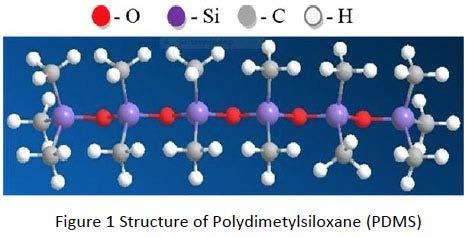
12 minute read
High Temperature Grease Utilizing New Silicone
High Temperature Grease
Utilizing New Silicone Based Fluids
Dr. Manfred Jungk and Aleksandra Nevskaya
Dow Corning GmbH
Introduction
Silicone, or as per IUPAC nomenclature Polysiloxane, represents a wide variety of polymeric chains and networks constructed around a backbone of Si-O-Si atoms. The Si-O bonds of silicones are >30% stronger than C-C bonds of hydrocarbons. The Si-O-Si angle is wider compared to C-C-C; this gives to the molecule great flexibility. The strength, length, and flexibility of silicone bonds impart many unique properties, including low melting temperature, fluidity, low glass transition temperature, and increased compactness. For the use as lubricating base fluid their exceptional oxidative stability and temperature-viscosity indices stand out. Their synthesis and manufacturing process is complex, starting from the reduction of Quartz with Carbon to yield elemental Silicon. Then using a fluid bed reaction process Silicon and Methylchloride form a mixture of Chlorosilanes with the majority being Dichlorodimethylsilane. Hydrolysis of distilled Chlorosilanes and subsequent polymerization result in Polysiloxanes.
The most common silicone structure is polydimethylsiloxane (see Figure 1) which is used in many applications including lubricants as well but has limited wear resistance. Polydimethylsiloxane based greases and compounds find use as O-ring and Valve lubricant, Damping grease, Plastic Gear lubricant or Brake Caliper grease. Phenyl groups on the silicone molecule provide additional thermal and oxidation resistance but do not improve lubricity. Polyphenylmethylsiloxane based greases are used in Metal-to-metal applications requiring high temperatures such as Clutch Release bearings or requiring slip prevention such as Overrunning Clutches. Trifluoropropyl substituted siloxanes exhibit reasonable wear protection and load carrying capacity, though their oxidation stability is not as good as that of the above mentioned Phenyl substituted materials. Typical applications of Polytrifluoropropylmethylsiloxanes
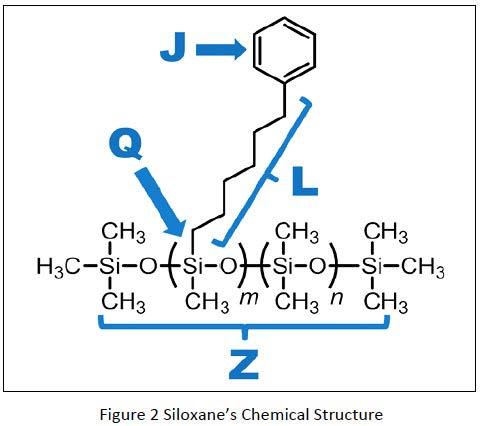
are for pumps, mixers or valves in the chemical industry and Circuit Breakers. This paper describes the development of a model to predict tribological properties of above mentioned as well as newly synthesized Silicones. Some examples of the new fluids will be compared with Hydrocarbon based fluids.
New Silicone structures
In order to characterize a Silicone where Methyl groups have been substituted we use a nomenclature as described in Figure 2, where J stands for the type of substitution, L for the length in Carbon atoms of an alkyl chain substitution, Q for the percentage of Silicon atoms of the Siloxane polymer chain where methyl groups have been substituted by J and Z the number of Silicon Atoms in the Siloxane polymer chain.
In addition the commonly used Polydimethylsiloxanes, Polyphenylmethylsiloxanes and Polytrifluoropropylmethylsiloxanes new Polycyclohexylmethylsiloxanes, Polyalkylmethylsiloxanes, and Polyphenylalkylmethylsiloxanes were synthesized either by Hydrosilation reaction with a respective Olefin or through Hydration of Phenyl substituted Silcones.
