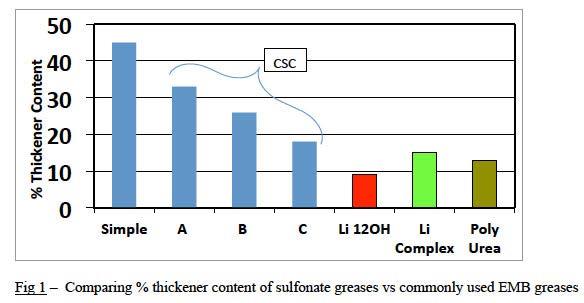
11 minute read
The Effect of Composition of a Calcium Sulfonate Complex Grease on the Key Parameters for Electric Motor Bearing Grease
Solongo Wilson Wayne Mackwood
Introduction
Calcium Sulfonate Complex (CSC) grease continues to grow in popularity as a premium grease for both end users and manufacturers. The 2014 NLGI Annual Survey has indicated that it accounts for almost 2% of the world grease production [1]. It is ideally suited to applications where heat, water, and high loads are present [4]. Several papers have shown that it can be used in a wide range of applications, from wheel bearings, food processing, nuclear power generation, steel mills, to marine equipment, and even wind turbines [2-13].
Simply put, an electric motor can be defined as a machine that converts electrical energy into mechanical energy. Electric motors can make up more than half of any plant’s rotating equipment. In mining, electricallydriven draglines and shovels use electric motors for powering all of the rotating equipment on board. These motors can be lubricated by oil or grease, depending on the orientation or application. In the case of greaselubricated motors, the predominant grease of choice is a polyurea-thickened grease, particularly for factoryfill bearings [14]. Lithium Complex grease and even simple Lithium grease may be recommended and used. Regardless of the type of thickener chosen, however, the primary functions of an EMB grease would be to reduce friction, prevent wear, protect bearings against corrosion, and act as a seal to prevent entry of contaminants. Therefore, key properties to consider when formulating would include high temperature life, operation at high speeds, wear protection, and corrosion resistance. Extreme pressure performance is not typically considered critical. A high percentage of electric motors operate at 3600 rpm, with a few operating at higher speeds of 5000 up to 20000 rpm.
With Calcium Sulfonate Complex grease becoming more popular in heavy industries, and finding increasing use throughout a plant, its consideration for use in EMB lubrication is a natural next step.
This paper will present a first look at several aspects of formulating a high performance CSC grease for electric motor bearings. In particular it will examine the effect of base oil type, base oil viscosity, and thickener content on the performance properties of the grease.
Background
An evaluation of several electric motor bearing manufacturers’ grease recommendations show that the most commonly suggested grease thickeners are polyurea, lithium, and lithium complex [15]. There is a distinct absence of calcium sulfonate complex grease in these recommendations. This study sought to assess the suitability of CSC grease in EMB applications, despite concerns about relatively high thickener contents when compared to other greases. In fact, the focus of the study was the manufacture of a new low-thickener content product aimed at fulfilling the requirements of an EMB grease. Fig 1 below shows the evolution of the calcium sulfonate grease technology from a simple thickener to processes with declining thickener contents. Manufacturers of CSC grease have the option to vary thickener contents from below 20% to over 30% [1618]. The process described in Patent 5,308,514 (Method C) results in thickener contents more in line with other thickener types [18].
Experimental
Ten (10) lab-made samples were generated in order to investigate the effect of method of manufacture, base oil group (I-V), base oil viscosity and effect of polymer. The majority of the samples was made via a new method aimed at reducing overall thickener content. Selected samples were duplicated using the standard method of manufacture in order to make a direct comparison with their lower-thickener counterparts. The samples were generally formulated to a final base oil viscosity of 40cSt – a lower viscosity than typical commercially-available EMB greases (approx. 100cSt) – in order to offset the slightly higher thickener content. Furthermore, a viscosity of 40cSt was more easily achieved for all groups of base oil than formulating to 100cSt. All samples were trimmed to an NLGI Grade 2, additized with a standard aminic anti-oxidant and were all manufactured using a 400 TBN semisynthetic sulfonate.
Testing included dropping point (ASTM D2266), roll stability (D1831), PDSC (D5483) as well as in-house hot plate and oven panel testing. Finally, the rheological behaviour of all samples compared to two commercially available EMB greases was evaluated.
