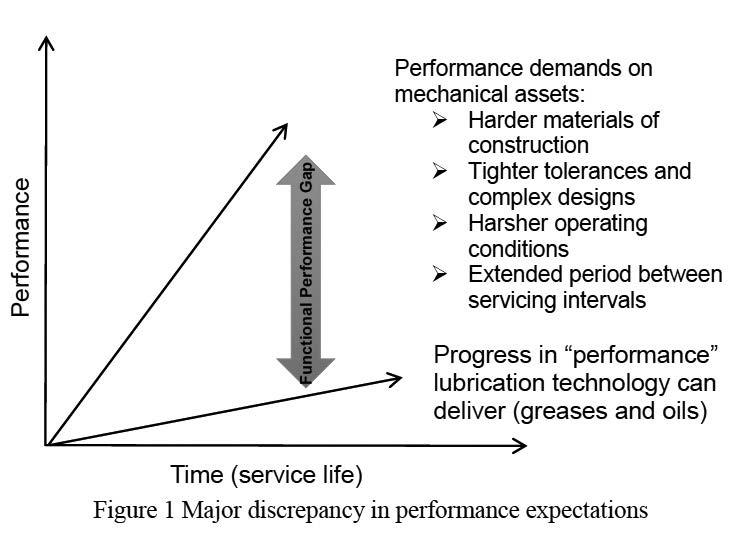
30 minute read
Super Additive Packages: The Next Generation of Lubrication Performance Enhancing Additives
SUPER-ADDITIVE PACKAGES:
Ajay P. Malshea*, Wenyang Zhanga, Melanie Murphya, and Greg Schwartzb a nGlide Division, NanoMech, Inc., 2447 Technology Way, Springdale, AR 72764 b NanoMech Energy, 100 Crescent Court, Suite 440, Dallas, TX 75201
*Contacting author- Email: ajay.malshe@nanomech.com; (Dr. Malshe is also a Distinguished Professor and Endowed Chair Professor of Mechanical Engineering at the University of Arkansas, Fayetteville, AR)
Abstract
Traditional additive packages address critical functions including anti-wear, anti-friction, extreme pressure, corrosion resistance, and related others for a wide selection of greases. The tight balance of additive chemistries, with interplay among their chemical compatibility as well as their synergistic response with the mating surfaces, is critical and typically fully exploited when building a well-balanced grease product. However, over the decades this tight balance has become even tighter as lubricant manufacturers are addressing exponential demands from manufactures of mechanical devices. Mechanical devices such as gear boxes, valves, ball bearings, pin joints, and others are experiencing severe demands for lubrication due to harder and harder materials of construction, tighter and tighter tolerances, extended lubricant changing interval cycles and drastic limitations on pricing for lubrication engineering. Among all the applications, the critical driving force for expanding this scope of traditional lubricants is boundary lubrication, where direct contact of multiple mechanical surfaces is driving the energy and durability equation.
Super-additive packages are the next generation of additives, capable of working with or without, and above and beyond the established traditional additive packages. These super-additive packages are engineered using fundamentals of material-genomics allowing one to dial-in and enhance the functional performance of selected properties, depending on the end application. This technical report is presenting a specific case study, especially for demonstrated performance of superadditives in fully formulated market available greases used for various large market sectors. An atlas of such super-additives to work alongside traditional additives is at the heart of this new platform to be used with a wide selection of off-the-shelf lubricant greases or customized specialty greases.
Introduction
Globally, as population and industrialization are growing, there is an exponential growth in the demand for energy use. The demand for energy is primarily driven by human activities in two types of systems—electrical systems and dynamic mechanical systems. Especially, growth in the population and industrialization, and growth in mechanical devices are almost moving in parallel. In the dynamic mechanical devices, the driving factors for energy losses are due to friction, material losses due to wear, the collective down time, and the cost of maintenance. These issues have become severe across various industry sectors. Another key observation is that many of these energy hungry mechanical components/systems are being rapidly designed and redesigned for better performance with tighter and tighter tolerances under harsher operating conditions, and for extended lubrication maintenance intervals.
These mechanical devices continue to face demanding (quantitatively and qualitatively) boundary lubrication conditions. Lubricating film, also called tribofilm, is the last line of defense under the boundary lubrication
[1]. These tribofilms results from thermodynamic metastable conditions due to transient loading and thermal conditions during asperity-to-asperity contact engaging various chemistries in lubricants. Especially, these complex lubrication chemistries and related functions are delivered using greases and oils as media containing state-of-the-art solid and/or liquid lubricants and functional additives (e.g. for anti-wear, anti-friction, extreme pressure, etc.)
Especially in most greases, manufacturers use multiple soap matrix or inorganic thickeners carrying oil and functional additives. Over the time, grease technology has super-matured and been customized to achieve intricate, tighter balance of chemistries and desired functions. Especially, the critical properties of greases for boundary lubrication are application specific for coefficient of friction, wear, load carrying capacity, oxidation/corrosion resistance, water resistance, thermal stability, and last but not the least, for wide operating temperatures and other environmental conditions. This customization of greases, over the years, tailored for specific application conditions have resulted in a range of products.
For example, one of the major and application specific users of grease lubricants is the gas and oil sector. Applications range from drilling to fracking, production to transportation, and refining to end-users across the hydrocarbon supply chain. Highly specialized steels and metal alloys such as Inconel, with micron to submicron tolerances and harsh operating conditions (from -70 °F to +700 °F), in on- and off-shore conditions and for the highest desired safety are becoming common to gas and oil components/systems. Many times it has been noted that on one mechanical system, such as a gate valve or a ball valve or others, more than one type of grease lubricant needs to be applied to meet those part specific custom conditions, occasionally resulting in manufacturing errors. At the same time, these products are being challenged as the gas and oil sector is adapting to harsher exploration conditions such as the oil sands project in Canada exposed to extreme abrasive and cold conditions, geothermal exploration in Iceland and Indonesia, and subsea exploration at thousands of feet below the sea level in various parts of the world.
At this time, for the energy gas and oil boom in the US and the world, there is a critical need for current grease lubrication technology to innovate and adapt rapidly to meet these growing aggressive new performance demands from various mechanical systems/ sectors and bridge the application specific functional gap (Figure 1). Innovation in additives is one of the most effective ways for desired innovation and adaptation to bridge this functional gap. In fact, the path of innovation in additive technology must address the Holy Grail of the lubrication industry which is to deliver multiple chemistries for multiple functionalities at the tip of every asperity in interacting surfaces. The observed size of these asperities, measured using high magnification microscopes, in boundary lubrication is typically submicron to nanoscale. So as to address these region specific functional demands, it is apparent that delivery of additives at submicron to nanoscale is imminent. This challenge also presents unique opportunities to discover nano and submicron scale science for understanding novel science, and applying those discoveries to deliver new set of engineering properties at those length scales using multi-component additive packages, and those which could work seamlessly with established current grease platform with state-of-the-art additives and fully formulated lubricants.
