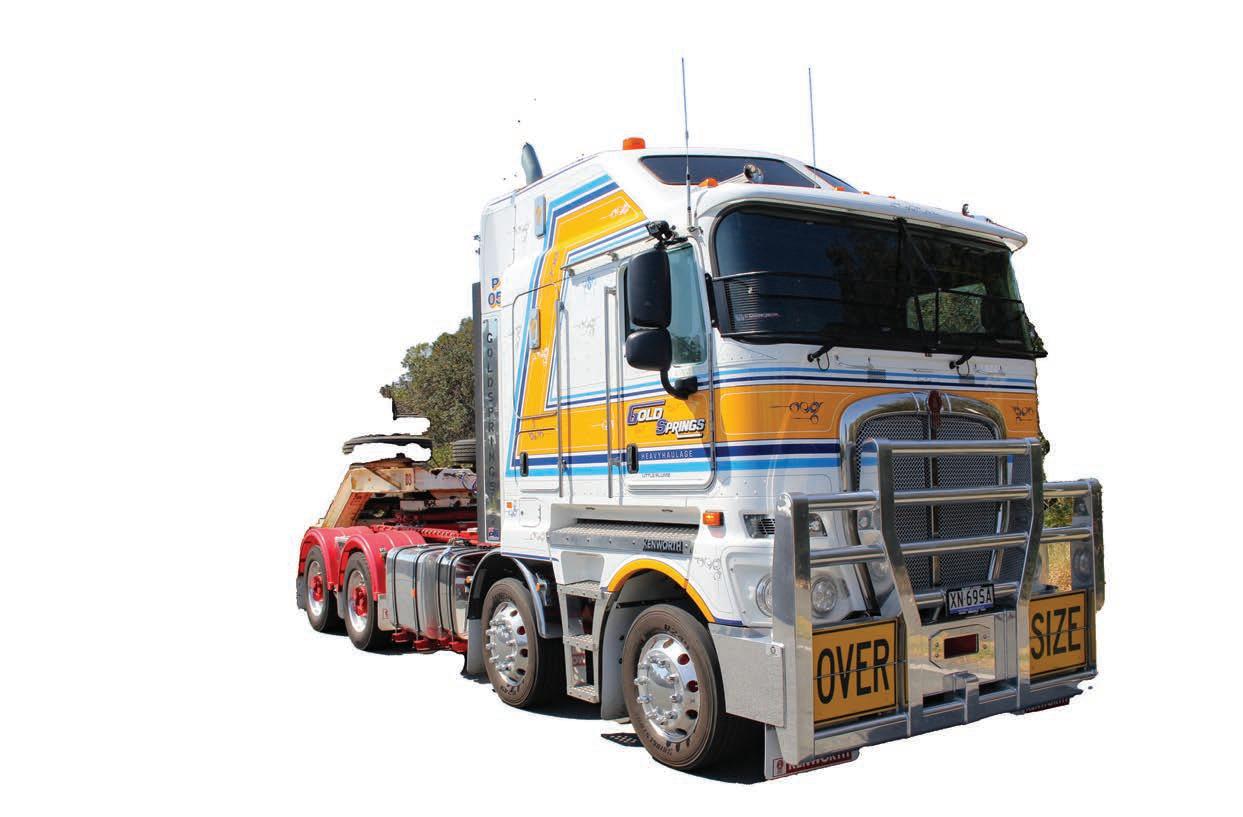
13 minute read
Haul Rise
RISE HAUL
Heavy-duty truck axle manufacturer Meritor has introduced its P610 hub-reduction drive axle to the Australian market. Goldsprings Heavy Haulage has specified the product in a new Kenworth K200 8x4 prime mover.
