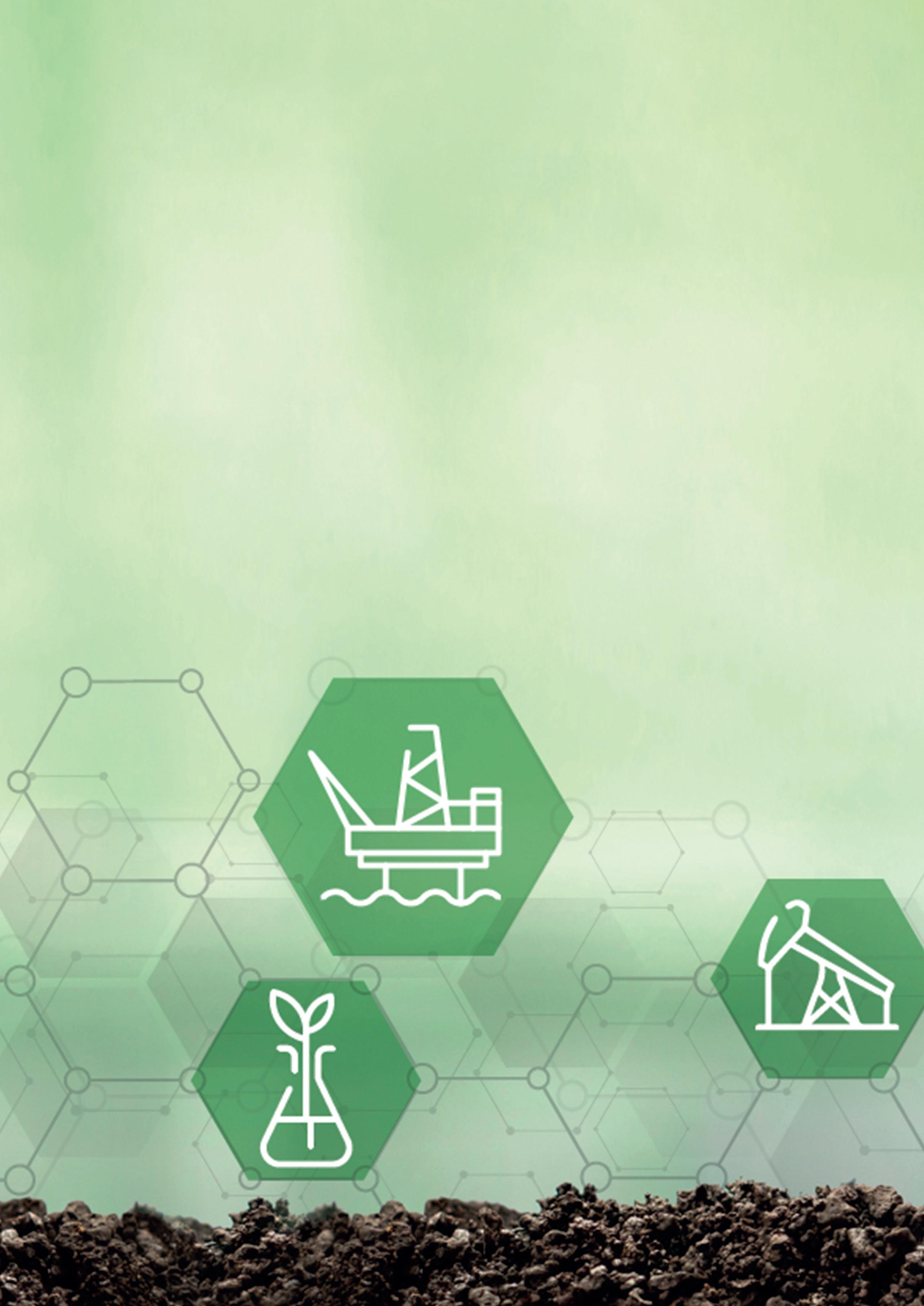
9 minute read
Future-proofing our pipelines
Jonathan Wylde, Global Head of Innovation, and Nihal Obeyesekere, Head of Global Innovation Integrity Management, both at Clariant Oil and Mining Services, have been developing a range of new corrosion inhibitors for deepwater applications, with a particular focus on sustainability. In this interview, they tell World Pipelines about the challenges of sustainably preventing oilfield corrosion, their recent work, and the solutions they have discovered so far.
