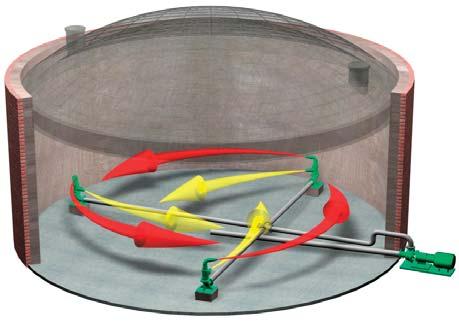
4 minute read
It’s in the mix: Rotamix® mixing systems improve process performance
What sets Rotamix apart from the rest is an absence of moving parts in its unique mixing system, which creates an even distribution of mixing energy. How does it work?
As biogas production capacity continues to increase, Vaughan Rotamix ® stands ready to provide reliable, efficient hydraulic mixing to maximize biogas production from anaerobic digestion. In addition to digesters, Rotamix is the solution for mixing all tanks in the solids handling process. Unlike most other means of tank mixing, which have mechanical components in the process, Rotamix has no moving parts in the tank, ensuring maximum performance and minimal maintenance requirements.
Advertisement
THE SYSTEM
Vaughan Rotamix is an engineered system of fl oor and wall mounted nozzles with fl ow supplied by a Vaughan Chopper Pump ® . The nozzles provide evenly distributed fl ow throughout the tank volume, ensuring complete mixing of the tank contents, while the Vaughan Chopper Pump continually conditions the digester contents, while providing industry-leading effi ciency. This combination results in lower operating costs
A Rotamix 20-metre cone, with arrows to show how it moves than conventional draft tubes or mixers, with a more effi cient breakdown of organic solids and increased biogas production. For smaller applications, like Fats, Oils, & Grease (FOG) tanks, Rotamix also off ers externallymounted nozzles which minimise piping and maximise mixing volume.
THE PROCESS
Rotamix incorporates several basic principles of physics and hydraulics, including uniform field of flow, vortical field of flow, induced flow and surface contact. Combined together, this unique mixing system optimises solids and bacteria contact while creating an even distribution of mixing energy. Dual-Zone Mixing ensures even mixing velocity across the entire crosssection of the tank, which produces an even fl ow fi eld that creates a homogenous volume, ensuring an even distribution of solids and constant temperature. This improves digester performance and prevents settled solids from reducing process volume.
Each Rotamix design is unique, varying based on many factors including sludge rheology, tank geometry, and process considerations. Vaughan uses state-of-theart Computational Fluid Dynamics (CFD) modeling to design each system and can accurately model not just the tank geometry, but also piping and other obstructions to ensure proper mixing.
A Rotamix nozzle
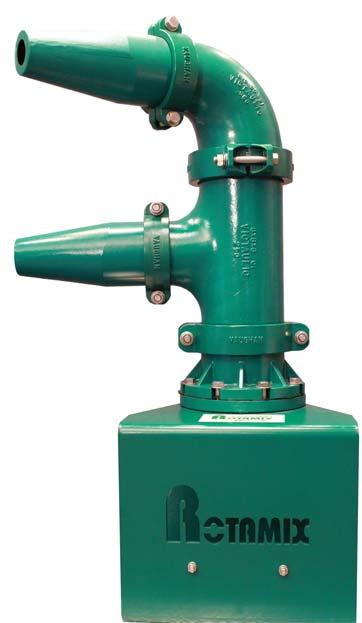
FOAMBUSTER
In many digesters, foaming can be a major operational challenge. This is why Vaughan has developed the Foambuster mixing assembly, which can be added to any Rotamix system or provided as a standalone system. The Foambuster mixing assembly works by using an integrally mounted splash-plate to produce a fi eld of droplets which suppress foaming at the surface before it can interfere with process operation.
ROTAMIX REDUCED ENERGY ADVANTAGE
Vaughan Rotamix can be paired with a
Variable Frequency Drive (VFD) to further reduce energy requirements without sacrificing mixing power. For a typical system, mixing energy can be reduced for 22 hours a day with the remaining two hours being at full power to resuspend heavier solids and promote biological contact. By varying the mixing energy this way, energy savings of over 50 per cent can be achieved.
RO2MIX
Rotamix is not just for anaerobic digesters anymore, and Vaughan Company is proud to off er Ro2Mix aerobic mixing systems. Ro2Mix uses the same quality mixing assemblies and dependable Vaughan Chopper Pumps as Rotamix, but has been adapted for aerobic processes. Aeration is provided either through integral venturi aerators or separate conventional bubble diffusers. Aeration requirements can be drastically reduced by providing separate hydraulic mixing, and this means smaller blowers, or in the case of venturi aerators, no blowers at all.
OTHER PROCESS TANKS
Rotamix is not just for digesters, and the Vaughan Rotamix can be used in any process where mixing is the key to success. Rotamix keeps sludge blend tanks and sludge equalisation tanks providing a homogenous feed to either a digester or dewatering press, and prevents deposition and sludge dewatering in sludge storage tanks. Rotamix can also be applied to lagoons, aerobic basins and anoxic zones, equalisation basins, and more.
CASE STUDY
At the Fairfi eld-Suisun Sewer District (FSSD), located 35 miles (56.3 kilometres) Northeast of San Francisco in the United States, Vaughan installed a Rotamix system in one of two identical anaerobic digesters to allow for the facility to directly evaluate if the Rotamix system provided any improvement over their existing gas mixing system. The FSSD uses biogas produced in the anaerobic digesters to power generators which supplement plant power use, meaning any improvements

to biogas production directly translate to operational savings for the facility in the form of decreased power cost. The digesters each measured 29 metres in diameter with a total volume of about 500 cubic metres and received primary and thickened waste activated sludge from the facility, with equivalent volatile solids loading.
After the Rotamix system was operational, both digesters were monitored for a period of eight months to determine if the Rotamix system had showed improved performance over the existing gas mixing system. At the end of eight months, the data showed the digester with the Rotamix system had managed to produce 31 per cent more methane from identical volatile solids loading, while using 12 per cent less operational energy. This provided for a combined 49 per cent increase in overall digester effi ciency.
CONCLUSION
The process of producing biogas from anaerobic digestion is undoubtedly important, and Vaughan Rotamix promises reliable yet cost-eff ective mixing performance.
Furthermore, unlike most other means of tank mixing, which have mechanical components in the process, Rotamix has no moving parts in the tank, ensuring maximum performance and minimal maintenance requirements. WWA All images are credited to Vaughan
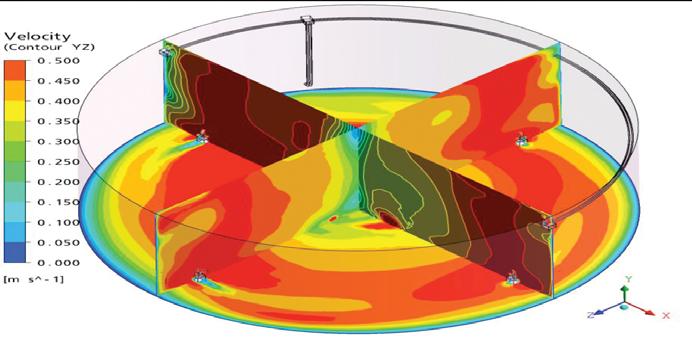
Velocity plots have proven that small diameter nozzles producing high velocity provide more complete mixing than larger diameter low-velocity nozzle designs using equal amounts of energy.