
6 minute read
Automatic Particle Identification and Counting in Greases
Rich Wurzbach, Evan Bupp, Lisa Williams MRG Labs, York, PA, USA Tod Canty, JM Canty, Buffalo, NY, USA
ABSTRACT
Particle counting is a well-established and important consideration in the quality control of new oils and hydraulic fluids. Particle counting is used to monitor the effectiveness of equipment cleanliness protection and particle removal equipment. For greases, the limited ability to filter once obtained by the end-user customer has generally resulted in this focus on particle counting and cleanliness to be overlooked. Additionally, the flow limitations of greases have prevented the use of typical oil particle counting tools from being applied in like manner to grease as a cleanliness verification and evaluation tool. Methods utilizing the preparation of a thin-film of grease for inspection, coupled with new imaging, identification and measurement tools are being developed to automate and standardize an approach to particle counting. Since the impact of abrasive contaminants can be equally destructive in grease lubricated components, tools that enable the monitoring of particulate may allow intervention to minimize abrasive and fatigue wear due to particulate initiated damage.
Metal spectroscopy and ferrous debris monitoring techniques are typically used to evaluate wear and contaminant ingress in greases. There are many ways to determine the elemental content of in-service greases – including Rotating Disc Electrode spectroscopy, Inductively Coupled Plasma spectroscopy, Atomic Absorption spectroscopy, and X-Ray Fluorescence Spectroscopy. These metal spectroscopy techniques are used to detect mixing of different thickeners, wear metals, and anti-oxidant elements remaining by determining the elemental make up of the samples. Ferro-magnetic material is detected using ferrous debris monitoring instrumentation. A sensor is used to measure disturbances in the electromagnetic field caused by ferro-magnetic particles – allowing a quick and nondestructive way to analyze the total ferro-magnetic content in a sample. Microscopic techniques, including analytical ferrography, can be used to look at the wear particle surfaces and determine nature and origin of the wear particle.
Most of these methods is well-known and proven in the industry as effective ways to look at wear particles. However there have been limited techniques to test total particulate in grease, or reliably evaluate new greases for dirt and other contaminant particles. Methods that have been used include “Federal Standard 791D, Method 3005.4, Dirt Content of Grease”, which is a microscopic evaluation using glass plates, and the Hegman gage. The Hegman gage is a sloped channel in a metal block, where a scraper is used to drag the particles to the narrow end. Another method is ASTM D1404 “Deleterious Particles”, which involves placing grease between two plastic plates and rotating them under load. The resulting scratches are counted as an indication of the destructive potential of the grease.
These manual methods for grease particulate evaluation are time consuming and subjective. New technology has been developed using particle imaging as a screening tool for potential damaging wear and contaminant particles present in the grease. This new method allows for a nonsubjective, quantitative and qualitative evaluation of new and used greases to help address the destructive potential of particles in greases.
The Grease Thief Analyzer is a device used to measure the consistency of greases using the die extrusion
method. This method is outlined in ASTM D7918 [2], the standard method for testing inservice greases by integrated tester. The analyzer uses a 1 gram sample and extrudes it as a thin film on a plastic substrate. The plastic substrate is typically then divided into sections for subsequent analysis. In this new method, a source of high intensity light is placed below the substrate, and a high-resolution microscopic camera is place at the opposite side. Additionally, a modification is made to the substrate positioning table, with a cut-out hole to allow the backlight to access the substrate. The images produced are evaluated by a software algorithm to distinguish discrete particles from other optical artifacts. Additionally, the shapes and characteristics of the particles are evaluated to identify the types of particles present, for those particles larger than 20 microns.
The ability to uniformly present the grease as a thinfilm for optical evaluation presents a new opportunity to use proven methods of particle counting and classification that have been utilized for liquid oil samples, such as the methods outlined in ASTM D7596. Using successful lighting methods and software algorithms, with adjustments to both to account for difference in the grease thin-film medium, particle counting of greases becomes feasible.
Particle counting would not be quite the same as the methods used for oil analysis, nor the standard ISO 4406 reporting format for particle counts. Instead, a new scale is proposed that identifies particles down to 10 micron, and provides for three size ranges of >10 micron, >25 micron, and >75 micron. The selection of this scale is consistent with methods used by ASTM proposed standards, including the Hegman gage method. The software is designed to identify the particles, size the particles and then ultimately provide a cleanliness code for the grease. This process could serve as a screening tool for additional wear tests that may need to be performed such as metal spectroscopy or analytical ferrography.
RESULTS
The direct imaging camera setup took advantage of the thin film deposition and strobe backlight in order to achieve optimal transmission of light through the grease. By using strobe backlighting, the presence of shadows was removed which was the cause of false identification of particles in previous versions of testing. The use of a light equalization filter improved the contrast of particles seen within the grease. The testing demonstrated the effectiveness of the strobe LED method in providing sufficient particle illumination for detection and classification.
