33 minute read
Web coating defects: Steps to improve coating-weight uniformity
By Edward D. Cohen, Ph.D., president, Edward D. Cohen Consulting, Inc.
Editor’s Note: This article is the second in a four-part series that discusses the major web-coating defects, their various causes and the technology and methods needed to eliminate them and to prevent their recurrence. Part One appeared in the 2011 Quarter 1 issue.
Coating-weight non-uniformities are one of the major loss categories in the web-coating process. Because the performance of the coating is a function of the actual coating weight, a uniform coating at the desired coating weight, over the entire substrate, is essential to producing a saleable quality product. The coating weight must be uniform within a roll, down-web and cross-web and give an average coating weight that is within specification. If the coating weight, uniformity and roll average vary outside of limits, the product will not function as intended and will be scrapped, resulting in a yield loss and increasing costs. Another source of losses is a higher coatingweight lane in the machine direction. This heavy lane does not completely dry and causes roll laps to stick together in storage, and the roll is not useable. If too much coating is applied, it may not affect product performance but can raise costs by wasting material. This can be a major concern when expensive raw materials are used or may be in limited supply. Another need for
TABLE 1: Coater variables that affect coating weight
Coater line-speed uniformity, web tracking Coating-solution viscosity, percent-solids, surface tension, temperature control Coating applicator type, fabrication precision, variables level and variation in run Coating-station design, fabrication, rigidity, settingsprecision sustainability in production run Pump uniformity Substrate flatness Preventative maintenance improved uniformity is that many of the newer products have thinner coating weights and tighter specifications.
Technical approach
To obtain a uniform coating weight over the entire substrate, the coating applicator must deposit a uniform, wet coating thickness. The applied coating will then maintain its thickness throughout the coater unless it is physically damaged and is distorted. This damage can be done by contact with a roll that contacts the coating or by high air velocity in the dryer. Difficulty in obtaining high uniformity depends on several coater variables (see Table 1). All of these must be optimized and reproduced for improved uniformity.
Because of the high number of variables, a structured process is the best approach to optimize and upgrade uniformity. A random procedure will be time-consuming, expensive and may not achieve the best operating conditions. The suggested major steps in this process are: • Determine product-uniformity requirements • Select coating-weight measurement technique • Select appropriate coating method • Optimize and maintain coating solution and coater-operating conditions • Upgrade coater to meet desired requirements, if needed • Institute operating procedures, quality-control systems and data-management systems.
Determine product-uniformity requirements
The first step in the improvement process is to determine the uniformity specifications needed. These specifications should be based on the performance required by the customer and should not be either over- or under-specified. To characterize and control uniformity, there are several key measurements: • The coating-weight values in the Transverse Direction (TD), across the substrate from edge to edge • The coating-weight values in the Machine Direction (MD), from the start to end of the substrate roll • The roll average that is calculated from the previous values • Average of all rolls in production campaign.
Figure 1 shows two typical coating-weight profiles. There are no industry standards to express uniformity. This can cause confusion because two sources can give different numbers and yet have the same uniformity. A single TD-profile measurement will give lower uniformity values than all the measurements in the roll. There are a variety of statistical functions used to describe the variability in these profiles and to permit comparison of various profiles. The best function to use is (high-low)/average expressed as percent. This measurement will show the spikes in the coating profile that will adversely affect performance. When reporting values, the function used to calculate value should be shown. The roll average should be the average of several TD-profile measurements. The MD variation can be calculated from the TD profiles.
After deciding on uniformity specifications, it also must be determined if the coating line is capable of meeting these requirements and identifying process-limiting hardware. In some cases, the existing unit cannot meet the goal requirements, and the coater must be upgraded. Some examples of process limits include wrong coating method is used, linespeed variations are too high and measurement system cannot measure desired product range.
Select a coating-weight measurement technique
In this step, select a coating-measurement method that gives the precision and reproducibility needed. Measurements can be made by sampling the web, then doing static measurements, or it can be done online with continuous measurements as the web is coated. Sensitivity of the method should be lower than the product requirements. If it were higher, then differences in the actual coating would not be detected. Ideally, the current analytical method should be suitable. If not, then a new method is needed.
Online measurement is the best technique because it gives rapid results and complete inspection of the coated substrate on coater. With this system, adjustments can be made on the coater, and results are seen immediately. It also cuts costs compared to a static system by minimizing out-of-limits material during the measurement time. A rapid-detection feature is
Coating-Weight Profile High Center
Machine-Direction Profile 3 Lanes
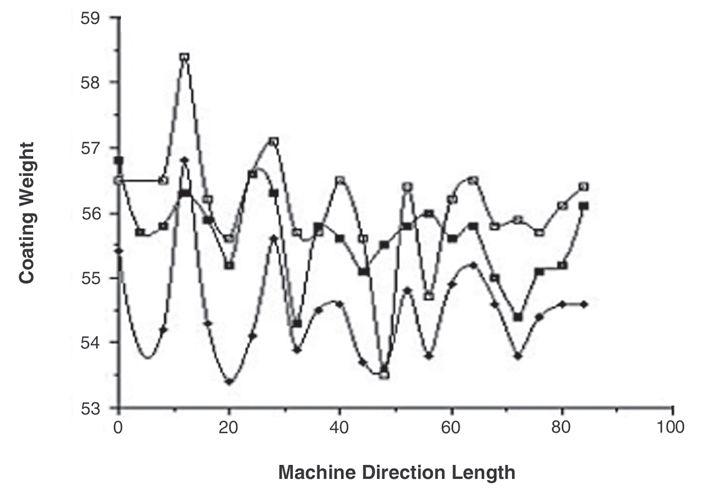
FIGURE 1: Coating-weight profiles
t continued from page 75 TABLE 2: Online coating-weight sensors
Total-weight gauges: Beta, Gamma, X-Ray Transmission, backscatter Need two gauges; one before the coating station to measure the substrate, and a second after the coating station to measure substrate + coating. Subtract to get coating weight.
Direct coat-weight gauges: Infrared, Beta Backscatter, X-Ray Fluorescence Directly measure the coating; can be single-point or scanning.
TABLE 3: Coating-applicator uniformity
Poor uniformity, 10 Percent Blade/knife, dip & scrape, dip & squeeze Doctor blade, Mayer Rod, Meniscus Spray, Comma direct/indirect, Dip Forward roll
good uniformity, 5 Percent Reverse-roll, hot-melt, nip-roll extrusion Curtain standard, direct-roll hot-melt, air-knife
Superior uniformity, 2 Percent Slot-die, reverse-roll precision Curtain with edge guide, multilayer slide Micro-gravure, gravure-direct, gravure/offset gravure-direct with chambered doctor blade gravure-reverse
very important for small-volume production because it minimizes waste by rapidly attaining coating-weight equilibrium. There are many online-measurement techniques available (see Table 2).
