
5 minute read
No harm, no foul with FORTILIFE
Modern problems require modern solutions, and in the case of biofouling in challenging wastewater, DuPont steps up to the plate with its FILMTEC TM FORTILIFE TM technology.
The more a shirt is washed, the faster its colour fades. According to DuPont Water Solutions ASEAN/ANZ Regional Marketing Manager Halim Sutanto, this is similar to what typical membranes go through in the wastewater treatment process.
Advertisement
This is where the company’s FILMTEC TM FORTILIFE TM product range comes in. Powered by FILMTEC TM technology, the FILMTEC TM FORTILIFE TM product family is designed for plants and facilities that need an industry-leading nanofi ltration (NF) and reverse osmosis (RO) water treatment that is reliable, easy to clean, and that would benefi t from a durable, robust membrane.
DuPont’s FILMTEC TM FORTILIFE TM product family consists of four elements: • FILMTEC TM FORTILIFE TM CR100 Element, designed with ultra-low diff erential pressure to provide improved hydraulic balance in a biological fouling system. • FILMTEC TM FORTILIFE TM XC-N Element, which converts a large fraction of RO concentrate into pure, easier-to-crystallise salt solutions. • FILMTEC TM FORTILIFE TM XC70 Element, which maximises the RO recovery rate by off ering the ability to achieve reject Total Dissolved Solids (TDS) level >70,000 ppm within standard reverse osmosis (RO) operating limits. • FILMTEC TM FORTILIFE TM XC80 Element, which lowers brine volume and maximises water recovery by achieving reject Total Dissolved Solids (TDS) level > 80,000 ppm within standard RO operating limits.
Explained Sutanto at the recent INDOWATER exhibition, “FORTILIFE TM is a foulingresistant membrane specifi cally designed for challenging wastewater, where people experience biofouling and organic fouling — the FORTILIFE TM family of RO elements is designed to tackle these challenges.
FILMTEC TM membrane is globally known and proven to be more durable compared to other brands of membrane available in the market, but if we can further enhance that by reducing the frequency of chemical cleaning, we can prolong the membrane life and that will save a lot of cost for our customers.”
Dr Somil Mehta, South Asia regional technical service and development leader at DuPont Water Solutions, elaborated, “FORTILIFE TM is cutting-edge technology. It’s a new platform in RO membrane technology, based on innovative membrane design… FORTILIFE TM brings in a very superior flow profile and fouling resistance to much harsher wastewater than what the industry has dealt with in the past. By using FORTILIFE TM , we can help improve the operation of the system by reducing the chemical Clean in Place (CIP) frequency, and in some cases we can also save energy of the operation — so all in all these improvements will help to save the cost of the wastewater treatment process.”
FORTILIFE TM also helps users with their sustainability goals, but one key challenge lies in getting customers on board with the technology off ered.
Said Sutanto, “We all defi nitely agree that there are savings in terms of energy and reducing the cleaning frequency, and that means that the end-user can enjoy a more reliable and stable system, less cleaning and more uptime.
Having said that, we need to put in the eff ort to bring this awareness to our customers. Some of our customers are comfortable with our standard products, which basically means that they work well, but we need to convey to them that there are savings with
FORTILIFE TM technology and show them where the value is. We need to create awareness and guide our customers, so they are more open to adopting such technology because eventually customers do benefi t from this product.”
So far, the FORTILIFE TM product range has been well-received by end-users in India’s textile industry.
Somil explained, “In some wastewater cases, the wastewater is so harsh that current technology, or any RO membrane for that matter, is not suitable to treat these types of waters. In the textile wastewaters from India, the chemical oxygen demand (COD) of the water is very high, and if you use currently existing RO membranes, they won’t last more than three months. However, we have successfully demonstrated the use of our FORTILIFE TM membranes for more than one and a half years in such types of diffi cultto-handle wastewater, and I believe this technology will bring the next-generation revolution to the industry.”
Another highlight of the FORTILIFE TM product range, as explained by regional lead, sustainability, advocacy and communications, Chloe Tan, is that the elements are designed
The DuPont team at the recent INDOWATER exhibition
to tackle challenging wastewater and bring a more cost-eff ective approach to industrial wastewater challenges.
“Industrial plants like textile plants which are often located in areas with limited raw water availability and strict effluent discharge regulations, minimal or zero liquid discharge may be required to expand the production capacity by converting more wastewater into reusable water. Minimal liquid discharge (MLD) can help minimise manufacturing operating costs and maximise water recovery while reducing the amount of energy required to operate, comparing to zero liquid discharge (ZLD).
FORTILIFE TM fi ts perfectly into the reuse and recycling of wastewater. As a global leader in water separations and solutions, we thrive to continually looking for innovations to help our customers solve water challenges around the world. We are committed to continually working with our customers to achieve the main purpose of water sustainability and shifting towards a circular economy by closing the loop for water usage.”
