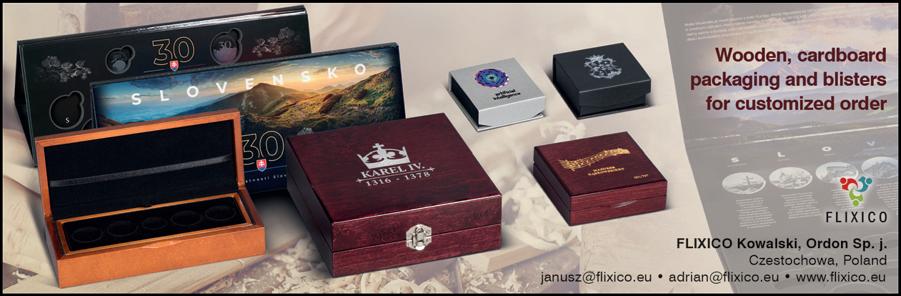
1 minute read
IN EUROPE
Headquartered in The Netherlands, Samlerhuset Group was established in 1994 by partners Ole Bjørn Fausa and Reidar Nilsen. From humble beginnings, the company now has a presence in 15 different countries and markets across Europe, operated by a total of 750 staff.
Equally impressive is the fact that Samlerhuset Group also owns the famous Mint of Norway, where a large part of its production takes place. The Mint of Norway, situated in the former mining town of Kongsberg, is the country’s second-longest running manufacturing entity, having been founded as far back as 1686. In 2003, the Central Bank of Norway sold a 50% stake in the mint to the Samlerhuset Group which later bought the remaining shares in the Mint in 2015.
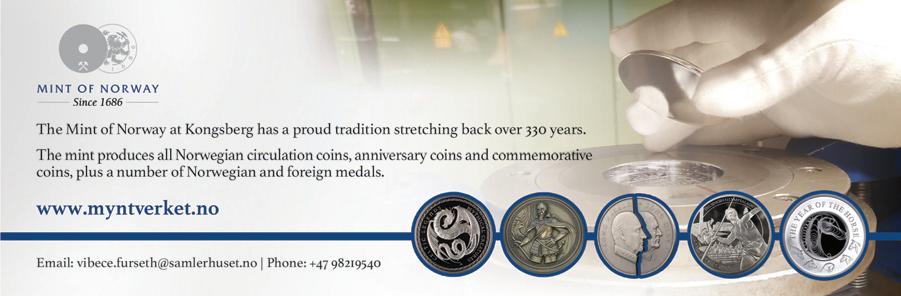
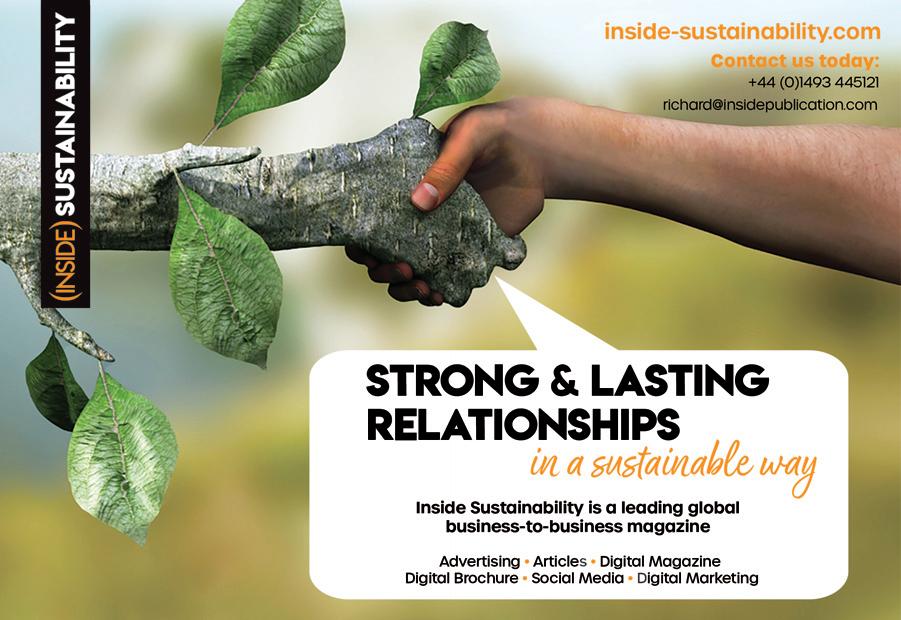
The Mint of Norway still produces all of the legal tender coinage for Norway as well as several other countries, but a substantial part of its work today is in striking the medals, commemorative coins and other collectables commissioned by Samlerhuset Group.
Better in the metal
As one of Europe’s largest coin companies, Samlerhuset Group specialises in the direct marketing of coins, commemorative medals and related collectables to all of its markets across the continent. The company prides itself on superior products made to the highest quality standards and delivered with its trademark first-class service to customers.
Outside of its own manufacturing capacity at the Mint of Norway, Samlerhuset Group also boasts an extensive network of some of the top mints around Europe who together ensure that Samlerhuset Group can accommodate almost any product specification required by a customer.
Big-ticket projects
Samlerhuset Group’s project portfolio is the best example of the company’s manufacturing versatility. Past projects span some truly epic events, celebrations and milestones including minting the Nobel Peace Prize medals, and selling various medals and collectables for the Olympic Games.
Notable recent projects include Samlerhuset’s substantial donations and participation in significant projects alongside non-profit companies such as Waterloo 200, The Imperial War Museum and the In Flanders Fields Museum.
While these projects are impressive, Ms Mulon took us behind the scenes of the even more impressive amount of background work required to bring them to life, owing to the surprising number of moving parts involved.
“From the conceptualisation of the product until its final stage of readiness for shipping to the customer, takes about six months,” Ms Mulon explained. “The process includes dozens of partners, established processes, highly experienced employees, top-notch creative designers, effective production and logistics and of course, great sales and marketing.
“I don’t think many people outside of the industry realise how demanding the process is.”
Paying it forward
A critical part of Samlerhuset Group’s mission is social and environmental responsibility, not only in its local markets but also globally. To this end, Ms Mulon highlighted two social responsibility programmes that the company is involved with.
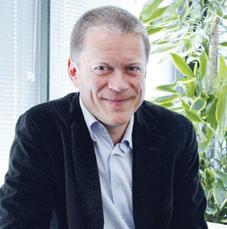