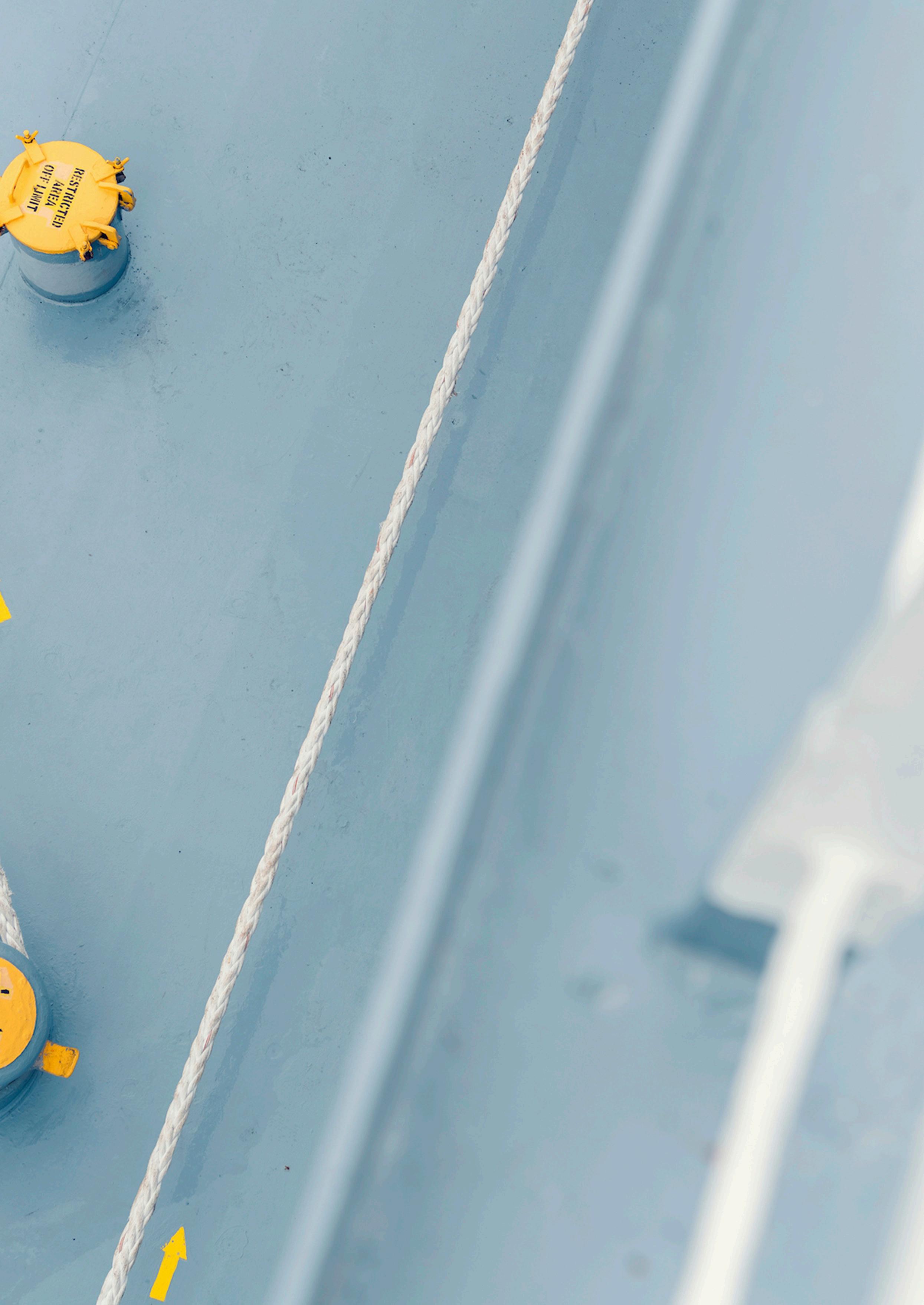
10 minute read
Learning the ropes for mooring safety and sustainability
Veronika Aspelund, Wilhelmsen Ships Service, Norway, considers how investing in better and higher-durability ropes promotes safety in vessel mooring operations, as well as lowering environmental impact and reducing the cost of replacement.