Table 1 lists the fluids that have been measured for the development of the model with its designated nomenclature to describe its molecular structure. Specific Volume and viscosity measurements were determined in the temperature range from 25 to 125 oC. Pressure viscosity indices were taken from high-pressure viscometric literature data and compared to calculated values from film thickness measurements. Generally spoken the literature data fit reasonably well into the range of calculated data at different
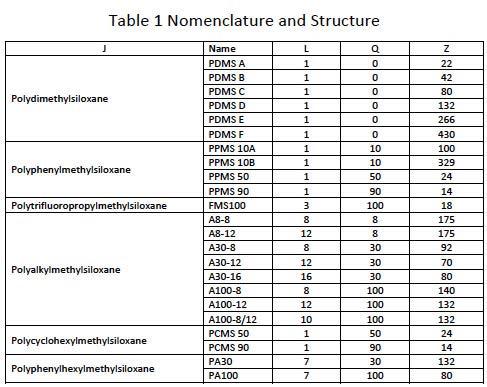
test temperatures. Elastohydrodynamic film thickness was measured at temperature range from 30 to 125 oC using a PCS thin-film tribometer at a maximum Hertzian pressure of 0.54 GPa, while speed was incrementally decreased from 4.35 to 0.020 m/s under nominally pure rolling conditions. Friction measurements were made at disk speeds from 5.00 to 0.025 m/s with the ball attached to a motor-driven shaft to vary the slide-to-roll ratio at a maxi-mum Hertzian pressure of 0.82 GPa. Boundary friction data were obtained using a ball (dia. 3/8”: Steel HRC~60 ) on disc (52100: Steel HRC~35) tribometer in fully flooded condition at 5kg Load, Disc Speed of 50mm/s with Entrainment Speed of 25mm/s for a total 1000 Revolutions.
Table 2 gives a snapshot of some of the experimental data for illustration purposes. Silicones are well-known for their temperature resistance and high Viscosity index. The data show that film formation capabilities of silicones are comparable with PAO and much more stable at higher temperatures. But boundary friction and wear values are higher compared to Polyalphaolefine (PAO) base oils. However, we have identified alkyfunctional silicone structures (A100-8, A100-12, A30-16, A100-8/12) showing low friction and good wear resistance. Two substances (A8-8 and PCMS 90) have high EHL friction values for potential use in traction fluid application.
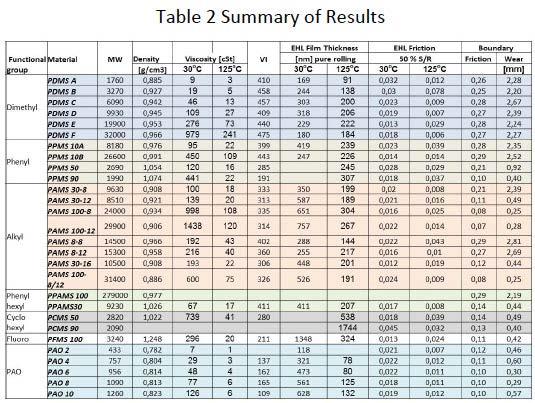
Model from Molecule to Friction
A model to predict the tribological performance of a silicone fluid from its chemical structure was recently developed in cooperation with Northwestern University. Figure 3 shows schematically the calculation method to start from individual atoms building a polymer molecule to derive at the rheological data of the polymers with its shear, temperature and pressure dependency.
Knowing the molecular structure from Nuclear Magnetic Resonance (NMR) spectroscopy and Gel Permeation Chromatography (GPC – giving the molecular length and its distribution by the polydisperity) the Molecular Weight Mw and Van der Waals Volume (using the Van der Waals Radii of each atom) νw can be easily calculated.
The Molecular Packing Factor (MPF) is the quotient of Specific Van der Waals Volume over measured Specific Volume v0. The Specific Volume at room temperature and atmospheric pressure ν0 can be calculated using Molecular Packing Factor. The viscosity (η0) can be calculated using the structure-viscosity equation of Berry and Fox which includes the parameters of Radius of Gyration and Monomeric Friction. The Tait Equation of State (v(T, P)) describes the pressure and temperature dependence of the Specific Volume and The Tait Doolittle equation (η (T, P)) which is used to calculate the temperature and pressure dependence of the Viscosity.
In the next step of the model we have identified the Total Friction Coefficient from Rheological parameters as calculated above. Total Friction is the sum asperity and film friction. The Hamrock Dowson equation is often used to calculate film thickness of elastohydrodynamic lubrication. But rather than going through the complex equation we will look qualitatively at the influencing parameters. When speed increases, film thickness increases. If contact loading increases, film thickness goes down. The contact load depends on the applied load. The materials tendency to expand when compressed hence the Poisson ratio and the materials elasticity hence the Young’s modulus. Rougher surfaces lead to lower film thickness, while the curvature of the non-conformal moving bodies impacts the contact load. The film thickness to composite surface roughness ratio determines if the load is carried by a mixture of asperity and fluid film (boundary and mixed lubrication) or totally by the fluid film (full film lubrication). Greenwood/Trip and Patir/Cheng used Greenwod/Williamson model along with simplifying assumptions based on engineering surfaces to calculate the contact pressure as a function of separation distance. The friction in unlubricated contact arises from metal to metal contact and was measured at μdry=0.3. Thus the asperity friction is derived by multiplying that value with the quotient of above calculated pressure over the pressure at zero film thickness. Fluid film friction is the quotient of mean shear stress over mean pressure. Mean pressure in the interface is computed by integration over the contact surface area while the shear stress distribution over the range of shear rates (depending on velocities) and viscosities is determined by a modified version of the Carreau model. The total friction is the addition of asperity friction and film friction at same loading.