Utilizing the opacity of the particles, as determined by the brightness of particles based on the amount of transmitted light that can pass through, differentiation is being made between metal particles and non-metals, for particles over a certain threshold dimension. Current work has established that particles with an equivalent spherical dimension of >20 microns can be classified based on this opacity characteristic as metals or nonmetals, as well as major dimensions and aspect ratio.
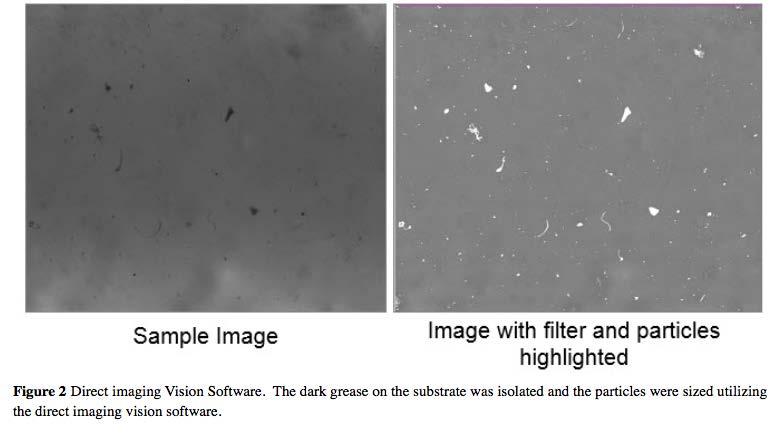
Figure 3 shows an oil sample that was prepared with ferrous debris particles, and introduced to a flow cell. Evaluation of these particles first works to identify all particulate larger than 4 microns, and provide a total particulate count for the sample. By applying algorithms for shape and opacity, additional designations can be made as shown in Table 1.
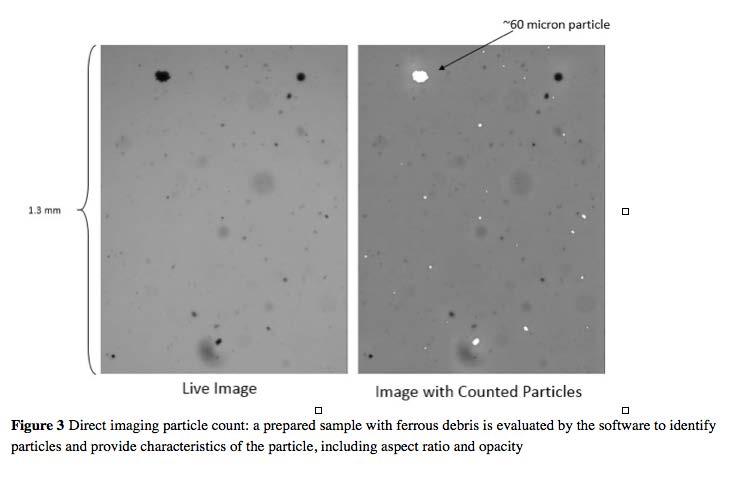

Applying these sample algorithms to the grease samples evaluated as a thin-film can generate a cleanliness quantification using the 10-25-75 micron designations, and classify percentages of particle types as shown in Table 1.
FUTURE WORK
The direct imaging vision software and camera set up has been shown to be a useful technique in identifying particles prepared from a new or used grease sample. Future work includes integrating this technology into the extrusion die grease analyzer as described in ASTM D7918 to serve as a screening tool for particle analysis. This will automate and standardize the process for particle counting in greases, provide a method for counting and classifying particle sizes for cleanliness determination of new greases, and serve as a screening tool for identification of particles and the need to perform microscopic analysis for inservice grease samples. The data being generated by samples analyzed by the integrated system will be presented to the ASTM Integrated Tester subcommittee for technical review and consideration for future balloting as an addition to the ASTM D7918 method for grease analysis.
REFERENCES
[1] ASTM D1404 / D1404M-99(2014), Standard Test
Method for Estimation of Deleterious Particles in Lubricating Grease, ASTM International, West
Conshohocken, PA, 2014.
[2] ASTM D7596-14, Standard Test Method for
Automatic Particle Counting and Particle Shape
Classification of Oils Using a Direct Imaging
Integrated Tester, ASTM International, West
Conshohocken, PA, 2014.
[3] ASTM D7918-15, Standard Test Method for
Measurement of Flow Properties and Evaluation of Wear, Contaminants and Oxidative Properties of Lubricating Grease by Die Extrusion Method and Preparation, ASTM International, West
Conshohocken, PA, 2015.
KEYWORDS
Grease, In-Service, Wear, Particle Count