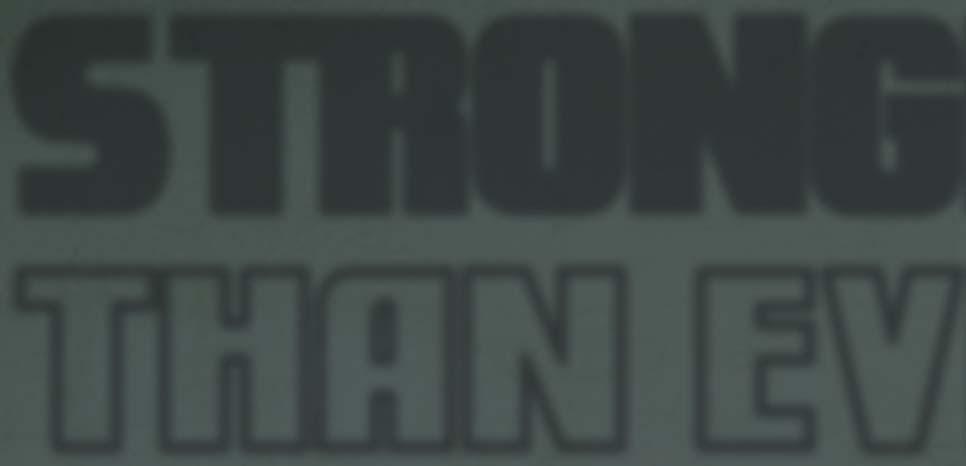
19 minute read
Stronger Than Ever
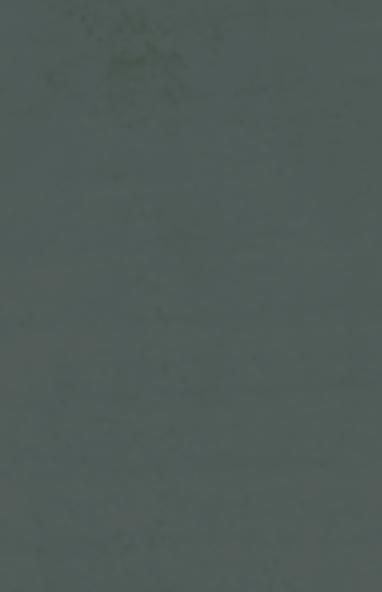
Martin Provencher, OSIsoft, explains how digitalisation could help cement companies emerge from the COVID-19 pandemic stronger than ever.
ement companies are facing a
Ctwofold crisis brought on by the global COVID-19 pandemic. Demand for cement and concrete is falling because of widespread economic disruption: according to an August report from the International Finance Corporation (IFC), global demand for cement in 2020 is expected to be 3% less than in 2019. Excluding China, where more than half of the world’s cement is produced and consumed, the drop in demand is an even steeper 6.4%. For many plants, which were already operating at less than full capacity, the impact of sudden plunges in the market on slender profi t margins is a lot to absorb.
The second piece of the crisis is internal: the impact on people, processes, and workplace culture. While contending with disruptions in markets, cement companies are also facing the new pandemic realities that every business must now confront.
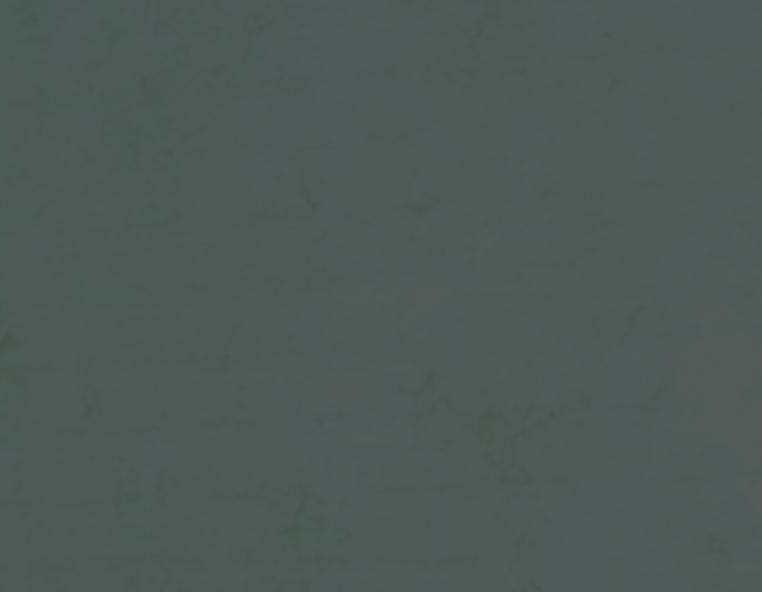




Navigating the COVID-19 workplace is a challenge on many fronts, from facilitating remote work to implementing new safety protocols on site. The potential upsets of illness and quarantine mean that key operators are more likely to be absent without warning; a workplace exposure might result in an entire team being suddenly taken offline.
For a business as capital-intensive as cement production, rapid change is difficult, but as seen during the COVID-19 pandemic, change can happen quickly, and businesses must be able to adapt just as quickly. The best tool a business can use to survive and thrive in the midst of pandemic uncertainty is one that was already transforming the industry before COVID-19 turned it upside down – data.
With the right approach to data, digital transformation has the power to make measurable positive impacts on just about any aspect of business – from managing supply chains to wringing waste out of processes to making better use of valuable people and equipment. The key is taking a holistic approach. A data management system that serves as a single source of truth across an enterprise can break down informational silos between different teams or different sources of data and yield valuable insights that can only be captured by analysing rich, contextual data in real-time.
