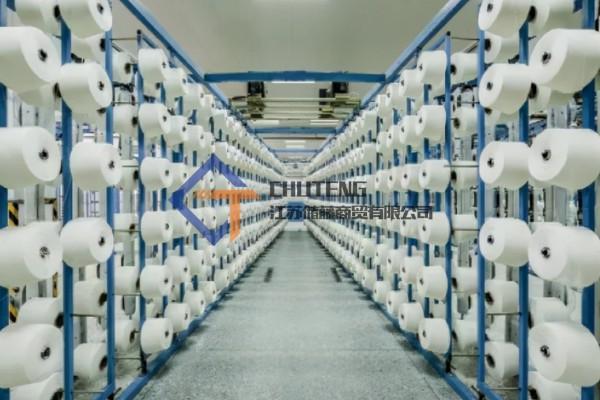
4 minute read
How To Choose Good Quality Denim Fabric (below) ?
How To Choose Good Quality Denim Fabric (below) ?
Choose Good Quality Denim Fabrics
Advertisement
In the last article, we analyzed how to make denim from The Raw Material, Spinning, and Indigo Dyeing, and in this article, we continue to explain.
Weaving
Indigo-dyed warp yarns (vertically) will be interwoven with white weft yarns (horizontally) through a specific tissue structure to create a denim fabric.
For the warp and weft yarns to be interwoven on the weaving machine to form the fabric, the entire warp yarn must be divided into two uppers. Lower layers according to the pattern required by the fabric organization, creating a space for the weft guide (shuttle, slice shuttle, rapier, air or water jet, etc.) to pass through - the bobbin opening - to introduce the weft yarn for interweaving with the warp yarn.
A shuttle means that a narrow shuttle loom (old-fashioned loom) is used, while a slice shuttle, rapier, air-jet, or water jet, a shuttleless loom (modern loom) is used. The shuttle and shuttleless looms difference is that the shuttle loom produces a much narrower width of denim with a woven edge, commonly referred to as a red edge/bare ear, so this slim width denim is also collectively known red edge fabric.
The so-called shuttle loom is equipped with a shuttle and uses the shuttle to drive the weft yarn in a constant horizontal reciprocating motion, creating a woven edge on both edges of the fabric.
However, as the color of this fabric edge is determined by the color of the input selvage, there will also be black ears, gold ears, silver ears, blue ears, purple ears, etc.
It is important to stress that there is no essential difference between red selvage fabric and other denim in terms of the craftsmanship and quality of the product. Whether it is red ears or any different ears, it does not mean that its quality is better. It is generally more expensive because the fabric is a product of low productivity, time-consuming and labor-intensive, and the high cost leads to higher prices.
The fact that there was no woven edge was irrelevant to most consumers, so the slow and inefficient narrow-width shuttle loom was gradually phased out of mass commercial production from the 1940s onwards.
Of course, in the eyes of the original cattle enthusiast, it was not so much the quality as a vintage sentiment that made Barefoot the first brand to use the red hem. It was it that created this iconic denim feature that drew so many imitations from replica brands.
After the whole
Denim can be cut and sewn directly into jeans once woven, known as raw denim, dry denim, or unwashed denim, or what we call raw cow. You can think of this type of denim as denim in its natural state, untreated blank denim.
However, this untreated denim will have a variable degree of shrinkage after the first wash. This is why most denim brands, whether raw cattle brands or other mass-produced denim brands, choose sanforised denim, i.e., denim that has been pre-shrunk. (In fact, there are very few denim fabrics on the market that are entirely untreated.)
Denim is spun, dyed, and woven so that the yarn is under continuous tension, stretching its length and width. If the fibers do not shrink to their original size before the denim is made into jeans, they shrink once the fibers relax and return to their average length, i.e., they are washed.
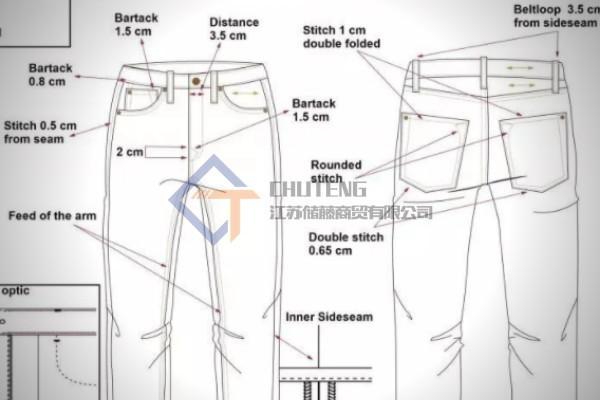
Sanforization refers to the pre-shrinking of the fabric by water, steam, heat, and pressure to facilitate the design of the subsequent cut. The shrinkage of jeans made from pre-shrunk denim has been reduced from 5-10% to a maximum of 1-3%, which is already minimal. With or without a wash treatment, the shrinkage of the jeans is no longer significant, making it easier to choose a size.
Many people ask whether sanforized and one-wash are considered raw cattle or not, but this is a bit difficult to define. Anyway, whether or not they have been pre-shrunk or official stripped doesn't have much of an effect on the cattle being raised.
Without any treatment, denim can look shaggy due to the excess hairiness of the cotton fibers. There is no dimensional stability to speak of, so usually, apart from raw cattle, denim is finished, which can effectively improve the style and feel of the denim.
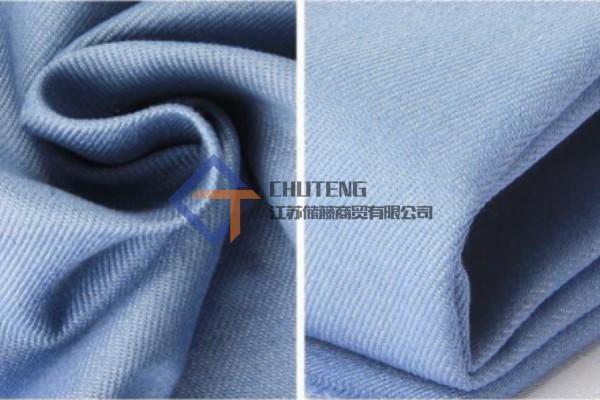
There are two types of finishing: functional finishing, which is used to correct or prevent dimensional stability problems, and creative finishing, which improves the look and feel of the fabric.
While avid raw cattle enthusiasts want to keep their jeans in their most original and pristine condition, most consumers look for a soft, comfortable fit and a personalized look created by washing.
After finishing the denim fabric, it can remove the hairiness and impurities on the fabric surface, making the fabric surface smooth and bright. Eliminate the potential shrinkage of the internal fabric stress, control the finished warp and weft shrinkage rate and eliminate the possible weft distortion internal stress so that the product can obtain a stable shape in advance. Change the fabric feel and sewing performance. Which is the last part of denim fabric production; output finished fabric for garment processing.
Plain indigo jeans are no longer able to meet the demands of a market that is constantly asking for new colors and a softer touch, which is why denim manufacturers are continually exploring new technologies to enhance the feel, style, and visual impact of their fabrics.
To read the previous article you can click here!
That's all there is to know about denim fabric production. If you are interested in our products, you can click contact us!