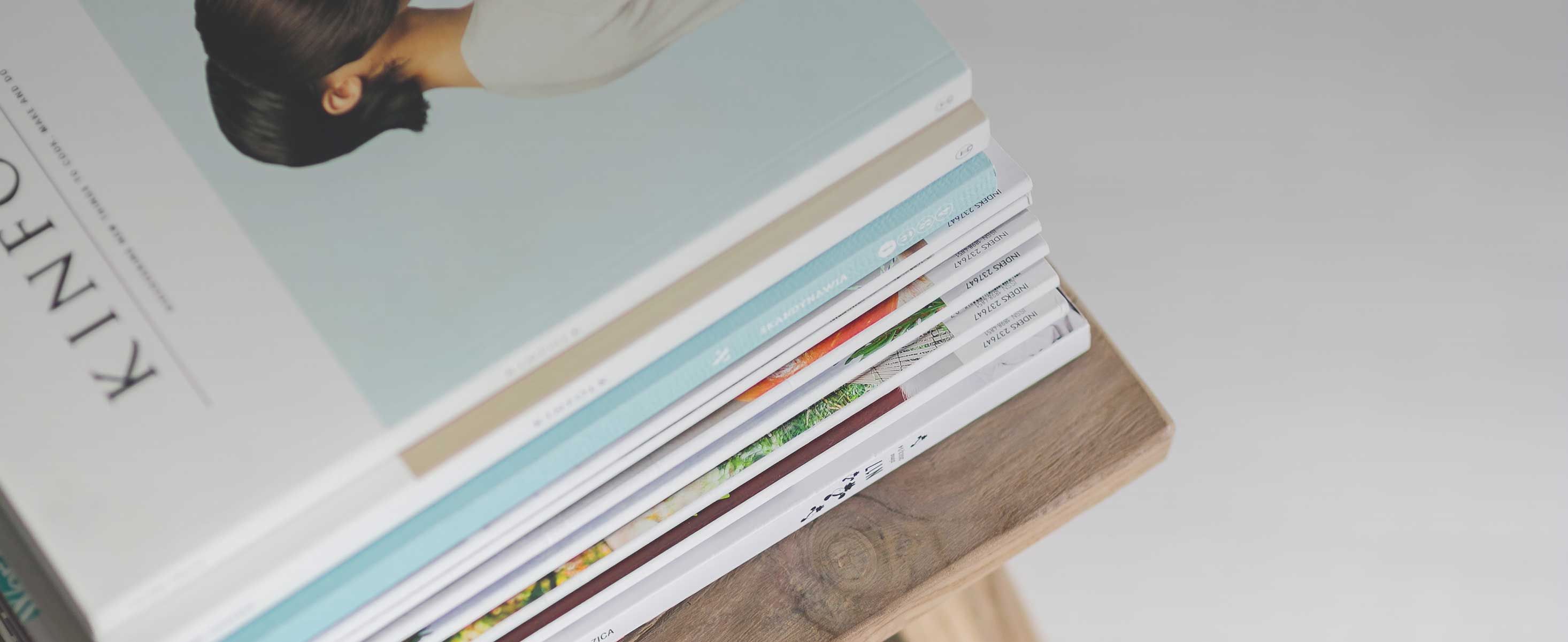
13 minute read
PROJECT RISK ASSESSMENT
Activity/Area Services / Trades Hazards Risk Level (L,M,H)
Job preparation & readiness All Trades Unfamiliar with work place M
Housekeeping All Trades Falls Slips and trips
M
Use of electrical equipment All Trades Electric shock Dangerous electrical event
M
Use of ladders and trestles/planks All Trades Falls H Mandatory Controls
SWMS will be prepared for all work conducted by the sub contractor. The SWMS will be reviewed by ORBIT HOMES before the commencement of work. The Project Manager will monitor compliance to the SWMS. All contractors will review WHS Management Plan on each job. Housekeeping standards are to be kept to prevent the introduction of additional risks –slips/trips, dust exposure, falling objects. All rubbish to be placed at front of lots in bins provided. The ORBIT HOMES Project Manager will monitor sub contractors to ensure they are aware of and complying with the following during their inspections: All electrical equipment and leads must be Tested & Tagged every 3 months. Electrical tools/leads will be visually inspected to ensure they have a current test tag and are not damaged. New tools are also required to be Tested & Tagged prior to using on site. RCD’s are being used between the electrical plant and the temporary power source. Electrical (10amp) leads don’t exceed 25m in length and are not joined together to exceed 25m in length. Where there is no power supply within 25m of the work area, a generator set may be used. This will require a separate risk assessment based on the model and type of plant and the workplace conditions at the time Applies to all ladders All ladders are to be adequately secured against displacement whilst in use. Ensure that the structure/material supporting the top of the ladder can withstand the load. All ladders are to have firm, level footing No objects are to be carried in workers hands whilst traversing a ladder. All objects must be carried in a suitable backpack or manipulated by using a haulage line. All ladders used are to be of an industrial strength & clearly marked "For Industrial Use" with a load rating of not less than 120kg. Only one (1) person is to access a ladder at any one time All sub contractors must utilise a 2 lank min 450mm wide when using planks and trestles under 2m off the ground. Extension ladder specific requirements Single & Extension Ladders are to be pitched at an angle of approximately (1) horizontal to (4) vertical (1:4) or approximately 75 degrees to the horizontal. Single & Extension ladders are not to be used to support planks. Ladders are to be placed so that they extend approximately 1 metre above the area requiring access. If a person is to use a Single or Extension Ladder for access: o The person maintains three points of contact. o The ladder is secured at or near the top and/or bottom to prevent it moving.
