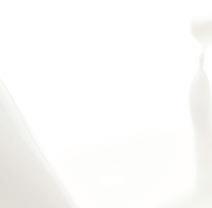
5 minute read
PACK EXPO International Returns to Chicago
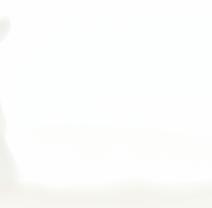
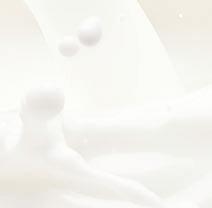
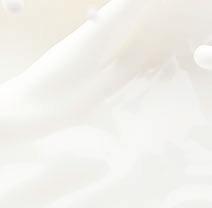

s A CM Connect wireless vibration monitor is attached to an
Alfa Laval DuraCirc circumferential piston pump, helping operators make informed maintenance decisions.
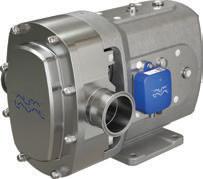
PHOTO COURTESY OF ALFA LAVAL The redesign repositions the Gore Vent for greater durability and less risk of water ingress. The more compact design features burst seat cleaning functionality that significantly reduces water and cleaning agent consumption during clean in process (CIP). A QR code provides easy online access for maintenance sta to support materials and direct support. The ThinkTop fits on any Alfa Laval valve, making retrofits easier.
The war in Ukraine, high inflation, and climate concerns are having an economic impact on processors, changing priorities for product specification in both Europe and the U.S. “We’ve seen a higher level of focus on automation to increase e ciency standards to compensate for these e ects,” says Russell Jones, commercial sales manager for pumps at Alfa Laval.
Better cleaning, fewer risks
“Manufacturers are doing everything possible to avoid product recalls or losses,” says Tom Zuckett, Americas Northeast regional sales manager for PSG, a Dover company. “That’s why we’ve designed our Wilden Saniflo Hygienic Series air-operated double-diaphragm (AODD) pumps to be highly cleanable and drainable.”
A free-draining flow path enables CIP capability. “Additionally, when equipped with Wilden’s PureFuse integral pistol diaphragm technology, the common bacteria trap in standard diaphragms is eliminated,” Zuckett says. “Pure-Fuse diaphragms are also much easier to clean between product changeovers and have a much longer service life. Because the diaphragm doesn’t hold back fluids, bacteria traps are eliminated.”
The AODD pumps also help in production environments commonly manned by new operators, Zuckett points out. “These operators have fewer skills, so air-operated systems are easier for them; they’re more forgiving,” he says.
Energy e ciency is also a factor for the Wilden Saniflo Hygienic Series pumps. An innovative air distribution system reduces compressed air costs by up to 60%, Zuckett notes.
While centrifugal pumps are the most widely used in the food and beverage industry, Zuckett says, rotary style positive displacement pumps come in second. “Their drawback is that they need to be taken apart to be cleaned,” he says. “That’s one reason why twin-screw pumps, which can be cleaned in place, are increasingly popular. Since motor speed can be controlled with a variable-frequency drive, processors don’t need to buy a second pump to produce the higher speeds required for the cleaning process.”
AODD pumps are earning a growing share of the marketplace. This style of pump o ers gentle handling and can handle large solids, such as found in the making of wine, yogurt, or jams, or in the viscous syrups used for soft drinks and energy drinks.
Helping hand for labor
Labor shortages continue to trouble every industry sector, and this factors heavily in cleaning and maintenance of pumps, notes Chris Stevens, CEO of Unibloc Hygienic Technologies. “Sanitation and maintenance demand a significant amount of time and attention,” he explains. “Within a meat and poultry processing plant, for example, an entire eight-hour shift is typically devoted to cleaning and sanitation. During this shift, pumps must be disassembled, cleaned and then reassembled, with the goal of accomplishing this process as quickly, safely, and e ciently as possible.”
This complex cleaning and maintenance cycle requires specialized tools and causes significant wear and tear on the pump, causing up to 95% of all pump damage. Parts can be lost or pumps damaged due to incorrect reassembly, which in turn results in the need for more replacement parts and extra maintenance.
“This makes it a priority for the pump and valve industry to consider both pump maintenance and performance to be critical design factors,” Stevens says. “A pump with fewer parts makes the entire process of disassembly, cleaning, and reassembly easier and quicker without ignoring performance and while adhering to the highest sanitation standards.”
He points to Unibloc’s Flotronic “One Nut” pump as one example. “While a typical air operated double diaphragm pump will take two to three hours to disassemble, clean, and put back together, an operator can complete the same process on a one-nut pump, which has one bolt and one washer, in 15 minutes or less,” he says. “Reassembly is a simple process and requires no special tools. This means fewer parts to potentially
s
Without tools, cleaning crews can quickly open the Unibloc clean-out-ofplace (COP) pump cover and swing it aside.
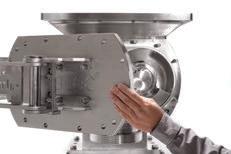
PHOTO COURTESY OF UNIBLOC
lose or misplace, fewer challenges for the labor force, and a much swifter cleaning process without sacrificing performance or sanitation.”
Other Unibloc pumps designed for ease of cleaning include the compact Flotronic Slimline, which is e ective in the transfer of highly viscous products such as dairy and mayonnaise. It features a crevice-free design with no internal welding to help facilitate thorough cleaning. A Texas-based salsa manufacturer, Stevens notes, found that a Slimline stainless-steel pump was able to save them an hour of time in the daily sanitation process compared to an AODD pump.
More sanitary pumps
Verder Hygienic Pumps makes a wide range of pump types, including high-e ciency centrifugal, twin screw, and peristaltic pumps. “Many fruit and vegetable processors are switching to sanitary style pumps in applications where previously a less hygienic pump or conveyor was always used,” explains Michael O’Grady, hygienic sales manager.
Though pumps might be a wise choice for these processors due to the high maintenance costs of conveyors, some were choosing ine cient pumps, O’Grady notes. In some cases, pumps were made of cast iron, which is not compatible with some of the acids released in the cutting process. Even pet food processors are switching to sanitary pumps from the less expensive industrial pumps they used in the past, he adds.
Manufacturers continue to make more pumps using the food-grade materials necessary for food and beverage applications. Verder’s twin screw Packo Fruit & Vegetable pumps, which are used for processing large particulates such as fruits,