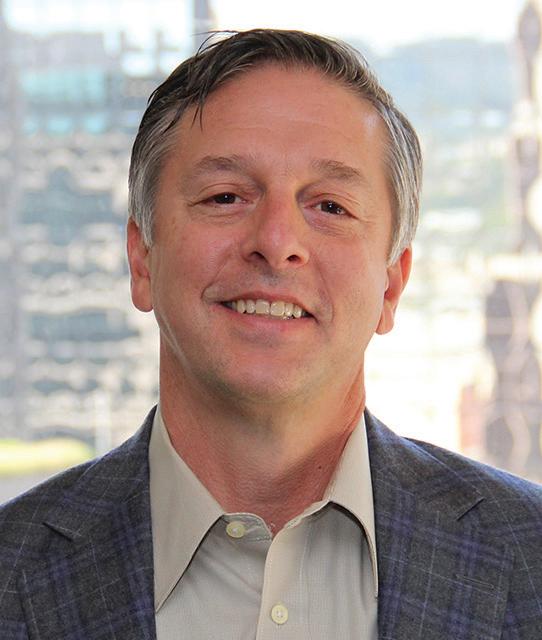
3 minute read
Legal Ease
Material cost increases, delays and lack of availability due to supply chain issues and other inflationary pressures continue to plague the construction industry. I gave a presentation on these topics in February at the National Association of Homebuilders’ International Builders’ Show in Las Vegas. If you missed that presentation, here are some suggestions for managing the risks of material cost increases, delays and availability issues. Who bears the risk of material cost increases is typically spelled out in the construction contract. For instance, where the parties enter into a so-called “lump sum” contract with a fixed price, the general contractor generally bears the risk of material costs increases over and above the lump sum price. Conversely, where the parties enter into a so-called “cost plus” contract pursuant to which the owner pays for the materials plus a contractor’s fee, the owner typically bears the risk of material costs increases. If an owner is hesitant to agree to a cost plus contract, the parties have the option of agreeing to a guaranteed maximum price (“GMP”) where the contractor bears the risk of cost increases over the GMP. Contractors can also include contingencies and/or allowances in their bids and budgets for materials whose costs are volatile. For instance, a lump sum bid or cost-plus budget can exclude certain materials, listing those as separate line items the costs of which will be determined if/when those materials become necessary, thereby allowing the parties to account for any interim cost increases. Alternatively, contractors can refuse to agree to a lump sum price at the time of contracting, choosing instead to set the final contract price at a date closer to commencement, such as the date the permit is issued.
Regardless of the type of contract, parties can also include a so-called “escalation clause” in the contract, which places the owner on notice that there may be material cost increases outside of the contractor’s control that the owner will be responsible for. Typically, such provisions require the contractor to notify the owner of such cost increases and the parties to execute a change order to account for the increased costs.
Advertisement
Where the parties are not only concerned about material cost increases but also material availability, a contract can include a provision allowing the contractor to substitute comparable materials in order to avoid increased costs or project delays due to issues with the originally specified materials. Of course, where a party requires the use of a specific material, that party should generally bear the risk of cost increases, delays and lack of availability of that material.
I also recommend that contractors establish relationships with material suppliers and base their bids and budgets on firm bids from their suppliers to ensure a steady supply of materials at a known cost. Similarly, contractors should get firm bids from their subcontractors upon which to base their bids and budgets and to enter into subcontracts as soon as possible after the prime contract is signed in order to avoid unexpected subcontractor cost increases and availability issues.
Contractors can also order products in bulk and/or store them on and/or offsite and may even require that the owner pay for storage costs, although contractors should be aware that materials stored offsite may not be covered by insurance and/or subject to lien in certain instances. Contractors building spec homes can also list homes as close as possible to completion, as opposed to commencement, in order to recoup increased material costs.
A contract can include a termination provision allowing one or both parties to terminate the contract in the event of unexpected material cost increases, delays or lack of availability. Even in the absence of such a provision, a party may be able to argue that a significant cost increase renders a project financially unfeasible or impractical and seek to terminate on that basis alone. Unfortunately, these arguments face an uphill battle if based merely on increased costs, unless the increase is attributable to force majeure or similar unexpected event outside of the parties’ control, like the COVID pandemic.
A general contractor can also try to shift some or all of the risk of material cost increases and delays to its subcontractors by entering into so-called “turnkey” subcontracts wherein the subcontractors supply both labor and materials. Of course, subcontractors face the same risk of cost increases as general contractors do and, therefore, can demand cost-plus subcontracts, impose GMP’s, as well as include escalation and/or substitution clauses in their subcontracts.
Finally, there is simply no good substitute for candid conversations about project issues, especially significant cost increases. As such, the sooner an owner is made aware of unexpected material cost increases the better. Owners are more likely to be receptive to paying or at least sharing in an unexpected material cost increase when the contractor timely communicates about the issue, especially when the owner understands that the contractor has little/no control this issue, which impacts the industry as a whole and not just one specific project.
In summary, material cost increases, delays and lack of availability affect the entire construction industry. As such, parties should be proactive in addressing these issues before they become a significant problem and cause an otherwise great project to turn into a distressed project. As always, contractors who are considering making changes to their contracts to address cost increases and/or other such issues should consult with experienced legal counsel.
Bill Joseph is a partner at Portland law firm Dunn Carney, LLP and the leader of the firm’s Construction & Design Team. He also serves as the HBA’s general counsel. His practice focuses on business litigation and transactional law with a specific emphasis on helping those in construction and related industries.