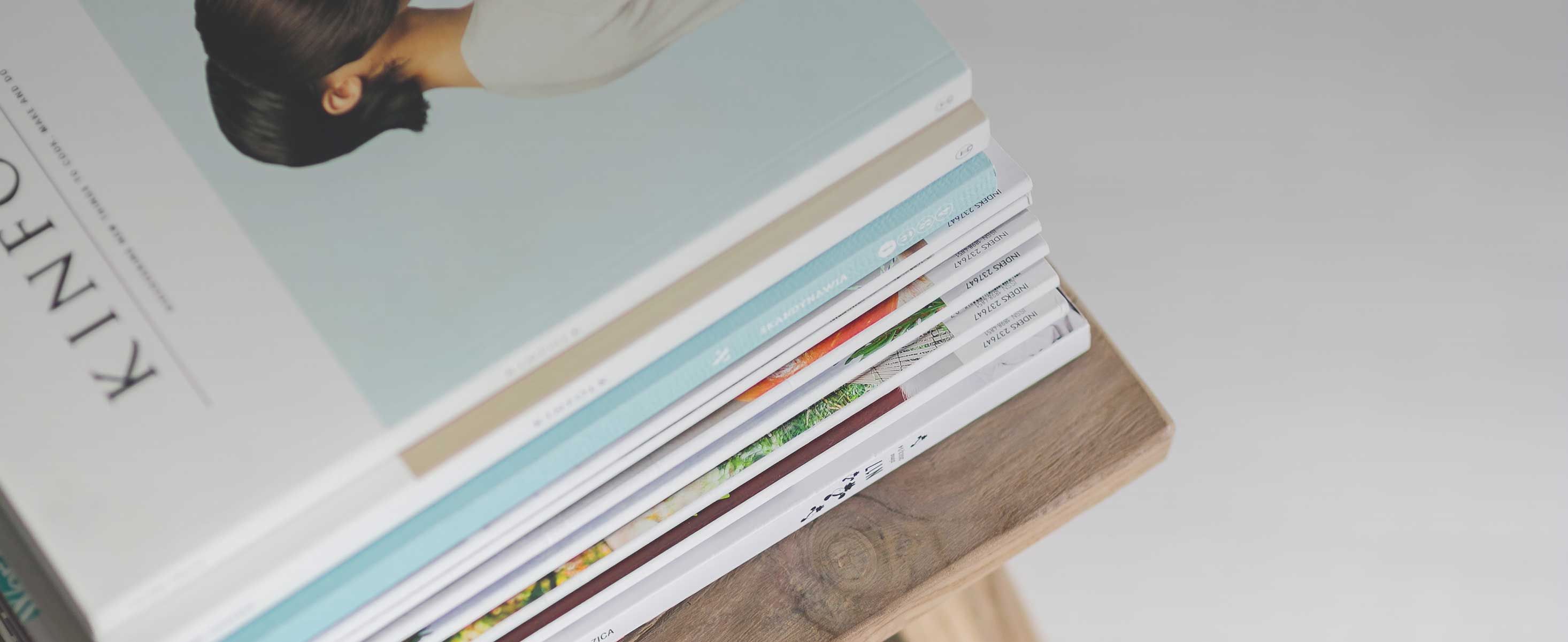
3 minute read
Testing Standards Ensure Product Is Usable for Its Purpose
By Greg Vassmer, technical coordinator, ARPM

Advertisement
Greg Vassmer ARPM Technical Coordinator
Most customers believe they have a practical understanding of whether a product fits its purpose. For example, a garden hose should not burst when the water is turned on. But because this concept is so key and disagreement so frequent, most suppliers go to great lengths to confirm a product works as customers believe it should.
So, how does a supplier determine a product is usable for its purpose?
Testing. For a garden hose, it might be a burst test – that is, pressurize a hose until it bursts (all very safely, of course). But how about a hydraulic hose operating under much higher pressure, sitting in the sun all day, rubbing up against a part of the bulldozer body at -40° C or perhaps 125° C?
The manufacturer of a hydraulic hose – for example, a fiber-reinforced hose for oil-based hydraulic fluids – has a much bigger burden confirming the product works as stated. Technological products typically are tested at three levels.
First, there’s development testing. At this stage, everything about the product could be new and untried. The raw materials, the subcomponents made by a second-tier supplier, the manufacturing technique and the design geometry all might be different from earlier models. Perhaps it has new rubber formulations for the hose cover and interior. The cover rubber will need to be tested for the effects of ozone, temperature and abrasion. The interior rubber will be tested for the effect of the hydraulic oil and temperature. Related tests will be run on other subcomponents, like the fiberreinforcing material. With this information, the designer makes prototype hoses for testing the geometry (diameters, wall thicknesses), the manufacturing technique (die size, adhesion and cure parameters), and finally, the finished product (flexibility, vacuum, abrasion and pressure). The idea is to find tests that mimic the products’ working environment and elicit the same failure characteristics as in the field. For products that last years, it is necessary to accelerate the aging/failure process. Consider a car engine crankshaft seal. If tested on a car, a seal will last 10 years or more – a long time to determine whether a design is good or to test several design ideas. Even when accelerated, a seal test in the lab lasts nearly six months.
The next level of testing begins once designers believe they have a working product (and many times, before). The goal is production qualification. A production batch is run, then parts are tested to determine whether the supplier reliably can make the product to specification, and if not, whether any defective parts before they are shipped. This leads to the last type of testing can be caught: Periodic tests run to confirm nothing has changed in the material, design or manufacturing process since the original qualification testing was done.
This test sequence is logical but complex to execute when the same hose goes to several customers and each could have a different set of tests to meet their requirements – or no tests at all. For a typical hydraulic hose, ISO 1436 (and the 10 other ISO test methods it references) outlines how the hose is tested. Hoses are tested for bend radius, burst pressure, low-temperature flexibility, cover adhesion, lining adhesion, vacuum, abrasion, ozone, fluid resistance for cover and lining and several dimensional features. If there is a change in the product material, design or manufacturing process, some or all the tests need to be run again.
The ISO 1436 does not stop there. Certain tests are expected to be run at intervals based on time (every 24 months), length of manufactured hose (every three kilometers) and warehouse production lot. As complex as this seems, without the standard there would be an even larger spaghetti bowl of individual supplier-customer test programs and conditions. Currently, the responsible ISO group – TC45/SC1 – is working on clarifying these test requirements and retest intervals.
Until now, the hydraulic hose has been used as an example. Test protocols like ISO 1436 exist for welding, steam, ammonia, oil suction and gasoline hose (all ARPM standards). And even further, test methods exist for most critical rubber products on the market today – many captured by one of the standards writing groups. All of them are efforts to ensure a product is merchantable or better. n