Safety is many companies’ top priority, and Wilhelmsen believes that a more holistic regulatory approach to mooring equipment and practice would help reduce risk to both crews and assets. It will also help buyers better understand which ropes they can and should use. Holistic guidelines should guide their choices not only for optimal operations, but also to promote sustainability as far as possible.
Setting the standard
Up to the present, the Oil Companies International Marine Forum (OCIMF) Mooring Equipment Guidelines 4th edition (MEG4) has come to be regarded as the industry ‘gold standard’ for vessel mooring equipment and operations. Although aimed primarily at tankers and LNG carriers, they are applicable to most other ship types. Multiple other guidelines offered by diverse stakeholders, including terminals, also look to MEG4. From 1 January 2024, the International Maritime Organization’s (IMO) revised SOLAS regulation II-1/3-8 and associated guidelines (MSC.1/Circ.1175) and development of new guidelines (MSC.1/Circ.1619 and MSC.1/Circ.1620) to prevent unsafe work situations during mooring operations come into force both for new buildings and existing vessels. These cover the design, inspection, and maintenance of mooring equipment, including lines and tails.
Rightship also urges vessel operators to implement MEG4 recommendations across their fleets under its RISQ 2.0 Section 10 Mooring Operations.
Bulk carriers, for example, will have to comply with Rightship requirements from 1 October 2022.
Terminals getting increasingly strict
On the terminals side, Wilhelmsen is in contact with leading terminal operators worldwide that are looking to adjust their guidelines based on MEG4.
Terminals are primarily concerned with ensuring the safety of port workers and preventing expensive accidents, such as a vessel drifting following a line breakage and blocking an approach channel. In their notices to ships’ masters, terminals typically insist that mooring ropes are in good condition. They focus mainly on inspections on board or request photos of ropes. Ships with ropes in poor condition, or ropes that do not comply with the terminal requirements, run the risk of being refused.
Most bulk terminals now specify that ropes should be used for five years only, to reduce the risk of breakage. However, Wilhelmsen is of the opinion that if a vessel selects high-end rope products designed for 8 – 10 years of use, it is a waste of money to replace them after only five years. Thorough understanding of individual products and optimal line management can avoid penalising good performers.
Durability and usability
With regard to LNG carriers, investing in more durable ropes with better usability is key for mitigating risk in mooring operations. Rope longevity is also an important factor in reducing waste and materials usage in rope production, while reducing overall cost of ownership. High-performance mooring ropes made from high modulus polyethylene (HMPE) offer the best strength-to-weight ratio in the market. At equivalent strength, an HMPE rope is seven times lighter than steel wire and three times lighter than a polyester rope. This increases its usability while reducing the total time spent by crew members on mooring operations and fuel consumption. HMPE ropes are more expensive than most other fibre ropes, although prices can vary significantly between manufacturers. However, when evaluating what investment to make, operators should consider not only differences in price but also in performance and expected lifetime, which has a lot to say in terms of the global ecological impact of rope production and total cost of ownership.
Rope performance and sustainability indicators
When it comes to selecting a HMPE mooring rope, vessel operators should consider the following factors: abrasion resistance, linear density and diameter, and strength-to-weight ratio.
Rope abrasion
Rope abrasion is one of the most common issues that affects rope longevity. Abrasion can be identified by the visible fraying on the rope, which will ultimately lead to breakage if the process continues. The ability of a rope to resist abrasive damage from rubbing against mooring equipment is critical to prolonging its usability. Abrasion also leads to the release of particles into the ocean, which is harmful to marine life. A rope with better abrasion resistance will release less material over time, reducing its environmental impact.
In addition, quality ropes with high abrasion resistance will not need to be replaced as often. This allows operators to avoid complex recycling and disposal processes while reducing waste and damage to the environment.
Linear density
Linear density is the measure of the weight of the rope per unit of length (g/m). Ropes with a lower linear density are much easier for crew members to handle on deck and require less material to manufacture, reducing their overall resource footprint. While some variation from the nominal diameter is to be expected, vessel operators should note that a large variation from the nominal diameter is likely indicative of a higher amount of material used to achieve the desired rope strength. This results in a larger diameter, and consequently a higher linear density and higher product footprint.
