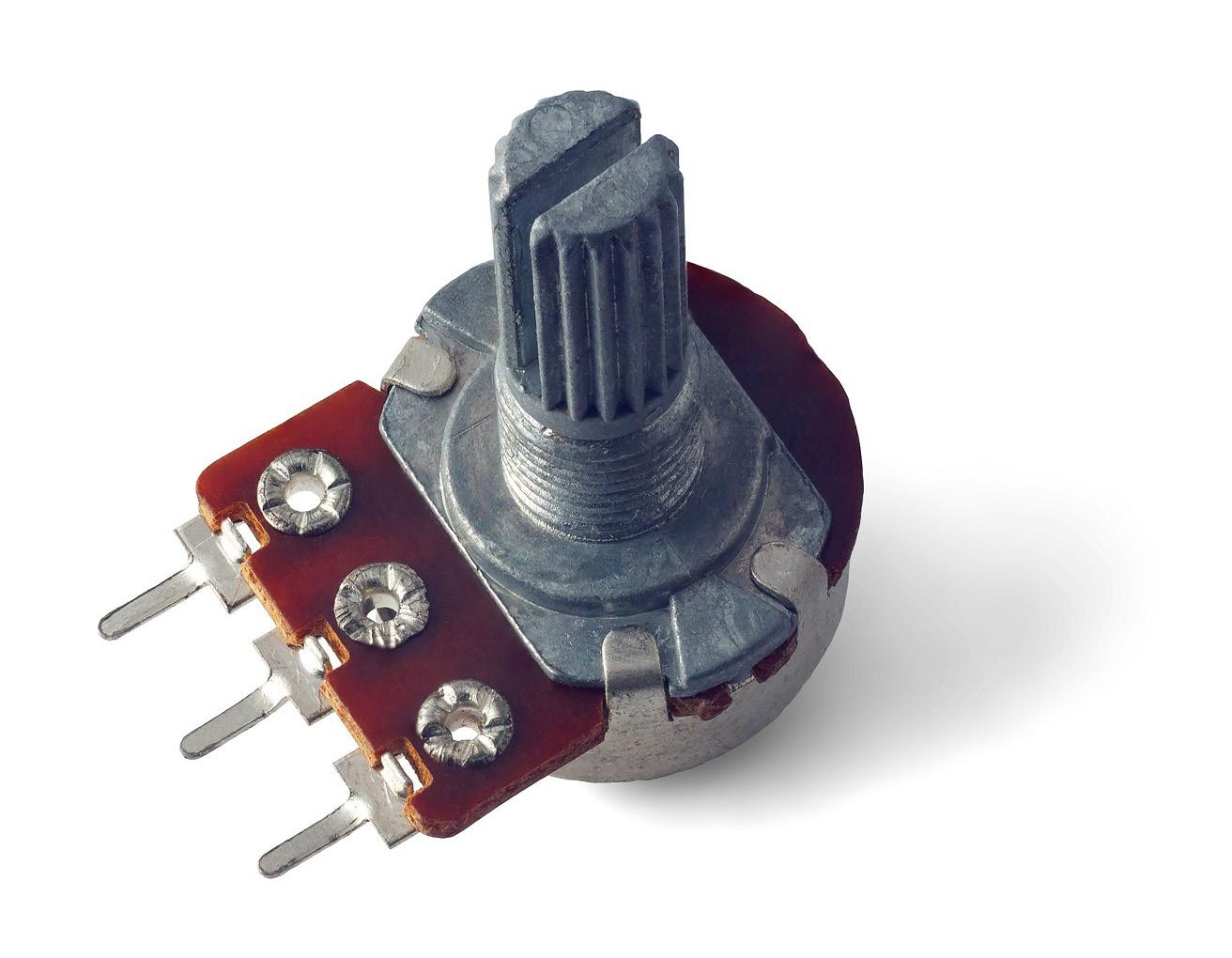
7 minute read
Improving Linear Actuator Design Flexibility with Noncontact Position Sensing
by Travis Gilmer, Thomson Industries Inc.
Many linear motion applications that use rodstyle electric actuators require information on the position of the load at every point of travel. However, because stroke lengths and applications vary, finding the ideal position feedback solution can be challenging. One of the most common methods for determining where the actuator is in its stroke uses potentiometers, also called pots. They track changes in electrical resistance or related voltage drops as the actuator extends and retracts.