What are the challenges that you are addressing with your work? To meet rising worldwide energy demand, the petroleum industry has increasingly turned to oil reserves in difficult-toaccess locations, such as subsea and deepwater environments. The harsh conditions in these environments present several challenges for oil and gas producers – most notably high salinity, high shear, high temperature, and high pressure. As a result, it is imperative to develop umbilical deliverable corrosion inhibitors that are designed specifically to withstand these conditions and to maximise the lifetime and safety of the components. We have also seen an increased demand for environmentally acceptable corrosion inhibitors, which is in line with our own, and Clariant’s, prioritisation of
Jonathan Wylde
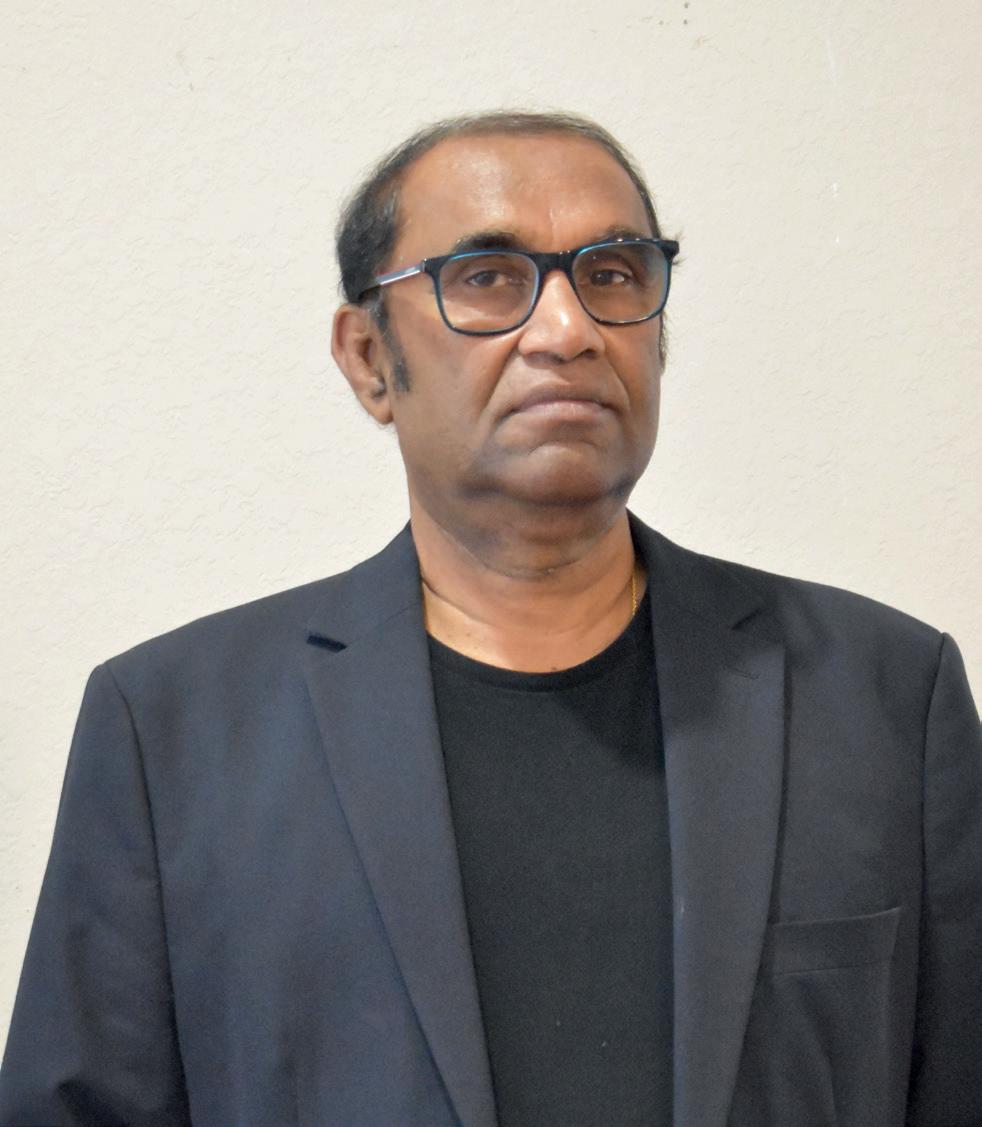
Nihal Obeyesekere
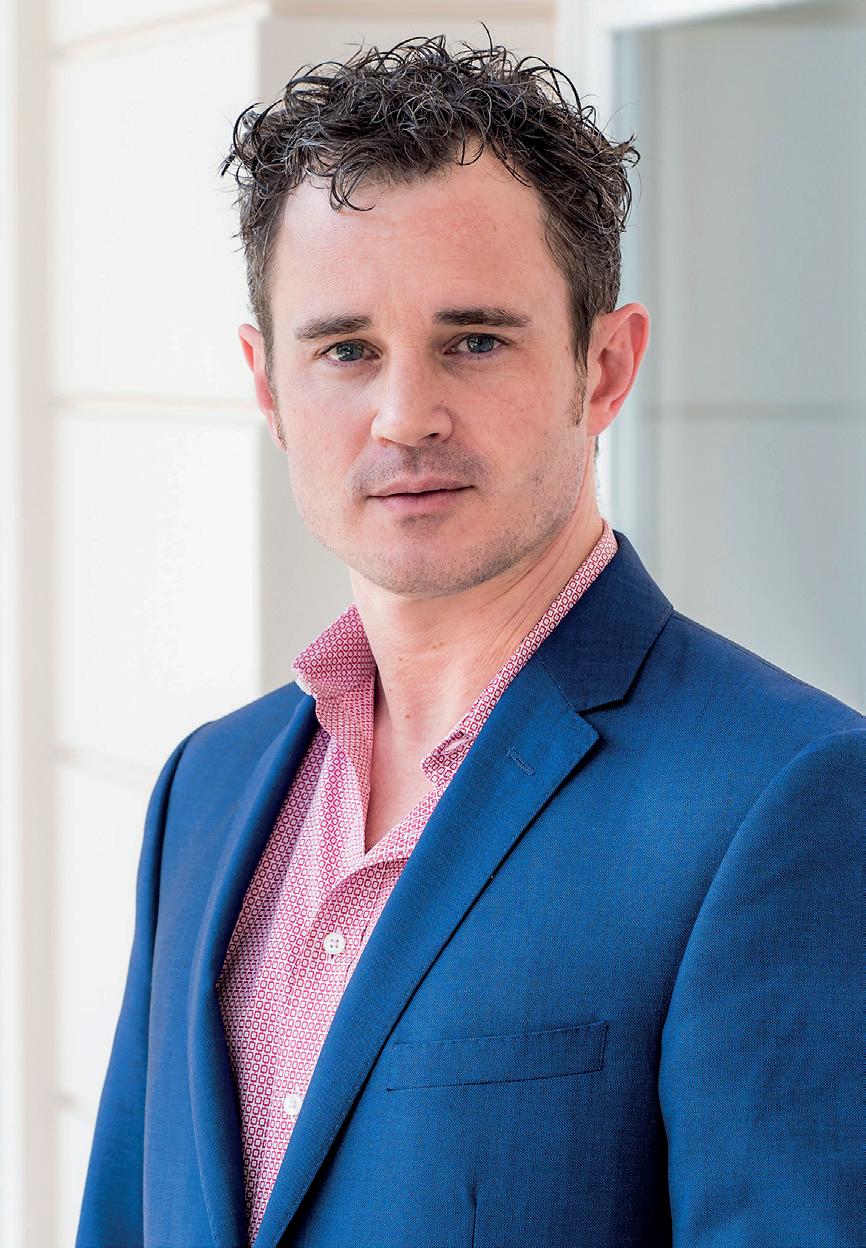
sustainability. In addition, we are in the process of aligning Clariant’s activities with the UN Sustainable Development Goals.
What does sustainability mean for Clariant and the industry? Since we work in the oil industry, a lot of people may be surprised to hear us talking about sustainability. We believe that it’s even more essential that we are helping the oil industry be as sustainable and environmentally conscious as possible. In the decades to come, there’s still going to be a need for the oil and gas industry and how we operate is going to be very important for meeting global sustainability and carbon emission targets. With our commitments to innovation and sustainability, we believe that companies like Clariant will help lead the way in this transformation.
Can you give a few examples of your activities in this area? We’ve spent many years pioneering ways to assess and minimise the eco-toxicity of our products. This is to ensure that they aren’t toxic to marine organisms and that they don’t bioaccumulate (i.e. that they aren’t fat soluble). We have also looked at making our products biodegradable to make sure that they don’t persist in the environment. These goals have given us a number of key performance indicators (KPIs) to drive towards as we develop more responsible and environmentally acceptable chemistry. More recently, we’re also working towards making sure that all of the products we use are responsibly sourced and sustainable. We’ve been moving away from petroleum-sourced products to use alternatives such as responsibly sourced palm oil or rapeseed oil – products that are grown rather than needing to be geologically extracted. We’re considering all of the feedstocks we use, how they’re harvested, and even how they are transported.