RESULTS AND DISCUSSION
Table 1 – Summary of results
All CSC samples gave excellent dropping values of 315°C+, good wear scar values <0.6mm and roll stability change under 10%, with the majority lying under 5%. With the exception of one, all CSC samples gave an OIT greater than 100min in PDSC testing.
When all of the above values are compared to those of two commercially available products, there are clear differences observed in dropping points, roll stability, and PDSC. Particularly noteworthy is the poor mechanical stability of the polyurea sample as well as its relatively low OIT of 26.7min when compared to the CSC samples.
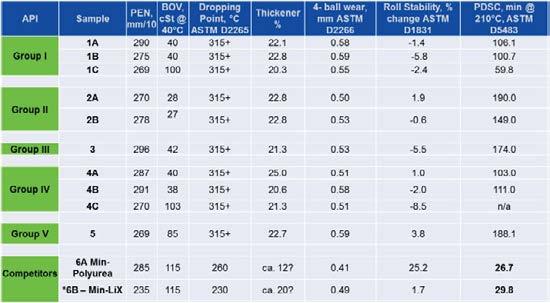
The mineral oil lithium complex sample, which was the only grade 3 sample in the series, also gave a relatively low OIT of 29.8min. These results indicate that the anti-oxidant used in these formulations is not suited to provide significant protection against oxidation at temperatures as high as 210°C. The CSC samples were all formulated with an aminic AO which is seen to provide sufficient anti-oxidancy.
Hot-Plate and Oven panel testing
These two tests served to characterize the high-temperature performance of the grease samples. In the in-house hotplate test, a pea-sized amount of each sample is subjected to a 440°C hot plate and observed for overall thermal stability. A poor-performing sample liquefies after a few seconds on the hot plate, whereas a thermally stable sample remains in solid form after several minutes on the hot plate. The results show a clear correlation to the dropping values as shown in Table 2 below.
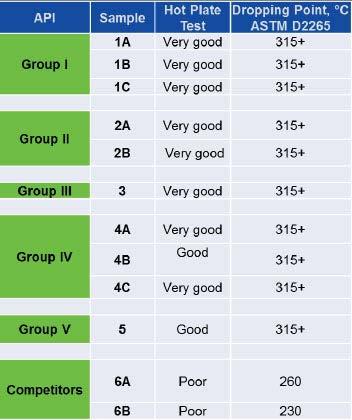
Table 2 – Correlation of hot-plate test performance to dropping point results
The oven panel test is a modified version of GM9075-P and involves coating a steel panel with a 30mil (0.8mm) film of grease and subjecting it to elevated temperatures (in this case 170°C) until the sample fails. Failure refers to excessive stiffening of the grease due to formation of oxidation products/resin. The panels were evaluated daily for change in colour, texture and presence of oil bleed.
The results showed a range in the number of days to failure, with the lowest number of days for the Group II samples. These samples had the overall lowest base oil viscosity of the series (ca. 28cSt) resulting in susceptibility to volatility. On the other hand, the best result was obtained from the mineral-LiX sample which was also the only Grade 3 sample present. Clearly, the amount of thickener – or conversely, the amount of oil – plays an important role in this test, since volatility is an important consideration. Further work on this study will include volatility testing (ASTM D972) Also apparent from the results was the significant colour change observed in the non-CSC based samples compared to the CSC samples. The former turned very dark brown/nearly black, whereas the latter darkened by a few shades compared to the original as seen by the fresh sample placed in the middle of the panels.
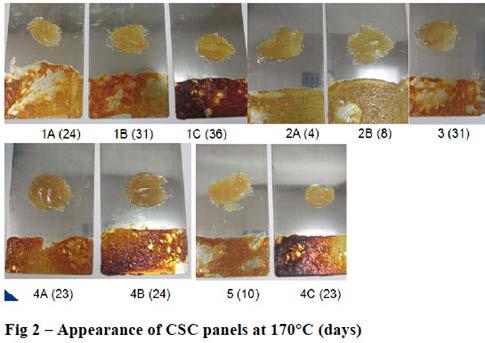
Rheometry
In order to characterize the visco-elastic properties of the samples, controlled-stress rheometry was performed at both low- and high temperatures using an Anton Paar Physica MCR 301 rheometer. In controlled-stress rheometry, a torque is imposed on one of the parallel plates (usually the upper) which sandwich a grease sample of known thickness. The resultant shear rate/ strain is measured allowing an analysis of the flow properties of the sample [22]. The instrument used in this study included software capable of generating such useful values as storage modulus (G’), loss modulus (G”), flow point, yield point etc. While it is true that in a parallel-plate set-up the shear rate varies from the centre of the plate outwards, the other commonly used geometry (cone-plate) also has its limitations. High rotational speeds can result in high centrifugal forces, resulting in grease being flung out. Since high temperature testing was an important consideration in this study, a parallel-plate geometry using 25mm sandblasted plates was chosen for all testing.
