
6 minute read
Fast and GMP-compliant labeling
Establishing a valid labelling process is key in pharma manufacturing. The process also needs to be as efficient, fast and sustainable as possible. When Steierl-Pharma, based in Bavaria, Germany, needed to optimise its new labelling machine with modern inspection technology, the pharma manufacturer turned to Omron for a suitable system.

H ARDLY ANY OTHER industry is subject to such stringent regulations and quality requirements as the pharmaceutical industry. This applies to active ingredients, manufacturing, product storage and labelling. Labels must be robust and adhere reliably to a product’s packaging for the usability period of up to five years. Labels carry important information such as the name of the pharmaceutical product, active ingredient(s), the manufacturer, and variable data such as expiration date, lot number and serialisation information. Steierl-Pharma is a medium-sized pharmaceutical company specialising in naturopathy. It produces medicines in liquid dosage form packaged in cylindrical glass containers with 3 600 units passing through the production line in one hour. Its product range includes medicines for the musculoskeletal system, to lower blood pressure, for relieving migraines or skin diseases, and for treating flu-like infections.
To ensure its labelling process is both efficient and sustainable, SteierlPharma consulted with automation experts at Omron. Since installing a new labelling system with smart camera technology, the manufacturer can label its products reliably and at a high speed. These labels are printed with variable data on batch designation, expiration date and if required, the dispensing notice “sample not for sale”.
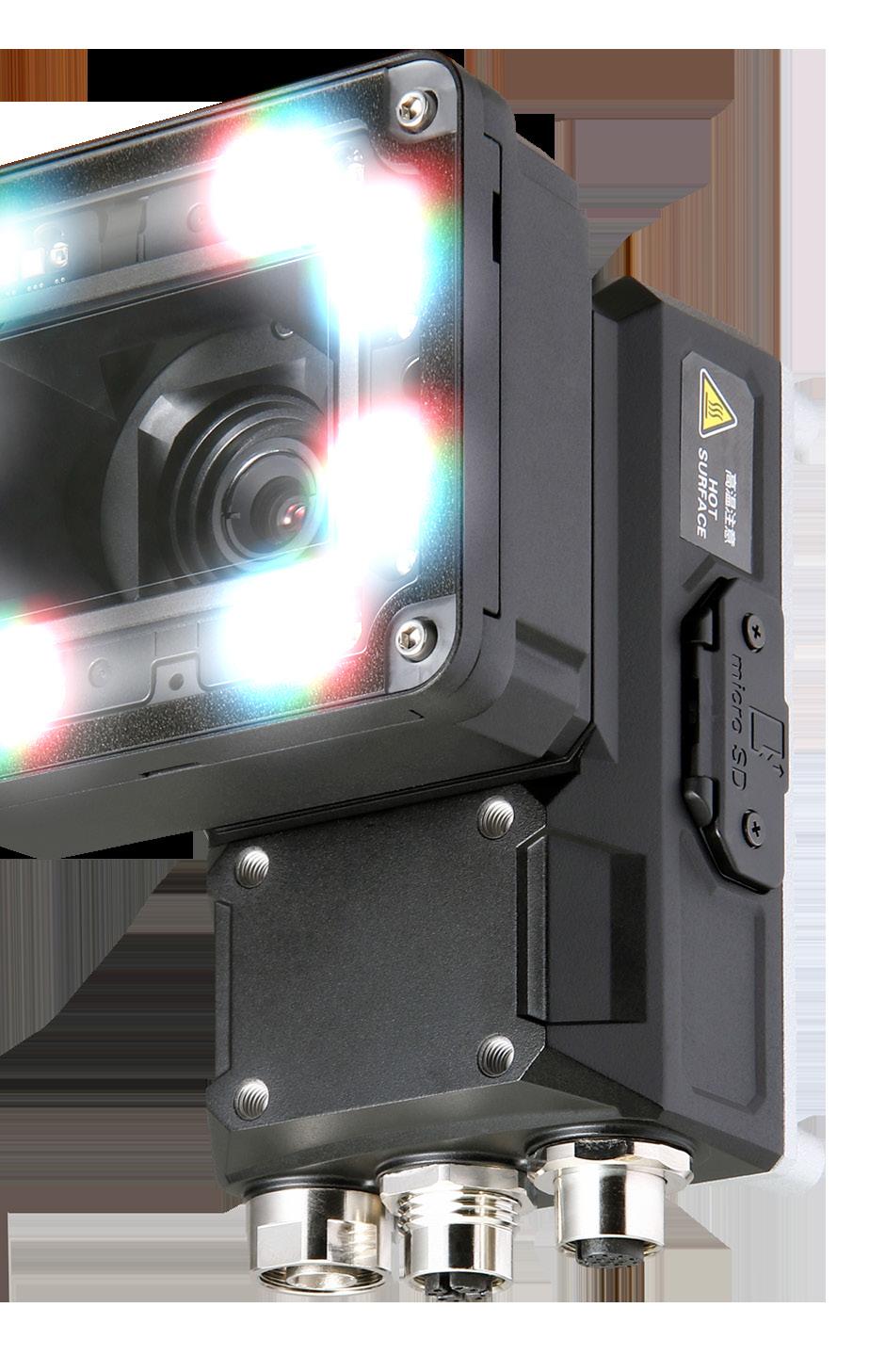
A CLOSER LOOK AT THE PROCESS
In pharma manufacturing, good manufacturing practices (GMP)certification guarantees process integrity and conformity with applicable regulations. Steierl-Pharma holds the required manufacturing license for medicinal products as well as a GMP certificate. The manufacturer’s filling and packaging line is designed with a production capacity of around 3 600 units per hour. It consists of a filling and capping machine, a labeller and a packaging machine. The line ensures a continuous and seamless process consisting of filling and closing the bottles with a dropper insert and a screw cap. The closed bottles then leave the cleanroom and enter the labeller, where they are labelled and inserted in a folding carton together with an information leaflet in the packaging machine.
