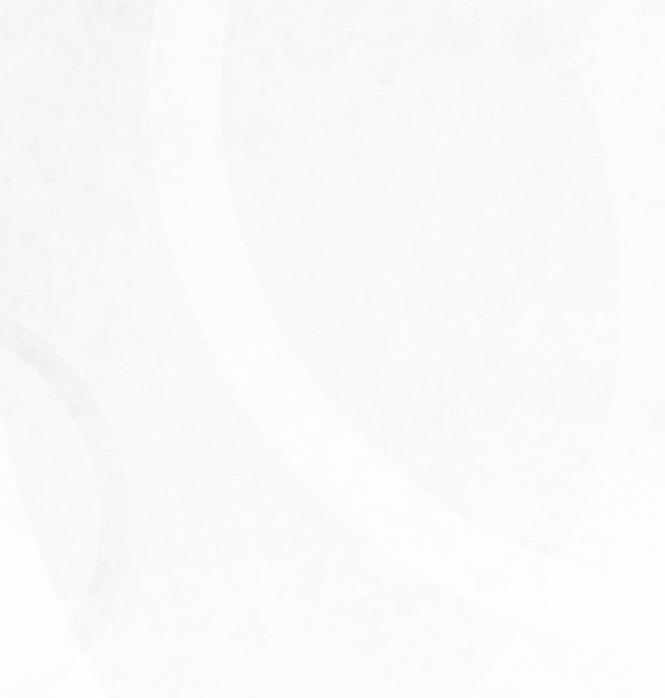
25 minute read
Catalyst Q&A
Explain why catalysts are so crucial to refining and petrochemical operations.
What are the main applications of your company’s catalysts or catalyst technologies within the downstream sector?
Rajesh Gattupalli, Honeywell UOP
Dr Meritxell Vila, MERYT Catalysts & Innovation
Dr Detlef Ruff, BASF

Lars Skyum, Haldor Topsoe A/S
The introduction of catalysis in 1933 changed refining by introducing a new capability to processes that had been governed only by pressure, temperature and time. Catalysts made it possible to break and rearrange molecular bonds to produce specific products. Since that time, catalysts have been made more efficient and selective. Just by coming into contact with a catalyst, hydrocarbons can break apart, combine, and rearrange themselves into different molecules. New catalysts rely on the invention of new materials to provide greater activity, reliability and durability.
Catalysts are crucial, not only in refining and petrochemical operations, but also in around 90% of all chemical processes. Thanks to the fact that they decrease the activation energy of the chemical reactions, increasing their velocity, we can carry out the desired reactions under milder operation conditions. Therefore, thanks to them, we can perform our desired reactions at lower temperature and pressure and we can obtain our products in less time. Consequently, we can consider catalysts as the biggest energy savers in the industry.
Therefore, catalysts are our best allies to maximise the profitability of our processes, because any improvement in the catalytic system (the catalyst together with the reactor design) has a direct impact on the yields, selectivity and the energy consumption of the reactions.
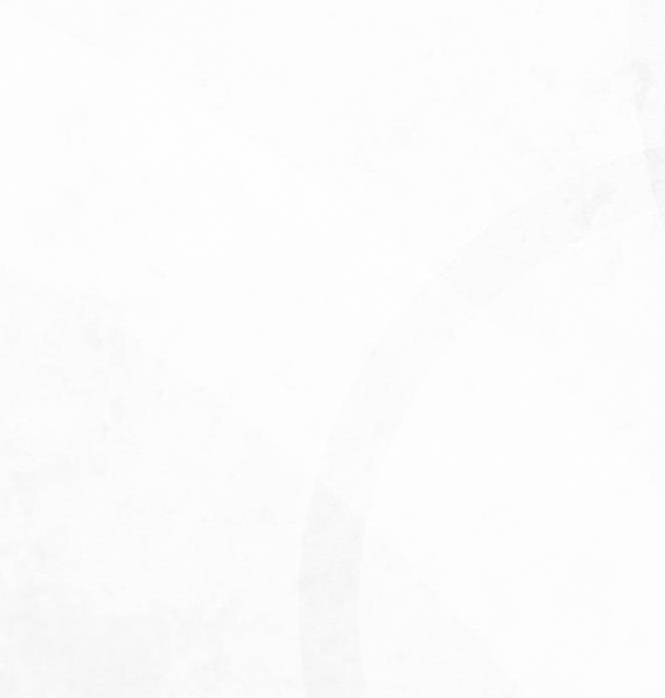
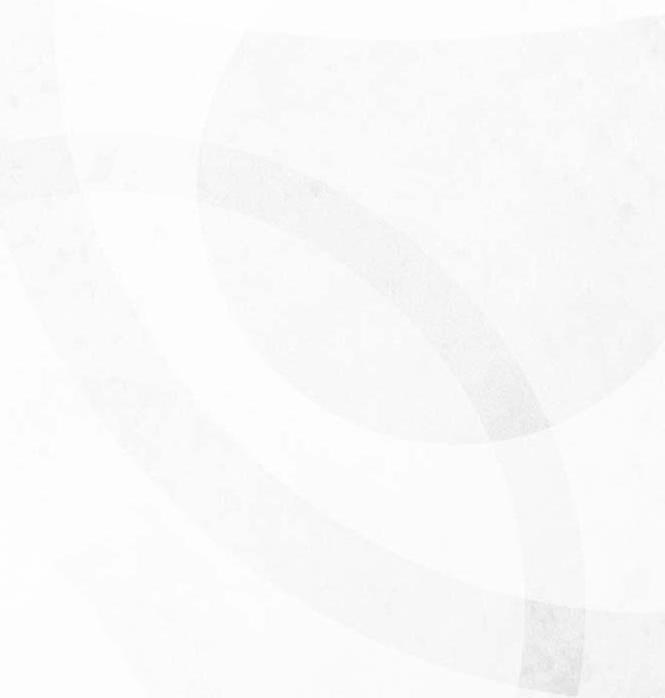
The catalyst division of BASF has a broad portfolio of products and services to support the downstream refining and petrochemical sector, which includes FCC catalysts and additives, a core suite of petrochemical catalyst solutions and adsorbent solutions. The portfolio covers selective hydrogenation catalysts for applications from C2 to C5+ hydrocarbons, Aromatics/olefin saturation catalyst and products for de-aromatisation, alcohol production, guard beds (sulfur, Cl, F), gas processing (removal of Hg, mercaptans, C6=, BTX and water), amine catalyst and olefin purification. BASF also facilitates the scale up and production of customer-specific catalyst formulations to meet customer-tailored requirements.
The refining industry continues to develop with dynamic technology changes influencing the productivity and needs in the industry. BASF remains an innovative long-term partner in the industry, meeting customers’ needs with excellent service, product innovation and technical refining expertise. Our goal is to be the partner of choice for refineries that energise the world.
Topsoe is a leading supplier of catalyst and licensed technologies used for renewable fuels, hydroprocessing, ammonia, methanol, and hydrogen technology. This includes blue and green offerings of all of these technologies. We also have catalyst and technologies available for removal of SOX, NOX and particulate matters from flue gasses, and catalysts for production of sulfuric acid.
In the hydroprocessing space we can supply the entire portfolio of catalysts: grading material for pressure drop control and protection against bulk catalyst contamination, all types of hydrotreating catalysts used in the naphtha to resid range (straight-run as well as cracked feedstocks), naphtha and diesel selective hydrocracking catalysts, and diesel dewaxing catalysts. For the processing of renewable feedstocks, Topsoe, as a part of our licensed Hydoflex technology, developed a whole family of tailor-made grading, hydrodeoxygenation (HDO) and dewaxing catalysts. For refiners, we also supply all catalysts used for hydrogen production. Furthermore, we have catalysts for claus tail gas treatment, benzene saturation and other petrochemical catalysts.
For methanol and ammonia plants, Topsoe is able to supply licensed technologies and all front-end and synthesis catalysts.
Rajesh Gattupalli, Honeywell UOP
UOP catalysts are used in a wide range of applications – to treat or purify feedstocks in preparation for subsequent catalytic processes that crack or rearrange hydrocarbons into new and homogeneous forms. These catalysts produce intermediate feeds for fuels production, performance enhancing additives such as alkylate and MTBE, and aromatics and olefins and other chemicals that are the basis for plastic resins, films and fibres. They are also used in a wide range of emerging sustainable energy processes including renewable fuels, hydrogen production, and carbon capture technologies.


