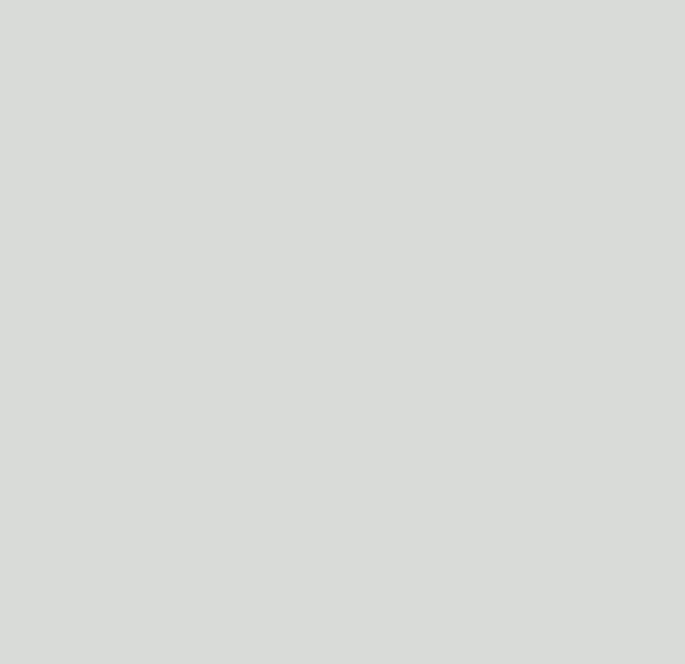
7 minute read
Focus On The Drive, Not The Destination
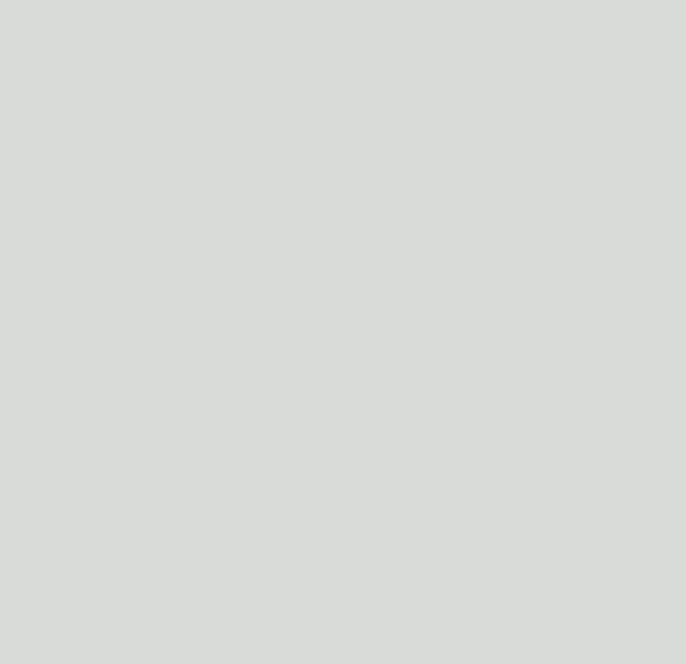
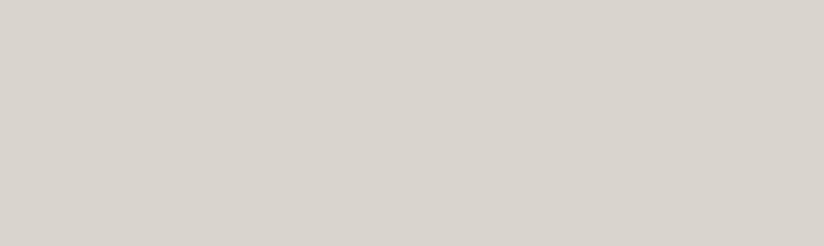
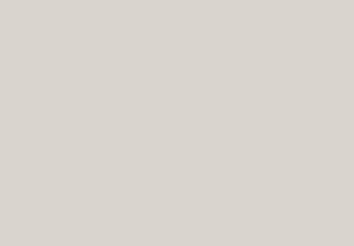
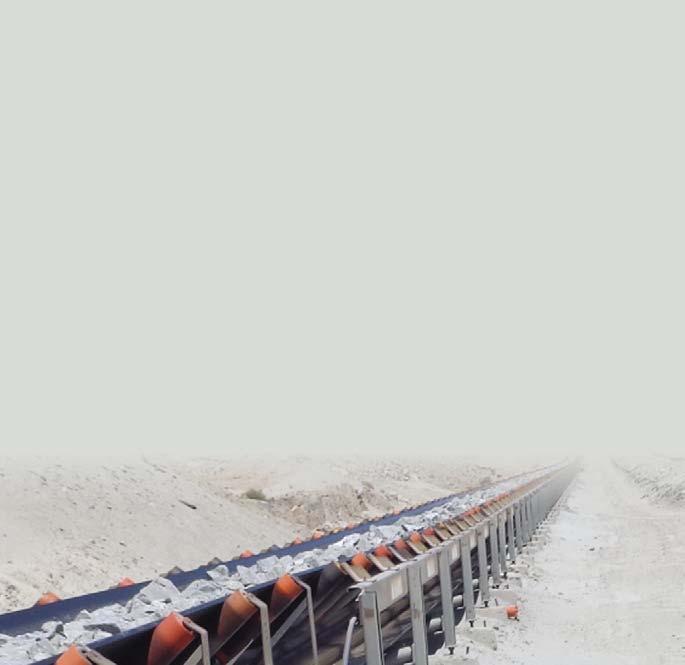

Dr. Heinz-Peter Ehren, KUMERA Getriebe GmbH, Germany, describes how a customised gearbox solution can increase reliability and reduce energy costs.
Powerful conveyors and their drive systems have a key role in surface mining. In ore mines, conveyor belts up to several kilometres long transport ore for further processing or transportation and reduce labour burden. The