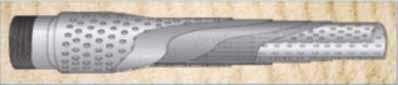
13 minute read
Gravel Pack Completions Successful History In Mediterranean Sea Gas Fields, Egypt
By
W.Gabr, S. Zayed, Belayim Petroleum Co. (PETROBEL)
Advertisement
Abstract
Mediterranean Sea offshore concessions are located about 30 – 60 km off the Northern Egyptian coast. More than 25 gas prospects have been identified. These accumulations are often characterized by several hydraulically independent reservoirs. Three gas-condensate fields were discovered by three exploratory wells in 1982, 1983 & 1995, finding several gas bearing intervals inside Wakar and Abu Madi Formations (Miocene age). Following, further 9 gas fields have been discovered identifying several lean gas bearing intervals inside Kafr El Sheikh Formation (Plioceneage). In 2002, a lot of wells started to produce sand causing severe problems to the surface facilities and reducing the concessions production potential. In 2003, a sand control campaign was undertaken in Mediterranean Gas fields to recover the full fields’ capacity using both Gravel Pack Completions (first time in Egypt in well PFM–7) and Expandable Sand Screen Completions (first time in Egypt in well PFM–8). By time, Expandable Sand Screen Completions proved its failure in many cases and are minimized to very limited cases. The aim of this poster is to highlight the advantage of Gravel Pack Completion technique used in North Port Said, Temsah & Baltim concessions over Expandable Sand Screen Completion technique focusing on successful case histories and its positive impact on production and reservoir potential.
INTRODUCTION
Most of the gas wells are producing from sandstone formations deposited in marine or delta environments. In the case of older and deep formations, sand grains are cemented by limestone or silica minerals, and in general the consolidation process is at a mature stage. More recent deposits, (starting approximately from the Miocene) are partially consolidated and their degree of cementation is non-existent or extremely low. In such reservoir, the sand production risk is extremely high. In most cases, sand production leads to serious operative problems affecting production and safety. This factor is one of the most important constraints in developing reservoirs in weak sandstone formations and, consequently, one of the main factors that determine the profitability of the investments. Before 2003, Petrobel suffered from sand production resulting in severe damage to the surface and topside facilities with very dangerous gas leakage (risk of fire occurrence) and reduction of the production potential below the contractual DCQ. To overcome the sand production problem, an action plan was defined as follows: Ó Perform production test using wellhead desander unit (WDU) for the existing flowing wells to define the optimum sand free rate. Ó Completion of the new wells and workover of the existing wells with sand control technique. This paper is presented to highlight Petrobel sand control experience using both Gravel Pack and Expandable Sand Screen Completions in the operated Mediterranean Sea gas fields and their impact on the production potential in addition to the advantage of Gravel Pack Completion techniques over Expandable Sand Screen Completions.
SAND PRODUCTION DEFINITION
Sand production can be defined as follows: The failure of weak sandstone causes the detach of the grains which are transported inside the well by the produced fluids. The physical process can be described by a two stages
mechanism (Fig–1): 1) The onset. The first stage is a process of failure of the reservoir rock in the vicinity of the wellbore walls. As a result, the original texture is destroyed and the grains are entirely loosened. Basically, there are two factors which trigger off sand production: Ó Rock strength. Ó The intensity of the forces applied to the formation around the well. In the majority of cases, the risk of triggering off sand production increases during the reservoir production stage, due to the fact that the effective pressures (i.e. those which act on the rock skeleton alone) increase in time. As a result, in many cases the strength of the formation is sufficient to withstand the forces applied at the production start-up; however, sand production is set off during reservoir production when the pore pressure decreases (and the effective pressure increases) by a certain entity. 2) Erosion and transport. The second stage starts after the rock matrix has been destroyed: the sand grains are eroded and transported inside the well by the fluids produced. The amount of sand produced and the way it is transported inside the well depend on the following factors: Ó Fluid velocity. Ó Fluid viscosity. Ó The effects of relative permeability in the case of twophase fluid production. Ó The size of the sand grains.
EXPANDABLE SCREEN TECHNOLOGY
Expandable screen technology as shown in Fig–2 presents an interesting alternative to traditional sand control techniques in both cased and open holes. The concept of the technology is to deploy a small OD screen to the productive interval of the well. The screen is then expanded against the casing or borehole wall by forcing a tapered cone through the ID of the screen. In the cased hole, the expanded screen covers the perforation tunnels to prevent sand production. In the open hole, the screen “re-stresses” the borehole walls to stabilize the well and prevent sand production. The ID through the expanded screen is large to allow deployment of conventional tools and equipment for future remedial operations. The current expandable screen design consists of overlapping layers of woven metal cloth sandwiched between and two slotted steel tubes for protection. The residual opening size of the slots in the steel tubes following expansion is a function of the degree of expansion; thus, the slots are not suitable or intended for sand control. The weave provides the sand control during well production and is designed to maintain a fixed opening following expansion of the screen. The openings in the weave are sized relative to the formation sand. Benefits of sand control using expandable screen technology include: Ó Eliminates pumping operations required with conventional gravel pack completions. Ó Small initial OD to allow deployment through restrictions common in remedial well operations. Ó Large ID following expansion to maximize future remedial operations. Ó Stabilizes borehole in open hole applications to stop formation sand from moving to minimize screen erosion/ plugging concerns. Ó Eliminates open annulus associated with conventional standalone screen to allow more reliable production log interpretation, stimulation treatments and water/gas shutoff operations.