Dr Meritxell Vila, MERYT Catalysts & Innovation
At MERYT Catalysts & Innovation we provide a wide portfolio of catalysts and adsorbents for refineries and petrochemical processes. The catalytic processes that we cover are FCC, hydrocracking, hydrotreatment, catalytic reforming, syngas, isomerisation, hydrogenation, dehydrogenation and etherification. We also supply selective adsorbents for purification of the different refinery and petrochemical plants streams.
Additionally, we provide selective catalytic reduction (SCR) technology for NOX emissions reduction in refinery and chemical plant furnaces.
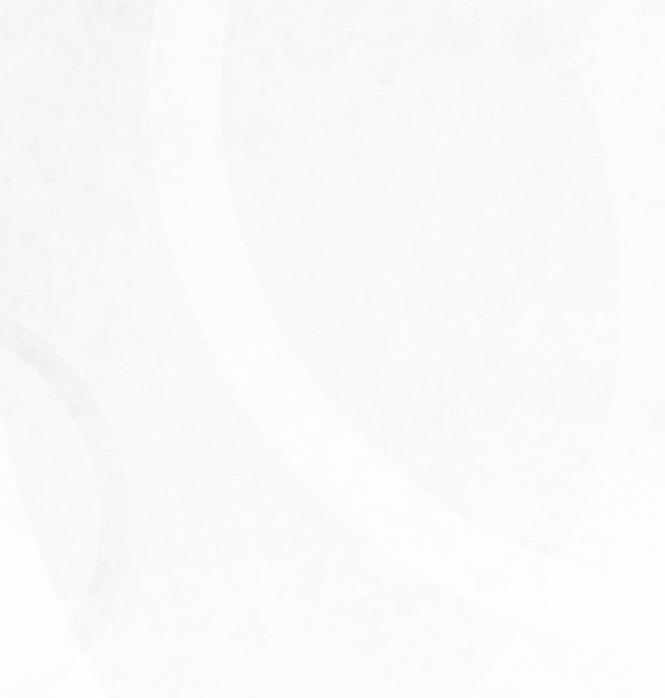
To what extent has the downstream catalyst/precious metals market changed over the past five years?

Dr Detlef Ruff, BASF
Excluding 2020, the overall refining and petrochemical catalyst market has continued to grow in the past five years in particular, driven by rising standards of living, population growth, and increasing demand for petrochemical products. Regulations have continued to evolve which has provided new opportunities in the catalyst market to support achieving tighter fuels specifications (IMO requirements for sulfur, gasoline sulfur, and octane), air emissions requirements, improved sustainability through renewable fuels processing and to adjust yield slates in support of these and other refining objectives. Additionally, the market continues to see moves towards more integrated petrochemical complexes and a shift in growth to the Asia Pacific and Middle East regions. As the need to achieve higher fuel economy standards and a focus on controlling greenhouse gas emissions becomes more important in North America and Europe, we see new opportunities to introduce new catalytic solutions and to support customers as they optimise their refinery operations.
More development has occurred in the last five years than in the previous 20. Refiners today are looking for catalysts that support process intensification, with greater efficiency than existing catalysts and that can perform multiple chemical conversions in a single step. As a result, refiners can process more feedstock with fewer and smaller units, requiring less real estate, equipment and energy.
The biggest changes to the platinum group metals (PGM) market over the last five years have been price volatility, elevated interest rates for leasing PGM and the overall availability of high-purity forms of these metals. Over 85% of all palladium above ground on earth is in automotive catalytic convertors, along with a substantial amount of platinum and rhodium. Sabin is not involved in the recycling of autocat, but we do share a common problem with that industry: a growing amount of ‘contamination’ in the catalyst feed arriving for recycling. In the autocat recycling industry, the introduction of tungsten (W) and silicon carbide (SiC) into the convertors to achieve higher emission control standards many years ago has resulted in processing challenges for the recyclers now that those older cars and convertors are being scrapped. In the petroleum and petrochemical industry, the problem is carbon (C) and coke. In past years, the catalyst user performed a ‘pre-reclaim burn’ in situ to reduce carbon contained, but many clients now leave the carbon mitigation to the precious metals recyclers. These two issues (increasing SiC and W in automotive catalysts, and increasing C in alumina-based petroleum/petrochemical catalysts) have combined to create huge recycling backlogs, higher treatment costs, and bottlenecks in the both the availability of palladium and recovery streams of PGM overall.
Rajesh Gattupalli, Honeywell UOP

Brad Cook, Sabin Metal Corp.

