunker heeft een groot display dat informatie geeft over het type materiaal en het gewicht van de grondstoffen in de weegbunker. Tijdens het mengen laten de weegbunkers tegelijkertijd hun product op de afvoerband lopen. De mengvijzel achter de afvoerband zorgt ervoor dat de mengkwaliteit gewaarborgd is. Het aantal weegbunkers dat kan worden geschakeld is ongelimiteerd. Rvs driefractiezeef Een grof en een fijn zeefdek scheiden de te grote en te kleine korrels van de juiste maat korrels.
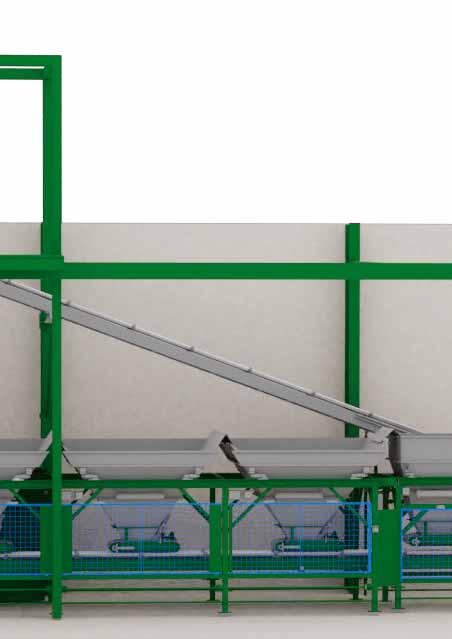
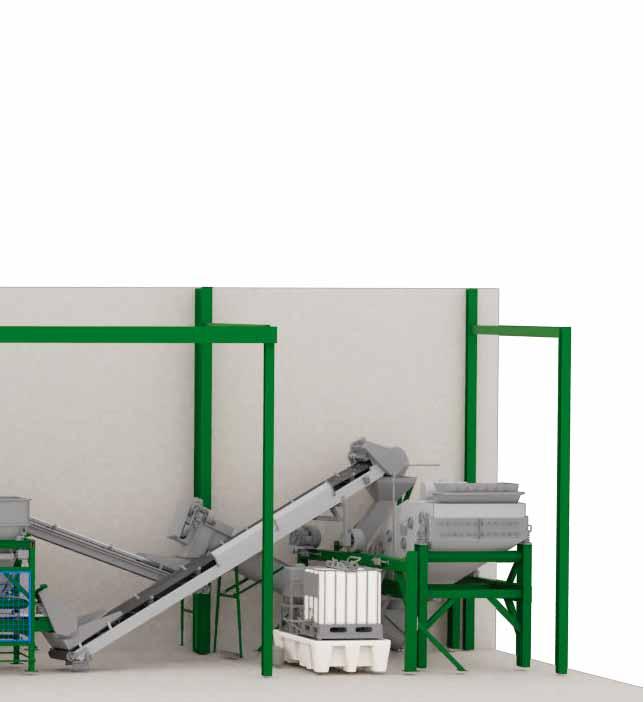
Weegbunkers Coating
Driefractie zeef
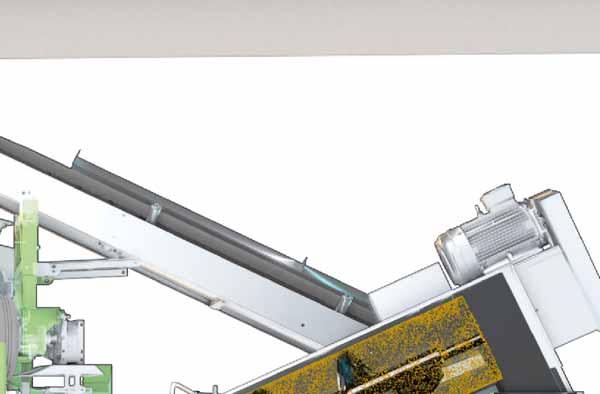
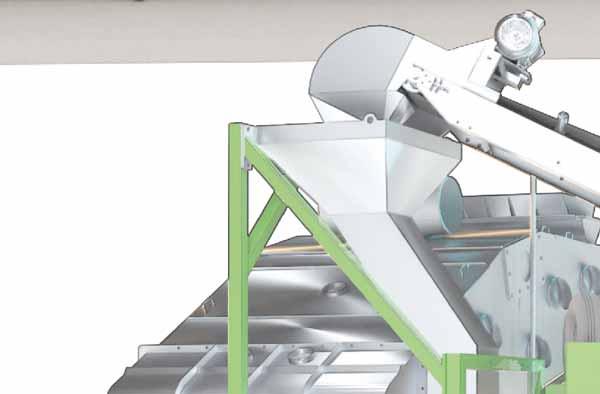
Mengvijzel voor de Weighcont Blender
Richting vulmachine
Grof product. (Het fijne product komt uit een buis die hier niet te zien is.) Product van juiste maat.