This nanoengineered multicomponent additive packages (NOT one element or one compound), and thus nanoengineered grease lubricants are the new class of advanced lubricant materials designed using principles of nanoscience and engineering such as macromolecular delivery, convergent assembly, multi-phase translation, and directed assembly. This timely progress proposes the next generation of opportunities, such as correcting friction at every asperity, the ability to enhance load carrying capacity by more than 100%, delivering oxidation resistance and corrosion resistance without adding additional corrosion inhibitors, super resistance to water washout at asperity level, and the last but not the least, the ability to seamlessly blend with fully formulated greases of various types with preexisting additives, solids and liquids. This next generation of advanced additive packages due to their following discussed superior functional abilities is called “superadditive” packages from this point onward [2-5]. This paper discusses these opportunities, specifically with a case study, for a gate valve used extensively globally in the gas and oil sector.
Engineering Problems
In this study, authors have identified a gate valve application for grease lubricant design, development and testing purposes. This application is one of the most severe applications in gas and oil sector. These valves experience direct metal-to-metal contact under high pressure, abrasive and corrosive fracking fluids, wide temp variation, etc. As shown in figure 2a, crosssection of a typical gate valve, and figure 2b, surface wear on a typical gate and a seat during operation, where needs to address such wear and related issues. This excessive sliding wear is caused by (1) high contact pressure (sometimes more than 10,000 psi) in reciprocating sliding motion between a gate and a seat which leads to difficulty of lubricant replenishment and failure of tribofilms, (2) fluids going through the valve removes lubricant applied on valves and hurts lubrication, (3) outside abrasive contaminants from fracking sands, muds, etc. causes excessive wear and (4) extreme temps, e.g. low temperature (-50 ˚F lowest) in northern region of US and Canada negatively affects flow properties of lubricant. An application specific design of nanoengineered superadditive package was developed for a traditional, fully formulated lubricant to address the above discussed chemo-mechanical problems (e.g. wear and extreme pressure protection, harsh operating condition, and low temperature). This specially designed lubricant solution was intended to deliver formation of a continuous robust tribofilm to avoid sliding wear, as well as survive in the severe operating conditions.
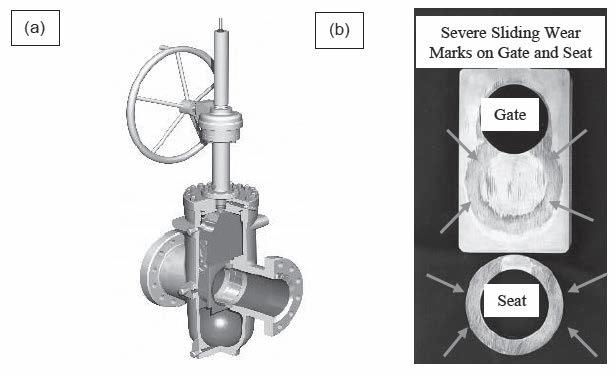
Figure 2: (a) Gate valve cross-sectional view [7]; (b) tested gate and seat of a gate valve which show clear sign of abrasive wear
Experimental Procedure
A fully formulated off the shelf grease with wellbalanced additive chemistry was selected as a benchmark, which is widely used extensively for gate valves in gas and oil sector, especially for arctic conditions. Application specific nanoengineered super-additive package was used to advance treat the benchmark grease formulation. This processing could be accomplished as a top-treatment as well as in the typical grease manufacturing process.
This new grease lubricant solution was tested to analyze tribological efficacy using industry standard analytical techniques such as four-ball wear, extreme pressure (EP), coefficient of friction, and grease penetration to study friction/wear reduction, load carrying capacity enhancement, and ability to maintain grease structure. A series of complementary grease qualification tests including copper corrosion, corrosion preventive, water spray-off, and reciprocating tribological testing, to simulate actual field boundary lubrication conditions, was performed for fully formulated benchmark grease and super-additive additized benchmark.
Scanning electron microscopy (SEM) and energy dispersive X-ray (EDS) techniques were used to analyze remaining protective layer after water spray-off test and tribo-chemical films formed in testing under boundary lubrication conditions. Following discussion presents details.
Material Selection
Benchmark Grease: fully formulated, commercially available mineral oil based bentonite thickened NGLI #1.5-2 grease (non-drop). This grease was selected for heavy duty gate valve applications especially due to harsh environmental conditions as well as for cost considerations for this open-loop mechanical system, where the grease is pumped in and out during fracking cycles. Product data sheet of fully formulated benchmark grease is shown in below table 1.
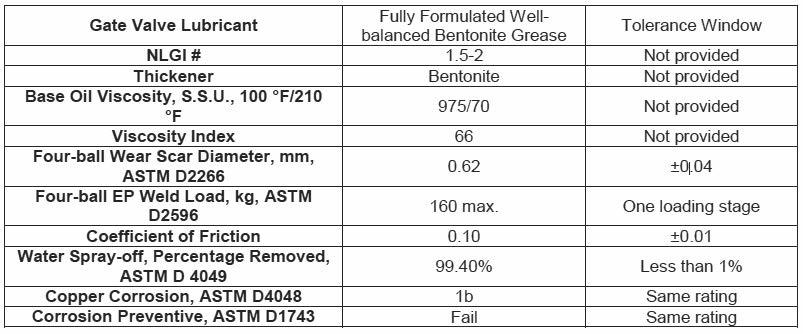
Super-additive Selection: In order to significantly enhance wear resistance, reduction in friction, and load carrying capacity provided by current benchmark grease, authors have selected traditional as well as super-additive multi-component chemistries for top-treatment (table 2), during the screening phase of this research. Following standard grease mixing procedures, a 6% treat rate was chosen due to the severe working conditions of the application.
Table 2: Selection of the State-of-the-art Additives and Nanoengineered Super-additive Systems for Top Treatment of Fully Formulated Benchmark Grease
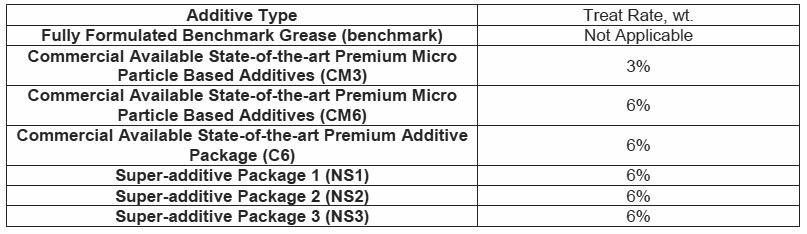
Testing Program
1. Screening Tests: screening tests were performed for all additive formulations along with benchmark to select best performing formulations for the following analysis and end user application.
Grease penetration (60 strokes worked penetration) was performed for all formulations using ASTM D217 Standard Test Methods for Cone Penetration of Lubricating Grease [8].
Wear performance was identified using ASTM D2266 Standard Test Method for Wear Preventive Characteristics of Lubricating Grease (Four-Ball Method) by measuring wear scar diameters. Coefficient of friction was also studied and recorded during ASTM D2266 test [9].
