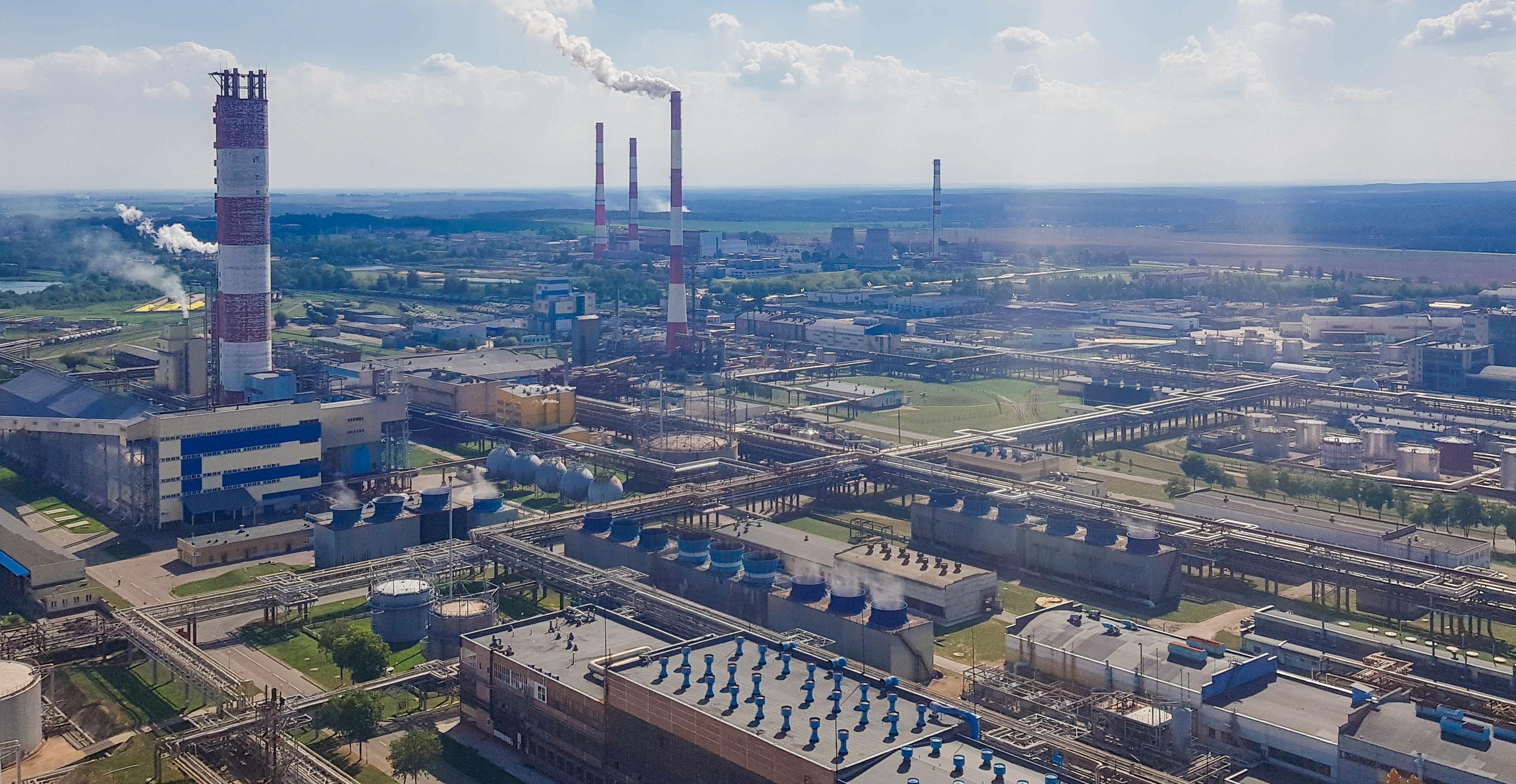
3 minute read
AMMONIA CRACKING
from HIL Issue 13
How Ammonia Cracking Could Produce 1 Million Tons Of Hydrogen
by Hannah Wintle
Advertisement
The prospect of an industrial ammonia cracking plant has been deemed a feasible method for large-scale hydrogen production, according to a recent study.
