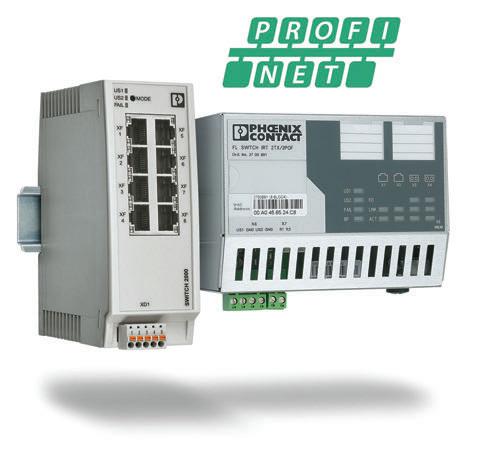
1 minute read
MAKING SENSE OF INDUSTRIAL NETWORKS
facilitates such things as diagnostics, configuration, redundancy, vertical integration, functional safety, and energy management. “Many of these capabilities in Profibus are baked into Profinet,” says Bowne.
The big di erence between the two, of course, lies in the physical layer. Whereas Profibus relies on RS-485, Profinet uses Ethernet. “This opens a world of possibilities,” observes Bowne. “Ethernet speeds are orders of magnitude greater.” Profinet’s telegram size is also larger, and Ethernet’s full-duplex nature allows Profinet to send and receive data simultaneously.
Besides handling larger amounts of bi-directional data, the Ethernet-based backbone also permits open communications. “Other protocols—such as OPC UA or HTTP—can coexist on a Profinet network,” says Bowne, indicating that “the network is now an infrastructure.”
These attributes have enabled Profinet to grow beyond its historic uses in industrial automation networking.
“The very first iteration of Profinet was developed for machine-to-machine integration,” notes Bowne. At the time, it was believed that “serial-based fieldbuses like Profibus would be used at the field level and that horizontal integration at the controller level would be achieved via Ethernet-based Profinet.”
Almost immediately, however, the automation industry found that Profinet would also work at the field level. Consequently, Profinet has progressed over the two decades since to include features for motion control, process automation, functional safety, and energy management.
Another benefit of Profinet is its determinism, which is not a native characteristic of Ethernet. Profinet can bring determinism to the factory floor by skipping the TCP/UDP and IP layers of the ISO/OSI Model and going directly from the data link layer (Layer 2) to the application layer (Layer 7) of the OSI model. This means that applications requiring synchronized, high-speed motion can use Profinet IRT (isochronous real-time) to provide sub-millisecond cycle times. is an intrinsically safe version of IEEE
Bowne points out that many of the mechanisms in Profinet IRT are also found in the Time-Sensitive Networking (TSN) standard being developed by the Institute of Electrical and Electronics Engineers (IEEE). “From this perspective, Profinet is ready for TSN,” he says. “It’s already written into our spec.” He expects the first Profinet over TSN devices to be released in a year or two.
Further Ethernet developments promise to extend the reach of Profinet. One of these is Ethernet-APL (advanced physical layer), a technology that brings Ethernet to field devices in hazardous areas.