Advertisement
To function as position-recording devices, potentiometers must maintain an electrical connection to the actuator power circuit. Designers can accomplish this using contact or noncontact potentiometer architectures. Contact-based position measurement has been the simplest and most economical approach but is limited in resolution, design flexibility and durability. Noncontact architectures overcome many of those drawbacks but have traditionally been too expensive to justify for many mainstream applications.
Today, however, the market for noncontact potentiometers has matured, and prices have dropped. Understanding the advantages of noncontact potentiometers will help motion system designers determine the most effective way to meet customer requirements.
Due to eliminating gearing and wipers, noncontact potentiometers better absorb shock and vibration from heavy-duty applications. These potentiometers, along with many other control and performance features, can be found in select electric linear actuators. One of the most common methods for determining where the actuator is in its stroke uses potentiometers, also called pots, to track changes in electrical resistance or related voltage drops.
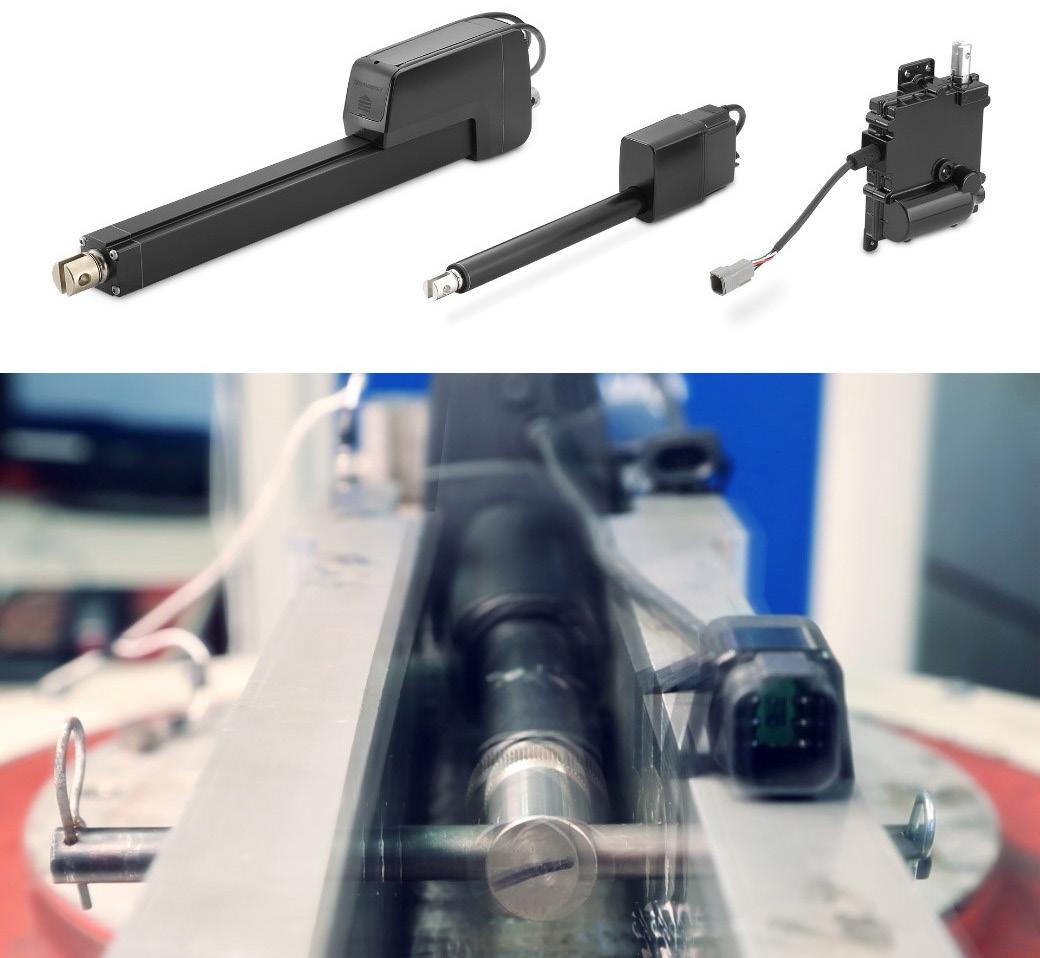
©DMITRY S. GORDIENKO – STOCK.ADOBE.COM
The Basics
Feedback voltage from a potentiometer typically changes from 0.5 VDC to 4.5 VDC as the actuator extends. Potentiometers are generally rated in ohms of resistance across their range and on the shaft’s number of turns (revolutions) from zero to full coverage. The most common units are 10k (ohms) 10 turns.
