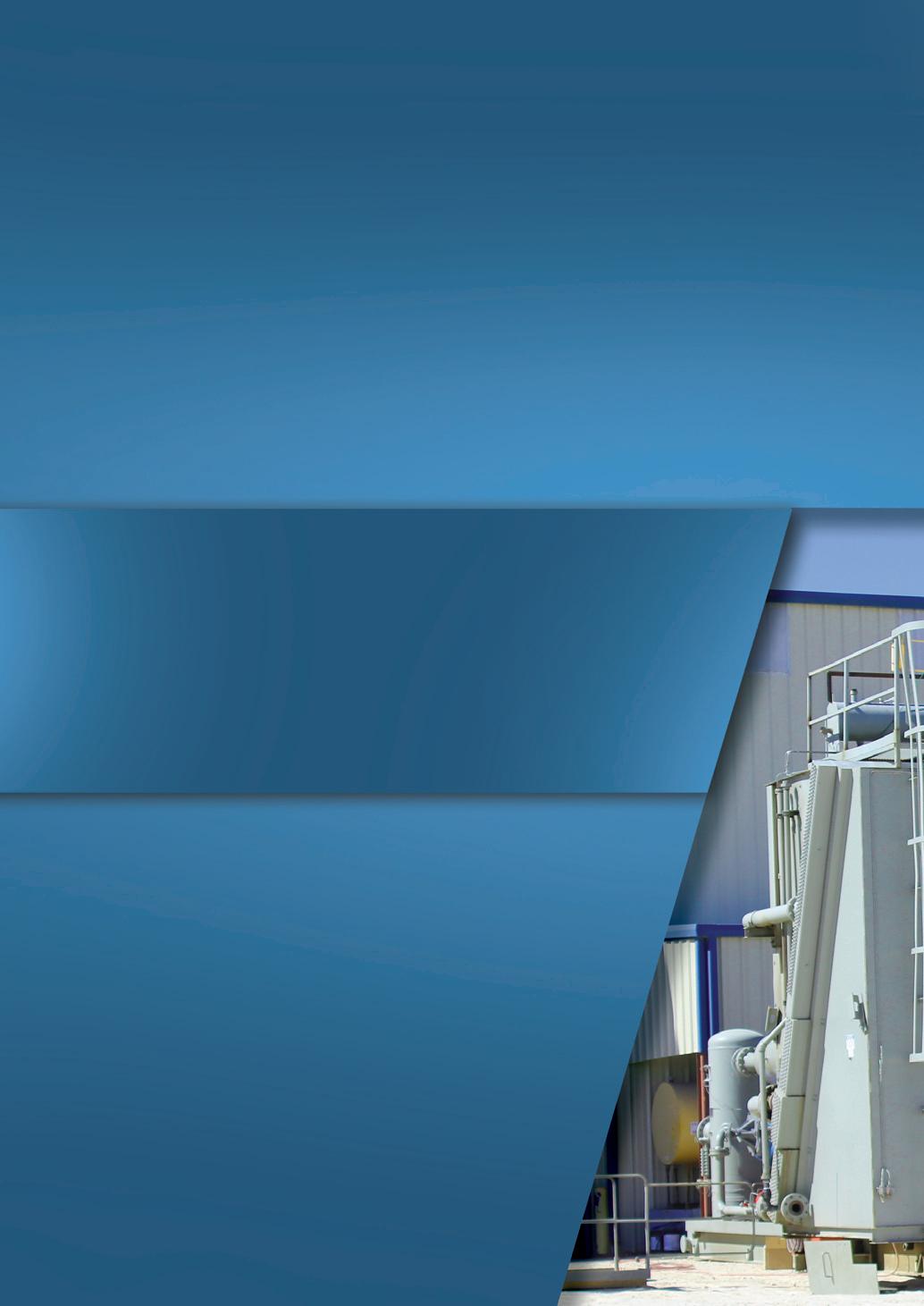
6 minute read
Compressor services across the USA
from OG34
ARKOS FIELD SERVICES I PROFILE
COMPRESSOR SERVICES
across the USA
Texas-based Arkos Field Services is an experienced compression and equipment service partner, specialising in all brands of natural gas compressors and engines. President Bill Sayre related recent events at Arkos and highlighted the depth of knowledge within the team, in conversation with Phil Nicholls.
