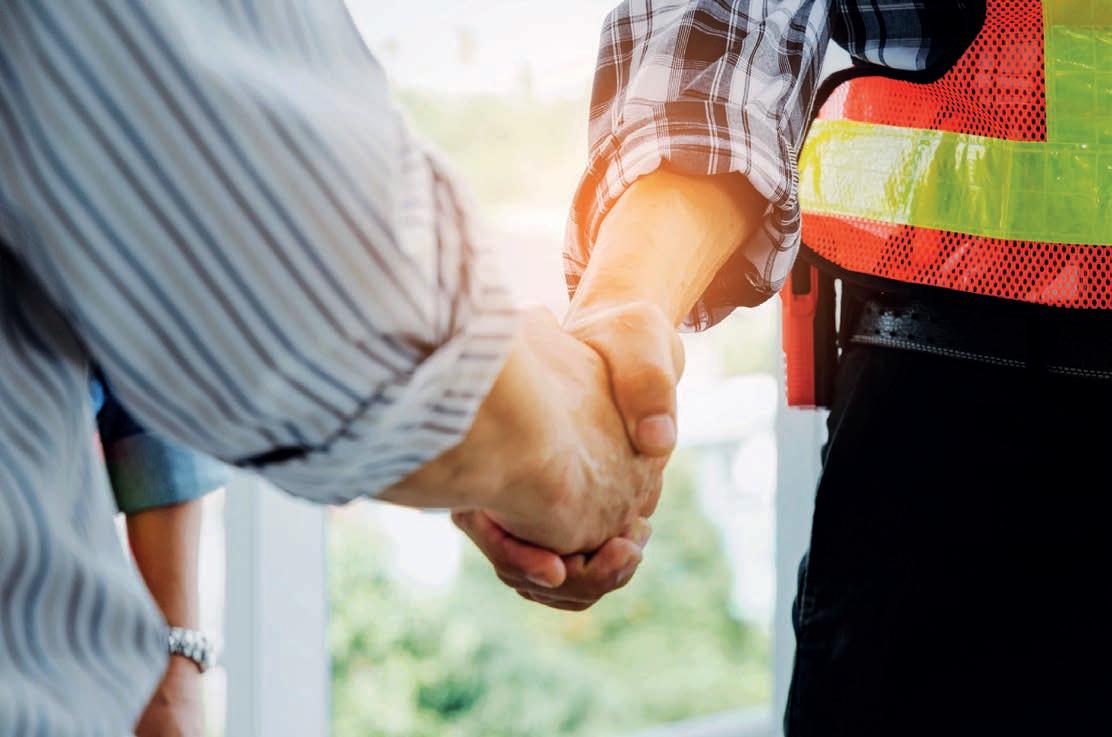
4 minute read
Breakdowns in project relationships
Relationships can make or break construction projects and conflict can have dire consequences. Dr. Gretchen Gagel looks at relationship breakdowns as one of the largest sources of waste in the construction industry.
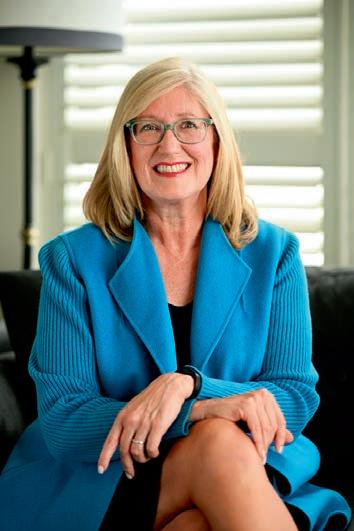
We’ve all been there on a construction project. At the start, everyone is getting along. We all agree on the goals and the metrics, and then something goes wrong. Then we all start collecting our own data to make sure we are not hung out to dry in claims court. We stop being transparent, we stop collaborating and maybe we even stop constructing.