Load carrying capacity of tested lubricants was determined using ASTM D2596 Standard Test Method for Measurement of Extreme-Pressure Properties of Lubricating Grease (Four-Ball Method) [10].
2. Grease Qualification Tests: after screening tests, the best performance multi-component super-additive 1 (NS1) formulation was selected for grease qualification testing, simulated tribological testing, and surface morphological and chemical analysis.
As the end user application could include bronze parts, copper corrosion was studied using ASTM D4048 Standard Test Method for Detection of Copper Corrosion from Lubricating Grease [11].
Corrosion resistant property was evaluated using ASTM D1743 Standard Test Method for Determining Corrosion Preventive Properties of Lubricating Greases [12].
Water resistant properties, especially spray-off resistance, was analyzed using ASTM D4049 Standard Test Method for Determining the Resistance of Lubricating Grease to Water Spray [13]. 3. Application Specific Tribological Testing: application specific tribological testing was designed to simulate boundary lubrication conditions of gate valve.
As shown in table 3—section 1, in order to best simulate field conditions in the lab and study friction and wear response of nanoengineered super-additive, testing parameters were carefully chosen for contact mechanics, mating materials, surface finish, load, speed, temperature, and duration of test. Per section 2, similar tribological testing was carried out on steel coupons with grease after water spray-off testing. The purpose of this test is to study thin protecting layer left by multi-component superadditive after tribological testing. Bruker UMT-3 multifunctional tribometer equipped with a high temperature linear reciprocating module was used in this study as shown in figure 3.
Table 3: Tribological Testing Parameters Simulating Field Application Conditions
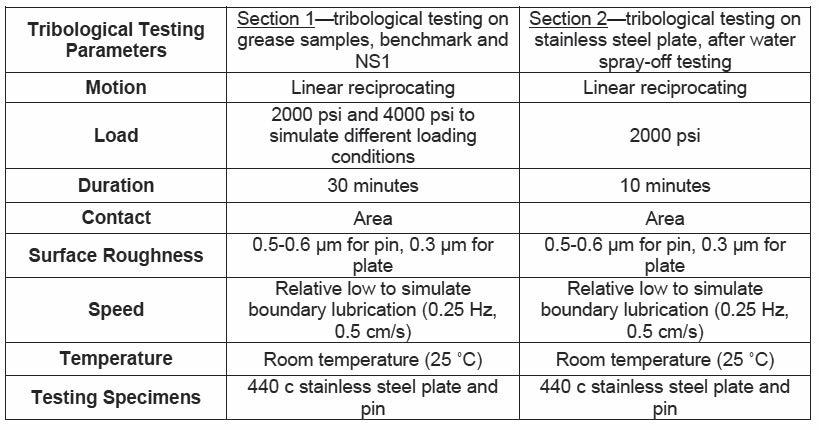
Figure 3: Multi-functional Tribometer with Linear Reciprocating Module
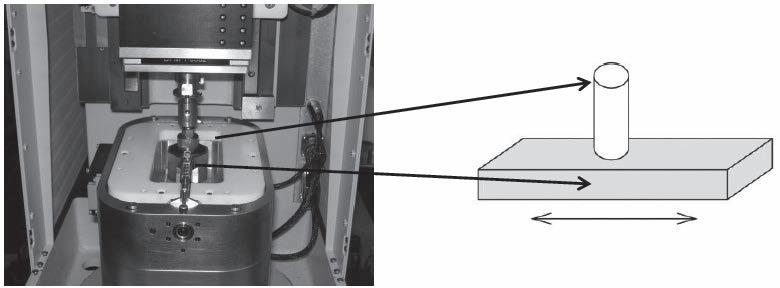
4. Morphological and Chemical Analysis: FEI XT Nova
Nanolab 200 focused ion beam/scanning electron microscopy (FIB/SEM) and built-in energy dispersive
X-ray spectroscopy (EDS) techniques were used for surface morphological and chemical analysis.
Surfaces of stainless steel plates after water sprayoff test were studied for benchmark and selected NS1 grease formulations using SEM and EDS to understand morphology and chemistry of the protective additive film. Wear tracks after tribological testing, using coupons after water spray-off testing, were also analyzed using SEM and EDS to study elemental composition and morphology of tribo-chemical films formed by lubricants. Stainless steel coupons were rinsed with heptane following standard cleaning procedure to remove excessive amount of lubricant left on the surface.
All tests were repeated at least 3 times to establish understanding of error range of each lubricant.
Results and Discussion
Part I. Screening Tests
To select best additive formulations, screening tests were performed. As shown in table 4, both CM3 and CM6 showed better friction, wear, and load carrying capacity performance than benchmark grease. Also, CM6 showed slightly better performance than CM3 with addition of 3% weight more in additive concentration. However, C6 commercially available and recommended additive package showed negative response in wear protection and grease consistency (softened benchmark grease to NLGI grade #1).
For nanoengineered super-additive lubricant packages, NS1 and NS2 showed very promising performance enhancement in every category. At the same time, the additized grease maintained grease consistency. Although NS3 showed superior performance in friction, wear, and EP (three loading stages over benchmark grease), it did change NLGI # below 1, unlike benchmark grease.
Table 4: Screening Testing Results of Various Selected Formulations in Comparison to Benchmark Grease (Note: data in parentheses is for tolerance window of reported testing results)
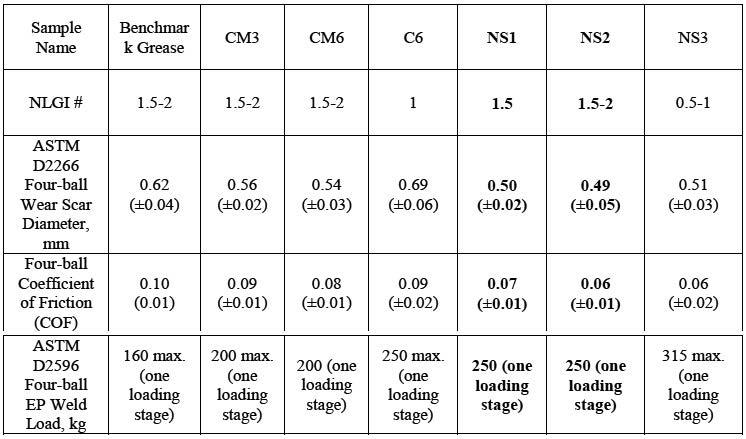
In a conclusion of screening tests, best performer NS1 and NS2 (highlighted in table 4) were selected for detailed grease qualification tests in the next step. C6 and NS3 were eliminated from contention due to negative performance response. Furthermore, CM3 and CM6 were eliminated because they did not show comparable results with NS1 and NS2 even under the same dosage rate.