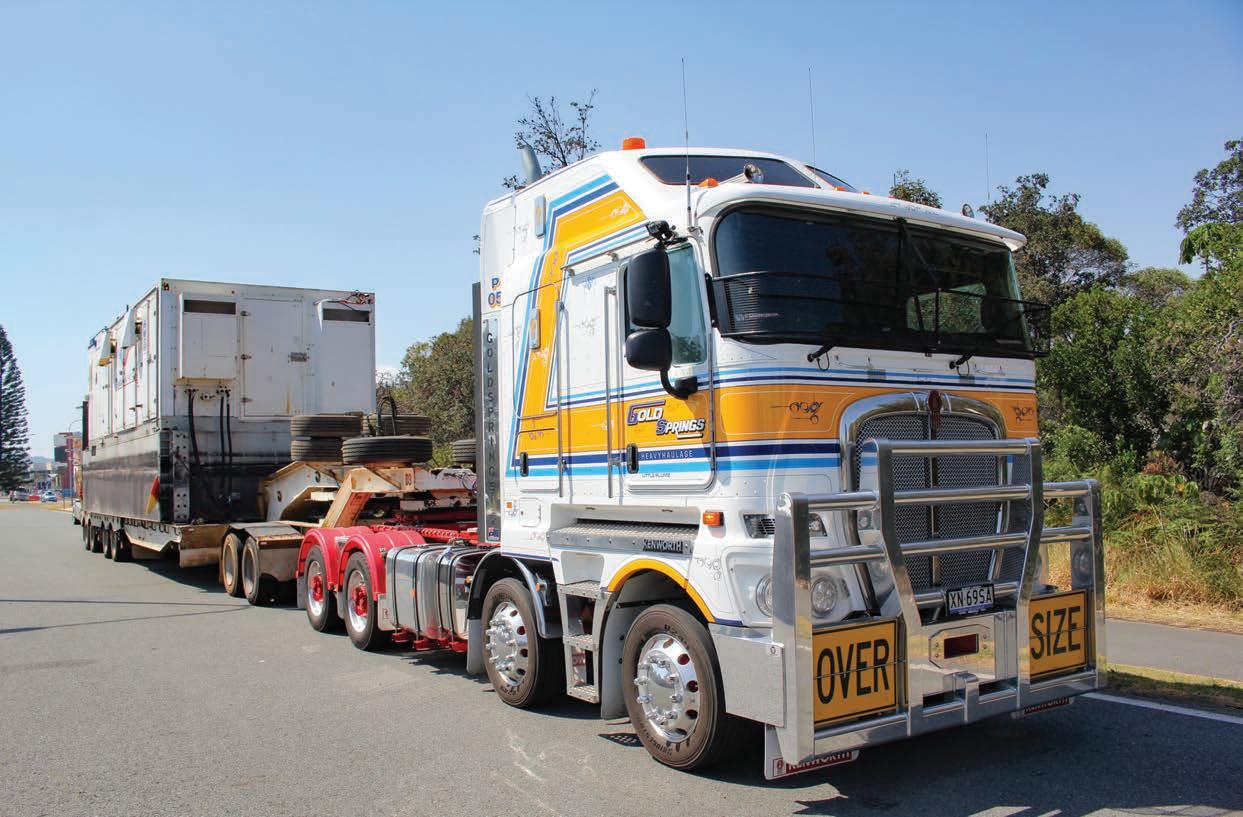
Hauling gross combination masses (GCM) of up to 240 tonnes up steep inclines requires axles and drivelines of Herculean proportions. Under these conditions standard heavyduty truck axles simply won’t cut the mustard and it’s necessary to employ hub-reduction units which feature a planetary gear set at each wheel end that significantly multiplies the torque delivered to the wheels by increasing the final drive ratio. As a leader in the truck axle manufacturing sphere, Meritor is constantly developing and reengineering its products to meet the ever-increasing demands of truck operators, particularly those at the ultra-heavy end of the heavy haulage spectrum. One such operator is Goldsprings Heavy
Haulage, a company based at Rutherford in the NSW Hunter Valley that has been in operation for more than 25 years. The company’s Director, Mark Goldspring, explains that he was looking for a hub-reduction axle that would be more efficient at highway speeds while still providing the low-end grunt necessary for steep climbs at maximum GCM. “We wanted to be able to maintain a higher road speed to enhance suitability for our application which involves moving oversize and ultra-heavy equipment all over Australia,” Mark says. “After looking into the new Meritor P610 axle we decided it was the most suitable for our operation.” Meritor’s hub-reduction axles have been available globally for some time, however the company has now considerably broadened the product’s appeal by re-engineering it to suit the Australian market. The first to capitalise on these improvements has been Kenworth — a popular choice among heavy haulage operators. According to Mark Goldspring, his 8x4 K200 which was delivered mid-2020 is the fifth Kenworth to be fitted with the P610 hub-reduction axles and while it’s early days and the truck is yet to cover 50,000km, it has shown fine fettle when hauling 100-tonne concrete beams up the mountain from Batemans Bay to Canberra. Adapting the P610 axle to suit the Kenworth chassis wasn’t a simple exercise for Meritor. That’s because it required a fabricated axle housing that is manufactured in the USA. In contrast, the P610 used in Volvo trucks has a cast iron housing. According to Renzo Barone, Meritor’s Australian Territory