Strength-to-weight ratio
In regards to strength-to-weight ratio, the breaking load of a rope is the maximum force under tension the rope can withstand until it breaks. The higher the breaking load, the greater the force the rope can withstand. At equivalent strength, ropes with a lower linear density require less materials to produce, which means less materials going to waste. Again, it is also lighter in weight and easier for the crew to handle.
Practical implications
Abrasion resistance and the amount of material used in the manufacturing of each rope affect long-term costs and environmental impact. It is thus important for shipowners to consider the performance of ropes very carefully before making a purchase decision. There is a large variation in unit cost of the ropes. The company’s own analysis shows that the most expensive rope is twice as expensive than the cheapest alternative, but larger variations are possible. However, in order to evaluate the total cost of ownership of the ropes, it is more relevant to look at the total cost of ropes over a longer period of time. Ropes with a longer lifespan usually offer the lowest cost of ownership.
Importance of rope maintenance
Constant wear and tear impacts the life of all types of ropes. A rope is chosen from strength when new, and the effect of use on that rope is often not taken into consideration. Taking proper care of long-lasting, high-performance ropes serves to enhance their longevity. Equipment on new ships should also be designed to help ropes last longer. There are some unfortunate examples of designers and builders trying to save money by cutting corners, resulting in equipment that can weaken ropes more quickly. To this end, Wilhelmsen collaborates not only with customers but also ports and terminals, unions, and class on rope design.
Long-term mooring partner
Wilhelmsen does not stop at delivering high-quality ropes, however. The company offers a total solution including service, inspection, and testing, as well as its dedicated Line Management Plan (LMP) software. The LMP

Making clean energy network a reality.
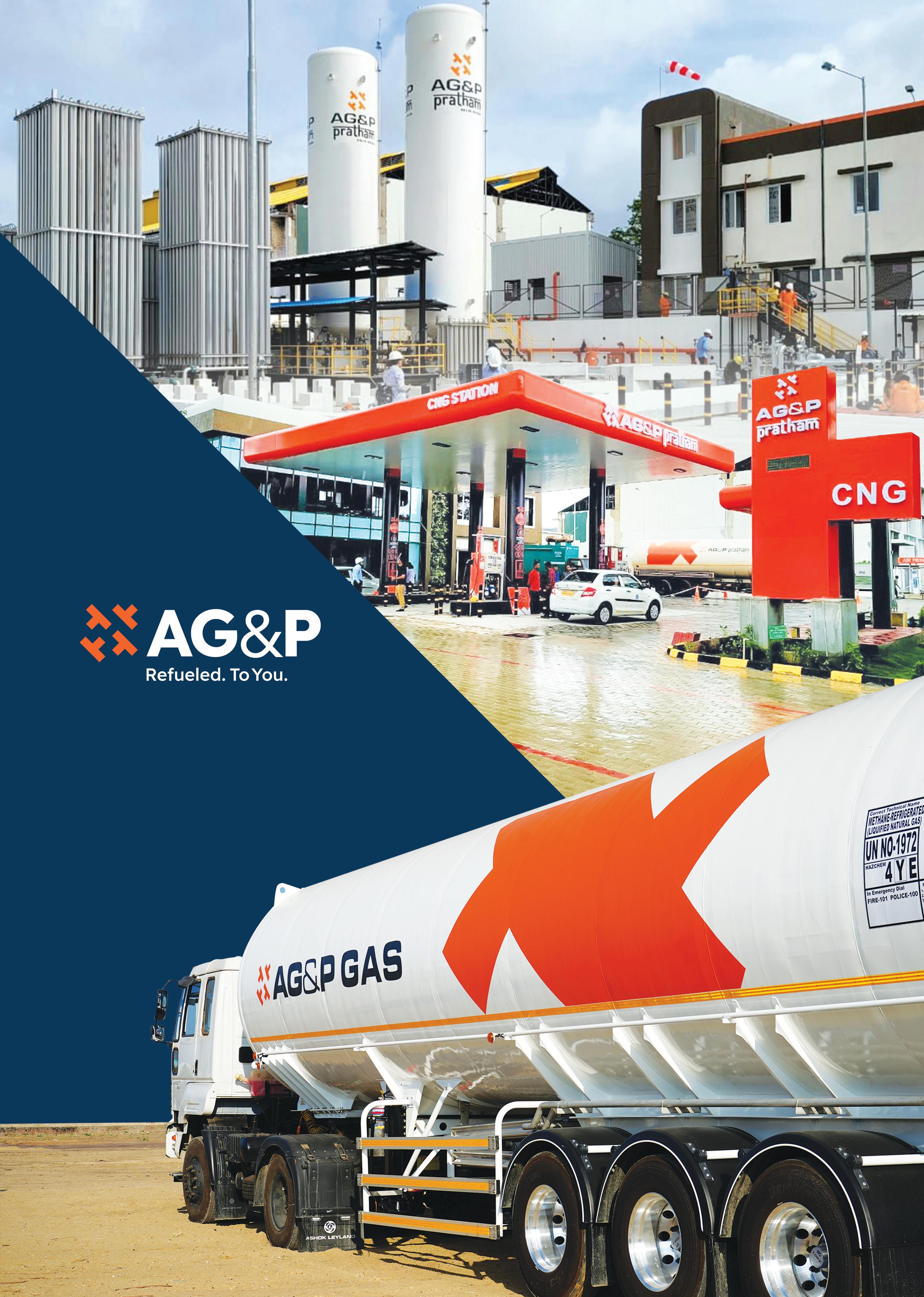
logs everything a vessel operator needs to show terminal inspectors in one place, including inspection data, certification, documentation, and mooring hours. Users can also add data on ropes produced by any manufacturer in addition to Wilhelmsen. Regular inspection and testing, in combination with info from the LMP, provides optimal oversight and a foundation for better decision making. Even though it is impossible to know the full load history of the rope in detail, good decisions are based on all the information available.
It is also important to bear in mind that rope management is unique to each individual vessel, considering the different forces acting on lines in different situations, such as being moored at a terminal in bad weather. And even if operators/terminals invest in sensor technologies that sound an alarm when there is high tension on a line, they can still snap on low loads with no alarm sounding due to previous overload. In those cases, there is no forewarning of an accident, which makes proper management essential.