Part II. Grease Qualification Tests
To further evaluate key properties such as corrosion and water resistance as required by the end user application, grease qualification tests were designed and carried out for benchmark grease and NS1 and NS2 super-additives additized benchmark formulations. As shown in table 5 (with tolerance window) compared with benchmark, NS1 formulated grease showed more than 20% reduction in wear, 30% reduction in friction, and 2 loading stages increase in weld load. More importantly, it is noteworthy that NS1 also enhanced corrosion and water resistant properties of benchmark grease without intentionally adding corrosion inhibitors and polymers for water resistance. Although there is only 2.6% improvement (table 5) in water spray-off removal of grease over the benchmark, a clear optical difference was observed between benchmark and NS1 formulated greases. As shown in figure 4b, no grease was left on the stainless steel plate for benchmark grease, but a thin layer of network of nanoengineered lubricant could be clearly seen on NS1 plate after water spray-off. This important observation was believed to be a result of well balanced and designed nanoengineered super-additive packages to form a network of surface protecting films among nano and sub-micron scale asperities, which could deliver a barrier for metallic parts from external corrosive and humid environment. Nanosized multi-component chemistries were demonstrated to form a surface protecting film and tribo-chemical films easier
than state-of-the-art lubricant additives along with better surface coverage as (1) nanosized chemistries can enter and bond with nano and submicron scale surface asperities; (2) nanoengineered additive packages deliver more surface area and metastable active material phases which contribute to better surface affinity and lucid film formation protecting almost every asperity; and (3) well designed multi-component macromolecular chemistries at nanoscale help efficient delivery and rapid activation of super-additive packages [1]. Morphological and chemical analysis of surface protecting film after water spray-off testing is discussed in Part IV of this paper.
Authors found out that NS2 additized grease formulation showed equally good tribological performance over benchmark and well-maintained corrosion and water resistant properties compared to benchmark. For non-technical reasons, NS1 formulation was recommended for the subsequent tribological testing, chemical analysis of tribo-chemical films, and field evaluation due to its superior tribological performance and corrosion/water resistance.
Table 5: Grease Qualification Testing Results of Benchmark Grease, NS1, and NS2 Chosen after Previous Screening Tests (Note: data in parentheses is for tolerance window of reported testing results)
Figure 4: Pictures of stainless steel plates (coated with benchmark grease and NS1 superadditive additized benchmark) before (4a) and after (4b) ASTM D4049 water spray-off testing
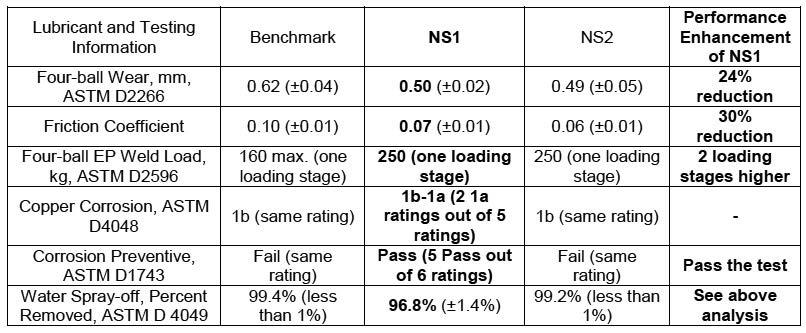
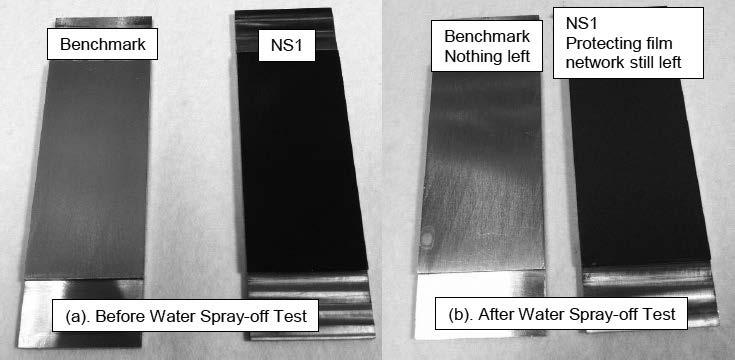
Part III. Application Specific Tribological Tests
Section 1—tribological testing on benchmark grease and NS1 additized benchmark grease
As shown in figure 5 and table 6, testing results obtained by simulating actual working conditions for gate valve for gate-ring contact, NS1 showed significant amount of wear reduction and weight loss (wear) reduction (up to 69% reduction) compared with benchmark grease, especially under higher loading condition of 4000 psi. Significant amount of sliding wear was observed for benchmark grease with deep scratches believed to be due to inability to withstand high-pressure boundary lubrication conditions and inability of traditional grease formulation to penetrate wear interface under severe contact. Very light wear marks were observed for NS1 additized benchmark grease. Moreover, 17% friction reduction was found for NS1 compared to benchmark grease at 2000 psi. This observation is also consistent with four-ball testing results.
Figure 5: Stainless Steel Testing Coupon with Circled Wear Marks after 2000 psi (5a) and 4000 psi (5b) Reciprocating Tribological Testing (see Table 3 for testing parameter details)
Table 6: Friction and Wear Results of Benchmark Grease and NS1 Additized Benchmark Grease under Simulated Boundary Lubrication Conditions for Gate Valve Gate-seat Contact
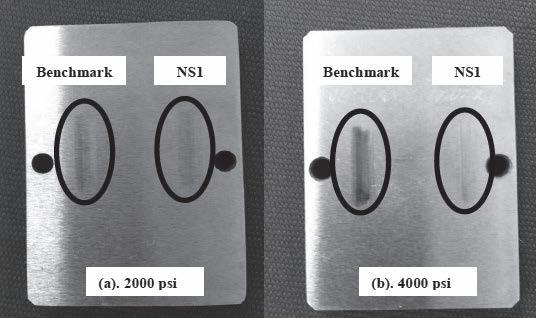
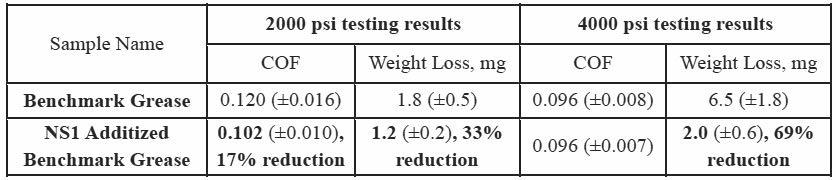
Section 2—tribological testing on stainless steel plate after water spray-off testing (testing is based on grease left on the plate)
As shown in figure 6 and table 7, NS1 formulated benchmark grease showed significant amount of reduction in friction and reduction in wear (e.g. weight loss reduction up to 70%) compared with benchmark grease. The intent of this was to study tribological performance of surface protecting film left on stainless steel coupon after water spray-off tests and special single coupon was prepared with leftover films after water spray-off from benchmark and NS1 treated benchmark greases. This test was carried out under boundary lubrication conditions for load of 2000 psi and predefined time duration of 10 minutes (see Figure 3 for testing parameter details). Significant amount of sliding wear was observed for benchmark grease with deep scratches due to inability to withstand high pressure boundary lubrication condition. Very light wear marks were observed for NS1 additized benchmark grease. This observation confirmed the advanced anti-wear (AW) / anti-friction (AF) / extreme pressure (EP) functionality of surface protecting films formed by nanoengineered lubricants. Under harsh operating conditions, the benchmark grease with state-of-the-art additive package failed to protect the surface, but the same grease treated with nanoengineered super-additives is able to form a surface protecting film to continue to provide these advanced functionalities. Surface morphological and chemical analysis of tribo-chemical films formed after reciprocating tribological testing are discussed in Part IV of this paper.