How can catalyst technologies help companies meet the challenge of increasingly competitive conditions in the downstream sector?
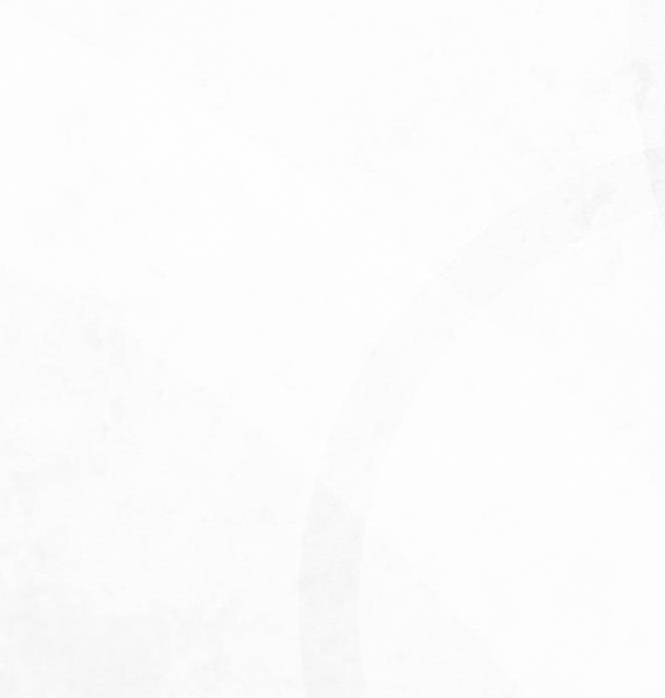
Rajesh Gattupalli, Honeywell UOP
Because catalysts are integral to process technology, newer and more capable catalysts can signifi cantly improve the economics of refi neries and petrochemical plants with reduced energy and water consumption, producing fewer low-value byproducts, and accommodating a wider range of feedstocks. They also facilitate the production of more sophisticated products as demand patterns change. This affords refi ners improved operating margins and slate fl exibility so molecules can be directed to processes where they will generate the greatest value. This is most evident with catalysts that can be used in existing capital assets – essentially reprogramming a refi nery to make new products without signifi cant capital investments.
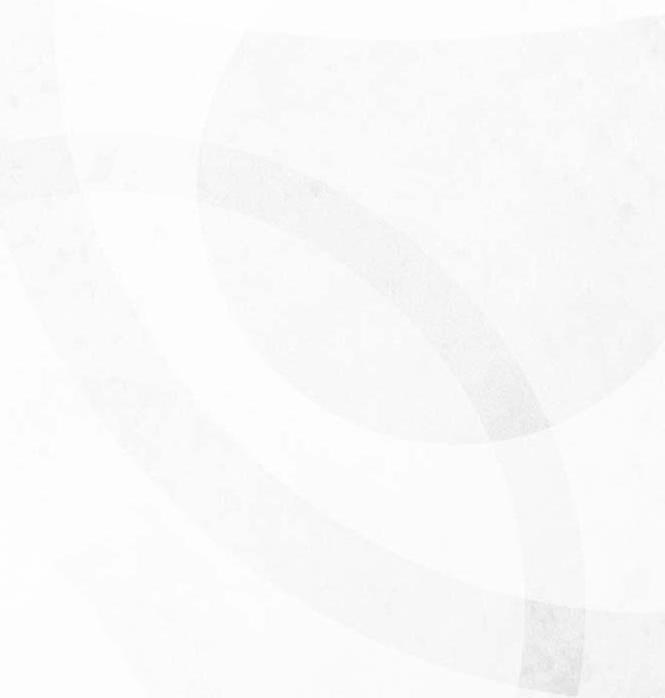
Dr Meritxell Vila, MERYT Catalysts & Innovation
Catalysts play a key role in the production scheme. Depending on them, we can have longer cycle lengths, lower hydrogen consumption (in hydrotreatment units), more propylene production (in FCC units), more cracking and therefore
more yield (in hydrocracking reactors), etc. Each process has its key variables to make it more profitable, meaning that there are a lot of variables to consider, including the price of the catalyst. In consequence, the selection of the right catalytic scheme for every one of our processes can increase our margin very importantly, improving our competitiveness.
In the refining sector now more than ever, catalysts play this key role, as the margin is lower than years ago. Every small improvement matters.
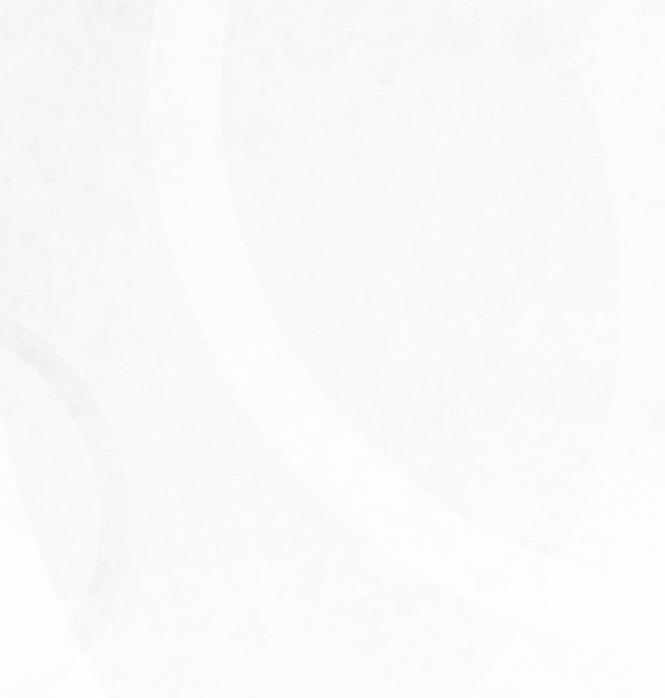
How can catalyst technology help companies meet strict environmental regulations?

Dr Detlef Ruff, BASF
BASF’s catalyst technologies directly reduce the impact of SOX and NOX emissions in the FCC unit. BASF offers SCR catalyst for NOX reduction, and other products such as the low NOX CO Promoter for NOX reduction and SOX reduction additives, like EnviroSOx, to reduce regenerator SOX emissions. Additionally, as constraints or requirements develop in the operational or regulatory environment, new catalytic solutions are developed to meet the new requirements and to help refiners meet environmental requirements.
Lars Skyum, Haldor Topsoe A/S

There are several environmental regulations for which there are catalyst-based solutions. Some are single-parameter specifications, such as caps on diesel sulfur content. Others comprise a broad set of requirements and incentives. An example is the renewable fuel standard (RFS) programme in the US, which aims to reduce greenhouse gas emissions.
Meeting some regulations may provide a payback if catalyst technology is applied. By reducing required operational temperatures and pressures, catalysts reduce energy requirements while also reducing production of CO2, NOX, and SOX. Improved catalysts intensify these benefits while also extending catalyst cycle life. Catalytic hydrotreating and hydrocracking continue to lead the way in producing ultra-low sulfur diesel (ULSD) and low-sulfur gasoline from ever more difficult feedstocks. The most significant recent driver is the IMO 2020 rule, which lowered the allowable sulfur content of marine fuel oil from 3.5 wt% to 0.5 wt%. The same catalyst technologies are also used to convert a wide array of plant-derived oils and waste products into renewable fuels and chemicals. Haldor Topsoe is a successful licensor of renewable fuels technology for 100% renewable fuels production (grassroots and revamps) and for co-processing, with a total of more than 500 000 bpd of production capacity licensed.
Catalytic mercaptan oxidation improves the sweetness of light fractions, such as LPG and naphtha, allowing them to meet product and pipeline specifications. SOX transfer additives decrease FCC SOX emissions by moving SOX from the regenerator to riser/reactor, where it is converted to H2S. The H2S is recovered and transported to a sulfur plant, where it is converted into elemental sulfur. Other catalytic processes, such as SNOX, reduce NOX and SOX in flue gases. Many catalytic processes contribute to meeting gasoline specifications by producing blend components with low benzene and low Reid vapour pressure (RVP). These include alkylation, isomerisation, and catalytic reforming. New alkylation processes employ ionic liquid or solid-state catalysts, which decrease utility requirements and reduce acid wastes.
Looking into the future, we are striving to stay ahead of the curve – by exploring the boundaries of science, continuing to provide excellent products, to anticipate greenhouse gas regulations by decreasing NOX and CO2 emissions, and to further develop promising carbon emission reduction technologies.