As the actuator screw extends or re-
Power to Break New GrouNd
Cummins is always looking for ways to help our customers succeed – pushing harder to deliver a range of power solutions, that help get the job done whilst reducing environmental impact. We’re breaking new ground with advanced diesel, renewable fuels, hybrid, battery electric and hydrogen, increasing productivity and lowering maintenance costs.
We’ve been powering agriculture for over 100 years and we’ll be doing so for 100 more. Delivering power, efficiency and reliability as well as peace of mind. So, no matter what powers your farm, Cummins has the technology to meet your needs.

tracts, discrete step-change in resistance occurs, which can be converted into linear position measures. The more turns the potentiometer takes before it reaches its full resistance range at the end of the stroke, the more precise the position measurement capability it can deliver.
A contact-based potentiometer reads these voltage changes by gliding its wiper across wire-round resistance coils, counting each move from one wrap to the next. Noncontact potentiometers read the voltage changes as well but do so with electromagnetic sensors instead of contacting wipers. The designer’s degree of flexibility in installing contact- or noncontact-based potentiometer position sensing depends largely on the users requirements. Customer requirements for resolution and durability will impact a designer’s options to use contact or noncontact position measurement.
Designing for High Resolution
With contact potentiometers, the designer’s primary option for increasing resolution is modifying the gearing to correlate potentiometer turns with motor or actuator screw turns. Designers who need position feedback across a full, long-stroke application might gear the potentiometer to turn less as it moves. For example, in a short-stroke application, if the customer required position information for only 40% of travel, they would sacrifice resolution because there would be less resistance change given the shorter travel time.
Because the number of wraps in the coil of a contact-based architecture is physically limited, there are only so many step changes to count, limiting the resolution of the position information it can deliver. And once a manufacturer has configured it for a specific number of turns needed to achieve the desired resolution, the design is set.
Noncontact potentiometers, on the other hand, enable higher resolution because they do not rely on physical wipers or gearing. Like contact-based potentiometers, noncontact sensors determine position by recording resistance changes across the stroke length. Instead of getting this information from a physical wiper touching a coil, they use an electromagnetic sensor that detects pulse changes in the surrounding magnetic field.
The sensor outputs this digital signal to a noncontact potentiometer’s integrated circuit, which converts it to analog for reading by the actuator’s onboard electronics. This signal represents the analog values as position. Because these signals do not need to correlate with physical constraints, the noncontact potentiometer gives virtually infinite granularity in measuring the stroke position.
Design Flexibility
The ability to record infinitesimally small voltage changes without physical contact and manage them through a software interface makes resolution programmable. If the end user needs tighter resolution, the designer can change it through the interface. For instance, if the application requires a high resolution between 0.5 volts (V) and 4.5 V, they can program the system to accomplish that. If the end user didn’t need as much resolution, the designers might program it to go to 2.5 V at the end of the travel. The designer can do it all with software rather than physical gear reductions.
Such programmability can be valuable in applications needing to change the stroke to compensate for different geometries. Actuators with contact potentiometers might return different feedback from different strokes. Correcting this would require dedicated gearing for each stroke length. With a programmable noncontact device, the designer can maintain the same feedback over the stroke regardless of changes in geometry. A user can keep that consistency without having to modify the physical architecture.
Noncontact potentiometers would also make it easier for the designer to program more complex movement profiles. For example, they may move forward a few millimeters or make a small set of movements back and forth to zero on the desired position.
Noncontact potentiometers can be valuable when the actuator must move repeatedly and consistently to a location, such as managing the flow gate in a seeding application. In these applications, the actuator operation may be controlled by a programmable logic controller (PLC) and hidden from an operator’s view, so there is no visual feedback to help determine whether the actuator traveled far enough. The programmability of noncontact potentiometers also makes them excellent for custom applications. One part number, for example, can be programmed to manage multiple stroke lengths.
THOMSON

Noncontact potentiometers are ideal for applications such as mobile off-highway/agricultural (left) and factory automation/automated guided, vehicles (right). In these applications, the actuators might be hidden from view and under the control of a PLC. The potentiometer can be programmed to drive the same distance and travel the same length every time.