Earlier this year, Arkos Field Services was recognised as an authorised service provider for Zahroof Valves Inc, manufacturer of the innovative StraightFlo valve for reciprocating gas compressors. This partnership expands even wider the range of services offered by Arkos.
“Being an authorised dealer is really about investing not only in the inventory that we need to make the product available, but also how we’re making an investment in our people,” explained President Bill Sayre. “At Arkos Field Services, we train our salespeople to understand Zahroof’s values and can communicate these details with the customer. We also train our technical people –our team of field service technicians.”
Arkos was formed in 2014, with a management team that has decades of industry experience. At the close of 2016, Swiss-based Burckhardt Compression took a minority stake in Arkos. This partnership with the worldwide market leader for reciprocating compressor systems – and the only manufacturer and service provider that covers a full range of reciprocating compressor technologies and services – brought great depth to the Arkos range.
Finally, in 2019, Burckhardt celebrated its 175th anniversary and purchased the remaining share of Arkos, bringing it into the fold as a fully owned subsidiary. The current organisation of Burckhardt Compression is divided into the Systems and Services divisions. While the Systems division is focused on the sale of new Burckhardt compressors, the Services division will maintain and repair any brand of compressor.
The parent Burckhardt Group has a global operation, but Arkos is focused on the US market with 160 employees spread across 11 locations.
Arkos sites are based around the Permian Basin, with additional facilities in Oklahoma, Pennsylvania, Louisiana and California.
“We have a very broad range of what we offer,” Mr Sayre said. “In our facilities, we can do revamps, reconfigurations of compressors, make-ready services and inspections. Arkos does everything associated with servicing a customer’s asset. This is whether the client is an end-user, consumer or producer, a midstream company or a contract compression rental company. If you move gas down the pipeline into the downstream business, then we provide the same services.”
Technical knowledge
This wide portfolio of services is further enhanced by the partnership with Zahroof Valves. The StraightFlo valve from Zahroof is marketed as a replacement for conventional valves and consists of standard modules or cartridges held stationary between a valve seat and carrier.