Figure 6: Stainless Steel Testing Coupon with Circled Wear Marks after 2000 psi Reciprocating Tribological Testing on Specimens after Water Spray-off Testing
Table 7: Friction and Wear Results of Benchmark Grease and NS1 under Simulated Boundary Lubrication Conditions after Water Spray-off Testing
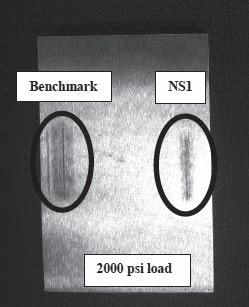
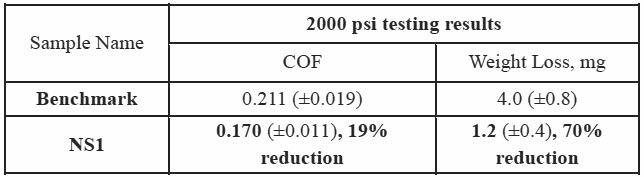
Surface morphological and chemical (elemental) evaluation was performed by SEM and EDS techniques to better understand the mechanism of superior performance provided by NS1. Two studies are presented in this section: (1) study of stainless steel plate coated with benchmark grease and NS1 additized benchmark grease after water spray-off testing. As shown in figure 7 and 8—the purpose of this study was to physically and chemically identify surface protecting film formed by benchmark grease, if any left after water-spray off, and NS1 additized benchmark grease; (2) study of tribochemical films on wear tracks for benchmark and NS1 additized greases, after water spray-off testing followed by tested reciprocating tribometer under boundary lubrication regime, as shown in figure 9 and 10—the purpose of this study is to understand delivery of functional nanoengineered multicomponent additive chemistries using NS1 additized benchmark grease and the mechanism for measured better tribological performance.
I. Chemical and morphological microscopic study of stainless steel plate coated with benchmark grease and NS1 additized benchmark grease after water spray-off testing
As shown in figure 7 (a) and (b) SEM micrographs, after water spray off testing, there is no benchmark grease left on the stainless steel coupon except several bentonite particles left on the plate as identified by Al and Si elements as shown in figure 7 (c), elemental mapping EDS results. Surface profile of steel substrate could be clearly seen since there is no protective film formed by benchmark grease. Very little or close to no amount of Al and Si elements were found as shown in figure 7 (d) and (e), EDS spectra and atomic ratio, which is consistent with SEM observation.
From figure 8 (a) and (b) SEM micrographs, clear lubricant coating/distribution was found on stainless steel coupon and texture of substrate (steel surface) could not be observed which also verified that a thin layer of surface protecting film was formed among surface asperities (texture) after water spray-off. Other evidence is that the atomic ratio of Fe element is extremely low as shown in figure 8 (e) which means the steel surface is well covered by a film so that electrons could not penetrate or escape from substrate for SEM analysis. In figure 8 (c) and (d), signatures of tribo active elements such as Mo, S, and N were found well dispersed in film/ lubricant substrate. Mo and S atomic ratio is closely maintained at 1:2 which partly shows there is no chemical reaction between NS1 and grease structure after water spray-off testing. Interestingly to note that Al and Si elemental concentration from bentonite is also significantly higher than benchmark grease studied in figure 7. It is believed that well dispersed nanoengineered super-additive strengthened the network structure of benchmark bentonite grease avoiding complete washout and at the same time, the strong surface affinity of nanoengineered super-additive chemistries bond and strengthened surface film on steel substrate. This dispersion strengthening effect is under further study to understand the bonding between nanoengineered additives and grease network structure for physical or chemical or hybrid bonding. Above microscopic observations well reconfirm macroscopic findings of water spray-off test with and without nanoengineered additive packages discussed and as shown in figure 4.
II. Chemical and morphological microscopic study of tribo-chemical films on wear tracks for benchmark and NS1 additized greases, after water spray-off testing followed by tested reciprocating tribometer under boundary lubrication regime
Wear tracks of benchmark grease after reciprocating tribological testing under boundary lubrication were studied for microscopic morphological and chemical analysis (figure 9). Significant amount of wear debris, sharp edges, and rough surfaces of wear tracks were observed in figure 9 (a) and (b) which are consistent with worse tribological performance observed during prior testing. More importantly, based on elemental analysis in EDS, wear tracks are dominated by Fe element and no tribo-chemical film (protective films) traces were found. This observation reflects that under harsh operating boundary lubrication gate valve condition, benchmark grease could not form tribo-chemical film to protect the surfaces. Due to no protective film formation, steel debris formed by direct metal-to-metal contact resulting: (1) in scratched surface to create more steel debris; (2) in asperity to asperity welding with surface under high
pressure and peeled off later to create more wear; (3) in welding among steel debris and asperities under high pressure to form larger and harder steel debris because of strain hardening which could significantly damage the surfaces. This explains wear mechanism and inability of surface protection of benchmark grease.
In a clear comparison to results in figure 9, in figure 10 (a) and (b), wear tracks of NS1 additized grease under the same tribological testing conditions showed much smoother wear tracks protected by continuous tribo-chemical film without steel debris. Tribo active elements Mo, S, and N were predominantly observed and found well dispersed in tribo-chemical films as shown in figure 10 (c) EDS elemental mapping results. In addition, multicomponent additive functional packets were either absorbed or embedded into tribofilms, ready to deliver for tribofilm replenishment and deliver their multi-functionalities for AW, AF, EP and anti-corrosion [1]. Interestingly, from the EDS quantification results in figure 10 (e), atomic ratio of Mo and S is found to be less than 1:2. This finding demonstrates chemical reaction under severe lubrication condition. It was believed that nanoengineered additive packages reacted with steel substrate to form multi-layer friction-polymer based tribo-chemical films to provide surface protection [1, 6]. Current finding clearly explained the superior performance of NS1 additized benchmark grease during tribological testing and its capability to continuously provide lubrication under harsh environmental conditions, such as after water spray-off testing and in an open loop mechanical system like a gate valve. Further Raman and XPS analyses are in progress to obtain the in-depth understanding of chemical compositions of tribo-chemical films.