Durability
Noncontact potentiometers have
durability advantages. Eliminating the gearing improved durability. Gearing is subject to routine wear, contamination and misalignment resulting from vibration and shock. As such, they are excellent candidates for replacing hydraulic cylinders that may be specified for environmentally challenged applications needing position control.
Eliminating the need for wiper contact and gearing gives noncontact potentiometers another durability advantage when compared to contact devices. In an application in which the actuator does not change position for an extended period, the wiper may vibrate and wear a dead spot on the coil. This would drop the signal and cause the potentiometer to fail. When this happens in a system that runs process logic, a contact device loses track of the position and can also interfere with some controlled moves. A movement profile that depends on a specific value will not find it, which could replace the potentiometer or the actuator.
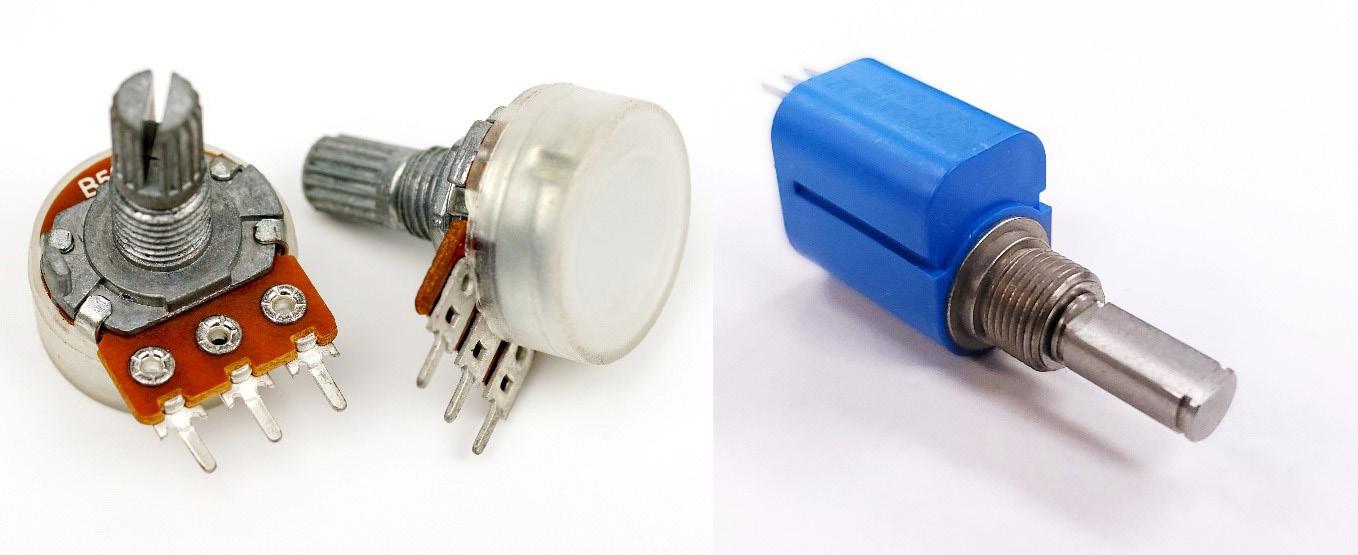
Breaking Contact
Designers who have believed that noncontact potentiometers were only for high-precision applications may want to revisit them for all applications. Even if high resolution is not critical, removing gearing from the bill of materials, programmable position feedback and a more rugged solution could offer significant advantages.
As the design and specification process becomes more iterative between engineering and customer teams, programmable capabilities such as the noncontact position sensing will deliver more tailored solutions in less time, without creating additional tooling.
