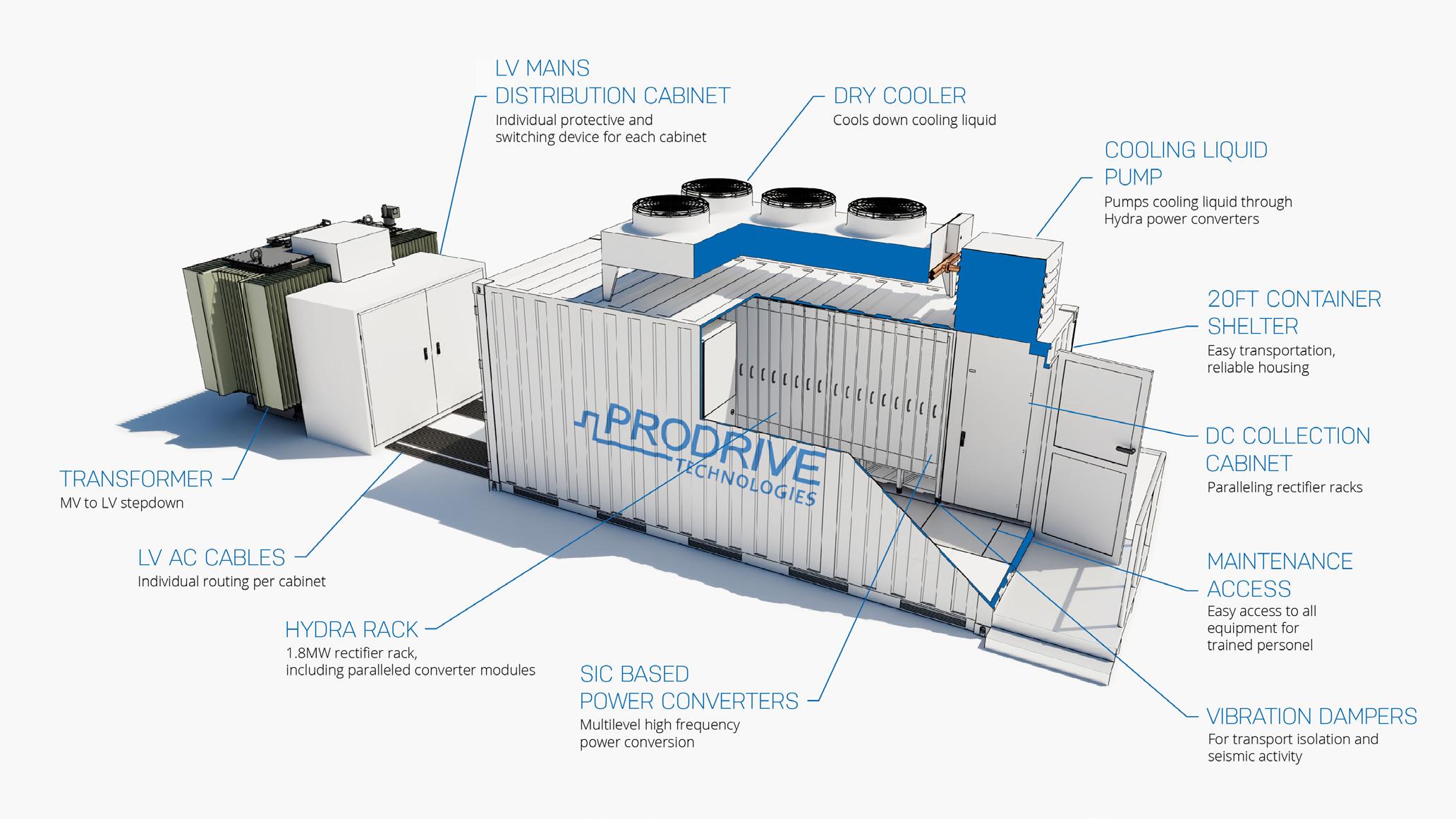
3 minute read
SCALABLE BULK RECTIFIER
from HIL Issue 09
HYDRA: PROVIDING A SCALABLE BULK RECTIFIER FOR GREEN HYDROGEN PRODUCTION
Scalability is one of the hottest topics in the hydrogen sector as we establish the supply chain around how hydrogen will be produced, stored and distributed. Focusing on R&D and future-proofing are often at the heart of unlocking this potential, and Prodrive Technologies have utilised this through its Hydra scalable bulk rectifier for green hydrogen production.
