
19 minute read
Industry 4.0: The importance of APS in automated lean production
Faced with a complex market environment featuring multiple varieties, fewer batches, shorter delivery times and more changes, custom furniture manufacturers are currently pressed for the support of a powerful production information management system. Since the planning and scheduling process is deemed as the core of production information, an information system is even more imperatively needed.
As the traditional enterprise resource planning (ERP) system is used to conduct production planning and schedule management, they poorly meet the corresponding needs of custom furniture manufacturers due to the lack of process data sources and limitations in the system architecture. Meanwhile, to meet the crying needs of the market, process software vendors within the custom furniture industry have investigated the needs of manufacturers and industrial characteristics of discreet and fl exible production. They have developed a dedicated advanced planning and scheduling (APS) system for the furniture industry, which is designed to address the fl aws in ERP’s planning module. Using algorithms, the system scheduling of the production process, and automatically generate the scheduling and production batch plans, etc. Consequently, such a system facilitates lean production by improving the kitting productivity, panel utilisation and processing effi ciency of orders. Taking a simple process in FinChinasoft's production information system for example, a custom order is split through Fin CAD/CAM and the order’s bill of materials (BOM) list is generated; the APS system then divides the parts into special-shaped workpieces and rectangular workpieces according to the manufacturing technique. Through the APS system's order and productionscheduling algorithms, the combined batches are automatically generated; rectangular panels and large-scale standard panels are allocated to the panel dividing saw, and special-shaped panels and batch size one panels head to the CNC nesting machine. Finally, the system is connected to the Fin Optimize Cloud Software to quickly obtain the cutting program fi les required by the nesting machine and saw equipment to begin production.
Advertisement
Nanxing Machinery has successfully combined its equipment and the Fin Optimize Cloud Software to maximise the advantages and effi ciency of their machines. This is how the APS system and Fin
makes full use of corporate resources to perform intelligent
Optimize Cloud Software work together. ADVANCED PLANNING AND SCHEDULING SOFTWARE The APS system has not only addressed the fl aws of the ERP module but also provided eff ective reinforcement for the existing ERP system. It automatically generates scheduling plans and production batch plans through algorithmic calculations to improve kitting productivity, panel utilisation and processing effi ciency of orders. The optimal computing engine can develop the most reasonable scheduling plan even under limited production capacity and provide furniture manufacturers with a more cost-eff ective scheduling plan.
1. INTELLIGENT ORDER-SCHEDULING ALGORITHM When an order is received, the ERP system can provide feedback of current material storage and production capacity of the plant according to the real-time scheduling results from the APS system. Through its intelligent order-scheduling algorithm, the system, taking into account the order delivery time, production cycle of parts, equipment capacity, and other planned order-
scheduling constraints, can automatically generate the optimal order scheduling plan. This allows users to achieve the most optimised scheduling of production resources, and thereby improve the overall kitting productivity of business orders and eff ectively shorten the overall delivery time. By comparing the detailed list of required materials with the material inventory, the system can generate timely feedback on material requirements, lack-of-stock requests and generate inventory for inventory being withheld, guarantee the availability for orders in planning and scheduling, and ensure just-in-time production with suffi cient materials. In addition, special features such as urgent order delivery capability could be also introduced. 2. INTELLIGENT AGGREGATION OF PRODUCTION BATCHES production batch plan based on the system's statistical analysis of order material composition, part size distribution, processing technology characteristics and other factors, combined with the number of parts in the batch, part area and product quantity. For example, if it accounts for 80% of the factory’s large-scale engineering orders, standard rectangular panels will be assigned to the panel dividing saw, and the specialshaped panels or batch size one panels that require fl exible production, accounting for 20%, will be assigned to the CNC nesting machine to effectively improve the rational allocation of equipment use, material utilisation and workshop production effi ciency. 3. SYSTEM INFORMATION SHARING FOR INTELLIGENT PRODUCTION SCHEDULING The APS system can be integrated with the manufacturing execution system (MES) and third-party ERP to fulfi l interactive integration of planned production with material inventory and production process data. This then allows the continual development towards intelligent production scheduling that features system autonomy, self-feedback and self-decisionmaking.
The system is remarkably eff ective in actual order scheduling. The use of the APS system has developed huge advantages (eg, reduced staff , improved effi ciency and increased utilisation) under the same restrictions. After having used the APS system, some customers found that batch scheduling optimised by the algorithm could reduce panel consumption by 1% to 3% compared to the original manual method. Assuming a factory's
The intelligent production-scheduling algorithm generates the

originally consumes 1,000 panels a day, the APS algorithm can save at least ten panels per day using automatic scheduling. Given that one panel costs about US$22.40, savings could reach up to US$224 daily and US$67,200 annually (based on 300 working days per year).
