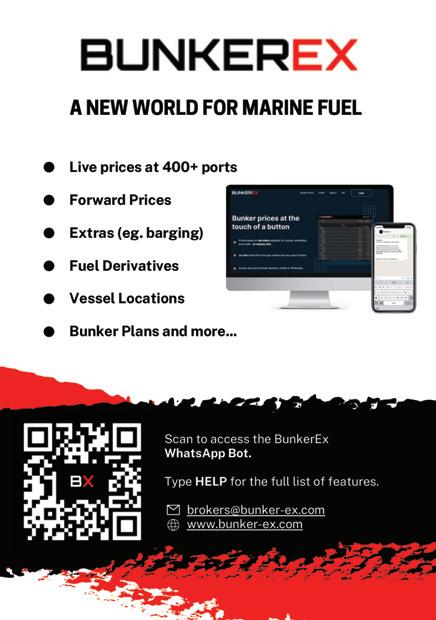
5 minute read
OF H E A V Y LIFT
Founded in 2014, Norway’s GPO Heavylift manages a fleet of bespoke, semi-submersible heavy lift vessels. The company specialises in carrying massive cargo loads across oceans to all corners of the globe. It is a difficult and specialised job requiring specialist people, specialised skills and, of course, a fleet of capable vessels. CEO Dagfinn Thorsen spoke to Richard Hagan about what it takes to carry the cargo that nobody else can.
When it’s time to move very large cargo across an ocean, you need GPO Heavylift and its fleet of custom-designed, semi-submersible heavy lift ships.
Advertisement
The company was established in 2014 by a group of Singaporean investors with experience in the offshore category. That same year, GPO Heavylift commenced the construction of its four bespoke semisubmersible heavy lift vessels. The fleet was specially designed by CEO Dagfinn Thorsen, together with a captain who is a long-time colleague, to suit the company’s specific needs.
Mr Thorsen, a 40-year veteran of the maritime industry, immediately established the commercial viability of the new ships when he secured a transport contract for the first vessel even before any steel was cut. “The contract was to move an Aibel platform to the Johan Sverdrup Phase 2 project owned by Equinor, from Thailand to Norway,” he recalled. “They required the same service again two years later and, based on our successful completion of the first one, we were awarded that contract, too.”
The four vessels were delivered starting with the first vessel in July 2017, while the second arrived in March 2018. The third was delivered in December 2019 and the fourth and final one was completed in October 2021. The fleet has the distinction of being the only four purpose-built semi-submersible vessels of equal design presently in operation in the world.
Specialised expertise
G PO Heavylift’s facilities span three sites and about fifteen staff. Its Singaporean office is responsible for the company’s financial administration, while its office in Oslo - with about six staff - is focused on chartering, engineering and operation. Technical Management and crewing are handled by Wilhelmsen Ship Management - also in Oslo, Norway.
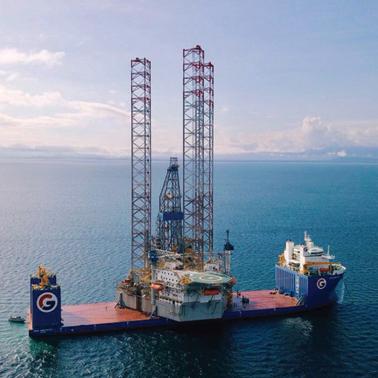
Within its staff complement, GPO Heavylift boasts three highly experienced loadmasters with decades of combined experience. The loadmasters are responsible for travelling to the ships and supervising the loading and discharge operations.
Mr Thorsen recalled how the pandemic and all its travel restrictions had forced the company to find new ways of conducting its business, particularly in the loading process. “We learned to do remote loading supervision. We even brought a company in to install video cameras both on the ship and on the quayside so that we could watch the loading operation from anywhere. We managed to conduct a loadout with people sitting in different places around the world, communicating remotely with the on-site crew and the yard. That was a new experience that we’d do again, but only if need be!”