Rajesh Gattupalli, Honeywell UOP
Because catalysts are the heart of most refining processes, we’re developing new catalysts that provide more cost-effective, lower environmental impact ways for refiners to produce the next generation of cleaner-burning fuels. This involves measurement of ‘six efficiencies’ – the highest value use of carbon and hydrogen, the lowest emissions of CO2, the lowest requirements for utilities and water, and the highest return on capital. Catalyst systems with higher activity, stability and selectivity are critical to meeting these objectives.
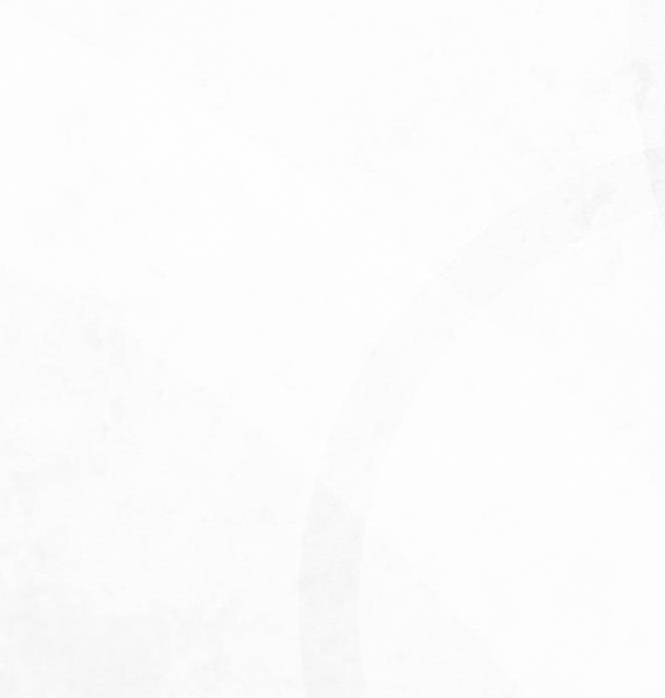
Dr Meritxell Vila, MERYT Catalysts & Innovation
Catalysts have been helping companies to meet environmental regulations since these started. For example, the MTBE catalyst was developed to substitute tetraethyl lead in the 1990s when lead was prohibited as an octane booster in gasolines. Hydrotreatment and hydrocracking catalysts help refi neries to reduce sulfur content in different fuels and have improved its activity to the required environmental regulations. For example, in Europe during the 1990s, diesel was allowed to contain 2000 ppmw of sulfur, whereas currently it must contain less than 10 ppmw. This reduction has been possible thanks to an impressive improvement in catalyst technologies. Other examples include the production of biofuels, where it is necessary to hydrogenate vegetable oils and other types of diffi cult feeds. Other very helpful and necessary catalysts can be found at sulfur recovery units, as these catalysts allow refi neries to meet the strict regulations of sulfur emissions at the stack. Catalysts can help us meet most of the strict environmental regulations.
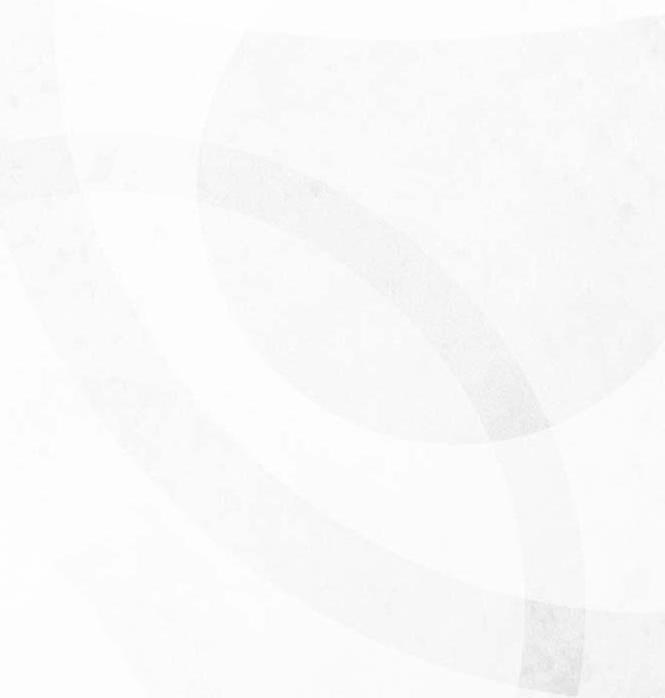
How will catalytic solutions help advance the growth of hydrogen production?
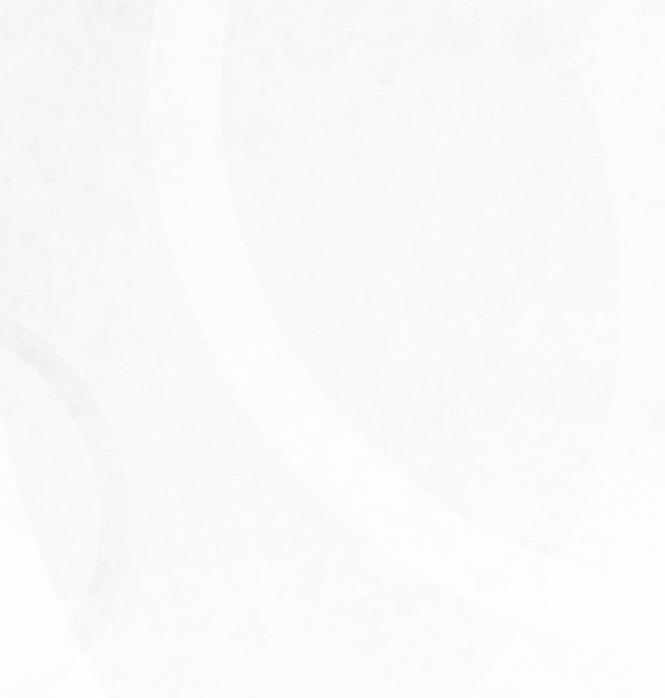
Lars Skyum, Haldor Topsoe A/S
Topsoe has developed a number of new catalysts for hydrogen production focusing on improving the economics for hydrogen producers.
Many hydrogen plants today are restricted by the minimum steam-to-carbon (S/C) ratio they can operate at due to the limitation of traditional iron chromium based high temperature shift (HTS) catalysts. By introducing the new SK-501 FlexTM HTS catalyst formulation, Topsoe has been able to remove this limitation and at the same time increase the catalyst activity level.
For plants operating at maximum throughput, this means that a more fl exible catalyst enables operation at a higher feed rate with a lower S/C ratio, which results in more hydrogen production from the plant. In other words, the SK-501 Flex is a non-CAPEX revamp for more hydrogen production.
In addition to the increased S/C ratio fl exibility, the new formulation of SK-501 Flex also puts an end to the health, safety, and environmental risks associated with handling and managing hexavalent chromium when compared to traditional HTS catalysts as it is 100% chromium free. Ultimately, there is no risks of exposure to hexavalent chromium during loading, operation, unloading, or fi nal disposal of the catalyst.


Dr Meritxell Vila, MERYT Catalysts & Innovation
Hydrogen production is absolutely linked with catalysts. There are several ways to produce hydrogen, but almost all of them are related to catalysts and/or adsorbents. The most traditional and established is the steam reforming of natural gas, naphtha, heavy fuel oil or coal. Although this is a mature technology, it is still the most economic one, and so we can expect it to be used for a long time, and any improvement in the catalysts involved will have a great impact in the process.
Hydrogen is also obtained by electrolysis of water, and if the electricity comes from renewable sources, we obtain green hydrogen. In this process, we have many different electrocatalysts, currently based in noble metals. There is a lot of research in order to improve these technologies, fi nding alternative non-noble metal electrocatalysts, to make this process more profi table.
Other hydrogen catalytic production processes are photocatalysis (obtention of hydrogen from water and sunlight), reforming of ethanol and sugars and cellulose biomass processing. All of these processes are the subject of deep research to increase the production of hydrogen.

