
11 minute read
INNOVATIONS IN ASPHALT
by James Careless
As defined by the Asphalt Recycling & Reclaiming Association (ARRA), “3D milling utilizes data from a digital model of a pavement surface to automate grade control during the milling process. The result is a dramatic increase in accuracy of milling depth and an overall increase in roadway smoothness relative to traditional methods in which depth of cut is manually controlled by a milling operator or groundman.”
Along with the benefits, the adoption of 3D milling technology also comes with equipment and training costs for asphalt paving companies. At OAPC’s Fall Asphalt Seminar in December 2022, a panel came together to discuss the opportunities and challenges of 3D milling technology.
IS 3D MILLING BENEFICIAL FOR REDUCING EMISSIONS OF GREENHOUSE GASES?
The consensus from the panel was a general ‘yes’. Using 3D-milling technology to prepare a roadbed for resurfacing can reduce emissions because the milling work can be done with more certainty.
“With 3D milling, you’re only going to mill it once,” says Jeramus Wakefield, Asphalt Supervisor at Aecon. “When you mill it the first time, you’ll be correcting the crossfall and the smoothness as much as possible. As a result, you are reducing how much you’re going to need.”
“The technology can predict the amount of RAP generated, which ultimately can result in the reduction of truck idle time and eliminate unnecessary trucking kilometres,” adds David Gauer, Territory Manager with Brandt Positioning Technology. “3D milling will result in greenhouse gas reduction in projects where the quantity of milling is reduced when compared to fixed depth milling process,” agrees Stephen Lee, head of the MTO’s Pavements and Foundations Section.
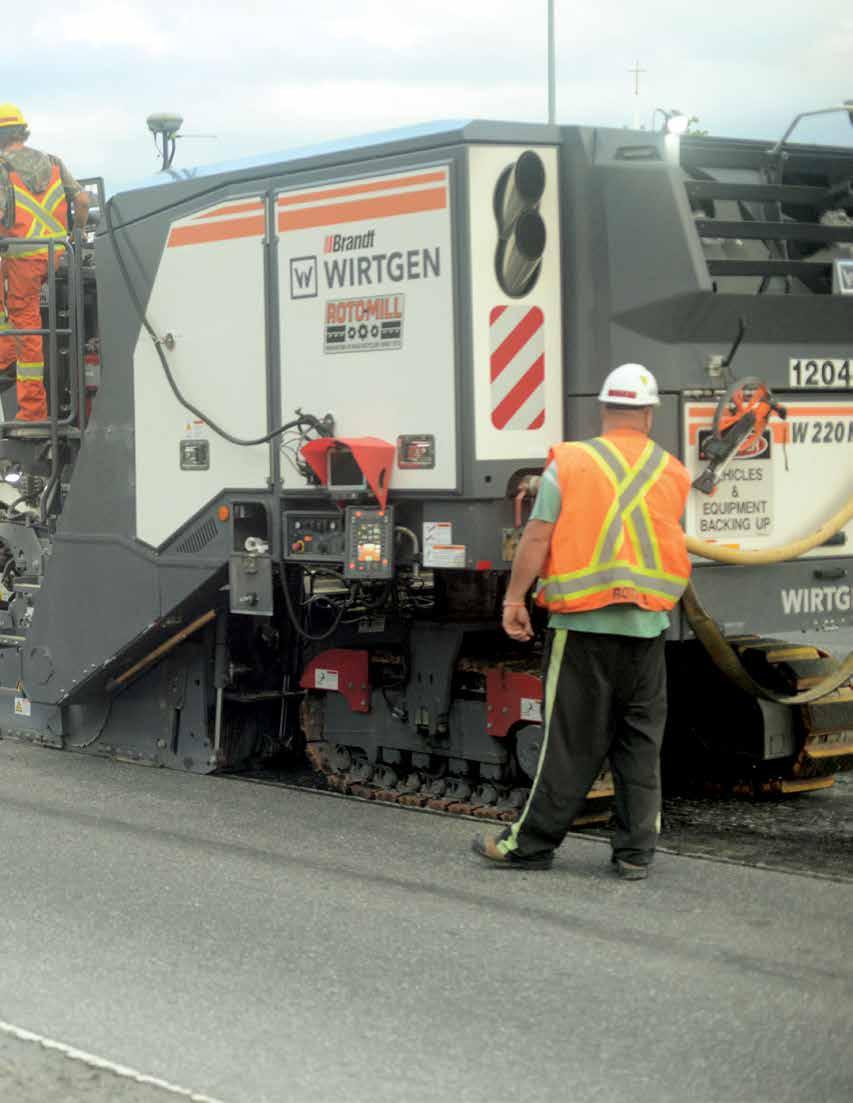
ARE PRODUCTION RATES AFFECTED BY THE 3D MILLING PROCESS? IF SO, ARE THEY INCREASED OR DECREASED?
A big concern for asphalt paving companies who are required to use 3D-milling technology is the impact on their workflow. Fortunately, the answer to this question is reassuring for the industry.
