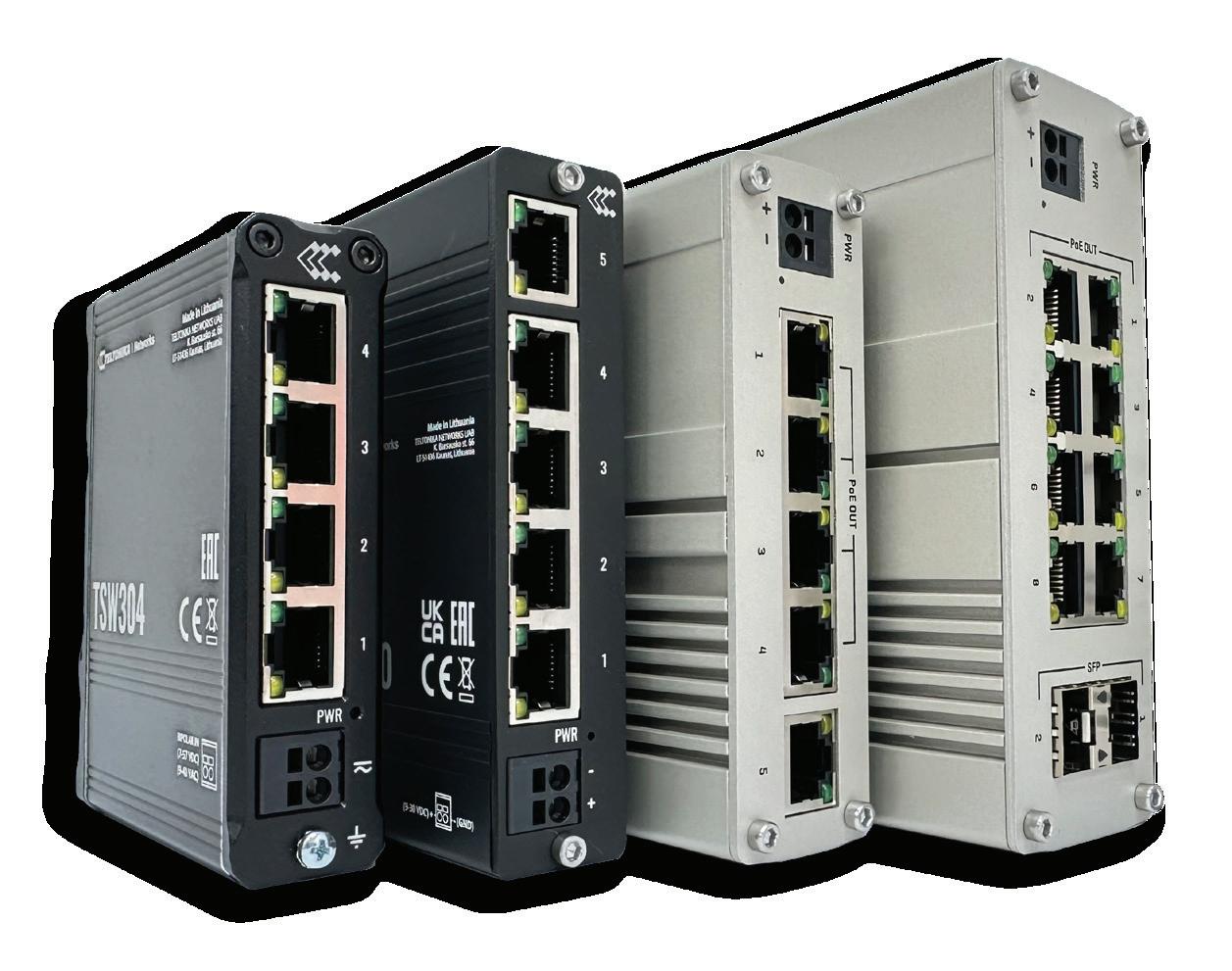
1 minute read
Control solution delivers benefits
When process system manufacturer BCH ran into a design challenge via the impending obsolescence of a key control component on its high-speed guillotine machine, it turned to Apex Dynamics. And according to BCH, the resulting performance improvements have been significant.
