
6 minute read
Synthetic Grease Formulated Using PAO-6 and mPAO-65
Introduction: Paul A. Bessette, * and Ked Hope**
*Triboscience & Engineering, Inc., Fall River, MA 02742 ** Chevron Phillips Chemical Co., LP, The Woodlands, TX 77380
Synthetic lubricants are superior to petroleum based products in terms of thermooxidative stability and low temperature performance. Numerous automotive requirements demand that lubricating grease function at -40ºC while military specification may demand serviceability to -54ºC. MIL PRF 32014 describes a lithium 12-hydroxystearate thickened blend of polyalphaolefins. The viscosity requirements of the specification can be achieved by blending PAO 6 and PAO 40. This paper describes a grease formulated with PAO 6 and mPAO 65. The high viscosity component was synthesized using a metallocene catalyst. The metallocene catalyzed PAO’s differ from conventionally PAO’s in that their pendent groups, the side chains, represent have a comblike structure with a chiral center at the branch carbon. The chirality provides for a random distribution of branch stereoregularity and isomer distribution to yield excellent low temperature properties. The kinematic viscosity requirements for the base oil in the grease are quite specific. At 40ºC, the maximum viscosity is 140 centistokes while at 100ºC the minimum viscosity is 16 centistokes. The specified viscosity requirements have been achieved for typical greases by blending PAO 6 and PAO 40. However, the military specification requires that the low temperature torque as determined by ASTM D1478 not exceed 14,000 g/cm for the starting torque and should not exceed 2800 g/cm for the running torque. We show that decene based PAO 40 is a viable blending component to achieve the viscometrics demanded by the specification while mixedmonomer fluids can be problematical. However, our work suggests that blends using mPAO 65 can produce stellar results in terms of low temperature torque requirements at -54ºC.
Typical Structures of PAO and mPAO materials:
Grease Preparation:

Approximately five kilograms of lithium 12-hydroxystearate grease were prepared from a blend of PAO-6 and mPAO-65 using dry thickener technology. The ratio of ingredients was chosen to produce an NLGI Grade 2 grease. All of the thickener and one half of the base oil blend were heated until the thickener was completely melted above 200ºC after which the balance of the base oil was added to rapidly quench the kettle contents. The gel and various additives were subsequently homogenized at 6000 psi. The composition of the finished grease is shown in Table 1.
Note: The formulation does not contain the necessary ingredients to meet all of the requirements of MIL PRF 32014. The main objective was to determine the viability of mPAO-65 as a blend component.
Table 2 lists the physical properties determined on the grease.
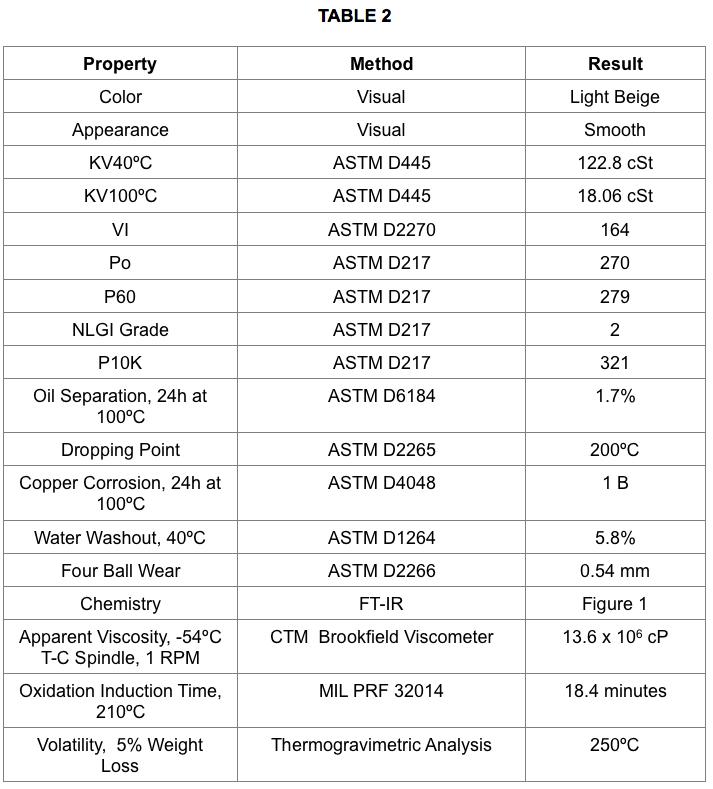
Based on the data presented in Table 2, the kinematic viscosity of the base oil meets the requirements of the specification and the desired NLGI consistency has been achieved. Moreover, the other physical and chemical properties are as expected for the grease. Figure 1 shows the infrared spectrum of the grease.
The infrared analysis clearly depicts a hydrocarbon. The asymmetric and symmetric stretching vibrations of the CH bonds occur at 2955, 2921, and 2851 cm-1 while low energy molecular motions occur at 1462, 1377, and 721 reciprocal centimeters. The prominent peak at 1579 cm-1 is the carbonyl group stretching vibration due to the thickener.The low temperature apparent viscosity of the mPAO 65 grease were compared to a similar grease that was formulated using PAO 40. The low temperature viscosity data for the two greases is shown in Figure 3.