With the rise of IIoT and the increasing affordability of sensors, even businesses operating in the challenging physical environments of cement manufacturing, mining, and materials have begun to embrace digital change. Companies that are using their operational data to generate insight and drive organisational change are poised to emerge from the global COVID-19 slowdown smarter, leaner, and more flexible than ever.
What is data good for?
A smarter workforce
Remote work is here, and it is not going away anytime soon. According to a recent GlobalData survey, only about 30% of workers who held full-time offi ce jobs before the pandemic want to return to on-premise work full-time, but in order to make remote work possible, companies need solid tools for monitoring, managing, and communicating from afar.
Through holistic data management, real-time data flowing from processes and equipment can be harnessed to create intuitive dashboards for remote users. Visualisations that track KPIs and other important parameters can serve as a window into assets and processes that can be viewed from anywhere. An enterprise-wide data infrastructure can create real-time notifications and alerts when parameters are exceeded and deliver them to the right people at the right time.
Integrating all of a company’s assets and data sources into a single data architecture also enables the use of machine learning, which can build on existing operator expertise and create new tools for predicting and optimising processes. This would mean companies need less operator oversight, and it might even lead to the development of complex autonomous processes.
By bringing all of its real-time asset and power plant operational data across multiple plants and locations into a single data infrastructure, Indian cement company, UltraTech, was able to give users across the company real-time access to critical information and monitor important assets from afar. Information-sharing between different parts of the company is now far easier and more consistent since the entire business is using the same PI System data infrastructure. With all of its data integrated, the company was able to establish new quality parameters, show trends for those parameters, and take corrective action swiftly and effi ciently. Data analysis for processes and equipment at any one of UltraTech’s locations can now be done from anywhere, and digital transformation is increasingly enabling the company to predict potential situations rather than just react to them.
Smarter assets
Equipment downtime and failure is costly, but without deep insight into asset and maintenance data, it is impossible to see exactly how much impact equipment downtime has on the bottom line. Real-time operational data can help prevent unplanned asset downtime, get more productivity out of assets and processes, and enable equipment maintenance to be scheduled for times when it is less disruptive to overall operations.
The increasing availability of rich, contextualised real-time operational data along with new machine learning tools enables analysis of large data flows in real time. This is fuelling a shift across many equipment-heavy, capital-intensive industries away from scheduled maintenance, and towards condition-based maintenance, or even predictive maintenance. By using real-time operational data to identify conditions that could lead to equipment problems, operators can perform maintenance when it is needed rather than on a set schedule – an approach that can cut down on both maintenance costs and equipment failures.
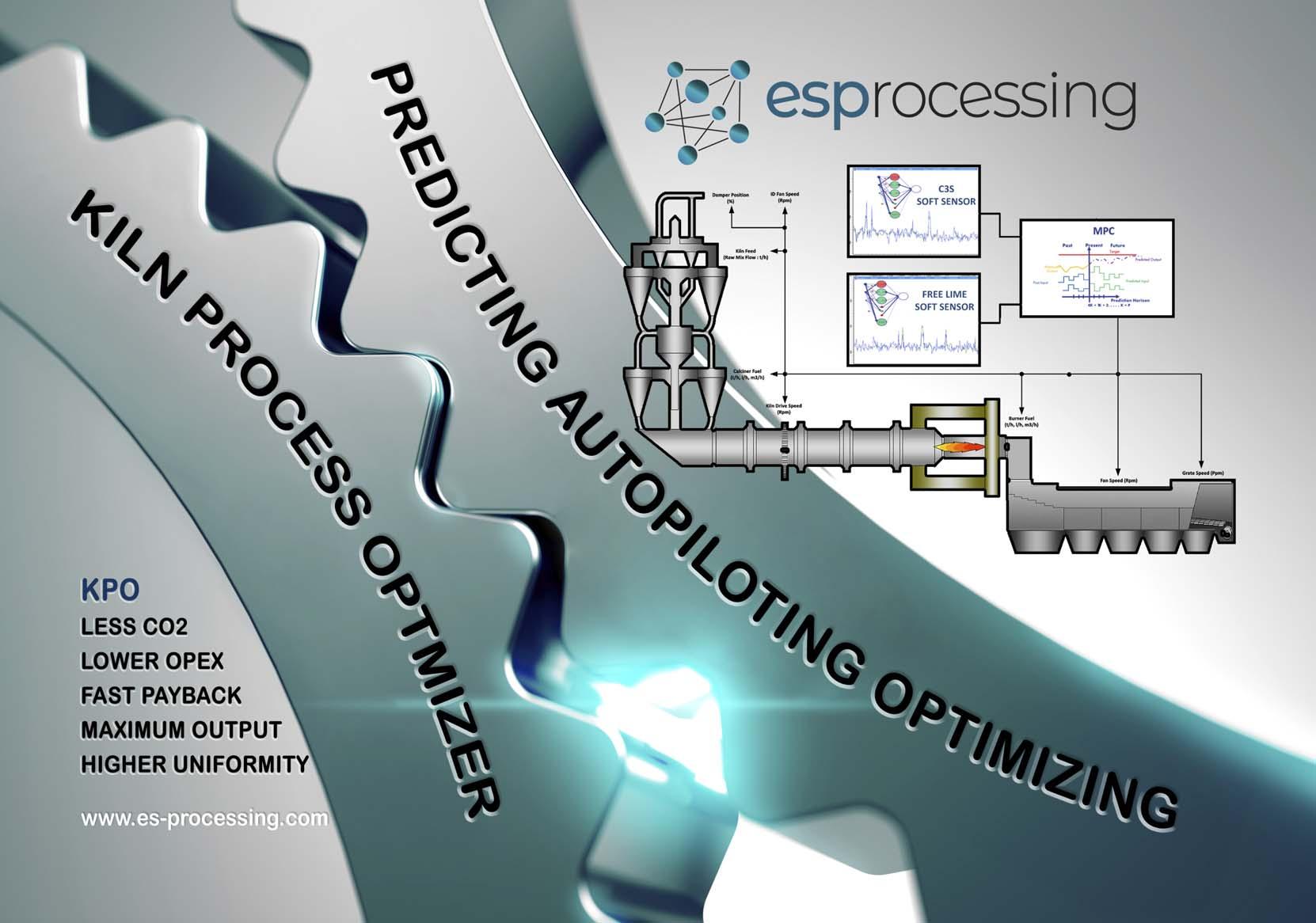

Another powerful tool that enables easy visualisation of data in the context of important equipment is a ‘digital twin,’ like the PI System’s Asset Framework (AF). AF creates a virtual model of the physical plant and its assets that can be used to build displays or expose system data to other systems for analysis. A digital twin layer in a data infrastructure allows operators to view and analyse data in the context of assets and the relationships between them.
