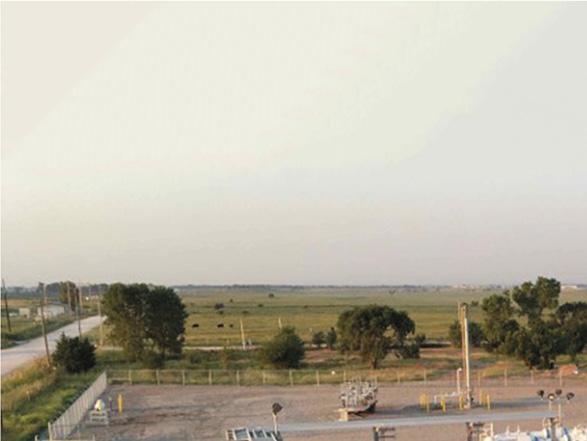
10 minute read
Thinking smarter and broader with repeatable design
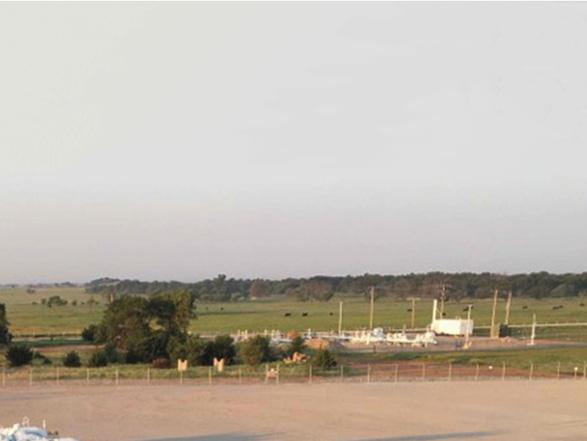



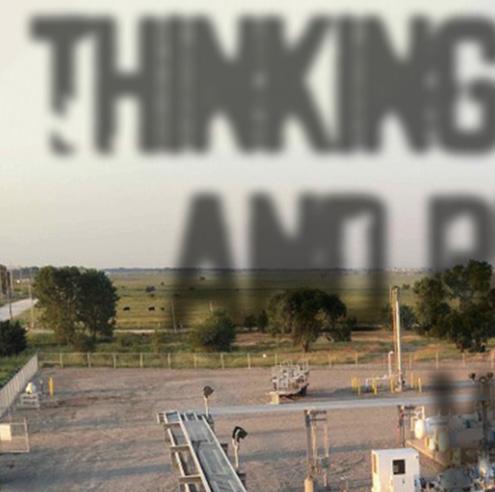

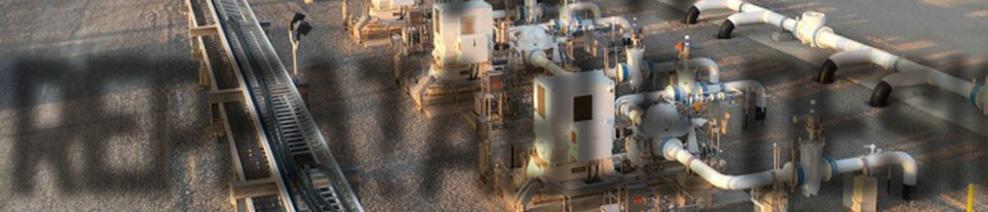
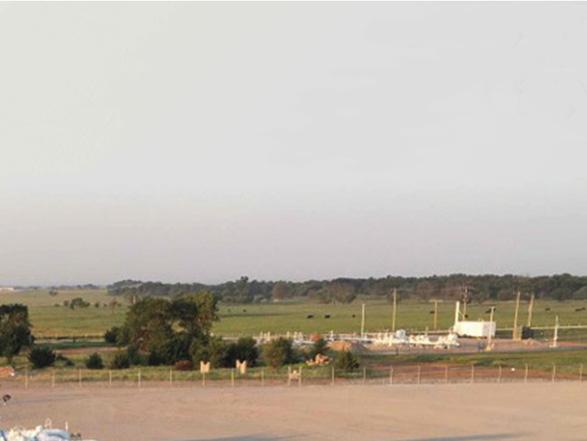
Ryan Hiestand, MBA, Project Manager, Burns & McDonnell, USA, discusses the benefits of repeatable design for the pipeline industry and outlines the seven steps of the design standardisation process.

