5 minute read
Code word: automating bending
Code word: automating bending
Studio 54 has been working in the field of professional refrigeration since 1994, supplying a wide range of products that guarantee top efficiency and reliability. Upright cabinets, counters and tables, chill blasters, display units and walls, as well as minibars and hot display cabinets, meet every organizational need for food preparation, conservation and display for the Ho.Re.Ca and retail (supermarket) sectors. In addition to its standard product range, which is appreciated for the quality of the materials used and its typically Italian contemporary design, Studio 54 also produces highly customized and tailored products to meet its clients’ specific needs.
“The company was founded with limited financial resources,” says Marco Bruseghin, Chairman of the Studio 54 BoD, “but with great passion, that of myself and my partners. Ours is a success story: today Studio 54 has 52 employees, 18 of which are office workers and 34 production staff; we produce around 7000 parts a year, with a turnover of around 15 million EUR, and we work in a global market: around 40% of our turnover comes from Italy, 50% from the rest of Europe, and 10% from Russia, the Arab countries, the United States, Canada and Australia. Obviously we aim to expand and penetrate new markets.”
A modern workshop
Since 2015, having reached financial stability and set aside the necessary resources, to improve its efficiency, Studio 54 has progressively renewed its machinery fleet, investing in advanced production equipment. The green light for this authentic revolution was given by the optical fiber laser cutting machine, which guarantees huge benefits in machining stainless steel. And after carefully scouting the market, Studio 54 opted for a Salvagnini L5 high-dynamic fiber laser, with 3000x1500 work range and 2 kW source, connected to an ADLL automatic loading/unloading system and an MCL automatic sorting device, able to work unmanned. The results have been more than satisfactory: handling after cutting has become much simpler and safer to manage, and today the L5 system runs for around 20 hours a day.

“The possibility of nesting standard steel sheets means that we can combine different parts and make use of the scrap which would otherwise be thrown away” Bruseghin explains. “Obviously we couldn’t have done this with either the punching machine or the shear, but with the laser we have reduced scrap by over 15%.”
Having improved productivity with the laser system, the time had come to overcome the bottleneck in the bending department, which couldn’t keep up with the L5 production rate. For this reason, in 2017, Studio 54 purchased a P4-2116 panel bender: a versatile, flexible and highly productive solution offering automatic set-up in masked time and which, with its universal bending tools from 0.4 to 3.2 mm, requires no re-tooling. And which benefits from the effectiveness of the HPT for manually loading and unloading sheet metal and bent parts. “The panel bender guarantees excellent results, even on stainless steel,” Bruseghin continues. “Stainless steel is a complex material, and with a conventional press brake it can easily be scratched and even dented. Thanks to the controlled tool movements, bending with a panel bender avoids these imperfections: our quality has increased exponentially, not to mention the speed: with the panel bender we produce much more than we did previously with 3 conventional press brakes run by 3 operators. And also in terms of cost per part produced, we have recorded significant advantages.”
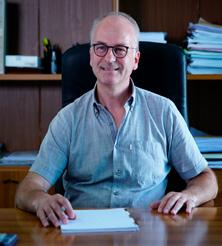
Marco Bruseghin, Chairman of the Studio 54 BoD
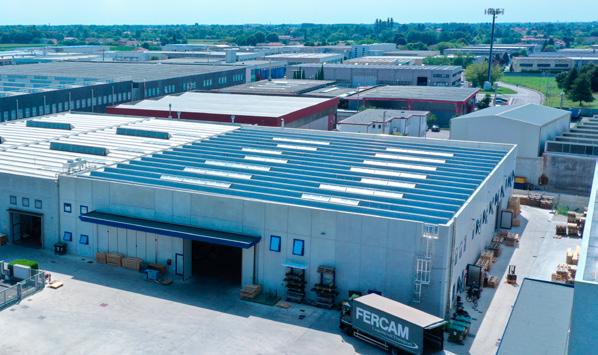
“There was just one more step to take to completely renew our technological fleet: investing in bending,” Bruseghin explains. “We immediately realized that the Salvagnini B3 press brake, in the version equipped with ATA, was the right machine for our production needs and our logic: this machine masks the set-up times, because when the operator calls up the code of a program, the machine sets up automatically with no risk of error.”
The press brake chosen by Studio 54 is a 3-metre B3, with 135 ton maximum bending force equipped with ATA, the automatic set-up device used to automatically change and adjust the upper and lower bending tool length, recovering production time and efficiency. Contributing significantly to reducing the variability that has always marked conventional bending, the ATA redefines the concept of time linked to the press brake: whatever the material, thickness and shape of the part being machined, each specific set-up has a certain, repeatable and foreseeable duration. The tool change is fast, the programming simple and user-friendly.
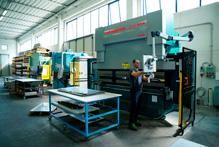
“With the ATA, we are able to avoid set-ups for both the upper and lower tools,” Bruseghin continues. “We work with very thin thicknesses, between 0.5 and 1.5 mm, all similar which are all managed with the same set of tools: we never change the punches and dies, we start bending straight away. Eliminating down times for tool changes and measurements, by automating all these activities with the ATA, offers huge advantages. In terms of output, I can say that in an 8-hour shift we have gained at least 40% in terms of productivity. Of course the press brake has to be programmed, but the operator doesn’t have to do it himself: the programmer who creates all the nests for the laser also creates the panel bender programs, and now the press brake programs too, so this clearly has advantages in terms of speed.”
An eye on the results
“We obtained very many results and advantages with these investments,” Bruseghin concludes. “Undoubtedly today we are much more versatile, we can produce any part practically in real time. We are much faster because the machinery is fast and integrated, perfectly suited for lean production and able to minimize set-ups and down times. And we have reduced our cost/piece ratio, thus gaining in competitiveness.”
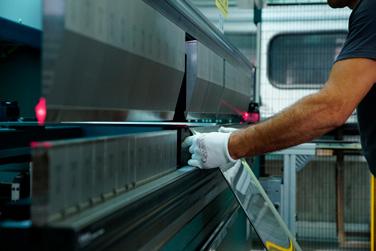