Peruvian cement maker, UNACEM, is using real-time data integrated with operator dashboards to identify the causes of equipment downtime and stabilise important processes. The company was having issues with bottlenecks between heating and dispatching in the grinding process, and operational procedures were not standardised. To tackle these problems, UNACEM started with a roadmap for process stabilisation, then systematically created standardised KPIs for every machine, product, shift, hour, and operator, using dashboards to compare real-time operational data to KPIs and projected metrics. Real-time insight is now allowing UNACEM operators to take corrective action before bottlenecks develop and adjust processes for target performance on the fly. Better data management with the PI System has improved cement milling runtime between 11 and 17%, yielding both environmental benefits and increased profit.
Sustainability
Environmental impact is already a pressing issue for the cement industry. Concrete is responsible for about 8% of global carbon emissions, and much of it is generated during the heat- and energy-intensive process of producing clinker. As the second-most used product in the world behind potable water, cement makes a large impact on the environment, but it also has vast potential to mitigate that impact across the entire life cycle of the product, from mining and production all the way through delivery, construction, use, and recycling.
Cement companies on the path to decarbonisation are approaching that goal through a variety of methods, from investing in carbon-capture technology to making their production processes more effi cient. At every step along the road, the ability to capture and analyse reliable operational data in real-time is key to supporting progress. Data can be used to support the decarbonisation of the cement industry through many pathways: slashing energy costs, increasing the productivity of processes, reducing waste, recovering excess heat, and more.
As a multinational industry leader with an ambitious goal – net-zero emissions concrete by the year 2050 – Mexico-based CEMEX is using digital transformation to support sustainability initiatives across its operations in more than 50 countries. More than a decade ago, CEMEX embarked on a digitisation project across its facilities worldwide, installing equipment sensors and using OSIsoft’s PI System as an enterprise-wide data architecture, but gathering the data was only the fi rst step. The real value lay in putting it into action.
CEMEX Operational Digital Technologies Manager, Rodrigo Javier Quintero, at an OSIsoft user conference in 2019, described data as “the new gold”, expressing that the company had a gold mine that they were not tapping.
As an energy-intensive piece of equipment, the rotary kiln that heats clinker was a prime target for optimisation. As part of an Industry 4.0 initiative, CEMEX set a goal of having autonomous kiln operations by 2022. The company started with just one piece of the process – clinker cooling, in which cold air is pushed into the system while heat from the raw material is recouped back into the system for process efficiency. Throughout the process, operators seek to optimise heat recovery, process stability, and product quality by controlling air input and cooling rates. Operator expertise is important to achieving good results.
CEMEX embarked on a project to use real-time operational data and machine learning to augment, and eventually supplant, the role of the expert operator in controlling the clinker cooling process, moving in a phased approach toward achieving ‘golden runs’ in cooling. The company was able to draw on a wealth of process data from the PI System and integrate it with third-party solutions from machine learning specialists, Petuum, to develop predictions for cooling process behaviour.
In the first stage of the project, PI System dashboards gave operators access to visualisations generated by the AI model that predicted system behaviour up to 25 minutes ahead of time, allowing the operators time to react to the projections and make adjustments. After achieving success in that realm, the project moved from prediction to prescription, using the AI model to suggest optimised settings to operators based on prior performance.