Activity/Area Services / Trades Hazards
Set up & using Scaffolds Including Mobile Scaffolds and Edge Protection/ Guardrail Including but not limited to
Scaffolders Falls Falling objects
Use of EWP’s Carpenters Painters Working around
Mobile Plant Falls Crush injury
Cutting Bricks, Blocks and Tiles Including but not limited to
Bricklayers,
Tilers Breathing in dust Particles entering eyes
Performing Hazardous Manual Tasks All Trades Hazardous Manual Tasks
Hazardous Chemical use and storage Environmental
Spill/Contamination Poisoning Fire/Burns Fume inhalation L The Sub Contractor is to have on hand a Hazardous Chemical Register and the Safety Data Sheets for all Hazardous Chemicals.
Risk Level (L,M,H)
H
M
Mandatory Controls
Scaffold above 4m is to be erected by a licensed scaffolder in accordance with the manufactures instructions and relevant standards, a separate SWMS will be obtained from the scaffolder if scaffold is being erected above 4m. Under 4m set up by competent persons and erecting procedures will be provided with the scaffold. If required signage is to be in place indicating scaffold is incomplete. Sign off indicating scaffold is erected in accordance with all relevant Australian Standards is to be received prior to anyone using the scaffold. All workers to maintain access within the stiles of the ladder. If the scaffold requires altering, the Sub Contractor is to contact the Project Manager to arrange. The
Sub Contractor is not to alter any part of the scaffold. Sub Contractor to notify the Project Manager immediately if they find the scaffold to be unsafe to work on. Operator to be competent and have licence for EWP with a boom over 11 metres (high risk work licence required). Where the EWP has a boom under 11m the person will have a yellow card & SL ticket for scissor lift. Undertake a site inspection to identify hazards and put in place the required control measures. Ensure that all maintenance and pre-start checks have been completed as per manufactures operating manual. The workers undertaking work in the EWP must consult with other workers in the vicinity and ensure that are aware of the hazards involved. Ensure clear path of travel no obstruction and level ground. Only lift loads that are within the load rating of the machine this includes persons and ensure all loads are kept within the work platform. Handrails are not be used for access. Obtain and secure appropriate safety harnesses. Check that safety harnesses are attached to the designated anchor point within the work platform.
M All trade must wear appropriate PPE to prevent inhalation of dust particles and prevent debris entering eyes.
