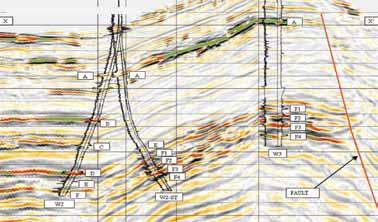
19 minute read
Production Technology Challenges in Deepwater Subsea Tie-Back Developments
By
E.A. Ageh, SPE, O.J. Uzoh, SPE, and I. Ituah, Shell Nigeria E&P
Advertisement
Abstract
The era of easy oil is coming to an end, a lot of the major reserve finds these days are located in very challenging operating environments such as deep and ultra-deep water. Subsea tie-back systems over the years have evolved as a solution to the challenge of harnessing these reserves in a cost effective manner. The challenges for subsea type developments are not only limited to the cost of drilling and infrastructure or the complexity of the subsea layouts but also the technology of assessing and producing the volumes to surface poses a great challenge. Production technology challenges include multi-phase fluid flow, completion design, flow assurance (hydrate mitigation & management), well intervention and long term well monitoring. Of particular concern are the issues of waterflood management, intelligent completion & production systems which are core to achieving increased ultimate reservoir recovery and production volumes required for cost effectiveness. This article highlights the major production technology challenges articulated for a typical long subsea tie-back development and discusses how these could be managed.
Introduction
For the sake of this review we considered a deepwater field located in the Gulf of Guinea. The field is comprised of a combination of stratigraphically and structurally trapped hydrocarbon accumulations in middle miocene turbidite reservoirs. Six oil-bearing reservoirs (A, B, C, D, E & F) have been targeted for development as shown in Figure 1, the reservoir bodies are stacked with distinct NNE to SSW orientation with the exception of “A” reservoir which has an east to west orientation. The proposed development concept is a tieback to a host facility (an FPSO) that is about 18 kilometers away and is the most optimal concept for economic development of the opportunity. The development philosophy is to fill ullage on the FPSO as host production declines and also to utilize existing infrastructure as much as possible. The expected full field development will consist of 32 subsea wells (17 production and 15 water injection) including dual zones completions (Smart wells).
Background
The base case development scheme includes: (Figure 2) Ó - Drilling of 25 wells in the first phase including 13 production wells and 12 injection wells. Ó - Connection of the production wells to four production manifolds and the injection wells to three injection manifolds. Each of manifolds has slots for six wells Ó - Laying of 10 in. subsea pipe-in-pipe single loop production flowline and injection flowline connecting the field to the host. Ó - Gaslift lines for riser-base gaslift Ó - Installation of risers at the starboard side of the FPSO to ensure connection of the subsea lines to topsides Ó - System of umbilicals and termination assemblies for controls and chemical injection.
Technical Challenges
One of the key technical challenge is how to design a robust production system to economically transport the production fluids from subsea wells to topsides and to be able to sufficiently mitigate all the flow assurance and operational risks. Flow assurance risks are crucial due to existing high pressures and low temperatures. The subsea system design and well completion design for this tie-back field was greatly influenced by flow assurance
mitigation strategies.mitigation strategies. Another major technical challenge for the field development Another major technical challenge for the field development is shallow hazard arising from small pockets of hydrocarbon is shallow hazard arising from small pockets of hydrocarbon accumulations that can be encountered in the drilling accumulations that can be encountered in the drilling of development wells. This is a major consideration in of development wells. This is a major consideration in the placement of drill center locations and casing design the placement of drill center locations and casing design schemes.schemes. Geotechnical challenges also exist, it is expected that planned Geotechnical challenges also exist, it is expected that planned surveys would provide sufficient data for risk mitigation. surveys would provide sufficient data for risk mitigation. On the subsurface, all the reservoirs exhibit structural and On the subsurface, all the reservoirs exhibit structural and stratigraphic complexities including faults, stratigraphic stratigraphic complexities including faults, stratigraphic barriers, etc. which have impact on recoveries. The major barriers, etc. which have impact on recoveries. The major challenge here is in the optimal placement of drainage zones challenge here is in the optimal placement of drainage zones to sufficiently recover economic volumes. to sufficiently recover economic volumes. Overall, key technology driver for any subsea project must Overall, key technology driver for any subsea project must center on the desire to produce the field in a most cost center on the desire to produce the field in a most cost effective and efficient manner. As most of today›s subsea effective and efficient manner. As most of today›s subsea developments are in frontier deep and ultra-deepwater developments are in frontier deep and ultra-deepwater regions, and at step-out distances that makes the use of regions, and at step-out distances that makes the use of existing infrastructure demanding, cost and feasibility are existing infrastructure demanding, cost and feasibility are two important challenges being faced by operators. two important challenges being faced by operators.