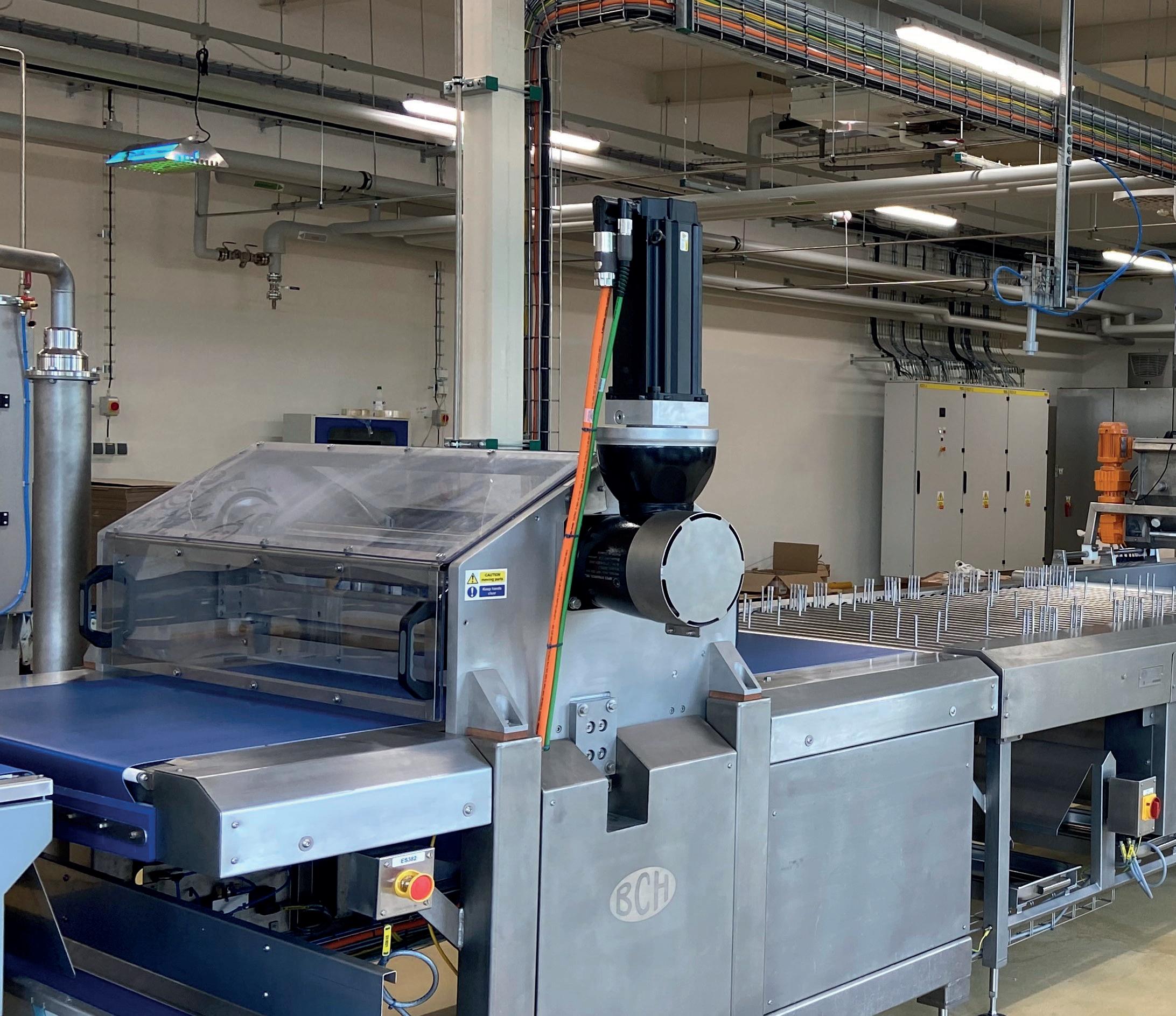
Advertisement
BCH was faced with the need to find a new servo gearbox solution on its high-speed guillotine machine which features as part of its extrusion systems and is also supplied as a stand-alone option for other industries including pet food. BCH took the opportunity to undertake a fundamental design review aimed at producing a guillotine with upgraded performance and enhanced versatility for smaller cutting at high line speed rates.
This pointed the company towards the Apex Dynamics range and in particular its KF180 high precision planetary gearbox series and in upgrading the machine design the changes have now been made to integrate the Apex KF180 gearbox. “We have been delighted with the results of the new design and the KF180 gearbox is proving itself to be a robust unit that can deal with the high speed long running service required,” explains BCH project manager Marc Oddy.
“In overall performance terms we have been able to increase our guillotine cutting speed to 600 rpm and also achieve better cutting accuracy on the length of 2 mm, compared to 5 mm previously.
“We chose the KF180, due to the two critical elements of good torque retention and continuous running capability and have not been disappointed at all with the actual performance of the unit,” continues Oddy. “Throughout this project we have had excellent technical and logistical support from Apex Dynamics and its local manager Malcolm Hillary has been very active in enabling us to test out the options we wanted to try.”
T 0121 227 5340
W www.apexdynauk.com