Advertisement
Working together with trusted partners, Prodrive Technologies has developed the Hydra rectifier system, featuring its SiCbased unique power converter technology. This provides an efficient and scalable solution for electrolyser manufacturers that is easily integrated and can be scaled up as a repeatable unit up to GW-scale capacity.
Silicon Carbide-based converters improve efficiency, as well as AC and DC current quality, without the need for external filters. The input can be connected to any medium-voltage AC by varying the MV to LV stepdown transformer, keeping the rest of the system standardised. The output supplies the DC voltage and current that the OEM or stack builder requires for their specific stack design. The Hydra is designed to inherently comply with grid codes, so external filters and compensation banks for incoming current are not needed.
The Hydra rectifier cabinets can be integrated into a containerised solution or on a skid, depending on customer requirements. The solution includes its own closed-loop liquid cooling system. The integrated solution is designed to maximise uptime by minimising maintenance. This allows green power to be utilised 24/7, whenever it is available and reduces ongoing costs compared to air-cooled solutions.
R&D is integral to scalability of green hydrogen production
Starting off by explaining how R&D is essential, Wouter van Gennip, Commercial Director at Prodrive Technologies, said: “We hire around 2500 people, with over 50 per cent of the workforce working on research and development. This means we are developing the projects rather than only manufacturing them. Putting ourselves at the heart of projects allows us to be at the forefront of the innovation behind scaling up hydrogen production.”
Focussing on how the unique power converter technology provides a more efficient and scalable solution, Wouter explained: “The core aspect to scalability is modularity. For us, we are using a 200 kW module that is in a rack, which can be combined into a containerised solution and scaled from there up to GW scale.
Hydra offers standardisation and dynamic range
For Wouter, the two keywords around scalability include standardisation and dynamic range: “Considering both these aspects allows for our equipment to be used anywhere, mainly across the US and Europe for now, and progress towards the equator.”
Different regions naturally have varying grid and environmental conditions, so in order to be scalable, you need a solution, such as the Hydra system, that can deal with unique conditions. Another factor to consider is that the mid-voltage each region has is converted to an input voltage that the equipment can handle.
Wouter expanded on this: “we have the flexibility within the transformer, which is easy to handle. Our system can solve this, which allows us to expand with the standardised system in mind.”
Scalability is an essential aspect of delivering more capacity, but Wouter also told Hydrogen Industry Leaders: “future-proofing is just as important. The voltage for stacks is currently sporadic in a range from 50 volts to 1500 volts. A lot of companies are around 400-600 volts which are fine for now but taking into account the lifetime of the project and the lifetime of the stacks; they typically won’t overlap very well.”
The sector must plan for more efficiency by 2030
With all the innovation going on, it is expected that the stack efficiency will be dramatically improved by the time the lifecycle of current stacks comes to an end. This means that by 2030 you won’t be replacing stacks like for like, so the system has to be adaptable to this today for implementation in the future.
Prodrive Technologies have flexibility on the mid-voltage side of things and the different stacks the system can handle, which uniquely positions the Hydra project above others. “We can easily scale to the right size of the customers’ needs today, but also upgradable to what they will need in the future,” Wouter added.
Expanding on the efficiency angle, the Hydra doesn’t require the use of filters, something which hampers efficiency between 1-2% ordinarily. Finally, Wouter said: “Operating at low total harmonic distortion helps with efficiency, and this offers a sum of efficiency that is considerably higher than other products. For example, at 1200Vdc, we are now at a peak efficiency of 98.4% grid-to-stack, which includes the transformer, the rectifier and the whole chain involved.”