Production Technology Solutions Production Technology Solutions Flow AssuranceFlow Assurance
The buildup of wax, scale, hydrate etc. in subsea flowlines, The buildup of wax, scale, hydrate etc. in subsea flowlines, wellheads and risers is a special problem for subsea wellheads and risers is a special problem for subsea production. For the subject field, given the temperature production. For the subject field, given the temperature regime of the wells and expected high arrival temperatures, regime of the wells and expected high arrival temperatures, the risk of wax deposition is very low as flow streams would the risk of wax deposition is very low as flow streams would be outside the wax deposition envelope. Scale deposition be outside the wax deposition envelope. Scale deposition risk in the wellbore, subsea hardware and flowlines is risk in the wellbore, subsea hardware and flowlines is conventionally managed by downhole scale inhibitor conventionally managed by downhole scale inhibitor injection. Managing scaling risks in the wellbore and injection. Managing scaling risks in the wellbore and perforations for subsea wells can have significant bearing perforations for subsea wells can have significant bearing on project /operation costs hence the management strategies on project /operation costs hence the management strategies have to be carefully considered depending on the anticipated have to be carefully considered depending on the anticipated severity and scaling tendencies of the reservoir fluids. For severity and scaling tendencies of the reservoir fluids. For our subject field periodic scale squeeze operations have been our subject field periodic scale squeeze operations have been selected as an optimal mitigation strategy. The main flow selected as an optimal mitigation strategy. The main flow assurance challenge is the prevention of hydrate formation assurance challenge is the prevention of hydrate formation in the wellbore, at the wellhead, production flowlines and in the wellbore, at the wellhead, production flowlines and risers. Insulation of the flowlines combined with hydrate risers. Insulation of the flowlines combined with hydrate inhibitor injection (Figure 4) at start-up and shutdown will inhibitor injection (Figure 4) at start-up and shutdown will be the primary flow assurance technique. be the primary flow assurance technique. The production flowlines will operate in multiphase flow, The production flowlines will operate in multiphase flow, and should operate above the hydrate formation temperature and should operate above the hydrate formation temperature and should not require hydrate inhibitor injection during and should not require hydrate inhibitor injection during steady flow.steady flow. For fields where wax deposition is a problem, huge For fields where wax deposition is a problem, huge investment in paraffin inhibitor, special VIT tubing types investment in paraffin inhibitor, special VIT tubing types and/or pipeline insulation or heating may have to be made. and/or pipeline insulation or heating may have to be made.