OVERCOMING HISTORICAL CHALLENGES
In 2019, a project team at SteierlPharma began initial considerations to introduce a replacement for an already older labelling machine. The labelling machine used until then already had a smart camera-based inspection system to check the identity of the label and the variable data (batch name and expiration date). However, this had two drawbacks. Labels were repeatedly misread as “bad” labels, and the units that
were in fact “bad” were not being rejected, but rather stopping the labelling process. This meant that when the machine stopped, the bottles backed up into the filling machine and the packaging machine ran empty. “So, we had a bottleneck in our process,” reports Steffen Wegner, managing director of Steierl-Pharma. “That’s why we worked with the machinery manufacturer Herma to find a suitable inspection system. The focus here was on high reliability and pricing.” The aim was to develop a labelling machine that not only met GMP requirements, but also ran without interruption during regular operation. One of the central criteria was that the new inspection system had to work particularly precisely. Bad units, such as those with an incorrect or illegible barcode or batch or expiry date errors, must be detected reliably. Steierl-Pharma wanted a high level of specificity and sensitivity to ensure the system only detects actual bad units and ejects them from the process. And with an output of around 60 labels per minute, the inspection system needs to complete the complex inspection tasks within a time window in the range of milliseconds.
SMART CAMERA OFFERS ENHANCED VISUAL INSPECTION
The central component in this project is the inspection system. Wegner explains: “We decided on the Omron FHV7 smart camera after running a test on our label material on site, supported by an Omron application engineer. We were effectively supported by Omron throughout the entire development process up to commissioning and qualification of the machine and beyond.” With the help of the FHV7, the Herma labelling machine at Steierl-Pharma checks the identity of the label based on the pharmaceutical code and verifies the batch number and expiration date via optical character validation (OCV) for compliance with the specifications. The FHV7 series smart camera provides illumination and image processing functionality for enhanced visual inspections. Due to its world-first, multi-colour light and a powerful highresolution 12-megapixel camera, just one FHV7 camera is needed to perform high-precision visual inspections of the production line.
During the performance qualification, the project managers involved were surprised by the extremely high specificity of the FHV7. “We could not believe the level of reliability of the Omron FHV7 inspection system. As part of the challenge test, we deliberately introduced mislabels, all of which were reliably detected – but with a throughput of several 10 000 labels, not a single good label was incorrectly read as a bad label,” reports Wegner. Even a single faulty unit could cause a lot of trouble in a GMP-regulated environment. By using the new camera, such situations do not occur, and the machine outages caused by the incorrect reading of actual good units can also be prevented. Another advantage of the Omron camera is the software, which is intuitive to use and does not require lengthy training. “I also really like the option of a customisable user interface, and so do the users. There is only one window in which, for example, the target code, batch designation and expiration date can be entered. Code verification and OCV can also be performed. It’s all very clear and simple,” explains Wegner. The software runs on any current Windows system and communicates directly with the FHV7 via the local network. He also praised the high inspection speed of the Omron system. The complex individual inspection of a label takes just 80 milliseconds, which Wegner says is “impressively fast”. Steierl-Pharma is very satisfied with the new labeller and Omron’s inspection technology. “In a highly regulated environment such as the pharmaceutical industry, manufacturers must be able to fully rely on the technology they implement while successfully completing the qualification thereof. This was the case at SteierlPharma,” says Wegner. “The cooperation with the sales and application team has been excellent.” Since Steierl-Pharma has had such a positive experience with Omron, it is planning to convert an existing packaging machine to Omron inspection technology in the near future. •
Omron – industrial.omron.co.za Steierl-Pharma – www.steierl.de