operational safety and reliability of the systems is of great importance since delays or shutdowns due to damage can cause immense downtime costs.
Environmental hazards such as extreme weather conditions and fluctuations, dust and dirt pollution, and falling rocks must also be considered for operational safety. Systems are often installed in impassable locations so low-maintenance concepts are required. In the event of service or damage, the downtime should be as short as possible.
Another high priority is the greatest possible ecological sustainability of raw material extraction. This is not only achieved through the high operational reliability and long service life of the systems, but also through the energyeffi cient operation of the individual drives. As a manufacturer of high-performance drives for conveyor systems, KUMERA is aware of its responsibility and strives to implement this in the best possible way in the development and manufacture of high-performance gear units for customer and applicationspecifi c operations.
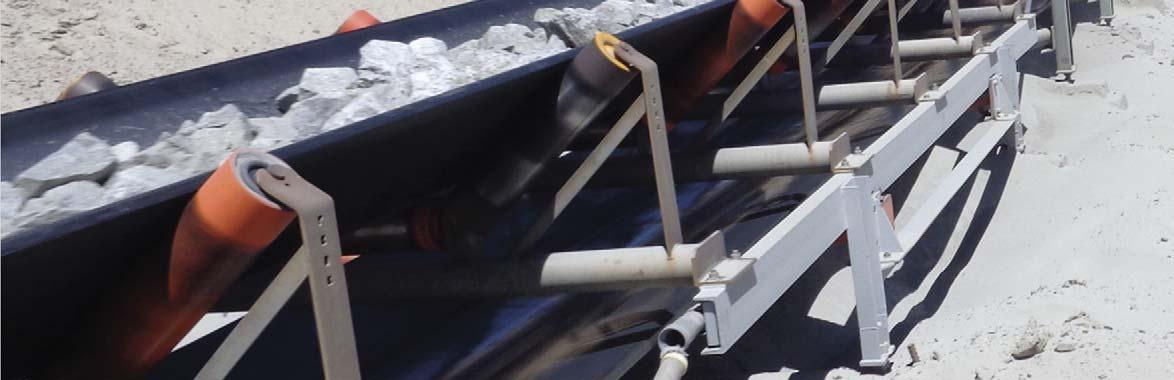
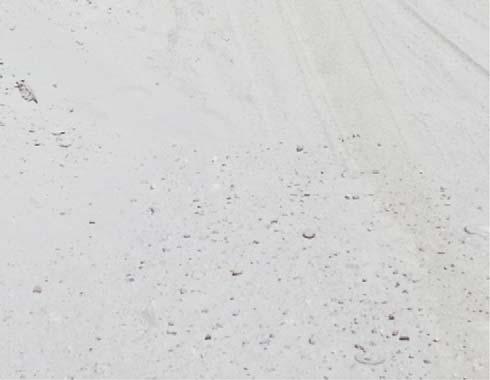
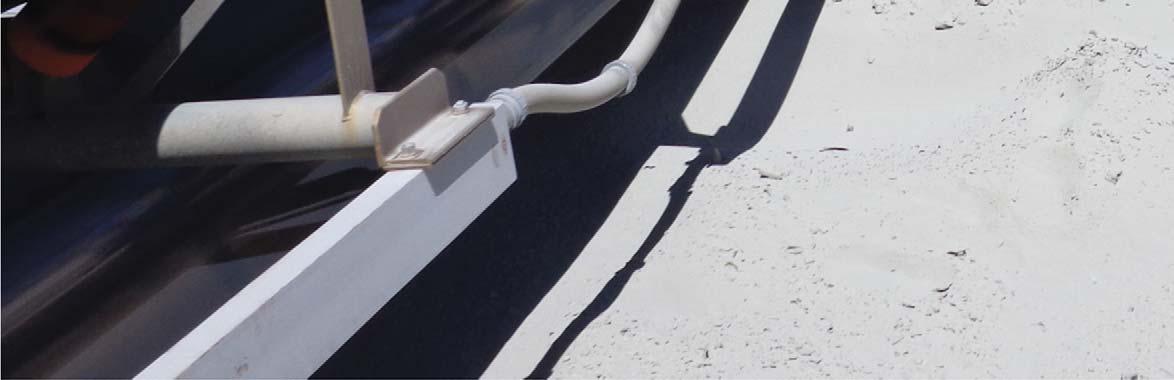
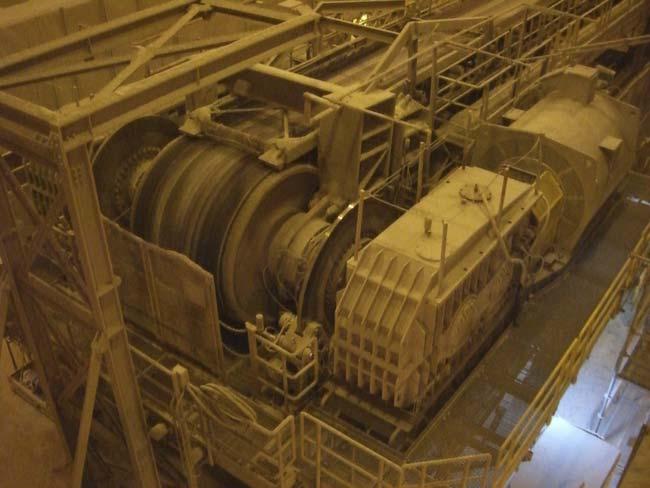
Figure 2. KUMERA conveyor belt drive solution – right position.