There is new excitement among pipeline design leaders and across the larger pipelines industry now that the development and use of consistent designs is widely available. Also known as repeatable design, design standardisation for pipeline facilities effectively aligns project stakeholders, objectives and scope, which helps capture and optimise schedule, cost and value for pipeline projects.
This approach is critical given the increasing industry pressures to make smart investment decisions for public and private infrastructure systems, new and ageing alike. For teams designing, creating and operating pipeline facilities, and for those charged with delivering the safety, efficacy and efficiency of each connective system, this is a test of whether they can shake free from traditional, timeconsuming ways to get to someplace smarter.
“Collaborative pipeline facility projects using repeatable design principles are providing results to owners by reducing schedules from conception to startup and driving down costs across the lifecycle of assets. Burns & McDonnell
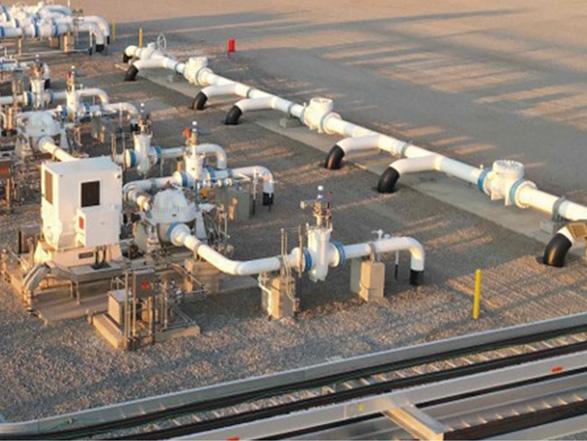
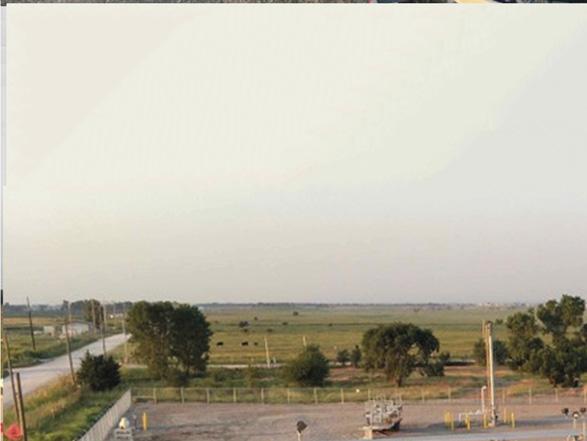

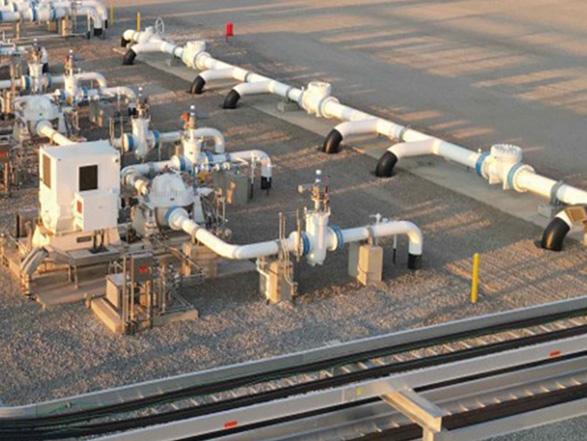
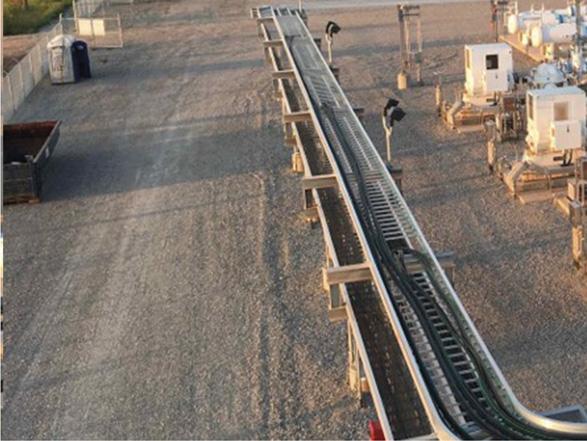
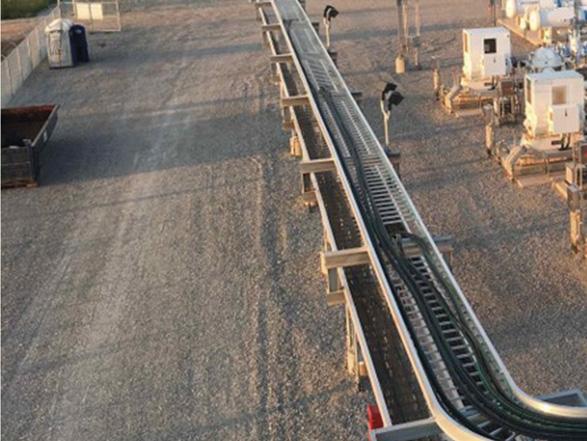
Figure 1. Pipeline standard design.