On the right hand side of Figure 4 the graphical user interface for the algorithm to calculate the tribological data from a molecular structure of a Silicone is shown. The Molecular structure such as the species (J), branch length (L), branch content (Q), polymer length (Z) and the polydisperity need to be entered together with application conditions as temperature, speed, loading and slide-to-roll ratio. Interface geometry such as radius and surface finish of the 2 bodies as well as the Young’s modulus and the Poisson ratio can be varied to be consistent with a tribological contact in question.
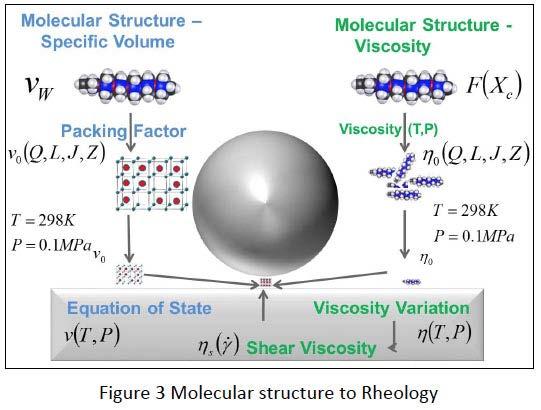
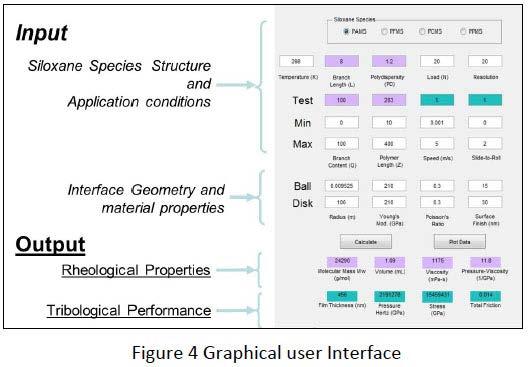
Comparison to Carbon based Fluids
Parallel to the development of the model larger quantities of Polyoctylmetylsiloxanes with varying branch percentage and molecular length were synthesized to evaluate their properties for use as lubricating base fluid in comparison to hydrocarbon based materials. Table 3 shows the Load carrying capacity as per SRV method, the Wear behavior according to 4-Ball test, oxidative stability according to the Oxidative Onset Temperature per Differential Scanning Calorimetric measurements in air, the viscosities and respective Viscosity Index. The data for the Polyoctylmetylsiloxane shows the minimum and maximum values of a series of more than 25 different fluids.
From the fluids shown for comparison the data for Polyalphaolefine (PAO 6), Polydimethylsiloxane (PDMS) and Fluorosilicone fit well in the range of those of the Octylmethyl fluids. The Perfluoropolyther’s data fit also in the range except their outstanding oxidative stability.
Another example of a newly synthesized Siloxane that was developed parallel to the model is a fluid for potential use as lubricant at high temperatures. Table 4 shows results from the new fluid compared to known Silicone and Hydrocarbon based fluids. While Fluorosilicones have reasonable 4-ball wear performance their high temperature capability is not as good as that of Phenyl Silicones as can be seen from the oxidative onset temperature of Differential Scanning Calorimetric measurements in air. The new Siloxane high temperature fluid exhibits overall good performance with respect to Viscosity Index, 4-Ball wear and Oxidative stability.
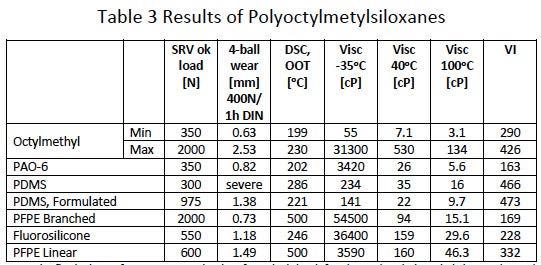
Greases formulated with the new new Siloxane show also 4-ball wear results comparable or better than other high temperature greases based on Perfluoropolyethers. Furthermore bearing tests using the FAG Fe9 Test show better performance at 220oC as compared to currently used high temperature greases.