Manager – Truck, the thick-walled fabricated steel axle housing is extremely strong and allows the suspension brackets to be welded on in different locations to suit a variety of truck brands of North American origin. “The fabricated housing allows us to weld on localised suspension bracketry which you can’t do with the cast housings that the European trucks utilise,” Renzo says. Another benefit of the P610, he explains, is that it has five planet gears in the wheel end instead of the usual four which provides additional tooth contact surface area, thus enhancing service life and durability under arduous conditions. “This is also the reason why the P610 performs very well at highway cruising speeds of up to 100km/h and doesn’t experience high heat build-up under these conditions,” Renzo says. “The design of the hub cap assembly has ample room to allow a good flow of oil which helps dissipate the heat.” The hub-reduction ratio of the P610 is 3.46:1 and there is a broad spread of differential ratios available starting at
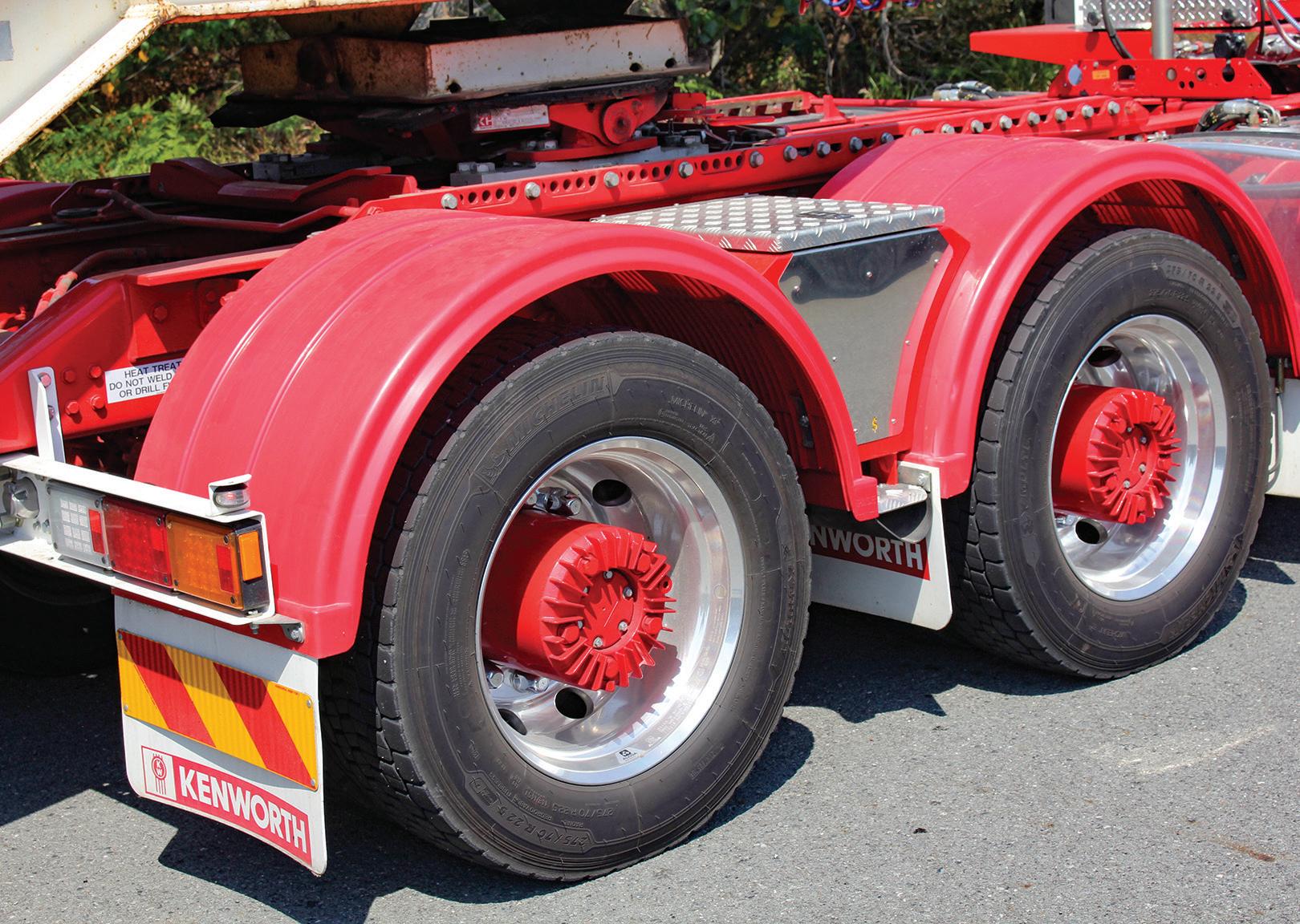
Meritor’s P610 hub-reduction axles on the Goldsprings’ K200.
Goldsprings’ K200 runs a 4.67 ratio for a cruising speed of 90km/h at 1,750 engine rpm in top gear.
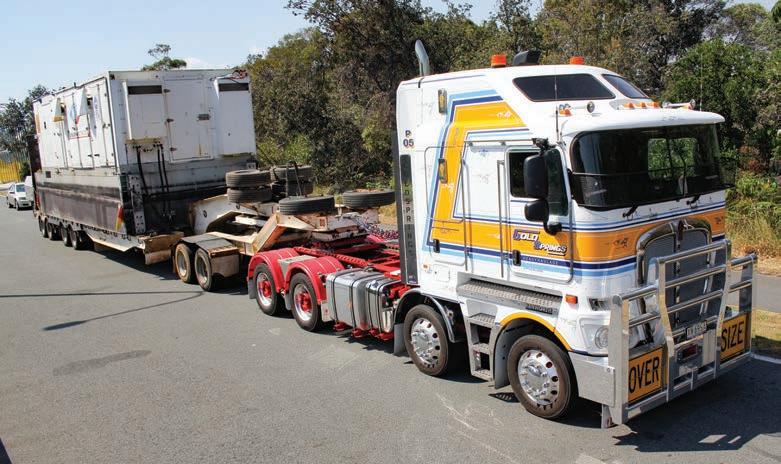
Mark Goldspring Director of Goldsprings Heavy Haulage
1:1 which provides a 3.46:1 final drive ratio through to7.20:1. There are, in fact, a total of ten final drive ratio options encompassing 3.46, 3.6, 3.77, 4.12, 4.57, 4.67, 5.4, 5.47, 6.2, and 7.2. Renzo is keen to point out that the differential carriers used in the P610 hub-reduction axle are common to other drive axles in the Meritor range, meaning that high levels of after-sales support and parts availability are assured. On that point, Renzo adds that the
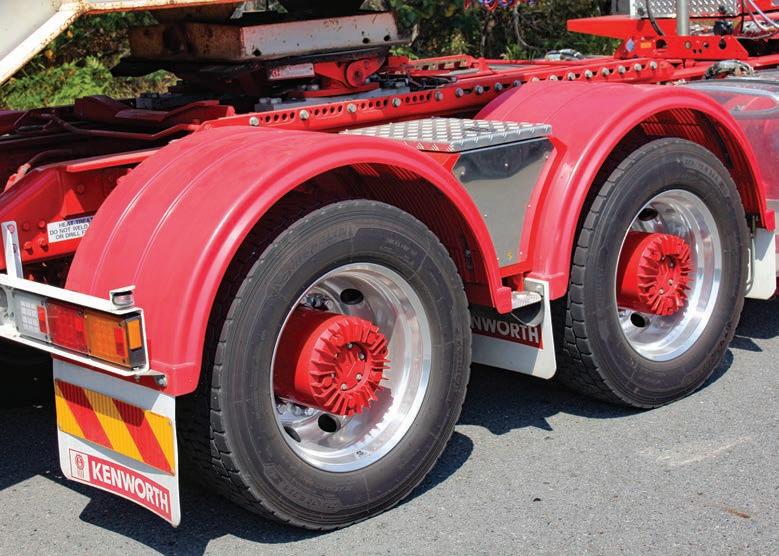
The 8x4 prime mover configuration is rarer on the East Coast. planetary gear set is readily serviceable with the sun and planet gears being easily and individually replaceable if necessary. He also adds that there is an array of magnets positioned inside the housing to contain any wear metals away from gear and bearing components. Goldsprings’ K200 runs a 4.67 ratio which enables a cruising speed of 90km/h at 1,750 engine rpm in top gear. According to