FIN OPTIMIZE CLOUD SOFTWARE Upon using the APS system’s intelligent scheduling in the preliminary stage, further improving the panel optimisation rate is the key to success for furniture enterprises. Presently, to improve the utilisation rate of panels, panel-type whole-house custom manufacturers across China generally merge multiple orders into one production batch, and optimise the layout of workpieces through optimisation software. Cutting optimisation software has also gradually developed into an important tool for processing the production data of process-splitting software, and has thus become a must-have product for such software companies in the industry. However, cutting optimisation software of diff erent companies may diff er in technical features according to deployment plan, supported equipment types and layout algorithm, which would directly aff ect the optimisation effi ciency, ease of use and extensibility of the software. This could ultimately aff ect customers’ user experience.
The Fin Optimize Cloud Software is an online layout optimisation system based on a cloud server. The user can log in to the system via the Internet on any computer at any time and place to easily upload and optimise the order data and get the desired layout result to coordinate with follow-up production. The core layout algorithms of the optimisation software also get updated and maintained regularly to continuously improve optimisation results, including the utilisation rate of materials and processing effi ciency of equipment. Currently, two optimisation algorithms – special-shaped layout algorithm and rectangular layout algorithm) – are being applied to the mainstream cutting devices, the CNC nesting machine and panel dividing saws, respectively.
ONLINE NESTING CLOUD SOFTWARE – SHAPED PARTS AND BATCH SIZE ONE An ordinary optimisation software can only complete the layout of rectangular workpieces. For special-shaped panels, the optimising process is performed by the rectangular outline. As a result, the vacant materials cannot be used rationally, adding to the cost of the enterprise. FinChinasoft's CNC nesting machine optimisation software uses intelligent algorithms to upload data to the cloud for automatic optimisation, achieving nesting of special-shaped panels, fi lling of layout and requires less manual work.
By using software to assist the automation equipment, the optimised utilisation rate and processing effi ciency of specialshaped workpieces are greatly improved. In addition to the optimisation, it can also perform multi-material optimal management, remodification of layout results, adding of standard parts, utilisation of material remainder, output reports, XML, CSV+MPR/BPP optimisation and other important features, which facilitate better management, raise production effi ciency and save investment costs. At present, the optimised utilisation rate for traditional rectangular workpieces is about 80%, and the number can be raised to 90% or even higher for specialshaped parts.
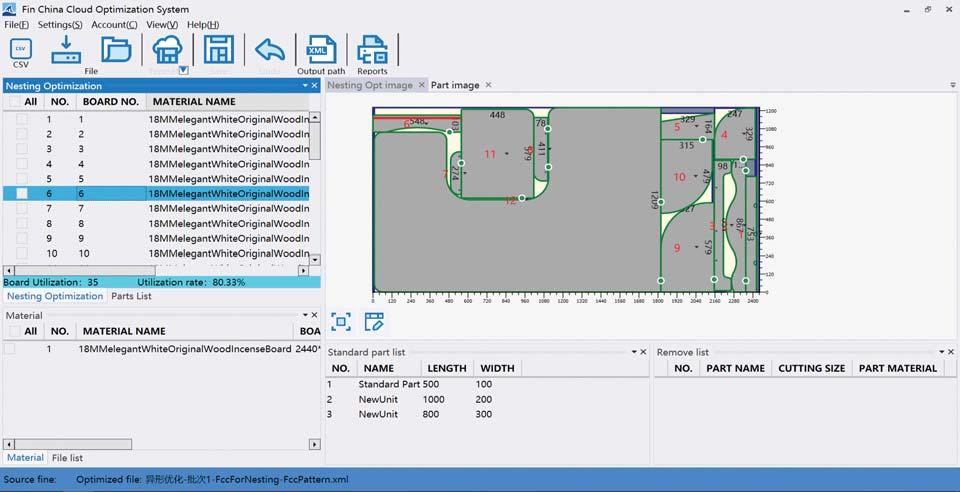
ONLINE SAWING OPTIMISATION SOFTWARE FOR RECTANGLE PARTS The web version of the online optimisation software is easy to use and allows the user to log in for layout anytime from anywhere, breaking the limitation of time and space. The newly added matching header function allows flexible matching to eliminate the restrictions that previous optimisation software have on part listing. The optimal layout is produced using the AI intelligent algorithm of the cloud server, and a variety of optimised formats are supported, including CSV, SAW, NXCUT and XML, to achieve seamless integration with the panel dividing saw.