Arkos technicians are certified as authorised service providers. While this new partnership helps Arkos offer a greater range of services to clients, it is also another acknowledgement of the depth of knowledge in the Arkos team.
“Arkos has a full-time, dedicated training department,” explained Mr Sayre, “where we train on every piece of equipment imaginable. One area that is crucial for us is the basic understanding of mechanical principles. Arkos is a third-party certified training facility, which we operate both internally and externally. We bring folks in, assess where they are, then provide the training that will take them to the highest level.”
The depth of knowledge at Arkos enables the technicians to offer exceptional levels of support to the customer, according to Mr Sayre: “We have the technical capabilities; no matter what brand of compressor, our team can always help the customer. Maybe they need a revamp, perhaps
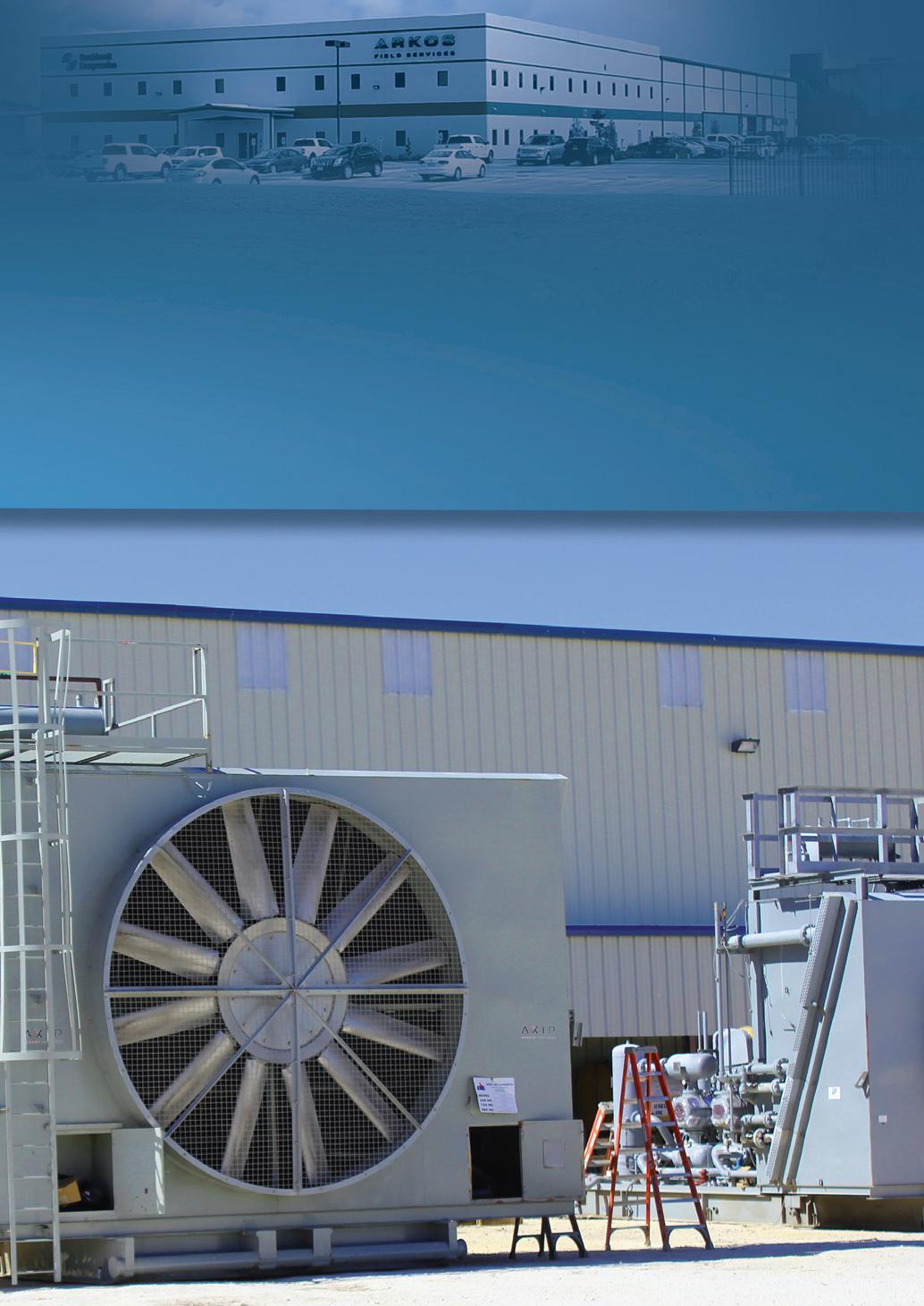
ARKOS FIELD SERVICES I PROFILE
a process requires updating, or an efficiency can be gained.
“Our technicians provide the client with a compressor integrity study, where we assess the engineering and analyse the compressor’s operation. We provide the client with a recommendation that will either improve reliability, performance or upgrade the compressor based on the current operating conditions.”
When an Arkos technician visits a client, the compressor could be anywhere up to 25 or 30 years old. Thanks to the level of knowledge and experience within the team, Arkos has the ability to bring the compressor back online, upgrading with the latest technology where required and ensuring that even these older assets remain productive for the client.
Skill challenges
To maintain this level of expertise within Arkos is a challenge. While the global supply chain disruption brought many problems, Mr Sayre recognised the difficulty of sourcing enough skilled staff as a greater obstacle for Arkos. The company takes deliberate steps to retain staff with competitive wages and an employee wellness program.
In partnership with sustaining the employees, Arkos also has an eye on broader environmental sustainability. As Mr Sayre observed, a compressor service can have several positive environmental impacts.
“Number one is how longer times between failures means fewer compressor services are needed,” he said. “These are an issue because before a compressor is serviced, the technician must vent the gas into the atmosphere.