What has been your company’s biggest recent achievement or innovation in terms of catalytic solutions?
Dr Detlef Ruff, BASF
At BASF, innovation never stops as our customer needs are continuously evolving and new products, services and optimisation efforts are required to meet emerging economic needs, operation constraints, and regulatory requirements.
The biggest achievement in the industry remains the ongoing innovation achievements and focus on continuously applying the new innovations to meet the market and specifi c customer needs. BASF Catalysts’ commitment to innovation and excellent technical service is in-tune with the ever-changing market and customer needs. The company continuously innovates and commercialises new products, supported by a global technical service group to ensure that BASF’s products and offerings deliver immediate value at individual customer sites. Innovation is a driving force that enables BASF’s customers to be more successful. BASF is pleased with our recent achievements in the past several years to deliver many groundbreaking new technologies (Valor®, Multiple Framework Topology, AIM, Improved Zeolite Y, Boron Based Technology) and products (FourtuneTM, Fourte®, ZEAL®, Altrium® and the application of Valor®) that have enabled customers to be more successful.
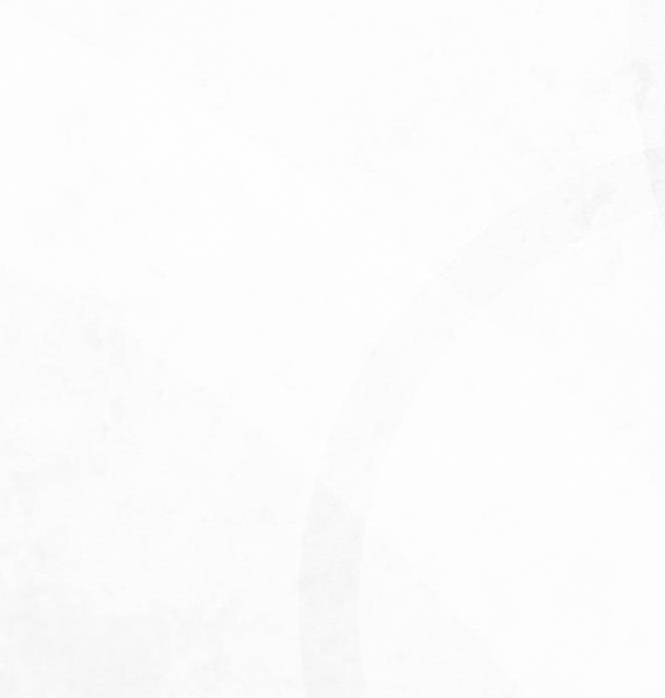
Lars Skyum, Haldor Topsoe A/S
In the early 2000s, Topsoe discovered a new activity site in hydroprocessing catalysts: the brim site. With this fi nding, the company developed the BRIM® technology, as well as the HyBRIMTM and most recently a new HySwellTM technology.
TK-6001 HySwellTM is a unique supported NiMo catalyst and the fi rst catalyst prepared with the HySwell technology. Since it was launched in 2019, Topsoe has achieved more than 10 sales with several already installed and performing excellently. The TK-6001 HySwell has delivered up to an impressive 17°C improvement compared to the previous catalyst in a commercial unit.
So far, only unsupported hydroprocessing catalysts are seen with such high activity. However, unsupported catalysts are very costly and cannot be regenerated.
HySwell catalysts can be regenerated, and they utilise the active metals better, which drives down cost compared to bulk-metal catalyst formulations. This is clearly more sustainable, and also more effi cient when targeting volume swell.
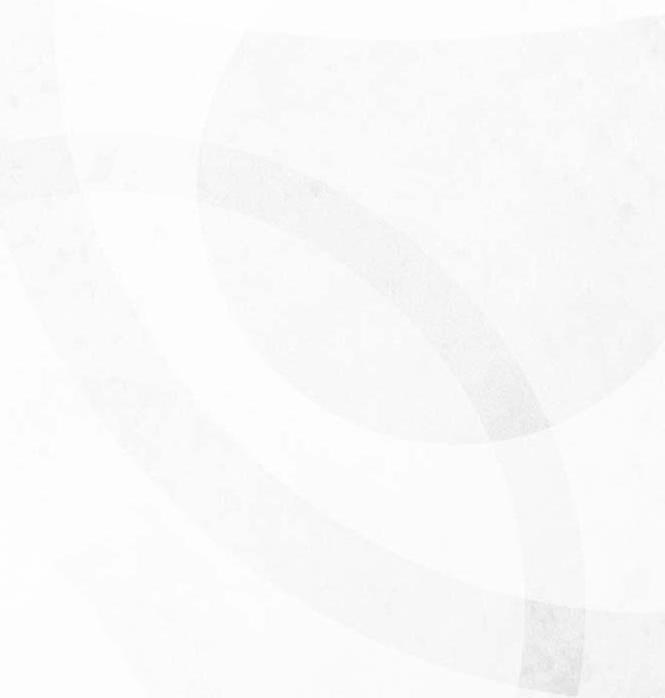

The ultra-high activity achieved with Topsoe’s HySwell catalyst preparation technology enables refi ners to upgrade fossil oil fractions which cannot be upgraded using other catalysts. The benefi ts include much better utilisation of the world’s fossil energy resources, and HySwell produces even cleaner and less polluting gasoline, jet, and diesel fuels.
Due to their high activity, HySwell catalysts will stay longer in service in any hydroprocessing unit. This means fewer production stops (and consequently significantly improved efficiency and profitability for the refiner), as well as reduced catalyst consumption, fewer operating resources, and less consumption of raw materials.

Brad Cook, Sabin Metal Corp.
Sabin has been working very hard for the last several years on two capacity issues. Firstly, the addition of a third kiln unit for the thermal reduction process that reduces carbon/coke contamination, which is now complete, certifi ed and in use. Secondly, our overall refi nery expansion, which will allow Sabin to make more pure platinum and palladium faster than ever before. We expect to announce the increased refi ning capability later this year.
What is the most challenging project that you have encountered recently?