A total of 18 parties, including the Port of Rotterdam, Air Liquide, bp, Shell, RWE, and Uniper, commissioned leading engineering and construction firm Fluor to perform a pre-feasibility study into the concept.
The study concluded that the technology required to safely convert ammonia into hydrogen is available today through a multistage approach, and offered insight into both centralised and decentralised options.
Ammonia, which is a more stable method of transporting hydrogen, would arrive at the plant where it will be converted back into hydrogen through an endothermic equilibrium reaction requiring an external heat supply.
Producing 1 million tons of hydrogen per year, equivalent to approximately 3000 tons per day, would result in an approximate consumption of 20,000 tons of ammonia per day.
With the ongoing global efforts to decarbonise and meet emissions targets, the prospect of producing such a quantity of hydrogen is encouraging. 1 million tons of green hydrogen per year could reduce CO2 emissions by about 10 million tons, according to the Port of Rotterdam.
Furthermore, thanks to designs based on the exclusive use of carbon-free fuel, the plant would produce no CO2 emissions.
Centralised or decentralised?
Three plausible options for ammonia cracking were provided by the report, two of which were centralised, meaning the cracking would happen in one location, and one decentralised option which necessitates multiple locations and cracking facilities.
Of the two centralised options suggested, the only difference was in their ammonia offloading and storage solutions, one demonstrating that six locations could be utilised while the other includes storage at the cracking location.
A final option would consist of six decentralised ammonia cracker plant locations, each with its own ammonia offloading and storage facilities.
Despite asserting that the cost is considered roughly equal for centralised and decentralised options, the report alluded to the capital cost advantages to building a centralised plant with offloading and storage solutions at the same location. Currently, there isn’t much of cost discrepancy between cracking ammonia in multiple process trains at different locations, or in the same number of trains at one location.
However, due to advances in technology, a larger amount of ammonia can be cracked in one train, which in turn reduces the amount of process trains required.
This directly benefits the concept of having one central facility, as the increased levels of production would cause a proportionate saving in costs.
Ultimately, despite the substantial investment required to fund a large-scale industrial ammonia cracker, the report found that 80-90% of the cost of H2 production is due to the cost of ammonia feedstock.
The Port of Rotterdam will host the facility
In its investigations, the study explored the Port of Rotterdam as a base for the facility including storage, conservatively estimating the space requirement for the one million tons of hydrogen capacity to fall between 200,000m2 and 450,000m2 Safety considerations were largely resolved by previous studies commissioned by the Port of Rotterdam, which have determined that large amounts of ammonia can be imported, stored, and transported within the safety contours of the port.
Additionally, companies in the Harbour Industrial Complex (HIC) are experienced and skilled in their handling of various chemicals and dangerous goods.
Ammonia cracking is already gaining momentum throughout Europe
For Air Liquide, this venture would be the latest in their portfolio of similar projects. Earlier this year, the French industrial gas supplier announced the construction of an industrial-scale, ammonia cracking plant at the Port of Antwerp. Operations at the plant are projected to begin in 2024.
At the time, Executive Vice President Michael J. Graff said: “More than ever, the Group is committed to making hydrogen a key element of the fight against climate change, in particular for the decarbonization of heavy industry and mobility.”
In Germany, Aramco and Linde Engineering jointly announced plans to develop their own ammonia cracking technology. Based on a new catalyst developed by Aramco and the King Abdullah University of Science and Technology, the ammonia cracking technology will be followed by a demonstration plant in northern Germany. Moreover, UK-based company AFC energy, a leading provider in fuel cell technology, recently announced a new ammonia cracking technology platform, with the hope of also overcoming challenges relating to hydrogen generation, storage, and transport.
Their cracker technology was accelerated in response to an increase in ammonia imports to Europe, in conjunction with the increasing need for the UK to address energy independence challenges arising out of the war in Ukraine.