Renzo, this is the most popular and ideal ratio in the heavy haulage realm. The unit also features the ultra heavy-duty Meritor Permalube RPL35 driveline which is a perfect match with the P610 axles in severe-duty applications. The tandem rides on Kenworth Six-Rod mechanical spring suspension. The twin steer axles are also Meritor items known as MFS-66, featuring a 6.5 tonne rating which enables a combined steer axle mass of 13 tonnes, subject to taper-leaf spring capacity and legal mass requirements. Goldsprings’ K200 8x4 represents something of an unusual configuration on the east coast, as opposed to the west coast where 8x4 prime movers are quite common. For Mark Goldspring, it was an ideal way to enable more weight on the steer, with the prime mover featuring an adjustable turntable which can be moved in small increments fore and aft to ensure the optimum weight is exerted on the steer axles. “The twin steer axles give us an extra four or five tonnes at the front compared with a single steer axle prime mover,” Mark says. “This means sometimes we don’t need to use a dolly which makes it quicker and easier to get into tight locations.” All up, Mark says he is very pleased with the performance of the Meritor P610 axles to date. “The axles stood up really well to the high weights and steep climbs out of Batemans Bay and we are looking forward to seeing how they perform on the longer hauls across Australia in midsummer with big weights,” he says. “In our heavy haulage operation, I think they are going to be a good thing for us.”
ENDLESS POSSIB
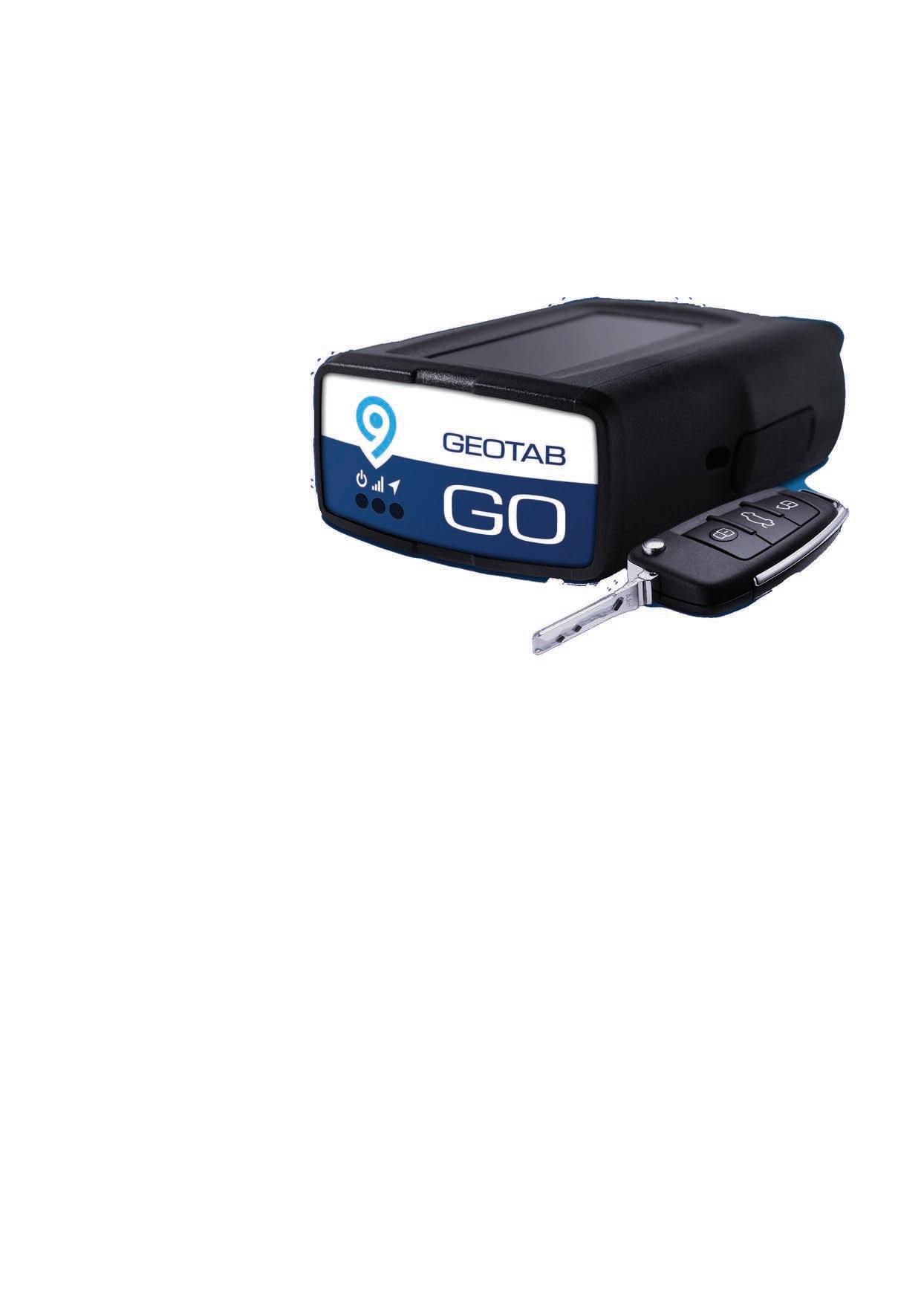
Geotab has been a leading force in fleet telematics in North America and Europe over the past two decades. The company is now expanding its footprint in Australia, offering what it describes as an allencompassing open platform telematics solution tailored to the trucking industry.
There’s no doubt that the global telematics market is growing rapidly as fleet managers seek to gain maximum knowledge about every aspect of the vehicles under their control. Streamlining vehicle operations through optimisation of all operating parameters can add up to considerable savings across the entire fleet. Geotab has a stated aim of advancing security, connecting commercial vehicles to the internet and