Select appropriate coating method
Each coating method has a unique, optimum set of operating parameters, line speed, coating-weight range and uniformity and quality that it can attain. Operating outside these parameters will yield a coated product; however, it will result in poor quality, uniformity and reproducibility. The coating method must be selected to provide the needed uniformity. Table 3 indicates the coating-weight uniformity capability for several methods and can be a guide to evaluating new processes. The Mayer Rod has a uniformity capability of ~10 percent. If 3 percent is needed, this method will never achieve it. If 2 percent is needed, slot-die or slide coating are the preferred methods. A frequent occurrence is that increasing speed may lead to poor uniformity. If the correct coating method is not available, a new coater system should be considered or work should be outsourced to a toll coater. FIGURE 2: Substrate effect in blade coating
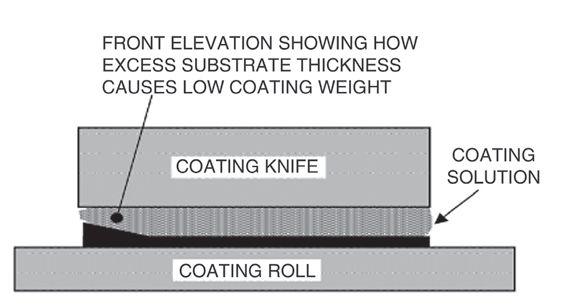
Optimize and maintain coating solution and coater operating conditions
Once the desired process conditions are determined, the key process variables must be controlled and maintained and coatingsolution properties need to be measured and reproduced. The viscosities and percent-solids are critical variables in controlling coating weight in all coating methods. These should be held to within very tight limits for all rolls coated. A good temperaturecontrol system helps maintain viscosity uniformity of the coating solution because viscosity changes with temperature. Inline viscosity-measurement systems should be considered. A single-point measurement of viscosity after a batch of solution is prepared is insufficient to control the process. Inline viscosity measurement can be coupled with a solvent-input system to adjust viscosity within control limits.
The self-metered, reverse-roll, dip, etc., and doctor-blade, airknife, etc., coating methods are open to the atmosphere, and the overflow material is recycled to the main-feed system and reused. As a result, the viscosity and percent-solids can change, which causes coating-weight variations. Viscosity measurements coupled with online measurements reduce variability.
In the pre-metered coating, slot-die, slide, etc., coating methods, there is no recirculation, so viscosity change is minimized, and the method is not as susceptible as other methods to viscosity changes. However, viscosity is a function of percent-solids, and metering a constant volume of solution will cause nonuniformities because solids deposited will vary. In addition, precision pumps are required and changed when wear is detected.
Substrate uniformity can affect coating-weight uniformities in the doctored coating methods. The doctor-blade removes the excess wet film, which is essentially parallel to the substrate. This gives a uniform coating weight if the substrate is also uniform. However, if the substrate is not flat or there are surface peaks and valleys, the coating weight will vary to the same extent as the thickness between doctor blade and substrate. Thus, an uneven substrate will lead to coating non-uniformities (see Figure 2). This is an important factor if a wide-web roll will be slit down to many narrow rolls.
Because of the high number of variables, a structured process is the best approach to optimize and upgrade uniformity.
Physical properties of the coating station also have an impact on all methods. The coating-station support design and fabrication must insure that the applicator is rigid and can maintain the needed tolerances and applicator settings during production. The normal operation of a coater imposes severe stresses on the coating station, thus it must be sufficiently rigid to avoid distortion during long production runs. The mechanical hardware that controls important process variables (such as applicatorto-roll gap and roll speed) needs to be designed and fabricated to give precise settings and maintain these settings during production. Any extra cost to have superior design will result in significant cost-savings and improved product down the line. A preventative maintenance program on all hardware is vital, and worn parts must be replaced when detected.
MD uniformity is primarily a function of the variations in the substrate’s linear speed across the applicator and variations in the profile of the substrate of the range-drive uniformity. Uneven speeds will lead to MD variation because coating weight is a function of web speed in roll-coating applications. Therefore, range drive, line speed and tension control may need to be improved for precise control. Similarly, in pre-metered, slot-die, curtain and slide coating, the flow to the web is constant and variations in substrate line speed will give MD variations. n
Edward D. Cohen, Ph.D., is president of Edward D. Cohen Consulting, Inc. (Fountain Hills, AZ). He has expertise in the coating and drying of thin films, coating-process development and scale-up, film-defect mechanisms and analyticalcharacterization techniques. With more than 35 years of experience in coating research, Cohen is the author of two books. He is also president of the Intl. Society of Coating Science and Technology, a DuPont Fellow, a technical consultant for AIMCAL and writes the “Web Coating Blog” for CONVERTING QUARTERLY. Cohen can be reached at 480-836-9452, e-mail: cohened146@aol.com
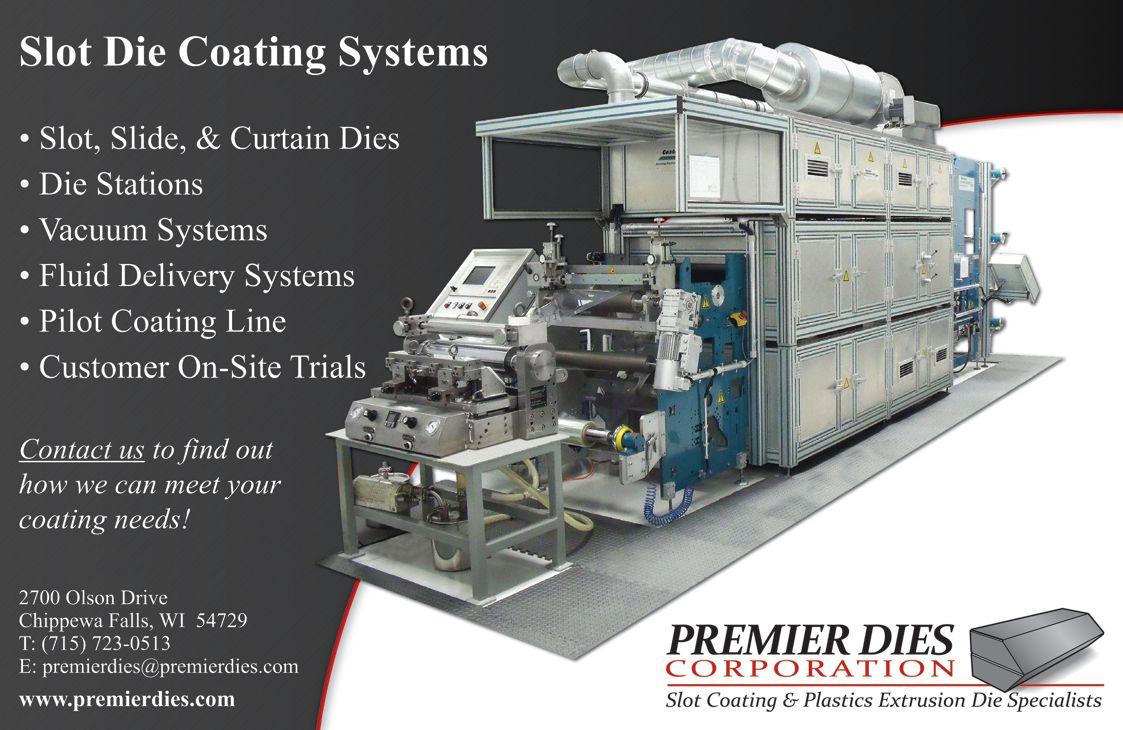
Water-based barrier coating compositions US Patent Application #20110027601 Charles G. Ruffner, Jr., et al (Cary, NC)
Abstract: A water-based barrier coating composition is disclosed that has improved barrier performance and enhanced stability. The water-based coating composition comprises a polymeric binder and an amine stabilizer, wherein the pH of the composition is equal to or greater than the pKa of the amine stabilizer. When desired, the disclosed coating composition may further include standard low-cost fillers, layered fillers capable of being at least partially exfoliated, nanoparticle fillers or mixtures thereof. A multilayer product comprising a layer of the disclosed water-based coating composition also is disclosed that has enhanced oxygen-barrier performance.