“Overall, the production is going to be the same, but it’s not really a ‘shave and pave’ anymore. It’s now about reconstructing/rehabilitating a road and fixing some of the problems that are there,” says Ben Hobbs, Director of Sales with ABTECH.”
“The advantage of 3D milling/variable depth design milling is that you will know your production rates before you start the project,” Gauer says. “The power of milling to a design means that within the software you can control the depth of milling and alter it to control the production rates.”

HOW IMPORTANT IS THE DIGITAL DESIGN MODEL (DDM) TO A PROJECT’S SUCCESS?
For a 3D-milling system to accurately mill a roadway to the appropriate depth throughout the full length of the roadbed, a high-density scan of the existing pavement needs to be taken. Using ground imaging technology such as LiDAR
(Light Detection and Ranging), GPR (Ground Penetrating Radar), etc., this scan shows the actual condition and composition of the roadbed. The data from the scan is then used to create a Digital Design Model (DDM).
During the panel discussion, the question was raised of how important the quality of the DDM is when it comes to successful 3D milling. “This is the most important part of the project that has to be done accurately,” says Steve Gostis, Paving Products Specialist with Toromont CAT. “The crew and machine rely on this data to get the job done.”
“Everything’s based on the Digital Design Model,” agrees Mike Deckert, Vice President of FLO Components Ltd. “If there are errors in the data or surface that the machine is following that are incorrect to the overall objective of the project, then there will be errors in the final project,” Gauer adds.
As to who should be responsible for storing these 3D models, opinions vary. “The road agencies are responsible,” Lee says. “The MTO project office will keep the DDM files as part of their project files.”
“The general contractor is responsible and it is up to their discretion on who they share it with,” says Gauer. “They are responsible for the final product. Therefore, they should control the data.”
The panelists also noted that the time of year that a highdensity scan was done can affect its accuracy for DDM usage. A scan taken during spring may not show what the roadbed condition will be in the fall when work is scheduled to be done. Changes will also occur from year to year, which is why up-todate high-density scans are preferred to create DDMs.
DOES 3D MILLING ADDRESS SCABBING OR THE POTENTIAL FOR SCABBING/PUNCH THROUGH?
Can 3D milling minimize issues such as scabbing (not fully removing the surface being milled) and punch through (cutting into the next layer)? “Theoretically yes,” says Gauer, “but we have to know what is existing on the road prior to milling” through boreholes and/or scans using GPR and other methods.
Loss Of Gps Signals During 3d Milling
3D milling-equipped excavators rely on GPS location signals to ensure the accurate execution of their DDMs. “If you’re in northern Ontario and you’re going through a rock cut, that could disrupt reception of the GPS signal which could be an issue,” Deckert says. The same is true for “urban canyons in downtown Toronto,” says Hobbs “We do lose GPS signals underneath bridges,” Wakefield adds.
WHAT TYPES OF PROJECTS HAVE BEEN COMPLETED USING 3D MILLING AND WHAT EXPERIENCES CAN BE SHARED?
According to the panelists, 3D milling has already been used successfully on a number of road projects across the province. “I have been involved in three types of projects: municipal road projects in the GTA, parking lot rehabs, and the 401 expansion from Mississauga to Milton,” says Gauer. “Our 3D milling equipment on the 401 was able to control the depth to make the old and new sections of the road match seamlessly. The contractor was able to predict the amount of asphalt needed to complete each section of the project, and to control trucking and plant production times using information from the DDM.”
DOES THE AGE OF THE MILLING MACHINE MATTER FOR ADAPTING IT TO USE 3D TECHNOLOGY?
Good news: “It does not matter,” Gostis says. “The short answer is no,” echoes Gauer. “We are able to automate most if not all milling machines that are correctly operational in Ontario. Older machines just might need specific sensors installed for the 3D milling technology to work.”
WHAT ARE THE MINIMUM REQUIREMENTS FOR USING 3D TECHNOLOGY IN MILLING?
More good news: “The machine must be set up for automatic grade and slope, but this is standard on all machines for milling applications,” Gostis says. “The minimum requirements would be a GPS system on the milling machine,” says Gauer.
IS IT BENEFICIAL TO USE 3D MILLING EQUIPMENT TO GENERATE RAP?
For environmental reasons, RAP (reclaimed asphalt pavement) is an important component in Ontario paving projects. According to the panelists, 3D milling can be used to create RAP and there are benefits in doing so.
“One benefit would be the predictability of the amount of RAP that would be produced during the project,” Gauer says. Another would be minimizing the amount of RAP produced during the milling process to match the “quantity required to obtain the smoothness of the end profile desired with final paving,” says Lee.
Potential Negative Impacts Of 3d Milling
Moving to 3D milling could entail financial risks for paving contractors due to the money they will have to invest in new equipment and training. Some question the impetus to roll out 3D milling in Ontario, especially as some jobs that could be designated as requiring 3D milling could actually be done using existing 2D systems.
So how big are the risks? Not very.