Dr Detlef Ruff, BASF
The challenges faced by the oil refi ning industry vary from region-to-region and from customer-to-customer, covering many diverse and often interconnected topics. Examples of the challenges to be faced every day in the refi ning and petrochemical industry include the impact of crude oil and refi nery product pricing; how to sustain long-term profi tability in uncertain market conditions; how to control operating expense; the impact of changing product specifi cations; how to improve agility and fl exibility to adopt the latest FCC catalyst technologies; how to meet changing environmental regulations and future policy changes; and how to train the new generation of professionals.
To be successful in this market, there is not one single most challenging project but a series of on-going diffi cult challenges which must be solved. The most diffi cult challenge is maintaining the continuous and balanced focus on all the
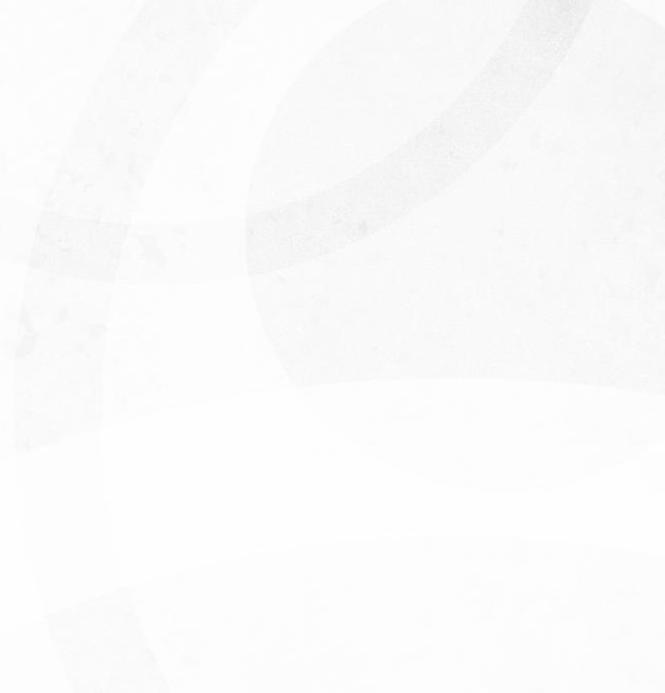
A WORLD OF SOLUTIONS FOR NEW PRODUCTS AND TECHNOLOGIES
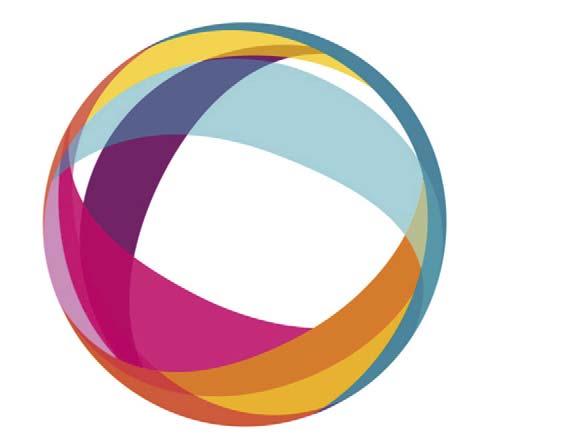
CEEIC

unique industry challenges to ensure all of our customers are successful in achieving their unique objectives with the solutions we provide. BASF’s focused commitment to partnership, service and innovative fl exible products are incredibly important to the success achieved by our customers and the refi ning industry.
Lars Skyum, Haldor Topsoe A/S
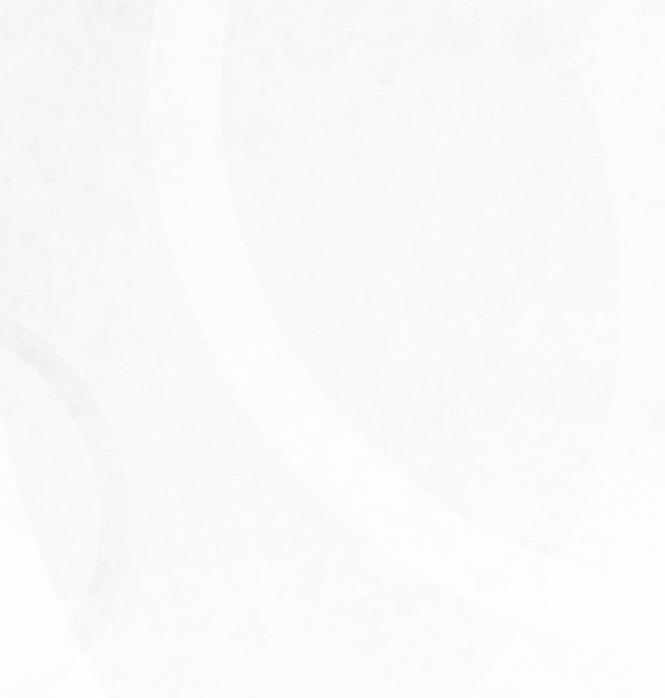
Topsoe is a licensor of many different process technologies in the refi ning and pretrochmical industries. Currently we are extremely busy with a very large number of renewable fuels projects in the US and EU. Half of these are grassroots projects and the other half are revamps of existing refi ning assets. In general, revamps are more complicated due to the fact that we have to reuse as much of the existing equipment as possible for the new purpose to miminise the required CAPEX, while maximising the capacity within the constraints of the existing equipment.
We have recently revamped a hydrocracking unit from fossil service to 100% renewable fuels service. In addition to the engineering skill set required for the reconfi guration, we had an added constraint – a 9 months time schedule from project kick-off to production of renewable fuels. It was quite challenging to do the required unit review, engineering, reconfi guration and procurement of the necessary new equipment, including reactor internals and catalyst to meet this very tight timeline. With an innovative project engineering execution strategy together with the EPC, we will be able to meet this timeline. The project will start up in the summer of 2021.

The industry encountered the steepest and fastest decline in demand for transportation fuels in history last year. This lowered production of jet fuel and gasoline, and lowered economic activity even affected diesel used for commercial transportation. Demand for petrochemicals also fell slightly. As a result, refi neries dialed down production and even shuttered some production, delaying some catalyst turnarounds. But demand for new catalyst designs remains strong, and as fuel demand continues to climb this year, turnarounds are rising as well.
How has the COVID-19 pandemic affected the downstream catalyst industry?
Rajesh Gattupalli, Honeywell UOP

Lars Skyum, Haldor Topsoe A/S
When the catalyst industry entered 2020, we came from a situation where the demand for hydroprocessing catalyst had increased year over year for a period of 2.5 years. As a result of the increasing demand, lead times were relatively long at the end of 2019, and our customers had therefore placed orders well in advance with delivery in 2020.
With the breakout of COVID-19, some customers had problems maintaining their planned turnaround activities due to restricted mobility of personnel, and at these sites catalyst suppliers were asked to delay the shipments if possible. Soon, the global demand for fuels decreased, and as the refi neries operated at lower utilisation rates, the catalyst life time was extended, resulting in lower demand and shorter lead times. A few refi neries have even been forced to shut down, and in these cases shipments were not only delayed but cancelled. Now, 1.5 years after the fi rst cases in China, the demand is slowly returning, especially in China and the US, whereas European customers are still moving some planned replacement from 2021 to 2022.
From a production point of view, Topsoe has been able to produce consistently despite COVID-19. We have been careful in preventing COVID-19 cases at our factories, and with good planning we have not had any issues securing raw materials. Despite the diffi cult situation, we have therefore not had any supply issues.