Means of closing a bag having a degradable, biodegradable and/or compostable coating
US Patent Application #20110038565
Andre Grob, et al (Singapore)
Abstract: The application relates to a means for closing a bag, in particular a bag made of bioplastics. The means for closing a bag comprises at least one wire covered at least partially with a coating of a bioplastics. The coating is a closed coating offering the wire corrosion protection when exposed at normal ambient conditions during storage or use of the means and the coating being degradable, biodegradable or compostable once the means is exposed to an environment suitable for decomposition.
Ablatable elements for making flexographic printing plates US Patent Application #20100285406 Michael T. Regan, et al (Fairport, NY)
Abstract: Flexographic printing plates and other relief images can be formed from a laser-ablatable element having a laserablatable layer that is from about 300 to about 4,000 microns in thickness. The laser-ablatable layer includes a film-forming material that is a laser-ablatable material or the film-forming material has dispersed therein a laser-ablatable material. The laser-ablatable material is a polymeric material that when heated to 300 deg C at a rate of 10 deg C/min, loses at least 60 percent of its mass to form at least one predominant low molecular weight product. The laser-ablatable material also comprises at least 0.01 weight/percent of a depolymerization catalyst that is a Lewis acid or organometallic-based catalyst. The element can be imaged by ablation at an energy of at least 1 J/cm2 to provide a relief image.
Novel material for infrared laserablated engraved flexographic printing plates US Patent Application #20100283187 Murray Figov (Ra’anana, IL)
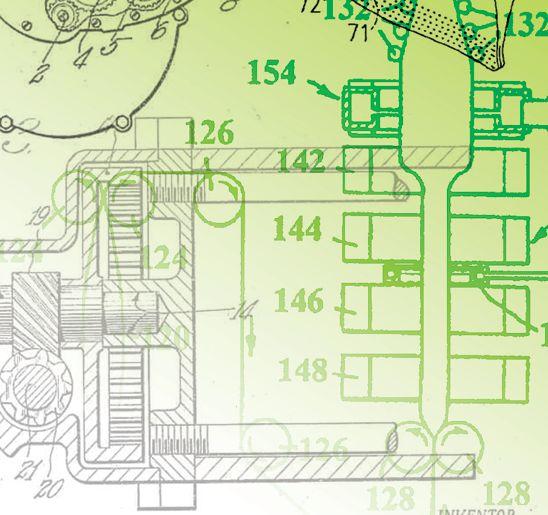
Abstract: A non-photosensitive flexographic liquid or paste precursor comprising a mixture of acrylate oligomers and acrylic or methacrylate monomers, infrared-absorbing material, fillers and heat-decomposable peroxide, which when heated forms a non-thermoplastic elastomeric solid material in the form of a flexographic-printing, blank engravable by infrared laser ablation.
Film-thickness measurement apparatus
US Patent Application #20110040510
Kazufumi Nishida (Musashino-shi, Japan)
Abstract: A film-thickness measurement apparatus may include a spectrum acquisition unit that irradiates a light onto a film and acquires a spectrum of a reflection light or a transmission light, a power-spectrum calculating unit that calculates a power spectrum, a film-thickness calculating unit that detects a peak position of the power spectrum and calculates a thickness of the film, a measurement-quality calculating unit that calculates a measurement quality of the thickness, a measurement-quality determining unit that determines whether the thickness is valid or invalid and a film-thickness output unit that outputs the thickness if the measurement-quality determining unit determines that the thickness is valid.
Method for manufacturing microcrystalline semiconductor film and thin-film transistor
US Patent Application #20110039402
Shunpei Yamazaki (Tokyo)
Abstract: A microcrystalline semiconductor film with high crystallinity is manufactured. In addition, a thin-film transistor with excellent electric characteristics and high reliability, and a display device including the thin-film transistor are manufactured with high productivity. A deposition gas-containing silicon or germanium is introduced from an electrode including a plurality of projecting portions provided in a treatment chamber of a plasma CVD apparatus. Glow discharge is caused by supplying high-frequency power, and thereby crystal particles are formed over a substrate, and a microcrystalline semiconductor film is formed over the crystal particles by a plasma CVD method. n
Triple-lip air ring increases cooling capacity, output on blown-film line
Davis-Standard’s (Bridgewater, NJ) new blown film-pilot line employs a new Triple-Lip Air Ring recognized for increased cooling capacity and output rates. One customer with an mLLDPEcoextruded film was limited to a rate of 15 ppi (pounds per in. of die circumference) due to high ambient temperatures and limited 10-year-old cooling technology. During a pilot trial, rates of 23 to 24 ppi were demonstrated comfortably with an improved thickness control of +/-4 percent. The Triple Lip’s singular design has one air ring, blower and chiller instead of two, with a counter-cooling concept along the hi-stalk and an easily adjustable elevator. Processors have a wider production range and improved outputs with a BUR (blow-up ratio) of 2.0:1 to 4.4:1. Performance increases in the 30 to 40 percent range are common with excellent thickness control. Film processors also can take advantage of simplified maintenance. DAVIS-STANDARD, 908-722-6000, www.bc-egan.com

Power, signal cable quick-release mechanism protects against vibration shakeout
Siemens Industry (Atlanta) introduces the Speed Connect, a new quick-release mechanism that protects against vibration shakeout on its Motion-Connect® line of power and signal cables. The Speed Connect release is said to make installation and changeover, even in very restricted space applications, fast and easy. No tools are required; just a one-quarter turn locks or unlocks the bayonet-style connectors. All Siemens Motion-Connect cables are system-tested to guarantee optimum performance in any motion-control system. Motion-Connect cables are fully shielded to prevent EMC noise emissions and protect the motion-control system from ambient environmental noise. Motion-Connect cables are certified to CE, VDE, UL and UL/CSA standards. SIEMENS, 800-879-8079, www.usa.siemens.com/motioncontrol
Web coater combines slot-nozzle, rotating-bar technologies for complete tool
Nordson Corp.’s (Duluth, GA) new TCHP TrueCoat slot applicators reportedly provide exceptional stripe or full-coating application accuracy in continuous web-coating processes. Streak-free coverage and excellent edge control make the TCHP particularly beneficial for labeling and tape applications. The compact, configurable design is ideal for coating a wide variety of substrates including papers, foils, films and nonwoven materials. The TrueCoat’s V-shaped body design provides flexible setup of web routing and guidance, and fast pattern changes are achieved with quick-change, replaceable slot nozzles. The flexibility and functionality of the TCHP slot applicator is shown in how it quickly and easily changes between traditional slotnozzle and rotating-bar technologies. A new nozzle-clamping design provides quick removal of dies for servicing. Optional anti-stick surface coating is said to ease cleaning. Standard application widths are available up to 31.5 in. Longer widths, up to 118 in., may be available upon request. NORDSON CORP., 800-683-2314, www.nordson.com