“The idea of milling and paving to a design is new to the industry and does have some risk,” says Gauer. “But that risk is minimized by potentially producing a far superior product, while finding problem areas prior to the bid or the start of operations.”
“There’s an upfront cost,” says Wakefield. “But overall, I would say that it is a savings.”
As for using 3D where 2D would do?
“Milling or paving just to the 2D slope might not fix the issues of the road,” Gauer says. “It ignores the depth and smoothness, which is ultimately left up to the operator of the machine. With the 3D DDM, you have a full picture of the project and can predict the outcomes.”
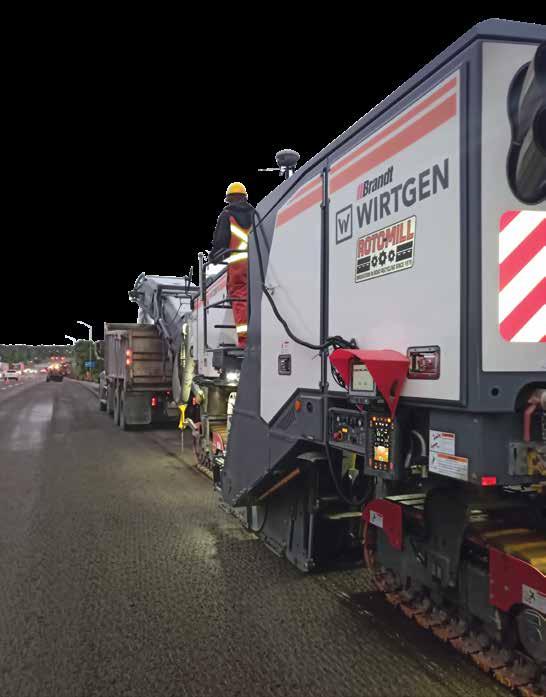
Clarifying The Opss 510 Specification
The rules for 3D milling in Ontario are laid out in Ontario Provincial Standard Specification (OPSS) 510, which is the result of ongoing consultation between the MTO and industry. This question was posed to the panel: “There are a few areas still requiring clarity and some direction in terms of the types and capability of the milling equipment, the smoothness of the milled surface, and how to measure elevation against the +/- 5 mm milled surface tolerance relative to texture expectations. The industry strongly feels that guidance for the machine should not be dictated by method, but by accuracy.
If the intention of the 510 specification is to say that the machine is controlled both vertically and horizontally, we think this is unachievable. Recognizing that it could take some time to replace existing fleets, why does the 510 specification not rely on stipulated requirements to achieve a milling tolerance of +/- 5 mm from the DDM?”
According to Gauer, this concern is unwarranted. “In my opinion I believe the technology can control the machine vertically and horizontally. It can also achieve a tolerance to 5 mm of the DDM.”
“I think there is some misinformation out there about the technology and its capabilities,” he adds. “The industry needs to consult with contractors in Canada who have used it successfully and have achieved project bonuses with the utilization of the technology.”
When asked, “Does the OPSS 510 allow or accommodate milling machines that use only local ground referencing systems?” the MTO’s Lee replies, “Yes, contractors always have the option to submit a Change Order for consideration.” Meanwhile, the 510 specification “will only be used on limited trial projects or contractor Change Order, Design Built, or Alternate Finance projects,” he says.
Another question posed was: “There have been many historical contracts where the existing HMA thickness was not sufficient to accommodate the specified milling depth. Does 3D milling eliminate the potential for ‘punch through’, and how does the 510 specification address this? “Use of GPR (ground penetrating radar) and borehole data to mitigate punch through will still be required. 3D milling will not eliminate punch through,” says Lee.
Encouraging Innovation
To wrap up the panel on 3D milling, OAPC asked the panelists to focus on recommendations that would encourage paving contractors to take a positive stance towards the adoption of 3D milling technology in Ontario. To this end, they were asked, “What advice can be offered toward reconciling the drive/push by most owners to be more innovative, and the industry’s stance that existing milling/paving equipment has the capability to provide an excellent finished product?”
On this point, Gostis says, “I believe that technology will continue to drive our industry forward, and as it does, accordingly we will have to adapt and keep up with it.”
Taking a more pragmatic stance, Gauer observes that “The technology is here and has been here for a while. The best advice I can give is to do your research, and reach out to contractors that have used the technology successfully.”
“The MTO is willing to talk and communicate with anybody working with them,” concludes Deckert. “There is no reason for Ontario paving contractors to go it alone in implementing 3D milling technology. The provincial government is willing to assist them in doing so.”
Session moderator: Mike Deckert, Flo Components
Panelists: David Gauer, Brandt Tractor Limited • Steve Gostis, Toromont CAT • Josh Guest, Roto-Mill • Ben Hobbs, ABTECH • Stephen Lee, MTO • Jeramus Wakefield, Aecon
A link to the PowerPoint presentation can be found on OAPC’s website under Publications & Education/Fall Asphalt Seminar Presentations
James Careless is an Ottawa-based freelance writer with credits in the National Post, Toronto Star, and AI’s Asphalt magazine.