providing webbased analytics to help customers better manage their fleets. The company claims its open platform and Marketplace – which offers hundreds of third-party solution options – allows both small and large businesses to automate operations by integrating vehicle data with their other data assets. As an IoT (Internet of Things) hub, the in-vehicle unit allows device expansion to provide additional functionality. Processing billions of data points a day, Geotab leverages data analytics and machine learning to help customers improve productivity, optimise fleets through the reduction of fuel consumption, and enhance driver safety. The company’s products are represented and sold worldwide through authorised Geotab resellers. Mark Bucknall, Geotab Associate Vice President Sales ANZ says the company is keen to announce its presence in Australia. “We’re big in North America and Europe and growing strongly worldwide, and we’ve had a presence for some years in Australia,” he says. “However, we have now established a local office and are building out our trucking solution to really help drive productivity and safety outcomes for Australian transport operators.” The open platform, Mark says, undergirds why Geotab is confident it has the best solution in a very competitive space. “We have a Marketplace of solutions, giving customers the ability to import and export their own data and integrate with their existing software. That could mean connecting with sensors monitoring vehicle mass or tyre pressures, sending data to ERP (Enterprise Resource Planning) systems for tax applications, or dash cams for safety and compliance checks,” he says. Geotab claims that after 20 years of continuous growth it has become the global leader in data collection for connected vehicles and is relied upon by more than 40,000 businesses. In fact, the company says on a global scale it collects around 40 billion data points daily from over two million connected vehicles, of which close to 800,000 are heavy trucks. Geotab’s fleet management platform is suitable for all kinds of fleets across the entire spectrum from the largest roadtrains to medium-duty trucks, vans and cars — whether internal combustion powered or electric vehicles (EV). The company drives fleet performance, it asserts, by focusing on six ‘pillars of innovation’ with each pillar delivering value to its customers by managing costs, increasing efficiency, or providing