By testing the model’s optimisation suggestions with guidance from expert operators, the company was able to move on with confidence to the final stage: autonomous operation. CEMEX now has the capacity to run
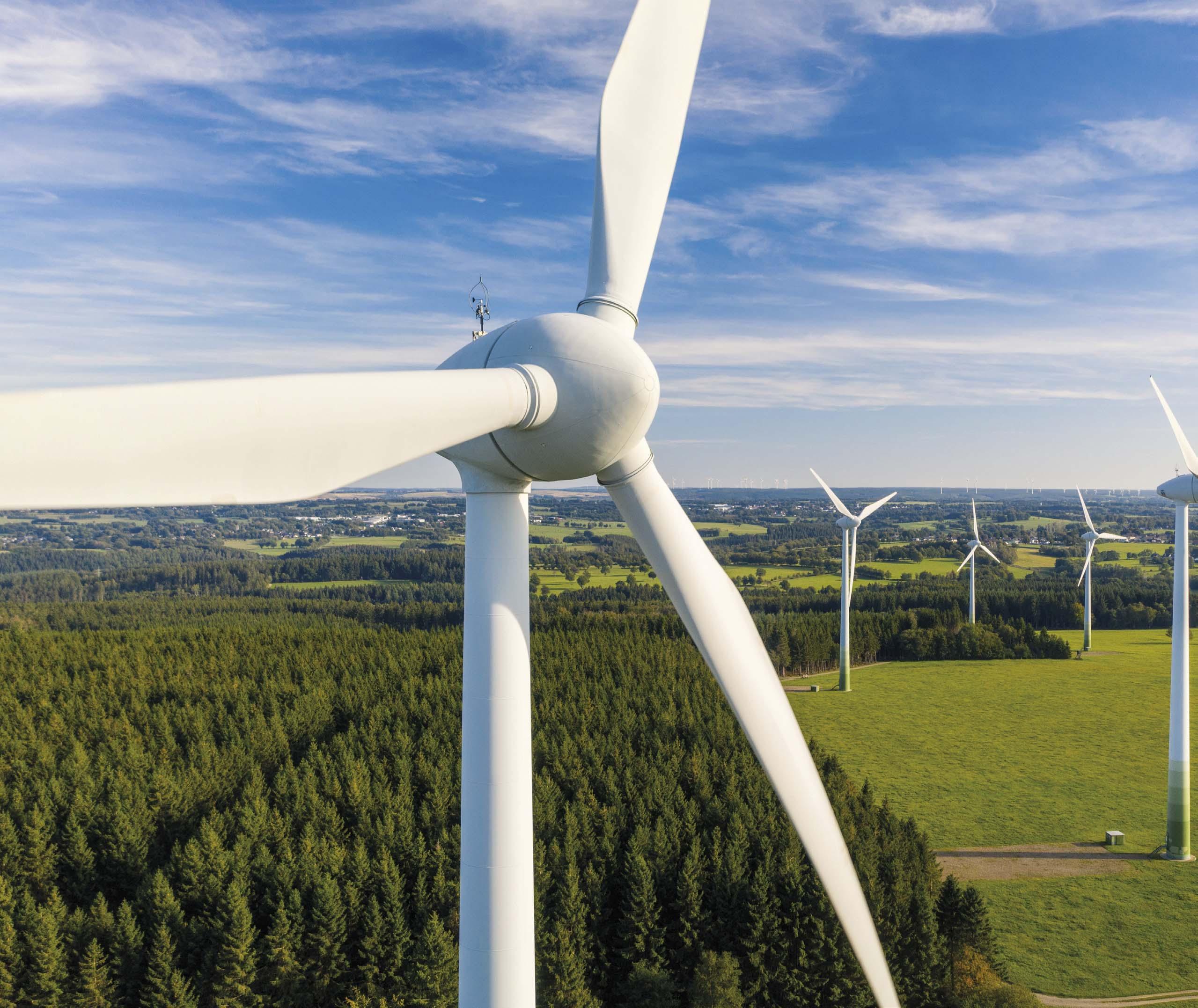
The premier source of the latest information for the renewable energy industry, covering solar, wind, bioenergy and storage.
the clinker cooling process on autopilot. The AI model optimises for energy efficiency while maintaining quality standards and predicting equipment problems before they occur. The proof is in the numbers. Autopilot operation of the clinker cooling process is now empowering CEMEX to realise energy savings of between 2 – 7%, reduce process variability by half a standard deviation, and increase overall yield by 5%.
Conclusion
Like the ethical and fi nancial imperative of decarbonisation, the new business challenges introduced by the COVID-19 pandemic are exerting new and unexpected pressures on the cement industry and forcing businesses to react in new and innovative ways in order to preserve their place in the market. But businesses that are able to adapt, innovate, and rise to the challenge will emerge from the pandemic even stronger than before.
“The pandemic and ensuing global slowdown have presented new challenges for the industry but also new opportunities,” the IFC wrote in its August 2020 report on the impact of COVID-19 on the cement industry. “Even as cement companies adjust to weakened demand, they can reset strategies to better position themselves once the market revives.”
Harnessing real-time operational data and developing the capacity to understand and act on it, is critical for companies that seek to adapt to a fast-changing world. The pandemic may be exerting new pressures on the industry, but the value of taking a holistic approach to data is the same as it has always been. The better processes are understood, the more opportunity there is to improve them.
Global publication
About the author
Martin Provencher is OSIsoft’s Industry Principal for Mining, Metals and Materials. He has more than 25 years of experience in Operations & Maintenance management and information technology. His knowledge of the industry was acquired through the position he held at Aluminerie Alouette, a large aluminium smelter located in Quebec, Canada, as the Operations & Maintenance Manager for Casthouse and Production Services and before that, as the Information Technology & Automation Manager. He has also been an active Industry 4.0 speaker and influencer for IBM as the Quebec Metals and Mining Leader in Canada and lately with Norda Stelo as Director for manufacturing and processing plants. Martin holds a Bachelor’s Degree in Computer Science with Artificial Intelligence focus from University of Quebec in Montreal.