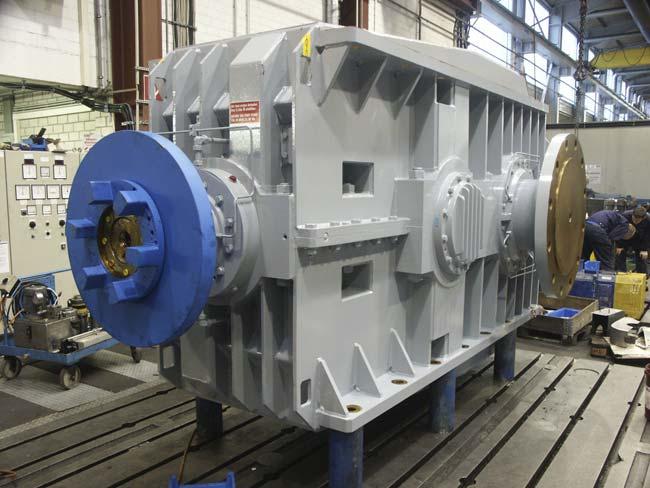
Figure 3. Highly effi cient KUMERA 2500 kW conveyor belt drive.
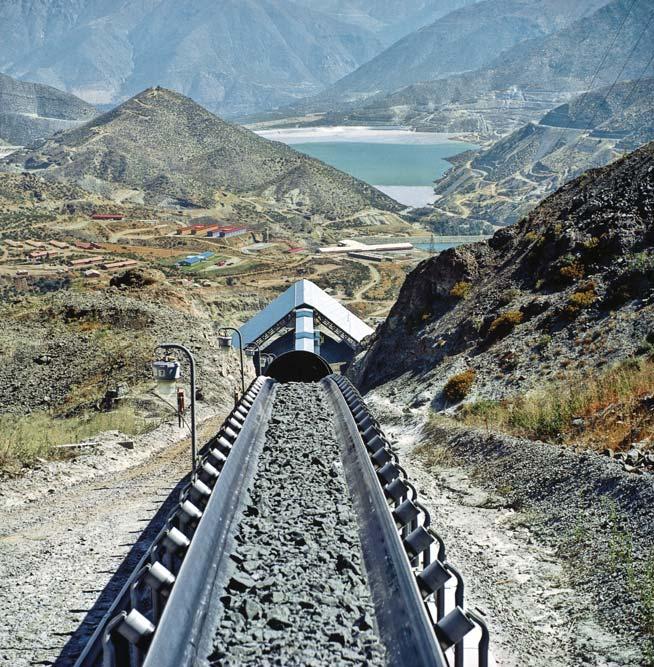
Figure 4. Conveyor belt slope downwards – generator mode.
Three-phase AC motors with the following gear variants are typically used as drive concepts for the conveyor belt systems.
Advantages of a standard gear with or without a fan include fast availability and the fact they are inexpensive. Their disadvantages, however, include the fact they have small outputs up to 1000 kW; gear ratios greater than 16:1 in three-stage design results in high power losses; there is less possibility of variation in differing installation and environmental conditions; and additional lubrication and cooling units are usually required for heat dissipation.
KUMERA’s customised gears have been designed to overcome the disadvantages experienced when using a standard gear with or without a fan. Advantages of the customised gears include: Optimised drive design for the respective application and the specified environmental conditions. Outputs over 2500 kW possible. In the two-stage design, ratios greater than 20:1 are possible, which reduces the power losses by up to 30% compared to three-stage gearboxes. There are a large variety of options, including universal installation options as a result of the double foot design. Compact design through the flange output shaft. No additional lubrication and cooling system. Higher operational safety due to a significantly lower number of components at risk of failure.
Disadvantages of KUMERA’s customised gears include the higher design effort and more complicated gear housing design due to the internal oil routing. This means higher costs, however, these are partially offset by saving the oil supply system.
The gearboxes are mounted on a base frame as a drive unit together with all additional components (e.g. brakes, torque support, etc.) and flanged on the belt drums. Depending on the power requirement, a conveyor belt is equipped with one or two driven belt drums, whereby each drive drum can be equipped with a drive on one or both sides. A conveyor belt is thus equipped with up to four drive units. A signifi cant advantage of having several drives per conveyor belt is that if one drive fails, the system can continue to operate – albeit with a reduced delivery rate – until the defective drive is repaired or replaced. Another advantage in connection with the universal gearbox design is that in the event of a defect with a replacement gearbox, any damage, regardless of the gearbox position in the system, can be repaired at signifi cantly lower costs than if the conveyor belt was driven by just one large drive.