Rheometry Results
In order to compare the performance of the samples at various temperatures, the “flow point” value was recorded from all stress sweep runs [19]. The change (Δ) in this shear stress value (τ, measured in Pa) was represented as a factor of the sample’s value at 25°C. Larger delta values indicate a greater deviance (whether stiffer or softer) in the mechanical stability of the sample at lower or higher temperatures. Conversely, a relatively small change across a wide temperature range suggests that the sample is expected to perform well in the bearing at both decreased and elevated temperatures. For example, Fig 4 shows a factor of 19.6 when comparing the shear stress values of the 40cSt Group I sample at 25°C vs. at -25°C. Specifically, a shear stress of 6131Pa had to be applied to the -25°C sample in order to overcome the stiffening; this value is 19.6 times that of the 25°C shear stress value of 312Pa.
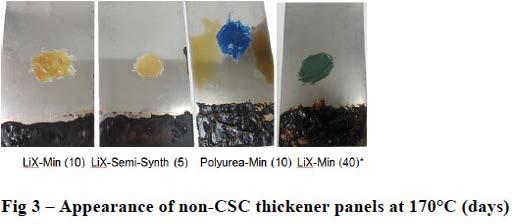
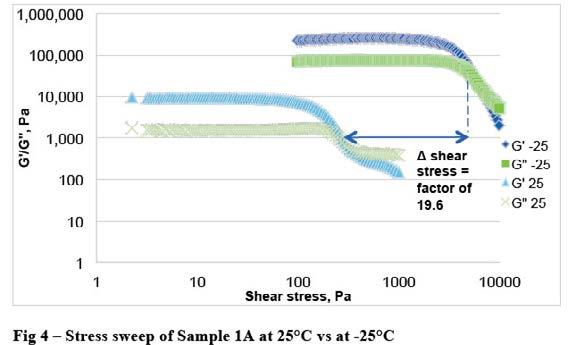
On the other hand, at an increased test temperature of 100°C, sample 1A was significantly softer, therefore a shear stress of 133Pa was sufficient to elicit the flow point, as shown in Fig 5, corresponding to a delta value of 2.3.
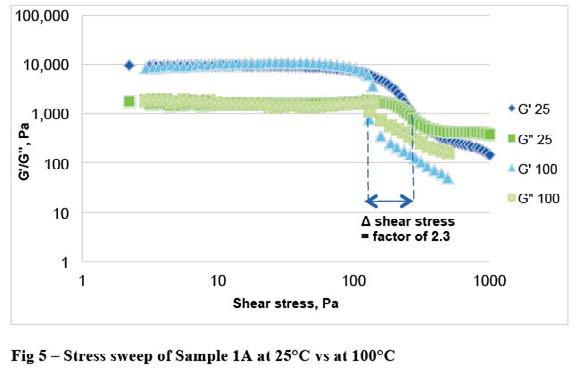
Table 3 – Summary of shear stress Δ values
High-temperature testing revealed that there is little differentiation among the samples. At 100°C, most samples gave a Δ shear stress value between 1 and 4, with the exception of the synthetic ester sample (5) which gave a value of 12.3. Likewise, at 195°C there is little spread among the values, with the 2 non-CSC thickener samples giving the highest values.
Greater differentiation was seen in low-temperature rheological testing. The Group I samples showed the poorest performance at -25°C, particularly sample 1B which contains 1% of a typical VI-improver type polymer. The lowest values were achieved using PAO. At an even lower temperature of -40°C, valid readings were only obtained for the Group III and IV samples. All others suffered from fracturing1 during the test measurement, leading to invalid readings.
The samples which showed the best performance across the entire temperature range were 4A and 4B, based on the standard and lower-thickener manufacturing methods, respectively. By decreasing the thickener content in sample 4A from 25% to a value of 20.6% in 4B, improvements were seen across the entire temperature range.
Conclusions
Using a method of manufacture which gives relatively low thickener content, a sample of calcium sulfonate complex grease based on PAO showed the best performance of all the samples generated. The sample gave good wear, excellent thermal and oxidative stability as well as good mechanical stability over a wide temperature range (-40°C up to 195°C). Such a sample would be suitable in a variety of electric motor bearing applications, particularly those that exist in harsher climates, e.g. mines in Canada. In order to further evaluate the performance of a proposed EMB calcium sulfonate complex grease, bearing life tests including ASTM D3336 and FE9 need to be performed. Compatibility of CSC with polyurea would also need to be carefully evaluated.