Shallow HazardsShallow Hazards
Shallow hazard studies are usually conducted at the start Shallow hazard studies are usually conducted at the start of any deepwater operation, to select well cluster sites with of any deepwater operation, to select well cluster sites with minimal geohazards. It is important to carryout a detailed minimal geohazards. It is important to carryout a detailed assessment of the seismic cross-sections for potential assessment of the seismic cross-sections for potential hazards such as shallow amplitude anomalies, gas chimneys, hazards such as shallow amplitude anomalies, gas chimneys, pockmarks and faults. Sometimes options for selection of pockmarks and faults. Sometimes options for selection of favourable locations may be limited hence the casing scheme favourable locations may be limited hence the casing scheme design will need to be robust to provide for contingency design will need to be robust to provide for contingency casing to ward off any unwanted pressure zone (figure 3) casing to ward off any unwanted pressure zone (figure 3)
RecoveryRecovery
Classical reservoir engineering methods [4] applied to Classical reservoir engineering methods [4] applied to understand the relationship between well drawdown and understand the relationship between well drawdown and ultimate recovery show that wells produced with lower ultimate recovery show that wells produced with lower backpressure are abandoned at lower pressure hence will backpressure are abandoned at lower pressure hence will usually recover more. For subsea tie-back developments, it usually recover more. For subsea tie-back developments, it is anticipated that many of the fields will be abandoned with is anticipated that many of the fields will be abandoned with high well head pressures due to the backpressure created high well head pressures due to the backpressure created by long pipelines/flowlines. This, coupled with the fact that by long pipelines/flowlines. This, coupled with the fact that production rates are reduced, again due to back pressure, is production rates are reduced, again due to back pressure, is expected to affect ultimate recovery from subsea wells. For expected to affect ultimate recovery from subsea wells. For the subject field and similar developments, waterflooding the subject field and similar developments, waterflooding may be a viable solution. For the subject field, planned may be a viable solution. For the subject field, planned recovery mechanism is an engineered waterflood, the recovery mechanism is an engineered waterflood, the tubing sizes have been designed for higher offtake rates. In tubing sizes have been designed for higher offtake rates. In addition, artificial lifting via gas injection at the riser base is addition, artificial lifting via gas injection at the riser base is considered to reduce backpressure effects. Use of Intelligent considered to reduce backpressure effects. Use of Intelligent Completions can also address reservoir management issues. Completions can also address reservoir management issues. Intelligent Well Technology (Smart Well Application) Intelligent Well Technology (Smart Well Application)
Operators often use intelligent well technologies for three Operators often use intelligent well technologies for three primary reasons:primary reasons: Ó Ó To reduce or eliminate intervention costs To reduce or eliminate intervention costs Ó Ó To accelerate production and reserves and improve To accelerate production and reserves and improve reservoir managementreservoir management Ó Ó To allow for additional recoverable reserves. To allow for additional recoverable reserves. For this subsea tie-back, use of intelligent wells was For this subsea tie-back, use of intelligent wells was proposed to improve the economics of the development. proposed to improve the economics of the development. Given the stacked nature of the reservoirs, smart well Given the stacked nature of the reservoirs, smart well application enables development of the marginal reservoirs, application enables development of the marginal reservoirs, and also helps in reservoir management. and also helps in reservoir management. Among key drivers of the smart well technologies are: Among key drivers of the smart well technologies are: Ó Ó Fewer, larger (tubulars and production rate) well Fewer, larger (tubulars and production rate) well Ó Ó completions which complement advanced directional completions which complement advanced directional drilling capabilitiesdrilling capabilities Ó Ó Pre-completion of primary, secondary and tertiary pays Pre-completion of primary, secondary and tertiary pays to exploit multiple reservoirs within the same primary to exploit multiple reservoirs within the same primary wellbore, favoring commingled production. wellbore, favoring commingled production. Ó Ó Overall increasing sensitivity to unplanned OPEX, driving Overall increasing sensitivity to unplanned OPEX, driving
reliability (availability) requirements. Intelligent Well Technology (IWT) encompasses two primary concepts Ó Surveillance in real time – making measurements of downhole flow and/or reservoir conditions possible in real time Ó Control in real time – the ability to remotely control zones via interval/inflow control valves ICV, by on/off control or choking (variable ICV) methods. Control is achieved by electric, hydraulic or electro-hydraulic (hybrid) actuation of a valve or sleeve.
Well Intervention
The remoteness of these subsea wells, coupled with a number of complex interactions between subsea wells, flowlines and the ocean environment make monitoring and intervention much more difficult. Also a shift to subsea production represents a significant departure from conventional production operations, and therefore presents a number of technical challenges. The single most-often-cited reason for running Intelligent Well Systems is intervention avoidance. Intervention carries with it a high cost, including rig cost, workover fluids, completion equipment, etc. In addition there is an opportunity cost that includes lost production for the duration of the intervention. Integrating intelligent well technology into subsea well architecture (figure 4) is actually a complex task since that would involve more dedicated support systems like power lines in umbilicals and additional power requirements for their usage.
