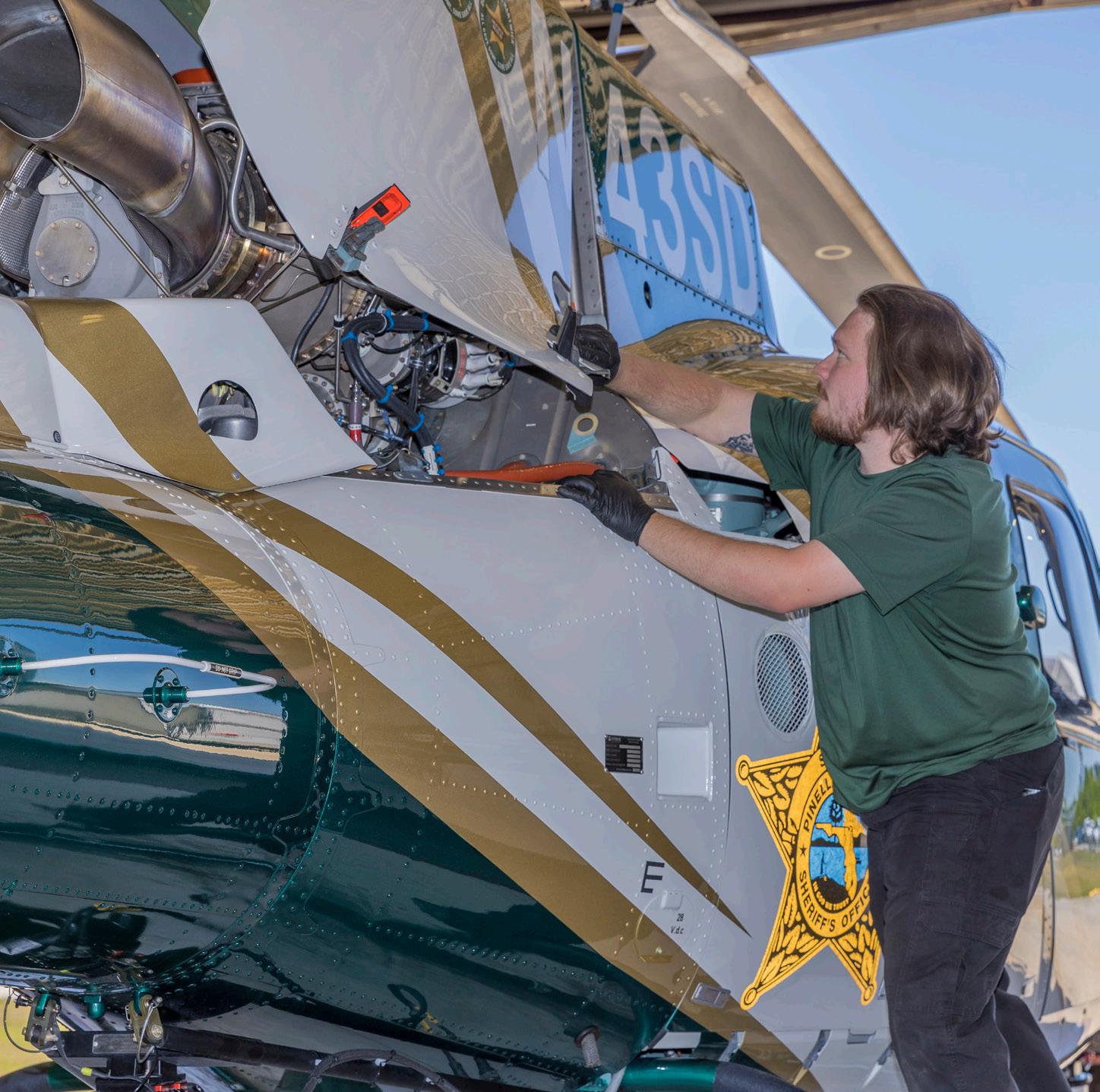
5 minute read
SPOTLIGHT Flight Mechanics Keep Our Eagle in the Air
BY LAURA L. SULLIVAN
If your car fails because of a lack of routine maintenance you might get stuck on the side of US 19. If your helicopter fails mid-flight, it’s another story entirely. Flight maintenance supervisor Brian Egnatuk, and flight mechanics Charles Galloza and Joshua Wells are responsible for the perpetual cycle of frequent inspections and repairs that keep our helicopters ready to support our deputies on the road.
