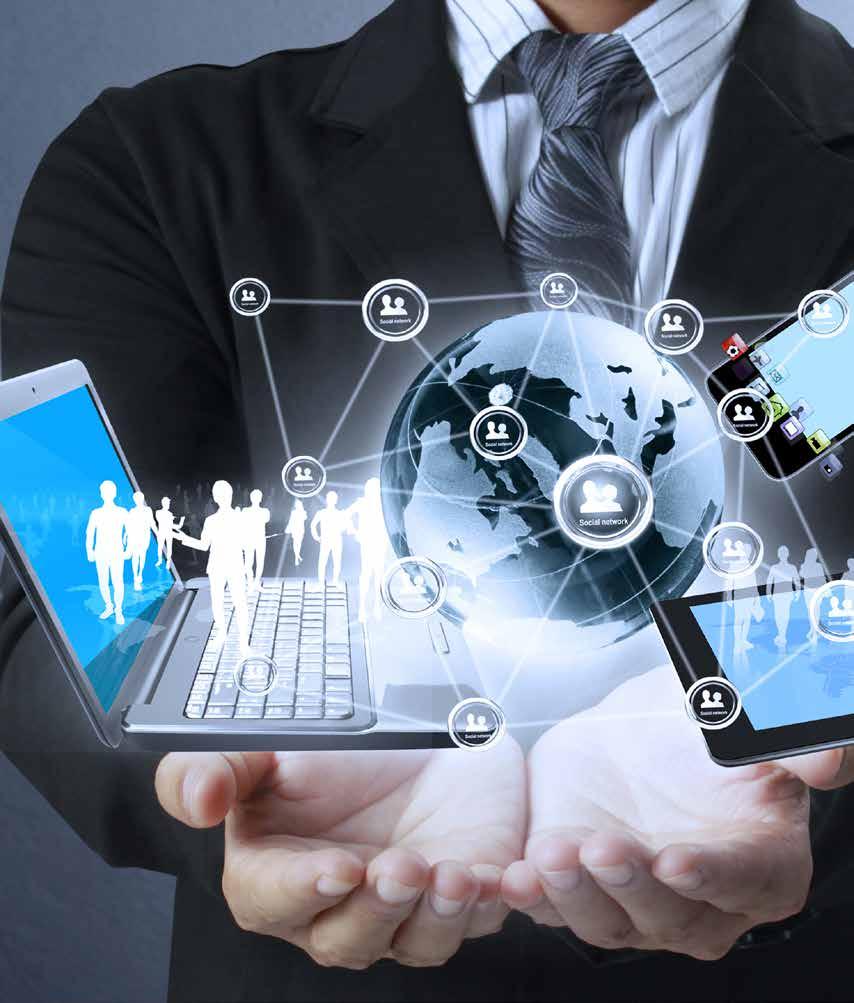
8 minute read
Leveraging Technology To Sustain Business
F
rom employee furloughs and layoffs to disrupted supply chains, there isn’t a corner of the hardwood industry that has been immune to the effects of COVID-19. The industry has been through many trials and tribulations over the last century, and faced each one head-on, adapting to changing circumstances to continue operations.
Today, as we face a global pandemic that has changed the very fabric of our society, the hardwood industry is once again adjusting to new ways of doing business. Thankfully, we live in an age where technology is available to overcome the new challenges we face and we can continue to conduct business.
Technology has made us more connected than we’ve ever been before. The pandemic pushed quick-thinking leaders to have office employees work from home - something many thought would never be possible for their business. Telecommuting has been proven effective. So, is this the new normal? Melissa Bradley, Professor of Impact Investing at Georgetown University, was quoted by the Aspen Institute saying, “Our interconnectedness is here to stay. I believe the work-from-home phenomenon will continue for three reasons. First, it reduces overhead for many companies. Second, it will be hard to ramp the former culture back up again if this lasts longer than six months. Finally, it was a trending concept before the virus.”
The use of software like Skype, GoToMeeting, and cloud file-sharing services has allowed many office and sales personnel throughout the hardwood industry to work from home. A recent NHLA Survey found that a majority of hardwood businesses have embraced the technology that allows their staff to work remotely, with the most popular being the video conferencing software, Zoom, followed by Facetime, and Microsoft Teams. Furthermore, the forced plunge into the world of telecommuting has been a positive experience for most businesses, with 58% of industry companies saying they will likely continue using this newfound communication technology with their staff after the pandemic is over.