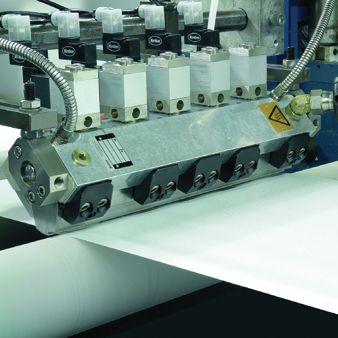
PLA modifier for film, sheet increases impact strength 10 to 20X, boosts clarity
Teknor Apex Co. (Pawtucket, RI) launches a clear impact modifier masterbatch for use with polylactic acid (PLA) bioplastics to provide substantial increases in impact strength while sustaining the excellent clarity of the base resin. Terraloy™ 90000 Series masterbatches are formulated with Biostrength® impact modifier at 5 to 10 percent levels. Terraloy 90000 complies with US Food & Drug Administration requirements for foodcontact applications at loadings up to 20 percent. In one series of standard tests with 2-mil cast-film tape, Terraloy 90000 Series masterbatch increased Gardner impact strength up to 16-fold, compared to unmodified or “neat” PLA. At the same time, haze levels increased from 4.1 to only 6.5 percent. Biostrength® is a registered trademark of Arkema, Inc. TEKNOR APEX BIOPLASTICS DIV., 401-724-8000, www.teknorapex.com
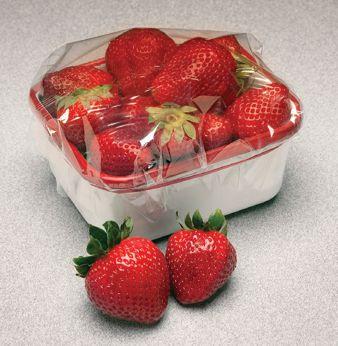
Digital load-cell amplifier offers versatile operation, easy installation
The Montalvo Corp.’s (Gorham, ME) new A4 Digital Amplifier is said to be the most versatile load-cell amplifier available. It automatically notifies operators of any faulty or damaged load cells and identifies the exact load cell needing replacement. Features include easy installation; can be calibrated and zeroed
t continued from page 79
with the push of one button; USB/PC interface; provides outputs that a customer’s drive or PLC can use to control tension or trim drives; used to remotely calibrate and graphically monitor both raw inputs from the load cells and amplifier outputs; has threechannel output: left, right, total; has multiple electronic output options: 0-10V or 4-20mA outputs, 0-100mA selectable and works with most semi-conductor and foil-gauge tension sensing load cells. THE MONTALVO CORP., 800-226-8710. www.montalvo.com
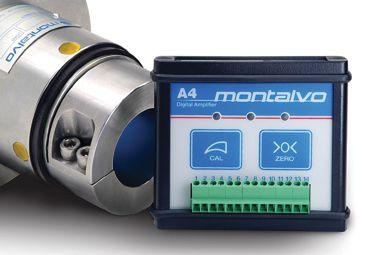
Directional-tear sealant films fit non-retort packaging applications
Toray Plastics (America) (North Kingstown, RI) expands its line of Torayfan® TreaTear™ directional-tear polypropylene sealant films, introduced in 2010 for retort applications, to include Torayfan® TreaTear LT52 and LT72 films for nonretort applications. Converters can manufacture attractive standup pouches that provide effortless, precise straight-line tear across the package every time, as well as offer improved rigidity and clarity. TreaTear LT52 and LT72 polypropylene films also perform as a drop-in sealant film for LDPE-sealant web applications. Available as thin as 30 microns (1.2 mil), TreaTear films offer yield advantages over traditional 60- or 70-gauge sealant films and source reduction benefits. LT52 film’s low haze provides four to five times better clarity than traditional LDPE-sealant films, making it ideal for window applications. LT72 film’s low seal-initiation temperature makes it suitable for pouches made with BOPP laminations. TORAY PLASTICS (AMERICA), INC., 401-294-4511, www.torayfilms.com
Photovoltaic-metallization materials help reduce dependence on fossil fuels
DuPont (Wilmington, DE) innovations in photovoltaics are key to the manufacture of both crystallinesilicon and thinfilm solar cells and modules. Materials include films, resins, encapsulation sheets, flexible substrates and photovoltaic metallizations. Four new Solamet® metallization pastes enhance the efficiency of solar cells, DuPont™ PV5400 series thin ionomer-based encapsulant sheets protect sensitive and cost-effective, thin-film solar modules, and a new Tedlar® PV2400 polyvinyl fluoride (PVF) film extends the availability of long-life backsheet material to better meet mounting demand in the industry.
DUPONT PHOTOVOLTAIC SOLUTIONS,
http://photovoltaics.dupont.com
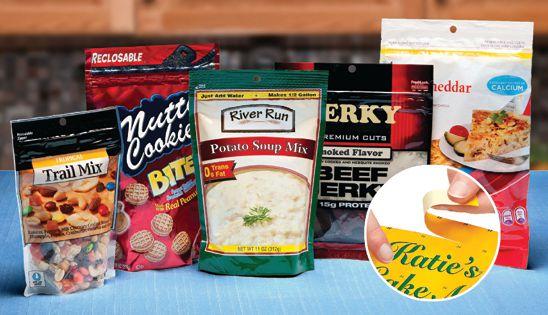
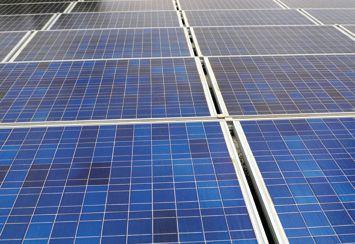
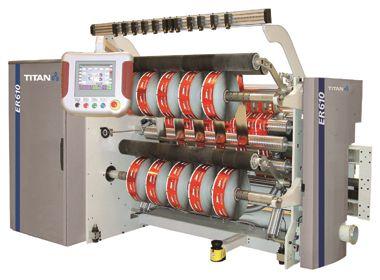
Twin-shaft, compact slitter features all-electric, oil-free operation, cuts waste
Atlas Converting Equipment, Ltd. (Kempston, UK) offers the Titan ER610 compact slitter/rewinder. A twin-shaft, cantilever slitter, it provides a more environmentally friendly slitting and rewinding solution with reduced power but all-electric, oil-free operation without hydraulics, a CCD edge-guide camera for reducing waste, a running speed of 1,500 fpm and an option for slit widths as narrow as 1.37 in. With about 100 installations worldwide, the Titan ER610 slitter has been a great success. Available in two widths—53 and 65 in. with a maximum rewind diameter of 24 in., it also features a 10-in. touchscreen control system and an integral edgetrim extraction system. The pneumatically controlled braking system provides accurate web tension control and a digital edge-guide system controls lateral movement of the unwind reel to +/-2 in. Slitting systems available include shear knives, rotary razor (burst) or razor slitting in air or groove. The Titan ER610 processes a wide range of flexible materials including plain, printed, coated or metallized film from 20 to 200 microns, a wide range of laminates and paper from 30 to 200 gsm. ATLAS CONVERTING NORTH AMERICA, 704-587-2450, www.atlasconverting.com
Rolls for super-thin coatings constructed to extremely tight tolerances
Webex (Neenah, WI) builds coating rolls for today’s super-thin web coatings to extremely tight tolerances. Roller tolerance (or concentricity) is measured as TIR—total indicated runout. The tighter the tolerance, the smaller the TIR dimension. The company has produced coating rolls with as little as 1 micron TIR—or 40 millionths of an inch variance from one end of the roll to the other. Because rolls are ground and polished with roll bearings in place, the manufacturer uses special bearings with certified tolerances. Most coating rolls also are heat-transfer rolls often specified with a chrome-plated finish. To ensure such exacting tolerances on coating rolls, the company uses an electronic gauge to measure roll TIR. Webex routinely produces tight-tolerance coating rolls with diameters of 6 to 24 in. and larger for lines running as fast as 3,000 fpm. WEBEX, 920-729-6666, www.webexinc.com
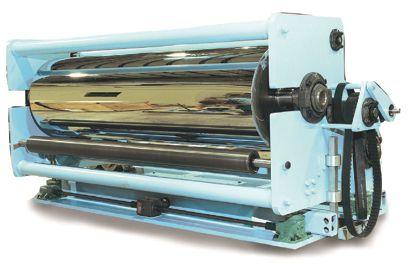