“Secondly, most gas compressors in the field today are engine driven. So, if we can fit a new, high efficiency valve into a compressor, then the client is now moving
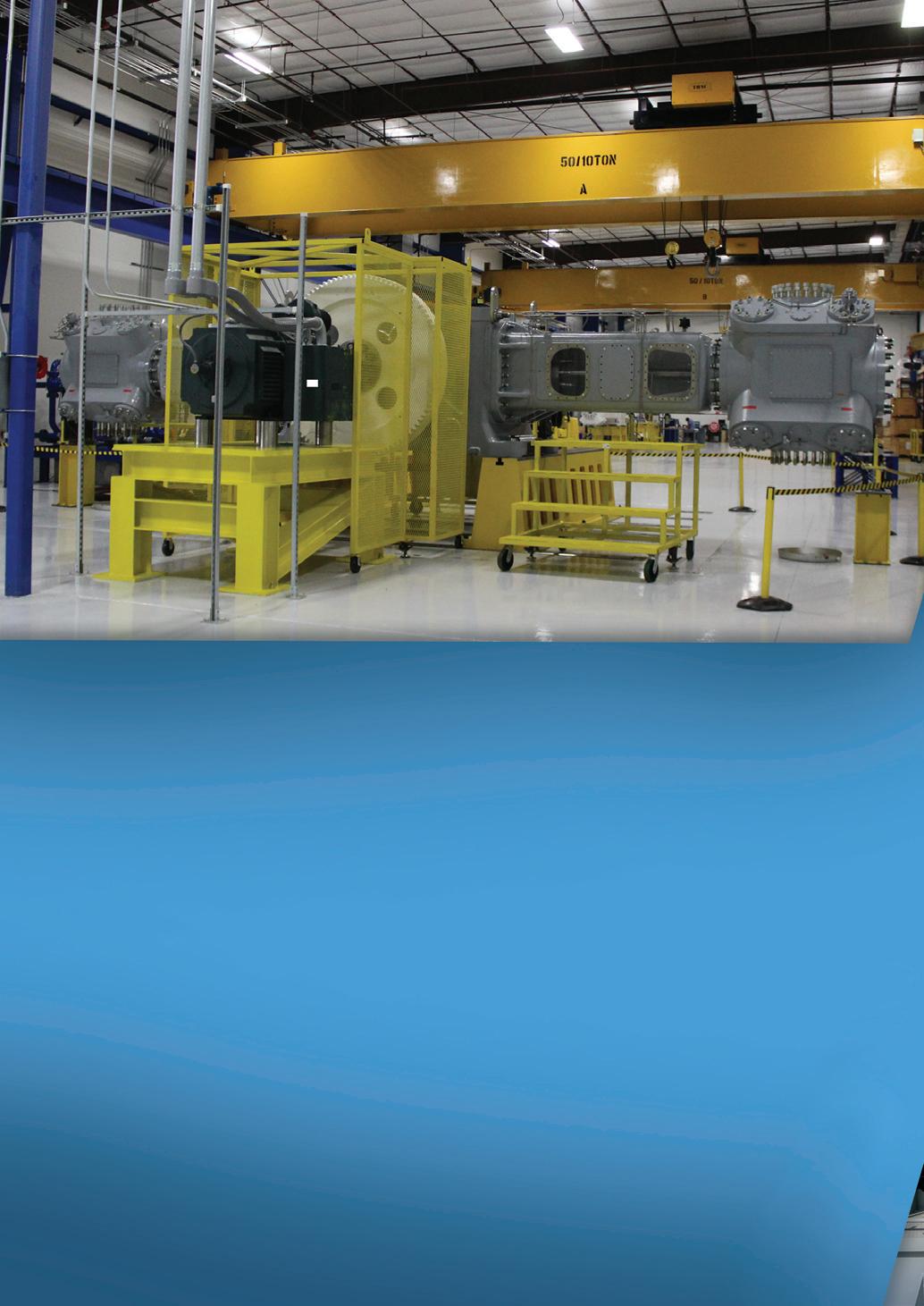

more gas using the same horsepower. It’s not just the government driving environmental standards, but our customers are also very focused and conscious of their environmental impact. These investments in upgraded control systems allow a client to take their units anywhere in the country, as they are already following the most stringent emission requirements for the compressor.”
Arkos has recently become an Authorised Murphy Provider (AMP) of FW Murphy’s new Engine Integrated Control System (EICS) for Waukesha VHP engines through Spindletop Energy Products’ new program.
Arkos is also an Authorised Genis dealer. Genis has integrated patented cooling technologies and controls into their compressor systems which drive efficiency and operational flexibility while also leading the industry in acquisition cost. Arkos is well positioned to sell and support these compressor systems.
Future opportunities
The future of Arkos is closely tied to the parent company Burckhardt Group with a forthcoming rebranding of the US operation under the Burckhardt banner. While this merger will not affect the range of compressors and services offered within the US, it will bring a simplified brand experience for the customer.
Looking to the broader energy sector, Mr Sayre sees opportunities for growth within the sector’s transition: “Even the solar business is positively impacting our compressor business, because we manufacture the hyper compressors used in the creation of plastics for solar panels.
“Hydrogen will be a big part of the energy market, certainly there’s a lot of investment happening there as the hydrogen mobility and energy expands. The focus at Arkos is to support the broader compression market and position our services to supply these new customer demands.