Advertisement
There’s a reason the Pinellas County Sheriff’s Office (PCSO) has three helicopters – that’s the only way to make sure one is always available if a deputy needs air support. Their strict maintenance schedule can keep them out of commission for days or weeks at a time. “Typically we like to keep one aircraft as the duty aircraft,” Galloza said. “When you start flying two at the same time, or even on rare occasions three, you start running into inspection times colliding, and then you can end up having no aircraft available.” It takes a lot of planning to time the flight hours and repairs just the right way to ensure there’s always an aircraft ready.
Although it can vary, on a typical day a helicopter might be in the air for a total of four to six hours between day and night shifts. Mechanics check the helicopter every day in the morning, looking over the general condition, making sure nothing is leaking. “Then when the flight crew comes they look it over too,” Galloza said. “They have a checklist.” The helicopters undergo an inspection every week after 30 hours of flight time. That inspection is fairly quick, but the 100-hour inspection takes a day or two.
The next level, which takes place after 150 hours of flight time, takes about a week.
“Our typical inspection is the 150,” Galloza said. “We clean the filters, change the oil in the tail rotor gear box. It’s just a little more in-depth maintenance – we’re taking things apart, greasing bearings, blade pins.”
The 600 hour inspection is even more intense. The landing gear is removed and inspected, and the whole rotor head and tail rotor are taken apart. The engine or gear box may be sent out for overhaul. As FAA mechanics they have the know-how to do those overhauls themselves but, “When it comes to component overhauls we send that out because they have all the tooling, they have the way to test it once they put it back in.”
When the 600 hour inspection is in progress, “It looks like a different aircraft,” Wells said. “All the panels are gone.” This level of inspection and maintenance takes a couple of months. That’s a long time for a helicopter to be out of commission – which is why it is so vital that the PCSO has three helicopters. We provide law enforcement aviation support for the entire county so there always has to be a helicopter ready to take off at a moment’s notice.
Minor leaks are a common issue. “You can fly with some things leaking,” Galloza said. While that might not sound very reassuring, he says they never even get close to the level of leaks the manufacturer allows.

If a pilot reports a leak and the mechanics say they’ll take care of it, the pilots never tend to follow up. However, one repair job leads to constant queries. “In their preflight the pilots might miss something that would be obvious to a mechanic, but one thing they always catch is when the air conditioner doesn’t work. If the blower isn’t 100 percent, they report it. It’s not the most common problem, but it is definitely the thing they complain loudest about.” And no, the helicopter doesn’t get grounded for a broken air conditioner, even in the middle of August.
PCSO flight mechanics check everything so thoroughly because a failure could be catastrophic. Some things are very bad: “If you had an issue with the tail rotor at a certain speed they may be able to control it.” If you’re hovering and the tail rotor goes out the helicopter would start spinning in a circle, but there are maneuvers and techniques to possibly get out of that, with a lot of luck. Other things are disastrous: “An absolute catastrophic failure would be with a pitch change link in the blade. There are three of them and they work in unison. If one of those was to shear off then one blade would fly out of track and either create too much or not enough lift. The aircraft would go into a roll. There’s really no recovering from that because your whole movement is based on that rotor head.”
The rigorous maintenance schedule and the unit’s emphasis on safety will make sure that nothing preventable goes wrong with the helicopters. Everything is inspected on schedule, and some components are replaced after a certain length of time even if they appear to be in perfect shape. The twelve pieces that hold the rotor head on, for example, are changed every 3,000 flight hours even if they still look brand new. Tools are calibrated every year and anything that expired is disposed of. Everything needs to be documented, even if it is just a filter or a lightbulb change. Galloza has been handling a lot of the paperwork lately. Wells, being newer, has been spared the worst of it.
Wells went through aviation school and then worked at a flight school before joining the PCSO. “I love it here… because I don’t have to do paperwork yet!” he joked. He always wanted to work on helicopters. “This is where I wanted to end up, working on an Airbus helicopter. I just think they’re fun to work on.” He considers himself lucky to be working with such knowledgeable professionals as Egnatuk and Galloza. “These guys know a lot, especially our supervisor, he’s been doing it for 30 years. It’s just crazy how much these guys know and how much I get to learn.”
“I always wanted to do avionics,” Galloza said, referring to the electrical components of the helicopter. He worked on planes at various places, including commercial airlines, but reached a point where he thought he wanted to get out of aviation so he applied with the PCSO as an automotive mechanic in 2014. Luckily they needed someone with an electrical background, and he started out in Fleet, doing installs for the Tahoes. “It wasn’t avionics, but at least it was electrical work.” Later he checked out the Flight Unit and made the move there in 2018. “I always wanted to work with helicopters but it’s hard to get those jobs.”
Galloza now gets to work on the avionics, just as he always hoped. “It took me a little while to get the blessing from the director of maintenance,” he said. “Our director has to answer for what we do, so he has to make sure we’re spooled up and okay before he can set us free.” Also, Egnatuk enjoys working with avionics himself, and there’s always a little competition for the most enjoyable work.