Heavy-duty core plugs provide strong, secure fit
Badger Plug (Greenville, WI), a supplier of material-handling and finished-goods protection products, meets converter needs for when larger rolls require extra protection to prevent crushed cores. Available in plastic, metal and wood in sizes from 1-1/2 to 60 in., heavyduty core plugs possess outstanding strength to help prevent crushed cores. Hundreds of different core-plug sizes and configurations including medium- and light-duty models are offered. BADGER PLUG, 920-757-7300, www.badgerplug.com
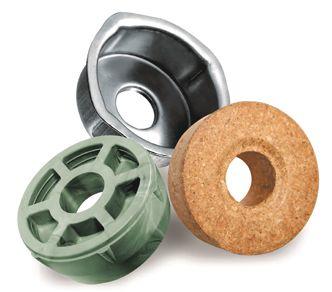
Web-measurement system features new terahertz technology for superior scanning inspection
Advanced Photonix, Inc. (Ann Arbor, MI) introduces reportedly the first online, industrial time domain, terahertz system for superior scanning web measurement. The Picometrix T-Ray 4000® for the converting/package printing marketplace uses pulsed terahertz technology—a non-nucleonic, non-ionizing, non-contact measurement solution that combines basis weight, percent moisture, caliper thickness and multilayer thickness measurements into one ultra-fast multifunction sensor. The T-Ray system has an unusual single-sided measurement format and can detect delamination and sense adhesion degradation with speed of light precision. A single T-Ray unit can replace multiple scanning nucleonic systems for lamination and composite lines. It provides superior precision and inherent safety for the product and manufacturing personnel. The T-Ray measures caliper thickness directly without a mass composition-dependent conversion. It offers the first web-scanning sensor that can feedback-control an automatic die using true caliper thickness precise to two femtoseconds of light speed. ADVANCED PHOTONIX, INC., 734-478-1656, www.advancedphotonix.com
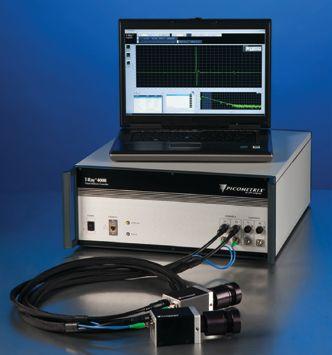
New dual-function center winder offers time-saving technology
The Catbridge Machinery (Parsippany, NJ) Model 902 cantilevered, duplex center winder also can log-wind largediameter rolls. It has all the capability and efficiency of a standard, cantilevered duplex slitter, winding to 31.5-in. on both shafts. Additionally, when there is a requirement to unwind, trim and rewind to diameters exceeding the maximum capacity of standard duplex models, the 902 accommodates this work. It can logwind diameters up to 48 in., depending on roll weight and shaft diameter. Log rolls are wound on the bottom shaft, which is operated in a lift-out mode. In addition to simply trimming, a few cuts also can be made for certain materials. The Model 902 winder incorporates Catbridge’s new automatic coreplacement feature, which allows cores to be precisely positioned, automatically, while the operator is performing packaging or other finished-roll discharge activities. After the cores are loaded on both rewind shafts, the machine automatically “picks and places” each core precisely where it needs to be for rewinding. Operating with automatic knife positioning, the core-placement system provides faster, more accurate setups. Time-savings, especially on narrow cuts where there are many cores, can be dramatic. Applications for this versatile duplex winder include
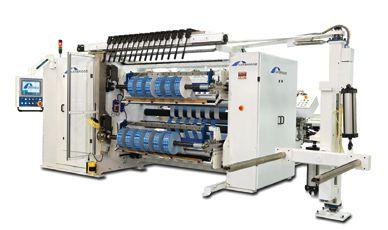
t continued from page 81 flexible packaging, foams, film laminations, pressure-sensitive label stock, window films and paper. CATBRIDGE MACHINERY, 973-808-0029, www.catbridge.com
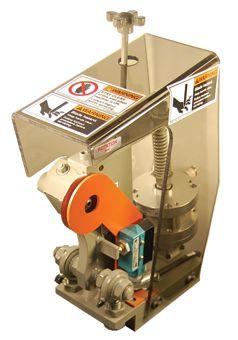
Auto-indexer safely extends core cutter knife life
Appleton Mfg. Div.’s (Neenah, WI) patented Automated Indexing Knife (AIK) for fixed knife cutters automatically rotates the core cutter knife to produce more clean-cut cores from every knife. The indexer automatically and precisely rotates the knife based on a preset number of cuts. While significantly extending knife life, hands-free automatic knife adjustments also improve worker safety and decrease downtime. Operators now only handle the knife for blade replacement. The AIK easily can be retrofitted to existing Appleton core cutters or added to new models. This easy-to-install indexer includes a control panel and a new knife holder. APPLETON MFG. DIV., 800-531-2002 www.appletonmfg.com/automatic-knife-index.php
New pattern system solves many corona-treating problems for film extruders
Enercon Industries Corp.’s (Menomonee Falls, WI) new Air Treat™ pattern corona treater is available as an option with the co.’s CSO corona treater, which features stainless-steel electrodes, several roll-covering options and high-performance power generation from Enercon’s Compak™ power supply models. The operator-friendly Air Treat’s benefits included new remote pattern-treating capabilities; remotely set segments from the operator’s panel; positive feedback on segment position; and waste reduction and increased productivity. ENERCON INDUSTRIES CORP., 262-255-6070, www.enerconind.com
Rebuild program repairs, restores magnetic printing, anvil cylinders
Bunting® Magnetics Co. (Newton, KS) introduces its Rebuild Program to repair and restore magnetic printing cylinders and anvil cylinders, refinishing all surfaces to meet exacting customer specifications. The service covers diecutting, folding carton, two-piece can, plastic container and corrugated cylinders. Technical services include replacement of cylinder bearers;
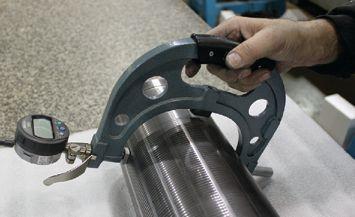
repair or replacement of damaged magnets; restoration of bent or damaged journals; installation of hardened races and complete refinishing of the surface of the cylinder. New parts are inspected prior to the cylinder being reassembled. All new bearers are installed to manufacturer’s specifications to ensure proper fit and prevent premature failure. Bunting’s Rebuild Program also offers detailed, on-site Plant Audits that provide visual inspection of all cylinders in stock. All surfaces, bearers and journals are inspected for damage or imperfections. The supplier performs a run-out test on all journals, bearers and the body of the cylinder to determine any deviations from specifications. BUNTING MAGNETICS CO., 800-835-2526, www.buntingmagnetics.com
Cleanroom coating equipment develops cost-effective machine design
New Era Converting Machinery, Inc. (Paterson, NJ) is currently in production of three cleanroom coating lines. New Eras’ expertise in the cleanroom equipment industry can help customers develop the most cost-effective machine design to meet their production requirements. The systems being manufactured at present range from class 100 to class 10,000 cleanroom.