A global industry requires a global publication
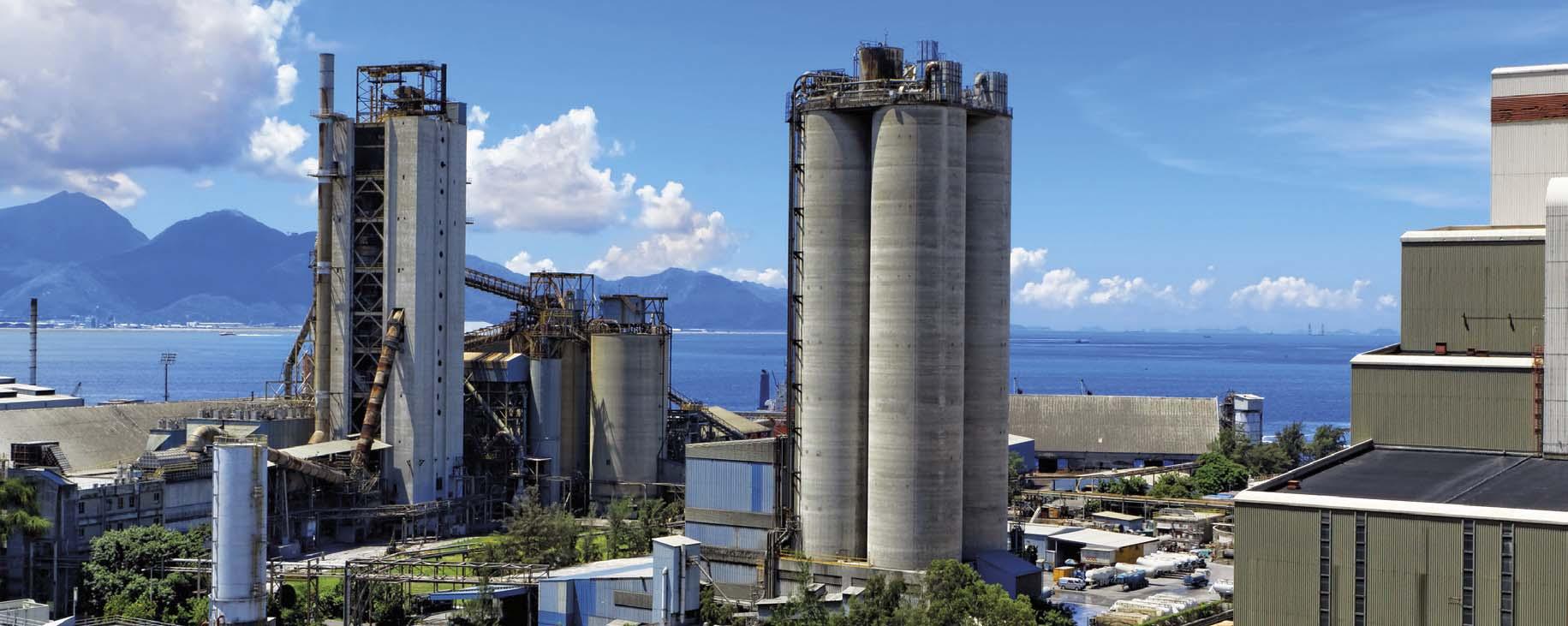

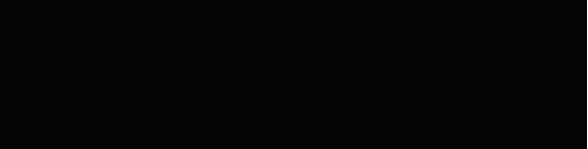

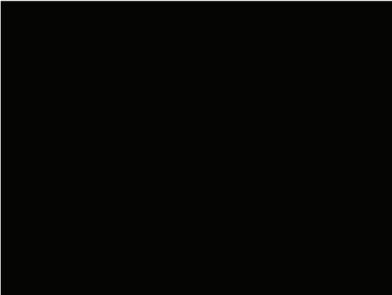
OPERATION
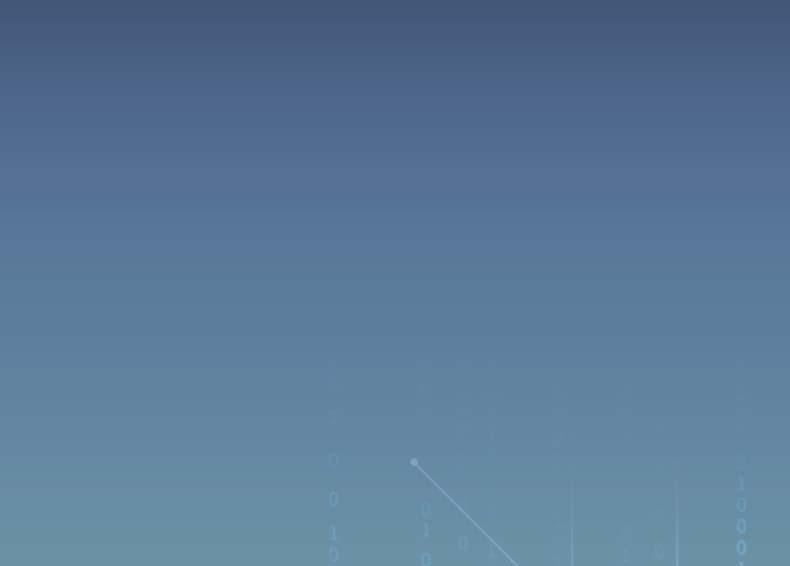
Angus Maclean, Proudfoot, discusses how cement manufacturers could optimise their business operations through Maintenance 4.0 and Target Operating Models.
Target Operating Model (TOM) can be a key strategy in revitalising business and profi tability by optimising, digitising and humanising operations. Developed from improvement potential based on past successful projects, a TOM identifi es ways to maximise business value by focusing on value creation through digital transformation and maintenance optimisation. The visibility it provides helps fi rms tackle business continuity or resilience issues, and it also has the added advantage of being IT supplier agnostic, making it suitable for both new and old businesses across multiple plants and countries.
This article covers the critical steps of designing and developing a best-fi t TOM for cement manufacturers’ unique operational needs, using a specifi c example developed for cement plants to illustrate the process.
