
4 minute read
Complete welding automation solutions Easy programming, maximized profit
Technology Easy programming, maximized profit
COMPLETE WELDING AUTOMATION SOLUTIONS
Tough competition in the heavy fabrication industry forces companies to continuously rethink their production and implement new techniques to boost competitiveness. Robotic welding solutions respond to rapidly developing market demands, bring more productivity, and enable dynamic manufacturing.
During the last decade, investing in a complete robotic welding solution has become more common within the heavy fabrication industry. There are various reasons behind the increasing interest in robotic welding, such as flexibility, better capacity, and user-friendly programming. These benefits ensure maximum efficiency even in high-mix low-volume production.
Whether we are talking about one-off production or mass production, the anatomy of a robotic welding solution typically includes the same elements: handling equipment, half portal (with one to three linear axis), a software system for programming, and control system to manage the welding station. The control system includes features, such as welding process analysis, safety alarms, and machine life-cycle notifications.
Each unit of the complete solution, such as handling equipment, welding process or the software system used, is analyzed and selected according to production requirements and customer needs.
Modular handling solutions
Efficient, precise and reliable handling equipment is the foundation for highquality robotic welding. When the robotic welding cell includes an external axis and a workpiece positioner, the cell can be optimized to match with both current as well as future needs in the production.
The reachability and weldability can be simulated beforehand, thanks to 3D-modeling and simulation software. If there is a need for changing the geometries in the workpiece for better reachability or weldability - so the robot can do its job - it can be done well ahead of time.
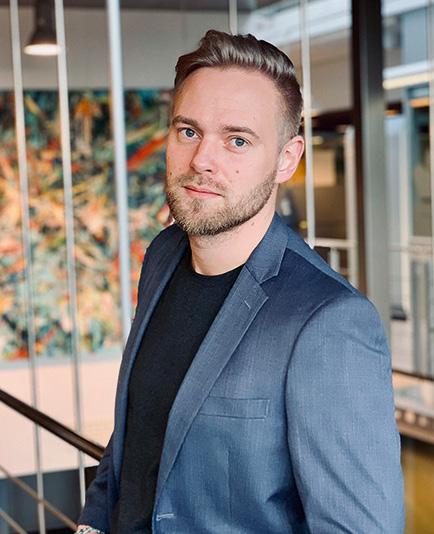
Robotic Manager, Automation and Robotics
About the author: Teemu Rusi
Contact: teemu.rusi@pemamek.com
15 years of experience from production automation in different industry sectors globally. Teemu has strong skills in industrial robotics whether if it’s programming, offline programming, simulation or layout design.
5 steps towards a successful implementation of robotic welding solution:
1. Thorough pre-design together with the supplier and purchaser.
2. Possible design changes in the products for example changing groove geometry or groove preparation method.
3. Welding process evaluation and modification into robotic welding.
4. Tailored and thorough training for all the participants.