NEW ERA CONVERTING MACHINERY, INC.,
201-670-4848, www.neweraconverting.com
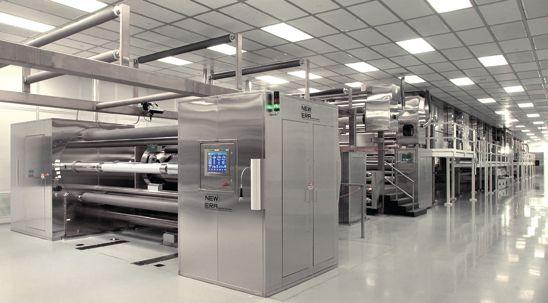
Back-up brushes benefit film/paperboard perforating, slitting operations
Finzer Roller’s (Des Plaines, IL) new Back-Up Brushes are completely changing the perforating, slitting and cross-hatch scoring of plastic webs and paperboard products. Both multiwallbag and plastic-web converters are rapidly replacing metal anvil rolls with Finzer Roller’s Back-Up Brushes. Among the product’s benefits: Accepts perforating pins or knives; reduces setup time, allowing simple tape measure installations; pins or knives do not damage the bristle; no more fitting or adjusting to match pin and knife points and misalignment is virtually impossible with free-wheeling back-up brushes. Back-Up Brushes are extremely uniform, presenting individual strands of bristle rather than clumps or tufts, and their controlled brush density allows unlimited bristle patterns from “open” to “super dense.” FINZER ROLLER, 888-486-1900, www.finzerroller.com
Flexible biopolymer easily processes on blown-film extrusion lines
FKuR Plastics Corp. (Cedar Park, TX) has launched Bio-Flex® F 2201 CL, a new transparent, flexible biopolymer that contains a high content of renewable resources and can be processed easily on standard LDPE blown-film lines and converting equipment. With approximately 60-percent renewable content, the resin’s mechanical properties exhibit a high elongation and flexibility along with good puncture resistance, says the supplier. Due to its good interply strength, Bio-Flex F 2201 CL is recommended as a mid-layer in a coextruded structure with Bio-Flex A 4100 CL in a transparent trilayer combination. As both polymers are clear, the transparency of a 2-µm film is close to 91 percent (light transmission). Such a multilayer structure is said to be ideal for VFFS applications. FKuR Plastics will exhibit at Interpack 2011 (Hall 9, Booth F14). FKUR PLASTICS CORP., 512-986-8478, www.fkur.com
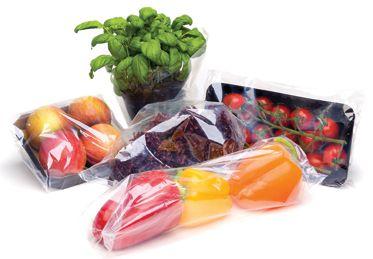
Continuous-motion puncher requires little maintenance, simple to use
Pearl Technologies, Inc.’s (Savannah, NY) patented Pivot Punch is spring-loaded for higher cycling speeds and features a built-in auto-alignment system. The unit requires little maintenance and is designed to be simple to use. Each Pivot Punch is guaranteed for the co.’s 30-day product satisfaction plan. Said to be much quieter than traditional ball-and-die punching, the unit offers converters long life and works on both thick and thin webs. PEARL TECHNOLOGIES, INC., 315-365-3742, www.pearltechinc.com
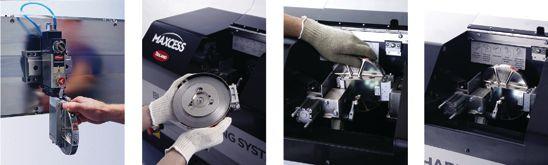
System sharpens Tidland-slitter blades on the cartridge in only 90 secs
Maxcess (Oklahoma City, OK) debuts the Tidland Blade Sharpening System, which gives customers the power to sharpen dull blades on their own schedule without removing the blade from the cartridge or sending the blades out to be reground or sharpened. The entire Tidland knife cartridge is inserted into unit, sharpened at the push of a button and ready to be placed back into operation in 90 secs. It can sharpen Class II and Class III Tidland knifeholders, including Performance Series, Series ‘C’ and e-Knifeholders. At a cost of $24,990, the system reportedly offers an ROI of as little as six months. Beta-site tests showed newly sharpened blades from the Tidland unit lasting up to 25 percent longer. MAXCESS TIDLAND, 800-426-1000, www.maxcessintl.com/sharp
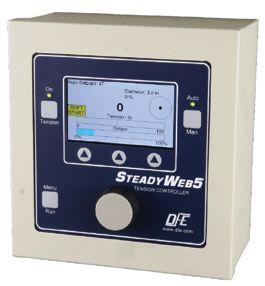
Web-tension controller speeds operator response with intuitive interface
Dover Flexo Electronics’ (Rochester, NH) new SteadyWeb™ 5 Digital Tension Controller gets operators up to speed with minimal training time via a streamlined, intuitive interface. Setup and configuration are a breeze with illustrated prompts and color graphics, and soft keys and the large, front dial allow easy scrolling through configuration values. Among the unit’s features: a large 4.3-in. graphic user interface; isolated 0-to-10 Vdc tension and control outputs, digital calibration and control for accuracy and signal stability; storage and recall settings for up to 32 job setups; choice of 100-240 Vac or 24 Vdc power input and choice of wall-mount full enclosure or panelmount for control-panel installation. DOVER FLEXO ELECTRONICS, 603-332-6150, www.dfe.com
Center-driven duplex slitter/rewinder joins converting-system line
Parkinson Technologies (Woonsocket, RI) launches the new Genesis 700 center-driven duplex slitter/rewinder. Designed for converters purchasing their first slitter or for companies needing flexible, targeted slitting capacity that’s easy to implement, the Genesis 700 meets today’s flexible-packaging and other web-material manufacturing demands. Able to handle film, film with liner, flexible packaging, label stock, laminates and papers, the system runs web widths up to 62 in. at speeds of up to 1,500 fpm. An industry leader in the development, design and manufacturing of webprocessing machinery for the plastics, nonwovens, paper and specialty-materials industries, Parkinson’s product brands include Parkinson winders, Dusenbery® Converting Systems, Marshall and Williams biaxial plastics-orientation lines and Key Filters plastic-extrusion melt-filtration equipment. PARKINSON TECHNOLOGIES, INC., 401-762-2100, www.parkinsontechnologies.com n
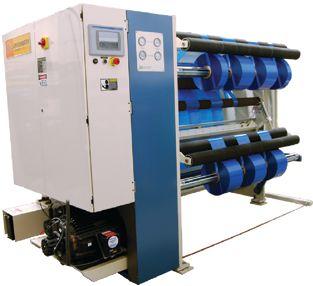
MAY 2011
4-6 2011 IADD*FSEA Odyssey: Nashville Convention Ctr., Nashville, TN. Intl. Assn. of Diecutters & Diemakers and the Foil & Specialty Effects Assn. www.odysseyexpo.org 10 Converting School – Drives in Web Handling: Crowne Plaza Downtown, Philadelphia. AIMCAL. www.convertingschool.com
10-11 Converting School – Web Handling & Converting (Europe):
Hotel Mercure-Louvain La Neuve, Brussels, Belgium. AIMCAL. www.convertingschool.com
12 Converting School – Optimizing Extrusion-Based Lamination
& Coating Technology: Crowne Plaza Downtown, Philadelphia. AIMCAL. www.convertingschool.com
12 Converting School – Winding: Machines, Mechanics &
Measurements (Europe): Hotel Mercure-Louvain La Neuve, Brussels, Belgium. AIMCAL. www.convertingschool.com 24 Converting School – Web Coating & Drying: Best Western Inn & Suites, Ontario, CA. AIMCAL. www.convertingschool.com 26 Converting Influence Spring 2011 Meeting: Bordini Ctr., Fox Valley Technical College, Appleton, WI. www.convertinginfluence.com 26 Converting School – Solution Preparation & Mixing: Best Western Inn & Suites, Ontario, CA. AIMCAL. www.convertingschool.com
JUNE 2011
12-15 2011 Intl. Conference on Web Handling: Stillwater, OK. Web Handling Research Ctr. at Oklahoma State University. http://iweb.okstate.edu 16 Vacuum Metallizing & Coating Seminar 2011: Hotel Casa 400, Amsterdam, The Netherlands. Alexander Watson Associates. www.awa-bv.com
16-17 Introduction to Pressure-Sensitive Technology Workshop
2011: Hotel Casa 400, Amsterdam, The Netherlands. Alexander Watson Associates. www.awa-bv.com
20 Multilayer Packaging Films 2011 – Americas: Sheraton Newark Airport, Newark, NJ. Applied Market Information, Ltd. www.amiplastics-na.com
