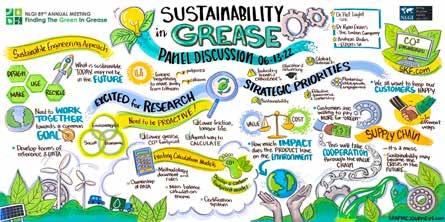
4 minute read
Sustainability Series
At the 2022 Annual Meeting, NLGI held a Sustainability Panel Discussion involving industry experts, Dr. Piet Lugt, SKF, Dr. Ryan Evans, The Timken Company and Andreas Dodos, Eldon’s. The discussion was moderated by Joe Kaperick, Afton Chemical Corporation. As NLGI continues to explore resources to help members with their sustainability efforts, please enjoy this “Sustainability Series” including additional insights on grease from cradle to grave. This sustainability series will run through the March/ April 2023 Spokesman issue.
Dr. Piet Lugt SKF
Dr. Ryan Evans
The Timken Company
Andreas Dodos
ELDON’s S.A.
If we think of the “footprint” in our industry as being the negative impacts of obtaining the raw materials and producing the grease and bearings, what are your thoughts about the positive impacts of these products and how we might quantify these?
The positive impact of lubricating grease is that it reduces friction and therefore helps in reducing energy consumption. The global bearing market is 140 million bearings . The total energy loss in these bearings is about 500 TWh/year. The equivalent of this is 66 million tons of oil equivalent (!) corresponding to about 1% of the total energy consumption (Bakolas, V.,Roedel, P., Oliver Koch and Pausch, M., A first approximation of the global energy consumption of ball bearings, Tribology Transactions, 2021). It is therefore significant to develop bearing solutions with reduced friction. By far most bearings are grease lubricated. Semi-dry friction typically gives a coefficient of friction of 0.6. By using (grease) lubrication this is reduced to say 0.04. one may argue that if there would be no lubricating greases the total energy consumption would be a factor 15 higher. So the word cannot do without lubrication. It is up to our community to reduce friction (performance of lubricants) and reduce the impact on the environment. - Piet Lugt; SKF Highly engineered bearings and greases improve machine efficiency and reduce friction throughout the lifetime of equipment – ultimately reducing the power loss experienced by their end users as compared to using lessengineered or standard bearings and greases for the same purposes. In addition, bearings that are optimized for durability and reliability can have longer service times in applications and require less maintenance and shorter replacement intervals. This can save the energy and materials required to produce replacement parts.
- Ryan Evans, The Timken Company
Do you think it is possible to ultimately come up with a single number that combines these “footprint” and “handprint” measurements?
It remains to be seen whether a single number can be agreed upon to illustrate the balance between carbon that is expended going into producing tribological components and lubricants and carbon use that is avoided in end-use equipment utilizing these technologies. We believe it is possible but will require many simplifying assumptions and agreements on definitions of inputs and outputs into that balance.
- Ryan Evans, The Timken Company
Are there other industry organizations that you are either working with or aware of that are doing work in the area of sustainability that you feel we should either model some aspect of within NLGI or that we could “piggyback” on to avoid duplication of effort?
Sustainability is high on the agenda of every company. SKF is working with Environdec (www.environdec.com) to create PCR (Product Category Rules = standardized LCA recipe) as well as EPD (Environmental Product Declarations = Type III / ISO 14025).. - Piet Lugt; SKF ELGI is launching a sustainability consortium. Individual companies are working create their own sustainability calculations at the request of their customers and stakeholders, usually within the context of a Corporate Social Responsibility (CSR) report. For example, The Timken Company published its Sustainable Engineering Process within its 2021 CSR (www.timken.com).
- Ryan Evans, The Timken Company
What specific actions do you think NLGI could or should take to help its member companies in relation to sustainability efforts?
• Create an agreed and standardized LCA recipe; a Product Category rule for greases • Work on Grease recyclability • Develop standardized test methods for bearing friction and degradability. • Provide a platform for joint research for - Reducing friction - Reducing the carbon footprint due to grease consumption - Zero Carbon cradle to cradle grease • Provide support/recommendation for non-hazardous greases (“white SDS”) - Piet Lugt; SKF NLGI should continue the sustainability dialogue and create networking opportunities to help companies, government agencies, and universities transparently share their progress on these topics and adopt best practices. NLGI should also encourage participation from all points in the value stream, from raw material suppliers to component manufacturers to equipment builders to end users. This may require engaging different functional area experts within organizations than typically associate with NLGI.
- Ryan Evans, The Timken Company
What is a “green grease”?
Green grease = 1) grease that has a very low friction = 2) grease that has a very low C02 footprint (cradle to cradle). = 3) grease without hazardous ingredients = 4) grease with as less as possible depletion of natural resources (eg. water,…) - Piet Lugt; SKF “Green grease” is a vague term. It may refer to a grease that was manufactured from renewable source materials. It may refer to a high-performance grease that has very high life and requires many fewer re-greasing maintenance intervals over the life of a bearing in an application. It may refer to a grease that is biodegradable, food safe, and non-toxic and thereby is easily and safely disintegrated at the end of its life as a lubricant.