Outlook
Besides the Polyoctymethyl- and the New High Temperature- Siloxanes developed in parallel, the model in form of the graphical user interface and its algorithm can be used to optimize the chemical structure for a specific tribological need. The plot of film thickness versus entrainment speed for Polyphenylmethylsiloxane (PPMS 90) and Polyalkylmethylsiloxane (A100-12) at different temperatures show that ring branches show nearly Newtonian behavior. High monomeric friction allows a relatively low molecular mass (Mw=1990 g/ mol for PPMS 90) to build viscosity, so shear thinning is low. For alkylfunctional fluids we see different behavior where low monomeric friction requires a relatively high molecular mass (Mw=29900 g/mol for A100-12) to build viscosity and shear thinning is high, thus linear branches may exhibit temporary shear-thinning. The plot of coefficient of friction versus film thickness at two different temperatures for cyclohexylmethylsiloxane PCMS 50, phenylmethylsiloxane PPMS 50 and standard polydimethylsiloxane PDMS shows that for PCMS the coefficient of friction does not change much by temperature. In case of PPMS and PDMS coefficient of friction drops down at higher temperatures. This means that Cyclohexyl siloxanes have greater thermal stability in the fluid film region. That indicates siloxanes are adaptable to diverse application, e.g. cycloalkysiloxanes as traction fluid or alkylsiloxanes as energy efficiency lubricants.
Besides tailoring siloxane fluids for specific tribological challenges as described above, the researcher could extend model to other types of chemical structures besides Silicones, explore the impact of mixtures and additives to the model or introduce functional groups (S, N, P) to the side groups.
References
1. Zolper, T.J., Li, Z., Chen, C., Jungk, M., Marks, T.J.,
Chung, Y.-W., Wang, Q.: Lubrication properties of poly-alpha-olefin and polysiloxane lubricants: molecular structure-tribology relationships. Tribol.
Lett. 48, 355–365 (2012) 2. Zolper, T.J., Li, Z., Jungk, M., Stammer, A.,
Stoegbauer, H.,Marks, T.J., Chung, Y.-W., Wang, Q.:
Traction characteristics of siloxanes with aryl and cyclohexyl branches. Tribol. Lett 49, 301–311 (2013) 3. Zolper, T.J., Seyam, A.M., Chen, C., Jungk, M.,
Stammer, A., Stoegbauer, H., Marks, T.J., Chung,
Y.-W., Wang, Q.: Energy efficient siloxane lubricants utilizing temporary shear-thinning. Tribol. Lett. 49, 525–538 (2013) 4. Zolper, T.J., Seyam, A.M., Chen C., Jungk, M.,
Stammer, A., Chung, Y.-W., Wang, Q.: Friction and
Wear Protection Performance of Synthetic Siloxane
Lubricants. Tribol. Lett. 51, 365–376 (2013) 5. Zolper, T.J., Jungk, M., Marks, T.J., Chung, Y.-W.,
Wang, Q.: Modeling polysiloxane volume and viscosity variations with molecular structure and thermodynamic state. Journal of Tribology 136(1), 011801/1-011801/12 (2014).
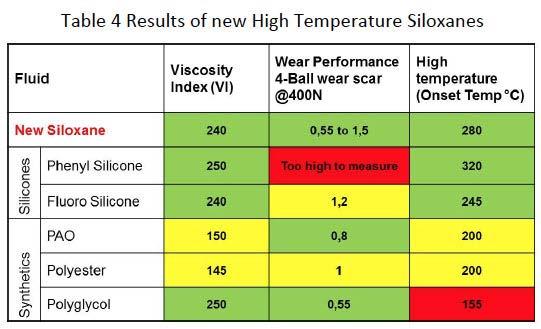
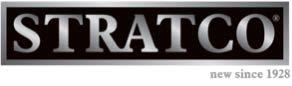
STRATCO HOSTS RIBBON CUTTING AT NEW WORLD HEADQUARTERS, WITH SCOTTSDALE MAYOR JIM LANE & INTERNATIONAL GUESTS
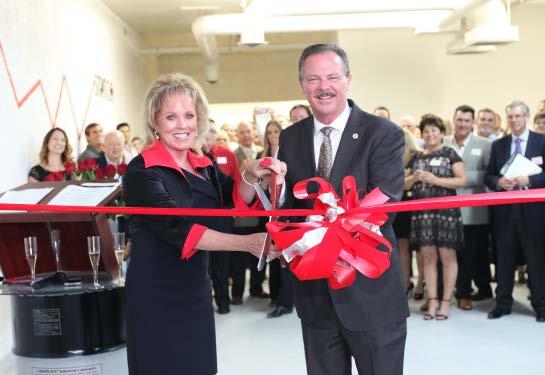
SCOTTSDALE, AZ -- STRATCO, Inc. celebrated its new world headquarters Open House with a special event that coincided with the Independent Lubricant Manufacturers Association (ILMA) Annual Meeting, Oct. 15-18, 2016. This event was highlighted by a ribbon cutting ceremony and champagne toast with Scottsdale Mayor, Jim Lane. The annual meeting is an international draw, and over 100 people attended the event at STRATCO in the Scottsdale Airpark district.