In the LNG context, requiring the highest standards of compliance and safety documentation, it is even more important that mooring lines be tested regularly and hold MEG4-compliant certification. Wilhelmsen has 40 service engineers in ports around the world to carry out inspections. One particular challenge for LNG carriers is elongation of lines on exposed moorings. Ropes or parts of ropes can be sent to the company’s test laboratory for further destruction testing to test the residual strength of those ropes. As recommended by MEG4, the company advises ropes should be replaced if they are found to be below 75% of their original strength.
Investing in new technology
Wilhelmsen can also step in to address key challenges on ropes and mooring operations generally such as when operators are using a certain terminal for the first time and require back-up expertise on regulations and products. Its conclusions are underpinned by a strong R&D heritage and it is also involved in creating ISO standards, Cordage Institute (CI) standards, and work on technical and sustainability issues as a member of Eurocord and the CI.
Wilhelmsen is also investing in a new technology project leveraging artificial intelligence and machine learning to simplify rope inspection. The application will enable vessel crews to submit photos of ropes on board and get insight on the severity of damages observed on the ropes, reducing the risk of conflicting subjective judgments and providing an independent assessment of their condition.
Striving towards circularity
While the company’s focus is on investing in and producing ropes that last for longer, it is also tackling the problem of dealing with end-of-life ropes. Today, there are no good sustainable solutions for reuse or upcycling. The best case is that retired ropes are returned and incinerated, but many are discarded and end up as part of the growing sea of marine plastic litter.
As a responsible producer, Wilhelmsen is working, firstly, on a model for return of ropes, and secondly, piloting a circular solution for retired ropes through its Circular Rope Project, which is part of a joint project between the Norwegian government, IMO, and UN Food and Agriculture Organization (FAO) called GloLitter Partnerships. The initiative involves identifying applications that do not use too much extra energy in the recycling process. If it can be shown how retired ropes can be reused or upcycled, a path can also be shown for reusing other types of marine litter. If the pilot succeeds, the company aims to be able to bring 10 000 tpy of retired ropes into circular solutions.
Quality ropes that last
Wilhelmsen takes its impact on the environment very seriously, and is constantly taking steps to design high-quality, long-lasting products to reduce waste and environmental damage.
