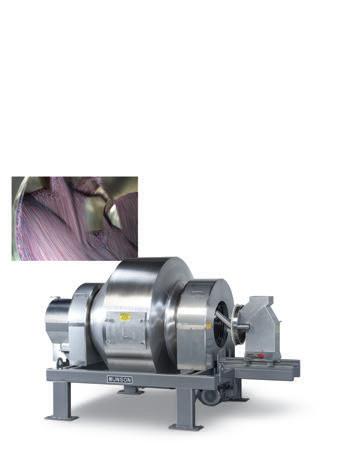
8 minute read
In the News
JOYCE FASSL | SENIOR EXECUTIVE EDITOR
Looking Back at 36 Years, but Looking Forward to What’s Next
I’ve had the tremendous fortune to work with some wonderful mentors and hundreds of phenomenal food manufacturing and publishing industry professionals over the past three decades. For that, I am truly grateful.
The year 1986 was a turning point in my life. It was the year I began my journey into the world of food and beverage manufacturing. I admit it was a little overwhelming at fi rst. My experience as a technical writer for a major software provider, followed by a position as an editor for IT/software publications, helped ease the transition to covering the food industry.
Thirty-six years later, I know I made the right decision, but I am soon ending my career in an industry I have grown to love. Although you may see a few articles from me later this year in ProFood World, this is my fi nal issue as a PMMI Media Group employee.
I want to take this opportunity to thank the people who stood beside me in both prosperous and challenging times. Without your support, I would not have been able to deliver the best content for our industry.
A million thanks to the food and beverage manufacturing professionals, advisory board members, industry suppliers, consultants, public relations professionals, and association partners, many of whom became friends and provided great story ideas, industry insights, and many laughs along the way.
I also had the fortune to work with some wonderful mentors and scores of phenomenal coworkers and publishing industry professionals over the past three and a half decades.
Over the next few months of this year, I plan to do some PART-TIME consulting work for PFW on our Manufacturing Innovation Awards and Sustainability Excellence Manufacturing Awards. Finally, I am looking forward to getting in some “me” time and continuing my passion for international travel and ballroom dancing.
Thank you for reading ProFood World and Joyce’s Voice.
Joyce Fassl has left the building.
EDITORIAL ADVISORY BOARD
CHRISTINE BENSE
CHIEF OPERATING OFFICER Ventura Coastal
GREG FLICKINGER
SENIOR VP, OPERATIONS Green Thumb Industries Inc.
JOHN HILKER
DIRECTOR OF MANUFACTURING Blommer Chocolate Company
VINCE NASTI
VP, OPERATIONS Nation Pizza & Foods
JIM PRUNESTI
VP, ENGINEERING Conagra Brands
LISA RATHBURN
VP, ENGINEERING T. Marzetti
MARK SHAYE
VP, ENGINEERING Ken’s Foods
TONY VANDENOEVER
DIRECTOR, SUPPLY CHAIN ENGINEERING PepsiCo
DIANE WOLF
FORMER VP OF ENGINEERING AND OPERATIONS Kraft Foods
BROOKE WYNN
SENIOR DIRECTOR OF SUSTAINABILITY Smithfi eld Foods
JOE ZEMBAS
DIRECTOR, ENGINEERING AND TECHNICAL SERVICES The J.M. Smucker Company
MUNSON® Ribbon, Paddle and Plow Blenders force agitators through stationary materials, imparting shear needed to reduce agglomerates and blend pastes and slurries. Choose from basic, low cost industrial units to state-of-the-art designs of 304/316 stainless with heating/cooling jackets, liquid spray additions, high-speed choppers/ intensifiers, and finishes to USDA Dairy and other standards. Extreme vessel rigidity allows tight agitatorto-vessel wall tolerances, resulting in a minimum “heel” of residual following discharge. Heavy- and extra-heavy-duty batch and continuous models in capacities from 1 to 1,150 cu ft (.03 to 32 m3). MUNSON® Vee-Cone Blenders feature smooth internal surfaces free of baffles, shafts and bearings, allowing unobstructed material flow, plus complete discharge through a gate valve for rapid cleaning or sanitizing of the easy-access interior. Uniform blends are typically achieved in 5 to 15 minutes with equal efficiency at fill volumes from 100% to 25% of capacity. Ideal for dry and granular materials, these blenders provide a tumbling action that is gentler than machines that force agitators through stationary material. Options include spray bars for liquid additions, Clean-In-Place (CIP) systems, abrasion-resistant steel construction, ASME-coded jackets and weigh batching accessories.
WORLD’S FASTEST BLENDING AND CLEAN UP
No other bulk solids mixer delivers this unique combination of benefits:
100% Uniform blending and/or liquid additions to 1 ppm in 2-1/2 minutes Total discharge with no segregation Ultra-gentle tumbling action (versus blades forced through batch) Ultra-low energy usage Equal efficiency from 100% to 15% of capacity Unlike other rotary mixers: – No internal shaft or seals contacting material – Every internal surface accessible – Significantly faster washdown – Seal changes 10x to 20x faster
Fast yet gentle 4-way mixing action: fold/tumble/cut/turn
ROTARY BATCH MIXER
Unlike Ribbon and Paddle Blenders with a single agitator shaft, MUNSON® Fluidized Bed Mixers feature two shafts with paddles that counter-rotate at higher speeds to fluidize material, achieving homogeneous blends in 10 seconds to 2 minutes. Low shear forces minimize friction with little or no degradation and insignificant heat generation of <0.6°F (1°C). Drop-bottom gates provide rapid discharge with no segregation and minimal residual. Ideal for short cycles and gentle handling of low- to medium-density powders and fragile flakes 50 lbs/ ft3 ( 800 kg/m3) with or without liquid additions. Capacities from 0.21 to 283 cu ft (6 L to 8 m3).