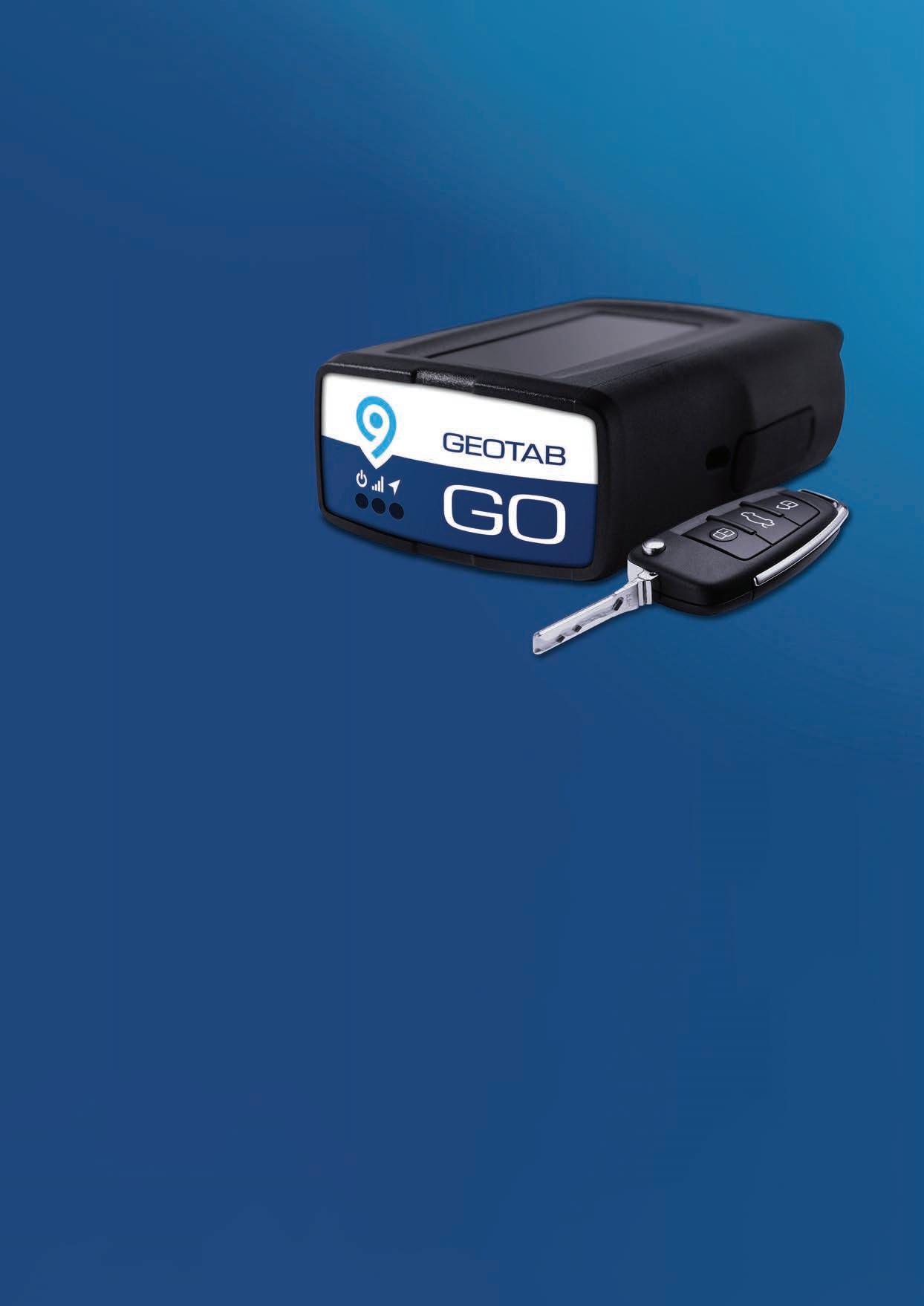
ILITIES
access to its Marketplace of partner services. The six pillars include Productivity – tracking routes and dispatching drivers to ensure a productive fleet; Optimisation – driving efficiencies and cost savings in fuel use and scheduled maintenance; Safety – analysing and encouraging safe driver behaviour with reports and in-vehicle coaching; Sustainability – reducing carbon dioxide and particulate emissions by integrating EVs into fleets; Compliance – ensuring road rule compliance with safety checklists and speeding reports; Expandability – open platform enables the customer to integrate hardware or software options in a tailored solution to drive performance. “We understand what Australian heavy truck operators are looking for and we are building our product portfolio to fully cater to this segment of the market,” Mark says. “We are looking to provide full details of this at the Brisbane Truck Show in May this year.” One of the unique features of Geotab’s open platform, he says, is it enables clients to import or export data to other systems. “We have our Marketplace which is like an App store that connects a lot of different providers,” Mark explains. “If, for example, a transport operator had their own internally built Electronic Work Diary or they used a third-party EWD that has been approved by the National Heavy Vehicle Regulator, that’s the sort of thing that we can integrate with the telematics data. “This means there are a lot of options for customising the platform so that it will do exactly what the transport operator needs it to do.” Another benefit of Geotab’s system, according to Mark, is that the data is recorded every time something changes rather than at set intervals of every 30 or 60 seconds. “Our curve algorithm selects the important data and discards the useless data which actually provides a more accurate presentation of what’s actually happening with the vehicle,” he says. In sum, Geotab’s telematics system is designed to provide the ultimate solution for data collection that is fully customisable to suit each operator’s individual requirements.