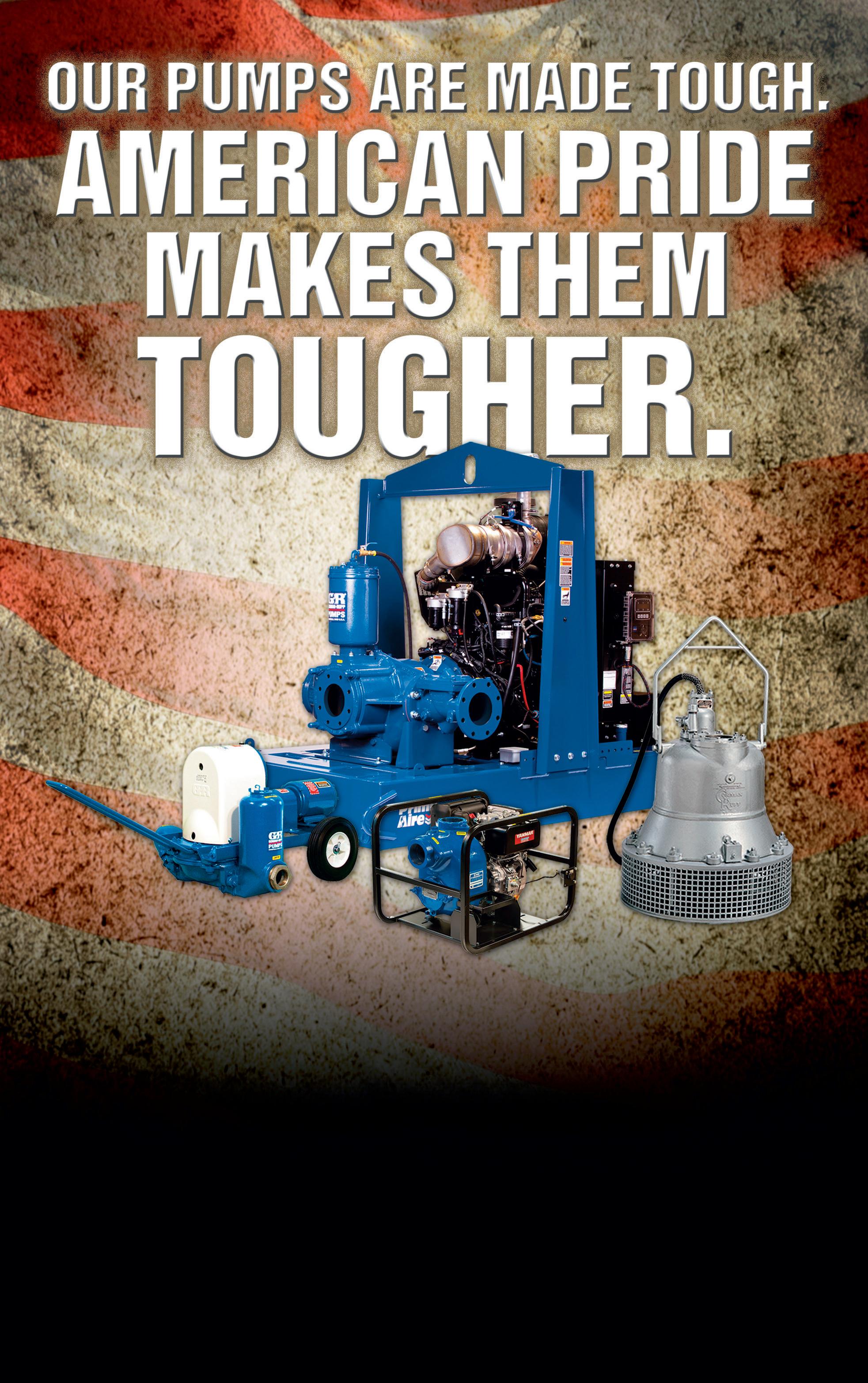
Travis Gilmer is a product line specialist for linear actuators at Thomson Industries, Inc.
Read More
https://oemoh.co/7s69gr
THOMSON
When you have a job to get done, you can count on Gorman-Rupp. Our product line includes self-priming centrifugal, standard centrifugal, priming-assisted, submersible and diaphragm pumps used extensively for dewatering applications in quarries, streams, foundations, mining, coffer dams and sewage bypass operations. Simple pump designs with few moving parts minimize the need for repair or service. On most models, routine field maintenance can be completed with common hand tools. And, Gorman-Rupp pumps are proudly manufactured right here in the U.S.A.
GORMAN-RUPP PUMPS
P.O. BOX 1217 I MANSFIELD, OH 44901-1217 I USA I GRPUMPS.COM PH: 419-755-1011 I FX: 419-755-1251 I GRSALES@GORMANRUPP.COM
476 © 2022 The Gorman-Rupp Company Gorman-Rupp Pumps USA is an ISO 9001:2015 and an ISO 14001:2015 Registered Company