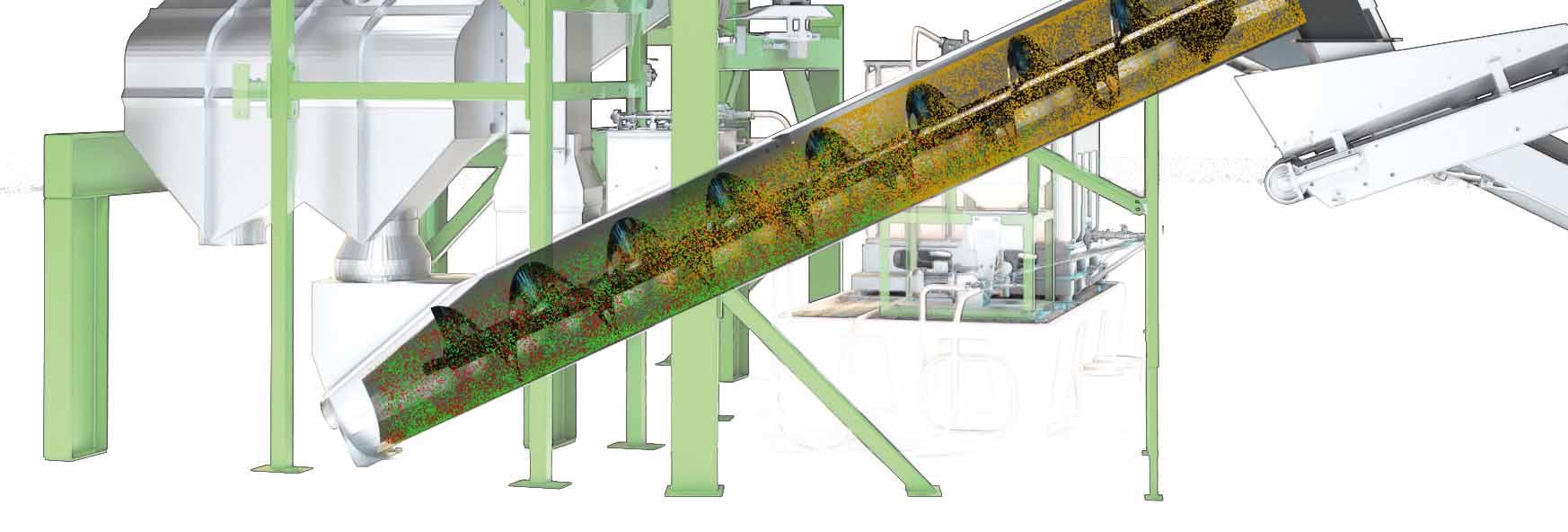
Een rvs vijzel achter de uitloop van de transportband waarborgt de menging. Hier kunnen ook microcomponenten of vloeistoffen toegevoegd worden als die nodig zijn voor de blend.