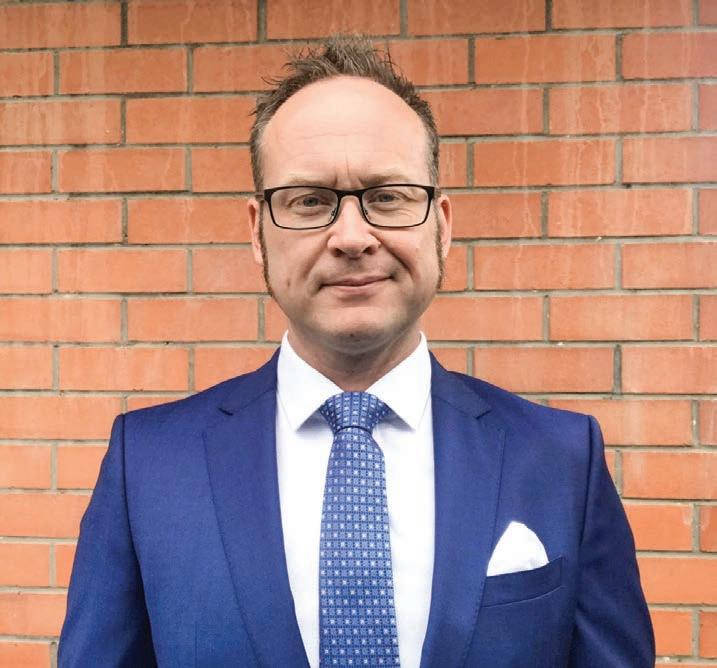
Mark Bucknall.
Mark Bucknall Geotab Associate Vice President Sales ANZ
Toll launched an EWD pilot project involving five of its drivers last year.
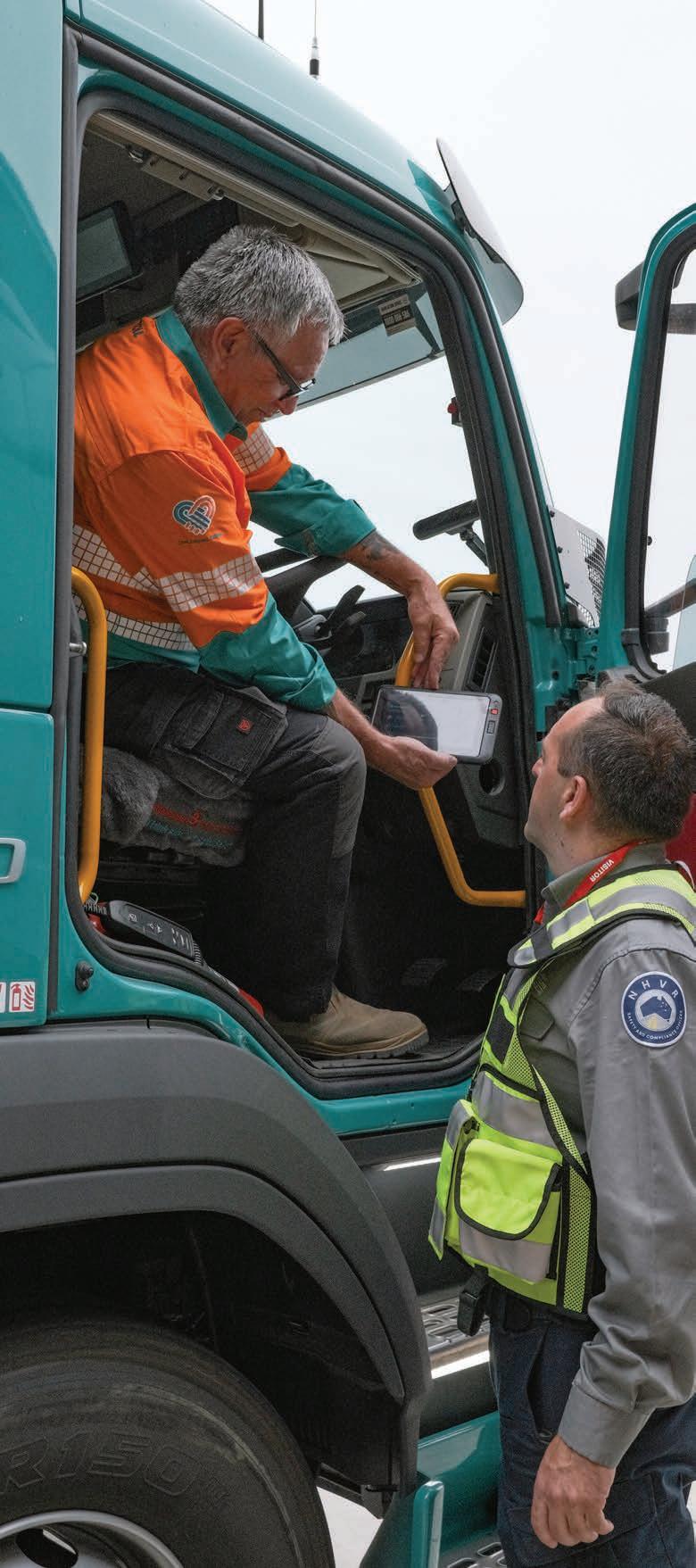
A SAFE BET
Late last year the road transport industry achieved a big step towards a safer workforce with the National Heavy Vehicle Regulator’s approval of Electronic Work Diaries. Teletrac Navman’s EWD solution approved for voluntary use as an alternative to written work diaries, as a digital fatigue management solution makes it easier for operators and drivers across Australia to manage their fatigue compliance.