Some of the tasks are fun, others not so much. “I’m not a big fan of doing corrosion,” Wells said. With a hot humid climate and a hangar right next to the salty air of the bay, they fight a constant battle against the elements. The helicopters get frequent engine rinses with distilled water, and they get a wash every 150 flight hours with a special soap.
“We’re a repair station, so the FAA could come out at any time and look at our work orders,” Galloza said. “They come once a year for a surprise visit. Being a repair station makes us more transparent. We’ve always had the culture of taking pride in our work.”
BY JUSTIN WALSH, FITNESS SPECIALIST
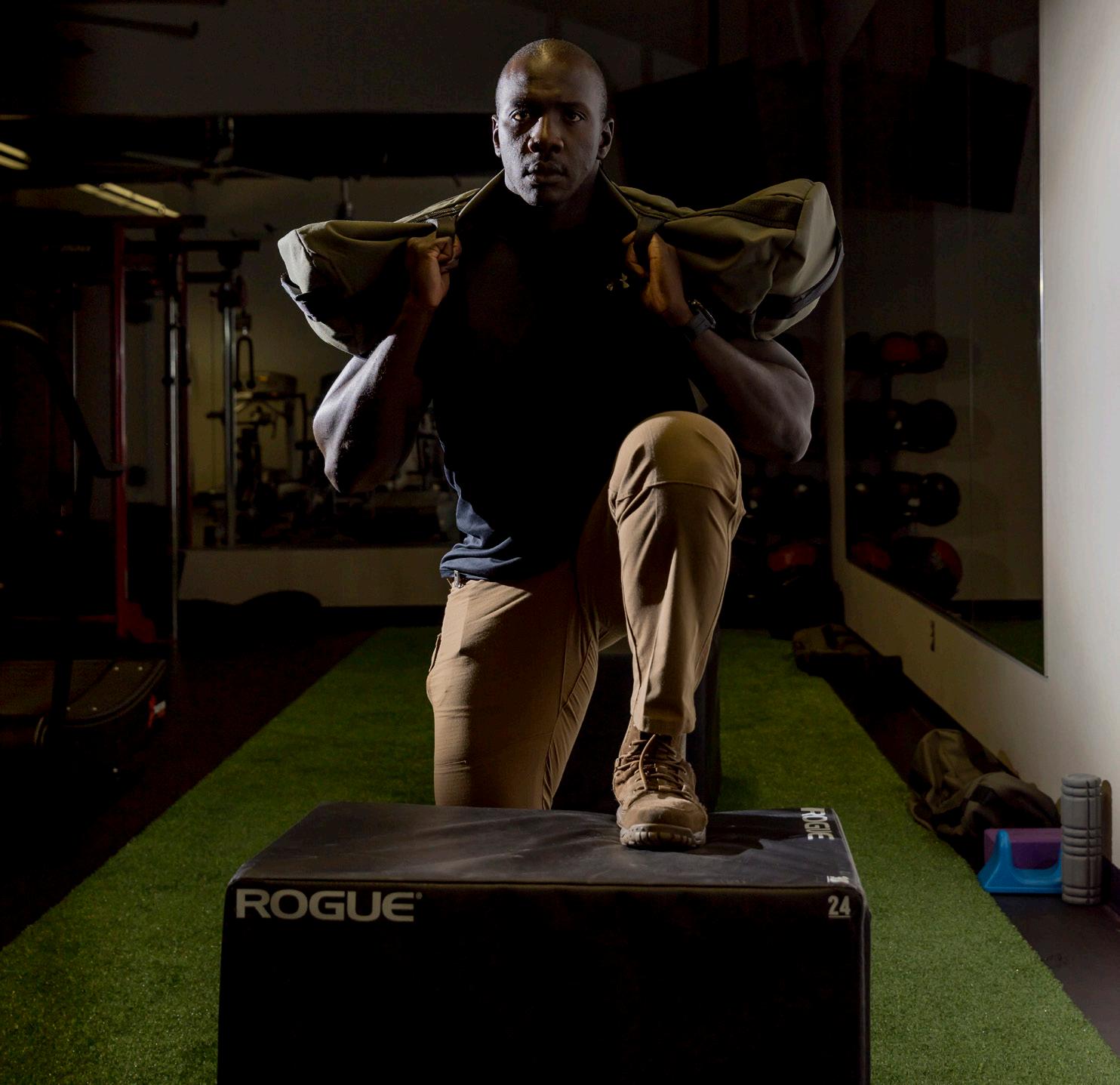