GRAVEL PACKING TECHNOLOGY
Gravel pack completion is the most used option for sand control, blocking the sand grain movement with a screen in front of the productive zone and placing gravel in the annular space between the screen and the casing (ICGP) or the sand face (OHGP). On Petrosaid fields, depending on the reservoir characteristics, various completion techniques were experienced. ICGP is the traditional and most adopted sand control method because of it is the simplest one and because of its wide range of applicability. It consists in perforating the casing in front of the formation, running the screen and filling with gravel the annular space and the perforations tunnels. As successful ICGP require a deep penetration of the perforations to over passing the wellbore damage zone and a tight packing of the annular space and perforation tunnels. This technique can be used practically everywhere sand control is needed but, with the income of other sand control methods, it is mainly selected when: Ó Good permeability of the formation. Ó Multiple zone completion is required. Ó Bore hole instability was expected during gravel placement. Ó Formation grain size reasonably large and uniform. Ó All productive layers could be penetrated by the perforations (no thin sand-shale layer are present). Ó Water presence that exclude formation fracturing. Ó Water breakthrough expected and water shut off is forecasted.
Petrobel applied this completion technique in Darfeel (7 wells, 9 completion) and Karous (2 wells) fields. With the aim to define the Flow Efficiency (F.E.) on these completions, Darfeel wells were tested before and after completion. After gravel packing, the wells were stimulated with HCl to remove the possible damage induced during the drilling and completion operation. Encouraging results were obtained with good completion efficiency. In fact, even if this is not the most aggressive technique, it is demonstrated by the productivity obtained for said wells, that the calculated average F.E. after the completion is 75%, ranging from a minimum of 54% to a maximum of 90%. Moreover, thanks to the right sizing and packing of the chosen gravel, 6 year after the start-up, the wells show the same efficiency over the time. High Rate water pack technique uses water as a carrier fluid for the gravel; it is the most popular alternative to gravel packing methods using polymers which can reduce the natural formation permeability. The completion method allows very tight annular packs. On high permeability zones, water packing has the disadvantage to have large completion fluid losses and the high leakoff rate, which can cause bridging in the screencasing annulus with consequent premature screen out. Trying to overcome the above mentioned problems, targeting high completion efficiency in a high permeable formation (k>500 mD) and minimizing the risk of opening fracture into the lower water bearing level, in well Nouras-3S HRWP was designed and performed at low rate to enhance gravel placement into the perforations. The successful of the HRWP job has been demonstrated by the positive performance of the well producing with F.E.=80% and gas rate of 13 MMScf/d. Nouras-1 is the second HRWP experience. The operation has been performed on 6 m sand level. Also in this case good productivity was achieved proved by F.E.=88% and high sand free gas rate, the well is producing with a rate of 56.5 MMScf/d. OHGP usually has a higher potential than ICGP, mostly due to more flow entry area (increased reservoir contact) and less formation damage.
OHGP is mainly preferred in:
Ó Reservoirs with clean sandstone formation without shale beds. Ó Multilayered reservoir to provide maximum exposure of all productive layers. Ó Presence of fine formation grains where high pressure drop in perforation tunnels are expected due to gravel plugging by fines. Ó Reservoirs where no water shut off are forecasted. Three successful OHGP were performed in the Petrosaid concession, two in Port Fouad field and the third one in Nouras field. In order to guarantee the maximum formation potential, in all the performed completion it was always applied the same procedure: Ó The casing is set above the target zone. Ó Targeted formation has been drilled and enlarged with a Drill In Fluid (sized salt or calcium carbonate drilling fluid). The wellbore enlargement has the double advantage to eliminate any drilling damage around the wellbore and to increase the inflow area. Ó The gravel pack screen is hung as an uncemented liner and the space between the screen and the formation face is packed with properly sized gravel. The procedure demonstrates its validity with very quick clean-up and high Flow Efficiency obtained in the wells where applied. In well PFM-07, the 7» liner has been set at the depth 3260 m MD, the 6» hole was drilled and undereamed to 12 ¼” from 3260.4 mMD to 3280.6 mMD, then the OHGP was performed. At the start-up (June, 2003), the well showed soon its great potentiality and, after a quick clean-up period, it was stabilized to a gas rate of 78 MMScf/d (3,500 bopd of associated condensate), limited by the erosion velocity on the 4 1 / 2” production tubing. In well PFMSW-03, the 7» liner has been set at the depth 3819.5 m MD. As in the previous well, the OHGP has been performed drilling and underreaming the 6» hole to 12 ¼” from 3920 m MD to 3838.5 m MD. At the start-up the well has been opened at 53 MMScf/d and gradually increased to 81 MMScf/d (3,600 bopd of associated condensate). In well Nouras-2, the well has been completed in a shallow formation with a low initial static pressure. Consequently high F.E. is mandatory to have good productivity potential. The use of DIF in the drilling and enlargement operation reduced the risk of wellbore collapse in the shallow and unconsolidated formation. The 9 5 / 8» casing was set at 756 mMD, the 8 1 / 2» was drilled and enlarged to 15» hole from 756 mMD to 781 mMD, then OHGP was performed. As for the other OHGP, great performance was achieved producing with F.E.=96% and rate of about 35 MMScf/d. In the all three experienced cases, great completion potential was obtained with an estimated average F.E. of 95%.