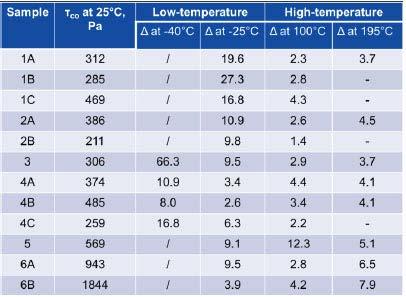
1 – At low temperatures, “fracturing” refers to the formation of two separate layers in the brittle grease sample in response to the high initial applied shear stress (i.e. high starting torque). There is no flow or interaction between the two layers, resulting in free spinning of the upper spindle.
References
1. 2013 NLGI Annual Survey, NLGI 2014. 2. Muir, R. “High Performance Calcium Sulfonate Complex Lubricating Grease” NLGI Preprint, 1987 Annual Meeting. 3. Kimura, Y., Takemura, J., Araki, J., Kojima, H., “Study of Synthetic Oil Based Calcium Sulfonate
Complex Grease”, Preprint, 2005 NLGI Annual Meeting. 4. Mackwood, W., Muir, R. “Calcium Sulfonate Grease… One Decade Later” NLGI Spokesman,
Volume 63, No. 5, 1999. 5. Mackwood, W., Muir, R., Brown, K., Austin, E. “Reduction in Power Plant Maintenance using
Calcium Sulfonate Complex Grease” Preprint, 2003 ELGI Annual General Meeting. 6. Samman, N., “High Temperature Greases” Preprint, 2006 NLGI Annual Meeting. 7. Schlobohm Sr., J., Faci, H., Cisler, B. “Steel Mill Greases: Evaluation and Analysis”, NLGI
Spokesman, Volume 69, No. 8, 2005. 8. Mackwood, W., Muir, R., Dunn, W. “Calcium Sulfonate Complex Grease. The Next Generation
Food Grade Grease.” NLGI Spokesman, Volume 17, 2003. 9. Mackwood, W. “The Next Generation Food Machinery Grease 10 Years On”, NLGI India
Conference, Ooty, India, February 3-5, 2011. 10. Schlobohm J. Sr., Faci, H. Cisler, B. “Steel Mill Greases: Evaluation and Analysis” NLGI
Spokesman, Volume 69, Number 8, pp. 8-13, November 2005. 11. Kumar, V., Nagar, S.C., George, TP., Sayanna, E., Mooken, R.T., Naithani, K.P., Malhotra, R.K.
“Specialty High Performance Grease for Multipurpose Applications”, Presented at the NLGI
India 2011 Conference, Ooty India, February 3-5, 2011. 12. Singh, T., Banerjee, S.K., Ravi, K. “Grease Compostion for Steel Plant Application”, Presented at the NLGI India 2011 Conference, Ooty India, February 3-5, 2011. 13. Mackwood, W. “Calcium Sulfonate Complex Grease. 25 Years Young.” Proceedings of the 2012
LTEF, Dalian China, 2012. 14. Underwood, “Grease-Lubricated Electric Motors – A New Perspective”, Machinery Lubrication (1/2008) 15. Christensen, P. “Lubrication of Rolling Bearings in Electric Machines”, EASA Tech Note No.19 16. Muir R.J., Blokhuis, W. “High Performance Calcium Borate Modified Overbased Calcium
Sulfonate Greases” U.S. Patent 4,560,489 (1985). 17. Olson, W.D., Muir, R.J., Eliades, T. “Sulfonate Grease Improvement” U.S. Patent 5,338,467 (1994) 18. Olson, W.D., Muir, R.J., Eliades, T., Steib, T. “Sulfonate Greases” U.S. Patent 5,308,514 (1994) 19. Lugt, “Grease Lubrication in Rolling Bearings” SKF; Wiley p.111 20. Delgado et al, “Thermorheological Behaviour of a Lithium Lubricating Grease” Tribology
Letters, Vol.23, No.1, July 2006 21. Salomonsson et al, “Oil/Thickener Interactions and Rheology of Lubricating Greases”, Tribology
Transactions, 50:302-309, 2007 22. Mezger, T. “The Rheology Handbook”, Vincentz-Verlag, Hannover, 2011