M
The Sub Contractor is to ensure their workers have knowledge of safe lifting practices including how to reduce the hazardous risk factors of: Awkward Postures High Force Duration Repetition Vibration Sub Contractors are to use mechanical and/or team lifting when possible – crane materials onto roof where possible. Sub Contractors will monitor safe and clear access and safe housekeeping practices.
Program Risks
Earthworks Surveyor, Carpenter, Electrician, Plumber, Excavator/Bobc at Working around
Mobile Plant Contact with underground services
Frame (Wall & Roof) and structural steel
Roof sheeting + Antenna, Vent pipe
Rough-in services
Internal cladding
Cabinets and Fitout services Concreter, Concrete Pump Plumber Electrician
Mobile Crane Carpenters Delivery trucks Scaffolders
Roofers Antenna Installer Plumber Mobile crane
Plumbers Electricians Carpenters Glazers Carpenters Delivery trucks
Plasterers Delivery trucks
Waterproofing Tilers Cabinet makers A/C Mechanic Roller Door
Installers
H
Sub Contractors using mobile plant will hold appropriate licensed where necessary and verification of competences will be provided. Underground services will be identified and marked before the commencement of earthworks. Sub Contractors onsite will be notified that mobile plant will be in use. Where multiple trades are in the area, exclusion zones will be established and a spotter will be used.
Exposed trenches and pier holes Working around mobile plant Falling objects Working around mobile plant Scaffolding –unsafe plant Falls
Falls Falling objects Scaffolding –unsafe plant Hazardous Manual
Tasks Falls
H
H
H
Sub Contractors are to supply a SWMS that addresses the risk and acceptable means of control. Where no common work at heights controls are in place, the contractor must provide their own. Sub Contractor personnel are to provide evidence of competence to undertake scope of work for plant and equipment. Sub Contractors are to supply a SWMS that addresses the risk and acceptable means of control. Where no common work at heights controls are in place, the Sub Contractor must provide their own. Sub Contractor personnel are to provide evidence of competence to undertake scope of work for plant and equipment. Structural steel will be erected by a licensed rigger Sub Contractors are to supply a SWMS that addresses the risks and acceptable means of control. Where no common work at heights controls are in place, the contractor must provide their own as per their contract. Sub Contractor personnel are to provide evidence of competence to undertake scope of work for plant and equipment.
M Sub Contractors are to supply a SWMS that addresses the risk and acceptable means of control.
Falling objects L
Falling Objects Falls Dust Poor housekeeping
M
Housekeeping standards are to be kept to prevent the introduction of additional risks – slips/trips, dust exposure, falling objects Sub Contractors are to supply a SWMS that addresses the risk and acceptable means of control. Sub Contractors are to supply a SWMS that addresses the risk and acceptable means of control. Where no common work at heights controls are in place, the Sub Contractor must provide their own. Housekeeping standards are to be kept to prevent the introduction of additional risks – slips/trips, dust exposure and falling objects.
Falling objects L Housekeeping standards are to be kept to prevent the introduction of additional risks – falling objects.
Program Risks
Cutting Engineered Stone Stone Masons Kitchen
Installers Breathing in silica dust
H
Painting Painters
Floor coverings
Fencing / Driveway Tilers Carpet layers Carpenters Water proofers
Machine operator Fencing contractors Concreters
Landscaping Turf/plant supplier Landscaper Labourer Bobcat/Machine operator Not limited to bobcat Environmental
Spill Hazardous
Chemicals Scaffolding Fume Inhalation Hazardous
Manual Tasks Hazardous
Chemicals Hazardous
Manual Tasks Working outdoors – UV Hazardous
Chemicals Working around mobile plant
Hazardous
Manual Tasks Working around mobile plant Working outdoors - UV
Explosive Power Tools All Trades Being hit by flying debris
Fatigue All Injury due to tiredness Accident driving to and from work
M
M
M
M
H
Subcontractor to wear appropriate PPE to prevent inhalation of silica dust when working with engineered stone. All cutting of engineered stone to be carried out in the correct controlled environment where possible. Where required to cut engineered stone on site, signs must be erected advising of this activity. All cutting must be carried out with a wet cut method and all residue to be removed from site. Under NO circumstances is the engineered stone to be dry cut.