Figure 7: (a). SEM image at 350x magnification of stainless steel plate coated with benchmark grease after water spray-off testing; (b). SEM image at 2000x magnification; (c). Elemental mapping results of EDS identified elements for studied surface at 350x SEM image; (d). EDS spectra of studied surface at 350x SEM image; (e). EDS elemental ratio calculated from above EDS spectra
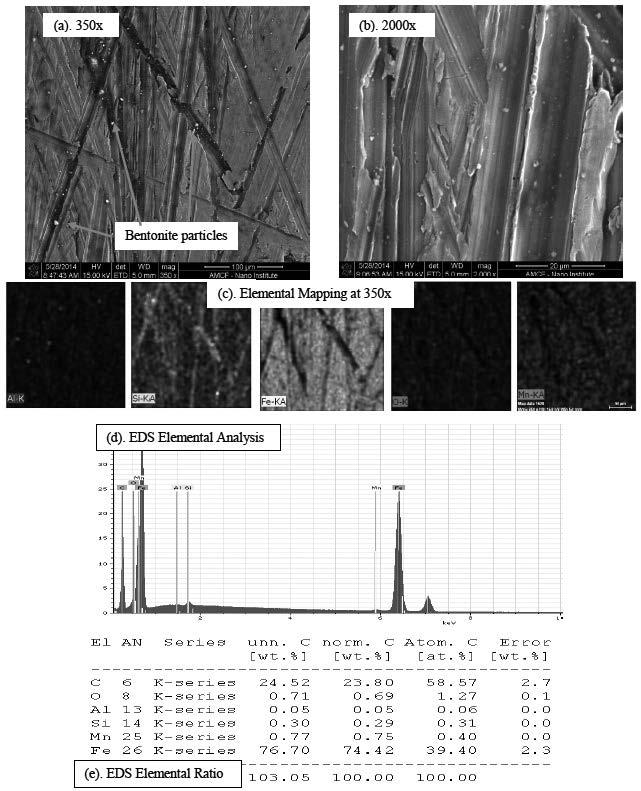
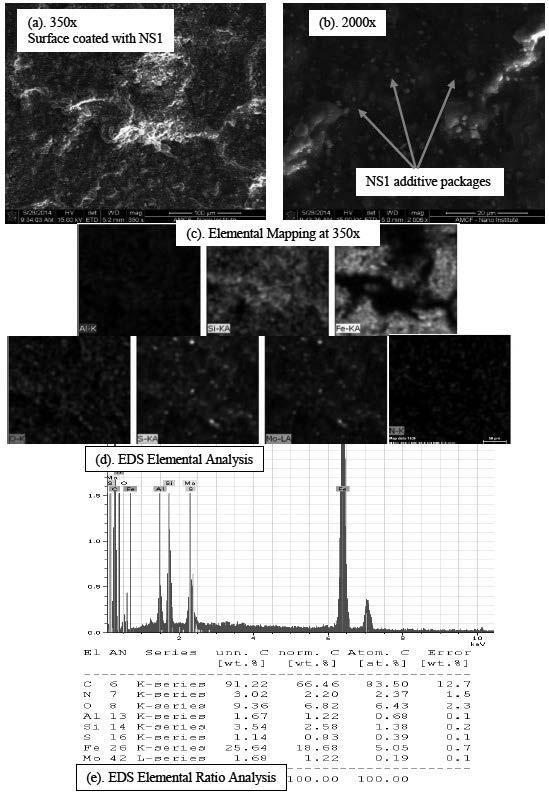
Figure 8: (a). SEM image at 350x magnification of stainless steel plate coated with NS1 additized benchmark grease after water spray-off testing; (b). SEM image at 2000x magnification; (c). Elemental mapping results of EDS identified elements for studied surface at 350x SEM image; (d). EDS spectra of studied surface at 350x SEM image; (e). EDS elemental ratio calculated from above EDS spectra
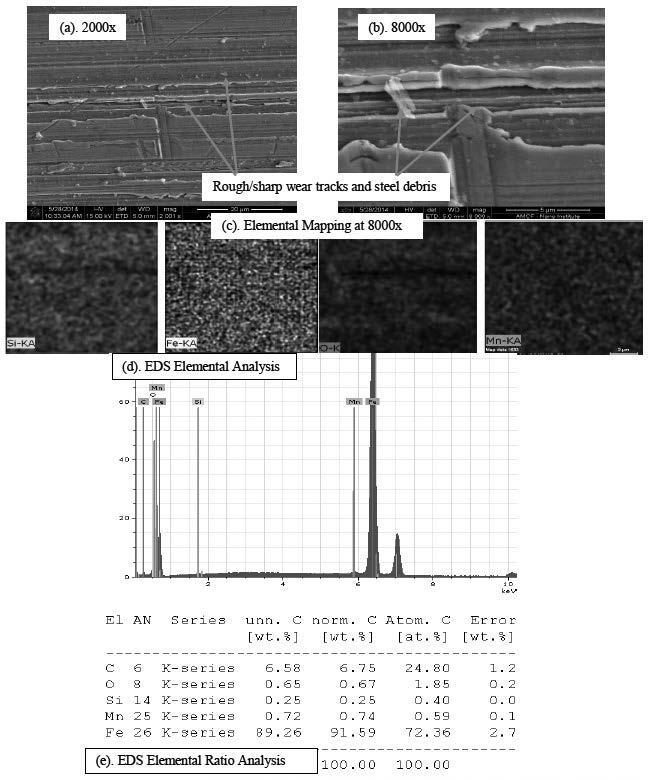
Figure 9: (a). SEM image at 2000x magnification of wear tracks of benchmark grease located at steel coupon (after water spray-off testing) tested by reciprocating tribometer under boundary lubrication; (b). SEM image at 8000x magnification; (c). Elemental mapping results of EDS identified elements for studied surface at 8000x SEM image; (d). EDS spectra of studied surface at 8000x SEM image; (e). EDS elemental ratio calculated from above EDS spectra
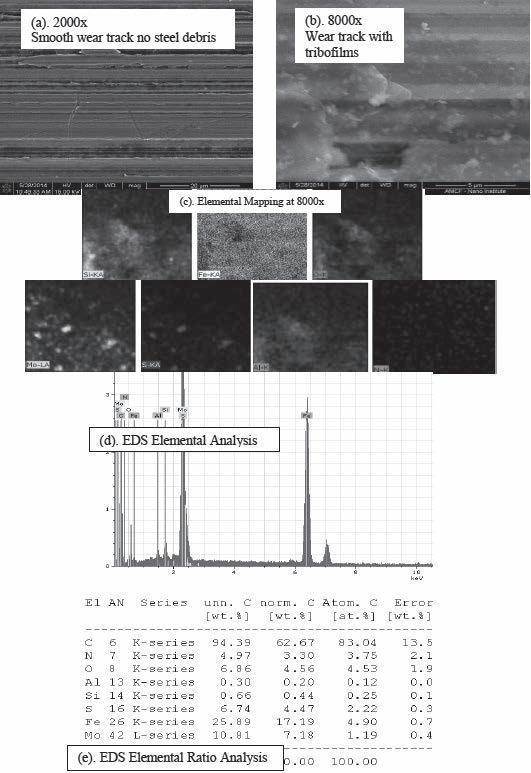
Figure 10: (a). SEM image at 2000x magnification of wear tracks with tribo-chemical films of NS1 additized grease located at steel coupon (after water spray-off testing) tested by reciprocating tribometer under boundary lubrication; (b). SEM image at 8000x magnification; (c). Elemental mapping results of EDS identified elements for studied surface at 8000x SEM image; (d). EDS spectra of studied surface at 8000x SEM image; (e). EDS elemental ratio calculated from above EDS spectra
Part V. Evaluation Benchmark and NS1 Additized Benchmark Grease for Gate Valves (Assembled for Frac-Tree) Under Fracking Conditions
NS1 additized benchmark grease was recommended for field-testing evaluation after showing excellent lab performance in various perspectives. Benchmark grease was also evaluated for base line control purpose. As shown in figure 11, gate valves filled with benchmark grease and NS1 additized benchmark grease were assembled in two separate frac-trees and tested at the same fracking sites under arctic conditions illustrated in table 8. All field testing work was controlled by the end user by well-established standard operating procedures. After the end user specified fracking cycles at the site were completed, both frac-trees were shipped back to the factory for disassembly, cleaning, and further part inspection/evaluation following standard operating procedures.