It is evident that using algorithms to make the most optimal production scheduling plans under limited production capacity can greatly improve furniture manufacturers’ kitting productivity, panel utilisation and processing effi ciency. As the core process of production informatisation, an APS system is becoming increasingly important in lean production. P

The “Smart&Human Factory” is SCM’s vision for the future of the furniture industry. It is a system of automated, modular and easily reconfi gurable fl exible cells, integrated with articulated and collaborative robots and self-guided autonomous mobile robot (AMR) shuttles that can be programmed according to the production unit plant to move and work alongside the operator in complete safety.
This new digital and smart factory is still user-friendly, and designed to satisfy the challenges of mass customisation even more effi ciently and eff ectively. This goes beyond traditional automated systems; the state of the art SCM cells can be put together by clients according to their vastly varying processing needs.
By using a series of combinations between the shuttle routes and fl exible processing cells, SCM's “Smart&Human Factory” concept can be expanded within the same production unit to create complete furnishings for bathrooms, kitchens, living areas and bedrooms.
Presented at LIGNA 2019, and after numerous implementations on cutting-edge markets in Europe, the US and China, SCM's “Smart&Human Factory” was re-proposed at the SCM LIVE SHOW held from 30 June to 2 July 2020. New additions were developed to further increase productivity and fl exibility, reduce waste and optimise end product quality even with more sensitive materials.