The company’s Timm Acera mooring ropes can offer significant cost savings over long periods and, thanks to their abrasion resistance and strength-to-weight ratio, will have a lower impact on the environment and a lower long-term cost of ownership compared to other HMPE ropes on the market, making them well-suited in the LNG carrier context.
The Timm Acera solutions for LNG carriers also includes its proprietary Snap Back Arrestor (SBATM) technology designed to significantly reduce the risk of rope ‘snap back’, which poses serious dangers for both vessel crew and quayside workers. The MEG4 guidelines were created based on the learnings from the accident on the LNG carrier Zarga while it was alongside at the South Hook LNG terminal in the UK in March 2015. That was a snap-back accident following a mooring line failure where a deck officer was badly injured, so the SBA fulfils an urgent need to improve mooring safety.
Figure 1. Timm Acera ropes with the Snap Back ArrestorTM safety feature.
Conclusion
Wilhelmsen’s key value proposition for customers is producing high-quality, durable ropes that facilitate safe mooring operations in line with MEG4 while offering optimal cost of ownership over time. By striving to minimise materials wastage during the production process and exploring novel ways to reuse and upcycle retired ropes, the company also aims to promote circularity and reduce marine plastic pollution, thereby contributing directly to customers’ own sustainability targets.
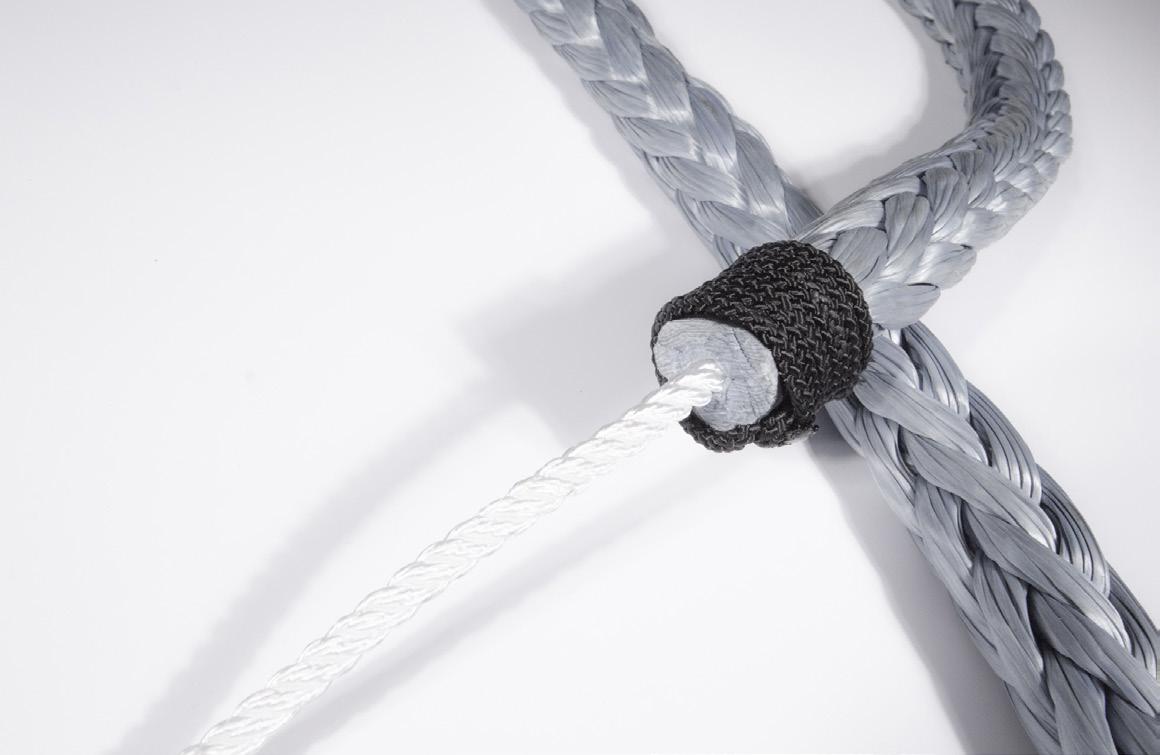