The seven steps of design standardisation
sites are evaluated for construction and commissioning, and lessons-learned logs help with the change management process. 1. Understand possible variations The first step of design standardisation is for select project stakeholders to participate in a facilitated process to understand possible variations of their infrastructure needs. These are likely to include factors such as pipe diameter, size and quantity of equipment, and geographic Figure 2. Identifies the design standard process for design standardisation. locations, among other considerations. Efforts are made to consolidate iterations, as well as to document and publish the list of possible variations to be shared continues to push the boundaries of repeatable design with the team. This early stage of information intake and programming, having just conducted our latest iteration of engagement informs a later stage focused on identifying standardising pipeline facility development in 2020,” says where standardisation could work. If it is determined at this Jason Hetherington, Managing Director of Logistics and first step that repeatable design is not a good fit, traditional Midstream at Burns & McDonnell. custom design approaches and optimisation are likely a more feasible approach. Design standardisation may be applied What is design standardisation? to portions of a project as long as there are at least two Application of design standardisation comes through the repeatable systems. design and use of standard ‘blocks’ of grouped equipment, piping and instrumentation in varying arrangements 2. Align stakeholders for a programme of similar projects. When feasible to Once the consolidated and published iterations based on spend additional time on upfront design and stakeholder possible variations have had a full owner review, it is time for alignment, the design of these blocks can be established the second step, to align stakeholders. Considerable emphasis and locked early in the programme. The blocks then can be is placed on gaining feedback and total buy-in from each of arranged to meet site conditions and space requirements, the many key stakeholder groups. This new approach allows and yet the contents of the blocks are not changed from 100% of the customisation of the blocks to occur before the site to site. site-specific design stage. Input provided much later in the
Since every design is the same through the design process can increase project cost and hinder schedule savings. standardisation process, each valve responds the same way, This process emphasises early alignment of stakeholders to all of the pump stations operate the same, and procurement optimally define standardisation of the specific layout and of major equipment and commodities can be negotiated and scope of work. awarded early for fabrication in controlled manufacturing Typically, leaders from each of the key stakeholder groups environments. Operations compliance officers appreciate have a say in the design. They should include: repeatable design, where the issues of quality assurance and ) Operations and maintenance. quality control (QAQC) are addressed and the integrity of manufactured components is maintained. Also, compliance ) Engineering subject matter experts. officers rarely turn down the chance to optimise for exterior conditions. Stakeholders welcome that time and cost savings ) Procurement. are increased because drawings are only issued once.
The bedrock of successful design standardisation is ) Construction co-ordinators. a comprehensive planning process that actively engages with key stakeholders from the beginning and consistently ) Compliance officers. throughout, and which brings forth a deep understanding and communication of the variations of the project. ) Commercial.