The new version – only an example of the various confi gurations that this production model can achieve based on customer needs – involves three modular, flexible automated cells integrated with articulated robots and interconnected by AMR selfguided shuttles.
CUTTING CELL The “morbidelli x200” nesting machining centre, designed for “batch 1” fl exible production and able to cut at 50 m/min, is directly integrated into the high-performing “fl exstore hp” automatic storage for boards. This allows the stored and labelled panel to be directly loaded on to the worktable which protects those panels with a delicate surface. Once the nesting function has terminated, an articulated robot unloads the operating panel directly from the worktable and positions the diff erent parts on the AMR shuttles which then depart towards the next cell for edgebanding.
Another new aspect concerns the management of smaller pieces and waste: the robot also picks these up, making them available for future made-to-order productions with a considerable reduction in waste material.
The cell is also designed such that the panels with no delicate surfaces can be manually unloaded from the belt.
The “pack” cut made with a blade that guarantees high productivity on repetitive logical cuts is done simultaneously to the nesting, offering excellent fl exibility when cutting single sheets. This function is carried out by the new “gabbiani p80” panel saw. This model off ers a number of exclusive advantages: a “saw-set” device for the automatic and precise setting of the tools, 60 mm and 80 mm blade projections, more powerful motors, an additional extractor outlet on the presser and automatic blade release with switch.
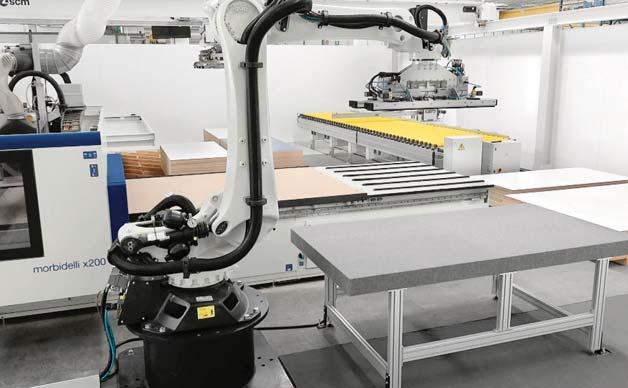
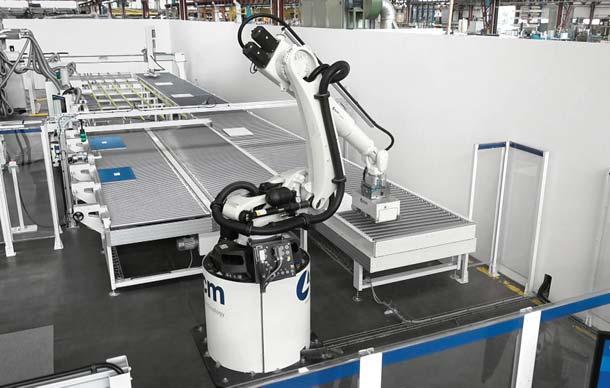
pack c 100
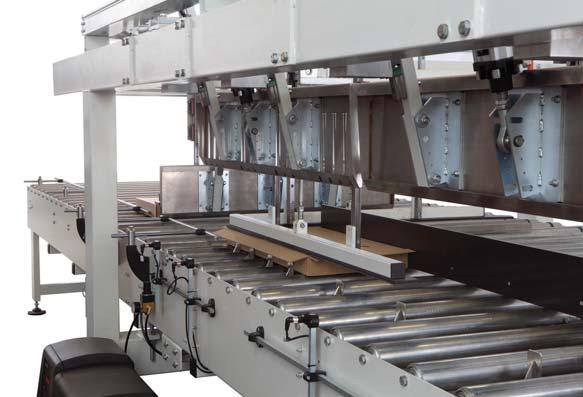