To date, drivers have been required to use mandatory paper-based written work diaries to comply with strict fatigue laws. Approved Electronic Work Diaries (EWDs) eliminate the risk of erroneous diary entries and lost diaries, while reducing data entry and inaccurate reporting. As the solution becomes mainstream and is adopted by more operators around Australia, the benefits to the wider transport industry and individual operators will become more apparent. From improved compliance and a reduction in red tape for both drivers and operators to more insightful data, proactive fatigue management will provide enhanced on-road safety for all road users. Fatigue is one of the three biggest
contributors to deaths on Australian roads after speeding and alcohol consumption, making it one of the most important issues to address for any operator. EWDs make it far easier to manage fatigue, by giving clear indications of work and rest times for both drivers and their managers well ahead of time, giving a clear view of the driver’s day ahead so they can better plan their journey. For drivers, the EWD device allows them to manage their own fatigue in real time no matter where they are on the road, as the solution works even when drivers are driving through areas which don’t have mobile reception. An electronic work diary enables drivers to more easily manage their responsibilities and compliance, giving fleet managers peace of mind that both their drivers and other road users are safe. Ease of use was front of mind for Teletrac Navman when designing the device, allowing drivers to record their work and rest hours by simply pressing a button, rather than spending time ruling lines and counting multiple time periods on pieces of paper. The benefits extend across other functions of the business, promoting better supply chain management and simplifying planning tools for drivers and transport operators. With the implementation of an EWD and fleet management solution into the business, compliance and safety become an opportunity for growth and improvement. While the business and drivers become proactive with fatigue, the competitive edge provided allow for efficiency and productivity gains according to Andrew Rossington, Teletrac Navman Chief Product Officer. “We are proud to be one of the first telematics providers to be granted full approval from the regulator to roll out our Electronic Work Diary as an alternative to written work diaries,” he says. “The solution will empower drivers and fleet operators to manage their own compliance, giving managers peace of mind that their drivers are safe. The benefits are there for everyone: better supply chain efficiencies, simple planning tools for drivers and transport operators and better road safety outcomes.” A long-term advocate of the solution, Toll Group is one of the first operators to roll out EWDs, launching a five-driver pilot project, with the view to expanding the technology to over 150 drivers by March 2021. Richard Turner, Global Head of Health, Safety and Environment at Toll Group, expects the solution will have a marked impact on both the value of the data being fed to back office and the obvious safety enhancements. “The arrival of EWDs is a very exciting moment for the industry and our organisation and we’re thrilled to be one of the first putting rubber to road. As an organisation, we are safety obsessed and this switch is another example of our ongoing focus on improving safety for our people and communities by investing in meaningful innovation,” he says. The benefit EWDs can bring to the transport and logistics sector is clear. When the coronavirus vaccine is eventually rolled out across Australia and the country opens up more widely, the trucking and logistics sectors will face immense pressures with increases in freight. As these stresses filter down through independent operators, to the truck drivers themselves, enhancing road safety has never been more important. Not only will the rollout of EWDs make the industry more efficient through sophisticated data analysis, it will also make it safer through easier on-theroad fatigue management.
Ease of use was front of mind for Teletrac Navman when launching its EWD.
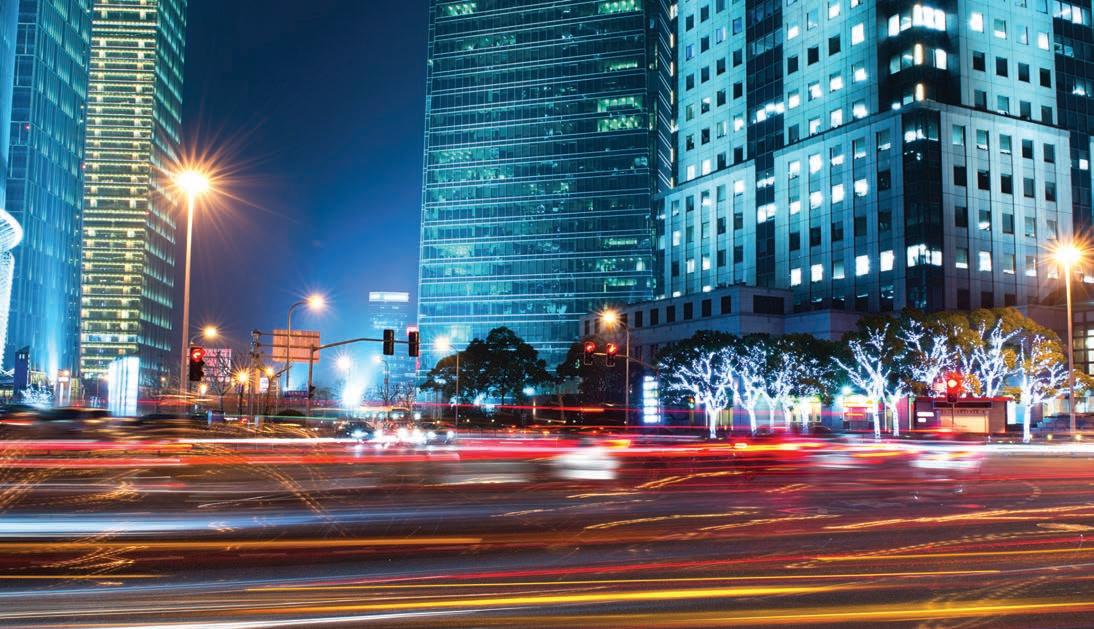