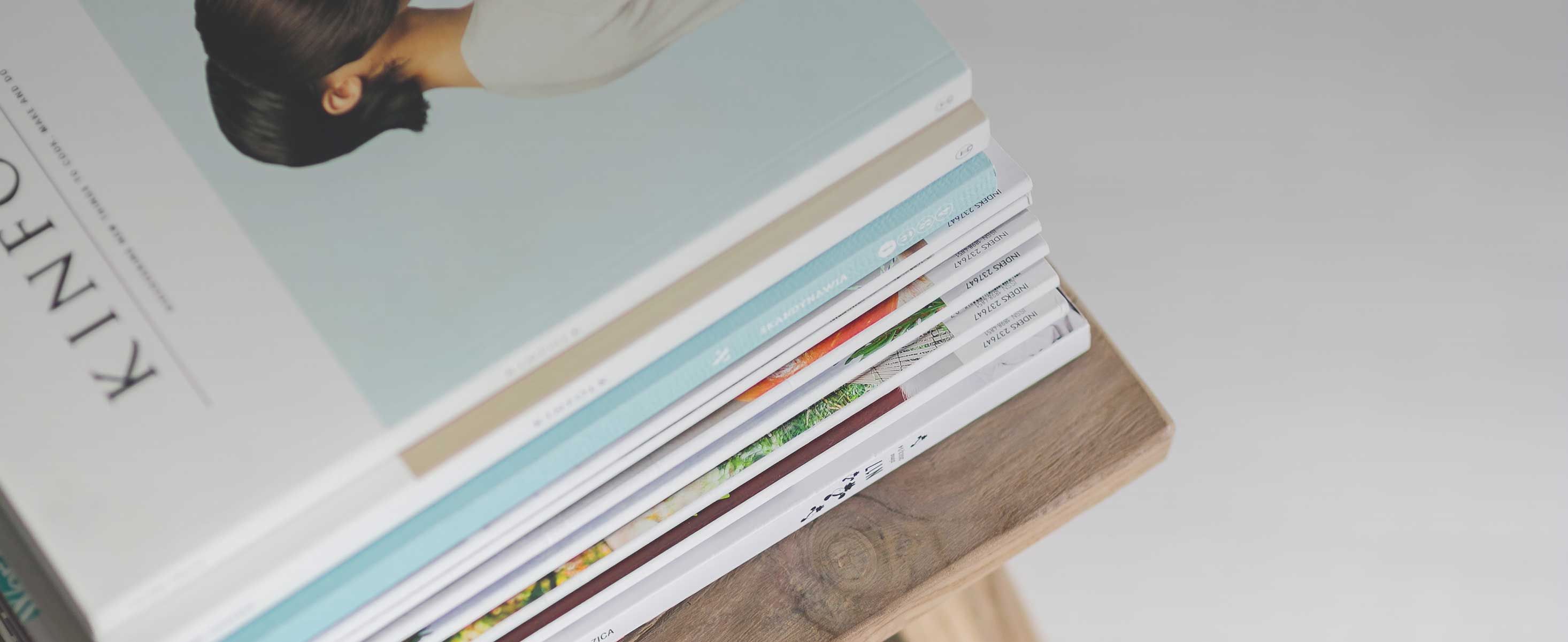
1 minute read
College of Engineering
David Hanna
College of Engineering
Advertisement
Mechanical Engineering
Faculty Mentor: Dr. Ajmal Yousuff
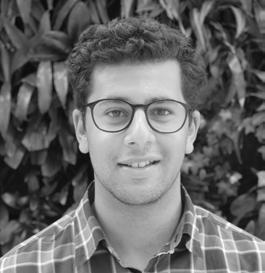
Mechanical Engineering & Mechanics
Translation of Vectoring Thrust on a Movable Platform
Quadcopters are used more every day, and the development of new technologies are essential for the broadening market. Most quadcopters have standard yaw, pitch, and roll features which move the entire vehicle to the desired location. The vehicle itself will tilt in the direction of the movement by leaning left, right, forward, and backwards. Dr. Yousuff and his students have developed new rotor groups to place on quadcopters that would allow the vehicle to turn in any direction without a complete shift of the entire body. These rotors will give the quadcopter the ability to hover in any orientation. Before flying, a testing platform was required to safely demonstrate the outstanding capabilities of the new rotor groups. I designed and constructed a movable semi-frictionless platform that has the ability to slide in two coordinate planes. A custom-made mount for the rotor can be easily attached to the platform, and the thrust provided from the propeller will be converted into movement along both axis. This platform will be used to test each rotor individually as well as the full quadcopter. It can be used to translate movement from any type of mountable thrust machine, and will be used for years to come.
College of Engineering
Sanjog Karki
College of Engineering
Mechanical Engineering
Faculty Mentor: Dr. Ajmal Yousuff
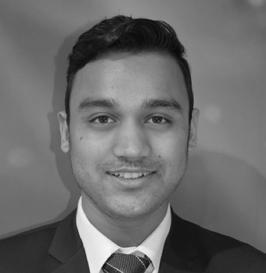
Mechanical Engineering & Mechanics
Compressed CO2 Thruster and Low-Friction Platform to Study the Dynamics of Docking in CubeSats
CubeSats are a class of nanosatellites originally developed in 1999 for education and space exploration. The standard CubeSat size uses 1U (one unit) measuring 10x10x10cms and typically weighs less than 1.33kg. Recent researches are focused on docking CubeSats in space to enable in-orbit assembly of larger structures like space telescopes or solar panels. Synchronizing position and attitude and maintaining relative speed are the major concerns for docking two CubeSats in space. Failure to precisely control speed, position, and attitude could result in collision of the CubeSats. This research focuses on creating an assembly to study the impact of contact between the chaser and the target CubeSats during docking maneuver. A low friction platform was crafted using laser-cut light weight wooden plank on top of lubricated ball bearings. The thruster, assembly of compressed CO2 cartridge and two electric solenoid valves, was placed atop the platform keeping the center of gravity at the center of the platform. The thrusters, controlled by an infrared remote programmed using Arduino, created thrust in two directions: forward and lateral. Using this assembly, researchers can study the dynamics of CubeSats in two-dimension.