Loading up on preparation
The CEO highlighted the fact that while the amount of work that goes into the loading process would surprise many casual observers, the first thing that often catches inexperienced people by surprise is a semi-submersible vessel’s operation in preparation for loading. “Some people are relatively surprised when they see the vessel begin submerging. We’ve even seen people ring the alarm system because they think that the ship is sinking!” he said with a chuckle.
With the typical understatement of a seasoned professional, Mr Thorsen described the process of loading 25,00030,000 tonne cargo as, “interesting,” adding: “Each and every project we’re involved with is different from previous projects. Even when you’re loading the same cargo at the same place, it’s still treated as totally new, every time.”
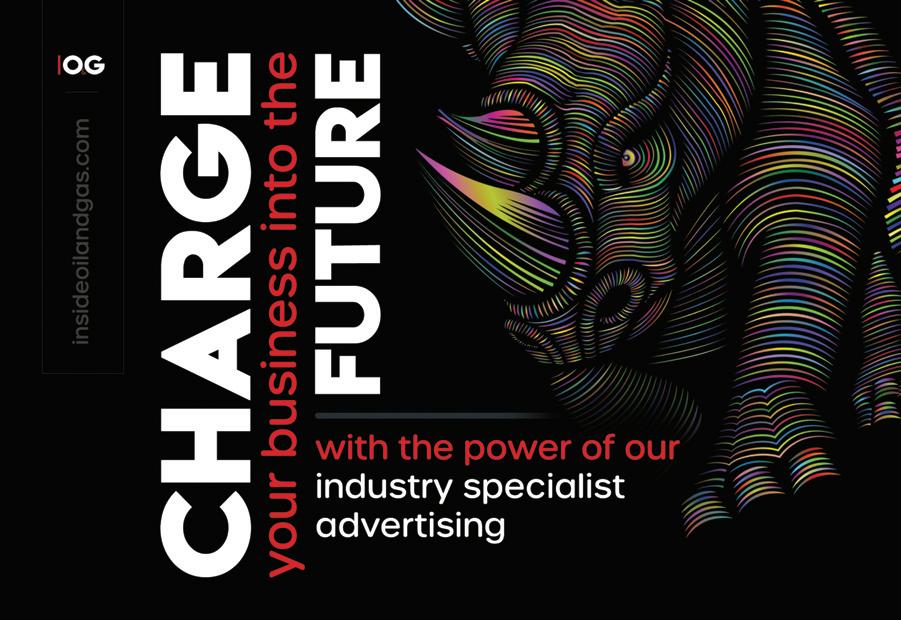
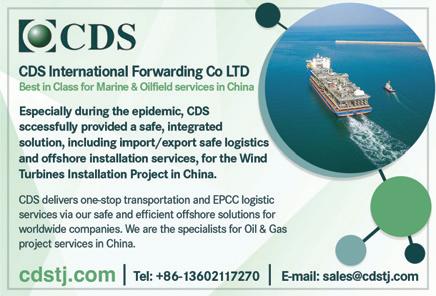
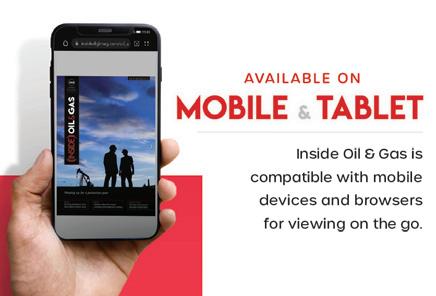
Given the massive size of some of the cargo being loaded on to GPO Heavylift’s vessels, preparation and constant attention to the smallest detail is absolutely imperative. “You have to begin by preparing the ship to receive the cargo,” Mr Thorsen explained. “This involves going through all of the drawings of the cargo and ensuring that the information therein is all correct. That said, these days it’s a bit easier because we’re able to request photos of the cargo ahead of time, to verify our preparations correctly.”
The next step is a big one and it involves preparing the GPO Heavylift vessel’s deck to receive the load. “We fit timber cribbing to the main deck in a pre-designed pattern so that it lines up with the bottom structure of the cargo. We have to land the cargo directly on top of the cribbing. There’s absolutely no room for error here because the positional tolerance is relatively small – normally not more than +/- 5cm.”