What does the future hold for the catalyst/precious metals market?
Dr Detlef Ruff, BASF
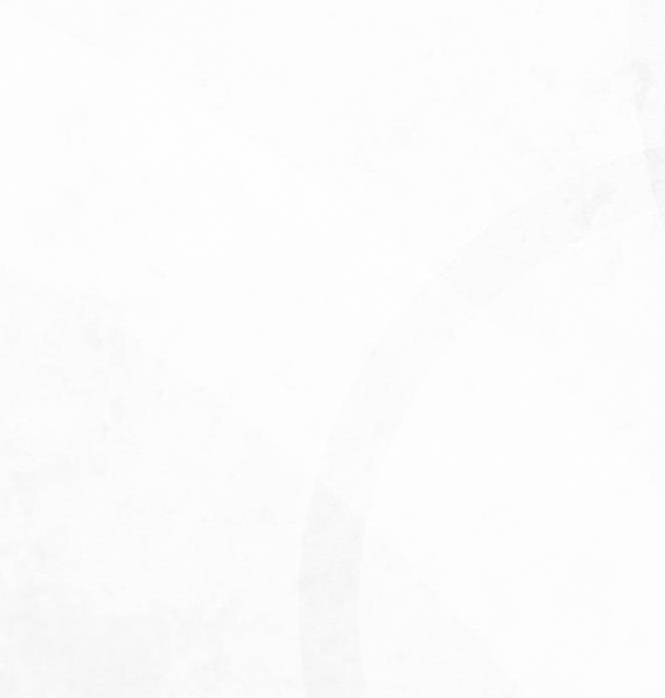
Catalysts are critical in the process of converting petroleum from crude and other feedstocks to refi ned products such as gasoline, diesel and petrochemical feedstocks such as naphtha and olefi ns. The demand for catalysts over the coming 5+ years is expected to grow in response to the recovery following COVID-19, the continued rising living standards, population growth and the increased integration of petrochemical production as part of refi nery operations. The industry focus on becoming more sustainable is also leading to a growth in demand for cleaner petroleum products and is a factor driving the global refi ning catalyst market. The refi ning and petrochemical market must anticipate and respond to a wide range of customer needs. A few of the major challenges are summarised here: New and improved innovative catalyst designs to support the market shifts to cleaner fuels, use of alternative feedstocks and to meet the growing demand for petrochemicals.
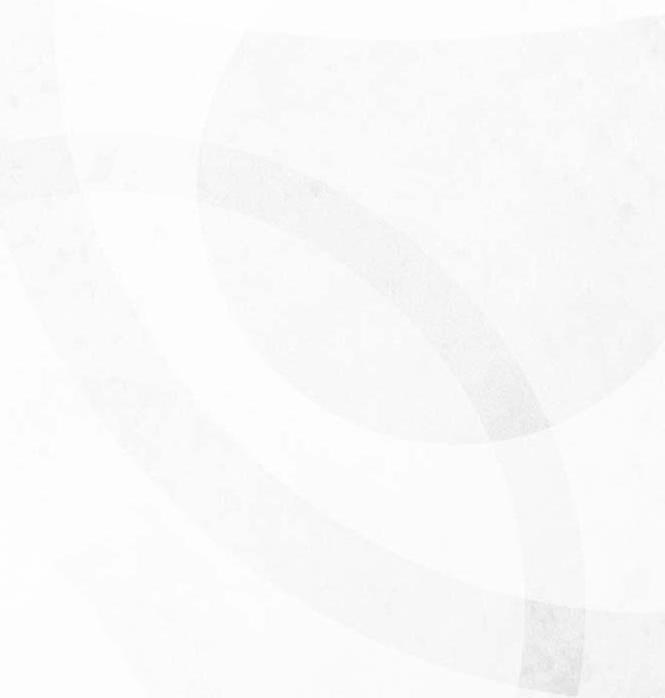

The premier source of the latest information for the renewable energy industry, covering solar, wind, bioenergy and storage.

Optimised catalyst performance to drive economic improvement at the refinery or petrochemical complex. Increased focus on unlocking refining potential through catalyst optimisation to unleash changes to current constraints and operational optimisation to improve profitability with an increasing need to evaluate response time to changing requirements. Supporting global and regional sustainability initiatives while meeting environmental regulations. Supporting requirements to develop methods to reduce greenhouse gas emissions and CO2 reduction as new feedstocks are evaluated and used, such as biofeed, pyrolysis oils from plastics, and other alternative feedstocks.
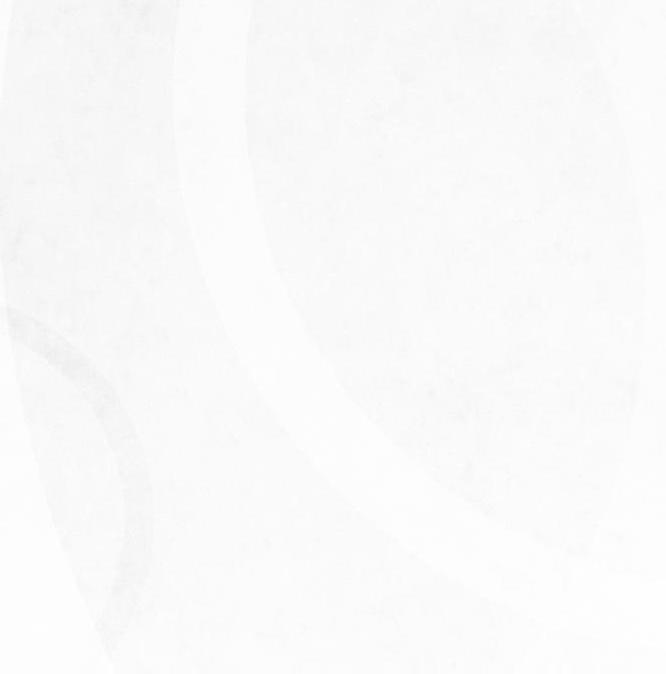
Brad Cook, Sabin Metal Corp.
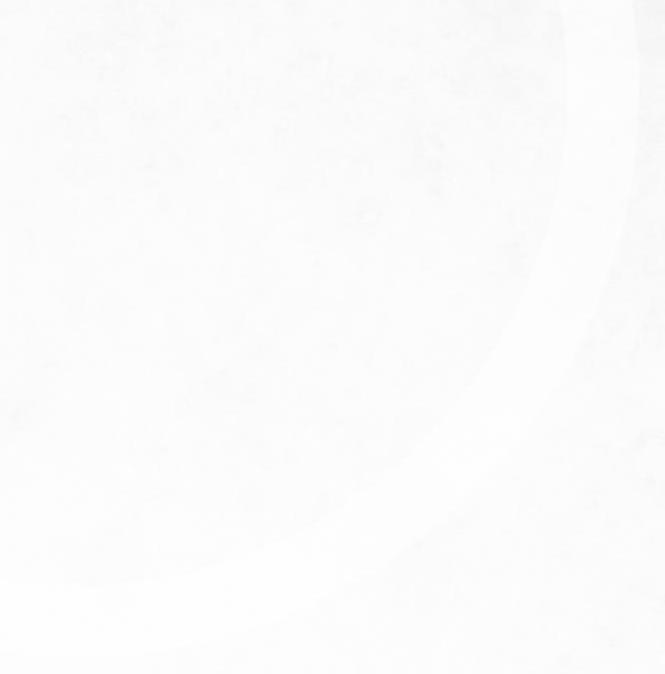
I am very bullish on PGM. PGM comes from South Africa and Russia almost exclusively, the ore quality is deteriorating, it is getting more expensive to pull each ounce out of the ground, and demand isn’t going down. The metals we call ‘precious’ were originally given that title based on their beauty and workability as jewellery. This made these metals highly sought after, which in turn made them valuable. They’re still considered very valuable for these same reasons, but today there are much greater reasons to be mindful of PGM: Conservation (pollution control, wise management of natural resources): the automotive catalysts and the industrial filtration units that reduce emissions. Energy (both creating energy and improving performance): fuel cells, gasoline, jet fuels, even your spark plugs are platinum-tipped. World health (disease prevention and cure): treatments, medical devices and pharmaceutical products that contain
PGM or are made using PGM.
PGMs remain at the forefront, the absolute cutting edge, of all three of these crucial technologies. Sabin, along with our competitors, customers and partners around the world, need to continue to work together to develop strategies to overcome the issues I’ve mentioned here. A cooperative effort is the only way to ensure that these crucial metals remain sustainable, available, and cost-effective for continued use into the world of our grandchildren and beyond.
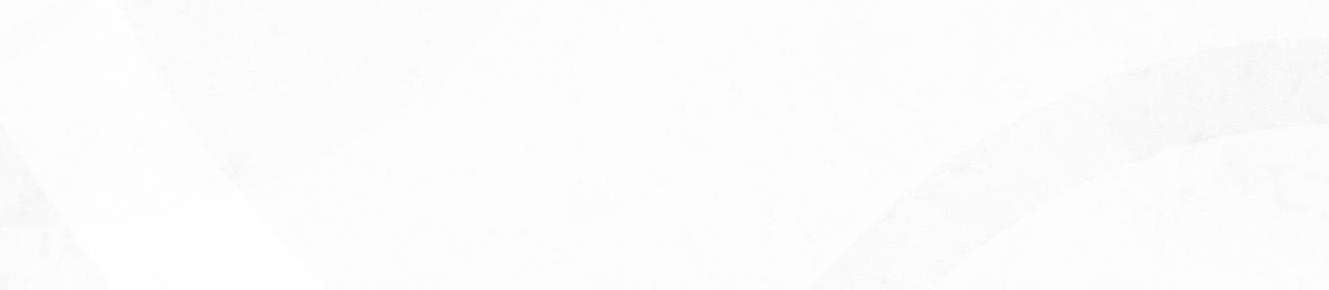
Page Number | Advertiser 21| ABC 04| Ariel Corp. 02| BASF 25| Elliott Group OBC| Eurotecnica 59| Haldor Topsoe 55| Honeywell UOP 37| John Zink Hamworthy Combustion
OFC & 29 | Merichem Company 61| MERYT Catalysts & Innovation 34| NEO Monitors