AUGUST 2011
23 Converting School – Web Coating & Drying (Europe): Hotel Mercure-Louvain La Neuve, Brussels, Belgium. AIMCAL. www.convertingschool.com
25 Converting School – Solution Preparation & Mixing (Europe):
Hotel Mercure-Louvain La Neuve, Brussels, Belgium. AIMCAL. www.convertingschool.com
SEPTEMBER 2011
6-8 TLMI Technical Meeting 2011: Swissôtel, Chicago. Tag & Label Mfrs. Institute. www.tlmi.com
12 Specialty Paper Industry Conference 2011: Hyatt Rosemont Hotel, Chicago. Alexander Watson Associates. www.awa-bv.com 26-28 CPP EXPO 2011: Convention Ctr., Las Vegas. H.A. Bruno LLC. www.cppexpo.com Co-located with PACK EXPO Las Vegas 2011. PMMI. www.packexpo.com
aD inDex
AIMCAL.....................................................www.aimcal.org.................................... 34, 73
Applied Materials, Inc................................www.appliedmaterials.com.......................... 1
Appleton Mfg, Division ..............................www.appletonmfg.com .............................. 39
AWA ..........................................................www.awa-bv.com....................................... 65
Badger Plug ..............................................www.badgerplug.com ................................ 57
Bunting Magnetics Co...............................www.buntingmagnetics.com...................... 47
Catbridge Machinery.................................www.catbridge.com ................................... 63
CBC Coating, Inc. .....................................www.cbccoating.com................................. 87
Celplast .....................................................www.celplast.com ...................................... 13
Charter Films.............................................www.charterfilms.com/barrier .................... 25
Comexi North America..............................www.comexigroup.com ............................... 9
CPP Expo..................................................www.cppexpo.com..................................... 84
Dana Films ................................................www.danafilms.com................................... 17
Davis-Standard, LLC.................................www.davis-standard.com ...inside front cover
Dover Flexo Electronics ............................www.dfe.com ............................................... 5 Harper graphic Solutions Division............www.harperimage.com.............................. 47
Henkel Corporation ...................................www.henkelna.com/tapesandlabels .......... 43
Intral ..........................................................www.intralac.com....................................... 23
MedCo Labs..............................................www.medcocoatedproducts.com .............. 87
MidStates Converting, Inc.........................www.msconverting.com............................. 87
Montalvo Corporation, The .......................www.montalvo.com/s4............................... 55
New Era Converting Machinery, Inc. ........www.neweraconverting.com.........back cover
Parkinson Technologies Inc......................www.parkinsontechnologies.com .............. 51
Pearl Technologies ...................................www.pearltechinc.com............................... 29
Pillar Technologies – an ITW Company ...www.pillartech.com.................................... 55
Polymag Tek Inc. ......................................www.polymagtek.com................................ 59
Premier Dies Corporation .........................www.premierdies.com ............................... 77
SAM North America LLC. .........................www.sam-na.com ...................................... 59
Taghleef Industries LLC............................www.ti-films.com............... .inside back cover
thelamco, Inc.............................................www.thelamco.com.................................... 87
Q: What is the best wrap angle
for a load-cell roller?
a: First, we must rephrase the question. There is no such thing as “best,” only “good enough.” The load-cell roller must be wrapped adequately so that an adequate tension signal is produced. Higher wrap angles will not be “better.” In fact, there is even the possibility that higher wrap angles will contribute slightly to wrinkles generated on that roller in marginal situations, just as would any other traction-enhancing effort.
So, how good of a tension signal do we need to size a minimum wrap angle? This is the only judgment required; the rest is pure calculation. Here there is a diversity of opinion. However, for a purely monitoring application, something like the ability to resolve 10 percent of the lightest tension is probably good enough. For controlling a drive, a common recommendation is 5 percent or less of the least tension to be run. A factor to consider here is that load cells are usually the easiest to get precise, so we normally don’t want to use up much of the total allowable error with something that is easy. The bulk of the total allowable error, often stated as a 5-percent maximum tension error in steady state and 10 percent during acceleration, must be allotted to more difficult things such as drive response.
Sure, this sounds a bit techie, but that is what design engineers do, or at least should do.
Calculating the factors
Once you decide how good your load-cell tension signal needs to be, the rest is calculation. You must first go to the load-cell specifications to look up values for things such as accuracy, hysteresis, linearity and repeatability. Normally, linearity or repeatability is the biggest and most limiting of the factors. However, load cells, especially strain-gagebased sensors, can usually resolve better than 0.2 percent of their capacity. Other factors that are needed for the calculation are minimum and maximum web width as well as the weight of the load-cell roller and the assembly to which it might be attached. Geometry is also required, such as the angles corresponding to web entry, web exit, loadcell sensing direction (which need not be either horizontal or vertical) and gravity.
The calculation for sizing the load cell is then “merely” statics (see diagram). First, you size load-cell capacity with a trial wrap angle, say 45 degs just for discussion. The size of the load cell must be the smallest model that will not be overloaded given all of the factors. Second, you backcalculate minimum wrap angle to resolve the minimum tension that you have decided is necessary for the quality required for your particular application using the specs for that cell. If the minimum wrap is less than the trial wrap, and the trial wrap does not overload the cell, you’re done. If not, you adjust the trial design in some way and reiterate until you get closure.
Sure, this sounds a bit techie, but that is what design engineers do, or at least should do. The result varies enormously. For board or metal, only a few degs are usually needed. For typical paper and film applications, a few tens of degs are often enough. However, for products such as tissue, you might have to use every “trick” and pull 180 deg up on a carbon-fiber roller.