FLEXIBLE EDGEBANDING CELL The new “batch 1” “stefani cell E” cell is confi gured with an articulated robot for the fully automatic management of panel loading and unloading operations. The solution combines the advantages of customised production and large volumes with a compact overall design and, above all, an accessible investment even for small and medium-sized enterprises. Parameters like colour, edge thickness, position and depth of the mortise, management of the protective fi lm and panel sizes can be continually changed without interrupting the production fl ow. With a new gantry panel return system for the automatic return of panels, the panel is automatically rotated to speed up the next in-feed. It will also be possible to unload at the end of the cycle in masked time with the next loop load.
PACKAGING CELL With two machines, this cell is the ideal solution for furniture kit manufacturers. The “cut c 200” is an automatic punching machine for the cutting and production of an open cardboard box with the required size and shape. The “pack c 100” is an automatic solution for packaging with hot glue, using a pre-punched cardboard sheet. All the operator has to do is position the product for packaging on the open box (in this case – the panels coming from the edgebanding cell). After which, the upper lid is automatically closed. Due to the automatic measurement change setting, packages can be created with diff erent box sizes positioned in sequence on the roller.
DIGITAL INTEGRATED WOODWORKING PROCESS In the “Smart&Human Factory”, the whole system is optimised by the “Digital Integrated Woodworking Process”. Software and digital services assist the customer at each stage of the furniture-creation process – from the planning and preparation of the data to the machine production, right up to production monitoring, maintenance and after-sales service.