Getting back to corrosion inhibitors more specifically, why is preventing corrosion so important? Every metal component is subject to corrosion and the oil and gas industry spends approximately US$1.5 billion each year trying to prevent corrosion. Extending the longevity of these components not only cuts down on costs, it also reduces the frequency with which these components need replacement – thus cutting waste as well. Preventing corrosion is also hugely important for maintaining the safety of pipelines and avoiding environmental incidents due to pipeline failures.
Could you say more about the unique challenges of deepwater applications? The combination of high pressure and high temperature (HPHT) in deepwater applications is a very significant challenge because most water-soluble organic chemicals aren’t stable under these conditions. Our recent work has focused on developing chemicals that are stable and effective in HPHT environments.
Another huge challenge is delivering these chemicals where they need to go, i.e. from a floating production facility to the wellhead on the bottom of the ocean. This usually entails roughly 6000 ft of distance to reach the ocean floor and another 20 miles of pipelines along the ocean floor. That means a 20 mile long, ⅜ in. diameter stainless steel tube, which is at 4˚C and 10 000 psi. It’s a very tortuous path for the chemicals and we go to painstaking detail to make sure that chemicals are going to survive that. There are so many things that can go wrong, and it’s a multi-million dollar mistake if a tube becomes blocked. So, we put just as much focus, attention, and care on ensuring delivery. We even have a dedicated process called DEPFLUXTM that certifies products that have undergone specific testing to guarantee the deliverability of a product under these conditions.
Figure 1. Multiple rotating cylinder electrode (RCE) devices are used to measure corrosion using the linear polarisation resistivity (LPR) electrochemical technique. Could you say more about your work on developing sustainable and environmentally acceptable corrosion inhibitors? There are three main areas we’re focusing on: developing brand new molecules, optimising formulations, and developing the best solutions according to the specific requirements of each individual application. For example, for one recent project, we designed and tested more than one hundred corrosion inhibitor formulations. From these, we developed several water- and oil-soluble products that are thermally stable above 200˚C (390˚F) while also
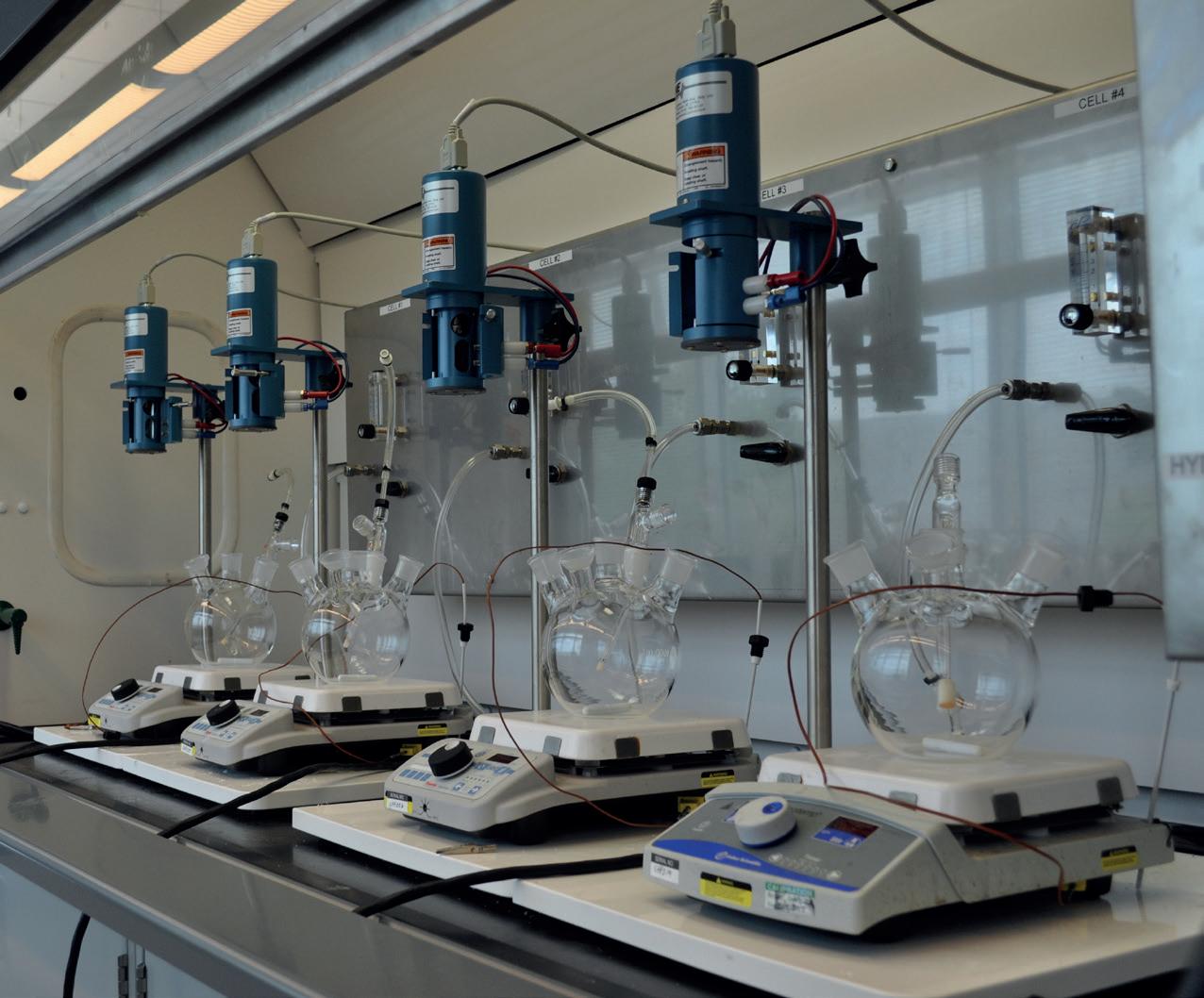
maintaining high efficacy. In particular, we developed one product that we found was stable at 200˚C for two months under inert HPHT conditions. After extensive performance testing, this product showed excellent performance under varied flow and shear stress regimes. We are also proud to say that this product is biodegradable and made from environmentally friendly starting materials.