Reliability Issues – Intelligent Well Systems
Intelligent Wells have evolved with development in completion technologies like downhole safety valves, sliding sleeves, downhole gauges, and other components that are becoming more and more reliable. With the extension of these components, Intelligent Wells can serve many purposes like flow control, downhole monitoring, and communication from the wellbore to the platform. The benefits are certainly desirable for most fields, but although close to 86% of all Intelligent Wells have experienced no failure, the number should be closer to 95% to call Intelligent Wells “mature” The most critical part that most often fails is the downhole electronics. One major technology gap is designing electronic gauges that can withstand severe downhole conditions because these components are the most sensitive to high temperatures. Thus fields with reservoirs of relatively higher temperatures, especially the deeper formations, may face higher risks of failure.
Well Integrity Monitoring
The ability to monitor the long term condition of a well is a special concern for subsea wells. The GOM has experienced a widespread occurrence of sustained casing pressure in producing wells. Methods to monitor and remediate this problem in subsea wells is an area of high interest and should not be ignored in the detailed design of the wells. Adequate measures need be put in place to provide for effective monitoring of well integrity.
Well Testing & Allocation (MPFM)
The traditional method of well testing and allocation has been by test separator information. For deepwater subsea type development there are significant challenges with this traditional separator well testing method. The challenges are further complicated by the subsea tie-back development. Some of the challenges bother on the need to: 1.Reduce number of risers and flow lines leading to a daisychain architecture. The impact of this reduction in number of flowlines and risers includes:
Reduction in flexibility to handle separate LP/HP production
Reduction in the flexibility for topside well testing
Production loss/deferment due to need for well testing 2.Mitigate Flow Assurance challenges such as slugging (unstable flow line conditions) 3.Design for appropriate operational range of test separators or flow meters The application of multiphase flowmeters (MPFM) brings new solutions to the well testing and allocation challenges. Multiphase flow meters provide real time production data enhancing reservoir management and production allocation. The application of Multiphase Flow Meters for well testing and production allocation is recommended. Most projects install MPFMs on each of the oil production subsea wellheads and at the topsides on each of the production risers so that a real time flow rate of oil, water and gas can be obtained. The MPFM on the wellhead will measure the three-phase production from the well in real time while the MFPM on the production riser will measure the combined three phase flow from all wells into the pipeline leading to the riser in real time.
Conclusion
A number of production technology solutions have been identified to mitigate some of the key production/injection challenges faced by a number of deepwater subsea tieback development projects. Subsea tie-back systems are currently the most cost effective development option for harnessing small to edium size hydrocarbon accumulations from deepwater and ultradeepwater plays.
Figure 1: Seismic depth profile along appraisal wells drilled in the field
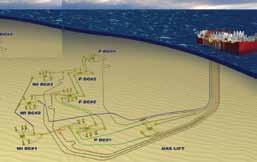
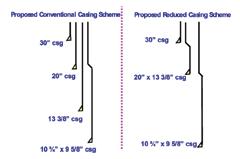
Figure 2: Subsea Architecture for the field development Figure 3. Casing Schemes

Figure 4. General Well Architechture


Vice President of CATEC:
We have lots of Competitive Advantages and plans to expand in MENA!

Shamel Elnomany is an Egyptian Engineer and has the Canadian nationality. He lived in Canada for 14 years and graduated from McMaster University in 2006, with dual degree from Mechanical Engineering and Business Management.
Directly after graduation he worked in Toronto, Canada for two years in Shaw Group, a reputable American EPC company with 7+ billion dollars in projects worldwide. He worked within an engineering team on a petrochemical project for SABIC.