In response to production planning needs, a new manufacturing execution system solution is integrated into the SCM machines to assist customers with programming and managing the production fl ow.
Maestro active watch, a supervisor and process optimisation software, allows users to monitor the state of each product being machined, from the start to the end of the process. Through production tracking, it allows the best use of the facility by reducing bottlenecks and downtime, making all machines work at full load.
The new human-machine interface multi-touch Maestro active demonstrates how it is possible to have even simpler and better control and interaction with the machine during the production stage.
Lastly, the IoT Maestro connect platform collects and analyses the data about the actual use of the machines, improves the availability and reduces downtime. P
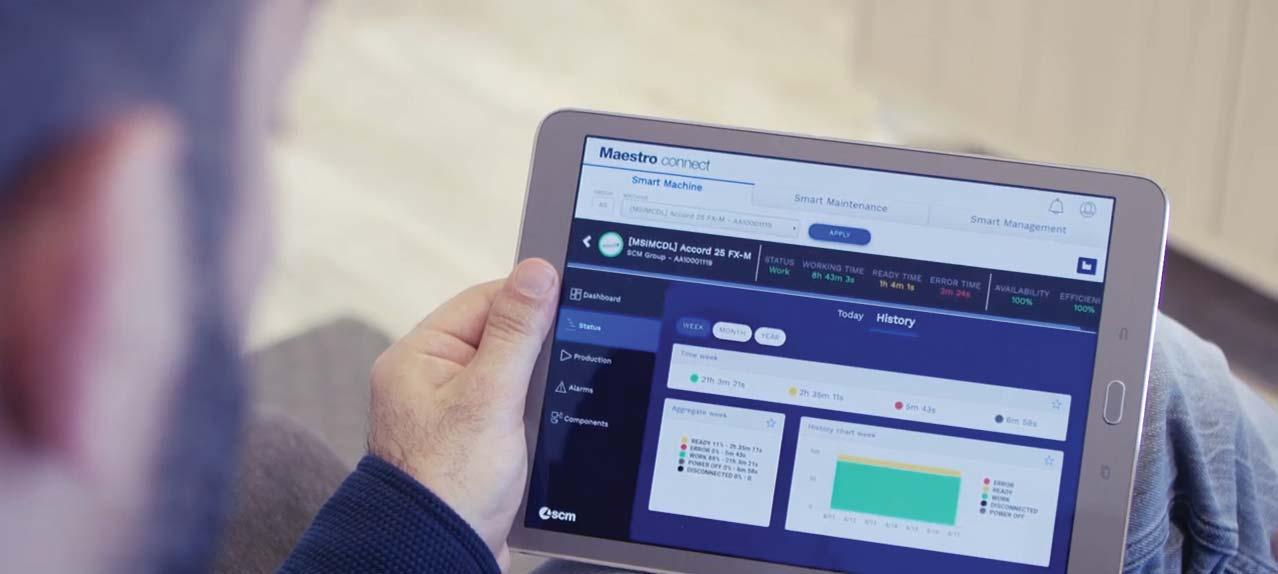
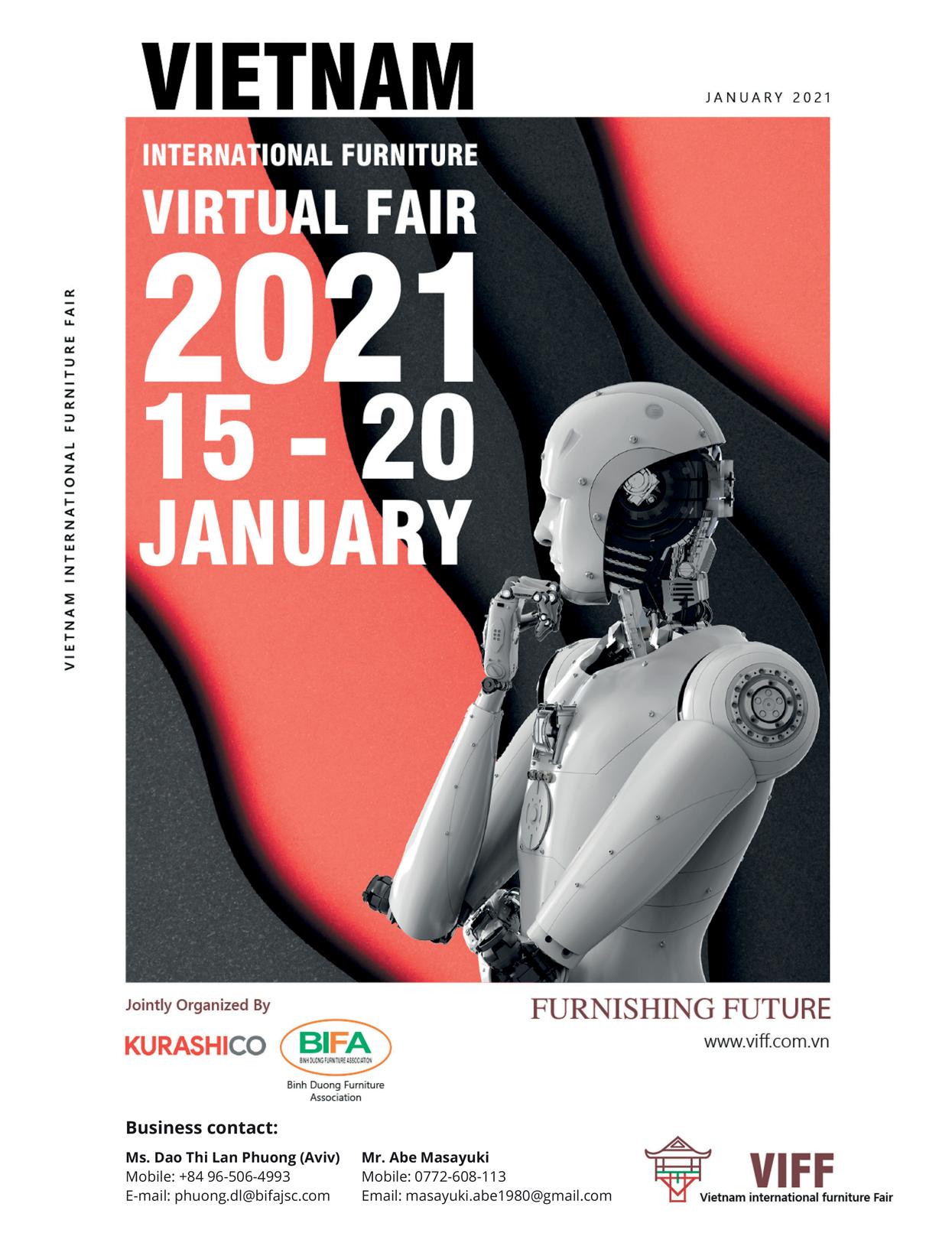
BIFA WOOD VIETNAM 2021 www.bifawoodvietnam.com
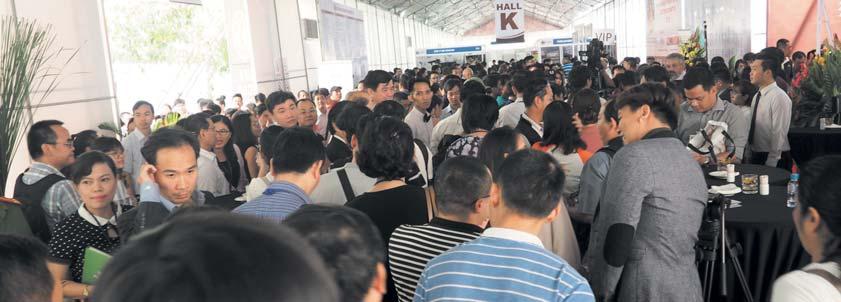
Venue: Binh Duong Convention & Exhibition Centre (open ground) Duong Hung Vuong, Phu Hoa ward, Thu Dau Mot city, Binh Duong province, Vietnam
Google Map QR code Exhibition Site
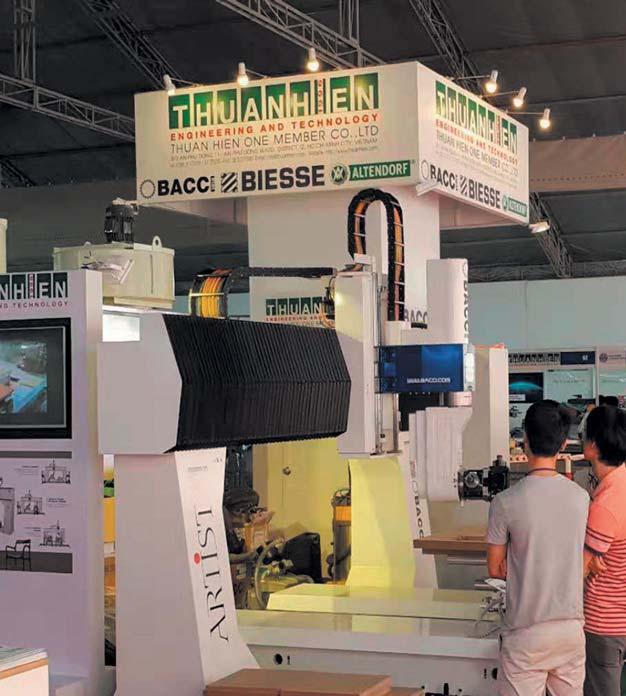
WOOD & WOODWORKING MACHINERY EXHIBITION

Enquiries For International Exhibitors
Pablo Publishing & Exhibition Pte Ltd 3 Ang Mo Kio Street 62 #01-23 Link@AMK Singapore 569139 Tel: (65) 6266 5512 Email: williampang@pabloasia.com info@pabloasia.com
WeChat Jointly organised by BINH DUONG FURNITURE ASSOCIATION (BIFA) PANELS & FURNITURE Group

LIGNA.21
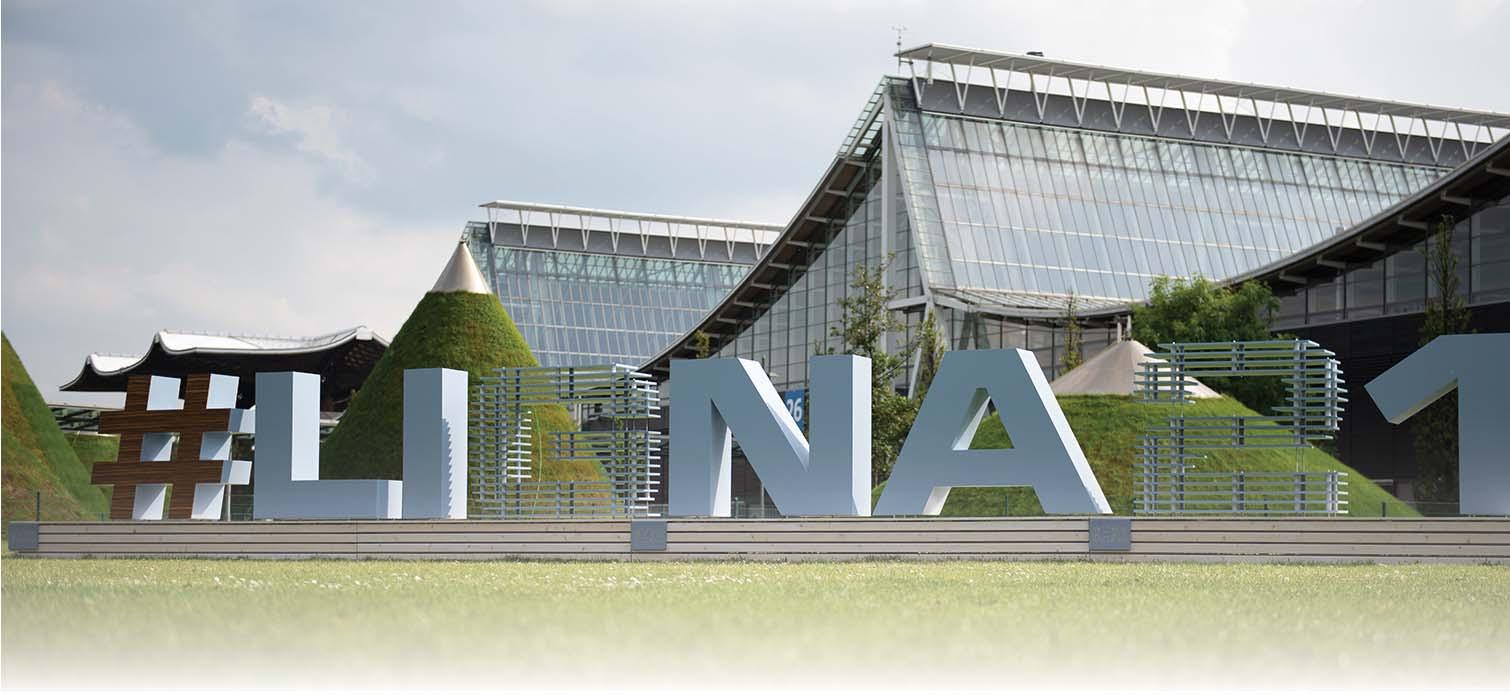
– Interview with Dr Bernhard Dirr and Mr Christian Pfeiff er
This article was fi rst published on LIGNA’s offi cial website (www.Ligna.de) and is reproduced here with permission.
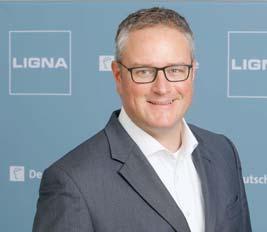
Dr Bernhard Dirr Mr Christian Pfeiff er