Is there anything that you would like to share about your approach to solving these challenges? We do everything possible to guarantee what we deliver through a whole host of tests, continual training and education for our researchers, and ensuring that we’re more than meeting all regulations. We have unique tests that are designed to mimic specific conditions and corrosion types. We‘re also designing new tests and equipment to adapt our tests to better mimic the field in a customisable way and to push the limits of available technologies. At the end of the day, one of the biggest components to our approach is our people. We recruit very carefully to have the best in the industry and we operate differently than many companies because our teams really treat each other and collaborate as equals.
What shifts have you seen in the industry during your careers? There’s been a huge shift towards sustainability in the past 10 years. The petroleum industry – in general led by major international oil companies – are increasingly looking for greener solutions. They’re looking to be more environmentally responsible and to reduce their carbon footprints. Clariant has also made sustainability their number one priority and we’re all committed to doing more to contribute to a greener, healthier, and safer future. Across the industry, we’ve also seen that companies have to promote sustainability to attract and recruit top talent. Young graduates want to know about the green policies of potential employers and they are highly motivated to pursue projects that will benefit the environment. What do you see as some of the biggest hurdles to the industry adopting more sustainable products and practices? For many years, Clariant has researched more environmentally friendly alternatives, even when there was not much demand for these solutions yet. In the past, these products were frequently more expensive than more conventional options, and this was a limitation for the oil industry. But the price for these products has significantly dropped since then, and these products perform just as well as their competitors. Environmentally friendly products now really offer win-win options for the industry – they are
Trench walls so straight you can hang a picture The trencher effect
What’s the trencher effect? One machine that can outwork multiple excavators while digging pristine trenches and creating its own backfill. Want optimal performance and trenches? Get a trencher.
financially feasible, they perform just as well, and they don’t harm the environment. That is our goal – to make these elusive triple bottom line scenarios possible by balancing the social, environmental, and financial factors.
What are you working on next? We’re looking at using more natural and environmentallyfriendly raw materials. These include plant-based products, sugars, fatty acids, and even things like coconut oil. We’re also been investigating amino acids, which are the basic building blocks of the proteins that are found in all living organisms. These are all environmentally-friendly, nontoxic, and biodegradable. Some of these raw materials may be a little more expensive than conventional products, but we think the industry is ready to accept these costs and make a commitment to the environment. In terms of making our operations more sustainable, Clariant is also decreasing its carbon footprint through small changes like making all of our chemicals highly concentrated so that we can use fewer solvents. We’re also cutting our electricity use by developing chemicals that don’t need as much heat to produce. Little changes like these can add up to have a high impact.