Teemu’s Top skills: • Sales-oriented mindset • Designing complete robotic solutions • Manufacturing process evaluation design
5. Good level of maintenance and follow up together with the supplier.
The right fit for high-mix low-volume production
High-mix low-volume production, which refers to the manufacturing of variety of products in smaller quantities, is becoming more common due to its ability to adapt to specific customer demands and productional changes. Enabled by robotic welding solutions, profitable high-mix low-volume production is one of the greatest advancements in welding automation.
The features that make robotic solutions a perfect match for high-mix, lowvolume production are the modern features that enable flexible production, but also modularity. Advanced robotic solutions with efficient offline programming and thorough simulation of dimensions can be optimized to one’s production and furthermore, they are easy to control.
Easy programming with PEMA WeldControl 300
Robotic welding enables high-quality results and increases productivity. What sometimes makes companies hesitant to start, is the thought that programming and controlling a robot would be challenging and complex.
Designed and developed in-house, PEMA WeldControl 300 is one of the most advanced robot programming systems available in the markets. The software family is designed to meet the needs of heavy welding automation; it is fast,
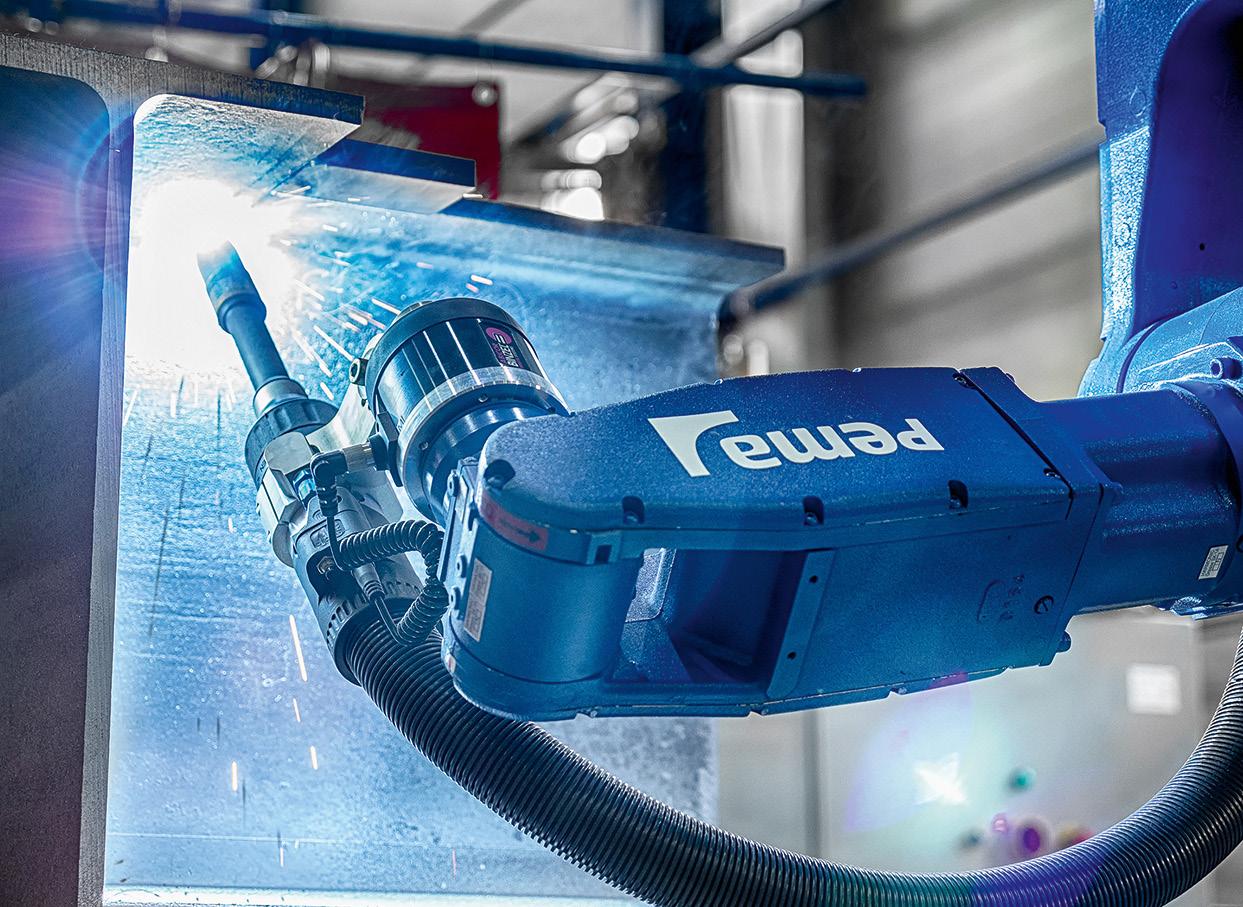
Solutions can be utilized 24/7, 8760 hours a year.
Each unit of a complete welding solution is analysed and selected according to production requirements and customer needs.
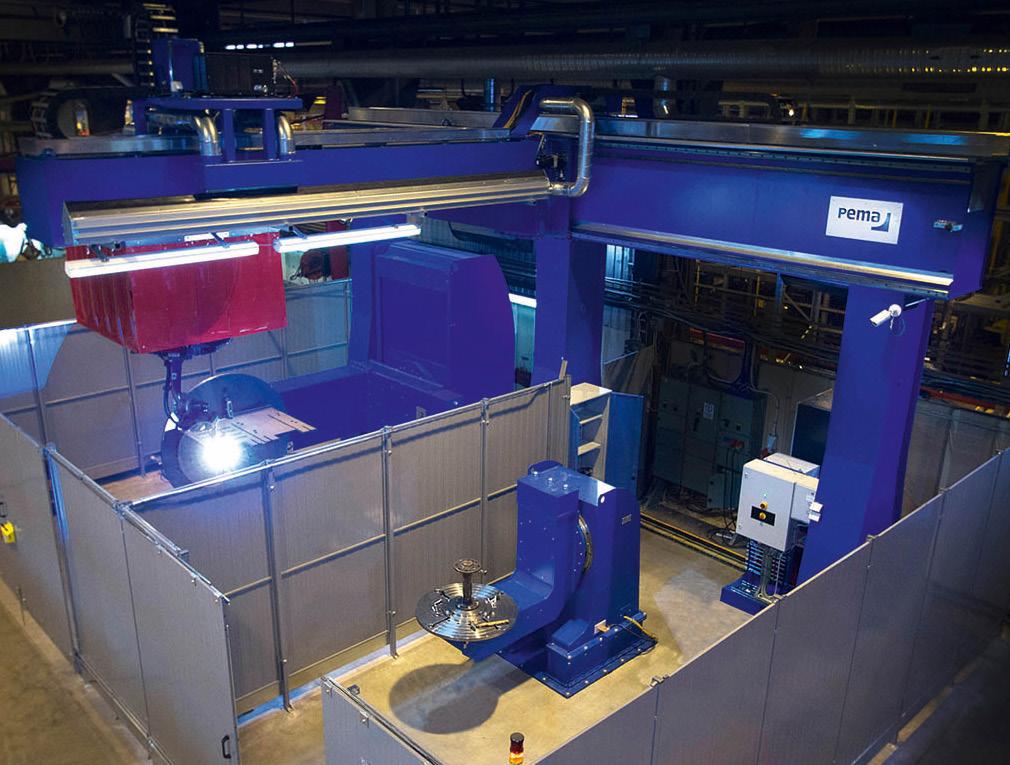
efficient, and can be applied to almost any production. With its three different software levels, OFFLINE, CREATE and SCAN, even programming one-off production can be completed rapidly without any manufacturing interruptions.
Modern features, such as automatically-generated welding paths, visual multilayer tools, mirror, and copy features, make programming easy and efficient, enabling the welder to become the operator.
PEMA WeldControl 300 OFFLINE -software is based on 3D-CAD-based offline programming. It enables programming of the next workpiece, while simultaneously welding another one, which results up to 10 times faster programming compared to online programming solutions. Above all, the software is designed to be easy to use, functional and fast.
Benefits of complete solutions:
- Reliable pre-analysis: Virtual modelling of the robotic solution with 3D and simulation
- Typically reached automation rate 50-80%
- Deposit rates up to 9 kg per automatic program running hour with only one MIG/MAG torch
- The solution can be utilized 24/7 and 8760h/year