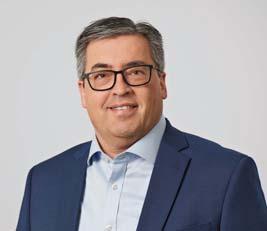
For months, COVID-19 has restricted many areas of public life. In this interview, Dr Bernhard Dirr, Director of the woodworking machinery division of the German Engineering Federation, and Mr Christian Pfeiffer, Global Director LIGNA & Woodworking Shows for Deutsche Messe (Hannover, Germany), explain how the pandemic has impacted LIGNA.21. Here, they outline the hygiene precautions and other measures that will be implemented and what to expect from the global industry’s fl agship fair scheduled to be held from 27 September to 1 October 2021 in Hannover, Germany.
How has the crisis aff ected suppliers of woodworking and wood processing machinery and business prospects in the sector?
Dirr: The COVID-19 pandemic has hit suppliers of machinery to the woodworking and processing industries in much the same way as it has aff ected many areas of mechanical and plant engineering. Many customers are very reluctant to invest. Machinery has either been idle or could not be operated, and in many regions it was not possible to visit plants and service machinery. But in addition to this, after three years of really good business, we were already seeing a signifi cant drop in orders towards the end of last year. So quite apart from the COVID-19 pandemic, the economy had already been slowing down, and the woodworking machinery sector has been harder hit than across much of the mechanical engineering sector.
However, the situation now seems to be easing, at least in Europe. It is, in any case, more predictable. In fact, sectors such as sawmill technology and timber house construction have got off rather lightly by comparison. Some of Germany’s furniture makers have signalled that the worst is now behind them, and the industry is generally optimistic that the 2020 dip in sales can be limited to 5%.