What do you consider your most significant contributions to the field so far? Nihal: I’ve spent the past 30 years dedicating my work to developing environmentally friendly and sustainable products. I’m very committed to doing my part to make the planet a little greener and safer for the next generation, which has fit perfectly with Clariant’s sustainability goals.
Jon: I have tried hard over the course of my career to document my experiences and learnings in the scientific literature and Clariant has been very kind to allow me (and many others) to achieve this by sponsoring collaboration and publication in both conferences and journal as well as the patent literature. I feel that some of our greatest achievements are soon to come and we are focused on many highly critical areas, not just corrosion and general integrity management, but also in the area of flow assurance and in particular organic deposition prevention – much like corrosion these products will focus on harsh environments and additionally bring a sustainability benefit.
What are your goals moving forward? Sustainability is at the core of what we do and we’re working towards making everything in Clariant’s Oil and Mining Services corrosion product line environmentally benign. The oil industry is going to continue being important and it’s incumbent on us to operate in a sustainable way. It’s so important to know how much CO2 the industry is producing and it’s in our hands to change that. As citizens of the world, we have a responsibility to do the right thing, and the right thing is to make sure that we work towards a better future for the planet and for generations to come.
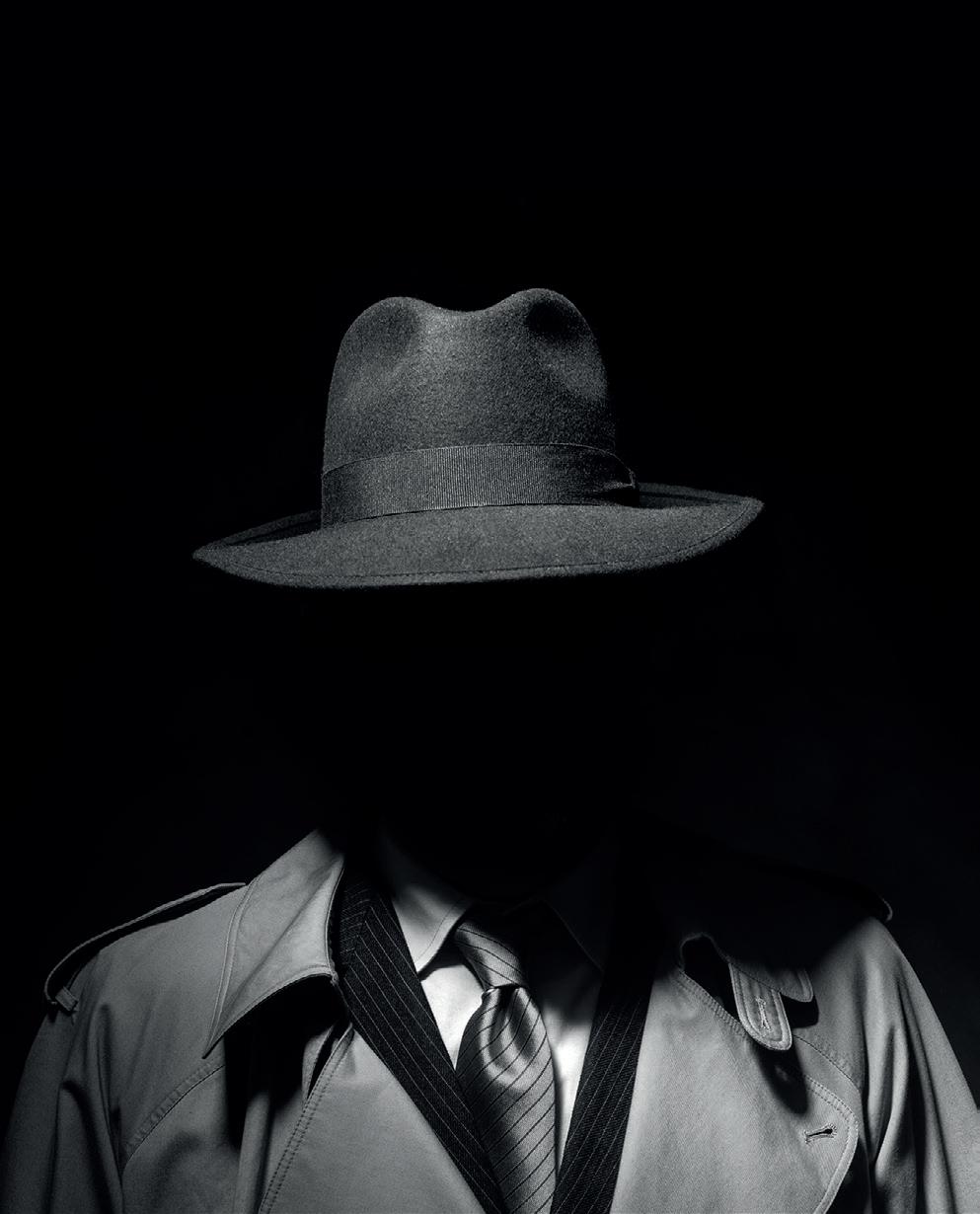
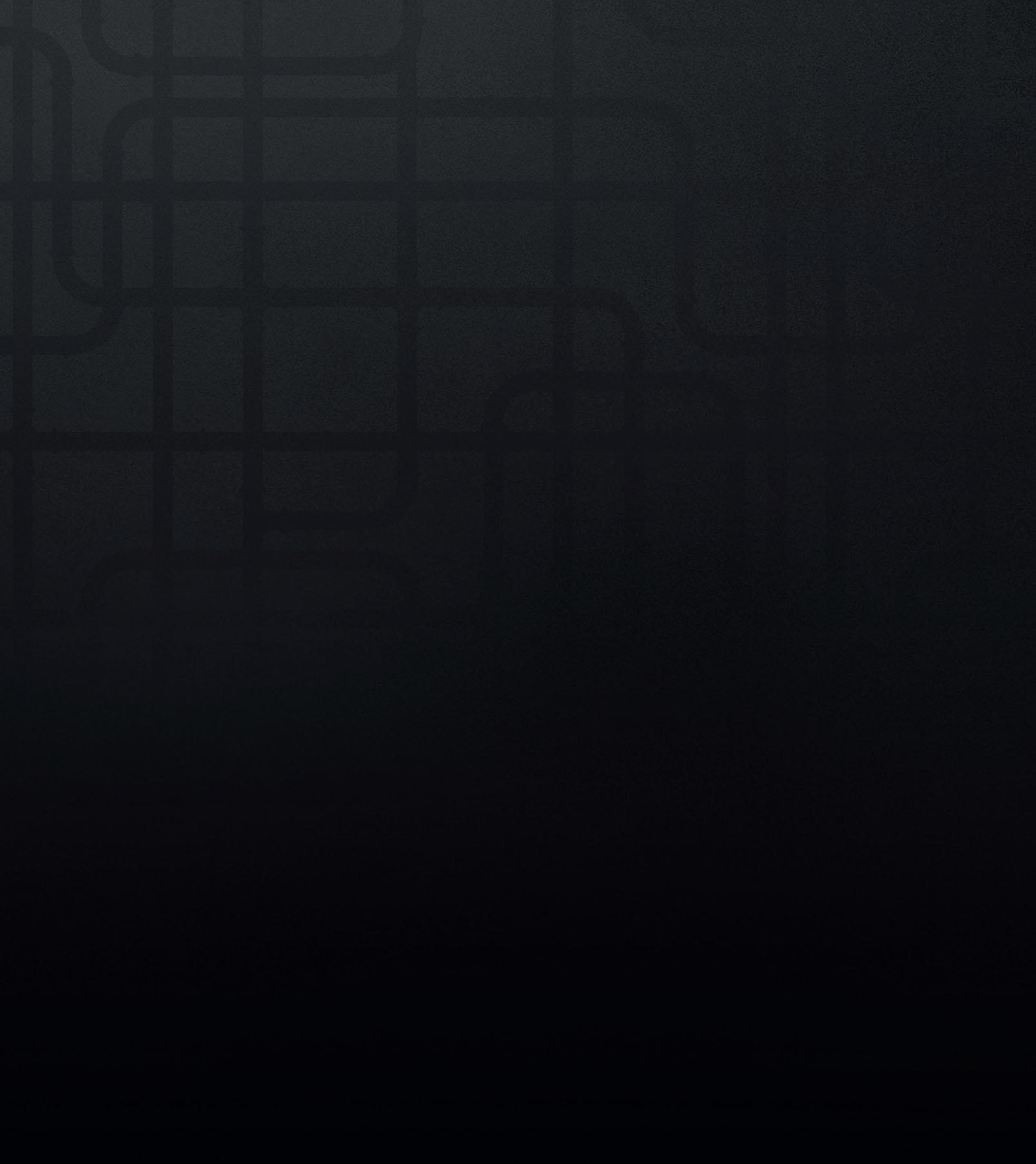
Accurate • Tough • reliable
THE LEADING BRAND OF HOLIDAY DETECTION EQUIPMENT SINCE 1953
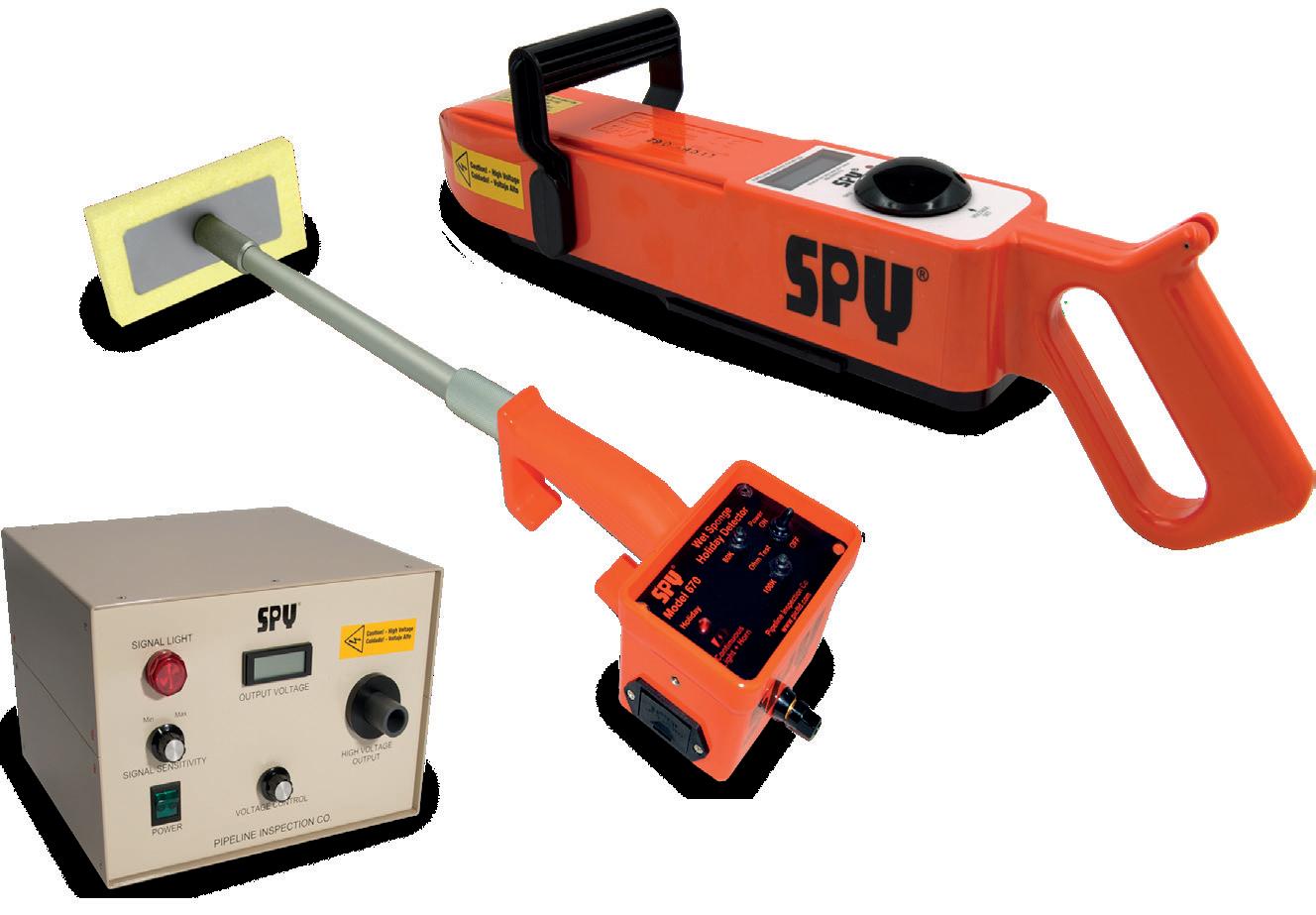