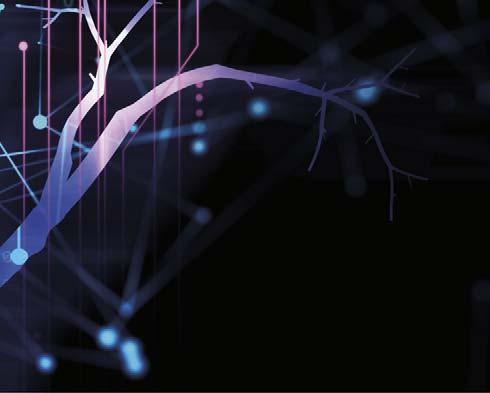
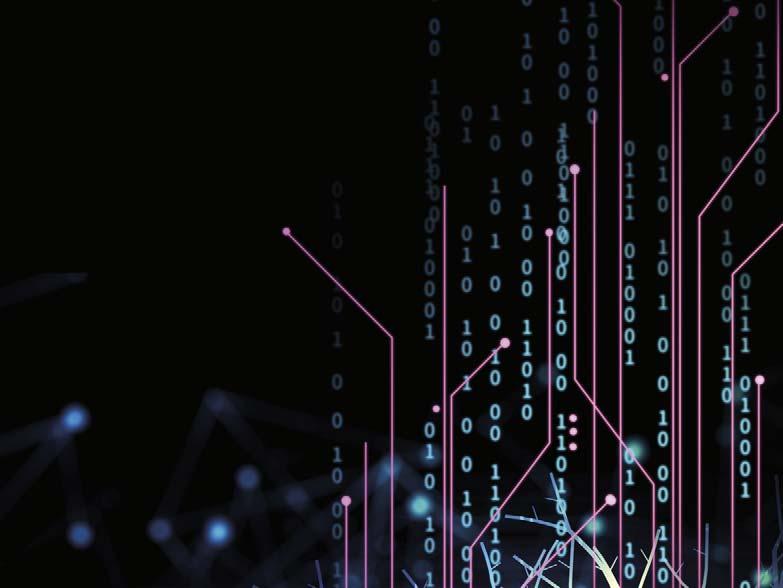
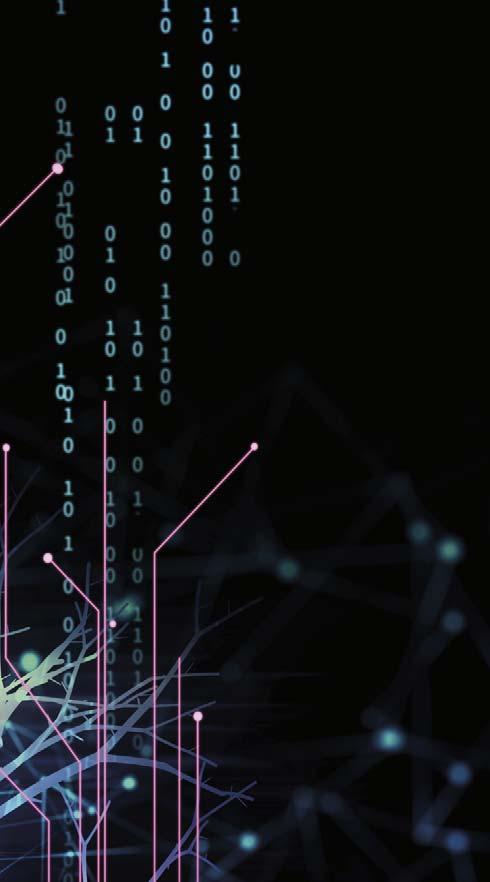
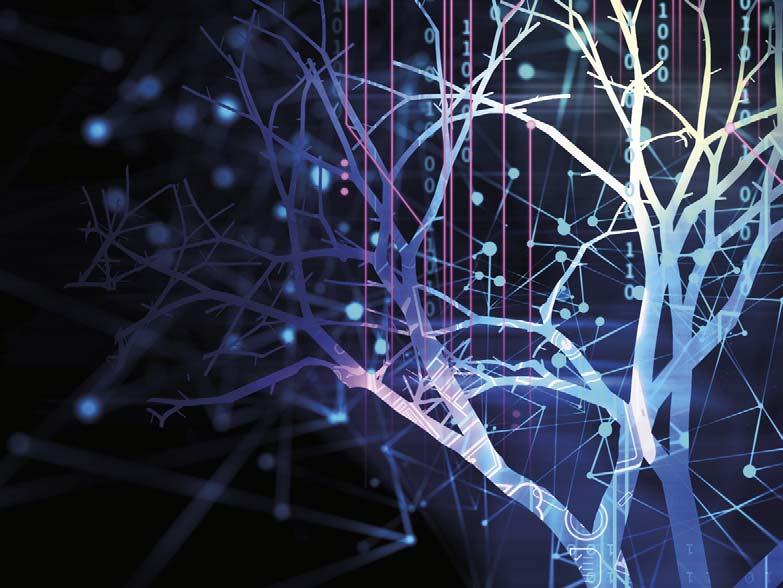
Cement plant target operating models – Maintenance 4.0 elements
Businesses impacted by the recent global crisis have been fi nding innovative ways to bounce back and get ready for a changed world. A key strategy to revitalise business and profi tability is to identify ways to maximise business value by focusing on value creation through operations and digital transformation with new models like TOM for business transformation.
Maintenance 4.0 elements
A TOM service, developed from improvement potential based on successful projects, takes approximately 20 weeks to design, develop and implement, and optimises business operations to create maximum value. Raw materials sourcing, production, maintenance, supply chain, outbound logistics, sales, suppliers, management processes and systems, strategy, and IT-digital capabilities are all critical elements of a TOM.