A seven step design standardisation process is the most sound, with stakeholders invited to review and consider To provide accurate design standard alignment, key how a pipeline facility will be designed and built and where stakeholders need to be included in the review of the the blocks could be located. Topography and layout of standardisation process early and often. Each key stakeholder
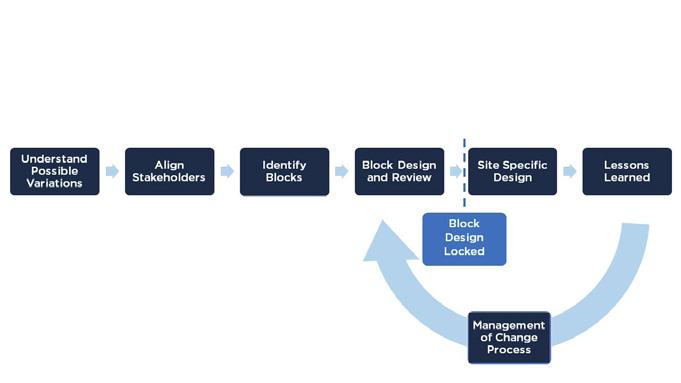
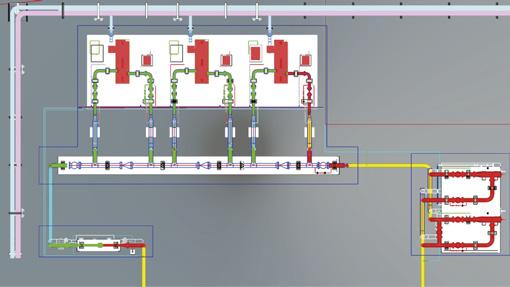
Figure 3. Identifies boundaries of ‘blocks’ (blue outlines) utilised on a recent pump station programme.
group also needs to identify important milestones when input is to be received before moving forward, and they should have the opportunity to share their contributions.
3. Identify blocks Driven by the iterations of possible layout variations, the project team and key stakeholders take the third step: identify blocks. Based on the previous steps, decisions are made about which pieces of equipment or piping layouts can be standardised. There are considerations of where blocks will start and stop and additional details are addressed, such as how to handle numbering, naming and tagging of blocks and components. All engineering systems should be considered when defining block start and stop points for each discipline.
4. Block design and review stage In order to transform the conceptual design into a concrete plan, the next step – the block design and review stage – incorporates comments from stakeholder leaders. After this stage the block design is locked and will not be modified during the project.
5. Site-specific design During the fifth step of the process, site-specific design, blocks are arranged by defined project layout standards based on geography, topography, tie-in locations, proximity to other equipment and maintenance access.
6. Lessons learned For the next step, the team is likely to facilitate lessons learned summits with key stakeholders, which should take place after all procurement and construction contracts are awarded, post startup and commissioning, and/or following one year of service.
7. Management of change process Lessons learned serve the final step, the management of change process, and inform future project block design and review stages, where blocks may be reconfigured and locked in again. The team is able to identify the lessons learned that will be applied to future sites and methods of deployment. These process improvements allow all involved to get smarter every time. Who are the beneficiaries of design standardisation? Those who benefit most from standardising the design of pipeline facilities are the owners of the infrastructure, as well as their teams in engineering, procurement, construction, and operation and maintenance.
Engineering team benefits: ) Decreases quantity of modified deliverables. • Ease of updating all blocks across different project sites based on varied site conditions. • Each system will respond to the same adjustments.
) Automates updates to deliverables, which improves quality and repeatability of design.
) Reduces design schedule.
) Reduces design cost.
Procurement/construction team benefits: ) Increases opportunity for shop fabrication in controlled manufacturing environments.
) Improves purchasing options and allows for a more regional or global approach.
) Decreases requests for information (RFIs) and field delays, and improves efficiencies due to crew familiarisation with design across sites, as well as from stakeholder input throughout the process.
) Increases quality.
) Decreases schedule.
) Improves safety.
Operation and maintenance team benefits: ) Standardises spare parts across assets.
) Establishes consistent operations procedures.
) Improves safety.
) Reduces downtime related to problems.
Why deploy repeatable design? There are three main reasons why repeatable design is worthwhile to deploy. The most compelling reason is that the schedule to get a pipeline into service is reduced. The second reason is the decrease in cost for design and construction of the project and future operations. The third is that this process allows for stakeholder participation and buy-in, which results in a smarter, fully informed configuration.