“We have software integrators, engineering staff, and sales staff that are all able to perform regular duties from remote locations. The use of programs such as TeamViewer, Zoom, VPNs, and Skype allows us to stay efficient and keep production flowing.” — Bob Pope, with SII Dry Kilns
“There is only one way to survive and thrive when faced with circumstances out of our control, and for which we are unprepared: Adapt.” — Charles F Glassman
NHLA member Bob Pope, with SII Dry Kilns, is a believer in telecommuting, saying, “We have software integrators, engineering staff, and sales staff that are all able to perform regular duties from remote locations. The use of programs such as TeamViewer, Zoom, VPNs, and Skype allows us to stay efficient and keep production flowing. The ability to transfer files for review and oversight allows us to verify that the work performed is accurate and on time. All of these things allow our team to stay focused on our number one goal – to help and support our customers.”
Imagine if a sawmill operator from 1918 – the height of the Spanish Flu – were to see what a sawmill looks like today. He would likely be awed at the efficiency of today’s mills, thanks mainly to automation. The number of lasers, computers, scanners, and sensors would amaze him. He might be shocked that the mill could run with so few people, allowing social distancing to keep employees safe.
Bob continued, “For a number of years now, all of our kiln control systems have come preinstalled with remote accessing software. This has allowed our customers to control and monitor their kilns from anywhere in the world. It has also allowed SII technicians to perform troubleshooting and installation of software updates remotely. So, in normal times what once might have been considered a luxury for kiln operators and mill managers has now made working remotely more of a necessity and a reality.”
Claus Staalner with WoodEye – an NHLA member that manufactures scanners for inspecting and measuring defects in wood - is proud of his company’s contribution to automation, explaining, “Technology and automation help both small and large producers.
TECHNOLOGY TO THE RESCUE IN OHIO
There is an issue that Ohio’s Appalachian hardwoods industry has faced for decades: a disjointed supply chain of loggers, craftsmen, and manufacturers that lacked the visibility needed to reach their maximum level of success. It was technology that provided a solution.
The Appalachian Partnership, Inc. (API) is a business-led nonprofit organization that provides programs and resources that help companies to improve their operations and meet their workforce needs. The Appalachian Partnership received an SBA Regional Innovation Cluster Grant in September of 2015 and hired a Wood Manufacturing Specialist, Frank Roberts, in December of the same year.
Frank brings decades of experience with him as he travels throughout Appalachian, Ohio, explaining what API has to offer. Technical consultation, quality control, needs assessment, production modeling, and other services were available to businesses of all sizes, from six employees to 150, at no cost. The professional services of Frank and his associates, Craig Albright and Patrick Bolton, helped many of Ohio’s hardwood businesses become more efficient, productive, and profitable.
For all the successful projects the API team accomplished through individualized consultation, there was still something missing. Huge leaps in technology and automation have transformed large sawmills into marvels of efficiency, accuracy, and production. Automation has seen dramatic changes in every step of the manufacturing and production process throughout the industry. “We realized the way the industry interacts in the state, across the country, and around the world hadn’t kept up with this automation technology,” Frank said. And just like that, OhioWoodProducts.com was born.
Designed to be Ohio’s foremost wood products resource, OhioWoodProducts. com is a single hub where distinct sectors of the hardwood industry can easily connect. At the heart of the website is the Ohio Wood Products Directory, which is used to help companies develop value-stream mapping strategies and to find new outlets for their products and services. The directory has three main functions: utilize accurate GIS mapping to see where companies are located geographically; provide a detailed profile page to market each company and offer the opportunity to be more visible in Ohio’s $26 billion hardwood industry. Through technology, the website creates an opportunity for businesses of all sizes to increase their national and international visibility and exposure.
The API team also sees a time in the not-too-distant future when the effort could expand beyond Ohio. “Other states are seeing what a powerful tool this is,” Frank said. “We now have the technology to build directories, databases, and search engines more easily and affordably than before.” He envisions the Appalachian regions from Pennsylvania to Georgia, benefiting from a similar platform. “When the economy rebounds, as it inevitably will, technology will help members of the hardwood community to be highly visible and readily accessible.”