To further ensure precision and security of the cargo, two massive guideposts are also welded to the vessel’s deck. These help to guide the cargo into exact position and to hold it in place.
“Once we see that the cargo is in position, we de-ballast the vessel and begin the lifting process. This can be quite challenging and very specific ballasting procedures have to be prepared in advance,” Mr Thorsen emphasised.
Lifting the ocean transport game
GPO Heavylift undertakes, on average, four to six transport jobs per ship per year. The shipment durations necessarily vary depending on complexity and length. Larger loads - for example a drilling rig - are too big for transiting canals and must be carried across the oceans, adding to the contract duration. But as Mr Thorsen highlighted, the versatility and safety of a heavy lift transit are proving to be irresistible for an increasing number of customers.
“There aren’t too many alternative means to carry the loads that we transport,” the CEO noted. “But it depends on the project.
For example, if a drilling rig needs to be transported across the open sea for more than five or seven days, then there aren’t too many options. Jackup rigs don’t have any alternatives to heavy lift, but selfpropelled rigs can sail by their own power Still, some companies prefer a dry tow (on the deck of a heavy lift vessel) because it’s safe and fast and they can save some money on insurance and crew. But all in all, almost everybody prefers to use a heavy lift vessel nowadays.”
GPO Heavylift’s managed fleet, namely GPO Grace, GPO Amethyst, GPO Sapphire and GPO Emerald, are identical in specification and feature an impressive length of 225m and a breadth of 48m. Of that, 183m of their length is available for loading, as is the complete breadth of 48m. All four vessels weigh in at 64,000 tonnes dwt and can submerge to a depth of 15 metres water above the deck.
The vessels feature fully redundant propulsion systems consisting of four 8,000 kW engines, as well as two 1,750 kW bow thrusters and two 1,000 kW stern thrusters. The vessels are also equipped with a DP2 dynamic positioning system
Of course, the fleet’s cargo lifting capacity is the centre of attention, and those numbers are impressive to say the very least. The fleet can lift Jackup rigs of up to 35,000 tonnes, and semi drilling rigs of up to 40,000 tonnes. A non-floating module of up to 25,000 tonnes can alternatively be carried, as can a spar-buoy.
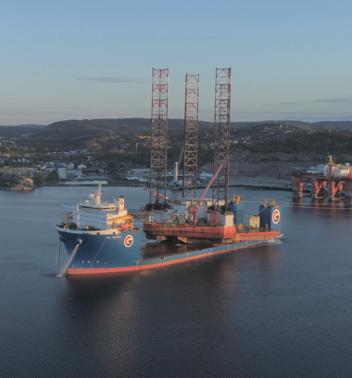
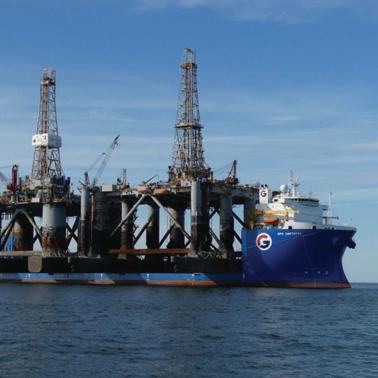
Mr Thorsen pointed to the identicality of the company’s fleet as a major selling point for larger projects. “Serious clients like the fact that our setup features four identical vessels. Our fleet is fast, they feature strong decks and reliable machinery matched to a unique ballast system. They’re much more versatile than most of the competition.”
Shipping into the future
Looking into his metaphorical crystal ball, the CEO was justifiably optimistic about the company’s prospects. “The offshore wind energy business has really taken off, so it’s become an increasingly interesting market for our vessels. In fact, all four vessels will be busy in offshore wind throughout summer 2023, carrying cargo from Europe to the US East coast, sailing back and forth a few times
“It’s such an active market that I hope to build more identical vessels,” he continued “We’re discussing with the vessels’ owner the possibility to build more vessels and hope we can proceed in due course.”
He concluded with some remarks about the business. “I’ve spent all my life in this industry; I like it so much that I work basically every day including weekends and public holidays. And I love my staff - I have really good people working here in GPO. I follow the ships online every day. The job is a huge part of my daily life.” n