If you’ve been reading my columns, you know I love to write about a topic that aligns with the theme of the edition. This edition’s theme, construction waste, offered up so many potential topics. One of the largest sources of waste in our industry is the waste associated with breakdowns in relationships on construction projects. The cost of conflict in our industry is enormous. I believe we all know how to fix it, and yet many times we do not.
Project examples
About a decade ago a project team called me in to help resolve what turned out to be a $20 million change order on a $40 million guaranteed maximum price (GMP) project. What had gone wrong? In this instance the contractor was too nice to a client that arguably shouldn’t have been executing their extremely unique project as a design/ build project. When the client wasn’t keeping up with the decisions necessary to keep the construction ahead of design, the contractor did not explicitly explain the cost of doing so until each small change and slow decision had resulted in a very big number. That is not helpful.
Or there is the situation I’ve come across many times where different people from different organisations on a project were hung out to dry on their last project, sworn that wasn’t going to happen on this one, and started covering their you-know-what from day one. These project cultures that lack trust and collaboration are stressful, and enormous amounts of time and energy are wasted.
A different story
Fortunately, I’ve seen many projects that reduce this waste in the following ways:
• Aligning project executives on values and behaviours – If the executives of a project are not aligned it is really difficult to align the rest of the team. As President of Continuum Advisory Group in the US, I had the good fortune to lead a team working with General Motors, Barton Malow and Gensler on a multi-billion-dollar program –three brownfield sites in the US and one in Mexico, sole-sourced (no tender) because speed to market was critical. We spent weeks up front ensuring that the seven executives from these three organisations were 100 per cent aligned on the values (lean, collaboration, win/win), identifying the behaviours that would or would not be tolerated, and discussing the metrics of success. We then met with the next 25 leaders of the projects, and then 60 more leaders of the projects, and gained their buy-in. We documented all of this, put it on big poster boards, and had all 60 people sign huge copies to be posted at each jobsite. We then indoctrinated every subcontractor so that they were in alignment as well. We had to make some tough personnel changes because not everyone got on board, and it sent a strong message. When a significant issue arose on one of the sites, it wasn’t swept under the rug, it was dealt with in a collaborative manner that focused upon solving the problem. We achieved outstanding results relative to safety, budget, schedule, and quality.
• Involving subcontractors – During my time at Continuum Advisory Group, we worked with Procter & Gamble to assist it in implementing lean practices on its projects throughout the world. I was able to see firsthand how involving subcontractors in the constructability of the project paid big dividends and reduced waste. On one project, the internal marketing client for P&G rejected the original 13-month schedule.
During a lean ‘pull planning’ session involving the client, the construction manager, the designers/engineers and all major subcontractors, it was the steel erection subcontractor that stepped up with incredible leadership that resulted in resequencing the project to deal with an equipment delay and achieving a ninemonth schedule. Our subcontractors have many valuable ideas, and we should be leveraging these people through strong relationships to reduce waste. Lean practices are focused entirely upon waste reduction, a good starting point as well. You can hear more about this example on the Greatness Podcast on Spotify, Episode 16.
• Training for collaboration – Most of us learned absolutely nothing during our formal or informal education about how to build relationships and collaborate. In the above example I asked Mike Staun, then Head of Construction at P&G, about how he was going to equip his people to better collaborate via lean practices. The thought had not crossed his mind. Investing in your people and giving them the skills they need to build strong relationships and collaboration can pay big dividends in reducing waste and improving project results.
There are a multitude of other ways to reduce the waste associated with breakdowns in relationships and trust in our industry. The first important step is to be mindful of this relationship-related waste and to put in place concrete strategies and tactics to reduce it.
Dr. Gretchen Gagel is Chair of Brinkman Construction (US), a member of the National Academy of Construction (US), a member of the Construction Industry Culture Taskforce (AUS), and an affiliate professor at the Australian National University and the University of Denver. As President/Managing Director of Greatness Consulting Pty Ltd she continues to advise organisations within the construction industry on optimising capital program delivery and developing talent. You can hear more from Gretchen on her Spotify podcast, “Greatness”.