Manufacturers of machinery for furniture production are already speaking of a normalisation of business, and things are also more promising in parts of the construction industry. But the area of most concern is the situation facing manufacturers of plant and machinery used to make wood-based panels. Here, orders have slumped by more than half.
Despite all the uncertainties about the risk of infection and travel restrictions, do you expect that it will be “business as usual” at the trade fair?
Pfeiff er: Despite all the challenges posed by the pandemic, the demand for space at LIGNA.21 continues to run high. The event will once again fi ll ten halls as well as the open-air site, and all the major players have decided to exhibit. It seems that after many weeks of social distancing, lockdowns, online-only events and video conferencing from home, the industry is really looking forward to getting together for direct, person-to-person dialogue.
Naturally, none of us can foresee when the pandemic will have largely run its course, or when an eff ective vaccine might become available. To that extent, we must be realistic. The global travel restrictions, alone, mean we can anticipate fewer attendees from abroad than at LIGNA 2019. It is likely that there will be outbreaks of infection for some time to come, so we need to fi nd new ways of helping companies stay in touch with the marketplace. Our plans therefore revolve around the situation as it is.
Consequently, we have teamed up with the relevant authorities and developed a detailed hygiene and safety concept involving face masks, distancing rules and hygiene precautions. We are doing our utmost to ensure the highest possible standards in hygiene, safety and medical care for all our exhibitors and visitors.
The pandemic has reduced the resources available to many companies. To what extent might this impact their trade show activities?
Dirr: Of course, the pandemic has created a great deal of uncertainty among exhibitors and poses many questions that we will all need to address in the months ahead. Some exhibitors will want to adapt their participation to these new conditions, while others may decide to stay away altogether. In our conversations with exhibitors, we have found that the majority are very clear about how important it is for them to return to normal and give their customers a clear sign that they are confi dent about prospects and committed to meeting up with them at the show so everyone can get back to business. We are pleased that – despite the crisis – so many companies have opted to take part in LIGNA and lay the groundwork for recovery all around. The time has come to surmount the challenges of the current situation, and LIGNA will prove instrumental to that. If the show manages to convey the vibrant spirit and diversity of our sector in a visual and tangible way, we will then be able to speak of a successful LIGNA 2021 no matter what the exhibitor and visitor statistics might say.
Every two years, LIGNA puts the focus on the future of our sector. Which topics and trends are likely to interest the visitors most this time?
Pfeiff er: As the sector’s leading international trade fair, LIGNA is not simply a global marketplace for tools, plant and machinery for the woodworking and wood processing industries – it is also an important platform for setting trends and highlighting developments across the sector. The transformation of woodworking, prefabrication techniques in timber construction, and process technologies in the bio-economy will take centre stage at the event next year. These three topics will be prominently featured at the exhibition, as well across various forums and special displays. Visitors will also be able to view many new developments and innovations, including a sophisticated machine park – a complex of systems, machines and tools operating live on site – which is unequalled worldwide.
There will also be a supporting programme with top professionals and experts outlining the key trends and developments in the sector. One highlight for primary industry is the Wood Industry Summit in Hall 26, which is devoted to innovative solutions in sawmill technology and the production of wood-based materials. The secondary industry is catered for at the LIGNA.Forum in Hall 11, where the focus will be on innovative processing technology, and the networking and integration of various processing stages.
Some trade show organisers are off ering virtual events. Do you think online formats can replace physical trade fairs?
Dirr: Well, the experience gathered with online trade fairs so far has been quite positive. Growing interest in online formats refl ects how important these platforms are, especially in times of crisis. But companies have reported that these virtual events seem to be reaching target groups which are quite diff erent from those they would normally expect to fi nd at physical trade fairs. In other words, virtual events represent an additional channel which will continue to complement traditional trade fairs even after things return to normal.
Nonetheless, direct business dialogue will remain of vital importance, and trade shows are an especially effi cient way of facilitating this, even given the precautions made necessary by the pandemic.
Will a virtual option be available for visitors who cannot travel to Germany in September 2021? Will LIGNA also be off ered online in some form or other?
Pfeiff er: We are currently working on a digital form of participation to supplement the traditional trade show format. In this way, we hope to attract exhibitors and visitors from key markets who are unable to travel to Hannover. However, it is our fi rm belief that the direct exchange between players in the sector is essential to doing business and concluding orders. LIGNA, in particular, off ers a special visual and physical trade show experience, as well as many great opportunities for nurturing contacts and networking. P