ROTARY LUMP BREAKERS REDUCE AGGLOMERATES, FRIABLE MATERIALS
Remove lumps and agglomerates from bulk foods, pharmaceuticals and chemicals, or break down glass and other friable materials. Dual rotors with three-point, single-piece breaking heads rotate with minimum clearance inside a curved, perforated bedscreen. On-size material exits through bedscreen apertures from 1/32 to 2-1/2 in. (0.8 to 63.5 mm) in diameter. The low profile design fits tight spaces between upstream and downstream process equipment, while side-removal bedscreens allow fast, in-place sanitizing. Square or rectangular inlets range from 15 to 48 in. (38 to 122 cm) in width—classifying screen apertures from 1/32 to 2-1/2 in. (0.8 to 63.5 mm) in diameter.
PIN MILLS REDUCE FRIABLE SOLIDS IN CONTROLLED SIZE RANGES
Also known as Centrifugal Impact Mills, these MUNSON® machines deliver coarse to fine grinding of friable powders, flakes and granules into controlled particle sizes at high rates per HP/kW. High-speed rotation of the inner disc creates centrifugal force that accelerates bulk material entering the central inlet of the opposing stationary disc. As material travels from the center to the periphery of the discs at high speed, it passes through a path of five intermeshing rows of rotating and stationary pins, with the desired tight particle size distribution obtained by controlling the rotor speed.
IN THE NEWS
Coca-Cola Targets Sustainability From Every Angle
AARON HAND | EDITOR-IN-CHIEF
Perdue Foods Names Kevin McAdams as President
Kevin McAdams has been appointed as chief operating o cer of Perdue Farms, as well as president of Perdue Foods. Most recently, McAdams served as Jack Links’ president, North America.
COCA-COLA IS AN ICONIC BRAND—a well-recognized taste in a well-recognized bottle. But when The Coca-Cola Co. aims to make a change to the norms of operation, it’s thinking not only about its fl agship beverage and all its variations, but a full range of waters, sparkling beverages, hydration and sports drinks, dairy and plant-based beverages, juices, co ees, teas…
“We have to take all of that into account when building a sustainability plan,” said Cloeann Durham, vice president of quality, safety, and environment for Coca-Cola’s North American Operating Unit. She was speaking to the audience at ISBT’s BevTech meeting in Frisco, Texas. Though CocaCola’s brands are positioned to grow, sustainability is equally important, she noted. “Seeing volume growth is great. But seeing volume growth without sustainability—it can outrun you really fast.”
The sustainability priorities themselves make up no short list either: helping solve the global packaging waste crisis, reducing carbon footprint through science-based targets while building resilience for climate events now and in the future, increasing water security for operations, protecting communities and nature, reducing added sugar across the portfolio while providing consumers with more choices and smaller packaging options, growing a more sustainable supply chain, advancing women and diversity, and supporting human rights.
Coca-Cola has passed several of its environmental, social, and governance (ESG) goals and is working toward plans that include 2025 packaging goals, a 2030 climate goal, a new 2030 water strategy, and a streamlined global beverage portfolio. In all of this, having support from the top has been vital. “We have the commitment at the highest level in our company,” Durham says, pointing to James Quincey, chairman and CEO.
Transparency to consumers
Transparency—publicly reported sustainability goals as well as accountability on those results—has been instrumental in driving Coca-Cola to continuously improve, Durham noted. The beverage industry has shifted considerably over the years. It’s no longer enough to put together a feel-good TV ad to convince consumers. “Data is all you really have to tell your story,” she says of today’s expectations. “Science-based targeting is o ering a di erent level of transparency.”
Coca-Cola’s sustainable business priorities cross a broad spectrum, but Durham dove a bit deeper into several areas. A signifi cant e ort is its World Without Waste initiative, which looks primarily at packaging and how to drive a circular economy to help reduce the carbon footprint of that package.
McCormick to Reduce CO2 Emissions by 86.8 Metric Tons
McCormick is partnering with Berry Global to produce 100% post-consumer recycled plastic bottles for its new assorted and neon food color product lines. The move will reduce associated CO2 emissions by 59% compared with the same bottles made from virgin material.
Mars CEO Grant F. Reid Stepping Down
Poul Weihrauch, global president at Mars Petcare, will take on the role of Mars CEO at the end of September.
Post Holdings to Expand Facility
Post Consumer Brands is investing up to $110 million to expand the cereal production capacity at its Sparks, Nev., facility.
Conagra Brands Opens New Plant
The $300 million, 245,000-sq-ft Waseca, Minn., facility processes vegetables, bought from nearby growers who use programs to help fi ght climate change, to support the company’s frozen meals business and Birds Eye brand.