“As a supporter of ILMA and the National Lubricating Grease Institute (NLGI), I was thrilled to host this event and share our facility - including our new lab, featuring the Pilot Contactor™ Reactor - with other industry professionals,” said Diane Graham, STRATCO CEO. “We were happy to see our friends and colleagues enjoying themselves and our beautiful Arizona weather.”
STRATCO has been involved in NLGI since its inception in 1933, and the European Lubricating Grease Institute (ELGI) since its inception 25 years ago.
STRATCO’s new location provides a more functional space for its Pilot Plant that is used for Research & Development, as well as for laboratory services for Customers in the development of lubricating grease formulations and the investigating of new product lines. These new facilities will bring benefit to STRATCO’s Customers in the Lubricating Grease industry and other industries where reacting, mixing and blending technologies are needed.
Since 1928, STRATCO has been known for the supply of the highest quality equipment available, including the STRATCO® Contactor™ reactor and Skid Mounted Pilot Plants. STRATCO is now expanding and upgrading its Grease Kettle designs. STRATCO’s Customers are located in 63 countries on six continents.
Originally based in Kansas City, MO, STRATCO, Inc. is a privately-held firm headquartered in Scottsdale, AZ. The company provides engineering and equipment manufacturing solutions to customers worldwide in the lubricating grease, modified asphalt and petrochemical industries. STRATCO, Inc. is a member of the STRATCO GLOBAL family of companies, which includes ECOPATH™, formed in 2004 to provide technology solutions to the modified asphalt industries.
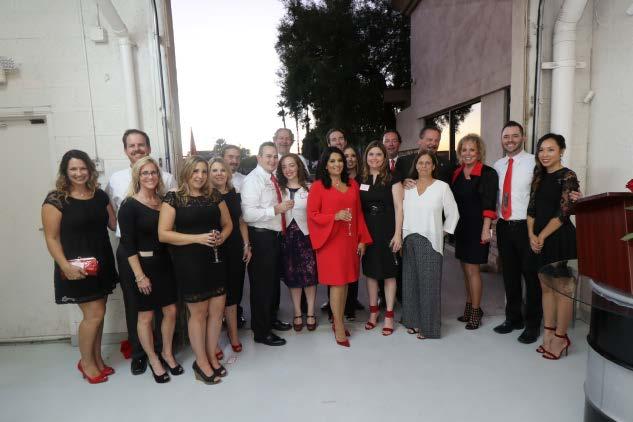
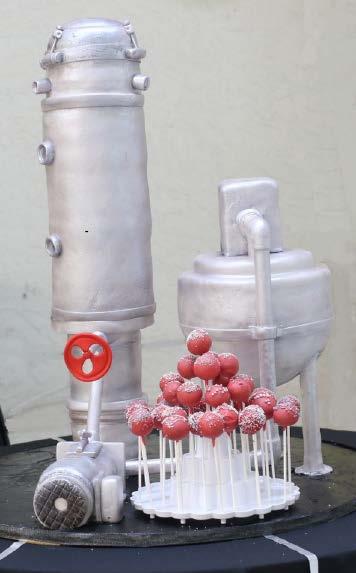
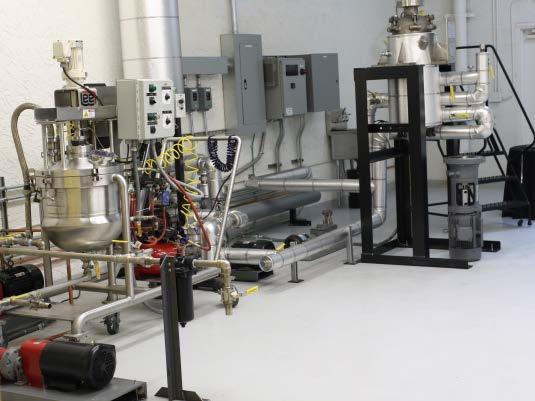