In addition, and perhaps equally important, design standardisation is an effective new approach. Burns & McDonnell recently completed a repeatable design case study on a pipeline system from Wyoming to Texas involving 25 pump station
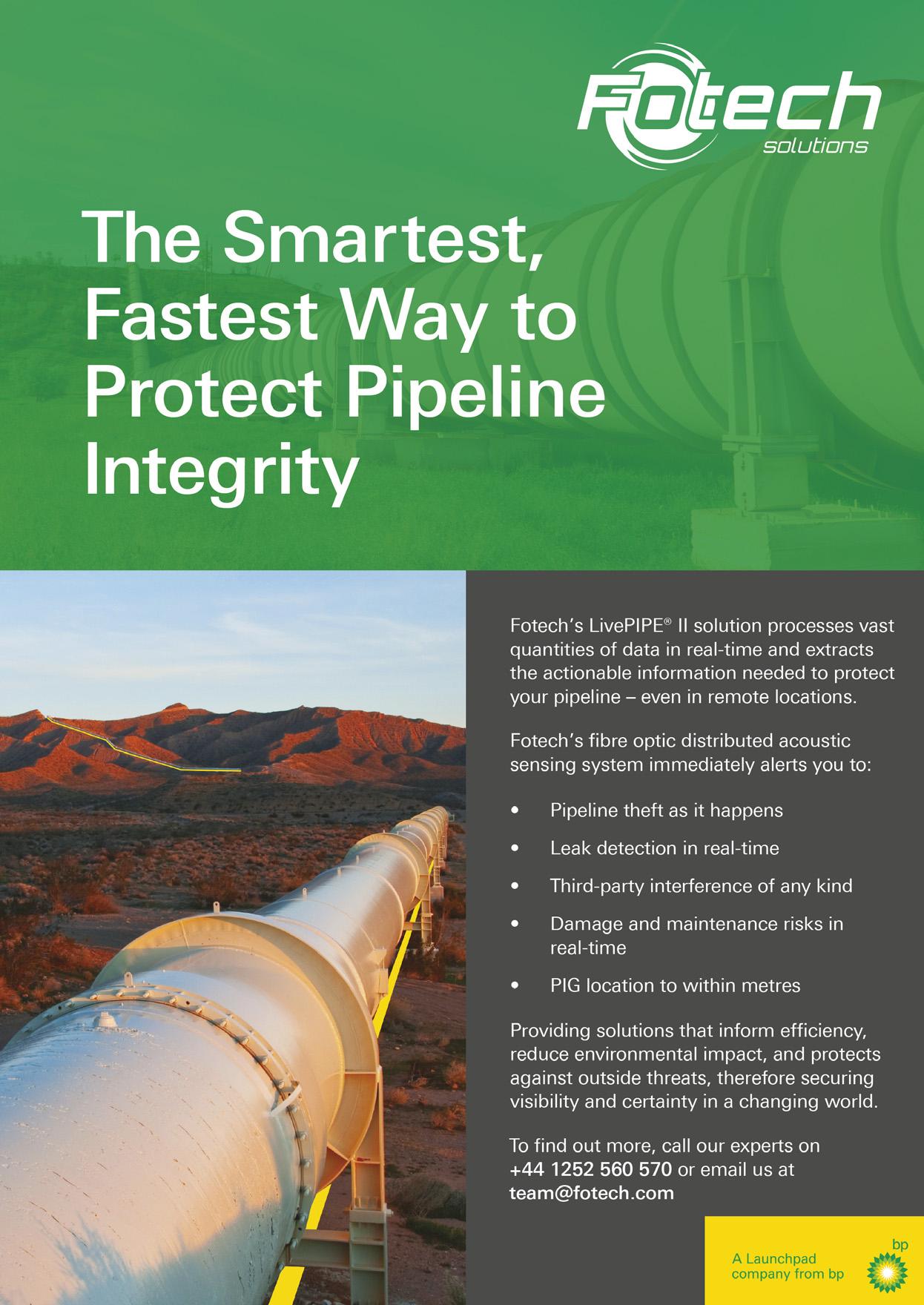
sites with four block variations, and with five blocks on each site. The team reached an average of 70% of typical ISOs that were repeatable and not redesigned, more than 80% of typical electrical and instrumentation (E&I) drawings, and significant total installed cost (TIC) reduction. The owner was very satisfied, having reduced its overall design cost and schedule by 50%. At the conclusion of construction, Burns & McDonnell was able to report that throughout the different phases of the project, the team was able to produce more drawings and give the owner more deliverables so that the scope could be better communicated while simultaneously reducing cost and schedule.