After inspection, for both test valves filled with benchmark grease and NS1 additized benchmark grease (figure 12 and 13): • NS1 additized grease applied parts gave considerable less surface damage (e.g. scratches, pittings, etc.) on hard gates and seats; • Density of scratches for NS1 additized grease applied parts was much less; • Severity of scratches, surface roughness Ra value was an order of magnitude less for NS1 additized grease lubricated valves; • Resistance to water washout was enhanced by NS1 additized grease. Gates and seats after disassembly still showed a thin layer of NS1 additized benchmark grease, which is consistent with previous lab results; • Gates and seats of benchmark grease could not be reused while gates and seats tested with NS1 can still be used again.
In summary, nanoengineered super-additive package, NS1 additized grease in field testing provide up to 90% reduction in wear volume and surface roughness reduction. Cumulative effect of the above functional advancements is that the life of parts in gate valve was extended by 25-50%, based upon field observation. (Disclaimer- data could partly vary from site-to-site and for operator pattern.)
Figure 11: Testing Frac Tree composed of 7-8 gate valves filled with benchmark grease or NS1 additized benchmark grease; Table 8 Field testing specifications to make sure benchmark grease and NS1 additized grease under the same testing conditions
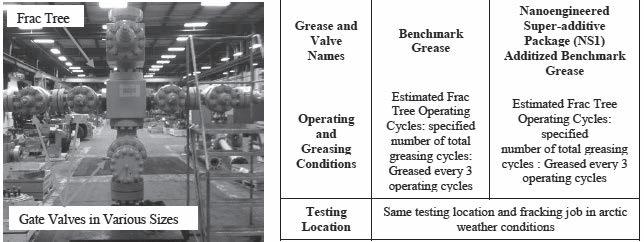
Figure 12: Gate surfaces of gate valves tested with benchmark grease (left picture with much higher Ra values and wear) and NS1 additized benchmark grease (right picture with much lower Ra value).
Figure 13: Seats surfaces of gate valves tested with benchmark grease (left two seats with deep scratches) and NS1 additized benchmark grease (right two seats with almost no wear).
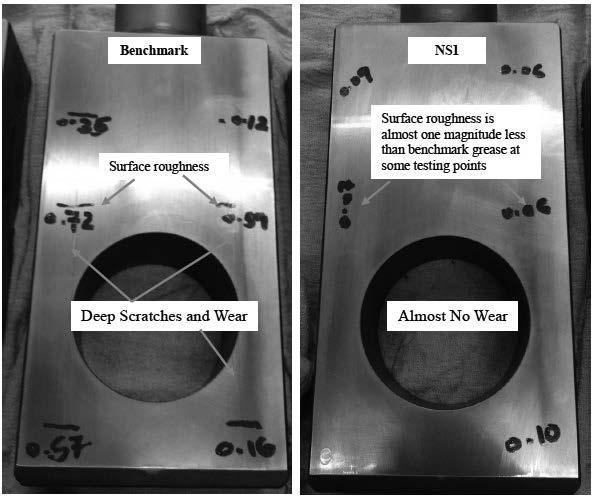
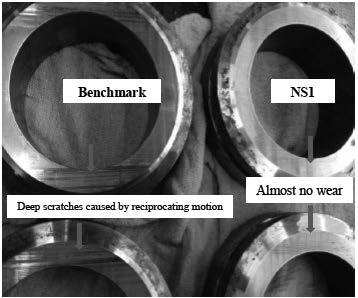
Conclusions and Future Directions
In summary, nanoengineered super-additive package additized benchmark bentonite clay grease provided advanced performance not only over fully formulated well-balanced benchmark bentonite clay grease, but showed the following results as well:
• Nanoengineered super-additive package 1 (NS1) showed 30% reduction in friction, 20% reduction in wear, and 2 EP loading stages higher in comparison to benchmark grease.
In another noteworthy finding, NS1 provided better corrosion (without intentionally adding corrosion inhibitors) and water resistant properties. Although better water resistance is not clearly reflected by numbers of traditional
ASTM 4049 testing results, consistent network of protecting film was found on stainless steel plate which was formed by nanoengineered super-additive package based on evidence from morphological and chemical analysis using SEM and EDS techniques. This surface protecting film network formed by nanoengineered superadditive packages is believed to be the last line of defense in field application to effectively protect machine surfaces. • Meanwhile, NS1 showed even better performance in friction and wear reduction, up to 70% reduction in weight loss, under application specific tribological testing to simulate actual boundary lubrication condition.
Smoother wear track and evidence of tribo active elements in wear tracks successfully demonstrated nanoengineered super-additive packages are delivered to mating surfaces to form protective tribo-chemical films even under harsh boundary lubrication conditions. Unlike benchmark grease, it showed no evidence of physical and chemical delivery of functional additives. • Cumulative effect of functional advancements in AW, AF, EP, anti-corrosion, water spray-off resistance for nanoengineered super-additive packages was demonstrated by field testing to provide up to 90% reduction in wear volume and surface roughness. • Further chemical composition analysis by
Raman and XPS techniques and surface profile analysis by 3D surface profilometer of tribochemical films formed by nanoengineered super-additive packages, low temperature performance (low temperature penetration and torque) of additized grease, and hydrocarbon resistance of studied lubricants are necessary and are in progress, and will be presented at suitable time.
Finally, this technical report has presented patented and patents’ pending breakthrough developments in a new class of lubricant additive packages (unlike nanoparticle component such as friction modifier elements and compounds like carbon, MoS2, WS2, borates, copper, etc.), designed and developed using principles of nanoscience and engineering such as macromolecular delivery, convergent assembly, multi-phase translation, and directed assembly. A new atlas of such multicomponent super-additives is being integrated for various greases based on Li, LiX, calcium sulphonate, bentonite, PFPE, silicone and other base chemistries. This new advancement progresses current scientific and technical understanding and works in complementary and synergistic nature to already established greases and their additive systems to meet the demands of advanced mechanical systems discussed in section on Introduction.