Besides the FORTILFE TM product range, DuPont also focused on raising awareness towards ion exchange resins (IERs) as an essential part of the wastewater treatment process.
Somil explained, “When you recover wastewater, there is a strong chance that you might have some salt precipitation — IERs can help to avoid that precipitation by removing the hardness. Another benefi t is that wastewater often has a higher amount of organic content or colour in the system, and IERs can be used to decolourise water or remove the organic content from the water. IERs have multiple benefi ts, and can be fi ne-tuned to design for each diff erent type of water.
There are certain types of wastewater where there is a presence of heavy metals, poisonous substances, fertilisers or, for example, arsenic. Such wastewaters are very diffi cult to treat, and unless there is a way to remove these poisonous substances, these waters are almost impossible to recover. Ion exchange is a technology that can help you remove those substances because of its specifi c affi nity for those heavy metals and substances like arsenic. Without ion exchange, such water would have normally just gone to waste, but with ion exchange you can recover this water.” WWA
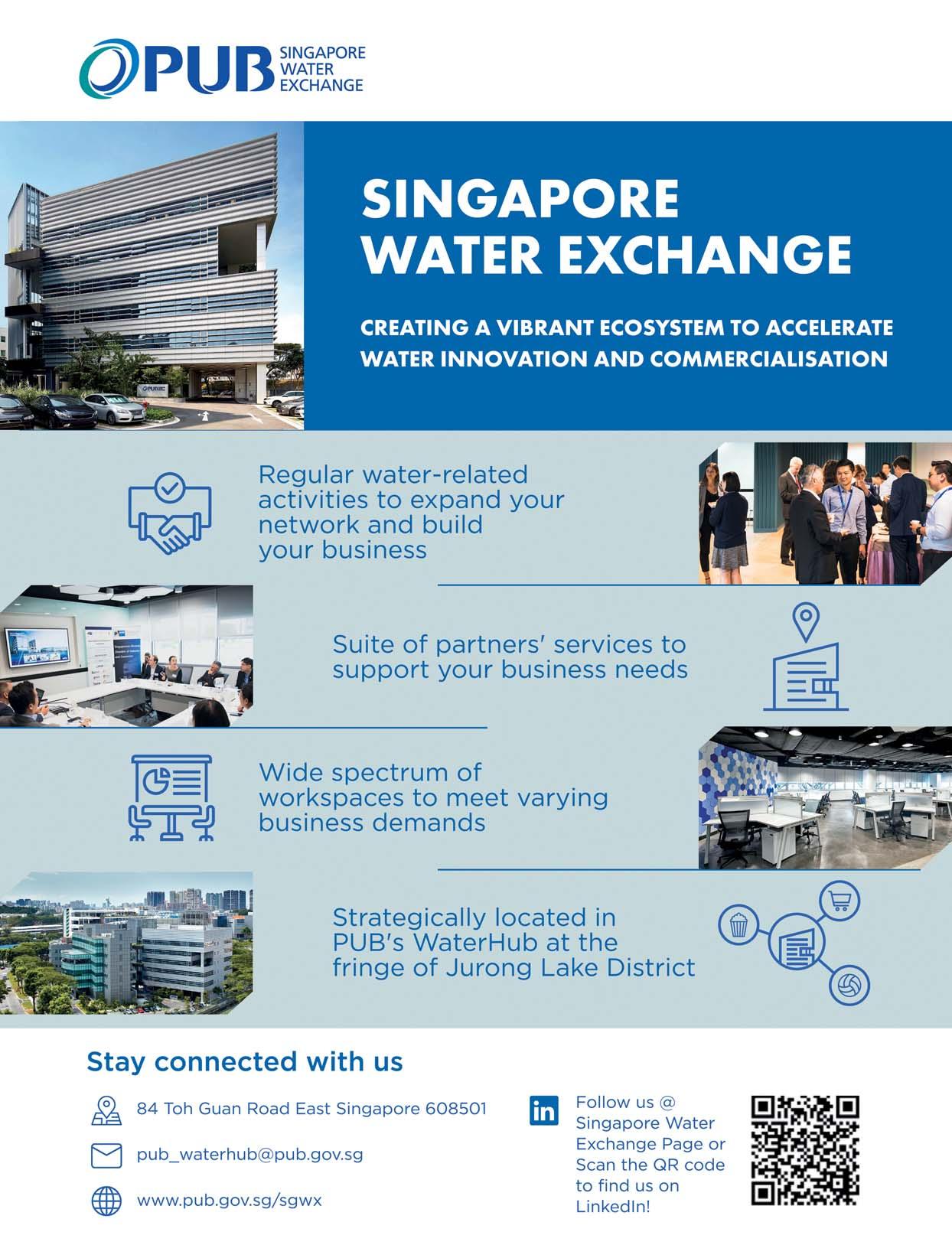