How do you know if the machine designer has done this homework? The most direct is to simply ask or insist on the calculations and calibration procedures. However, there are clues that the designer might be just guessing instead of designing. The first would be the absence of a quality statement, such as resolving 5 percent of the least tension. A second might be a “one-size-fits-all” generic recommendation for wrap angle. Another might be round numbers such a 30, 45, 90 or 120 degs. n
David R. Roisum, Ph.D. Consulting Technical Editor 920-312-8466 drroisum@aol.com www.roisum.com
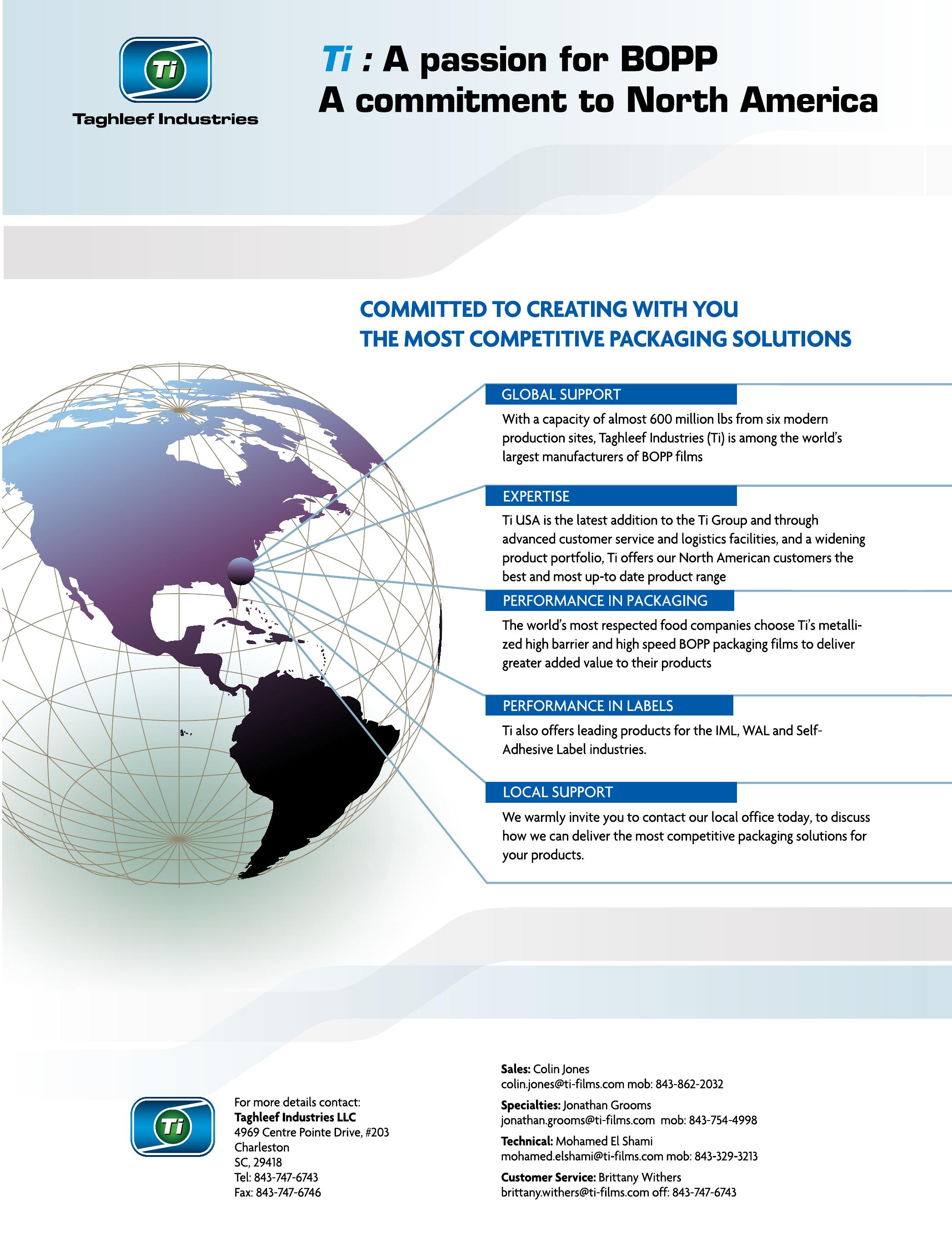
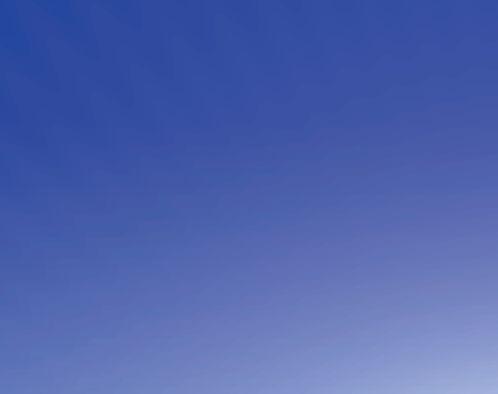
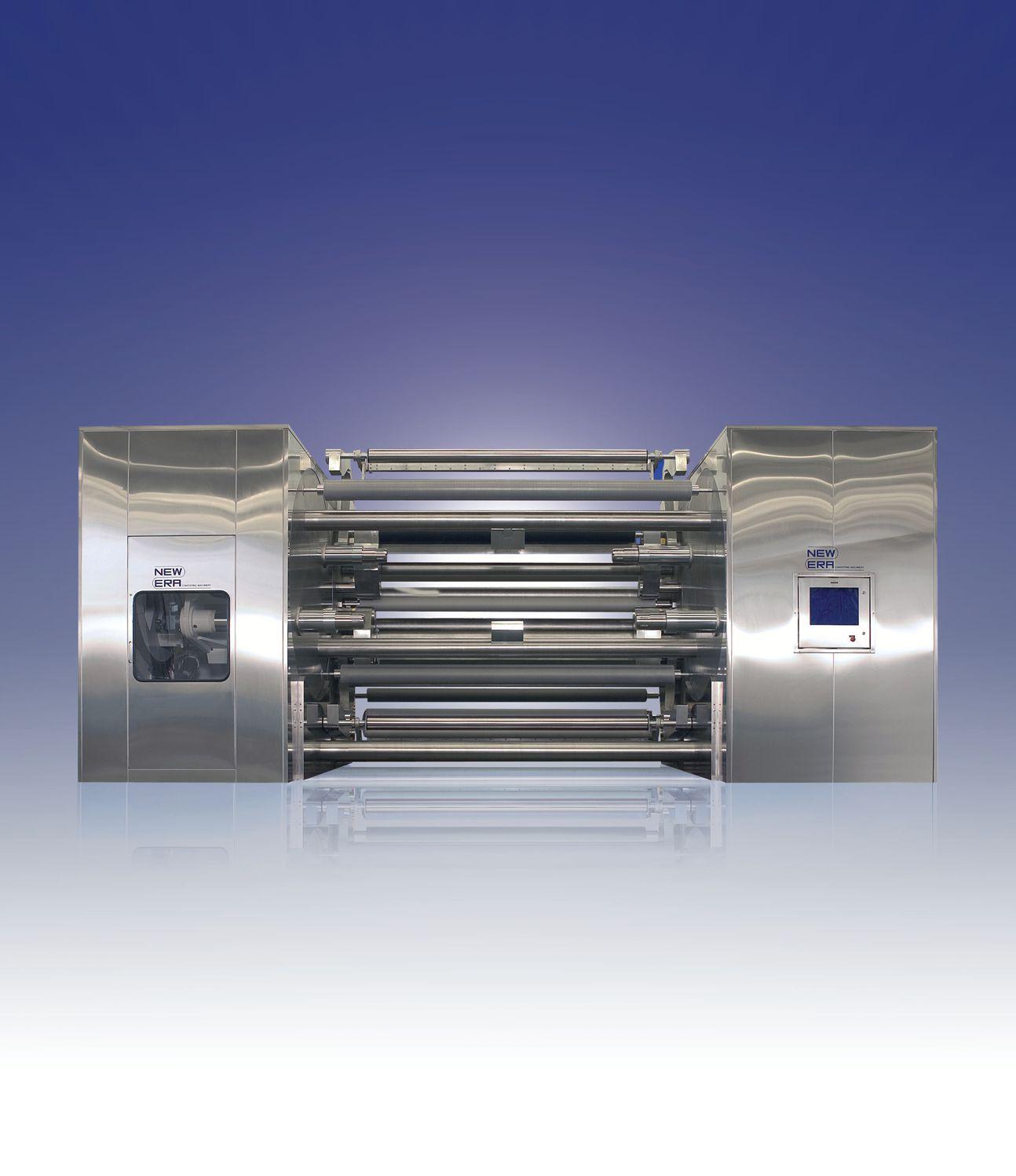