Burns & McDonnell is not alone in its findings about the value of design standardisation. The Construction Industry Institute (CII) reported a study in 2020 of 45 implementations of repeatable design for upstream, midstream and mining (UMM) projects, and the result of implementing this approach was 10% average savings in TIC, 15% in average schedule savings and 25% average savings over the lifecycle of the projects. Due to equipment conformity, cost savings were considerable in the UMM team’s ability to make the same changes at all repeatable project sites. By working together with stakeholders, it also discovered that in many cases some modules were more amenable to design standardisation. It was determined that while there need to be at least two repeatable systems, the site layout does not need to be 100% standardised. Additionally, the UMM team found that utilising the assets of all stakeholders involved in the project built more knowledge, yielded smarter decisions and resulted in statistically positive improvements across all systems and responsibilities.
Conclusion US energy demand has doubled every 20 years, and infrastructure spending is likely to increase dramatically in the range of trillions of dollars over the next decade. For the pipelines industry, innovative methods such as repeatable design undertaken by leading-edge facility owners and stakeholders will safeguard the design, construction and maintenance of the infrastructure needed for present day and future demand. Rather than the traditional, custom approach for all pipeline facility and pump station components, design standardisation offers proven cost and schedule savings, as well as a verified process for unified effort that improves safety and quality. This moment offers the industry the opportunity to get smarter, faster and to do more with the resources entrusted to us for stewardship.
AGRULINE XXL PIPES
HDPE PIPING SYSTEM FOR HIGH VOLUME FLOW
Outstanding life span Fast and easy installation For high-volume flows High-quality materials
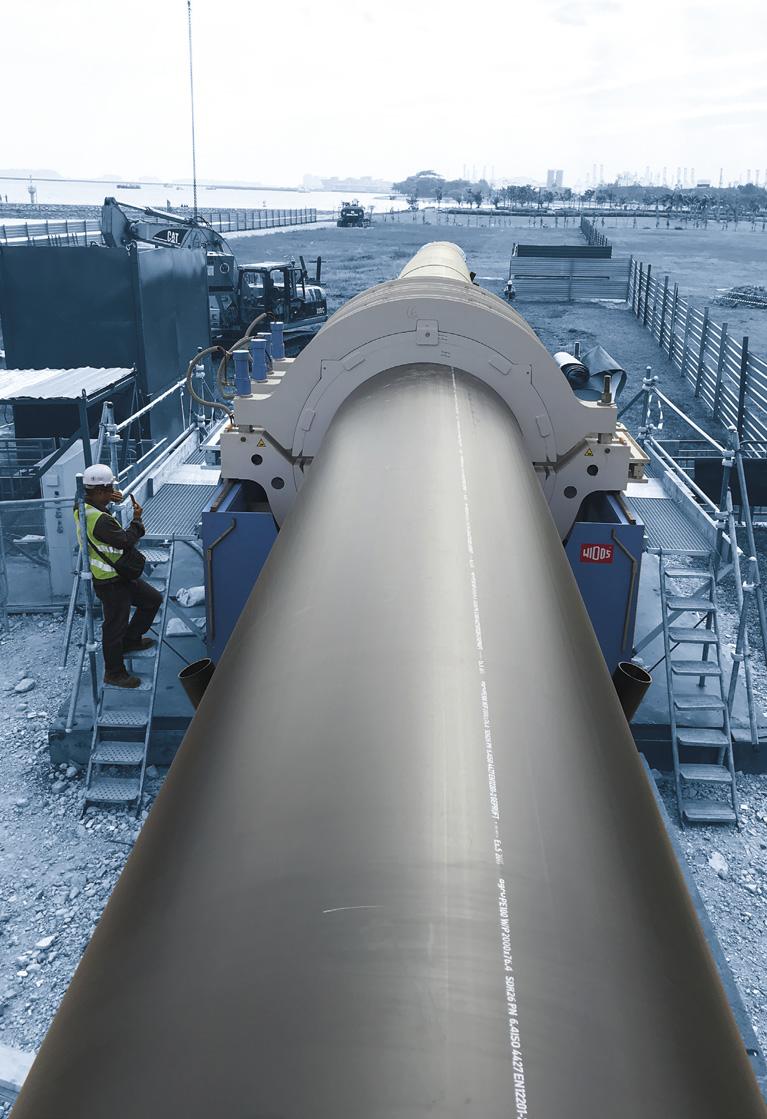
Heated tool butt welding machines from OD 20 mm up to OD 3500 mm