He moved to Egypt in 2008, and now he has been working in CATEC for the past nine years, becoming its VP in 2011. CATEC (Consulting And Technical Engineering Company) is one of the leading companies in the Middle East and Africa in the field of industrial boilers, specialty lubricants, special pumps, textile machinery, and solar systems. The company was established in 1980 and entered the oil services sector since 2001. The Company has hundreds of customers in more than 50 countries, and it is the official exclusive agent for several German reputable industrial manufactures. It also has many competitive advantages that made it a pioneer in the field of renting and operating boilers to Oil Services Companies as well as industrial factories. In addition, the company is keen on the permanent training of its Personnel, whether in Egypt or Germany, to raise the level of technical performance for them in order to offer the best service to customers. Petroleum Today Magazine had the honor to meet Engineer Shamel Elnomany, Vice President of CATEC, to identify the industrial areas of work and operations, as well as how the Company serves the Oil & Gas sector, and the company future vision for expansion in the MENA region.
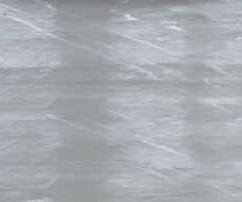
When was CATEC established and its work fields?
“CATEC was established in 1980 as an Engineering company, and obtained the exclusive agency of top European industrial manufacturers (mainly German). CATEC started working in textile machines and after 3 years the company entered the field of boilers, pumps and lubricants for all types of industrial applications.
The company is an exclusive agent of “BOSCH Industrial”
German company (formerly known as LOOS), and also provides boiler services throughout the Middle East &
Africa. CATEC also is an exclusive agent of “LUTZ”
German company for drum & container pumps, in addition to “Klüber Lubrication” German company for lubricants.
I would like also to add that Klüber possesses more than 2000 types of specialty lubricants used in delicate areas in all kinds of complex industrial applications, including the oil & gas sector” .

When did CATEC began to provide its services to Oil Sector Companies?
“As I said earlier, the company is the agent of “BOSCH
Industrial” in the field of boilers. In 2001 the company decided to buy boilers and redesign it with accessories inside 20ft containers for easy and quick mobilization. We rent our mobile boiler systems to oil services companies with our operation, consisting of engineers and technicians to operate the boilers on offshore & onshore rigs. We have started working first in Egypt and expanded after that throughout the MENA region. Now, we work in many Arab countries and our most important customers are SCHLUMBERGER, HALLIBURTON, EXPRO and
ALMANSOORI. Let me note that our containerized boilers are used in the Well Testing phase, as well as cleaning processes”.
We would like to highlight the number of company branches and the number of workers in it?
“The company has four offices in Egypt as well as a workshop and a warehouse in the industrial area of Borg Alarab in
Alexandria. We also have a temporary office in Canada to serve our projects in North America. We have hundreds of customers in more than 50 countries around the world, and the company has more than 60 full time employees, mainly Engineers. Our technical staff have the required Certificates, and our boilers have TÜV German certification”.
What is the competitive advantage that CATEC has?
“The company has several competitive advantages. For example, our operational staff has the highest technical level of qualified engineers and technicians to work on boilers, so that if any malfunction occurs in a boiler during operation they are capable to fix the problem on site, while our competitors’ operators cannot and their Engineer must be sent to fix problem. The second advantage is that the company is working in the field of boilers for more than 35 years now, and our BOSCH brand boilers are the best and most reliable in the world. Third advantage is that CATEC can provide a rental boiler for its clients upon request during two or three days only, and our prices are very competitive compared to our European competitors”.
How does CATEC give concern to its staff in terms of training and upgrading their technical and professional levels?
“CATEC puts training and raising the technical level of engineers and technicians as first priority to always exceed our customers’ expectations. The company gives training courses once a week in order to teach all the new technology of boilers, to keep up with technological progress. We also send several Engineers every year to BOSCH in Germany for intensive training on boilers and gain new knowledge. In addition our Engineers are faced with new boiler problems at factory sites, which also represents a kind of training. Also every three or four years we organize seminars and we invite managers and engineers of our clients’ companies for training on boilers and identify all what is new in this field. As a result of this training system, CATEC has countless maintenance contracts of various brands of boilers (not only BOSCH) throughout Africa, Middle East and South Asia”.

What is CATEC Company’s future vision for enlargements and offer more services for companies?
“We have visions and objectives aspirations of expansion in the coming years throughout the MENA region to gain more customers. We have also opened our Renewable Energy division in 2013, and already installed Solar systems in Egypt.