Sub Contractors are to supply a SWMS that addresses the risk and acceptable means of control. Where no common work at heights controls are in place, the contractor must provide their own. The Sub Contractor is to have on hand a Hazardous Chemical Register and the Safety Data
Sheets for all Hazardous Chemicals.
Sub Contractors are to supply a SWMS that addresses the risk and acceptable means of control. The Sub Contractor is to have on hand a Hazardous Chemical Register and the Safety Data
Sheets for all Hazardous Chemicals.
Sub Contractor personnel are to provide evidence of competence to undertake scope of work for plant and equipment. Mobile plant operators are to hold necessary licenses for plant operation and provide verification of competences Sub Contractors are to supply a SWMS that addresses the risk and acceptable means of control. The Sub Contractor is to have on hand a Hazardous Chemical Register and the Safety Data
Sheets for all Hazardous Chemicals. (with regard to hydrochloric acid to clean driveway)
Sub Contractors are to supply a SWMS that addresses the risk and acceptable means of control. Sub Contractor personnel are to provide evidence of competence to undertake scope of work for plant and equipment. Mobile plant operators are to hold necessary licenses for plant operation and provide verification of competences.
Sub Contractors are to implement a no go zone of a minimum 5m of open space from the explosive tool Sub Contractors are to ensure no persons are with in the exclusion zone when using the explosive tool Sub Contractors are to ensure consideration is given to rest breaks, work hours and travelling times to and from site. Sub Contractors are to consider the following factors that contribute to fatigue: physical demands of the work, climate, work environment, lifting and handling of materials.
SITE RULES
The following site safety rules apply to the site. Any persons deliberately violating these rules or other WHS requirements will be subject to disciplinary action. All personnel on site must ensure:
All safety signs are to be complied with in full. All danger tags and signs on electrical equipment and scaffolding must be obeyed. Work is to be done in a safe and professional manner. Safe systems of work and appropriate documentation must be available upon request. I.e. SWMS. No alcohol or illegal drugs are permitted on site and any person found to be affected by alcohol or drugs will be denied access to the site. Appropriate footwear, high-visibility clothes and correct PPE for the work activity being performed must be worn at all times. Do not use unsafe or faulty tools, ladders, electrical leads or other equipment under any circumstances. All plant and equipment must be fit for purpose and suitable for use. No piggy back leads or double adaptors are to be used on site. Electrical equipment and leads are to be inspected and tagged (3 monthly) and placed to avoid damage on site. A register of all plant must be available and kept on site. Ladders must only be used as per manufacturer’s requirements and be industrial 120 kg or above rated strength only. Work areas are to be kept clean with access ways free from hazards at all times. Rubbish is to be placed in the appropriate bins provided on site. All deliveries are to be placed in a safe storage location. A copy of the respective MSDS and Safe Work Method Statement is to be given to Orbit Homes Queensland upon request. All personnel undertaking works where a licence is required to operate plant must hold the appropriate licence before operating relevant plant. All
personnel are to be trained and instructed in the use of other plant and equipment where required. This includes general competency, certificates, licenses etc as required. Under no circumstances are operators permitted to use mobile phones whilst operating powered mobile plant. A blue/white construction induction card is required by all individuals entering a construction site. No person is to alter or remove any plant, equipment or safety device on site.
This includes scaffolds, handrails, barricades, signage, guards, etc. All work at heights must be risk assessed and relevant controls implemented.
Work conducted at 2m or over must have appropriate controls implemented and documentation provided. Maintain protection over all protruding elements, bolts or fixings. Penetrations or core holes are to be made safe at all times. Ensure all temporary bracing or propping is securely fixed and not liable to fall if knocked. Avoid working above other workers. Barricade around raised work platforms. Before using oxy acetylene welding equipment or igniting any flame, ensure charged fire extinguishers are brought to the area of the work. Theft of any kind will not be tolerated and will be reported directly to the police. All accidents/incidents, near misses, and injuries are be reported to the Orbit
Homes Queensland Construction Manager/Site Project Manager immediately. Comply with instructions given by Orbit Homes Queensland Site Management at all times, without exception.