Acknowledgements
Special acknowledgements to Cameron International Corporation staff for collaboration. Special thanks to John Bartos, Jim Lovin, Joe Gross, Vasanth Annamalai, Loc Hoang, Muneeb Dogar and all other related Cameron associates for all collaboration work and field testing support. Authors would also like to acknowledge Arkansas Analytical Facility (AAF) and Electron Optics Facility (EOF) for the use of SEM and EDS equipment and Dr. Mourad Benamara for related technical discussions.
References
1. Zhang, W.Y., Jahan, M.P., and Malshe, A.P., 2012,
Chemical Understanding of Friction Polymer Based
Tribo-chemical Films Derived from Nanolubricant,
ASTM Proceedings/Nanotribology, Paper No.
IJTC2012-61119, pp. 13-15. 2. Malshe, A. and Verma, A., Nanoparticles
Compositions and Methods for Making and Using the Same, Application Serial No. 12/160,758; US
Patent and Trademark Office; Filing Date: September 2, 2008. U.S. Patent No. 8,492,319 B1 (issued July 23, 2013) Multiple national and international allowed and pending applications. 3. Malshe, A., multiple national and international allowed and pending patent applications. 4. Zhang, W.Y., Demydov, D., Jahan, M.P., Mistry, K.,
Erdemir, A., and Malshe, A.P., 2012, Fundamental
Understanding of the Tribological and Thermal
Behavior of Ag-MoS2 Nanoparticle-based Multicomponent Lubricating System, Wear, 288, pp. 9-16. 5. Verma, A., Jiang, W.P., Abu Safe, H.H., Brown, W.D., and Malshe, A.P., 2008, Tribological Behavior of
Deagglomerated Active Inorganic Nanoparticles for
Advanced Lubrication, Tribology Transactions, 51(5), pp. 673-678. 6. Hsu, S.M. and Gates, R.S., 2005, Boundary
Lubricating Films: Formation and Lubrication
Mechanism, Tribology International, 38(3), pp. 305312. 7. www.c-a-m.com 8. ASTM D217 – 10 (2010) Standard Test Methods for Cone Penetration of Lubricating Grease. ASTM
International, West Conshohocken, PA. 9. ASTM D2266 – 01 (2008) Standard Test Method for
Wear Preventive Characteristics of Lubricating Grease (Four-Ball Method). ASTM International, West
Conshohocken, PA. 10. ASTM D2596 - 10e1 (2010) Standard Test Method for Measurement of Extreme-Pressure Properties of Lubricating Grease (Four-Ball Method). ASTM
International, West Conshohocken, PA. 11. ASTM D4048 – 10 (2010) Standard Test Method for
Detection of Copper Corrosion from Lubricating
Grease. ASTM International, West Conshohocken,
PA. 12. ASTM D1743 – 13 (2013) Standard Test Method for Determining Corrosion Preventive Properties of Lubricating Greases. ASTM International, West
Conshohocken, PA. 13. ASTM D4049 - 06(2011) Standard Test Method for Determining the Resistance of Lubricating
Grease to Water Spray. ASTM International, West
Conshohocken, PA.
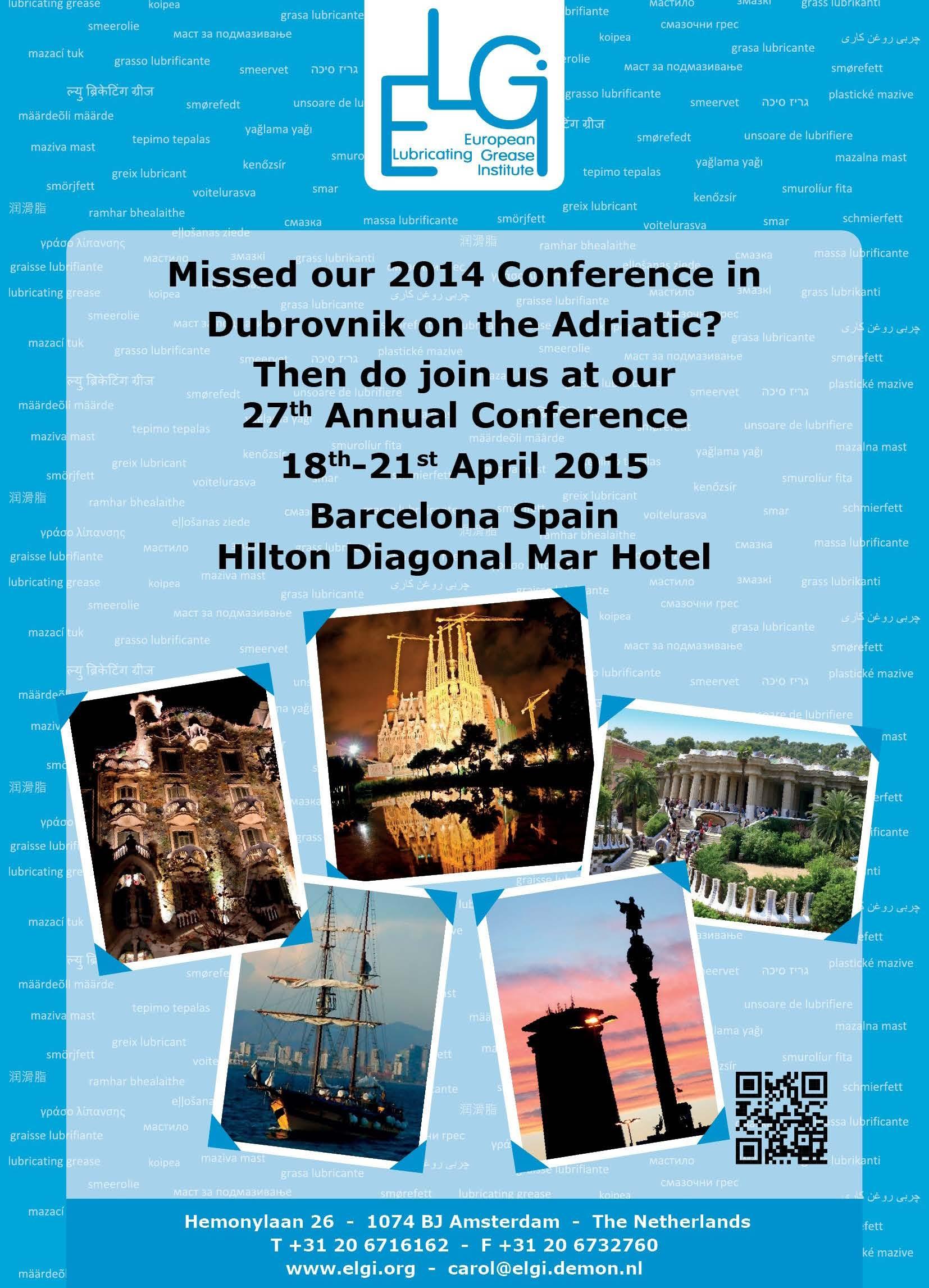