PRODUCTION & RESERVOIR POTENTIAL
It is worth mentioning that in the last 14 years, Petrobel completed 26 gas wells with Expandable Sand Screen (15 of them “i.e. more than 50%” are closed due to screen failures), 64 gas wells with Inside Casing Gravel Pack (33 of them are
closed due to water flooding, No screen failures reported) and 18 gas wells with Open Hole Gravel Pack (9 of them are closed due to water flooding, No screen failures reported). In the last 3 years and due to more advantages of Gravel Pack all over the other completion techniques, it is considered the first option in our company now while utilizing Expandable Sand Screen technique was decreased to the minimum. Petrobel succeeded to maximize production by applying that technology and increased the production by more than 1.4 Bscf/d.
CONCLUSIONS
Great results were obtained with the OHGP soon with the first application. In the two Port Fouad cases, wells are now producing with rate higher than 78 MMScf/d and they are limited by the erosion velocity on the completion tubing (4 ½”). We can summarize the conclusions in the following: Ó OHGP completion, using a proper DIF for both drilling the pilot hole and underreaming, Ó produce good results in terms of hole stability and preserving reservoir from damage. Ó Practically, it is a fair balance between simplicity and high flow efficiency. Ó HRWP demonstrate improvement in pack factor and well productivity. Ó integration of the relevant data in designing the best sand control solution is essential to ensure proper results. Ó More than 50 % failures in cases which ESS technique was applied. Ó Advantage of GP Completion techniques over ESS
Completions. Hence, it is considered the first option in our company now.
ACKNOWLEDGEMENTS
Authors gratefully thank and acknowledge the support received from the management of PETROBEL in the preparation of this paper. Authors also wish to thank colleagues from the Reservoir Engineering Sector and Baker Oil Tools for helping in the preparation of this paper and many others.
REFERENCES
1. Agip E&P Division, Corporate E&P Laboratories «Sand
Production Prediction». 2. Sand Production Prediction study, Feb.2002 Agip E&P Divition. 3. «Reservoir Description and Simulation of the Abu Madi
Paleovalley», ENI, July 2000. 4. «Baker Oil Tools Material», Baker Oil Tools, 2016. 5. «PETROBEL Data Base», PETROBEL, 2016.
APPENDIX
DCQ Daily Contract Quantity WDU Wellhead Desander Unit ICGP OD Inside Casing Gravel Pack Outside Diameter
ID Inside Diameter
OHGP
Open Hole Grave Pack DIF Drill In Fluid ESS Expandable Sand Screen HRWP High Rate Water Pack DIF Drill In Fluid
Fig 1: The two stages of sand production, observed during a compression test on a sandstone plug with a cavity: 1) the failure of the rock around the cavity because of shear bands occurrence; 2) erosion of the detached grains with the fluid flow.
Fig 2: The Express Screen

Instrumentation Tube Fittings & Valves
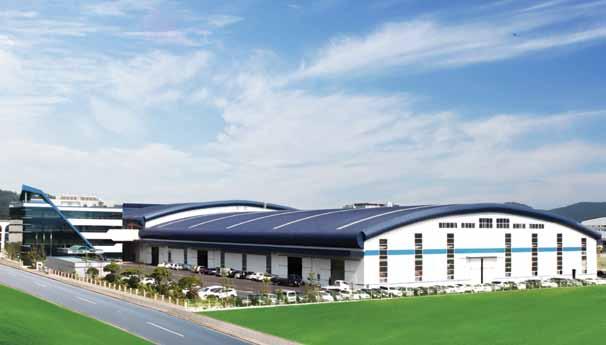
Al-Andalos For Engineering Works, Trading & Contracting Co. 9ARfaah St., Manshiet El-Bakry, Heliopolis, Cairo, Egypt - P.O.: 11331 Tel : +202 2257 7477 Fax : +202 2257 6555 Mob. : +20 10 6603 3398 E-mail: dklokegypt@andalos-group.com Website: www.dklok.com