AD INDEX
49| NISTM 17| NOXCO 38 & 63| Palladian Publications 18| Paratherm
IBC| Rezel Catalysts Corp. 57| Sabin Metal Corp. 43| Servomex 41| SulfurCon 2021 12 - 13| Sulzer
IFC| Total Lubricants 07| Uniper
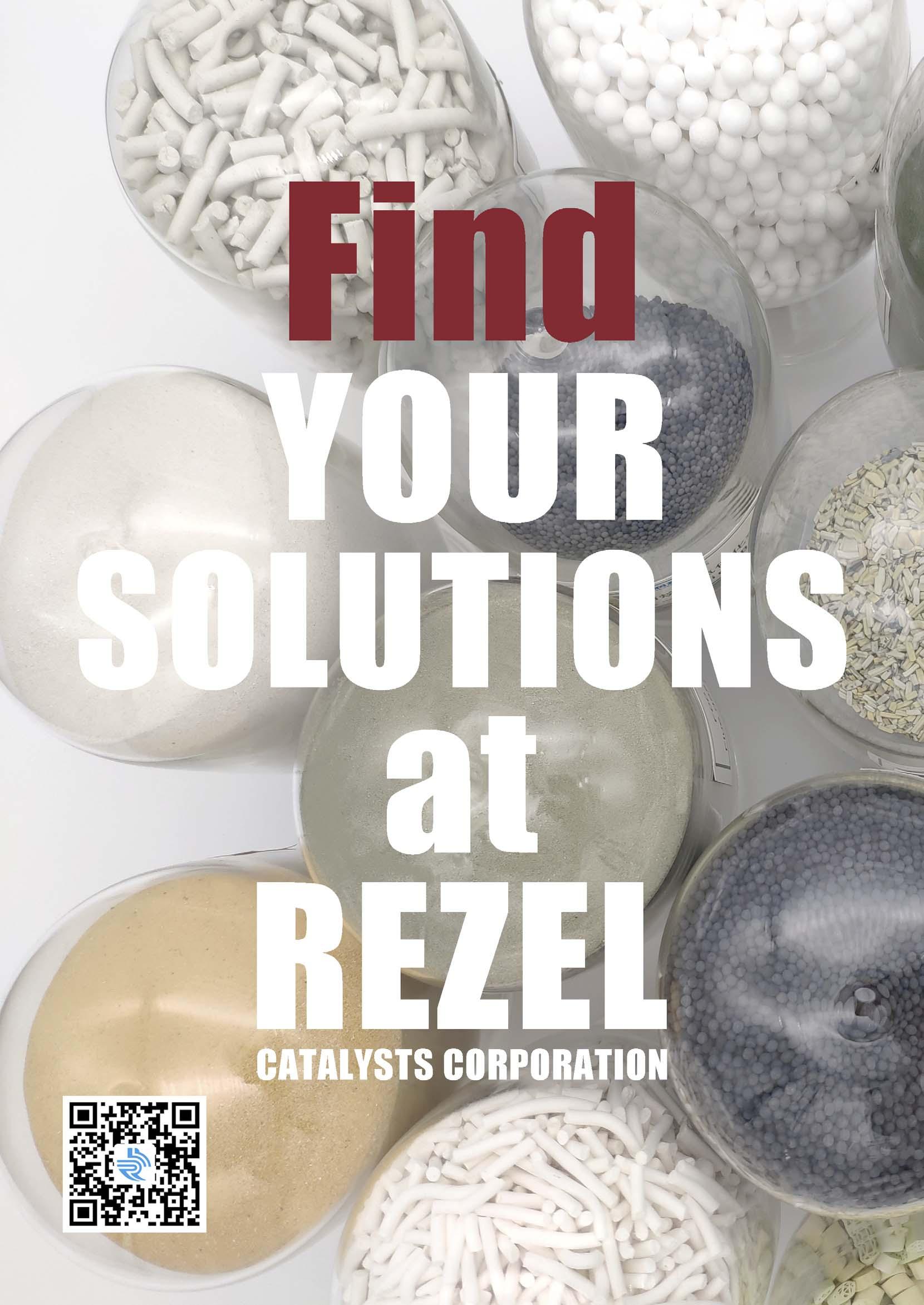
FFCs slurry oils sell for just a few hundred dollars/ton, but when converted into Carbon Black – a key component in high-end plastics, tire manufacturing, and other rubber-based components – they can reach a market price of $2,500 USD/ton.
ET Black™: the industry technology of choice
Eurotecnica’s modified furnace black process, ET Black™, efficiently converts slurry oils into a wide range of carbon black grades, giving you access to an exciting and fast-growing industry.
With guaranteed operating flexibility and reliability, easy maintenance, and a low CAPEX, ET Black™ has become the technology of choice for industry leaders like ADNOC Refining.
Contact us at www.igoforETBLACK.com to find out more.