Power
In addition to the drive concepts described, gearless direct drives are occasionally used in the upper power range, up to approximately 8000 kW. Here the conveyor belt is usually driven by a central, slow-running synchronous motor. As a result of the low utilisation and the elimination of mechanical losses in the gearbox, these drives also have a favourable energy effi ciency. However, this can only be achieved by tight tolerances in the permissible air gap between the stator and rotor of the motor. For this, high demands are placed on the
rigidity of the overall construction (foundations, shaft deflections, etc.). Since these individual drives are also comparatively heavy, the logistics involved in installing them in mostly inaccessible terrain are also a challenge. Another important disadvantage is that if the drive fails, the entire system comes to a standstill, which can result in immense downtime costs.
KUMERA conveyor belt drives are designed as a two-stage design when possible. Compared to a three-stage version with standard gear units, this has the advantage of 1% better effi ciency (approximately 98% instead of 97%). Whilst this does not sound like much initially, it does, however, turn out to be an ecologically and commercially signifi cant advantage.
For example, a KUMERA conveyor belt with 10 MW drive power (four drives at 2500 kW each), currently in use in a copper mine in Chile, has a saving of approximately 100 kW/h in motor operation by an effi ciency increase of 1%. For a conveyor system consisting of three conveyor belts, with a system utilisation of 80% on average and an operating time of 16 hrs/d and 250 d/y, this means an energy saving of approximately 960 MW/y. If still considering a system utilisation of 80% but 24/7 operation time and 14 days downtime for maintenance per year, the savings are up to 2016 MW.
In many applications the systems convey the material downhill, which means the operation is in generator mode. The higher effi ciency means the systems will generate approximately 100 kW/h of power more than a three-stage version with standard gear units.
Since the drives are usually installed throughout a mine in locations which are diffi cult to monitor visually, the most maintenance-free and uncomplicated operation is required. A main problem here is the dissipation of power losses in the transmission as heat. Standard gearboxes in this power and operating range are usually not able to dissipate the heat via the housing surface. Separate external oil supply systems with heat exchangers are used for this. Since there is generally no cooling water available at the installation site of the drives, oil-air coolers are mostly used. A critical disadvantage is that these oil systems show a high susceptibility to electronic, hydraulic, and mechanical failure in the harsh environment. Accordingly, efforts are being made to dispense with this for cooling and to use simpler, more reliable solutions.
Summary
KUMERA is focused on offering customised concepts and solutions based on each location’s unique conditions. One solution is to enlarge and design the housing surfaces of the gearbox in such a way that, in combination with appropriate fans on the drive shaft, heat is dissipated for a stable thermal balance. If these measures are not suffi cient, KUMERA offers further concepts such as integrated cooling tubes.
KUMERA endeavours to support plant manufacturers in the implementation of their drive concepts with the best possible gear design. KUMERA also offers support to system operators and tailor-made drive concepts for the renewal and improvement of operational safety and increased performance of conveyor belt drives. The KUMERA belt drives are subject to continuous improvement. At present, new concepts are nearing production, through which both greater power density and an increase in operational reliability under thermal performance limits will be achieved.
ENERGY SAVER
e nv ironmentally friend l y
becker products
The easily installed Becker Mewis Duct®, for vessels with a high block coeffi cient, reduces SOX, NOX and CO2 emissions. The device is placed in front of the propeller, has no moving parts, reduces noise, and saves energy by 6% on average.
Right: Bulk Carrier Loxandra Becker Mewis Duct®
Visit us at Marintec, Shanghai, China, German Pavilion, booth no. N2B4A-09, 7th - 10th December 2021