Operating models are found in most enterprises, whether they are plant, supply chain, logistics, or commercial models. However, very few businesses have end-to-end operating models. Through digitalisation, leaders can achieve signifi cant gains by having one global TOM model incorporating both global and local ‘Glo-Cal’ management elements. A key advantage of TOM is that the model is not affected by technology, making it suitable for both new and old businesses. Its solutions can be IT supplier agnostic.
A TOM provides visibility to help fi rms tackle business continuity or resilience issues – with visibility, management can make effective decisions to reduce costs, improve working capital and forecast their business.
The critical steps in designing and developing the best-fi t TOM include: Defi ning the framework and determining the number of foundation pillars, topics and elements required. Once the framework is determined, the ‘experts’ need to write up the content and how to implement each element.
This content is usually stored in KM clouds for ease of upgrading. Defi ning the maturity diagnostic and training the internal team. Questions are designed to assess the current situation. Proudfoot’s TOM has four levels: Emerging, Basic, Advanced, and Excellent/Sustainable. It is important to keep in mind that a TOM is not a maturity assessment matrix, but the IP and content that is stored in the cloud for each topic and element. Using Proudfoot’s TOM framework, it could take anywhere from six to 12 weeks to determine the element content, whereas it will only take an extra two days to develop the maturity assessment matrix for the content. Once this is done, a workshop format is used to check/assess all the Digital/I4.0 initiatives that are underway and to see what is needed to fi ll the gaps. An assessment of each of the cement businesses. Here, the TOM maturity assessment is used to assess the maturity of sites.



Figure 1. TOM design, development, assessment and implementation process.
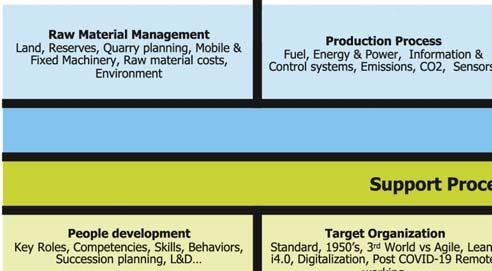

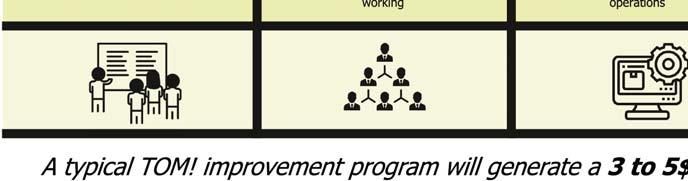
Figure 2. Topics covered in a cement TOM.
Implementation. The actions to improve and the roadmap on how to achieve them are designed (i.e. the Transformation Programme). Proudfoot links to these to performance KPIs to show the results, and the impacts on the P&L/balance sheet are identifi ed (Figure 1).
Maintenance 4.0 for cement plants
Cement TOMs help overcome the end-to-end technical, operational, fi nancial, commercial, digital, environmental, and organisational challenges that cement groups currently face, from the quarry to the client’s site (Figure 2).
A cement TOM typically has four pillars: Operational, Performance, People, and Growth & Innovation, and covers ten topics following the end-to-end process. Each topic is then broken down into multiple elements.
Initial design and development is typically done on Excel for ease of use, but as the model stabilises, it is moved to cloud applications such as Concerto Analytics. Concerto allows for simulation scenarios, multi-plant views, links to ERPs and cloud applications, and is fl exible enough for live large screen or smartphone viewing.
Most often, the model’s Maintenance 4.0 elements are to design, develop, implement or accelerate the new maintenance strategy and operating model by: Optimising the maintenance cost per ton. Increasing equipment availability. Increasing equipment reliability by raising mean time between failures (MTBF). Maximising the lifetime of equipment (optimal replacement CAPEX). Minimising spares and materials inventory value. Increasing the ‘discipline in execution’. Minimising external contractors and providing
‘people’ issues solutions.
When designing the maintenance element, probing questions are used, with an explanation on which best practices routines must be in place to reach each level. The lowest score is used as the fi nal score of the element. Each element is then linked to operational/ fi nancial KPIs and identifi ed if it impacts the P&L or Balance Sheet.
Proudfoot usually operates at two levels: Level 1 covers the key maintenance elements and is used in the overall business TOM. Level 2 allows the maintenance team to dive into much more detail and is often presented in the traditional maintenance pyramid format (Figure 3).