“We have a great team, working for a great company,” Mr Sayre concluded. “One of the exciting things about Burckhardt is that there aren’t many companies around today who have been in business for almost 180 years. Burckhardt Compression clearly has a formula for success. We have a team of skilled employees at Arkos, and everybody is service-minded. Everybody works with a spirit of urgency, getting things done and solving problems. When that is your mindset, the company becomes a great place to work.” n
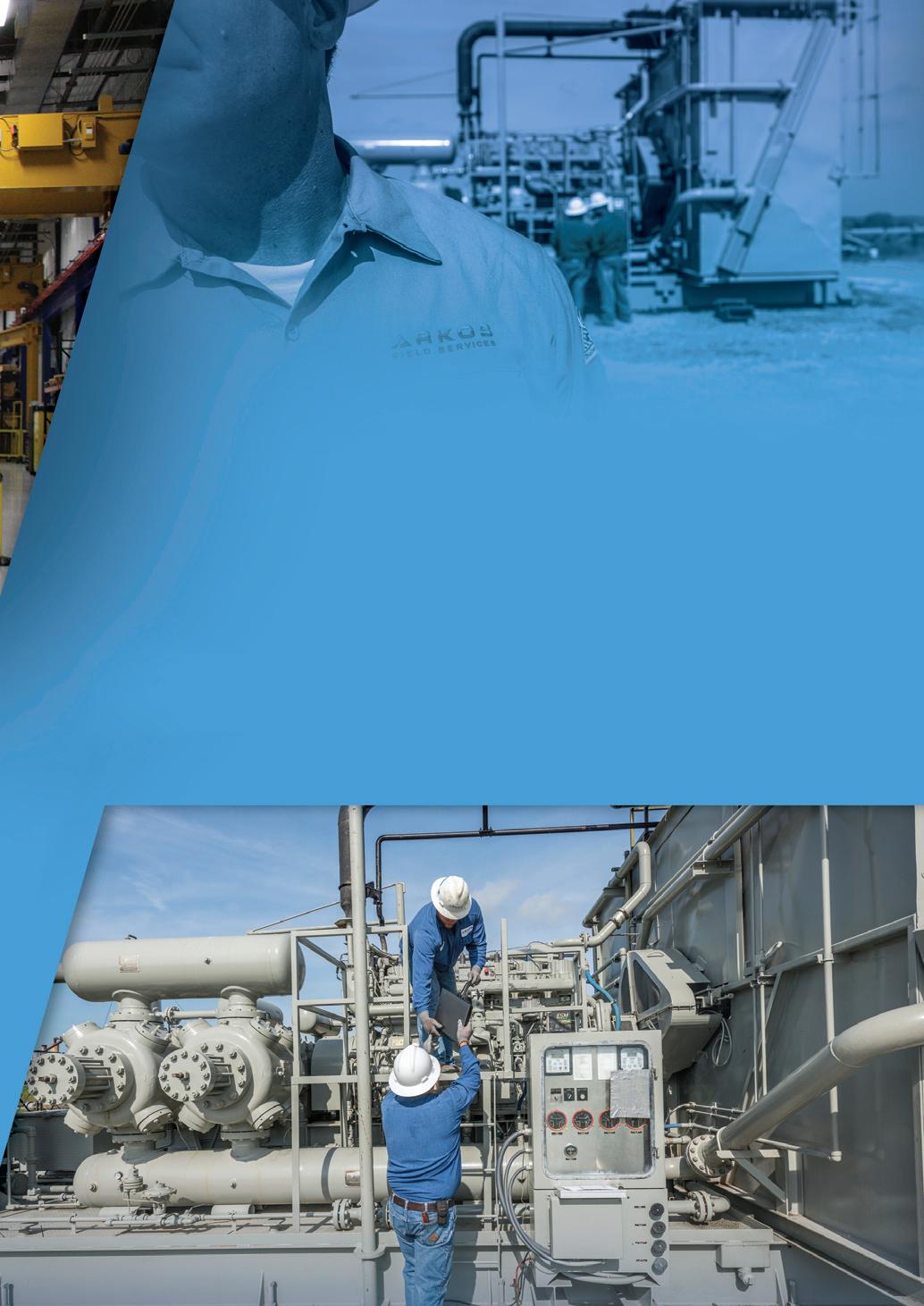