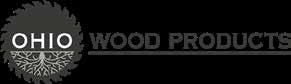
Employees at SII Dry Kilns monitor the progress of their kilns through the use of custom software.
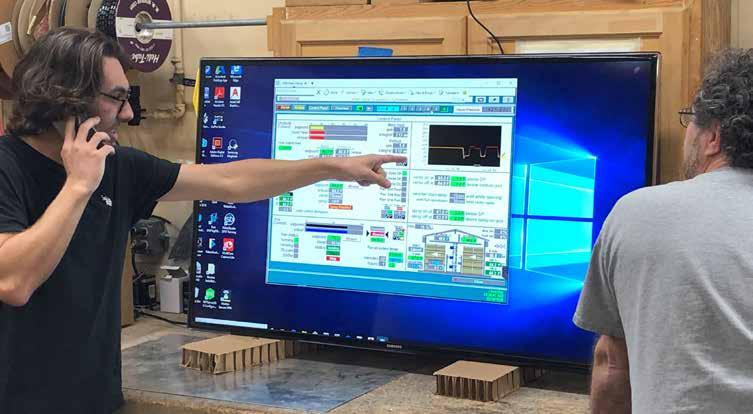
High efficiencies, reliable processing results, and production/process controls should always be held in the highest regard. In a time of a pandemic, having such tools in place allows for a much smoother pass-through.”
The hardwood industry plays a vital part in the supply chain for hundreds of end-products, including many items that are essential during this pandemic: testing swabs, face masks, packaging, pallets, Personal Protective Equipment (PPE), and more. So, it’s critical that businesses keep in touch with their customers. An easy way to stay connected is through the use of social and digital media.
Bob Pope understands the importance of social and digital options, saying, “During this time, we have used several different methods to stay in constant contact with our existing and potential customers - Facetime, Skype, Zoom and good ole fashioned conference calls. We continue to remain active in a variety of trade organizations, including the NHLA and work to support their efforts for remote training and productivity improvement.”
It’s difficult to say anything about the COVID-19 pandemic was lucky. But, looking at it objectively, we are fortunate the epidemic happened in 2020 and not 2010. Ten years ago, automation technology wasn’t anywhere near as effective as it is today. We didn’t have the remote-working options we have now, and the Internet speeds of 2010 could never handle the strain that our technological advances demand today. As the author Charles F Glassman once said, “There is only one way to survive and thrive when faced with circumstances out of our control, and for which we are unprepared: Adapt.” Fortunately, the hardwood industry has been adapting to challenges since its inception and will continue doing so during this pandemic, and any other crisis to come.
SOURCES:
NHLA Technology Survey, May 2020
https://www.economist.com/leaders/2020/04/04/big-techs-covid-19- opportunity
https://news.microsoft.com/covid-19-response/
https://www.manobyte.com/growth-strategy/leveraging-technology-forcovid-19-remote-working
https://www.bellevuereporter.com/news/eastsiders-utilize-technology-tokeep-things-running-during-covid-19-outbreak/
(https://www.aspeninstitute.org/blog-posts/how-covid-19-is-changingglobal-business/)
TRANSLATING OUR KNOWLEDGE INTO RESULTS FOR YOUR BUSINESS . . . THE NHLA INSPECTION SERVICES TEAM OF EXPERTS
The NHLA Inspection Services team is working and available to help you overcome any issues or problems you may be having. Reach out to your area inspector to arrange a consultation by phone or an in-person visit. We Are Here to Help You!
CANADA
n Mark Bear n Tom Byers n Mark Depp n Kevin Evilsizer n Simon Larocque
Dana Spessert Chief Inspector 901-399-7551 d.spessert@nhla.com
Mark Bear Territory: USA - Southern Region
South East and South Central 205-295-8018 m.bear@nhla.com Tom Byers Territory: USA - Northern Region
North Central and North East 814-431-5699 t.byers@nhla.com Mark Depp Territory: USA - Mid-Atlantic Region East and South East 814-246-4941 m.depp@nhla.com Kevin Evilsizer
Territory: USA Midwest & Western Regions North Central, Midwest, West and International 417-260-5416 k.evilsizer@nhla.com
Simon Larocque Territory: Canada 819-712-1640 s.larocque@nhla.com