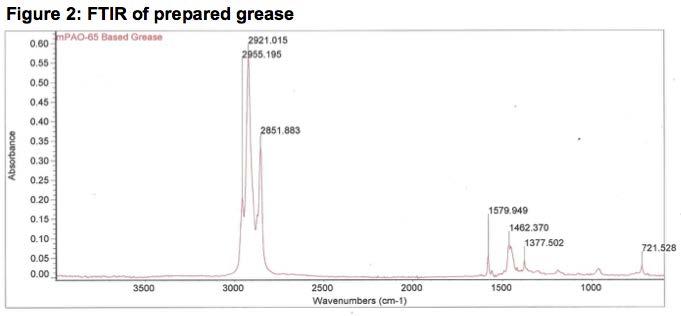
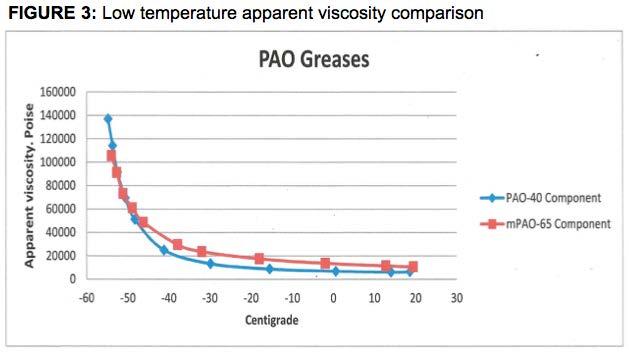
Based on the data shown in Figure 2, mPAO 65 appears to be a suitable blending component for formulating grease to the requirements of MIL PRF 32014. However, a crucial question arose as to the low temperature performance of grease formulated from mPAO 40 versus grease prepared using mPAO 65. Usually, for a given family of oils, a higher viscosity at 40ºC implies a higher viscosity at lower temperatures. However, a blend poses unique challenges and opportunities. The viscosity conundrum is this: mPAO 40 is less viscous than mPAO 65 and requires less PAO-6 to achieve the viscosity target of MIL PRF 32014 while mPAO 65 is more viscous resulting in additional PAO 6 to attain viscosities of 140 cSt max an 40ºC and 16 cSt min at 100ºC. Which fluid has the most influence on blend performance? The answers are provided in Table 3.
The results shown in Table 3 clearly demonstrate the influence of PAO 6 on the low temperature viscosity of the blends. This data was further corroborated with low temperature torque data determined at -54°C shown in Table 4. The viscosity index of the PAO 6 / mPAO 65 is 163 compared to 158. The slightly higher viscosity index is also indicative of the improved viscometrics achieved with the PAO 6 / mPAO 65 blend. FUrthremore, the measured -40°C viscosities shows a 12,933 cSt reduction in the viscosity representing nearly a 25% decrease.
Greases 1 and 2 meet the -54ºC torque requirements of the specification whereas the mix-monomer PAO 40 based grease does
not.
Figure 4 shows the oxidative stability of the mPAO 65 grease fortified with a sulfur based EP agent with AO activity. The test was run at 210°C according to the method in MIL PRF 32014. The extension of the oxidative induction time to nearly 60 minutes is a significant improvement over 48.7 minutes in comparison. In general, this increase is attributable to the improved oxidative stability of the mPAO component. In general, the oxidative stability tends to be governed by the weakest component when all things are equal, that is, when the additives are identical and at the same treat rates. In this case, the differences are in the amount of PAO 6 present as well as the high viscosity component. The extension of the oxidation induction time should translate to a more oxidatively stable or longer lasting material.
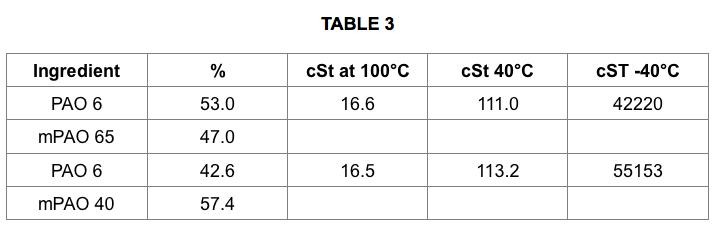
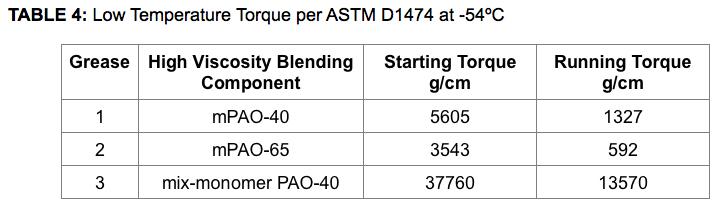

Summary & Conclusion
This paper has sought to examine a comparison of mPAO 65 to PAO 40 for use in grease. A simple lithium grease is used as an example although we would expect similar results for other thickener types. The results indicate that superior low temperature properties are achieved due to both a decrease in the amount of the high viscosity base oil as well as the superior low temperature properties of the mPAO This improvement in low temperature performance is evident in the 1) -40°C kinematic viscosity and 2) viscosity index for an equiviscous base oil blend at 100°C. Furthermore, in the fully formulated grease there is also a substantial reduction in the low temperature starting and running torque for the PAO 6 / mPAO 65 based lithium grease.
Another advantage that is observed is the increase in the oxidative stability of the mPAO based grease. Although this improvement is not as great in contrast to the low temperature advantages, it nonetheless is significant.
This mPAO 65 based lithium grease is intended to serve as just an example of what can be accomplished when using this material in a grease application. The improvements in low temperature performance and high temperature oxidative stability should also be applicable to other thickeners such as, lithium complex, calcium complex, bentonite and other thickener systems as well.