Cement businesses are experimenting with Maintenance 4.0 digitalisation IoT programmes. Some are having trouble getting paybacks, and are having issues related to digital architecture, cloud confusion, network bandwidth and
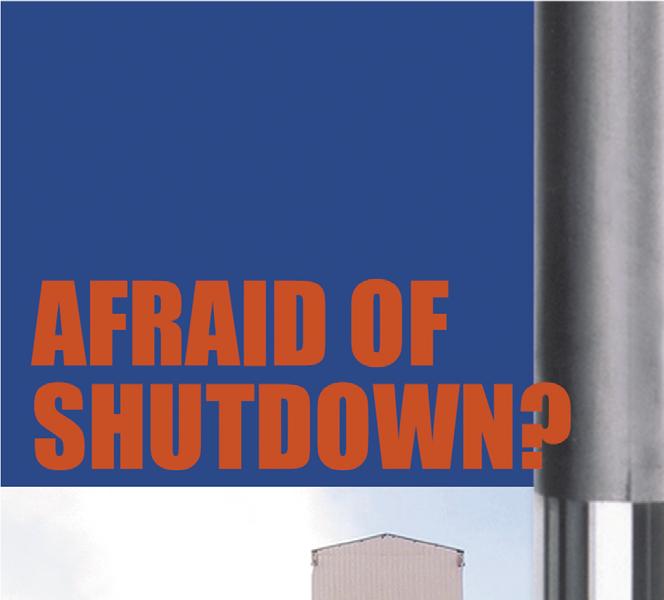
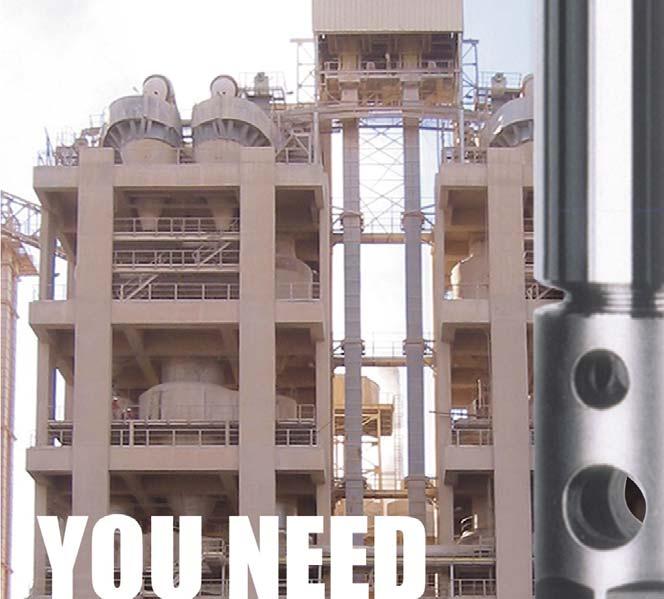
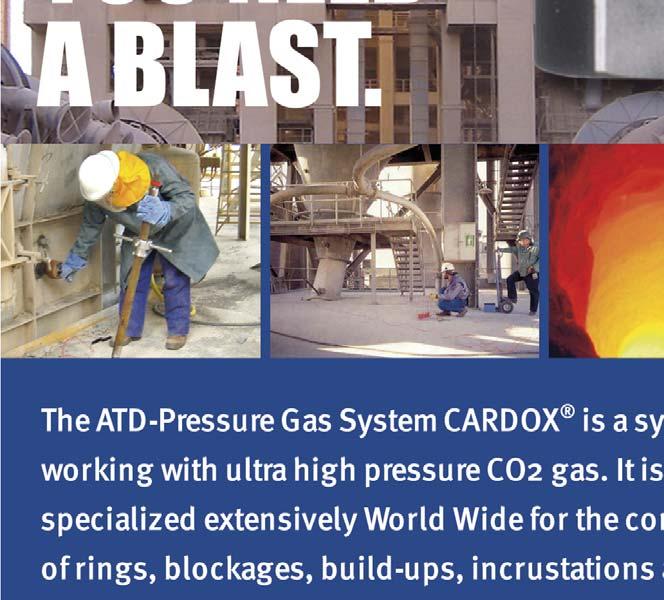

‘discipline in execution’. Proudfoot has seen a number of digitalisation initiatives during its projects, including: Real-time condition monitoring and performance management. Digital maintenance strategy. Predictive maintenance. Remote expert support maintenance. Digitised maintenance workfl ows (including
SOPs). Fleet management systems.
Optimising and digitalising value
Many teams have found that optimising and digitising are key to maximising value creation. But there is a considerable difference between them, and businesses must differentiate clearly between the two. Businesses must fi rst start from scratch to identify and assess the TOM elements and their contributions to value creation in the entire end-to-end value chain. Only then should they start prioritising the best-fi t solutions, whether digital or not.
For example, if a Maintenance 4.0 programme, a reasonable CAPEX budget, and the right digital solutions and resources do not improve sales, a trade-off should be made by investing in a sales-generating digital solution.
Similarly, there has been a proliferation of cloud software from Microsoft Azure to Amazon Web Services along the process value chains among different teams from programming, supply, production, third-party logistics and sales. In the future, this might make data analysis complicated, which is why companies must invest thoughtfully in the right solutions after careful planning and considerations.
Businesses can then generate an improvement roadmap which helps to monetise and estimate the time to benefi t by mapping each initiative. Typically, these are split into 4 – 5 months, 6 – 12 months, 1 – 2 years, and then further into categories such as Smart Operations, Smart Assets, and Smart Workforce.
Operating models are easily customisable for various businesses to obtain the best value creation. A typical TOM improvement programme will generate an improvement of US$3 – 5/t in earnings before interest, taxes, depreciation, and amortisation (EBITDA). The numbers in Figure 4 are average results based on projects that have been completed over the last ten years in cement plants across over 60 countries. As they span multiple plants and multiple countries, TOM provides multinational players a way of accelerating value creation across their organisations.
Conclusion
Figure 3. Example Level 2 Maintenance 4.0 pyramid.
Figure 4. TOM Maintenance 4.0 results.
TOM Maintenance 4.0 elements are to design, develop, implement or accelerate new maintenance strategies and operating models by addressing issues related to people, processes, equipment and technology. With the right TOMs, fi rms can stay agile in the face of disruption. A robust TOM is one that is built upon operational, performance, people, and growth & innovation pillars, and covers the end-to-end value chain. Operating models create value by facilitating operational transparency across the organisation through visualisation of higher level corporate strategy or vision, producing a transformation roadmap that everyone can align with.
About the author
Angus MacLean, Executive Vice President, Value Creation for Construction & Building Materials, EMEA, Proudfoot, is well respected in the industry for his valuable technical expertise in global transformation programmes, procurement excellence, revenue growth, acceleration of cash release, and overall cost reduction. Angus tactically leads teams to meet project goals with agility, and by managing risk, while engaging leaders at every level and creating behavioural change.
